ΠΠ°ΠΊΠ°Π»ΠΊΠ° (ΡΠ΅ΡΠΌΠΎΠΎΠ±ΡΠ°Π±ΠΎΡΠΊΠ°) ΡΡΠ°Π»ΠΈ Π² ΠΠ°Π±Π΅ΡΠ΅ΠΆΠ½ΡΡ Π§Π΅Π»Π½Π°Ρ
ΠΠ°ΠΊΠ°Π»ΠΊΠ° β ΡΠ΅ΡΠΌΠΈΡΠ΅ΡΠΊΠ°Ρ ΠΎΠ±ΡΠ°Π±ΠΎΡΠΊΠ°, Π·Π°ΠΊΠ»ΡΡΠ°Π΅ΡΡΡ Π² Π½Π°Π³ΡΠ΅Π²Π°Π½ΠΈΠΈ ΡΡΠ°Π»ΠΈ Π΄ΠΎ ΡΠ΅ΠΌΠΏΠ΅ΡΠ°ΡΡΡΡ Π²ΡΡΠ΅ ΠΊΡΠΈΡΠΈΡΠ΅ΡΠΊΠΎΠΉ (ΠΡ3 β Π΄Π»Ρ Π΄ΠΎΡΠ²ΡΠ΅ΠΊΡΠΎΠΈΠ΄Π½ΠΎΠΉ ΠΈ ΠΡ1 β Π΄Π»Ρ Π·Π°ΡΠ²ΡΠ΅ΠΊΡΠΎΠΈΠ΄Π½ΠΎΠΉ ΡΡΠ°Π»Π΅ΠΉ) ΠΈΠ»ΠΈ ΡΠ΅ΠΌΠΏΠ΅ΡΠ°ΡΡΡΡ ΡΠ°ΡΡΠ²ΠΎΡΠ΅Π½ΠΈΡ ΠΈΠ·Π±ΡΡΠΎΡΠ½ΡΡ ΡΠ°Π·, Π²ΡΠ΄Π΅ΡΠΆΠΊΠ΅ ΠΈ ΠΏΠΎΡΠ»Π΅Π΄ΡΡΡΠ΅ΠΌ ΠΎΡ Π»Π°ΠΆΠ΄Π΅Π½ΠΈΠΈ ΡΠΎ ΡΠΊΠΎΡΠΎΡΡΡΡ, ΠΏΡΠ΅Π²ΡΡΠ°ΡΡΠ΅ΠΉ ΠΊΡΠΈΡΠΈΡΠ΅ΡΠΊΡΡ. ΠΠ°ΠΊΠ°Π»ΠΊΠ° ΡΡΠ°Π»ΠΈ Π½Π΅ ΡΠ²Π»ΡΠ΅ΡΡΡ ΠΎΠΊΠΎΠ½ΡΠ°ΡΠ΅Π»ΡΠ½ΠΎΠΉ ΠΎΠΏΠ΅ΡΠ°ΡΠΈΠ΅ΠΉ ΡΠ΅ΡΠΌΠΈΡΠ΅ΡΠΊΠΎΠΉ ΠΎΠ±ΡΠ°Π±ΠΎΡΠΊΠΈ. Π§ΡΠΎΠ±Ρ ΡΠΌΠ΅Π½ΡΡΠΈΡΡ Ρ ΡΡΠΏΠΊΠΎΡΡΡ ΠΈ Π½Π°ΠΏΡΡΠΆΠ΅Π½ΠΈΡ, Π²ΡΠ·Π²Π°Π½Π½ΡΠ΅ Π·Π°ΠΊΠ°Π»ΠΊΠΎΠΉ, ΠΈ ΠΏΠΎΠ»ΡΡΠΈΡΡ ΡΡΠ΅Π±ΡΠ΅ΠΌΡΠ΅ ΠΌΠ΅Ρ Π°Π½ΠΈΡΠ΅ΡΠΊΠΈΠ΅ ΡΠ²ΠΎΠΉΡΡΠ²Π°, ΡΡΠ°Π»Ρ ΠΏΠΎΡΠ»Π΅ Π·Π°ΠΊΠ°Π»ΠΊΠΈ ΠΎΠ±ΡΠ·Π°ΡΠ΅Π»ΡΠ½ΠΎ ΠΏΠΎΠ΄Π²Π΅ΡΠ³Π°ΡΡ ΠΎΡΠΏΡΡΠΊΡ.
ΠΠ°ΠΊΠΈΠ΅ ΠΌΠ΅ΡΠ°Π»Π»Ρ ΠΏΠΎΠ΄Π»Π΅ΠΆΠ°Ρ ΠΊΠ°Π»Π΅Π½ΠΈΡ
ΠΠ°ΠΊΠ°Π»ΠΊΠ° ΠΌΠ΅ΡΠ°Π»Π»Π° β ΡΡΠΎ ΡΠ΅ΡΠΌΠΈΡΠ΅ΡΠΊΠ°Ρ ΠΎΠ±ΡΠ°Π±ΠΎΡΠΊΠ°, ΠΊΠΎΡΠΎΡΠΎΠΉ ΡΠ°ΡΠ΅ Π²ΡΠ΅Π³ΠΎ ΠΏΠΎΠ΄Π²Π΅ΡΠ³Π°ΡΡΡΡ ΡΠ³Π»Π΅ΡΠΎΠ΄ΠΈΡΡΡΠ΅ ΠΈ Π»Π΅Π³ΠΈΡΠΎΠ²Π°Π½Π½ΡΠ΅ ΡΡΠ°Π»ΠΈ Ρ ΡΠ΅Π»ΡΡ ΠΏΠΎΠ²ΡΡΠ΅Π½ΠΈΡ ΠΈΡ
ΡΠ²Π΅ΡΠ΄ΠΎΡΡΠΈ ΠΈ ΡΠ»ΡΡΡΠ΅Π½ΠΈΡ ΠΏΡΠΎΡΠ½ΠΎΡΡΠ½ΡΡ
Ρ
Π°ΡΠ°ΠΊΡΠ΅ΡΠΈΡΡΠΈΠΊ. ΠΠ΅ΡΠΊΠΎΠ»ΡΠΊΠΎ ΡΠ΅ΠΆΠ΅ Π²ΡΡΡΠ΅ΡΠ°Π΅ΡΡΡ ΡΠ΅ΡΠΌΠΎΠΎΠ±ΡΠ°Π±ΠΎΡΠΊΠ° ΡΠ²Π΅ΡΠ½ΡΡ
ΠΌΠ΅ΡΠ°Π»Π»ΠΎΠ², Π² ΡΠ°ΡΡΠ½ΠΎΡΡΠΈ ΠΎΡΠΏΡΡΠΊ, ΠΎΡΠΆΠΈΠ³ ΠΈ Π·Π°ΠΊΠ°Π»ΠΊΠ° ΠΌΠ΅Π΄ΠΈ, Π»Π°ΡΡΠ½ΠΈ ΠΈ Π±ΡΠΎΠ½Π·Ρ, Π° ΡΠ°ΠΊΠΆΠ΅ ΡΠΏΠ»Π°Π²ΠΎΠ² Π°Π»ΡΠΌΠΈΠ½ΠΈΡ ΠΈ ΡΠΈΡΠ°Π½Π°. ΠΠ΅ΠΎΠ±Ρ
ΠΎΠ΄ΠΈΠΌΠΎ ΠΎΡΠΌΠ΅ΡΠΈΡΡ, ΡΡΠΎ Π·Π°ΠΊΠ°Π»ΠΈΠ²Π°Π½ΠΈΠ΅ ΡΡΠΈΡ
ΡΠΎΠ΅Π΄ΠΈΠ½Π΅Π½ΠΈΠΉ Π² ΠΎΡΠ»ΠΈΡΠΈΠ΅ ΠΎΡ ΡΠ³Π»Π΅ΡΠΎΠ΄ΠΈΡΡΡΡ
ΡΡΠ°Π»Π΅ΠΉ Π½Π΅ Π²ΡΠ΅Π³Π΄Π° ΠΏΡΠΈΠ²ΠΎΠ΄ΠΈΡ ΠΊ ΠΈΡ
ΡΠΏΡΠΎΡΠ½Π΅Π½ΠΈΡ, Π½Π΅ΠΊΠΎΡΠΎΡΡΠ΅ ΡΠΏΠ»Π°Π²Ρ ΠΌΠ΅Π΄ΠΈ ΠΏΠΎΡΠ»Π΅ ΡΡΠΎΠ³ΠΎ, Π½Π°ΠΎΠ±ΠΎΡΠΎΡ, ΡΡΠ°Π½ΠΎΠ²ΡΡΡΡ Π±ΠΎΠ»Π΅Π΅ ΠΏΠ»Π°ΡΡΠΈΡΠ½ΡΠΌΠΈ ΠΈ ΠΌΡΠ³ΠΊΠΈΠΌΠΈ. ΠΠΎΡΠ°Π·Π΄ΠΎ ΡΠ°ΡΠ΅ ΠΈΠ·Π΄Π΅Π»ΠΈΡ ΠΈΠ· ΡΠ²Π΅ΡΠ½ΡΡ
ΠΌΠ΅ΡΠ°Π»Π»ΠΎΠ² ΠΏΠΎΠ΄Π²Π΅ΡΠ³Π°ΡΡΡΡ ΠΎΡΠΏΡΡΠΊΡ Π΄Π»Ρ ΡΠ½ΡΡΠΈΡ Π½Π°ΠΏΡΡΠΆΠ΅Π½ΠΈΡ ΠΏΠΎΡΠ»Π΅ ΠΎΡΠ»ΠΈΠ²ΠΊΠΈ, ΡΡΠ°ΠΌΠΏΠΎΠ²ΠΊΠΈ, ΠΏΡΠΎΠΊΠ°ΡΠΊΠΈ ΠΈΠ»ΠΈ Π²ΠΎΠ»ΠΎΡΠ΅Π½ΠΈΡ.
Π‘Π²ΠΎΠΉΡΡΠ²Π° ΡΡΠ°Π»ΠΈ ΠΏΠΎΡΠ»Π΅ Π·Π°ΠΊΠ°Π»ΠΊΠΈ
Π£Π³Π»Π΅ΡΠΎΠ΄ΠΈΡΡΠ°Ρ ΡΡΠ°Π»Ρ Π² ΠΏΡΠΎΡΠ΅ΡΡΠ΅ Π½Π°Π³ΡΠ΅Π²Π° ΠΏΡΠΎΡ
ΠΎΠ΄ΠΈΡ ΡΠ΅ΡΠ΅Π· ΡΡΠ΄ ΡΠ°Π·ΠΎΠ²ΡΡ
ΠΈΠ·ΠΌΠ΅Π½Π΅Π½ΠΈΠΉ ΡΠ²ΠΎΠ΅ΠΉ ΡΡΡΡΠΊΡΡΡΡ, ΠΏΡΠΈ ΠΊΠΎΡΠΎΡΡΡ
ΠΌΠ΅Π½ΡΠ΅ΡΡΡ Π΅Π΅ ΡΠΎΡΡΠ°Π², Π° ΡΠ°ΠΊΠΆΠ΅ ΡΠΎΡΠΌΠ° ΠΈ ΡΠ»Π΅ΠΌΠ΅Π½ΡΠΎΠ² ΠΊΡΠΈΡΡΠ°Π»Π»ΠΈΡΠ΅ΡΠΊΠΎΠΉ ΡΠ΅ΡΠ΅ΡΠΊΠΈ. ΠΡΠΈ ΠΊΡΠΈΡΠΈΡΠ΅ΡΠΊΠΎΠΉ ΡΠ΅ΠΌΠΏΠ΅ΡΠ°ΡΡΡΠ΅ 723 Β°C Π² Π΅ΡΠ΅ ΡΠ²Π΅ΡΠ΄ΠΎΠΌ ΠΌΠ΅ΡΠ°Π»Π»Π΅ Π½Π°ΡΠΈΠ½Π°Π΅ΡΡΡ ΡΠ°ΡΠΏΠ°Π΄ ΡΠ΅ΠΌΠ΅Π½ΡΠΈΡΠ° (ΠΊΠ°ΡΠ±ΠΈΠ΄Π° ΠΆΠ΅Π»Π΅Π·Π°) ΠΈ ΡΠΎΡΠΌΠΈΡΠΎΠ²Π°Π½ΠΈΠ΅ ΡΠ°Π²Π½ΠΎΠΌΠ΅ΡΠ½ΠΎΠ³ΠΎ ΡΠ°ΡΡΠ²ΠΎΡΠ° ΡΠ³Π»Π΅ΡΠΎΠ΄Π° Π² ΠΆΠ΅Π»Π΅Π·Π΅, ΠΊΠΎΡΠΎΡΡΠΉ Π½Π°Π·ΡΠ²Π°Π΅ΡΡΡ Π°ΡΡΡΠ΅Π½ΠΈΡ. ΠΡΠΎ ΡΠΎΡΡΠΎΡΠ½ΠΈΠ΅ ΡΠ³Π»Π΅ΡΠΎΠ΄ΠΈΡΡΠΎΠΉ ΡΡΠ°Π»ΠΈ ΡΠ²Π»ΡΠ΅ΡΡΡ ΠΈΡΡ
ΠΎΠ΄Π½ΡΠΌ Π΄Π»Ρ Π·Π°ΠΊΠ°Π»ΠΊΠΈ. ΠΡΠΈ ΠΌΠ΅Π΄Π»Π΅Π½Π½ΠΎΠΌ ΠΎΡ
Π»Π°ΠΆΠ΄Π΅Π½ΠΈΠΈ Π°ΡΡΡΠ΅Π½ΠΈΡ ΡΠ°ΡΠΏΠ°Π΄Π°Π΅ΡΡΡ, ΠΈ ΠΌΠ΅ΡΠ°Π»Π» Π²ΠΎΠ·Π²ΡΠ°ΡΠ°Π΅ΡΡΡ Π² ΠΈΡΡ
ΠΎΠ΄Π½ΠΎΠ΅ ΡΠΎΡΡΠΎΡΠ½ΠΈΠ΅. ΠΡΠ»ΠΈ ΠΆΠ΅ ΡΡΠ°Π»Ρ ΠΎΡ
Π»Π°ΠΆΠ΄Π°ΡΡ Π±ΡΡΡΡΠΎ, ΡΠΎ Π°ΡΡΡΠ΅Π½ΠΈΡ Π½Π΅ ΡΡΠΏΠ΅Π²Π°Π΅Ρ ΠΈΠ·ΠΌΠ΅Π½ΡΡΡΡΡ, ΠΈ ΠΏΡΠΈ ΠΎΠΏΡΠ΅Π΄Π΅Π»Π΅Π½Π½ΠΎΠΉ ΡΠΊΠΎΡΠΎΡΡΠΈ ΠΎΡ
Π»Π°ΠΆΠ΄Π΅Π½ΠΈΡ ΠΈ ΠΏΠΎΡΠΎΠ³ΠΎΠ²ΡΡ
ΡΠ΅ΠΌΠΏΠ΅ΡΠ°ΡΡΡΠ°Ρ
ΡΠΎΡΠΌΠΈΡΡΡΡΡΡ ΠΊΡΠΈΡΡΠ°Π»Π»ΠΈΡΠ΅ΡΠΊΠΈΠ΅ ΡΠ΅ΡΠ΅ΡΠΊΠΈ ΠΈ Ρ
ΠΈΠΌΠΈΡΠ΅ΡΠΊΠΈΠ΅ ΡΠΎΡΡΠ°Π²Ρ, ΠΏΡΠΈΠ΄Π°ΡΡΠΈΠ΅ Π΅ΠΉ ΡΠ°Π·Π»ΠΈΡΠ½ΡΠ΅ ΡΠΊΡΠΏΠ»ΡΠ°ΡΠ°ΡΠΈΠΎΠ½Π½ΡΠ΅ ΡΠ²ΠΎΠΉΡΡΠ²Π°.
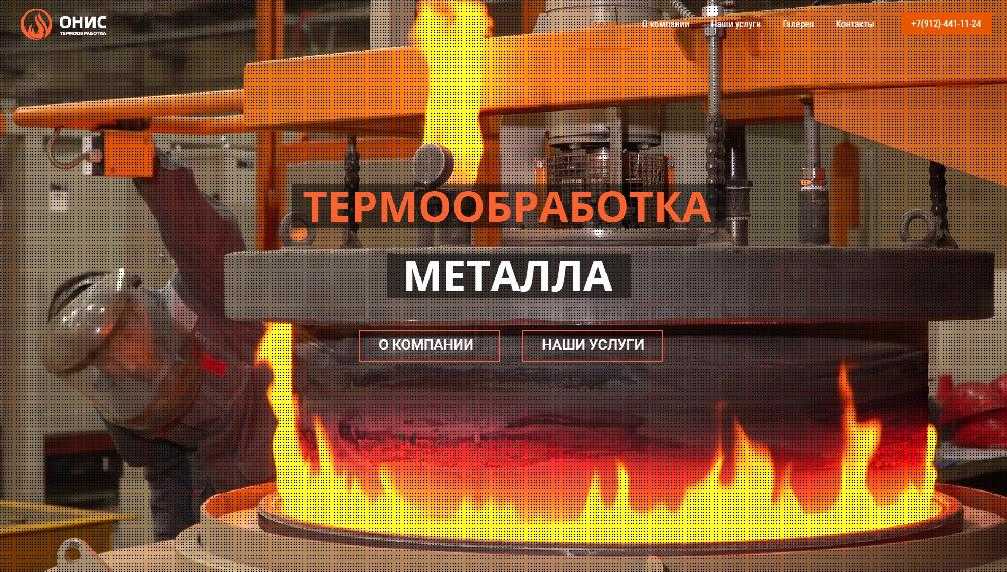
ΠΠ°ΠΊΠ°Π·Π°ΡΡ Π·Π²ΠΎΠ½ΠΎΠΊ
ΠΡΠΆΠ½Π° Π·Π°ΠΊΠ°Π»ΠΊΠ° ΡΡΠ°Π»ΠΈ Π² ΠΠ°Π±Π΅ΡΠ΅ΠΆΠ½ΡΡ
Π§Π΅Π»Π½Π°Ρ
? ΠΠ°ΠΊΠ°ΠΆΠΈΡΠ΅ Π·Π²ΠΎΠ½ΠΎΠΊ ΠΈ ΠΌΡ ΠΎΠ±ΡΡΠ΄ΠΈΠΌ Ρ ΠΠ°ΠΌΠΈ Π²ΡΠ΅ Π½ΡΠ°Π½ΡΡ ΠΏΡΠ΅Π΄ΡΡΠΎΡΡΠ΅ΠΉ ΡΠ°Π±ΠΎΡΡ!
