Журнал НАКС «Сварка и диагностика». Проекты правовых документов и стандартов
1. Новости Информационного отдела.
Рады сообщить, что с 1 марта база периодических изданий пополнилась журналом НАКС «Сварка и диагностика»
Информация об издании:
1. Издается с 2007 года;
2. Журнал зарегистрирован Федеральной службой по надзору в сфере связи и массовых коммуникаций. Свидетельство о регистрации ПИ № ФС77-47389 от 23 ноября 2011 г.;
3. Главный редактор: президент НАКС, академик РАН, заведующий кафедрой «Технологии сварки и диагностики» МГТУ им. Баумана Николай Павлович Алёшин;
4. Издательство: ООО «НАКС Медиа», г. Москва;
5. Периодичность выпуска – 1 раз в 2 месяца;
6. Тираж: 3000 экземпляров;
7. Объем журнала – 64 страницы;
8. Формат издания: А4;
9. Тип печати: полноцветная офсетная;
10. Распространение: каталог «Роспечати» и другие агентства;
11.
Журнал «Сварка и Диагностика» входит в Перечень российских рецензируемых научных журналов и изданий Высшей аттестационной комиссии (ВАК) Минобрнауки РФ.
Журнал «Сварка и Диагностика» включает в себя несколько разделов:
1. Информационный — новости Системы аттестации сварочного производства и деятельности Национального Агентства Контроля Сварки, а также обзоры профильных выставок, конференций, семинаров, освещаются значимые памятные даты и юбилеи.
2. Научно-технический — научные статьи и основные научные результаты диссертаций на соискание ученой степени доктора и кандидата наук.
3. Производственный — материалы о новейших исследованиях и достижениях в области сварки и родственных технологий в важнейших производственных сферах экономики России: в нефтегазовом комплексе, в атомной энергетике, машиностроении, в строительстве и других отраслях промышленности.
4. Библиография – обзор патентов и свидетельств РФ.
В журнале публикуются статьи известных ученых — академика НАН Украины Б. Е. Патона, академика РАН Н.П. Алёшина, руководителей научных школ и известных специалистов – д.т.н., профессора Г.В. Конюшков а (Саратов), д.т.н., профессора В.В. Атрощенко (Уфа), член-корреспондента РАН В.А. Лопоты (Москва), член-корреспондента РАН В.И. Лысака (Волгоград), д.т.н., профессора В.Ф. Лукьянова (Ростов-на-Дону), д.т.н., профессора В.А. Судника (Тула), д.т.н., профессора Я.Г. Смородинского (Екатеринбург) и других. В журнале публикуют результаты своих разработок известные в России организаторы промышленного производства, такие как д.т.н. А.С. Зубченко (Москва), д.т.н. А.В. Люшинский (Раменское), к.т.н. В.В. Рощин (Москва) и другие.
Поддержание высокого научно-технического уровня публикаций в журнале обеспечивает редакционная коллегия во главе с Н.П. Алёшиным. Несмотря на то, что журнал довольно молодой, с небольшой пока биографией, на сегодняшний день он является авторитетным периодическим изданием по сварке и родственным технологиям в России, о чем свидетельствует и импакт-фактор В настоящее время журнал активно развивается и укрепляет свои лидирующие позиции среди научных издательств России и стран СНГ.
2. Новости портала www.normacs.info
В базу NormaCS добавлены новые своды правил и изменения к сводам правил.
!!! И снова открыто публичное обсуждение проекта изменения № 1 ТР ТС 032/2013 «О безопасности оборудования, работающего под избыточным давлением».
Утверждена методика разработки нормативов на работы по подготовке проектной документации, но приказ пока еще не опубликован.
Минстрой РФ опубликовал стандарт «Умного города» — набор базовых и дополнительных мероприятий, которые предстоит выполнять всем городам-участникам ведомственного проекта Цифровизации городского хозяйства «Умный город» в срок до 2024 года.
В статье приведено мнение аналитиков о грядущем подорожании жилья.
Проекты правовых документов и стандартов:
проект изменения № 1 ТР ТС 032/2013 «О безопасности оборудования, работающего под избыточным давлением»;
два проекта ГОСТ Р и один проект ПНСТ по материалам для автомобильных дорог;
проект пересмотра ГОСТ 5640-68 Сталь.
три проекта ГОСТ по сельскохозяйственной технике.
ПОДРОБНЕЕ:
ПНСТ (проект). Дороги автомобильные общего пользования. Метод определения условий эксплуатации конструктивных слоев дорожных одежд
Текст обсуждения:
Публичное обсуждение проекта продлится до 01 мая 2019 г.
В настоящее время в РФ действуют комплексы стандартов, регламентирующие системы проектирования асфальтобетонных смесей. Также действуют различные стандарты по классификации битумных вяжущих материалов применяемых для асфальтобетонных смесей. При этом применимость битумных вяжущих для дорожного строительства зависит от климатических и транспортных условий их эксплуатации. Климатические условия эксплуатации в свою очередь определяются расчетными температурами дорожных покрытий, которые в свою очередь зависят от температур воздуха в районе строительства автодороги.
Скачать текст проекта
Скачать пояснительную записку
Участвовать в обсуждении
ГОСТ 5640 (проект, первая редакция). Сталь. Металлографический метод оценки микроструктуры листового проката и ленты
Текст обсуждения:
Публичное обсуждение проекта взамен ГОСТ 5640-68 продлится до 01 мая 2019 г.
Проект стандарта разрабатывается взамен межгосударственного стандарта ГОСТ 5640- 68 с целью включения методов оценки структурной полосчатости с помощью эталонов и с помощью автоматического анализа изображений, а также включения соответствующей шкалы для определения балла.
В ГОСТ 5640-68 имеются стандартные шкалы только для феррито-перлитной полосчатости, тогда как современные стали могут иметь феррито-бейнитную, бейнитную или более сложную структуру. Кроме того, используемый в ГОСТ 5640-68 метод стандартных шкал устарел, так как субъективен и дает лишь полуколичественное описание структуры от 0-го до 5-го балла для ограниченного класса сталей, для которых в ГОСТ 5640-68 имеется соответствующая стандартная шкала.
Скачать текст проекта
Скачать пояснительную записку
Участвовать в обсуждении
ГОСТ (проект, RU, первая редакция). Техника сельскохозяйственная. Раздатчики кормов. Методы испытаний
Текст обсуждения:
Публичное обсуждение проекта продлится до 30 апреля 2019 г.
Стандарт распространяется на раздатчики, раздатчики-смесители кормов стационарные и мобильные, применяемые в животноводстве, и устанавливает методы их испытаний.
В настоящее время всеми МИС Минсельхоза России СТО АИСТ 19.1−2008 используется при испытаниях вышеуказанных типов машин и устанавливает методы оценки только функциональных показателей и не содержит методы оценки безопасности конструкции, надежности, энергетических, эксплуатационно-технологических, экономических показателей. Аналогичные национальные, и межгосударственные стандарты по испытанию раздатчиков кормов отсутствуют.
При разработке проекта межгосударственного стандарта учтены требования действующих межгосударственных и национальных стандартов по видам оценок.
Скачать текст проекта
Скачать пояснительную записку
Участвовать в обсуждении
ГОСТ (проект, RU, первая редакция). Техника сельскохозяйственная. Машины и инвентарь для обрезки плодовых деревьев и виноградных кустов, удаления, измельчения обрезков лозы и веток. Методы испытаний
Текст обсуждения:
Публичное обсуждение проекта продлится
Стандарт распространяется на навесные, прицепные и самоходные машины и инвентарь для обрезки плодовых деревьев, виноградных и ягодных кустов, удаления, измельчения обрезков лозы и веток, подвязки виноградных побегов и устанавливает методы их испытаний.