ΠΡ ΠΏΠ΅ΡΠ΅Π·Π²ΠΎΠ½ΠΈΠΌ ΠΠ°ΠΌ Π² ΡΠ°Π±ΠΎΡΠ΅Π΅ Π²ΡΠ΅ΠΌΡ.
ΠΠΌΡ
Π’Π΅Π»Π΅ΡΠΎΠ½
ΠΠ°ΠΆΠΈΠΌΠ°Ρ ΠΊΠ½ΠΎΠΏΠΊΡ, ΠΡ Π΄Π°Π΅ΡΠ΅ ΡΠΎΠ³Π»Π°ΡΠΈΠ΅ Π½Π° ΠΎΠ±ΡΠ°Π±ΠΎΡΠΊΡ ΠΏΠ΅ΡΡΠΎΠ½Π°Π»ΡΠ½ΡΡ Π΄Π°Π½Π½ΡΡ Π² ΡΠΎΠΎΡΠ²Π΅ΡΡΡΠ²ΠΈΠΈ Ρ ΡΡΠ»ΠΎΠ²ΠΈΡΠΌΠΈ,ΡΠΊΠ°Π·Π°Π½Π½ΡΠΌΠΈ ΠΏΠΎ ΡΡΡΠ»ΠΊΠ΅
ΠΠ»Π°ΡΡΠΈΡΠΈΠΊΠ°ΡΠΈΡ ΠΊΠ°Π»Π΅Π½ΠΈΡ ΡΡΠ°Π»ΠΈ
ΠΠΈΠ΄Ρ Π·Π°ΠΊΠ°Π»ΠΊΠΈ ΡΡΠ°Π»Π΅ΠΉ ΠΊΠ»Π°ΡΡΠΈΡΠΈΡΠΈΡΡΡΡ ΠΏΠΎ ΡΠΈΠΏΡ ΠΈΡΡΠΎΡΠ½ΠΈΠΊΠ° Π½Π°Π³ΡΠ΅Π²Π° ΠΈ ΡΠΏΠΎΡΠΎΠ±Ρ ΠΎΡ
Π»Π°ΠΆΠ΄Π΅Π½ΠΈΡ ΠΌΠ΅ΡΠ°Π»Π»Π°. ΠΡΠ½ΠΎΠ²Π½ΡΠΌ ΠΎΠ±ΠΎΡΡΠ΄ΠΎΠ²Π°Π½ΠΈΠ΅ΠΌ Π΄Π»Ρ Π½Π°Π³ΡΠ΅Π²Π° Π΄Π΅ΡΠ°Π»Π΅ΠΉ ΠΏΠ΅ΡΠ΅Π΄ Π·Π°ΠΊΠ°Π»ΠΈΠ²Π°Π½ΠΈΠ΅ΠΌ ΠΏΠΎ-ΠΏΡΠ΅ΠΆΠ½Π΅ΠΌΡ ΡΠ²Π»ΡΡΡΡΡ ΠΌΡΡΠ΅Π»ΡΠ½ΡΠ΅ ΠΏΠ΅ΡΠΈ, Π² ΠΊΠΎΡΠΎΡΡΡ
ΠΌΠΎΠΆΠ½ΠΎ ΡΠ°Π²Π½ΠΎΠΌΠ΅ΡΠ½ΠΎ ΡΠ°Π·ΠΎΠ³ΡΠ΅Π²Π°ΡΡ ΠΌΠ΅ΡΠ°Π»Π»ΠΈΡΠ΅ΡΠΊΠΈΠ΅ ΠΈΠ·Π΄Π΅Π»ΠΈΡ Π»ΡΠ±ΡΡ
ΡΠ°Π·ΠΌΠ΅ΡΠΎΠ². ΠΡΡΠΎΠΊΡΡ ΡΠΊΠΎΡΠΎΡΡΡ Π½Π°Π³ΡΠ΅Π²Π° ΠΏΡΠΈ ΠΏΠΎΡΠΎΡΠ½ΠΎΠΉ ΠΎΠ±ΡΠ°Π±ΠΎΡΠΊΠ΅ ΠΈΠ·Π΄Π΅Π»ΠΈΠΉ ΠΎΠ±Π΅ΡΠΏΠ΅ΡΠΈΠ²Π°Π΅Ρ Π·Π°ΠΊΠ°Π»ΠΊΠ° Ρ ΠΏΡΠΈΠΌΠ΅Π½Π΅Π½ΠΈΠ΅ΠΌ ΡΠΎΠΊΠΎΠ² Π²ΡΡΠΎΠΊΠΎΠΉ ΡΠ°ΡΡΠΎΡΡ (ΠΈΠ½Π΄ΡΠΊΡΠΈΠΎΠ½Π½Π°Ρ Π·Π°ΠΊΠ°Π»ΠΊΠ° ΡΡΠ°Π»Π΅ΠΉ) (ΡΠΌ. ΡΠΎΡΠΎ Π½ΠΈΠΆΠ΅). ΠΠ»Ρ Π·Π°ΠΊΠ°Π»ΠΈΠ²Π°Π½ΠΈΡ Π²Π΅ΡΡ
Π½ΠΈΡ
ΡΠ»ΠΎΠ΅Π² ΡΡΠ°Π»ΡΠ½ΡΡ
ΠΈΠ·Π΄Π΅Π»ΠΈΠΉ ΠΏΡΠΈΠΌΠ΅Π½ΡΡΡ Π΄ΠΎΠ²ΠΎΠ»ΡΠ½ΠΎ Π½Π΅Π΄ΠΎΡΠΎΠ³ΡΡ ΠΈ ΡΡΡΠ΅ΠΊΡΠΈΠ²Π½ΡΡ Π³Π°Π·ΠΎΠΏΠ»Π°ΠΌΠ΅Π½Π½ΡΡ Π·Π°ΠΊΠ°Π»ΠΊΡ, Π³Π»Π°Π²Π½ΡΠΉ Π½Π΅Π΄ΠΎΡΡΠ°ΡΠΎΠΊ ΠΊΠΎΡΠΎΡΠΎΠΉ β Π½Π΅Π²ΠΎΠ·ΠΌΠΎΠΆΠ½ΠΎΡΡΡ ΡΠΎΡΠ½ΠΎ Π·Π°Π΄Π°ΡΡ Π³Π»ΡΠ±ΠΈΠ½Ρ ΠΏΡΠΎΠ³ΡΠ΅Π²Π°. ΠΡΠΈΡ
Π½Π΅Π΄ΠΎΡΡΠ°ΡΠΊΠΎΠ² Π»ΠΈΡΠ΅Π½Π° Π»Π°Π·Π΅ΡΠ½Π°Ρ Π·Π°ΠΊΠ°Π»ΠΊΠ°, Π½ΠΎ Π΅Π΅ Π²ΠΎΠ·ΠΌΠΎΠΆΠ½ΠΎΡΡΠΈ ΠΎΠ³ΡΠ°Π½ΠΈΡΠ΅Π½Ρ Π½Π΅Π±ΠΎΠ»ΡΡΠΎΠΉ ΠΌΠΎΡΠ½ΠΎΡΡΡΡ ΠΈΡΡΠΎΡΠ½ΠΈΠΊΠ° ΠΈΠ·Π»ΡΡΠ΅Π½ΠΈΡ.
ΠΠ°ΠΊΠ°Π»ΠΈΠ²Π°Π½ΠΈΠ΅ Π² ΠΎΠ΄Π½ΠΎΠΉ ΡΡΠ΅Π΄Π΅
ΠΡΠΈ ΡΠ°ΠΊΠΎΠΌ ΡΠΏΠΎΡΠΎΠ±Π΅ Π·Π°ΠΊΠ°Π»ΠΊΠΈ Π½Π°Π³ΡΠ΅ΡΠΎΠ΅ Π΄ΠΎ Π·Π°Π΄Π°Π½Π½ΠΎΠΉ ΡΠ΅ΠΌΠΏΠ΅ΡΠ°ΡΡΡΡ ΠΈΠ·Π΄Π΅Π»ΠΈΠ΅ ΠΈΠ· ΡΡΠ°Π»ΠΈ ΠΏΠΎΠΌΠ΅ΡΠ°ΡΡ Π² ΠΆΠΈΠ΄ΠΊΠΎΡΡΡ, Π³Π΄Π΅ ΠΎΠ½Π° ΠΎΡΡΠ°Π΅ΡΡΡ Π΄ΠΎ ΠΏΠΎΠ»Π½ΠΎΠ³ΠΎ ΠΎΡΡΡΠ²Π°Π½ΠΈΡ. Π ΠΊΠ°ΡΠ΅ΡΡΠ²Π΅ Π·Π°ΠΊΠ°Π»ΠΎΡΠ½ΠΎΠΉ ΡΡΠ΅Π΄Ρ Π΄Π»Ρ ΡΠ³Π»Π΅ΡΠΎΠ΄ΠΈΡΡΡΡ ΡΡΠ°Π»Π΅ΠΉ ΠΈΡΠΏΠΎΠ»ΡΠ·ΡΡΡ Π²ΠΎΠ΄Ρ, Π° Π΄Π»Ρ Π»Π΅Π³ΠΈΡΠΎΠ²Π°Π½Π½ΡΡ β ΠΌΠΈΠ½Π΅ΡΠ°Π»ΡΠ½ΠΎΠ΅ ΠΌΠ°ΡΠ»ΠΎ. ΠΠ΅Π΄ΠΎΡΡΠ°ΡΠΎΠΊ ΡΡΠΎΠ³ΠΎ ΠΌΠ΅ΡΠΎΠ΄Π° Π·Π°ΠΊΠ»ΡΡΠ°Π΅ΡΡΡ Π² ΡΠΎΠΌ, ΡΡΠΎ ΠΏΠΎΡΠ»Π΅ ΡΠ°ΠΊΠΎΠ³ΠΎ Π·Π°ΠΊΠ°Π»ΠΈΠ²Π°Π½ΠΈΡ Π² ΠΌΠ΅ΡΠ°Π»Π»Π΅ ΡΠΎΡ ΡΠ°Π½ΡΡΡΡΡ Π·Π½Π°ΡΠΈΡΠ΅Π»ΡΠ½ΡΠ΅ Π½Π°ΠΏΡΡΠΆΠ΅Π½ΠΈΡ, ΠΏΠΎΡΡΠΎΠΌΡ Π² ΡΡΠ΄Π΅ ΡΠ»ΡΡΠ°Π΅Π² ΠΌΠΎΠΆΠ΅Ρ ΠΏΠΎΡΡΠ΅Π±ΠΎΠ²Π°ΡΡΡΡ Π΄ΠΎΠΏΠΎΠ»Π½ΠΈΡΠ΅Π»ΡΠ½Π°Ρ ΡΠ΅ΡΠΌΠΎΠΎΠ±ΡΠ°Π±ΠΎΡΠΊΠ° (ΠΎΡΠΏΡΡΠΊ).
Π‘ΡΡΠΏΠ΅Π½ΡΠ°ΡΠ°Ρ Π·Π°ΠΊΠ°Π»ΠΊΠ°

ΠΠ·ΠΎΡΠ΅ΡΠΌΠΈΡΠ΅ΡΠΊΠ°Ρ Π·Π°ΠΊΠ°Π»ΠΊΠ°
ΠΡΠΈ ΠΈΠ·ΠΎΡΠ΅ΡΠΌΠΈΡΠ΅ΡΠΊΠΎΠΌ Π·Π°ΠΊΠ°Π»ΠΈΠ²Π°Π½ΠΈΠΈ ΠΈΠ·Π΄Π΅Π»ΠΈΠ΅ ΡΠ°ΠΊΠΆΠ΅ Π²ΡΠ΄Π΅ΡΠΆΠΈΠ²Π°Π΅ΡΡΡ Π² Π·Π°ΠΊΠ°Π»ΠΎΡΠ½ΠΎΠΉ Π²Π°Π½Π½Π΅ ΠΏΡΠΈ ΡΠ΅ΠΌΠΏΠ΅ΡΠ°ΡΡΡΠ΅, ΠΏΡΠ΅Π²ΡΡΠ°ΡΡΠ΅ΠΉ ΡΠΎΡΠΊΡ ΠΌΠ°ΡΡΠ΅Π½ΡΠΈΡΠ°, Π½ΠΎ Π½Π΅ΡΠΊΠΎΠ»ΡΠΊΠΎ Π΄ΠΎΠ»ΡΡΠ΅. Π ΡΠ΅Π·ΡΠ»ΡΡΠ°ΡΠ΅ ΡΡΠΎΠ³ΠΎ Π°ΡΡΡΠ΅Π½ΠΈΡ ΡΡΠ°Π½ΡΡΠΎΡΠΌΠΈΡΡΠ΅ΡΡΡ Π² Π±Π΅ΠΉΠ½ΠΈΡ β ΠΎΠ΄Π½Ρ ΠΈΠ· ΡΠ°Π·Π½ΠΎΠ²ΠΈΠ΄Π½ΠΎΡΡΠ΅ΠΉ ΡΡΠΎΠΎΡΡΠΈΡΠ°. Π’Π°ΠΊΠ°Ρ ΡΡΠ°Π»Ρ ΡΠΎΡΠ΅ΡΠ°Π΅Ρ Π² ΡΠ΅Π±Π΅ ΠΏΠΎΠ²ΡΡΠ΅Π½Π½ΡΡ ΠΏΡΠΎΡΠ½ΠΎΡΡΡ Ρ ΠΏΠ»Π°ΡΡΠΈΡΠ½ΠΎΡΡΡΡ ΠΈ Π²ΡΠ·ΠΊΠΎΡΡΡΡ. ΠΡΠΎΠΌΠ΅ ΡΠΎΠ³ΠΎ, ΠΏΠΎΡΠ»Π΅ ΠΈΠ·ΠΎΡΠ΅ΡΠΌΠΈΡΠ΅ΡΠΊΠΎΠΉ Π·Π°ΠΊΠ°Π»ΠΊΠΈ Π² ΠΈΠ·Π΄Π΅Π»ΠΈΠΈ ΡΠ½ΠΈΠΆΠ°ΡΡΡΡ ΠΎΡΡΠ°ΡΠΎΡΠ½ΡΠ΅ Π½Π°ΠΏΡΡΠΆΠ΅Π½ΠΈΡ.
ΠΠ°ΠΊΠ°Π»ΠΊΠ° Ρ ΡΠ°ΠΌΠΎΠΎΡΠΏΡΡΠΊΠΎΠΌ
ΠΡΠΎΡ Π²ΠΈΠ΄ ΡΠ΅ΡΠΌΠΎΠΎΠ±ΡΠ°Π±ΠΎΡΠΊΠΈ ΠΈΡΠΏΠΎΠ»ΡΠ·ΡΠ΅ΡΡΡ Π΄Π»Ρ Π·Π°ΠΊΠ°Π»ΠΈΠ²Π°Π½ΠΈΡ ΡΠ΄Π°ΡΠ½ΠΎΠ³ΠΎ ΠΈΠ½ΡΡΡΡΠΌΠ΅Π½ΡΠ°, ΠΊΠΎΡΠΎΡΡΠΉ Π΄ΠΎΠ»ΠΆΠ΅Π½ ΠΎΠ±Π»Π°Π΄Π°ΡΡ ΡΠ²Π΅ΡΠ΄ΡΠΌ ΠΏΠΎΠ²Π΅ΡΡ
Π½ΠΎΡΡΠ½ΡΠΌ ΡΠ»ΠΎΠ΅ΠΌ ΠΈ Π²ΡΠ·ΠΊΠΎΠΉ ΡΠ΅ΡΠ΅Π΄ΠΈΠ½ΠΎΠΉ. ΠΠ³ΠΎ ΠΎΡΠΎΠ±Π΅Π½Π½ΠΎΡΡΡ Π·Π°ΠΊΠ»ΡΡΠ°Π΅ΡΡΡ Π² ΡΠΎΠΌ, ΡΡΠΎ ΠΈΠ·Π΄Π΅Π»ΠΈΠ΅ ΠΈΠ·Π²Π»Π΅ΠΊΠ°Π΅ΡΡΡ ΠΈΠ· Π·Π°ΠΊΠ°Π»ΠΎΡΠ½ΠΎΠΉ Π΅ΠΌΠΊΠΎΡΡΠΈ ΠΏΡΠΈ Π½Π΅ΠΏΠΎΠ»Π½ΠΎΠΌ ΠΎΡ
Π»Π°ΠΆΠ΄Π΅Π½ΠΈΠΈ. Π ΡΡΠΎΠΌ ΡΠ»ΡΡΠ°Π΅ Π΅Π³ΠΎ Π²Π½ΡΡΡΠ΅Π½Π½ΡΡ ΡΠ°ΡΡΡ Π΅ΡΠ΅ ΡΠΎΠ΄Π΅ΡΠΆΠΈΡ Π΄ΠΎΡΡΠ°ΡΠΎΡΠ½ΠΎΠ΅ ΠΊΠΎΠ»ΠΈΡΠ΅ΡΡΠ²ΠΎ ΡΠ΅ΠΏΠ»Π°, ΡΡΠΎΠ±Ρ ΠΏΡΠΎΠ³ΡΠ΅ΡΡ Π²Π΅ΡΡ ΠΎΠ±ΡΠ΅ΠΌ ΠΌΠ΅ΡΠ°Π»Π»Π° Π΄ΠΎ ΡΠ΅ΠΌΠΏΠ΅ΡΠ°ΡΡΡΡ ΠΎΡΠΏΡΡΠΊΠ°. Π’Π°ΠΊ ΠΊΠ°ΠΊ ΠΏΠΎΠ²ΡΠΎΡΠ½ΡΠΉ Π½Π°Π³ΡΠ΅Π² ΠΈΠ·Π΄Π΅Π»ΠΈΡ ΠΎΡΡΡΠ΅ΡΡΠ²Π»ΡΠ΅ΡΡΡ Π±Π΅Π· Π²Π½Π΅ΡΠ½Π΅Π³ΠΎ Π²ΠΎΠ·Π΄Π΅ΠΉΡΡΠ²ΠΈΡ Π·Π° ΡΡΠ΅Ρ Π²Π½ΡΡΡΠ΅Π½Π½Π΅ΠΉ ΡΠ΅ΠΏΠ»ΠΎΠ²ΠΎΠΉ ΡΠ½Π΅ΡΠ³ΠΈΠΈ, ΡΠ°ΠΊΠΎΠΉ Π²ΠΈΠ΄ ΡΠ΅ΡΠΌΠΈΡΠ΅ΡΠΊΠΎΠΉ ΠΎΠ±ΡΠ°Π±ΠΎΡΠΊΠΈ Π½Π°Π·ΡΠ²Π°ΡΡ Π·Π°ΠΊΠ°Π»ΠΊΠΎΠΉ Ρ ΡΠ°ΠΌΠΎΠΎΡΠΏΡΡΠΊΠΎΠΌ.
Π‘Π²Π΅ΡΠ»Π°Ρ Π·Π°ΠΊΠ°Π»ΠΊΠ°
Π‘Π²Π΅ΡΠ»Π°Ρ Π·Π°ΠΊΠ°Π»ΠΊΠ° ΠΏΡΠΈΠΌΠ΅Π½ΡΠ΅ΡΡΡ Π΄Π»Ρ ΡΡΠ°Π»ΡΠ½ΡΡ ΠΈΠ·Π΄Π΅Π»ΠΈΠΉ, ΠΏΠΎΠ²Π΅ΡΡ Π½ΠΎΡΡΠΈ ΠΊΠΎΡΠΎΡΡΡ ΠΏΡΠΈ ΡΠ΅ΡΠΌΠΎΠΎΠ±ΡΠ°Π±ΠΎΡΠΊΠ΅ Π½Π΅ Π΄ΠΎΠ»ΠΆΠ½Ρ ΠΏΠΎΠ΄Π²Π΅ΡΠ³Π°ΡΡΡΡ ΠΎΠΊΠΈΡΠ»Π΅Π½ΠΈΡ. ΠΡΠΈ ΡΠ°ΠΊΠΎΠΉ ΡΠ΅ΡΠΌΠΎΠΎΠ±ΡΠ°Π±ΠΎΡΠΊΠ΅ ΡΡΠ°Π»Ρ Π½Π°Π³ΡΠ΅Π²Π°Π΅ΡΡΡ Π² Π²Π°ΠΊΡΡΠΌΠ½ΡΡ ΠΏΠ΅ΡΠ°Ρ (ΡΠΌ. ΡΠΎΡΠΎ Π½ΠΈΠΆΠ΅) ΠΈΠ»ΠΈ Π² ΠΈΠ½Π΅ΡΡΠ½ΡΡ Π³Π°Π·ΠΎΠ²ΡΡ ΡΡΠ΅Π΄Π°Ρ (Π°Π·ΠΎΡ, Π°ΡΠ³ΠΎΠ½ ΠΈ ΠΏΡ.), Π° ΠΎΡ Π»Π°ΠΆΠ΄Π°Π΅ΡΡΡ Π² Π½Π΅ΠΎΠΊΠΈΡΠ»ΡΡΡΠΈΡ ΠΆΠΈΠ΄ΠΊΠΎΡΡΡΡ ΠΈΠ»ΠΈ ΡΠ°ΡΠΏΠ»Π°Π²Π°Ρ . ΠΡΠΈΠΌ ΡΠΏΠΎΡΠΎΠ±ΠΎΠΌ Π·Π°ΠΊΠ°Π»ΠΈΠ²Π°ΡΡ ΠΈΠ·Π΄Π΅Π»ΠΈΡ, ΠΊΠΎΡΠΎΡΡΠ΅ Π½Π΅ Π΄ΠΎΠ»ΠΆΠ½Ρ ΠΏΠΎΠ΄Π²Π΅ΡΠ³Π°ΡΡΡΡ Π΄Π°Π»ΡΠ½Π΅ΠΉΡΠ΅ΠΉ ΡΠ»ΠΈΡΠΎΠ²ΠΊΠ΅, Π° ΡΠ°ΠΊΠΆΠ΅ Π΄Π΅ΡΠ°Π»ΠΈ, ΠΊΡΠΈΡΠΈΡΠ½ΡΠ΅ ΠΊ ΡΠΎΠ΄Π΅ΡΠΆΠ°Π½ΠΈΡ ΡΠ³Π»Π΅ΡΠΎΠ΄Π° Π² ΠΏΠΎΠ²Π΅ΡΡ Π½ΠΎΡΡΠ½ΠΎΠΌ ΡΠ»ΠΎΠ΅.
ΠΠ±ΠΎΡΡΠ΄ΠΎΠ²Π°Π½ΠΈΠ΅ Π΄Π»Ρ ΡΠ΅ΡΠΌΠΎΠΎΠ±ΡΠ°Π±ΠΎΡΠΊΠΈ ΡΡΠ°Π»Π΅ΠΉ
ΠΡΠ½ΠΎΠ²Π½ΠΎΠ΅ ΠΎΠ±ΠΎΡΡΠ΄ΠΎΠ²Π°Π½ΠΈΠ΅, Π½Π° ΠΊΠΎΡΠΎΡΠΎΠΌ ΠΏΡΠΎΠ²ΠΎΠ΄ΠΈΡΡΡ ΡΠ΅ΡΠΌΠΈΡΠ΅ΡΠΊΠ°Ρ ΠΎΠ±ΡΠ°Π±ΠΎΡΠΊΠ° ΠΈΠ·Π΄Π΅Π»ΠΈΠΉ ΠΈΠ· ΡΡΠ°Π»Π΅ΠΉ ΠΈ ΡΠ²Π΅ΡΠ½ΡΡ ΠΌΠ΅ΡΠ°Π»Π»ΠΎΠ², ΡΠΎΡΡΠΎΠΈΡ ΠΈΠ· Π΄Π²ΡΡ ΠΎΡΠ½ΠΎΠ²Π½ΡΡ Π³ΡΡΠΏΠΏ: ΡΡΡΠ°Π½ΠΎΠ²ΠΎΠΊ Π΄Π»Ρ Π½Π°Π³ΡΠ΅Π²Π° Π·Π°Π³ΠΎΡΠΎΠ²ΠΎΠΊ ΠΈ Π·Π°ΠΊΠ°Π»ΠΎΡΠ½ΡΡ Π²Π°Π½Π½. ΠΠ°Π³ΡΠ΅Π²Π°ΡΠ΅Π»ΡΠ½ΡΠ΅ ΡΡΡΡΠΎΠΉΡΡΠ²Π° Π²ΠΊΠ»ΡΡΠ°ΡΡ Π² ΡΠ΅Π±Ρ ΡΠ»Π΅Π΄ΡΡΡΠΈΠ΅ Π²ΠΈΠ΄Ρ ΠΎΠ±ΠΎΡΡΠ΄ΠΎΠ²Π°Π½ΠΈΡ:
- ΠΌΡΡΠ΅Π»ΡΠ½ΡΠ΅ ΡΠ΅ΡΠΌΠΎΠΏΠ΅ΡΠΈ;
- ΡΡΡΡΠΎΠΉΡΡΠ²Π° ΠΈΠ½Π΄ΡΠΊΡΠΈΠΎΠ½Π½ΠΎΠ³ΠΎ Π½Π°Π³ΡΠ΅Π²Π°;
- ΡΡΡΠ°Π½ΠΎΠ²ΠΊΠΈ Π΄Π»Ρ Π½Π°Π³ΡΠ΅Π²Π° Π² ΡΠ°ΡΠΏΠ»Π°Π²Π°Ρ ;
- Π³Π°Π·ΠΎΠΏΠ»Π°Π·ΠΌΠ΅Π½Π½ΡΠ΅ ΡΡΡΠ°Π½ΠΎΠ²ΠΊΠΈ;
- Π°ΠΏΠΏΠ°ΡΠ°ΡΡ Π»Π°Π·Π΅ΡΠ½ΠΎΠΉ Π·Π°ΠΊΠ°Π»ΠΊΠΈ.
ΠΠ΅ΡΠ²ΡΠ΅ ΡΡΠΈ Π²ΠΈΠ΄Π° ΠΌΠΎΠ³ΡΡ Π²ΡΠΏΠΎΠ»Π½ΡΡΡ ΠΏΡΠΎΠ³ΡΠ΅Π² Π²ΡΠ΅Π³ΠΎ ΠΎΠ±ΡΠ΅ΠΌΠ° ΠΈΠ·Π΄Π΅Π»ΠΈΡ Π΄ΠΎ ΡΡΠ΅Π±ΡΠ΅ΠΌΠΎΠΉ ΡΠ΅ΠΌΠΏΠ΅ΡΠ°ΡΡΡΡ, Π° ΠΏΠΎΡΠ»Π΅Π΄Π½ΠΈΠ΅ β ΡΠΎΠ»ΡΠΊΠΎ ΠΏΠΎΠ²Π΅ΡΡ
Π½ΠΎΡΡΠ½ΠΎΠ³ΠΎ ΡΠ»ΠΎΡ ΠΌΠ΅ΡΠ°Π»Π»Π°. ΠΡΠΎΠΌΠ΅ ΡΠΎΠ³ΠΎ, Π²ΡΠΏΡΡΠΊΠ°ΡΡΡΡ ΠΈ ΡΠΈΡΠΎΠΊΠΎ ΠΈΡΠΏΠΎΠ»ΡΠ·ΡΡΡΡΡ ΠΏΠ΅ΡΠΈ Π΄Π»Ρ Π·Π°ΠΊΠ°Π»ΠΊΠΈ ΠΌΠ΅ΡΠ°Π»Π»ΠΎΠ², Π² ΠΊΠΎΡΠΎΡΡΡ
Π½Π°Π³ΡΠ΅Π² ΠΎΡΡΡΠ΅ΡΡΠ²Π»ΡΠ΅ΡΡΡ Π² Π²Π°ΠΊΡΡΠΌΠ΅ ΠΈΠ»ΠΈ Π² ΡΡΠ΅Π΄Π΅ ΠΈΠ½Π΅ΡΡΠ½ΠΎΠ³ΠΎ Π³Π°Π·Π°. ΠΠ°ΠΊΠ°Π»ΠΎΡΠ½ΡΠ΅ Π²Π°Π½Π½Ρ ΠΏΡΠ΅Π΄ΡΡΠ°Π²Π»Π΅Π½Ρ ΡΡΠ°Π»ΡΠ½ΡΠΌΠΈ Π΅ΠΌΠΊΠΎΡΡΡΠΌΠΈ-ΠΎΡ
Π»Π°Π΄ΠΈΡΠ΅Π»ΡΠΌΠΈ Π΄Π»Ρ ΡΠ°Π·Π»ΠΈΡΠ½ΡΡ
ΠΆΠΈΠ΄ΠΊΠΎΡΡΠ΅ΠΉ, Π° ΡΠ°ΠΊΠΆΠ΅ ΡΠΏΠ΅ΡΠΈΠ°Π»ΡΠ½ΡΠΌΠΈ ΡΠΈΠ³Π»ΡΠΌΠΈ ΠΈΠ· Π³ΡΠ°ΡΠΈΡΠ° ΠΈ ΠΏΠ΅ΡΠ°ΠΌΠΈ Π΄Π»Ρ ΡΠ°ΡΠΏΠ»Π°Π²ΠΎΠ² ΡΠΎΠ»Π΅ΠΉ ΠΈΠ»ΠΈ ΠΌΠ΅ΡΠ°Π»Π»ΠΎΠ². Π ΠΊΠ°ΡΠ΅ΡΡΠ²Π΅ Π·Π°ΠΊΠ°Π»ΠΎΡΠ½ΡΡ
ΠΆΠΈΠ΄ΠΊΠΎΡΡΠ΅ΠΉ ΡΠ°ΡΠ΅ Π²ΡΠ΅Π³ΠΎ ΠΈΡΠΏΠΎΠ»ΡΠ·ΡΡΡ ΠΌΠΈΠ½Π΅ΡΠ°Π»ΡΠ½ΠΎΠ΅ ΠΌΠ°ΡΠ»ΠΎ, Π²ΠΎΠ΄Ρ ΠΈ Π²ΠΎΠ΄ΠΎΠΏΠΎΠ»ΠΈΠΌΠ΅ΡΠ½ΡΠ΅ ΡΠΌΠ΅ΡΠΈ. ΠΠ»Ρ ΡΠ°ΡΠΏΠ»Π°Π²ΠΎΠ² ΠΌΠ΅ΡΠ°Π»Π»ΠΎΠ² ΠΎΠ±ΡΡΠ½ΠΎ ΠΏΡΠΈΠΌΠ΅Π½ΡΡΡ ΡΠ²ΠΈΠ½Π΅Ρ ΠΈΠ»ΠΈ ΠΎΠ»ΠΎΠ²ΠΎ, Π° Π΄Π»Ρ ΡΠ°ΡΠΏΠ»Π°Π²ΠΎΠ² ΡΠΎΠ»Π΅ΠΉ β ΡΠΎΠ΅Π΄ΠΈΠ½Π΅Π½ΠΈΡ Π½Π°ΡΡΠΈΡ, ΠΊΠ°Π»ΠΈΡ ΠΈ Π±Π°ΡΠΈΡ. ΠΠ°ΠΊΠ°Π»ΠΎΡΠ½ΡΠ΅ Π²Π°Π½Π½Ρ Π΄Π»Ρ ΠΆΠΈΠ΄ΠΊΠΈΡ
ΡΡΠ΅Π΄ ΠΈΠΌΠ΅ΡΡ ΡΠΈΡΡΠ΅ΠΌΡ Π½Π°Π³ΡΠ΅Π²Π° ΠΈ ΠΎΡ
Π»Π°ΠΆΠ΄Π΅Π½ΠΈΡ ΡΠ°Π±ΠΎΡΠ΅ΠΉ ΠΆΠΈΠ΄ΠΊΠΎΡΡΠΈ Π΄ΠΎ ΡΡΠ΅Π±ΡΠ΅ΠΌΠΎΠΉ ΡΠ΅ΠΌΠΏΠ΅ΡΠ°ΡΡΡΡ, Π° ΡΠ°ΠΊΠΆΠ΅ ΠΌΠ΅ΡΠ°Π»ΠΊΠΈ Π΄Π»Ρ ΡΠ°Π²Π½ΠΎΠΌΠ΅ΡΠ½ΠΎΠ³ΠΎ ΡΠ°ΡΠΏΡΠ΅Π΄Π΅Π»Π΅Π½ΠΈΡ ΠΆΠΈΠ΄ΠΊΠΎΡΡΠΈ ΠΈ ΡΠ°Π·ΡΡΡΠ΅Π½ΠΈΡ ΠΏΠ°ΡΠΎΠ²ΠΎΠΉ ΡΡΠ±Π°ΡΠΊΠΈ.
ΠΠΈΠ΄Π΅ΠΎ ΠΎΠ±ΠΎΡΡΠ΄ΠΎΠ²Π°Π½ΠΈΡ
Π’Π΅ΠΌΠΏΠ΅ΡΠ°ΡΡΡΠ° Π΄Π»Ρ Π·Π°ΠΊΠ°Π»ΠΊΠΈ
ΠΠΎΡΠΌΠ°ΡΠΈΠ²Π½Π°Ρ ΡΠ΅ΠΌΠΏΠ΅ΡΠ°ΡΡΡΠ° Π½Π°Π³ΡΠ΅Π²Π° ΡΡΠ°Π»ΠΈ ΠΏΡΠΈ Π΅Π΅ Π·Π°ΠΊΠ°Π»ΠΊΠ΅ Π½Π°ΠΏΡΡΠΌΡΡ Π·Π°Π²ΠΈΡΠΈΡ ΠΎΡ ΠΌΠ°ΡΡΠΎΠ²ΠΎΠΉ Π΄ΠΎΠ»ΠΈ ΡΠ³Π»Π΅ΡΠΎΠ΄Π° ΠΈ Π»Π΅Π³ΠΈΡΡΡΡΠΈΡ
Π΄ΠΎΠ±Π°Π²ΠΎΠΊ. Π ΡΠ΅Π»ΠΎΠΌ Π½Π°Π±Π»ΡΠ΄Π°Π΅ΡΡΡ ΡΠ»Π΅Π΄ΡΡΡΠ°Ρ Π·Π°Π²ΠΈΡΠΈΠΌΠΎΡΡΡ: ΡΠ΅ΠΌ ΠΌΠ΅Π½ΡΡΠ΅ ΡΠΎΠ΄Π΅ΡΠΆΠ°Π½ΠΈΠ΅ ΡΠ³Π»Π΅ΡΠΎΠ΄Π°, ΡΠ΅ΠΌ Π²ΡΡΠ΅ ΡΠ΅ΠΌΠΏΠ΅ΡΠ°ΡΡΡΠ° Π·Π°ΠΊΠ°Π»ΠΊΠΈ.