В настоящее время всеми МИС Минсельхоза России СТО АИСТ 15.1−2010 используется при испытаниях вышеуказанных типов машин и устанавливает методы оценки только функциональных показателей и не содержит методы оценки безопасности конструкции, надежности, энергетических, эксплуатационно-технологических, экономических показателей. Аналогичные национальные, и межгосударственные стандарты по испытанию машин и инвентаря для обрезки плодовых деревьев и виноградных кустов, удаления, измельчения обрезков лозы и веток отсутствуют.
При разработке проекта межгосударственного стандарта учтены требования действующих межгосударственных и национальных стандартов по
видам оценок.
Скачать текст проекта
Скачать пояснительную записку
Участвовать в обсуждении
ГОСТ (проект, RU, первая редакция). Техника сельскохозяйственная. Машины для подготовки семян. Методы испытаний
Текст обсуждения:
Публичное обсуждение проекта продлится до 30 апреля 2019 г.
Стандарт распространяется на комплекты оборудования, линии и машины для калибрования, шлифования, сегментирования, дражирования, протравливания, протравливания с инкрустацией, термического и электрофизического обеззараживания семенного материала и устанавливает методы их испытаний.
В настоящее время всеми МИС Минсельхоза России СТО АИСТ 15.1−2010 используется при испытаниях вышеуказанных типов машин и устанавливает методы оценки только функциональных показателей и не содержит методы оценки безопасности конструкции, надежности, энергетических, эксплуатационно-технологических, экономических показателей. Аналогичные национальные и межгосударственные стандарты по испытанию машин для подготовки семян отсутствуют.
При разработке проекта межгосударственного стандарта учтены требования действующих межгосударственных и национальных стандартов по видам оценок.
Скачать текст проекта
Скачать пояснительную записку
Участвовать в обсуждении
Все новые проекты стандартов выложены на нашем сайте в разделе проекты http://www.normacs.info/projects
Диагностика сварных конструкций
Техническая диагностика сварных конструкций – занимается установлением и изучением признаков, характеризующих техническое состояние изделий, для предсказания возможных отклонений контролируемых параметров (например, длина трещины или толщина изделия) за допустимые пределы, вследствие чего возникают внезапные отказы. Техническая диагностика даёт возможность оценить продолжительность эксплуатации изделия, т. е. его долговечность при появлении дефектов.
Основными задачами диагностики технического состояния являются контроль и оценка качества изделия. В задачу контроля качества входят измерение размеров, определение свойств, проверка сплошности и однородности материала и конструктивного элемента с обязательной проверкой соответствия материала и изделия регламентируемым требованиям НТД.
Диагностирование (испытания) при исследовании процессов старения, износа и усталости материалов, выбор параметров конструкций, позволяющих определить их техническое состояние, и оценку фактических значений диагностических параметров, достигнутых при изготовлении, проводят в основном В лабораторных условиях на относительно ограниченном числе образцов. При испытаниях используют тестовые воздействия на конструкции, то есть воздействуют на объект только для целей диагностики.
Диагностирование в процессе эксплуатации осуществляется при рабочих воздействиях либо внешним осмотром конструкций, либо при помощи диагностической аппаратуры, дающей возможность измерять или контролировать нужный параметр с заданной точностью.
Для перехода от измеренных физических величин к искомым параметрам, характеризующим искомые свойства материалов конструкций, используют тарировочные зависимости, то есть производят настройку диагностических средств на образцах с известными и по возможности близкими к контролируемому объекту свойствами.
Цель неразрушающих методов контроля сводится к обнаружению дефектов и к постановке задачи по контролю и оценке качества материала в исходном состоянии. Неразрушающие методы контроля служат инструментом для улучшения качества конструирования и технологических процессов изготовления аппаратов и конструкций.
Диагностика и ремонт сварочного оборудования
Сервисный центр магазина «Сварка» выполняет диагностику и ремонт сварочных аппаратов: Selco, Wallius, Wameta, Сварис, FoxWeld, EWM, Kemppi, ESAB, ПДГ и др. Производим ремонт инверторных сварочных аппаратов или любого другого типа.
Правила проведения диагностики сварочного оборудования
- Оборудование принимается для диагностики только в чистом виде.
Очистка от пыли и грязи — платная услуга.
- Стоимость диагностики — БЕСПЛАТНО.
- Срок проведения диагностики: от — до 5‐ти рабочих дней. В случае необходимости отправки оборудования Изготовителю срок диагностики согласовывается дополнительно.
Правила проведения платного ремонта оборудования
- Оборудование принимается в платный ремонт после оплаты диагностики.
- Срок ремонта от 3 до 30 дней согласовывается индивидуально.
- Срок гарантии на проведённый ремонт определяется типом отремонтированного узла.
Вы можете отремонтировать сварочный аппарат в нашем сервисе, для этого обратитесь в магазин сварочного оборудования.
Получите информацию о наличии необходимого сварочного оборудования в Петербурге, а также о возможности купить сварочный аппарат со скидкой по акции, приобретению по акции средств защиты: костюм сварщика, сварочные маски, спецодежду для сварщиков со спилком.
У нас Вы можете купить сварочные электроды всех диаметров, газовую горелку, газовый баллон от 5 до 50 л, а также купить в розницу и оптом профессиональное сварочное оборудование.
Мы ждем Вас в нашем сервисном центре.
Подробная инструкция по ремонту сварочного оборудования.
Внимание! Аппарат принимается на ремонт только в чистом виде и кабелей заземления и электрододержателей.
Гарантийный ремонт аппаратов
- Если аппарат на гарантии, клиент предоставляет гарантийный талон.
- Если аппарат не гарантийный, покупатель оплачивает сумму диагностики.
- Не гарантийные аппараты принимаются в ремонт только после оплаты диагностики.
- Продавец делает скан гарантийного талона. Гарантийный талон остается на руках у клиента. С задней стороны гарантийного талона ставится дата приемки аппарата в ремонт с печатью СЦС.
- Продавец делает два экземпляра акта о приемке на ремонт и помещает их в папку «РЕМОНТ» за файлом «В РАБОТЕ» в отдельном файле, туда же кладется скан гарантийного талона и чека. В акте указываются возникшие неисправности, указывается, что это гарантийный ремонт, а так же модель и серийный номер.
Акт приемки оборудования в ремонт:
- модель и серийный номер аппарата,
- обязательная сумма диагностики, согласованная с покупателем,
- описание дефекта и наличие внешних механических повреждений (следы ударов, вмятины, оплавленные коннекторы и вилки, выдернутые из корпуса кабель и т.д.).
- комплектация (коробка, наличие ремня и т.п.)
- копия гарантийного талона,
— гарантийный или не гарантийный ремонт, - ФИО покупателя или название компании и телефоны для связи,
- подписи сотрудника магазина и покупателя.
- Покупателю сообщается, в течение какого времени ему позвонят и назовут стоимость ремонта.
- При перемещении аппаратов в мастерскую, необходимо приложить к аппарату один экземпляр акта приемки на ремонт, на нее наладчик вносит следующую информацию: проведенные работы и их стоимость, замена деталей, с прилагаемыми кассовыми и товарными чеками и акт перемещения. Если аппаратов передается несколько штук – все они вносятся в один акт перемещения.