ΠΠ°ΡΠΊΠ° ΡΡΠ°Π»ΠΈ | Π’Π΅ΠΌΠΏΠ΅ΡΠ°ΡΡΡΠ°, Π‘ | ||
---|---|---|---|
Π·Π°ΠΊΠ°Π»ΠΊΠΈ | ΠΎΡΠΆΠΈΠ³Π° | ΠΎΡΠΏΡΡΠΊΠ° | |
15Π | 800 | 780 | 200 |
65Π | 815 | 790 | 400 |
15Π₯, 20Π₯ | 800 | 870 | 400 |
30Π₯, 35Π₯ | 850 | 880 | 450 |
40Π₯, 45Π₯ | 840 | 860 | 400 |
50Π₯ | 830 | 830 | 400 |
50Π2 | 805 | 830 | 200 |
40Π₯Π | 870 | 880 | 550 |
ΠΠ₯13 | 1050 | 860 | 750 |
3Π₯13 | 1050 | 880 | 450 |
35Π₯ΠΠ‘ | 870 | 860 | 500 |
30Π₯ΠΠ‘Π | 900 | 860 | 210 |
Π£7, Π£7Π | 800 | 780 | 170 |
Π 9, Π 12 | 1250 | 860 | 580 |
Π 9Π€5, Π 9Π5 | 1250 | 860 | 590 |
Π 18Π€2 | 1300 | 900 | 590 |
Π¨Π₯15 | 845 | 780 | 400 |
9Π₯Π‘ | 860 | 730 | 170 |
Π 18Π5Π€2 | 1280 | 860 | 580 |
1Π₯14Π18Π2ΠΠ Π | 1150 | 860 | 750 |
4Π₯14Π1482Π | 1200 | 860 | 750 |
ΠΠΏΡΠ΅Π΄Π΅Π»Π΅Π½ΠΈΠ΅ ΡΠ΅ΠΌΠΏΠ΅ΡΠ°ΡΡΡΡ Π½Π°Π³ΡΠ΅Π²Π° Π² ΠΏΡΠΎΠΌΡΡΠ»Π΅Π½Π½ΠΎΠΌ ΠΏΡΠΎΠΈΠ·Π²ΠΎΠ΄ΡΡΠ²Π΅ ΠΎΡΡΡΠ΅ΡΡΠ²Π»ΡΠ΅ΡΡΡ ΠΏΠΎΡΡΠ΅Π΄ΡΡΠ²ΠΎΠΌ ΠΊΠΎΠ½ΡΠ°ΠΊΡΠ½ΡΡ
ΠΈ Π±Π΅ΡΠΊΠΎΠ½ΡΠ°ΠΊΡΠ½ΡΡ
ΠΏΠΈΡΠΎΠΌΠ΅ΡΡΠΎΠ². Π ΠΏΠΎΡΠ»Π΅Π΄Π½ΠΈΠ΅ Π΄Π΅ΡΡΡΠΈΠ»Π΅ΡΠΈΡ ΡΠΈΡΠΎΠΊΠΎΠ΅ ΡΠ°ΡΠΏΡΠΎΡΡΡΠ°Π½Π΅Π½ΠΈΠ΅ ΠΏΠΎΠ»ΡΡΠΈΠ»ΠΈ ΠΈΠ½ΡΡΠ°ΠΊΡΠ°ΡΠ½ΡΠ΅ ΠΏΡΠΈΠ±ΠΎΡΡ, ΠΏΠΎΠ·Π²ΠΎΠ»ΡΡΡΠΈΠ΅ Π΄ΠΈΡΡΠ°Π½ΡΠΈΠΎΠ½Π½ΠΎ Π·Π°ΠΌΠ΅ΡΡΡΡ ΡΠ΅ΠΌΠΏΠ΅ΡΠ°ΡΡΡΡ Π² Π»ΡΠ±ΠΎΠΉ ΡΠΎΡΠΊΠΈ ΠΏΠΎΠ²Π΅ΡΡ
Π½ΠΎΡΡΠΈ Π½Π°Π³ΡΠ΅ΡΠΎΠΉ Π΄Π΅ΡΠ°Π»ΠΈ. ΠΡΠΎΠΌΠ΅ ΡΠΎΠ³ΠΎ, ΠΏΡΠΈΠ±Π»ΠΈΠ·ΠΈΡΠ΅Π»ΡΠ½ΡΡ ΡΠ΅ΠΌΠΏΠ΅ΡΠ°ΡΡΡΡ ΡΠ°Π·ΠΎΠ³ΡΠ΅Π²Π° ΡΡΠ°Π»ΠΈ ΠΌΠΎΠΆΠ½ΠΎ ΠΎΠΏΡΠ΅Π΄Π΅Π»ΠΈΡΡ ΠΏΠΎ ΡΠ²Π΅ΡΠΎΠ²ΡΠΌ ΡΠ°Π±Π»ΠΈΡΠ°ΠΌ.
Π’Π΅Ρ Π½ΠΎΠ»ΠΎΠ³ΠΈΡ ΠΊΠ°Π»Π΅Π½ΠΈΡ ΠΌΠ΅ΡΠ°Π»Π»Π°
Π’Π΅Ρ
Π½ΠΎΠ»ΠΎΠ³ΠΈΡ Π·Π°ΠΊΠ°Π»ΠΊΠΈ ΡΡΠ°Π»Π΅ΠΉ ΡΡΠ΅Π±ΡΠ΅Ρ ΡΠΎΠ±Π»ΡΠ΄Π΅Π½ΠΈΡ ΡΡΠ΄Π° ΡΡΠ΅Π±ΠΎΠ²Π°Π½ΠΈΠΉ ΠΊ ΠΏΡΠΎΡΠ΅ΡΡΠ°ΠΌ Π½Π°Π³ΡΠ΅Π²Π° ΠΈ ΠΎΡ
Π»Π°ΠΆΠ΄Π΅Π½ΠΈΡ Π·Π°ΠΊΠ°Π»ΠΈΠ²Π°Π΅ΠΌΡΡ
Π΄Π΅ΡΠ°Π»Π΅ΠΉ. Π ΠΏΠ΅ΡΠ²ΡΡ ΠΎΡΠ΅ΡΠ΅Π΄Ρ ΡΡΠΎ ΠΎΡΠ½ΠΎΡΠΈΡΡΡ ΠΊ ΡΠΊΠΎΡΠΎΡΡΠΈ ΡΠ°Π·ΠΎΠ³ΡΠ΅Π²Π° ΠΈ ΠΎΡ
Π»Π°ΠΆΠ΄Π΅Π½ΠΈΡ ΠΌΠ΅ΡΠ°Π»Π»Π°. ΠΠΊΠΎΠ½ΠΎΠΌΠΈΡΠ΅ΡΠΊΠΈΠ΅ ΠΏΠΎΠΊΠ°Π·Π°ΡΠ΅Π»ΠΈ ΡΠ΅ΡΠΌΠΈΡΠ΅ΡΠΊΠΎΠ³ΠΎ ΠΏΡΠΎΡΠ΅ΡΡΠ° ΡΡΠ΅Π±ΡΡΡ ΠΌΠ°ΠΊΡΠΈΠΌΠ°Π»ΡΠ½ΠΎ Π±ΡΡΡΡΠΎΠ³ΠΎ ΠΏΠΎΠ²ΡΡΠ΅Π½ΠΈΡ ΡΠ΅ΠΌΠΏΠ΅ΡΠ°ΡΡΡΡ Π΄ΠΎ Π½ΠΎΠΌΠΈΠ½Π°Π»ΡΠ½ΠΎΠΉ, Ρ. ΠΊ. ΠΏΡΠΈ ΡΡΠΎΠΌ ΡΠ°ΡΡ
ΠΎΠ΄ΡΠ΅ΡΡΡ ΠΌΠ΅Π½ΡΡΠ΅ ΡΠ½Π΅ΡΠ³ΠΈΠΈ. ΠΠ΄Π½Π°ΠΊΠΎ ΡΠΊΠΎΡΠΎΡΡΠ½ΠΎΠΉ Π½Π°Π³ΡΠ΅Π² ΠΏΡΠΈΠ²ΠΎΠ΄ΠΈΡ ΠΊ Π±ΠΎΠ»ΡΡΠΎΠΌΡ ΠΏΠ΅ΡΠ΅ΠΏΠ°Π΄Ρ ΡΠ΅ΠΌΠΏΠ΅ΡΠ°ΡΡΡ ΠΌΠ΅ΠΆΠ΄Ρ ΠΏΠΎΠ²Π΅ΡΡ
Π½ΠΎΡΡΠ½ΡΠΌ ΡΠ»ΠΎΠ΅ΠΌ ΠΈ ΡΠ΅ΡΠ΄ΡΠ΅Π²ΠΈΠ½ΠΎΠΉ ΠΈΠ·Π΄Π΅Π»ΠΈΡ, ΡΡΠΎ ΠΌΠΎΠΆΠ΅Ρ ΠΏΡΠΈΠ²Π΅ΡΡΠΈ ΠΊ Π΅Π³ΠΎ Π΄Π΅ΡΠΎΡΠΌΠ°ΡΠΈΠΈ ΠΈ Π²ΠΎΠ·Π½ΠΈΠΊΠ½ΠΎΠ²Π΅Π½ΠΈΡ ΡΡΠ΅ΡΠΈΠ½. ΠΠΎΡΡΠΎΠΌΡ ΠΏΡΠΎΠ³ΡΠ΅Π² Π½Π° Π²ΡΡ Π³Π»ΡΠ±ΠΈΠ½Ρ Π΄Π΅ΡΠ°Π»ΠΈ Π΄ΠΎ ΠΏΠΎΠ»Π½ΠΎΠ³ΠΎ Π΅Π΅ ΡΠ°Π·ΠΎΠ³ΡΠ΅Π²Π° Π΄ΠΎΠ»ΠΆΠ΅Π½ ΠΏΡΠΎΡ
ΠΎΠ΄ΠΈΡΡ ΠΏΠ»Π°Π²Π½ΠΎ, Π° Π΅Π³ΠΎ Π²ΡΠ΅ΠΌΡ ΠΎΠΏΡΠ΅Π΄Π΅Π»ΡΠ΅ΡΡΡ ΡΠ΅Ρ
Π½ΠΎΠ»ΠΎΠ³ΠΎΠΌ-ΡΠ΅ΡΠΌΠΈΡΡΠΎΠΌ Ρ ΠΏΠΎΠΌΠΎΡΡΡ ΡΠΌΠΏΠΈΡΠΈΡΠ΅ΡΠΊΠΈΡ
ΡΠΎΡΠΌΡΠ» ΠΈ ΡΠ°Π±Π»ΠΈΡΠ½ΡΡ
Π·Π½Π°ΡΠ΅Π½ΠΈΠΉ. ΠΡ ΡΠΊΠΎΡΠΎΡΡΠΈ ΠΈ ΡΠ΅ΠΌΠΏΠ΅ΡΠ°ΡΡΡΠ½ΡΡ
ΠΏΠ°ΡΠ°ΠΌΠ΅ΡΡΠΎΠ² ΠΎΡ
Π»Π°ΠΆΠ΄Π΅Π½ΠΈΡ ΡΡΠ°Π»ΠΈ, ΡΠ°Π·ΠΎΠ³ΡΠ΅ΡΠΎΠΉ Π²ΡΡΠ΅ ΠΊΡΠΈΡΠΈΡΠ΅ΡΠΊΠΎΠΉ ΡΠΎΡΠΊΠΈ, Π½Π°ΠΏΡΡΠΌΡΡ Π·Π°Π²ΠΈΡΠΈΡ ΠΏΡΠΎΡΠ΅ΡΡ ΡΠΎΡΠΌΠΈΡΠΎΠ²Π°Π½ΠΈΡ ΡΡΡΡΠΊΡΡΡΡ ΠΈ ΡΠΎΡΡΠ°Π²Π° Π·Π°ΠΊΠ°Π»Π΅Π½Π½ΠΎΠ³ΠΎ ΠΌΠ΅ΡΠ°Π»Π»Π°. Π ΠΏΡΠΈΠΌΠ΅ΡΡ, ΠΏΡΠΈ Π±ΡΡΡΡΠΎΠΌ ΠΎΡ
Π»Π°ΠΆΠ΄Π΅Π½ΠΈΠΈ Π² Π²ΠΎΠ΄Π΅ Ρ ΠΊΠΎΠΌΠ½Π°ΡΠ½ΠΎΠΉ ΡΠ΅ΠΌΠΏΠ΅ΡΠ°ΡΡΡΠΎΠΉ ΠΌΠΎΠΆΠ½ΠΎ ΠΏΠΎΠ»ΡΡΠΈΡΡ ΡΠ³Π»Π΅ΡΠΎΠ΄ΠΈΡΡΡΡ ΡΡΠ°Π»Ρ Ρ ΠΌΠ°ΡΡΠ΅Π½ΡΠΈΡΠ½ΠΎΠΉ ΡΡΡΡΠΊΡΡΡΠΎΠΉ, Π° ΠΏΡΠΈ ΠΎΡ
Π»Π°ΠΆΠ΄Π΅Π½ΠΈΠΈ Π² ΠΌΠ°ΡΠ»Π΅ ΠΈΠ»ΠΈ Π³ΠΎΡΡΡΠ΅ΠΉ Π²ΠΎΠ΄Π΅ ΠΏΠΎΠ»ΡΡΠ°Π΅ΡΡΡ ΡΡΠΎΠΎΡΡΠΈΡ. ΠΠ°ΠΆΠ΄ΠΎΠΉ ΠΌΠ°ΡΠΊΠ΅ ΡΡΠ°Π»ΠΈ ΡΠΎΠΎΡΠ²Π΅ΡΡΡΠ²ΡΡΡ ΡΠ²ΠΎΠΈ Ρ
Π°ΡΠ°ΠΊΡΠ΅ΡΠΈΡΡΠΈΠΊΠΈ ΠΈ ΡΠ΅ΠΌΠΏΠ΅ΡΠ°ΡΡΡΠ½ΡΠ΅ ΡΠ΅ΠΆΠΈΠΌΡ Π·Π°ΠΊΠ°Π»ΠΊΠΈ, ΠΊΠΎΡΠΎΡΡΠ΅, ΠΏΠΎΠΌΠΈΠΌΠΎ ΠΏΡΠΎΡΠ΅Π³ΠΎ, Π·Π°Π²ΠΈΡΡΡ ΠΎΡ ΡΠ°Π·ΠΌΠ΅ΡΠ° ΠΈ ΡΠΎΡΠΌΡ Π΄Π΅ΡΠ°Π»ΠΈ. ΠΠΎΡΡΠΎΠΌΡ Π½Π° ΠΏΡΠΎΠΈΠ·Π²ΠΎΠ΄ΡΡΠ²Π΅ ΡΠ΅ΡΠΌΠΈΡΠ΅ΡΠΊΠ°Ρ ΠΎΠ±ΡΠ°Π±ΠΎΡΠΊΠ° Π΄Π΅ΡΠ°Π»Π΅ΠΉ ΠΏΡΠΎΠ²ΠΎΠ΄ΠΈΡΡΡ Π² ΡΠΎΠΎΡΠ²Π΅ΡΡΡΠ²ΠΈΠΈ Ρ ΠΌΠ°ΡΡΡΡΡΠ½ΠΎΠΉ ΡΠ΅Ρ
Π½ΠΎΠ»ΠΎΠ³ΠΈΠ΅ΠΉ ΠΈ ΠΎΠΏΠ΅ΡΠ°ΡΠΈΠΎΠ½Π½ΡΠΌΠΈ ΠΊΠ°ΡΡΠ°ΠΌΠΈ, ΡΠ°Π·ΡΠ°Π±Π°ΡΡΠ²Π°Π΅ΠΌΡΠΌΠΈ Π΄Π»Ρ ΠΊΠ°ΠΆΠ΄ΠΎΠ³ΠΎ ΠΈΠ·Π΄Π΅Π»ΠΈΡ.
Π€ΠΎΡΠΎ ΠΎΠ±ΠΎΡΡΠ΄ΠΎΠ²Π°Π½ΠΈΡ
ΠΠΎΠ½ΡΠ°ΠΊΡΡ
ΠΠ΄ΡΠ΅Ρ: 423825, Π Π΅ΡΠΏΡΠ±Π»ΠΈΠΊΠ° Π’Π°ΡΠ°ΡΡΡΠ°Π½, Π³. ΠΠ°Π±Π΅ΡΠ΅ΠΆΠ½ΡΠ΅ Π§Π΅Π»Π½Ρ, ΡΠ». ΠΡΠΎΡΠΈΠ»ΡΠ½Π°Ρ, 106
Π’Π΅Π»: +7 (8552) 77-83-68
Email: [email protected]
Π’Π΅ΡΠΌΠΈΡΠ΅ΡΠΊΠ°Ρ ΠΎΠ±ΡΠ°Π±ΠΎΡΠΊΠ° β ΡΡΠ°Π»ΠΈ β ΠΌΠ΅ΡΠ°Π»Π»ΠΎΠ² β Π²ΠΈΠ΄Ρ β ΡΠ²ΠΎΠΉΡΡΠ²Π°.
Π§ΡΠΎ ΡΠ°ΠΊΠΎΠ΅ ΡΠ΅ΡΠΌΠΎΠΎΠ±ΡΠ°Π±ΠΎΡΠΊΠ° ΠΈΒ Π·Π°ΡΠ΅ΠΌ ΠΎΠ½Π° Π½ΡΠΆΠ½Π°?
Π’Π΅ΡΠΌΠΈΡΠ΅ΡΠΊΠ°Ρ ΠΎΠ±ΡΠ°Π±ΠΎΡΠΊΠ° (ΡΠ΅ΡΠΌΠΎΠΎΠ±ΡΠ°Π±ΠΎΡΠΊΠ°, Π’Π)Β β ΠΏΡΠΎΡΠ΅ΡΡ ΡΠ΅ΠΏΠ»ΠΎΠ²ΠΎΠΉ ΠΎΠ±ΡΠ°Π±ΠΎΡΠΊΠΈ ΠΈΠ·Π΄Π΅Π»ΠΈΠΉ ΠΈΠ·Β ΠΌΠ΅ΡΠ°Π»Π»ΠΎΠ² ΠΈΒ ΡΠΏΠ»Π°Π²ΠΎΠ² ΡΒ ΡΠ΅Π»ΡΡ ΠΈΠ·ΠΌΠ΅Π½Π΅Π½ΠΈΡ ΠΈΡ
Β ΡΡΡΡΠΊΡΡΡΡ ΠΈΒ ΡΠ²ΠΎΠΉΡΡΠ² Π²Β Π·Π°Π΄Π°Π½Π½ΠΎΠΌ Π½Π°ΠΏΡΠ°Π²Π»Π΅Π½ΠΈΠΈ, Π·Π°ΠΊΠ»ΡΡΠ°ΡΡΠΈΠΉΡΡ Π²Β Π½Π°Π³ΡΠ΅Π²Π΅ ΡΒ Π·Π°Π΄Π°Π½Π½ΠΎΠΉ ΡΠΊΠΎΡΠΎΡΡΡΡ Π΄ΠΎΒ ΠΎΠΏΡΠ΅Π΄Π΅Π»Π΅Π½Π½ΠΎΠΉ ΡΠ΅ΠΌΠΏΠ΅ΡΠ°ΡΡΡΡ, Π²ΡΠ΄Π΅ΡΠΆΠΊΠ΅ Π²Β ΡΠ΅ΡΠ΅Π½ΠΈΠ΅ ΠΎΠΏΡΠ΅Π΄Π΅Π»ΡΠ½Π½ΠΎΠ³ΠΎ Π²ΡΠ΅ΠΌΠ΅Π½ΠΈ ΠΈΒ ΠΏΠΎΡΠ»Π΅Π΄ΡΡΡΠ΅ΠΌ ΠΎΡ
Π»Π°ΠΆΠ΄Π΅Π½ΠΈΠΈ ΡΒ Π·Π°Π΄Π°Π½Π½ΠΎΠΉ ΡΠΊΠΎΡΠΎΡΡΡΡ Π΄ΠΎΒ Π±ΠΎΠ»Π΅Π΅ Π½ΠΈΠ·ΠΊΠΎΠΉ ΡΠ΅ΠΌΠΏΠ΅ΡΠ°ΡΡΡΡ.
ΠΠ°Π΄Π°ΡΠ° ΡΠ΅ΡΠΌΠΎΠΎΠ±ΡΠ°Π±ΠΎΡΠΊΠΈΒ β ΠΏΡΡΠ΅ΠΌ Π½Π°Π³ΡΠ΅Π²Π° ΠΈΒ ΠΎΡ Π»Π°ΠΆΠ΄Π΅Π½ΠΈΡ Π²ΡΠ·Π²Π°ΡΡ Π½Π΅ΠΎΠ±ΡΠ°ΡΠΈΠΌΠΎΠ΅ ΠΈΠ·ΠΌΠ΅Π½Π΅Π½ΠΈΠ΅ ΡΠ²ΠΎΠΉΡΡΠ² Π²ΡΠ»Π΅Π΄ΡΡΠ²ΠΈΠ΅ Π½Π΅ΠΎΠ±ΡΠ°ΡΠΈΠΌΠΎΠ³ΠΎ ΠΈΠ·ΠΌΠ΅Π½Π΅Π½ΠΈΡ ΡΡΡΡΠΊΡΡΡΡ. Π’Π΅ΡΠΌΠΎΠΎΠ±ΡΠ°Π±ΠΎΡΠΊΠ° ΡΠ²Π»ΡΠ΅ΡΡΡ ΠΎΠ΄Π½ΠΈΠΌ ΠΈΠ·Β Π²Π°ΠΆΠ½Π΅ΠΉΡΠΈΡ ΡΡΠ°ΠΏΠΎΠ² ΡΠ΅Ρ Π½ΠΎΠ»ΠΎΠ³ΠΈΡΠ΅ΡΠΊΠΎΠ³ΠΎ ΠΏΡΠΎΡΠ΅ΡΡΠ° ΠΏΡΠΎΠΈΠ·Π²ΠΎΠ΄ΡΡΠ²Π° ΠΌΠ΅ΡΠ°Π»Π»ΠΈΡΠ΅ΡΠΊΠΈΡ ΠΈΠ·Π΄Π΅Π»ΠΈΠΉ. ΠΡΠΎ ΠΎΠ΄Π½Π° ΠΈΠ·Β ΡΠ°ΠΌΡΡ ΠΎΡΠ²Π΅ΡΡΡΠ²Π΅Π½Π½ΡΡ Β ΠΈ, Π½Π΅ΡΠΌΠΎΡΡΡ Π½Π°Β ΠΊΠ°ΠΆΡΡΡΡΡΡ ΠΏΡΠΎΡΡΠΎΡΡ, ΠΎΠ΄Π½Π° ΠΈΠ·Β ΡΠ°ΠΌΡΡ ΡΠ»ΠΎΠΆΠ½ΡΡ ΠΈΒ Π±ΡΠ°ΠΊΠΎΠ½ΠΎΡΠ½ΡΡ ΠΎΠΏΠ΅ΡΠ°ΡΠΈΠΉ ΠΏΡΠΈ ΠΈΠ·Π³ΠΎΡΠΎΠ²Π»Π΅Π½ΠΈΠΈ ΠΌΠ΅ΡΠ°Π»Π»ΠΈΡΠ΅ΡΠΊΠΎΠΉ ΠΏΡΠΎΠ΄ΡΠΊΡΠΈΠΈ.
Π’Π΅ΡΠΌΠΎΠΎΠ±ΡΠ°Π±ΠΎΡΠΊΡ ΠΏΡΠΈΠΌΠ΅Π½ΡΡΡ ΠΊΠ°ΠΊ ΠΏΡΠΎΠΌΠ΅ΠΆΡΡΠΎΡΠ½ΡΡ ΠΎΠΏΠ΅ΡΠ°ΡΠΈΡ Π΄Π»Ρ ΡΠ»ΡΡΡΠ΅Π½ΠΈΡ ΡΠ΅Ρ Π½ΠΎΠ»ΠΎΠ³ΠΈΡΠ΅ΡΠΊΠΈΡ ΡΠ²ΠΎΠΉΡΡΠ² (ΠΎΠ±ΡΠ°Π±Π°ΡΡΠ²Π°Π΅ΠΌΠΎΡΡΠΈ Π΄Π°Π²Π»Π΅Π½ΠΈΠ΅ΠΌ, ΡΠ΅Π·Π°Π½ΠΈΠ΅ΠΌ ΠΈΒ Π΄Ρ.) ΠΈΒ ΠΊΠ°ΠΊ ΠΎΠΊΠΎΠ½ΡΠ°ΡΠ΅Π»ΡΠ½ΡΡ ΠΎΠΏΠ΅ΡΠ°ΡΠΈΡ Π΄Π»Ρ ΠΏΡΠΈΠ΄Π°Π½ΠΈΡ ΠΌΠ΅ΡΠ°Π»Π»Ρ ΠΈΠ»ΠΈ ΡΠΏΠ»Π°Π²Ρ ΡΠ°ΠΊΠΎΠ³ΠΎ ΠΊΠΎΠΌΠΏΠ»Π΅ΠΊΡΠ° ΠΌΠ΅Ρ Π°Π½ΠΈΡΠ΅ΡΠΊΠΈΡ (Π°Β Π²Β ΡΡΠ΄Π΅ ΡΠ»ΡΡΠ°Π΅Π² ΠΈΒ ΡΠΈΠ·ΠΈΠΊΠΎ-Ρ ΠΈΠΌΠΈΡΠ΅ΡΠΊΠΈΡ ΡΠ²ΠΎΠΉΡΡΠ²), ΠΊΠΎΡΠΎΡΡΠΉ ΠΎΠ±Π΅ΡΠΏΠ΅ΡΠΈΠ²Π°Π΅Ρ Π½Π΅ΠΎΠ±Ρ ΠΎΠ΄ΠΈΠΌΡΠ΅ ΡΠΊΡΠΏΠ»ΡΠ°ΡΠ°ΡΠΈΠΎΠ½Π½ΡΠ΅ Ρ Π°ΡΠ°ΠΊΡΠ΅ΡΠΈΡΡΠΈΠΊΠΈ ΠΈΠ·Π΄Π΅Π»ΠΈΡ.
ΠΠ΅Π· ΡΠ΅ΡΠΌΠΎΠΎΠ±ΡΠ°Π±ΠΎΡΠΊΠΈ Π½Π΅Π²ΠΎΠ·ΠΌΠΎΠΆΠ½ΠΎ ΠΎΠ±Π΅ΡΠΏΠ΅ΡΠΈΡΡ Π΄ΠΎΡΡΠΈΠΆΠ΅Π½ΠΈΠ΅ Π½Π°Π΄Π»Π΅ΠΆΠ°ΡΠΈΡ ΡΠΊΡΠΏΠ»ΡΠ°ΡΠ°ΡΠΈΠΎΠ½Π½ΡΡ Ρ Π°ΡΠ°ΠΊΡΠ΅ΡΠΈΡΡΠΈΠΊΒ β Π΄ΠΎΡΡΠ°ΡΠΎΡΠ½ΠΎ ΡΠΊΠ°Π·Π°ΡΡ, ΡΡΠΎ ΡΡΠ°Π½Π΄Π°ΡΡΠ½Π°Ρ Π΄Π»Ρ Π±ΠΎΠ»ΡΡΠΈΠ½ΡΡΠ²Π° ΠΈΠ½ΡΡΡΡΠΌΠ΅Π½ΡΠΎΠ² ΡΠ΅ΡΠΌΠΎΠΎΠ±ΡΠ°Π±ΠΎΡΠΊΠ° (Π·Π°ΠΊΠ°Π»ΠΊΠ° ΡΒ Π½ΠΈΠ·ΠΊΠΈΠΌ ΠΎΡΠΏΡΡΠΊΠΎΠΌ) ΠΏΠΎΠ²ΡΡΠ°Π΅Ρ ΡΠ²Π΅ΡΠ΄ΠΎΡΡΡ ΠΈΒ ΠΏΡΠΎΡΠ½ΠΎΡΡΡ ΠΈΠ·Π΄Π΅Π»ΠΈΠΉ Π²Β 3-4Β ΡΠ°Π·Π°!
ΠΡΠ΅ ΡΠ»ΠΎΠΆΠ½Π΅Π΅ ΠΎΠ±ΡΡΠΎΠΈΡ Π΄Π΅Π»ΠΎ ΡΒ ΠΈΠ·Π½ΠΎΡΠΎΡΡΠΎΠΉΠΊΠΎΡΡΡΡ: Π΄Π°ΠΆΠ΅ Π΄Π΅ΡΠ°Π»ΠΈ, ΡΠ΅ΡΠΌΠΎΠΎΠ±ΡΠ°Π±ΠΎΡΠ°Π½Π½ΡΠ΅ ΠΏΠΎΒ ΡΠ°Π·Π½ΡΠΌ ΡΠ΅ΠΆΠΈΠΌΠ°ΠΌ Π½Π°Β ΠΎΠ΄ΠΈΠ½Π°ΠΊΠΎΠ²ΡΡ ΡΠ²Π΅ΡΠ΄ΠΎΡΡΡ ΠΈΒ ΠΏΡΠΎΡΠ½ΠΎΡΡΡ, ΠΌΠΎΠ³ΡΡ ΡΠ°Π·Π»ΠΈΡΠ°ΡΡΡΡ ΠΏΠΎΒ ΠΈΠ·Π½ΠΎΡΠΎΡΡΠΎΠΉΠΊΠΎΡΡΠΈ Π²Β 1,5-3 ΡΠ°Π·Π° ΠΈΠ·-Π·Π° ΡΠ°Π·Π»ΠΈΡΠΈΠΉ Π²Β ΠΌΠΈΠΊΡΠΎΡΡΡΡΠΊΡΡΡΠ΅ (ΠΏΠΎΒ ΡΡΠΎΠΉ ΠΏΡΠΈΡΠΈΠ½Π΅ Π΄Π»Ρ ΠΎΡΠ²Π΅ΡΡΡΠ²Π΅Π½Π½ΡΡ
Π΄Π΅ΡΠ°Π»Π΅ΠΉ Π²Β ΡΠ΅ΡΡΠ΅ΠΆΠ°Ρ
ΠΎΠ³ΠΎΠ²Π°ΡΠΈΠ²Π°ΡΡΡΡ ΡΡΠ΅Π±ΠΎΠ²Π°Π½ΠΈΡ Π½Π΅Β ΡΠΎΠ»ΡΠΊΠΎ ΠΊΒ ΠΌΠ΅Ρ
Π°Π½ΠΈΡΠ΅ΡΠΊΠΈΠΌ ΡΠ²ΠΎΠΉΡΡΠ²Π°ΠΌ, Π½ΠΎΒ ΠΈΒ ΠΊΒ ΠΌΠΈΠΊΡΠΎΡΡΡΡΠΊΡΡΡΠ΅).
ΠΠΎΒ ΡΠΊΠ°Π·Π°Π½Π½ΡΠΌ ΠΏΡΠΈΡΠΈΠ½Π°ΠΌ ΡΠ΅ΡΠΌΠΎΠΎΠ±ΡΠ°Π±ΠΎΡΠΊΠ° ΡΠ²Π»ΡΠ΅ΡΡΡ Π²Π°ΠΆΠ½Π΅ΠΉΡΠΈΠΌ ΠΏΡΠΎΡΠ΅ΡΡΠΎΠΌ ΠΏΡΠΈ ΠΈΠ·Π³ΠΎΡΠΎΠ²Π»Π΅Π½ΠΈΠΈ ΠΎΡΠ²Π΅ΡΡΡΠ²Π΅Π½Π½ΡΡ ΠΌΠ΅ΡΠ°Π»Π»ΠΈΡΠ΅ΡΠΊΠΈΡ ΠΈΠ·Π΄Π΅Π»ΠΈΠΉ.
ΠΡΠ½ΠΎΠ²Π½ΡΠ΅ ΡΠΈΠΏΡ ΡΠ΅ΡΠΌΠΎΠΎΠ±ΡΠ°Π±ΠΎΡΠΊΠΈ
Π’Π΅ΡΠΌΠΈΡΠ΅ΡΠΊΠ°Ρ ΠΎΠ±ΡΠ°Π±ΠΎΡΠΊΠ° ΠΏΠΎΠ΄ΡΠ°Π·Π΄Π΅Π»ΡΠ΅ΡΡΡ Π½Π°Β ΡΡΠΈ ΠΎΡΠ½ΠΎΠ²Π½ΡΡ ΡΠΈΠΏΠ°: ΡΠΎΠ±ΡΡΠ²Π΅Π½Π½ΠΎ ΡΠ΅ΡΠΌΠΈΡΠ΅ΡΠΊΡΡ (Π’Π), Ρ ΠΈΠΌΠΈΠΊΠΎ-ΡΠ΅ΡΠΌΠΈΡΠ΅ΡΠΊΡΡ (Π₯Π’Π) ΠΈΒ Π΄Π΅ΡΠΎΡΠΌΠ°ΡΠΈΠΎΠ½Π½ΠΎ-ΡΠ΅ΡΠΌΠΈΡΠ΅ΡΠΊΡΡ.
- Π‘ΠΎΠ±ΡΡΠ²Π΅Π½Π½ΠΎ ΡΠ΅ΡΠΌΠΈΡΠ΅ΡΠΊΠ°Ρ ΠΎΠ±ΡΠ°Π±ΠΎΡΠΊΠ° ΠΏΡΠ΅Π΄ΡΡΠΌΠ°ΡΡΠΈΠ²Π°Π΅Ρ ΡΠΎΠ»ΡΠΊΠΎ ΡΠ΅ΠΌΠΏΠ΅ΡΠ°ΡΡΡΠ½ΠΎ-Π²ΡΠ΅ΠΌΠ΅Π½Π½ΠΎΠ΅ Π²ΠΎΠ·Π΄Π΅ΠΉΡΡΠ²ΠΈΠ΅ Π½Π°Β ΠΌΠ΅ΡΠ°Π»Π» ΠΈΠ»ΠΈ ΡΠΏΠ»Π°Π².
- ΠΒ ΡΠΎΠΌ ΡΠ»ΡΡΠ°Π΅, ΠΊΠΎΠ³Π΄Π° ΠΏΡΠΈ ΡΠ΅ΡΠΌΠΎΠΎΠ±ΡΠ°Π±ΠΎΡΠΊΠ΅ ΡΠ΅Π»Π΅Π½Π°ΠΏΡΠ°Π²Π»Π΅Π½Π½ΠΎ ΠΈΠ·ΠΌΠ΅Π½ΡΠ΅ΡΡΡ Ρ ΠΈΠΌΠΈΡΠ΅ΡΠΊΠΈΠΉ ΡΠΎΡΡΠ°Π² ΠΏΠΎΠ²Π΅ΡΡ Π½ΠΎΡΡΠ½ΡΡ ΡΠ»ΠΎΠ΅Π² ΠΌΠ΅ΡΠ°Π»Π»Π° (ΡΠΏΠ»Π°Π²Π°), ΡΠΎΒ ΡΠ°ΠΊΠ°Ρ ΠΎΠ±ΡΠ°Π±ΠΎΡΠΊΠ° Π½Π°Π·ΡΠ²Π°Π΅ΡΡΡ Ρ ΠΈΠΌΠΈΠΊΠΎ-ΡΠ΅ΡΠΌΠΈΡΠ΅ΡΠΊΠΎΠΉ.