На актах перемещения ставят свой подписи сотрудники, отгрузившие аппарат и принявшие его. Один из актов остается в магазине, второй – у менеджера по ремонту.
- В мастерской принимает аппарат наладчик и менеджер по ремонту. Последний ведет учет ремонтных аппаратов в реестре.
- После диагностики аппаратов менеджер по ремонту передает информацию по электронной почте о ее итогах (гарантийный случай или нет, стоимость работ, деталей и т.д.). Сотрудник магазина связывается с покупателем и озвучивает стоимость работ, если ремонт не гарантийный. Ремонт начинается только после согласия покупателя с названной суммой. В случае отказа покупателя, аппарат возвращается без возврата суммы диагностики.
- Сотрудник заносит в акт заявки на ремонт полученную информацию от наладчика и итог разговора с клиентом.
- Сотрудник, который забирает аппарат обратно, расписывается в приемке аппарата на двух актах о перемещении аппарата. Акты возвращаются в папку.
- После ремонта аппарата на заявке на ремонт должны быть указаны все исправленные неисправности, стоимость деталей и затраченное на ремонт время.
- При возвращении аппаратов из мастерской, на самом аппарате наклеивается надпись «готово», сотрудники магазина отзваниваются клиенту о готовности аппарата. В актах о перемещении делается пометка о приемке аппарата с мастерской с указанием даты.
- После возвращения аппарата клиенту, в заявках и гарантийном талоне делается отметка «выдано клиенту» с указанием даты и подписями сотрудника, выдавшего аппарат, и печатью СЦС и клиента. Также клиенту выдается заявка о приемке на ремонт с описанием проведенных работ и стоимостью.
- После окончания всех операций документы вкладываются в файл, который перемещается за файл «ОТРАБОТАННЫЕ».
Не гарантийный ремонт аппаратов
- Если аппарат не гарантийный, покупатель оплачивает сумму диагностики.
- Не гарантийные аппараты принимаются в ремонт только после оплаты диагностики.
- В заявке указываются возникшие неисправности, указывается, что это не гарантийный ремонт, а так же модель и серийный номер.
- 3-й экземпляр отдается клиенту. В акте указываются возникшие неисправности, указывается, что это не гарантийный ремонт, а так же модель и серийный номер.
Акт приемки оборудования в ремонт:
- модель и серийный номер аппарата,
- обязательная сумма диагностики, согласованная с покупателем,
- описание дефекта и наличие внешних механических повреждений (следы ударов, вмятины, оплавленные коннекторы и вилки, выдернутые из корпуса кабель и т.д.)
- комплектация (коробка, наличие ремня и т.п.)
— гарантийный или не гарантийный ремонт, - ФИО покупателя или название компании и телефоны для связи,
- подписи сотрудника магазина и покупателя.
- Покупателю сообщается, в течение какого времени ему позвонят и назовут стоимость ремонта.
- При перемещении аппаратов в мастерскую, необходимо приложить к аппарату один экземпляр акта приемки на ремонт, на нее наладчик вносит следующую информацию: проведенные работы и их стоимость, замена деталей, с прилагаемыми кассовыми и товарными чеками и акт перемещения.
Если аппаратов передается несколько штук – все они вносятся в один акт перемещения. На актах перемещения ставят свой подписи сотрудники, отгрузившие аппарат и принявшие его. Один из актов остается в магазине, второй – у менеджера по ремонту.
- В мастерской принимает аппарат наладчик и менеджер по ремонту. Последний ведет учет ремонтных аппаратов в реестре.
- После диагностики аппаратов менеджер по ремонту передает информацию по электронной почте о ее итогах (гарантийный случай или нет, стоимость работ, деталей и т.д.). Сотрудник магазина связывается с покупателем и озвучивает стоимость работ. Ремонт начинается только после согласия покупателя с названной суммой. В случае отказа покупателя, аппарат возвращается без возврата суммы диагностики.
- Сотрудник заносит в акт заявки на ремонт полученную информацию от наладчика и итог разговора с клиентом.
- Сотрудник, который забирает аппарат обратно, расписывается в приемке аппарата на двух актах о перемещении аппарата.
- После ремонта аппарата на заявке на ремонт должны быть указаны все исправленные неисправности, стоимость деталей и затраченное на ремонт время.
- При возвращении аппаратов из мастерской, на самом аппарате наклеивается надпись «готово», сотрудники магазина отзваниваются клиенту о готовности аппарата. В актах о перемещении делается пометка о приемке аппарата с мастерской с указанием даты.
- После возвращения аппарата клиенту, в заявках делается отметка «выдано клиенту» с указанием даты и подписями сотрудника, выдавшего аппарат, и печатью СЦС и клиента. Также клиенту выдается заявка о приемке на ремонт с описанием проведенных работ и стоимостью.
Стоимость диагностики – БЕСПЛАТНО. Чек прикрепляется к гарантийному талону или акту о приемке в случае не гарантийного ремонта. Взимается с клиента при приемке аппарата на ремонт. Если по каким-либо причинам оплата не была принята, то об этом делается пометка в заявке на ремонт, как и при оплате по безналичному расчету.
При выдаче аппарата клиенту пробивается чек на сумму ремонта, указанную в акте на ремонт или выставляется счет, если оплата по безналичному расчету.
Все продаваемое в магазине сварочное оборудование имеет необходимые сертификаты государственного образца.
На оборудование всех производителей предоставляется гарантийное обслуживание. Также все производители силами своих сервисных центров осуществляют и послегарантийное обслуживание.
Наш магазин «Сварка» работает только с теми производителями, качество оборудования и уровень обслуживания которых находятся на высоком уровне.
Гарантийные сроки и адреса сервисных центров:
- Сварог — Гарантия 5 лет распространяется на аппараты серии ARC и MIG с максимальным током сварки до 200 А (модели аппаратов уточняйте у менеджеров) и все аппараты серий PRO и EASY. На остальные аппараты, включая промышленные модели гарантия — 24 месяцев.
- KEMPPI — гарантийный срок 24 месяца.
- GYSMI — гарантийный срок 12 месяцев.
- EWM — гарантийный срок 36 месяцев
- ESAB — гарантийный срок 24 месяца.
- Lincoln Electric — гарантийный срок от 24-х до 36-и месяцев в зависимости от модели сварочного аппарата.
- Fubag — 12 месяцев
- Aurora — гаантийный срок 24 месяцев
- Ресанта — 12 месяцев
- 3M — гарантийный срок 24 месяца.
- FoxWeld — гарантийный срок 12 месяцев.
- Trafimet — гарантийный срок 6 месяцев.
Студенческая весна
← НазадДаты проведения: 06 — 09 апреля 2021 г.
Место проведения: МГТУ им. Н.Э. Баумана, научно-учебный комплекс «Машиностроительные технологии» (НУК МТ)
Видеозапись открытия конференции 2021 года.
Всероссийская конференция является традиционным ежегодным научно-техническим мероприятием для студентов факультета «Машиностроительные технологии» МГТУ им. Н.Э.Баумана, на которое приглашаются студенты других Российских технических ВУЗов. Цель конференции – рассказать о самостоятельно выполненных научно-исследовательских проектах, приобрести навыки участия в подобных мероприятиях, обменяться идеями и опытом, соотнести уровень собственных разработок с работами других участников.
Конференция имеет конкурсный характер. В ходе работы экспертная комиссия определяет лучшие студенческие работы и распределяет призовые места. Итоги работы экспертная комиссия объявляет в заключительный день работы конференции.