- ΠΒ Π΅ΡΠ»ΠΈ Π½Π°ΡΡΠ΄Ρ ΡΒ ΡΠ΅ΡΠΌΠΈΡΠ΅ΡΠΊΠΈΠΌ ΠΏΡΠΎΠΈΠ·Π²ΠΎΠ΄ΠΈΡΡΡ Π΅ΡΠ΅ ΠΈΒ Π΄Π΅ΡΠΎΡΠΌΠ°ΡΠΈΠΎΠ½Π½ΠΎΠ΅ Π²ΠΎΠ·Π΄Π΅ΠΉΡΡΠ²ΠΈΠ΅, ΠΏΡΠΈΠ²ΠΎΠ΄ΡΡΠ΅Π΅ ΠΊΒ Π²Β ΠΈΠ·ΠΌΠ΅Π½Π΅Π½ΠΈΡ ΡΡΡΡΠΊΡΡΡΡ, ΡΠΎΒ ΡΠ°ΠΊΠ°Ρ ΠΎΠ±ΡΠ°Π±ΠΎΡΠΊΠ° Π½Π°Π·ΡΠ²Π°Π΅ΡΡΡ Π΄Π΅ΡΠΎΡΠΌΠ°ΡΠΈΠΎΠ½Π½ΠΎ-ΡΠ΅ΡΠΌΠΈΡΠ΅ΡΠΊΠΎΠΉ (Π΅ΡΒ Π²ΠΈΠ΄Ρ: ΡΠ΅ΡΠΌΠΎΠΌΠ΅Ρ Π°Π½ΠΈΡΠ΅ΡΠΊΠ°ΡΒ β Π’ΠΠ, ΠΌΠ΅Ρ Π°Π½ΠΎΡΠ΅ΡΠΌΠΈΡΠ΅ΡΠΊΠ°ΡΒ β ΠΠ’Π ΠΈΒ Π΄Ρ.). ΠΠ°Β ΡΠΈΡ.Β 1Β ΠΏΡΠΈΠ²Π΅Π΄Π΅Π½Π° ΠΊΡΠ°ΡΠΊΠ°Ρ ΠΊΠ»Π°ΡΡΠΈΡΠΈΠΊΠ°ΡΠΈΠΎΠ½Π½Π°Ρ ΡΡ Π΅ΠΌΠ° ΠΎΡΠ½ΠΎΠ²Π½ΡΡ Π²ΠΈΠ΄ΠΎΠ² ΡΠ΅ΡΠΌΠΈΡΠ΅ΡΠΊΠΎΠΉ ΠΎΠ±ΡΠ°Π±ΠΎΡΠΊΠΈ ΠΌΠ΅ΡΠ°Π»Π»ΠΎΠ² ΠΈΒ ΡΠΏΠ»Π°Π²ΠΎΠ².
ΠΠΈΠ΄Ρ ΠΈΒ ΠΎΡΠΎΠ±Π΅Π½Π½ΠΎΡΡΠΈ ΡΠΎΠ±ΡΡΠ²Π΅Π½Π½ΠΎ ΡΠ΅ΡΠΌΠΈΡΠ΅ΡΠΊΠΎΠΉ ΠΎΠ±ΡΠ°Π±ΠΎΡΠΊΠΈ
Π‘ΠΎΠ±ΡΡΠ²Π΅Π½Π½ΠΎ ΡΠ΅ΡΠΌΠΈΡΠ΅ΡΠΊΠ°Ρ ΠΎΠ±ΡΠ°Π±ΠΎΡΠΊΠ° Π²ΠΊΠ»ΡΡΠ°Π΅Ρ Π²Β ΡΠ΅Π±Ρ ΡΠ»Π΅Π΄ΡΡΡΠΈΠ΅ ΠΎΡΠ½ΠΎΠ²Π½ΡΠ΅ Π²ΠΈΠ΄Ρ:
- ΠΡΠΆΠΈΠ³ 1-Π³ΠΎ ΡΠΎΠ΄Π°
- ΠΡΠΆΠΈΠ³ 2-Π³ΠΎ ΡΠΎΠ΄Π°
- ΠΠ°ΠΊΠ°Π»ΠΊΡ ΡΒ ΠΏΠΎΠ»ΠΈΠΌΠΎΡΡΠ½ΡΠΌ ΠΏΡΠ΅Π²ΡΠ°ΡΠ΅Π½ΠΈΠ΅ΠΌ
- ΠΠ°ΠΊΠ°Π»ΠΊΡ Π±Π΅Π· ΠΏΠΎΠ»ΠΈΠΌΠΎΡΡΠ½ΠΎΠ³ΠΎ ΠΏΡΠ΅Π²ΡΠ°ΡΠ΅Π½ΠΈΡ
- ΠΡΠΏΡΡΠΊ
- Π‘ΡΠ°ΡΠ΅Π½ΠΈΠ΅
ΠΡ
Β ΠΈΡΠΏΠΎΠ»ΡΠ·ΡΡΡ ΠΊΠ°ΠΊ Π΄Π»Ρ ΡΡΠ°Π»Π΅ΠΉ, ΡΠ°ΠΊ ΠΈΒ Π΄Π»Ρ ΡΠ²Π΅ΡΠ½ΡΡ
ΠΌΠ΅ΡΠ°Π»Π»ΠΎΠ² ΠΈΒ ΡΠΏΠ»Π°Π²ΠΎΠ². ΠΠ°ΠΆΠ΄ΡΠΉ ΠΈΠ·Β ΡΡΠΈΡ
Π²ΠΈΠ΄ΠΎΠ² ΡΠ΅ΡΠΌΠΎΠΎΠ±ΡΠ°Π±ΠΎΡΠΊΠΈ ΠΏΠΎΠ΄ΡΠ°Π·Π΄Π΅Π»ΡΡΡ Π½Π°Β ΡΠ°Π·Π½ΠΎΠ²ΠΈΠ΄Π½ΠΎΡΡΠΈ, ΡΠΏΠ΅ΡΠΈΡΠΈΡΠ΅ΡΠΊΠΈΠ΅ Π΄Π»Ρ ΡΠ°Π·Π»ΠΈΡΠ½ΡΡ
ΡΠΏΠ»Π°Π²ΠΎΠ².
ΠΡΠΎΠ±Π΅Π½Π½ΠΎΡΡΠΈ ΠΎΡΠΆΠΈΠ³Π°Β I ΡΠΎΠ΄Π°
ΠΡΠΆΠΈΠ³ IΒ ΡΠΎΠ΄Π°Β β Π½Π°Π³ΡΠ΅Π² Π΄ΠΎΒ ΠΎΠΏΡΠ΅Π΄Π΅Π»ΡΠ½Π½ΠΎΠΉ ΡΠ΅ΠΌΠΏΠ΅ΡΠ°ΡΡΡΡ ΠΌΠ΅ΡΠ°Π»Π»Π° ΠΈΠ»ΠΈ ΡΠΏΠ»Π°Π²Π°, Π½Π°Ρ ΠΎΠ΄ΡΡΠ΅Π³ΠΎΡΡ Π²Β Π½Π΅ΡΡΠ°Π±ΠΈΠ»ΡΠ½ΠΎΠΌ ΡΠΎΡΡΠΎΡΠ½ΠΈΠΈ Π²Β ΡΠ΅Π·ΡΠ»ΡΡΠ°ΡΠ΅ ΠΏΡΠ΅Π΄ΡΠ΅ΡΡΠ²ΠΎΠ²Π°Π²ΡΠ΅ΠΉ ΠΎΠ±ΡΠ°Π±ΠΎΡΠΊΠΈ, ΡΒ ΡΠ΅Π»ΡΡ ΠΏΡΠΈΠ²Π΅Π΄Π΅Π½ΠΈΡ Π΅Π³ΠΎ Π²Β Π±ΠΎΠ»Π΅Π΅ ΡΡΠ°Π±ΠΈΠ»ΡΠ½ΠΎΠ΅ ΡΠΎΡΡΠΎΡΠ½ΠΈΠ΅Β β Π½Π°ΠΏΡΠΈΠΌΠ΅Ρ, Π΄Π»Ρ Π³ΠΎΠΌΠΎΠ³Π΅Π½ΠΈΠ·Π°ΡΠΈΠΈ, ΡΠ½ΡΡΠΈΡ Π²Π½ΡΡΡΠ΅Π½Π½ΠΈΡ Π½Π°ΠΏΡΡΠΆΠ΅Π½ΠΈΠΉ, ΡΠ΅ΠΊΡΠΈΡΡΠ°Π»Π»ΠΈΠ·Π°ΡΠΈΠΈ.
ΠΡΠ½ΠΎΠ²Π½ΡΠ΅ Π΅Π³ΠΎ ΠΏΠΎΠ΄Π²ΠΈΠ΄Ρ: Π³ΠΎΠΌΠΎΠ³Π΅Π½ΠΈΠ·ΠΈΡΡΡΡΠΈΠΉ ΠΎΡΠΆΠΈΠ³, ΡΠ΅Π»Π°ΠΊΡΠ°ΡΠΈΠΎΠ½Π½ΡΠΉ ΠΎΡΠΆΠΈΠ³ (ΠΎΠ½Β ΠΆΠ΅Β β ΠΎΡΠΆΠΈΠ³ Π΄Π»Ρ ΡΠ½ΡΡΠΈΡ Π²Π½ΡΡΡΠ΅Π½Π½ΠΈΡ Π½Π°ΠΏΡΡΠΆΠ΅Π½ΠΈΠΉ), Π΄ΠΎΡΠ΅ΠΊΡΠΈΡΡΠ°Π»Π»ΠΈΠ·Π°ΡΠΈΠΎΠ½Π½ΡΠΉ ΠΎΡΠΆΠΈΠ³, ΡΠ΅ΠΊΡΠΈΡΡΠ°Π»Π»ΠΈΠ·Π°ΡΠΈΠΎΠ½Π½ΡΠΉ ΠΎΡΠΆΠΈΠ³.
ΠΒ ΠΠΠ Β«Π’Π΅Ρ Π½ΠΎΠΏΠ°ΡΠΊ ΠΠΌΠΏΡΠ»ΡΡΒ» ΠΈΠ·Β ΡΠΊΠ°Π·Π°Π½Π½ΡΡ ΠΏΠΎΠ΄Π²ΠΈΠ΄ΠΎΠ² ΠΏΡΠΈΠΌΠ΅Π½ΡΠ΅ΡΡΡ Π³Π»Π°Π²Π½ΡΠΌ ΠΎΠ±ΡΠ°Π·ΠΎΠΌ ΡΠ΅Π»Π°ΠΊΡΠ°ΡΠΈΠΎΠ½Π½ΡΠΉ ΠΎΡΠΆΠΈΠ³Β I ΡΠΎΠ΄Π° ΡΒ ΡΠ΅Π»ΡΡ ΡΠ½ΡΡΠΈΡ Π½Π°ΠΏΡΡΠΆΠ΅Π½ΠΈΠΉ ΠΏΠΎΡΠ»Π΅ ΡΠ»Π΅ΠΊΡΡΠΎΡΠ²Π°ΡΠΊΠΈ ΠΈΒ ΠΏΠΎΡΠ»Π΅ Π½Π΅ΠΊΠΎΡΠΎΡΡΡ ΠΎΠΏΠ΅ΡΠ°ΡΠΈΠΉ ΠΌΠ΅Ρ Π°Π½ΠΈΡΠ΅ΡΠΊΠΎΠΉ ΠΎΠ±ΡΠ°Π±ΠΎΡΠΊΠΈ (ΡΠ»ΠΈΡΠΎΠ²ΠΊΠΈ, ΠΏΠΎΠ»ΠΈΡΠΎΠ²ΠΊΠΈ)Β β ΡΡΠΎΡ Π²ΠΈΠ΄ ΠΎΡΠΆΠΈΠ³Π°.
ΠΡΠΎΠ±Π΅Π½Π½ΠΎΡΡΠΈ ΠΎΡΠΆΠΈΠ³Π°Β II ΡΠΎΠ΄Π°
ΠΡΠΆΠΈΠ³ IIΒ ΡΠΎΠ΄Π° (ΠΈΠ»ΠΈ ΡΠ°Π·ΠΎΠ²Π°Ρ ΠΏΠ΅ΡΠ΅ΠΊΡΠΈΡΡΠ°Π»Π»ΠΈΠ·Π°ΡΠΈΡ)Β β Π½Π°Π³ΡΠ΅Π² Π²ΡΡΠ΅ ΡΠ΅ΠΌΠΏΠ΅ΡΠ°ΡΡΡΡ ΠΏΠΎΠ»ΠΈΠΌΠΎΡΡΠ½ΠΎΠ³ΠΎ ΠΏΡΠ΅Π²ΡΠ°ΡΠ΅Π½ΠΈΡ ΡΒ ΠΏΠΎΡΠ»Π΅Π΄ΡΡΡΠΈΠΌ Π½Π΅ΠΏΡΠ΅ΡΡΠ²Π½ΡΠΌ (Π½Π΅ΠΈΠ·ΠΎΡΠ΅ΡΠΌΠΈΡΠ΅ΡΠΊΠΈΠΌ) ΠΈΠ»ΠΈ ΡΡΡΠΏΠ΅Π½ΡΠ°ΡΡΠΌ (ΠΈΠ·ΠΎΡΠ΅ΡΠΌΠΈΡΠ΅ΡΠΊΠΈΠΌ) ΠΎΡ
Π»Π°ΠΆΠ΄Π΅Π½ΠΈΠ΅ΠΌ Π΄Π»Ρ ΠΏΠΎΠ»ΡΡΠ΅Π½ΠΈΡ ΡΡΠ°Π±ΠΈΠ»ΡΠ½ΠΎΠ³ΠΎ ΡΡΡΡΠΊΡΡΡΠ½ΠΎΠ³ΠΎ ΡΠΎΡΡΠΎΡΠ½ΠΈΡ ΡΠΏΠ»Π°Π²Π°.
ΠΠ±ΡΠ·Π°ΡΠ΅Π»ΡΠ½ΡΠΌ ΡΡΠ»ΠΎΠ²ΠΈΠ΅ΠΌ Π½Π΅ΠΈΠ·ΠΎΡΠ΅ΡΠΌΠΈΡΠ΅ΡΠΊΠΎΠ³ΠΎ ΠΎΡΠΆΠΈΠ³Π° ΡΠ²Π»ΡΠ΅ΡΡΡ Π΄ΠΎΡΡΠ°ΡΠΎΡΠ½ΠΎ ΠΌΠ΅Π΄Π»Π΅Π½Π½ΠΎΠ΅ ΠΎΡ Π»Π°ΠΆΠ΄Π΅Π½ΠΈΠ΅, ΡΠΎΠ³Π΄Π° ΠΊΠ°ΠΊ ΠΏΡΠΈ ΠΈΠ·ΠΎΡΠ΅ΡΠΌΠΈΡΠ΅ΡΠΊΠΎΠΌ ΠΎΡΠΆΠΈΠ³Π΅ ΡΡΠΎ ΡΡΠ»ΠΎΠ²ΠΈΠ΅ Π½Π΅ΠΎΠ±ΡΠ·Π°ΡΠ΅Π»ΡΠ½ΠΎ.
ΠΠ°ΠΏΡΠΎΡΠΈΠ², Π²Β ΡΡΠ΄Π΅ ΡΠ»ΡΡΠ°Π΅Π² ΡΠ΅ΠΊΠΎΠΌΠ΅Π½Π΄ΠΎΠ²Π°Π½ΠΎ ΠΌΠ°ΠΊΡΠΈΠΌΠ°Π»ΡΠ½ΠΎ Π±ΡΡΡΡΠΎΠ΅ ΠΎΡ Π»Π°ΠΆΠ΄Π΅Π½ΠΈΠ΅ ΠΌΠ΅ΡΠ°Π»Π»Π° Π΄ΠΎΒ ΡΠ΅ΠΌΠΏΠ΅ΡΠ°ΡΡΡΡ ΠΈΠ·ΠΎΡΠ΅ΡΠΌΠΈΡΠ΅ΡΠΊΠΎΠΉ Π²ΡΠ΄Π΅ΡΠΆΠΊΠΈ (Π½Π°ΠΏΡΠΈΠΌΠ΅Ρ, ΡΠ°ΠΊΠΎΠΉ Π²ΠΈΠ΄ ΠΎΡΠΆΠΈΠ³Π°, ΠΊΠ°ΠΊ ΠΏΠ°ΡΠ΅Π½ΡΠΈΡΠΎΠ²Π°Π½ΠΈΠ΅, ΠΏΡΠ΅Π΄ΡΡΠΌΠ°ΡΡΠΈΠ²Π°Π΅Ρ ΠΌΠ°ΠΊΡΠΈΠΌΠ°Π»ΡΠ½ΠΎ Π±ΡΡΡΡΠΎΠ΅ ΠΎΡ Π»Π°ΠΆΠ΄Π΅Π½ΠΈΠ΅ Π΄ΠΎΒ ΡΠ΅ΠΌΠΏΠ΅ΡΠ°ΡΡΡΡ, ΠΏΡΠΈ ΠΊΠΎΡΠΎΡΠΎΠΉ ΡΠΊΠΎΡΠΎΡΡΡ ΠΏΠΎΠ»ΠΈΠΌΠΎΡΡΠ½ΠΎΠ³ΠΎ ΠΏΡΠ΅Π²ΡΠ°ΡΠ΅Π½ΠΈΡ ΠΌΠ°ΠΊΡΠΈΠΌΠ°Π»ΡΠ½Π°, ΡΒ ΠΏΠΎΡΠ»Π΅Π΄ΡΡΡΠ΅ΠΉ ΠΈΠ·ΠΎΡΠ΅ΡΠΌΠΈΡΠ΅ΡΠΊΠΎΠΉ Π²ΡΠ΄Π΅ΡΠΆΠΊΠΎΠΉ ΠΏΡΠΈ Π΄Π°Π½Π½ΠΎΠΉ ΡΠ΅ΠΌΠΏΠ΅ΡΠ°ΡΡΡΠ΅).