Уважаемые участники!
Ждем Вас весной 2022 года на следующей, 16-й конференции!
Ключевые даты:
декабрь — подготовить работу;
февраль — подача заявки через форму на сайте;
первая декада марта — подача тезисов на электронный адрес конференции;
вторая декада марта — участники проверяют свои работы;
первая декада апреля — регистрация, открытие и основные заседания конференции;
первая декада апреля — вручение призов и закрытие конференции.
История и миссия конференции
Конференция «Студенческая научная весна: Машиностроительные технологии» — это праздник студентов нашего факультета и родственных кафедр других вузов, где можно поделиться с коллегами своими открытиями, идеями и конструкциями. Поделиться радостью от результатов самостоятельно выполненной работы. Выслушать доклады товарищей и зарядиться энтузиазмом, почувствовать вкус к труду ученого.
Конференция проходит с 2007 года и является продолжением традиции студенческих конференций, сложившейся за время работы университета. В 2007 работали подсекции только кафедры «Обработка металлов давлением» (МТ-6), а с 2008 года участвуют все кафедры факультета «Машиностроительные технологии» (МТ) МГТУ им. Н.Э.Баумана. Конференция всероссийская: за все годы проведения в ней приняли участие представители более 40 вузов и колледжей России и СНГ, сделано 2898 докладов. В 2021 году — 21 подсекция на 13 секциях, 239 докладов. За 15 лет истории подготовкой конференции занимались студенты факультета под руководством к. т.н., доц. МТ-6 Гладкова Ю.А., к.т.н., доц. МТ-4 Сырицкого А.Б, д.т.н., проф. МТ-4 Комшина А.С., к.т.н., доц. каф. МТ-6 Белокурова О.А. Последние годы переписку с участниками и сбор материалов конференции выполняли Панова Ирина Андреевна (выпускница каф. МТ6, ранее председатель СНТО им. Н.Е. Жуковского факультета МТ), Аникина Валерия Сергеевна (выпускница кафедры МТ-6), Токарева Анна Сергеевна (студентка кафедры МТ-6). В 2021 году сбор материалов выполнялся коллективом студентов — волонтеров: Медведева Елизавета Сергеевна (МТ-6), Мишечкина Ольга Владимировна (МТ-6), Дроздова Юлия Владимировна (МТ-4), Плаксина Екатерина Тимофеевна (МТ-4).
Сердцем конференции является постоянно действующий сайт – www.studvesna.ru. На нем собрана коллекция трудов за все годы работы. Каждый участник и руководитель может найти тезисы и статьи по своим выступлениям.
Адрес оргкомитета
105005, Россия, г. Москва, 2-ая Бауманская ул., д. 5, МГТУ им. Н.Э.Баумана, каф. МТ-4
Сайт конференции: http://studvesna.ru
Е-mail конференции: [email protected]
Е-mail оператора конференции, компании ООО «КванторФорм»: [email protected]
Российское общество по неразрушающему контролю и технической диагностике (РОНКТД) приглашает специалистов и компании НК и ТД принять участие в выставке и деловой программе XIV специализированной выставки с международным участием «Сварка. Контроль и диагностика». Выставка будет проходить 25-27 ноября 2014г. в Екатеринбурге (МВЦ «Екатеринбург-Экспо», Бульвар Экспо, 2). Выставка «Сварка. Контроль и диагностика» представляет новейшие сварочные технологии, оборудование и материалы, оборудование неразрушающего контроля и технической диагностики, энергосберегающую сварочную продукцию. В рамках выставки состоятся XIV международная научно-техническая конференция «Сварка и родственные технологии» и ХXVII Уральская конференция «Физические методы неразрушающего контроля (Янусовские чтения)». РОНКТД поддерживает форум и приглашает специалистов и компании НК и ТД принять участие в коллективном стенде партнеров РОНКТД на данной выставке. В рамках сотрудничества РОНКТД и организаторов выставки выставкой партнерам Общества предоставляется возможность принять участие в коллективном стенде партнеров РОНКТД на специальных условиях – со скидкой 40% на выставочную площадь. Основные разделы выставки по направлению СВАРКА: дуговая и контактная сварка, наплавка и газотермическое напыление, резка и пайка металлов, лазерная обработка, производство сварочных материалов, вспомогательное сварочное оборудование, автоматизация, механизация и роботизация сварочных процессов, механическая обработка сварных соединений, защита от вредных воздействий. Работа конференции «Физические методы неразрушающего контроля (Янусовские чтения)» пройдет по следующим разделам:
В форуме традиционно принимают участие компании из России, Украины, Беларуси, Германии, Франции, Италии и Китая. Выставку посещают представители строительной, нефтегазовой, машиностроительной, металлургической и других отраслей промышленности), среди них крупные делегации: Корпорация «Уралвагонзавод», «ВСМПО-АВИСМА», ФГУП «Производственное объединение «МАЯК», ОАО «Уралмашзавод», Машиностроительный завод им. В.В. Воровского, ОАО Машиностроительный завод имени М.И. Калинина, ЗАО «Энергомаш», ОАО «ГАЗПРОМНЕФТЬ-УРАЛ» и представители многих других. Скачать проект Форума Скачать схему выставки Контактная информация организаторов: сайт, тел.
С уважением, Дирекция РОНКТД тел. +7 (499) 245 56 56 факс +7 (499) 246 88 88 Данный адрес e-mail защищен от спам-ботов, Вам необходимо включить Javascript для его просмотра.
|
курсы центра «Контроль и диагностика» в Москве
«НУЦ «Контроль и диагностика» проводит обучение и квалификацию специалистов сварочного производства в соответствии с программами обучения Международного института сварки для следующих категорий персонала:
- Международный инженер по сварке
- Международный технолог по сварке
- Международный специалист по сварке
- Международный инспектор по сварке
- Международный сварщик
В Европе и мире есть ассоциации, имеющие общественно-профессиональный характер. Именно эти профессиональные неправительственные ассоциации разрабатывают политику и правила проведения обучения персонала и присвоения квалификации.
В настоящее время существуют две международные инженерные ассоциации, объединяющие мировую сварочную общественность. Это Международный институт сварки (МИС), основанный в 1948 г., в состав которого входят более 50 развитых стран мира, и Европейская федерация по сварке (EФС), основанная в 1971 г. и включающая 28 стран Европы.
В рамках МИСа и ЕФС создана во взаимодействии с ISO глобальная гармонизированная система обучения, квалификации и сертификации персонала сварочных производств, основанная на соблюдении требований стандартов серии ISO 9000, ISO 14000, ISO 3834/EN 729 и ISO 14731/EN 719 при производстве ответственных сварных конструкций и сертификации сварочных производств в части квалификации персонала.
Для внедрения и обеспечения деятельности в каждой стране член МИСа учреждает Уполномоченный национальный орган (ANB).
В России Российским научно-техническим сварочным обществом (РНТСО) был учрежден в 2001 г. и признан Международным институтом сварки Уполномоченный Национальный Орган по квалификации сварочного персонала — НОУДПО «Научно-учебный центр «Контроль и диагностика» — с правом выдачи дипломов международного образца, признаваемых во всех промышленно развитых странах мира.
Для обучения по программам Международного института сварки необходимо направить заявку в адрес «НУЦ «Контроль и диагностика»
Реестр владельцев международных дипломов.
Более детальную информацию можно получить у наших специалистов.
Центр экспертизы, диагностики и контроля
Одним из подразделений АО «Спецмашмонтаж» является Центр экспертизы, диагностики и контроля (ЦЭДК).
ЦЭДК является экспертной организацией, специализирующейся в области промышленной безопасности. Также ЦЭДК проводит обучение и аттестацию сварщиков.
Экспертиза промышленной безопасности
ЦЭДК осуществляет следующую деятельность по проведению экспертизы промышленной безопасности:
- проведение экспертизы проектной документации на разработку, строительство, расширение, реконструкцию, техническое перевооружение, консервацию и ликвидацию опасного производственного объекта
- проведение экспертизы технических устройств, применяемых на опасном производственном объекте (паровых и водогрейных котлов; трубопроводов пара и горячей воды III и IV категорий; сосудов работающих под давлением; грузоподъемных кранов, подъемников (вышек) всех видов; систем газоснабжения)
- проведение экспертизы иных документов, связанных с эксплуатацией опасных производственных объектов
Область аттестации ЦЭДК
ЦЭДК аттестован на проведение экспертизы промышленной безопасности для следующих объектов и оборудования подведомственных Ростехнадзору РФ.
Объекты котлонадзора:
- паровые и водогрейные котлы
- электрические котлы
- сосуды, работающие под давлением свыше 0,07 МПа
- трубопроводы пара и горячей воды с рабочим давлением пара более 0,07 МПа и температурой свыше 115°С
- барокамеры
Системы газоснабжения (газораспределения):
- наружные газопроводы стальные
- детали и узлы, газовое оборудование
- внутренние газопроводы стальные
Подъемные сооружения:
- грузоподъемные краны
- подъемники (вышки)
- лифты
- краны-трубоукладчики, краны-манипуляторы
- платформы подъемные для инвалидов
- крановые пути
Объекты горнорудной промышленности:
- здания и сооружения поверхностных комплексов рудников, обогатительных фабрик, фабрик окомкования и аглофабрик
- шахтные подъемные машины
- горно-транспортное и горнообогатительное оборудование
Объекты угольной промышленности:
- шахтные подъемные машины
- вентиляторы главного проветривания
- горно-транспортное и углеобогатительное оборудование
Оборудование нефтяной и газовой промышленности:
- оборудование для освоения, бурения, эксплуатации и ремонта скважин
- оборудование газонефтеперекачивающих станций
- газонефтепродуктопроводы
- резервуары для нефти и нефтепродуктов
Оборудование металлургической промышленности:
- металлоконструкции технических устройств, зданий и сооружений
- газопроводы технологических газов
- цапфы чугуновозов, стальковшей, металлоразливочных ковшей
Оборудование взрывопожароопасных и химически опасных производств:
- оборудование химических, нефтехимических и нефтеперерабатывающих производств
- резервуары для хранения взрывопожароопасных и токсичных веществ
- изотермические хранилища
- криогенное оборудование
- оборудование аммиачных холодильных установок
- печи, котлы ВОТ, энерготехнологические котлы, котлы-утилизаторы
- компрессорное и насосное оборудование
- центрифуги, сепараторы
- цистерны, контейнеры (бочки), баллоны для взрывопожароопасных и токсичных веществ
- технологические трубопроводы, трубопроводы пара и горячей воды
Здания и сооружения (строительные конструкции):
- металлические конструкции (в том числе стальные конструкции мостов)
Методы диагностики и контроля
ЦЭДК проводит диагностику и неразрушающий контроль надежности основных рабочих свойств и параметров объектов или отдельных его элементов различными методами при изготовлении, строительстве, монтаже, ремонте, реконструкции, эксплуатации и экспертном обследовании.
Виды (методы) неразрушающего контроля:
- визуальный и измерительный контроль
- ультразвуковой контроль
- радиационный контроль
- контроль проникающими веществами
- магнитный контроль
- оптико-эмиссионный контроль
- акустико-эмиссионный контроль
Неразрушающий контроль сварных соединений |
Радиационный контроль сварных соединений |
Центр оснащен современным диагностическим оборудованием для проведения неразрушающего контроля.
Средства визуально-измерительного контроля:
- видеоэндоскоп «Olympus»
- комплект для визуального и измерительного контроля ВИК
- универсальный шаблон сварщика УШС-3
- люксметр «ТКА-ПКМ»
- прибор портативный для измерения шероховатости поверхности TR100
- дальномер лазерный Leica DISTO D5
- нивелир оптический 4Н-3КЛ
- нивелир лазерный Leica Rugby 670
- теодолит оптический 4Т30П
- твердомер электронный малогабаритный переносной ТЭМП-2
Средства ультразвукового контроля:
- ультразвуковой дефектоскоп УД2-140
- ультразвуковой толщиномер А1207
- ультразвуковой толщиномер А1208
Средства радиационного контроля:
- рентгеновский аппарат МАРТ-250
- рентгеновский аппарат «Арина-02»
- рентгеновский аппарат «Арина-6»
- рентгеновский аппарат «МИРА-2Д»
- рентгеновский аппарат РАП 150/300
- рентгеновский аппарат ПИОН-2М
Средства магнитного метода контроля:
- магнитопорошковый дефектоскоп МД-6
- измеритель напряженности магнитного поля ИМАГ-400Ц
- измеритель концентрации напряжений ИКН-5М-32
- контрольный образец для магнитопорошковой дефектоскопии ст.
20
- контрольный образец для магнитопорошковой дефектоскопии сталь 15Х25Т
Средства оптико-эмиссионного метода контроля:
- спектрометр оптико-эмиссионный «PMI-Master»
Средства акустико-эмиссионного метода контроля:
- акустико-эмиссионная система «Малахит»
Вспомогательное оборудование:
- негатоскоп ОД-10Н
- негатоскоп ОД-11Н
- негатоскоп «Ранет»
- денситометр цифровой DD 5005-220
- газоанализатор непрерывного определения метана ГНОМ1
Оптико-эмиссионный спектрометр |
Рабочий инструмент инженера-дефектоскописта: ультразвуковые дефектоскопы, рентгеновский аппарат, твердомер и др. Приборы акустико-эмиссионного контроля и видеоэндоскоп «Olympus» |
Обучение и аттестация сварщиков
ЦЭДК занимается подготовкой высококвалифицированных сварщиков. ЦЭДК является аттестационным пунктом НАКСа, проводит обучение и аттестацию сварщиков 1-го уровня.
Центр оснащен сварочным оборудованием ведущих мировых производителей, позволяющим проводить обучение по следующим видам сварки: ручная дуговая сварка покрытыми электродами, ручная аргонодуговая сварка неплавящимся электродом, полуавтоматическая сварка в среде защитных газов, газовая сварка. В качестве материалов используются конструкционные, углеродистые, легированные, высоколегированные жаростойкие и коррозионно-стойкие стали, алюминий и его сплавы, цветные металлы.
Также в ЦЭДК отрабатываются режимы сварки металлоконструкций и трубопроводов, выполняется наладка сварочного оборудования.
В настоящее время в центре работает высококвалифицированный инженерно-технический персонал, который постоянно повышает свою квалификацию, изучает новые методы неразрушающего контроля и осваивает современное оборудование в специализированных учебных центрах.
Обучение сварщиков |
Перейти на страницу «Неразрушающий контроль» Механического завода «Спецмашмонтаж».