Π Π°Π·Π½ΠΎΠ²ΠΈΠ΄Π½ΠΎΡΡΡΡ ΠΏΠΎΠ»Π½ΠΎΠ³ΠΎ Π½Π΅ΠΈΠ·ΠΎΡΠ΅ΡΠΌΠΈΡΠ΅ΡΠΊΠΎΠ³ΠΎ ΠΎΡΠΆΠΈΠ³Π°Β II ΡΠΎΠ΄Π° ΡΠ²Π»ΡΠ΅ΡΡΡ Π½ΠΎΡΠΌΠ°Π»ΠΈΠ·Π°ΡΠΈΡ (ΠΎΡ
Π»Π°ΠΆΠ΄Π΅Π½ΠΈΠ΅ Π½Π°Β ΡΠΏΠΎΠΊΠΎΠΉΠ½ΠΎΠΌ Π²ΠΎΠ·Π΄ΡΡ
Π΅). ΠΒ ΠΠΠ Β«Π’Π΅Ρ
Π½ΠΎΠΏΠ°ΡΠΊ ΠΠΌΠΏΡΠ»ΡΡΒ» Π΄Π»Ρ ΠΎΡΠ²Π΅ΡΡΡΠ²Π΅Π½Π½ΡΡ
ΠΈΠ·Π΄Π΅Π»ΠΈΠΉ ΠΈΠ·Β Π΄ΠΎΡΠ²ΡΠ΅ΠΊΡΠΎΠΈΠ΄Π½ΡΡ
ΡΡΠ°Π»Π΅ΠΉ Π²Β ΠΊΠ°ΡΠ΅ΡΡΠ²Π΅ ΠΏΡΠ΅Π΄Π²Π°ΡΠΈΡΠ΅Π»ΡΠ½ΠΎΠΉ ΡΠ΅ΡΠΌΠΎΠΎΠ±ΡΠ°Π±ΠΎΡΠΊΠΈ (ΠΏΠ΅ΡΠ΅Π΄ ΠΏΠΎΡΠ»Π΅Π΄ΡΡΡΠ΅ΠΉ Π·Π°ΠΊΠ°Π»ΠΊΠΎΠΉ) ΠΏΡΠΈΠΌΠ΅Π½ΡΠ΅ΡΡΡ ΠΏΡΠ΅ΠΈΠΌΡΡΠ΅ΡΡΠ²Π΅Π½Π½ΠΎ ΠΈΠ·ΠΎΡΠ΅ΡΠΌΠΈΡΠ΅ΡΠΊΠΈΠΉ ΠΎΡΠΆΠΈΠ³ (Π»ΠΈΠ±ΠΎ Π½ΠΎΡΠΌΠ°Π»ΠΈΠ·Π°ΡΠΈΡ ΡΒ ΠΏΠΎΡΠ»Π΅Π΄ΡΡΡΠΈΠΌ Π²ΡΡΠΎΠΊΠΈΠΌ ΠΎΡΠΏΡΡΠΊΠΎΠΌ, ΠΊΠΎΡΠΎΡΠ°Ρ ΠΏΡΠΈΠ²ΠΎΠ΄ΠΈΡ ΠΊΒ ΠΏΠΎΠ»ΡΡΠ΅Π½ΠΈΡ ΠΏΠΎΡΡΠΈ ΡΠ°ΠΊΠΎΠΉΒ ΠΆΠ΅ ΡΡΡΡΠΊΡΡΡΡ), Π°Β Π΄Π»Ρ ΠΎΡΠ²Π΅ΡΡΡΠ²Π΅Π½Π½ΡΡ
ΠΈΠ·Π΄Π΅Π»ΠΈΠΉ ΠΈΠ·Β Π·Π°ΡΠ²ΡΠ΅ΠΊΡΠΎΠΈΠ΄Π½ΡΡ
ΡΡΠ°Π»Π΅ΠΉΒ β ΡΡΠ΅ΡΠΎΠΈΠ΄ΠΈΠ·ΠΈΡΡΡΡΠΈΠΉ ΠΎΡΠΆΠΈΠ³.
ΠΠ»Ρ ΠΌΠ΅Π½Π΅Π΅ ΠΎΡΠ²Π΅ΡΡΡΠ²Π΅Π½Π½ΡΡ ΠΈΠ·Π΄Π΅Π»ΠΈΠΉ ΠΈΠ·Β Π΄ΠΎΡΠ²ΡΠ΅ΠΊΡΠΎΠΈΠ΄Π½ΡΡ ΡΡΠ°Π»Π΅ΠΉ ΠΏΡΠΈΠΌΠ΅Π½ΡΠ΅ΡΡΡ ΠΏΡΠ΅ΠΈΠΌΡΡΠ΅ΡΡΠ²Π΅Π½Π½ΠΎ Π½Π΅ΠΈΠ·ΠΎΡΠ΅ΡΠΌΠΈΡΠ΅ΡΠΊΠΈΠΉ ΠΎΡΠΆΠΈΠ³ (ΠΏΡΠ΅ΠΈΠΌΡΡΠ΅ΡΡΠ²Π΅Π½Π½ΠΎ ΡΒ ΡΠ΅Π»ΡΡ ΡΠ»ΡΡΡΠ΅Π½ΠΈΡ ΠΎΠ±ΡΠ°Π±Π°ΡΡΠ²Π°Π΅ΠΌΠΎΡΡΠΈ ΠΏΡΠΈ ΠΏΠΎΡΠ»Π΅Π΄ΡΡΡΠ΅ΠΉ ΠΌΠ΅Ρ Π°Π½ΠΈΡΠ΅ΡΠΊΠΎΠΉ ΠΎΠ±ΡΠ°Π±ΠΎΡΠΊΠ΅).
ΠΡΠΎΠ±Π΅Π½Π½ΠΎΡΡΠΈ Π·Π°ΠΊΠ°Π»ΠΊΠΈ ΡΒ ΠΏΠΎΠ»ΠΈΠΌΠΎΡΡΠ½ΡΠΌ ΠΏΡΠ΅Π²ΡΠ°ΡΠ΅Π½ΠΈΠ΅ΠΌ
ΠΠ°ΠΊΠ°Π»ΠΊΠ° ΡΒ ΠΏΠΎΠ»ΠΈΠΌΠΎΡΡΠ½ΡΠΌ ΠΏΡΠ΅Π²ΡΠ°ΡΠ΅Π½ΠΈΠ΅ΠΌΒ β Π½Π°Π³ΡΠ΅Π² Π²ΡΡΠ΅ ΡΠ΅ΠΌΠΏΠ΅ΡΠ°ΡΡΡΡ ΠΏΠΎΠ»ΠΈΒ¬ΠΌΠΎΡΡΠ½ΠΎΠ³ΠΎ ΠΏΡΠ΅Π²ΡΠ°ΡΠ΅Π½ΠΈΡ ΡΒ ΠΏΠΎΡΠ»Π΅Π΄ΡΡΡΠΈΠΌ Π΄ΠΎΡΡΠ°ΡΠΎΡΠ½ΠΎ Π±ΡΡΡΡΡΠΌ ΠΎΡ Π»Π°ΠΆΠ΄Π΅Π½ΠΈΠ΅ΠΌ Π΄Π»Ρ ΠΏΠΎΠ»ΡΡΠ΅Π½ΠΈΡ ΡΡΡΡΠΊΡΡΡΠ½ΠΎ-Π½Π΅ΡΡΡΠΎΠΉΡΠΈΠ²ΠΎΠ³ΠΎ ΡΠΎΡΡΠΎΡΠ½ΠΈΡ (Π²Β ΡΡΠ΄Π΅ ΡΠ»ΡΡΠ°Π΅Π²Β β ΡΠΈΠΊΡΠ°ΡΠΈΠΈ ΡΡΡΠΎΠΉΡΠΈΠ²ΠΎΠ³ΠΎ Π²ΡΡΠΎΠΊΠΎΡΠ΅ΠΌΠΏΠ΅ΡΠ°ΡΡΡΠ½ΠΎΠ³ΠΎ ΡΠΎΡΡΠΎΡΠ½ΠΈΡ).
ΠΠ°ΠΊΠ°Π»ΠΊΠ° ΡΒ ΠΏΠΎΠ»ΠΈΠΌΠΎΡΡΠ½ΡΠΌ ΠΏΡΠ΅Π²ΡΠ°ΡΠ΅Π½ΠΈΠ΅ΠΌ ΠΏΡΠΈΠΌΠ΅Π½ΡΠ΅ΡΡΡ Π΄Π»Ρ ΠΏΠΎΠ΄Π°Π²Π»ΡΡΡΠ΅Π³ΠΎ Π±ΠΎΠ»ΡΡΠΈΠ½ΡΡΠ²Π° ΠΌΠ°ΡΠΎΠΊ ΡΡΠ°Π»ΠΈ. ΠΒ ΡΠ΅Π·ΡΠ»ΡΡΠ°ΡΠ΅ Π·Π°ΠΊΠ°Π»ΠΊΠΈ ΠΏΡΠΎΠΈΡΡ ΠΎΠ΄ΡΡ Ρ.Π½. ΠΌΠ°ΡΡΠ΅Π½ΡΠΈΡΠ½ΠΎΠ΅ ΠΈ/ΠΈΠ»ΠΈ Π±Π΅ΠΉΠ½ΠΈΡΠ½ΠΎΠ΅ ΠΏΡΠ΅Π²ΡΠ°ΡΠ΅Π½ΠΈΡ.
ΠΠ°ΡΡΠ΅Π½ΡΠΈΡΠ½ΠΎΠ΅ ΠΏΡΠ΅Π²ΡΠ°ΡΠ΅Π½ΠΈΠ΅ (ΠΠ)Β β ΠΏΠΎΠ»ΠΈΠΌΠΎΡΡΠ½ΠΎΠ΅ ΠΏΡΠ΅Π²ΡΠ°ΡΠ΅Π½ΠΈΠ΅, ΠΏΡΠΈ ΠΊΠΎΡΠΎΡΠΎΠΌ ΡΡΡΡΠΊΡΡΡΠ½ΡΠΉ ΠΏΠ΅ΡΠ΅Ρ
ΠΎΠ΄ Π²ΡΡΠΎΠΊΠΎΡΠ΅ΠΌΠΏΠ΅ΡΠ°ΡΡΡΠ½ΠΎΠΉ ΡΠ°Π·Ρ ΡΒ Π³ΡΠ°Π½Π΅ΡΠ΅Π½ΡΡΠΈΡΠΎΠ²Π°Π½Π½ΠΎΠΉ ΠΊΡΠ±ΠΈΡΠ΅ΡΠΊΠΎΠΉ (ΠΠ¦Π) ΡΠ΅ΡΠ΅ΡΠΊΠΎΠΉ (Π°ΡΡΡΠ΅Π½ΠΈΡΠ°) Π²Β Π½ΠΈΠ·ΠΊΠΎΡΠ΅ΠΌΠΏΠ΅ΡΠ°ΡΡΡΠ½ΡΡ ΡΠ°Π·Ρ ΡΒ ΠΎΠ±ΡΠ΅ΠΌΠ½ΠΎΡΠ΅Π½ΡΡΠΈΡΠΎΠ²Π°Π½Π½ΠΎΠΉ ΠΊΡΠ±ΠΈΡΠ΅ΡΠΊΠΎΠΉ (ΠΠ¦Π) ΡΠ΅ΡΡΡΠΊΠΎΠΉ (ΠΌΠ°ΡΡΠ΅Π½ΡΠΈΡ) ΠΏΡΠΎΠΈΡΡ
ΠΎΠ΄ΠΈΡ ΠΏΡΡΡΠΌ ΠΈΡ
Β ΡΠΏΠΎΡΡΠ΄ΠΎΡΠ΅Π½Π½ΠΎΠ³ΠΎ ΠΏΠ΅ΡΠ΅ΠΌΠ΅ΡΠ΅Π½ΠΈΡ, ΠΏΡΠΈΡΠ΅ΠΌ ΠΎΡΠ½ΠΎΡΠΈΡΠ΅Π»ΡΠ½ΡΠ΅ ΡΠΌΠ΅ΡΠ΅Π½ΠΈΡ ΡΠΎΡΠ΅Π΄Π½ΠΈΡ
Π°ΡΠΎΠΌΠΎΠ² ΠΌΠ°Π»Ρ ΠΏΠΎΒ ΡΡΠ°Π²Π½Π΅Π½ΠΈΡ ΡΒ ΠΌΠ΅ΠΆΠ°ΡΠΎΠΌΠ½ΡΠΌ ΡΠ°ΡΡΡΠΎΡΠ½ΠΈΠ΅ΠΌ.
ΠΠ°ΡΡΠ΅Π½ΡΠΈΡΠ½ΠΎΠ΅ ΠΏΡΠ΅Π²ΡΠ°ΡΠ΅Π½ΠΈΠ΅ ΠΏΡΠΎΡΠ΅ΠΊΠ°Π΅Ρ Π²Β ΠΎΠΏΡΠ΅Π΄Π΅Π»ΡΠ½Π½ΠΎΠΌ ΠΈΠ½ΡΠ΅ΡΠ²Π°Π»Π΅ ΡΠ΅ΠΌΠΏΠ΅ΡΠ°ΡΡΡ, Π·Π°Π²ΠΈΡΡΡΠ΅ΠΌ ΠΏΡΠ΅ΠΈΠΌΡΡΠ΅ΡΡΠ²Π΅Π½Π½ΠΎ ΠΎΡΒ ΡΠΎΡΡΠ°Π²Π° ΡΡΠ°Π»ΠΈ ΠΈΠ»ΠΈ ΡΠΏΠ»Π°Π²Π° (ΡΠ΅ΠΌΠΏΠ΅ΡΠ°ΡΡΡΠ° Π½Π°ΡΠ°Π»Π° ΠΌΠ°ΡΡΠ΅Π½ΡΠΈΡΠ½ΠΎΠ³ΠΎ ΠΏΡΠ΅Π²ΡΠ°ΡΠ΅Π½ΠΈΡ ΠΎΠ±ΠΎΠ·Π½Π°ΡΠ°Π΅ΡΡΡ ΠΊΠ°ΠΊΒ ΠΠ, Π°Β ΡΠ΅ΠΌΠΏΠ΅ΡΠ°ΡΡΡΠ° ΠΊΠΎΠ½ΡΠ° ΠΌΠ°ΡΡΠ΅Π½ΡΠΈΡΠ½ΠΎΠ³ΠΎ ΠΏΡΠ΅Π²ΡΠ°ΡΠ΅Π½ΠΈΡΒ β ΠΊΠ°ΠΊ ΠΠ).
ΠΠ΅ΠΉΠ½ΠΈΡΠ½ΠΎΠ΅ (ΠΏΡΠΎΠΌΠ΅ΠΆΡΡΠΎΡΠ½ΠΎΠ΅) ΠΏΡΠ΅Π²ΡΠ°ΡΠ΅Π½ΠΈΠ΅ (ΠΠ)Β β ΠΏΠΎΠ»ΠΈΠΌΠΎΡΡΠ½ΠΎΠ΅ ΠΏΡΠ΅Π²ΡΠ°ΡΠ΅Π½ΠΈΠ΅, ΠΏΡΠΎΡΠ΅ΠΊΠ°ΡΡΠ΅Π΅ Π²ΡΡΠ΅ ΡΠ΅ΠΌΠΏΠ΅ΡΠ°ΡΡΡΡ Π½Π°ΡΠ°Π»Π° ΠΌΠ°ΡΡΠ΅Π½ΡΠΈΡΠ½ΠΎΠ³ΠΎ ΠΏΡΠ΅Π²ΡΠ°ΡΠ΅Π½ΠΈΡΒ ΠΠ, ΠΏΡΠΈ ΠΊΠΎΡΠΎΡΠΎΠΌ ΠΈΠ·ΠΌΠ΅Π½Π΅Π½ΠΈΠ΅ Π²Π·Π°ΠΈΠΌΠ½ΠΎΠ³ΠΎ ΡΠ°ΡΠΏΠΎΠ»ΠΎΠΆΠ΅Π½ΠΈΡ Π°ΡΠΎΠΌΠΎΠ² ΠΊΡΠΈΡΡΠ°Π»Π»Π° ΠΈΠ·Β ΠΠ¦Π-ΡΠ°Π·Ρ Π²Β ΠΠ¦Π-ΡΠ°Π·Ρ (Π±Π΅ΠΉΠ½ΠΈΡ) ΠΏΡΠΎΠΈΡΡ ΠΎΠ΄ΠΈΡ ΠΏΠΎΡΡΠ΅Π΄ΡΡΠ²ΠΎΠΌ ΠΏΡΠ΅ΠΎΠ±ΡΠ°Π·ΠΎΠ²Π°Π½ΠΈΡ ΡΠ΄Π²ΠΈΠ³Π°.