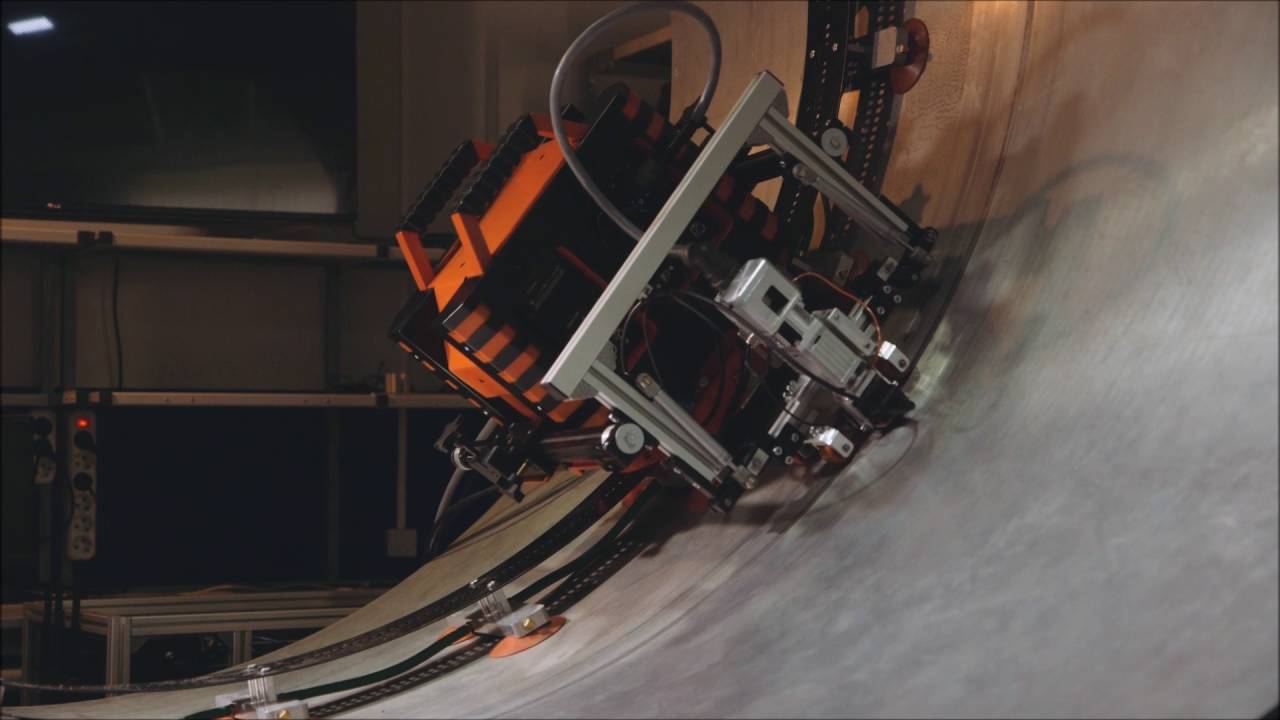
Диагностика орбитальной сварки и ремонт сварочной головки TIG
Ручная диагностика и ремонт сварочных аппаратов просты для ручных сварочных аппаратов. Это то, что часто делается полностью в цехе даже для относительно сложных установок, таких как аппараты для газо-вольфрамовой дуговой сварки (GTAW). То же самое нельзя сказать о сложных аппаратах для орбитальной сварки. Это гораздо более сложные системы, которые включают индивидуальные зубчатые передачи, небольшие сервоприводы и узкоспециализированные модули управления. Гораздо меньше проблем, которые средний оператор может диагностировать и исправить самостоятельно.
Многие части диагностики орбитальной сварки и ремонта сварочной головки вольфрамовым электродом в среде инертного газа (TIG) требуют междисциплинарных навыков, которые у большинства сварщиков просто не было возможности развить. Это вызывает беспокойство, потому что аппараты орбитальной сварки являются критически важной инфраструктурой, а вышедшая из строя машина может задерживать сроки на несколько недель, ожидая ремонта — либо отгрузки производителю, либо до прибытия представителя.
Орбитальные и ручные аппараты обладают некоторыми общими характеристиками, которые опытные сварщики могут диагностировать и ремонтировать самостоятельно.
При этом орбитальные и ручные машины имеют некоторые общие характеристики, которые опытные сварщики могут диагностировать и ремонтировать самостоятельно. Благодаря удаленной поддержке по телефону или другим устройствам в аппаратах орбитальной сварки есть много других неисправностей, которые можно легко диагностировать и устранить в мастерской.
Устранение неполадок аппарата для орбитальной сварки в полевых условиях Большинство неисправностей аппаратов для орбитальной сварки часто являются основными, видимыми проблемами, которые могут быть устранены оператором на месте без руководства.Утечки охлаждающей жидкости и газа — очевидные проблемы, которые относятся к этой сфере. Ремонт часто бывает так же прост, как затягивание соединения или замена шланга. Это просто, и это может сделать почти каждый.
Потенциально менее очевидными, но все же легко решаемыми проблемами являются силовые соединения. Когда дело доходит до проблем с синхронизацией в схемах сварки или напряжении дуги, наиболее вероятной причиной является не дефект или повреждение сварочной головки, а неплотное соединение где-то между сварочной головкой и источником питания.Проверка, чтобы убедиться, что все соединения надежно закреплены, должна быть первым шагом в контрольном листе технического обслуживания орбитальной сварки при попытке диагностировать проблему, наряду с включением его в повседневный 5-минутный контрольный список ежедневных проверок аппарата для дуговой сварки.
Другой аналогичный простой ремонт может быть не очевиден, но группа технической поддержки производителя должна быть в состоянии помочь вам в устранении неполадок. Дистанционная диагностика орбитальной сварки может помочь выявить эти проблемы и провести персонал на месте по этапам, необходимым для ремонта сварочной головки TIG или проверки источника питания, что в конечном итоге сэкономит всем затраты на простой оборудования.
Орбитальные сварочные аппараты — это сложные системы, сочетающие точную механику с компьютерными контроллерами. Существует изрядное количество простых шагов, которые можно пропустить или выполнить неправильно, что в конечном итоге может вызвать сообщения об ошибках или проблемы со сваркой. Ошибка калибровки перед сваркой является примером такого рода ремонта, который трудно диагностировать, но легко исправить.
Перед началом сварки головки для орбитальной орбитальной сварки должны найти исходное положение, с которым они сравнивают положение для всех частей сварочного параметра.Не путайте это с более тщательной ежегодной калибровкой, чтобы убедиться, что все части системы орбитальной сварки работают в пределах ожидаемых параметров. Если сварочная головка не может найти исходное положение, появится сообщение об ошибке; если он обнаружит неправильное исходное положение, это может отрицательно повлиять на качество сварки. Причина этих проблем может быть не очевидна для тех, кто не знаком с системами орбитальной сварки. Тем не менее, это простое решение, включающее настройку простого переключателя, который оператор может легко провести по телефону с производителем.
Службы удаленной диагностики могут определить простые и легко поддающиеся устранению услуги, не убирая аппараты орбитальной сварки с объекта.
Существуют и другие простые сообщения об ошибках или легко устранимые неисправности, которые на первый взгляд могут показаться сложными проблемами, требующими услуг производителя. Службы удаленной диагностики могут определять простые и легко поддающиеся ремонту услуги, не удаляя аппараты орбитальной сварки с объекта или не выводя их из строя на длительный период времени, что отрицательно сказывается на сроках.
Будущее удаленной диагностики и ремонта Возможности подключения в современном мире предлагают множество диагностических возможностей для производственного оборудования, например орбитальную сварку через Интернет вещей в сварке. Данные о процессе сварки, полученные с помощью взаимосвязанного оборудования для орбитальной сварки, можно использовать для точной и быстрой удаленной диагностики проблем со сварочным оборудованием. Их можно использовать для прогнозирования проблем до того, как у них появится возможность разработать методы профилактического обслуживания, обеспечивающие значительную экономию времени.
Однако, что более прозаично, эта сеть также предлагает легкий и быстрый доступ к подробным инженерным чертежам систем орбитальной сварки. Это позволяет сварщикам со средним опытом лучше анализировать и диагностировать проблемы при ремонте сварных швов TIG в полевых условиях, особенно под руководством человека с большим опытом. Это удаленное обслуживание может быть улучшено за счет использования других удаленных технологий, таких как дополненная реальность, когда опытный техник производителя может видеть то, что видит оператор станка, и может направлять его через настройку, диагностику и даже ремонт, если это необходимо.
Компания Arc Machines, Inc. была пионером в использовании многих технологий орбитальной сварки и продолжает оставаться лидером в области создания сетей данных по сварке, а также дистанционной диагностики и ремонта орбитальной сварки. По вопросам продукции обращайтесь по адресу [email protected] , а по вопросам обслуживания обращайтесь по адресу [email protected] . Чтобы разработать индивидуальное решение, свяжитесь с нами , чтобы организовать встречу.
Диагностика сварки посредством оптимизации скопления частиц и выбора функций
В предыдущем докладе был представлен подход к диагностике сварки, основанный на плазменной оптической спектроскопии. Он состоял из использования алгоритмов оптимизации и синтетических спектров для получения профилей участия видов, участвующих в плазме. Здесь обсуждается модификация модели: с одной стороны, алгоритм управляемого случайного поиска был заменен реализацией оптимизации роя частиц.С другой стороны, был включен этап выбора признаков для определения тех спектральных окон, в которых будет происходить процесс оптимизации. Будут показаны как экспериментальные, так и полевые испытания, чтобы проиллюстрировать производительность решения, которое улучшает результаты предыдущей работы.
1. Введение
Сварочные процессы играют важную роль в современной промышленности, поскольку они используются в широком спектре промышленных сценариев. Некоторые типичные примеры, которые следует упомянуть, — это изготовление тяжелых компонентов для атомных электростанций (например,g., парогенераторы), автомобили, двигатели для аэронавтики и трубки для различных энергетических применений или гражданского строительства. В некоторых из этих применений требования к качеству сварки очень жесткие: пористость, возникающая в процессе сварки трубы с трубной решеткой парогенератора, является хорошим примером в этом отношении.
Одной из основных проблем, с которыми сталкиваются инженеры на ранних этапах определения конкретной процедуры сварки, является сложность физических характеристик процесса [1, 2].Хотя были предприняты как теоретические, так и экспериментальные работы, опыт показывает, что определение оптимальных параметров для данного сценария требует выполнения предыдущих исследований в лаборатории, а затем проведения испытаний сварки купонов для проверки прогнозируемого поведения. Несмотря на все эти усилия, дефекты будут появляться в процессе, даже если все переменные будут тщательно контролироваться. Это подразумевает использование как разрушающих, так и неразрушающих методов оценки для исследования полученных швов и проверки их соответствия требуемым стандартам.
Для процессов лазерной и дуговой сварки были предложены различные подходы к мониторингу, основанные на использовании электрических [3–5], акустических [6, 7] и оптических датчиков [8, 9]. Также использовались промышленные камеры видимого диапазона, обычно с помощью фильтров и источников освещения [10, 11], и инфракрасная термография также использовалась как для онлайн, так и для офлайн-контроля [12, 13]. Среди всех этих альтернатив только первая была серьезно коммерциализирована, поскольку она позволяет установить надежное окно процесса.Однако некоторые дефекты, такие как обнаружение ложных материалов в стыке, невозможно обнаружить с помощью этого подхода. Помимо выбранной сенсорной технологии, большое внимание было уделено стратегиям обработки, предназначенным для обнаружения дефектов [14, 15] и классификации [16–18].
Оптическая спектроскопия плазмы также изучалась на предмет ее применения в диагностике сварки [19, 20], и в настоящее время она является одним из наиболее перспективных решений в этой области. Невосприимчивость оптического волокна к сильным электромагнитным помехам, возникающим во время процесса, надежность спектроскопических анализов различных частиц, обнаруживаемых в плазме, и возможность выявления паразитных материалов в сварочной ванне являются одними из наиболее важных факторов. преимущества.Типичным подходом при использовании спектроскопии плазмы в этом контексте было определение электронной температуры плазмы с помощью двух или более линий излучения одного и того же вида [19–22]. Однако у него есть свои ограничения, такие как неопределенность в идентификации линий излучения плазмы, что привело к исследованию других параметров мониторинга [23–25].
Недавно были предложены новые альтернативы анализа: например, Sibillano et al. [26] представили так называемую методику картирования ковариаций для анализа динамики плазмы при лазерной сварке, а Грослиер и др.[27] изучали применение анализа шага к сигналам напряжения и тока в процессе сварки внахлест (MIG-MAG). Другой метод основан на генерации синтетических спектров для согласования с реальными экспериментальными данными с помощью алгоритмов оптимизации [28]. Таким образом, полученные профили участия выбранных видов показали четкую корреляцию с событиями качества. Однако некоторые проблемы привели к пересмотру и усовершенствованию предыдущей модели. С одной стороны, ранее выбранный алгоритм оптимизации, CRS6 (Controlled Random Search-6), был заменен простой реализацией PSO (Оптимизация роя частиц) [29].С другой стороны, было примечательно, что профили Ar II продемонстрировали недостаточную чувствительность к некоторым дефектам в некоторых экспериментальных результатах, обсуждаемых в [28], что, как предполагалось, было связано с использованием относительных интенсивностей из NIST [30]. локальная база данных для генерации синтетических спектров. Для решения этой проблемы в модели был рассмотрен алгоритм выбора признаков, обеспечивающий выбор более узкого спектрального диапазона, в котором будет проводиться оптимизация.
2. Параметры спектроскопического контроля для онлайн-контроля сварки
Электронная температура плазмы 𝑇𝑒 — это спектроскопический параметр, обычно используемый в качестве параметра контроля в данной структуре.Хотя более точную оценку этой температуры можно получить с помощью графика Больцмана [31], это решение, которое подразумевает рассмотрение нескольких эмиссионных линий и дополнительного процесса регрессии, обычно заменяется упрощенным выражением [19]: 𝑇𝑒 = 𝐸𝑚 (2) −𝐸𝑚 (1) 𝐼𝑘ln (1) 𝐴 (2) 𝑔𝑚 / 𝐼 (2) 𝜆 (1) (2) 𝐴 (1) 𝑔𝑚, (1) 𝜆 (2) (1) где — энергия верхнего уровня, 𝑘 постоянная Больцмана, интенсивность линии излучения, вероятность перехода, 𝑔 статистический вес, и ngth длина волны, связанная с соответствующей линией излучения.Для частного случая дуговой сварки (1) меняется, включая в логарифме знаменателя частное между энергиями верхнего уровня линии излучения [32].
Появление дефектов связано с возникновением возмущений на профиле 𝑇𝑒, но, хотя корреляция между этим спектроскопическим параметром и качеством швов доказана [19–22], есть некоторые проблемы, такие как выбор эмиссионных линий для участия в оценке 𝑇𝑒, что привело к исследованию альтернативных подходов.
Анализ длины волны, связанной с максимальной интенсивностью излучения плазменного континуума [23], среднеквадратичным сигналом плазмы [25], а также методом от линии к континууму, используемым с алгоритмом выбора признаков [24], являются некоторыми решениями, которые были недавно исследованы. Совершенно другой подход был предложен в [28], где модель, основанная на определении так называемых профилей участия плазменных частиц, была построена путем генерации синтетических спектров, а затем с использованием алгоритмов оптимизации, чтобы попытаться согласовать реальные сварочные спектры .Синтетические спектры создаются после идентификации наиболее значимых видов, участвующих в процессе, и с использованием локальной копии базы данных со спектроскопической информацией о необходимых элементах. В этом процессе используются как центральные длины волн, так и относительные интенсивности, но последние порождают проблемы сходимости этапа оптимизации, если рассматривать широкий спектральный диапазон. Эта проблема была идентифицирована в [28], поскольку Ar II, преобладающий компонент в нашем сценарии в анализируемом диапазоне длин волн (195–535 нм), не показал ожидаемого ответа на некоторые дефекты, в то время как другие профили (Fe I, Mn I, Ar I) позволили правильно выявить дефекты.
Возможное решение этой проблемы заключается в определении более узких спектральных окон, в которых будет выполняться процесс оптимизации и, как следствие, генерация профилей участия. Очевидно, это приводит к неопределенности в выборе наиболее подходящих спектральных диапазонов с точки зрения обнаружения дефектов. Подобная проблема изучалась в [24], где алгоритм выбора признаков (SFFS) [33] использовался для определения тех эмиссионных линий, которые наиболее различаются с точки зрения обнаружения дефектов.Результаты показали высокую зависимость между выбранным спектральным диапазоном и соответствующим профилем мониторинга выходного сигнала. Помимо этой модификации, простая реализация алгоритма PSO (оптимизация роя частиц) будет использоваться вместо исходного CRS6, поскольку будет продемонстрировано, что первый демонстрирует улучшенную вычислительную производительность.
3. Модификации оригинальной модели
3.1. Алгоритм оптимизации: PSO
В исходной реализации (см. Рисунок 1) для выполнения этапа оптимизации использовался управляемый алгоритм случайного поиска, CRS6.Естественная эволюция модели заключается во включении лучшего алгоритма с точки зрения вычислительной производительности всего решения. В этой связи стоит упомянуть, что эта модель изначально не предназначена для использования в сценарии анализа в реальном времени, а предназначена для лучшего понимания динамики различных частиц в плазме и их поведения при появлении различных дефектов в процессе сварки. . Однако его можно использовать в качестве поддержки других спектроскопических подходов для онлайн-мониторинга (например,g., в технико-экономических обоснованиях), что оправдывает поиск более эффективных реализаций.
После некоторых начальных исследований PSO был выбран в качестве хорошего кандидата, учитывая его простоту и широкое распространение в нескольких сценариях. В области сварки некоторые авторы выбрали алгоритмы PSO для решения оптимизации ключевых параметров сварки [34] или для этапа обучения нейронных сетей [35]. PSO был первоначально предложен в 1995 году [29], и он вдохновлен социальным поведением стая птиц и стайкой рыб, претерпев много изменений с момента его первоначальной формулировки, с новыми версиями и приложениями.Помимо уже упомянутых, типичными областями применения PSO были анализ изображений и видео, проектирование антенн или выработка электроэнергии и системы, просто чтобы упомянуть некоторые примеры.
Исходный алгоритм PSO можно резюмировать следующим образом. (1) Инициализировать совокупность частиц со случайным положением и скоростями по измерениям D в пространстве поиска. (2) Оценить предопределенную функцию соответствия оптимизации для каждой частицы. (3) Сравните последнюю оценку пригодности текущей частицы с ее «предыдущим лучшим» 𝑝 лучшим.Если текущее значение лучше, то best будет обновлено, а 𝑝𝑖 (предыдущее наилучшее положение) будет обновлено до текущего местоположения 𝑥𝑖. (4) Определите частицу в рое с наибольшим успехом до сих пор (𝑔best) и назначьте ее местоположение на. (5) Приступайте к изменению скорости и положения каждой частицы в рое в соответствии со следующим выражением: 𝑣id (𝑡 + 1) = 𝑤𝑣id (𝑡) + 𝑐1𝑟1𝑝id (𝑡) −𝑥id (𝑡) + 𝑐2𝑟2𝑝gd (𝑡) −𝑥id, 𝑥 (𝑡) id (𝑡 + 1) = 𝑥id (𝑡) + 𝑣id (𝑡 + 1). (2) (6) Если условие остановки выполнено, то выйти с наилучшим на данный момент результатом; в противном случае повторите с пункта 2.Каждая частица внутри роя определяется своим положением 𝑋𝑖 и скоростью 𝑉𝑖 в 𝐷-мерном пространстве поиска, где 𝑋𝑖 = 𝑥𝑖1, 𝑥𝑖2,…, 𝑥𝑖𝐷𝑉, (3) 𝑖 = 𝑣𝑖1, 𝑣𝑖2,…, 𝑣𝑖𝐷. (4)
В (2) 𝑤 — инерционный вес, 𝑐1 и 𝑐2 — положительные постоянные , обычно определяемые как скорость обучения, а 𝑟1 и 𝑟2 — случайные функции в диапазоне [0,1]. Уравнение (2) описывает базовый алгоритм PSO, где значения параметров 𝑤, 𝑐1 и 𝑐2 могут существенно повлиять на поведение алгоритма [15], даже делая его нестабильным.Вес инерции можно интерпретировать как текучесть среды, в которой движутся частицы роя, и типичные значения могут быть между 0,4 и 0,9. Параметрам 𝑐1 и 𝑐2 обычно присваивается значение 2, хотя они могут иметь значительное влияние на результаты поиска. Кроме того, рекомендуется поддерживать скорости частиц в диапазоне [−𝑉max, + 𝑉max], но оптимальное значение 𝑉max зависит от конкретной анализируемой задачи. Альтернативой (2) является использование так называемого метода сужения [36]: 𝑣id𝑣 (𝑡 + 1) = 𝜒id (𝑡) + 𝑐1𝑟1𝑝id (𝑡) −𝑥id (𝑡) + 𝑐2𝑟2𝑝gd (𝑡) −𝑥id, 𝑥 (𝑡) id (𝑡 + 1) = 𝑥id (𝑡) + 𝑣id (𝑡 + 1), (5) где 2𝜒 = √𝜙 − 2 + 𝜙2−4𝜙, 𝜙 = 𝜙1 + 𝜙2> 4.(6)
Типичные значения этих параметров: 𝜙 = 4,1, 𝜙1 = 𝜙2 и 𝜒 = 0,7298. Хотя в этом нет необходимости, рекомендуется установить 𝑉max = 𝑋max.
После того, как решение, описанное в (5), было реализовано, были выполнены некоторые тесты для сравнения производительности PSO с результатами, предлагаемыми CRS6, которые суммированы в таблице 1, где Условие — это условие остановки 𝜀 алгоритма: || 𝑓 ∗ − 𝑓̂𝑥 ∗ || ≤𝜀, (7) где 𝑓 (𝑥) — функция, которую необходимо минимизировать, 𝑓 ∗ — минимум, 𝑥 ∗ — значение, которое необходимо найти в процессе оптимизации, а ̂𝑥 ∗ — приближение к 𝑥 ∗.
|