ΠΠ΅ΠΉΠ½ΠΈΡ, ΠΏΡΠΈ ΡΠΎΠΏΠΎΡΡΠ°Π²ΠΈΠΌΡΡ ΡΒ ΠΌΠ°ΡΡΠ΅Π½ΡΠΈΡΠΎΠΌ ΡΠ²Π΅ΡΠ΄ΠΎΡΡΠΈ ΠΈΒ ΠΏΡΠΎΡΠ½ΠΎΡΡΠΈ, ΠΎΠ±Π»Π°Π΄Π°Π΅Ρ Π³ΠΎΡΠ°Π·Π΄ΠΎ Π±ΠΎΠ»Π΅Π΅ Π²ΡΡΠΎΠΊΠΎΠΉ ΡΠ΄Π°ΡΠ½ΠΎΠΉ Π²ΡΠ·ΠΊΠΎΡΡΡΡ, ΠΏΠΎΡΡΠΎΠΌΡ Π΄Π»Ρ ΠΌΠ½ΠΎΠ³ΠΈΡ ΠΈΠ·Π΄Π΅Π»ΠΈΠΉ, Π³Π΄Π΅ ΡΡΠ΅Π±ΡΠ΅ΡΡΡ ΡΠΎΡΠ΅ΡΠ°Π½ΠΈΠ΅ Π²ΡΡΠΎΠΊΠΈΡ ΠΏΡΠΎΡΠ½ΠΎΡΡΠΈ ΠΈΒ ΠΏΠ»Π°ΡΡΠΈΡΠ½ΠΎΡΡΠΈ, ΠΏΠΎΠ»ΡΡΠ΅Π½ΠΈΠ΅ Π΄Π°Π½Π½ΠΎΠΉ ΡΡΡΡΠΊΡΡΡΡ ΡΠ²Π»ΡΠ΅ΡΡΡ ΠΏΡΠ΅Π΄ΠΏΠΎΡΡΠΈΡΠ΅Π»ΡΠ½ΡΠΌ.
ΠΠΎΒ Π½Π΅Π΄Π°Π²Π½Π΅Π³ΠΎ Π²ΡΠ΅ΠΌΠ΅Π½ΠΈ ΠΎΒ ΠΌΠ°ΡΡΠ΅Π½ΡΠΈΡΠ½ΠΎΠΌ ΠΈΒ Π±Π΅ΠΉΠ½ΠΈΡΠ½ΠΎΠΌ ΠΏΡΠ΅Π²ΡΠ°ΡΠ΅Π½ΠΈΡΡ
Π³ΠΎΠ²ΠΎΡΠΈΠ»ΠΈ ΡΠΎΠ»ΡΠΊΠΎ ΠΏΡΠΈΠΌΠ΅Π½ΠΈΡΠ΅Π»ΡΠ½ΠΎ ΠΊΒ ΡΡΠ°Π»ΡΠΌ, ΠΎΠ΄Π½Π°ΠΊΠΎ Π²Β ΠΏΠΎΡΠ»Π΅Π΄Π½ΠΈΠ΅ Π΄Π΅ΡΡΡΠΈΠ»Π΅ΡΠΈΡ ΠΎΠ±Π½Π°ΡΡΠΆΠ΅Π½ΠΎ ΡΡΡΠ΅ΡΡΠ²ΠΎΠ²Π°Π½ΠΈΠ΅ ΠΌΠ°ΡΡΠ΅Π½ΡΠΈΡΠ½ΠΎΠ³ΠΎ ΠΏΡΠ΅Π²ΡΠ°ΡΠ΅Π½ΠΈΡ Π²Β Π½Π΅ΠΊΠΎΡΠΎΡΡΡ
ΡΠΏΠ»Π°Π²Π°Ρ
Π½Π°Β ΠΎΡΠ½ΠΎΠ²Π΅ ΡΠΈΡΠ°Π½Π°, Π½ΠΈΠΊΠ΅Π»Ρ ΠΈΒ Π΄Ρ. ΡΠ²Π΅ΡΠ½ΡΡ
ΠΌΠ΅ΡΠ°Π»Π»ΠΎΠ².
ΠΠΈΠ΄Ρ Π·Π°ΠΊΠ°Π»ΠΊΠΈ ΡΒ ΠΏΠΎΠ»ΠΈΠΌΠΎΡΡΠ½ΡΠΌ ΠΏΡΠ΅Π²ΡΠ°ΡΠ΅Π½ΠΈΠ΅ΠΌ
ΠΒ ΠΏΡΠΎΠΌΡΡΠ»Π΅Π½Π½ΠΎΡΡΠΈ ΠΏΡΠΈΠΌΠ΅Π½ΡΡΡΡΡ ΡΠ»Π΅Π΄ΡΡΡΠΈΠ΅ Π²ΠΈΠ΄Ρ Π·Π°ΠΊΠ°Π»ΠΊΠΈ ΡΒ ΠΏΠΎΠ»ΠΈΠΌΠΎΡΡΠ½ΡΠΌ ΠΏΡΠ΅Π²ΡΠ°ΡΠ΅Π½ΠΈΠ΅ΠΌ:
- ΠΠ°ΠΊΠ°Π»ΠΊΠ° ΡΒ Π½Π΅ΠΏΡΠ΅ΡΡΠ²Π½ΡΠΌ ΠΎΡ
Π»Π°ΠΆΠ΄Π΅Π½ΠΈΠ΅ΠΌ Π²Β ΠΎΠ΄Π½ΠΎΠΉ ΡΡΠ΅Π΄Π΅ (Π²ΠΎΠ΄Π΅, Π²ΠΎΠ΄Π½ΡΡ
ΡΠ°ΡΡΠ²ΠΎΡΠ°Ρ
ΠΏΠΎΠ»ΠΈΠΌΠ΅ΡΠΎΠ² Π»ΠΈΠ±ΠΎ Π½Π΅ΠΎΡΠ³Π°Π½ΠΈΡΠ΅ΡΠΊΠΈΡ
ΡΠΎΠ»Π΅ΠΉ, Π²Β ΠΌΠ°ΡΠ»Π΅).
ΠΡΠΎ ΡΠ°ΠΌΡΠΉ ΠΏΡΠΎΡΡΠΎΠΉ ΠΈΒ ΡΠ°ΡΠΏΡΠΎΡΡΡΠ°Π½ΡΠ½Π½ΡΠΉ Π²ΠΈΠ΄ Π·Π°ΠΊΠ°Π»ΠΊΠΈ, Π½ΠΎΒ ΠΎΠ½Β ΡΠ°ΡΡΠΎ ΡΠΎΠΏΡΡΠΆΠ΅Π½ Π»ΠΈΠ±ΠΎ ΡΒ ΠΏΠΎΠ»ΡΡΠ΅Π½ΠΈΠ΅ΠΌ ΠΏΠΎΠ½ΠΈΠΆΠ΅Π½Π½ΡΡ ΠΌΠ΅Ρ Π°Π½ΠΈΡΠ΅ΡΠΊΠΈΡ ΡΠ²ΠΎΠΉΡΡΠ² (ΠΊΠ°ΠΊ ΠΏΡΠ°Π²ΠΈΠ»ΠΎ, ΠΏΡΠΈ Π·Π°ΠΊΠ°Π»ΠΊΠ΅ Π²Β ΠΌΠ°ΡΠ»Π΅ ΠΈΠ»ΠΈ ΡΠ°ΡΡΠ²ΠΎΡΠ°Ρ ΠΏΠΎΠ»ΠΈΠΌΠ΅ΡΠΎΠ²), Π»ΠΈΠ±ΠΎ ΡΒ ΠΏΠΎΠ²ΡΡΠ΅Π½Π½ΡΠΌΠΈ Π·Π½Π°ΡΠ΅Π½ΠΈΡΠΌΠΈ Π·Π°ΠΊΠ°Π»ΠΎΡΠ½ΡΡ Π΄Π΅ΡΠΎΡΠΌΠ°ΡΠΈΠΉ ΠΈΒ ΡΠΈΡΠΊΠΎΠΌ ΠΎΠ±ΡΠ°Π·ΠΎΠ²Π°Π½ΠΈΡ Π·Π°ΠΊΠ°Π»ΠΎΡΠ½ΡΡ ΡΡΠ΅ΡΠΈΠ½ (ΠΊΠ°ΠΊ ΠΏΡΠ°Π²ΠΈΠ»ΠΎ, ΠΏΡΠΈ Π·Π°ΠΊΠ°Π»ΠΊΠ΅ Π²Β Π²ΠΎΠ΄Π΅ ΠΈΒ Π²ΠΎΠ΄Π½ΡΡ ΡΠ°ΡΡΠ²ΠΎΡΠ°Ρ Π½Π΅ΠΎΡΠ³Π°Π½ΠΈΡΠ΅ΡΠΊΠΈΡ ΡΠΎΠ»Π΅ΠΉ).ΠΠΎΒ ΡΡΠΎΠΉ ΠΏΡΠΈΡΠΈΠ½Π΅ Π²Β ΠΠΠ Β«Π’Π΅Ρ Π½ΠΎΠΏΠ°ΡΠΊ ΠΠΌΠΏΡΠ»ΡΡΒ», ΠΊΠ°ΠΊ ΠΏΡΠ°Π²ΠΈΠ»ΠΎ, ΠΏΡΠΈΠΌΠ΅Π½ΡΠ΅ΡΡΡ ΡΠΎΠ»ΡΠΊΠΎ Π½Π΅ΠΏΡΠ΅ΡΡΠ²Π½Π°Ρ Π·Π°ΠΊΠ°Π»ΠΊΠ° Π²Β ΠΌΠ°ΡΠ»Π΅ ΠΈΒ ΡΠ΅ΠΆΠ΅Β β Π²Β ΡΠ°ΡΡΠ²ΠΎΡΠ°Ρ ΠΏΠΎΠ»ΠΈΠΌΠ΅ΡΠΎΠ², ΠΏΡΠΈΡΠ΅ΠΌ ΠΏΡΠ΅ΠΈΠΌΡΡΠ΅ΡΡΠ²Π΅Π½Π½ΠΎ Π΄Π»Ρ ΠΈΠ·Π΄Π΅Π»ΠΈΠΉ Π½Π΅Π±ΠΎΠ»ΡΡΠΎΠ³ΠΎ ΡΠ΅ΡΠ΅Π½ΠΈΡ.
- ΠΡΠ΅ΡΡΠ²ΠΈΡΡΠ°Ρ Π·Π°ΠΊΠ°Π»ΠΊΠ° (Π·Π°ΠΊΠ°Π»ΠΊΠ° Π²Β Π΄Π²ΡΡ
ΡΡΠ΅Π΄Π°Ρ
) ΡΒ Π±ΡΡΡΡΡΠΌ ΠΎΡ
Π»Π°ΠΆΠ΄Π΅Π½ΠΈΠ΅ΠΌ (Π²Β Π²ΠΎΠ΄Π΅) Π΄ΠΎΒ ΡΠ΅ΠΌΠΏΠ΅ΡΠ°ΡΡΡ Π²ΡΡΠ΅Β ΠΠ ΠΈΒ ΠΏΠΎΡΠ»Π΅Π΄ΡΡΡΠΈΠΌ Π±ΠΎΠ»Π΅Π΅ ΠΌΠ΅Π΄Π»Π΅Π½Π½ΡΠΌ ΠΎΡ
Π»Π°ΠΆΠ΄Π΅Π½ΠΈΠ΅ΠΌ (Π²Β ΠΌΠ°ΡΠ»Π΅ ΠΈΠ»ΠΈ Π½Π°Β Π²ΠΎΠ·Π΄ΡΡ
Π΅) Π²Β ΠΈΠ½ΡΠ΅ΡΠ²Π°Π»Π΅ ΠΠΒ β ΠΠ.
ΠΠ»Π°Π²Π½ΡΡ ΡΠ»ΠΎΠΆΠ½ΠΎΡΡΡ ΠΏΡΠ΅Π΄ΡΡΠ°Π²Π»ΡΠ΅Ρ ΡΠΎΠ±ΠΎΠΉ ΡΠΎΡΠ½ΡΠΉ ΠΏΠΎΠ΄Π±ΠΎΡ Π²ΡΠ΅ΠΌΠ΅Π½ΠΈ Π²ΡΠ΄Π΅ΡΠΆΠΊΠΈ Π²Β ΠΊΠ°ΠΆΠ΄ΠΎΠΉ ΠΈΠ·Β ΡΡΠ΅Π΄ (ΠΎΡΠΎΠ±Π΅Π½Π½ΠΎ Π΄Π»Ρ ΠΈΠ·Π΄Π΅Π»ΠΈΠΉ ΠΏΠ΅ΡΠ΅ΠΌΠ΅Π½Π½ΠΎΠ³ΠΎ ΡΠ΅ΡΠ΅Π½ΠΈΡ).
ΠΠΎΒ ΡΡΠΎΠΉ ΠΏΡΠΈΡΠΈΠ½Π΅ Π²Β ΠΠΠ Β«Π’Π΅Ρ Π½ΠΎΠΏΠ°ΡΠΊ ΠΠΌΠΏΡΠ»ΡΡΒ» ΠΏΡΠ΅ΡΡΠ²ΠΈΡΡΠ°Ρ Π·Π°ΠΊΠ°Π»ΠΊΠ° (ΡΠ΅ΡΠ΅Π· Π²ΠΎΠ΄Ρ Π²Β ΠΌΠ°ΡΠ»ΠΎ) ΠΊΠ°ΠΊ ΠΏΡΠ°Π²ΠΈΠ»ΠΎ, ΠΏΡΠΈΠΌΠ΅Π½ΡΠ΅ΡΡΡ ΡΠΎΠ»ΡΠΊΠΎ Π΄Π»Ρ ΠΈΠ·Π΄Π΅Π»ΠΈΠΉ ΡΡΠ°Π²Π½ΠΈΡΠ΅Π»ΡΠ½ΠΎ ΠΏΡΠΎΡΡΠΎΠΉ ΡΠΎΡΠΌΡ, ΠΏΡΠΈΡΡΠΌ Π²ΡΠ΅ΠΌΡ Π²ΡΠ΄Π΅ΡΠΆΠΊΠΈ Π²Β ΠΊΠ°ΠΆΠ΄ΠΎΠΉ ΠΈΠ·Β ΡΡΠ΅Π΄ Π²ΡΡΡΠΈΡΡΠ²Π°Π΅ΡΡΡ Π΄Π»Ρ ΠΊΠ°ΠΆΠ΄ΠΎΠ³ΠΎ ΠΈΠ·Π΄Π΅Π»ΠΈΡ ΠΈΠ½Π΄ΠΈΠ²ΠΈΠ΄ΡΠ°Π»ΡΠ½ΠΎ ΠΈΒ ΠΈΡΠΏΠΎΠ»ΡΠ·ΠΎΠ²Π°Π½ΠΈΠ΅ΠΌ ΡΠΏΠ΅ΡΠΈΠ°Π»ΠΈΠ·ΠΈΡΠΎΠ²Π°Π½Π½ΠΎΠΉ ΠΏΡΠΎΠ³ΡΠ°ΠΌΠΌΡ. - ΠΠ°ΠΊΠ°Π»ΠΊΠ° ΡΒ ΡΠ°ΠΌΠΎΠΎΡΠΏΡΡΠΊΠΎΠΌ Π·Π°ΠΊΠ»ΡΡΠ°Π΅ΡΡΡ Π²Β ΡΠΎΠΌ, ΡΡΠΎ ΠΈΠ·Π΄Π΅Π»ΠΈΠ΅ ΠΏΠΎΠ³ΡΡΠΆΠ°Π΅ΡΡΡ Π²Β Π·Π°ΠΊΠ°Π»ΠΎΡΠ½ΡΡ ΡΡΠ΅Π΄Ρ Π½Π°Β ΠΎΠ³ΡΠ°Π½ΠΈΡΠ΅Π½Π½ΠΎΠ΅ Π²ΡΠ΅ΠΌΡ ΡΒ ΡΠ°ΠΊΠΈΠΌ ΡΠ°ΡΡΡΡΠΎΠΌ, ΡΡΠΎΠ±Ρ ΡΠ΅ΠΌΠΏΠ΅ΡΠ°ΡΡΡΠ° ΠΏΠΎΠ²Π΅ΡΡ
Π½ΠΎΡΡΠΈ Π±ΡΠ»Π° ΡΡΡΠ΅ΡΡΠ²Π΅Π½Π½ΠΎ Π½ΠΈΠΆΠ΅Β ΠΠ, Π°Β ΡΠ΅ΠΌΠΏΠ΅ΡΠ°ΡΡΡΠ° ΡΠ΅ΡΠ΄ΡΠ΅Π²ΠΈΠ½ΡΒ β Π²ΡΡΠ΅Β ΠΠ, Π·Π°Β ΡΡΡΡ ΡΠ΅Π³ΠΎ ΠΏΠΎΡΠ»Π΅ ΠΈΠ·Π²Π»Π΅ΡΠ΅Π½ΠΈΡ ΠΈΠ·Π΄Π΅Π»ΠΈΡ ΠΈΠ·Β Π·Π°ΠΊΠ°Π»ΠΎΡΠ½ΠΎΠ³ΠΎ Π±Π°ΠΊΠ° ΠΏΡΠΎΠΈΠ·ΠΎΡΠ»ΠΎ Π²ΡΡΠ°Π²Π½ΠΈΠ²Π°Π½ΠΈΠ΅ ΡΠ΅ΠΌΠΏΠ΅ΡΠ°ΡΡΡΡ ΠΏΠΎΒ ΡΠ΅ΡΠ΅Π½ΠΈΡ ΠΈΠ·Π΄Π΅Π»ΠΈΡ, ΠΏΡΠΈΠ²ΠΎΠ΄ΡΡΠ΅Π΅ ΠΊΒ ΡΠ°ΠΌΠΎΠΎΡΠΏΡΡΠΊΡ ΠΏΠΎΠ²Π΅ΡΡ
Π½ΠΎΡΡΠ½ΡΡ
ΡΠ»ΠΎΡΠ² ΠΈΠ·Π΄Π΅Π»ΠΈΡ.
ΠΠ°Π½Π½ΡΠΉ ΡΠΏΠΎΡΠΎΠ± Π·Π°ΠΊΠ°Π»ΠΊΠΈ ΡΠ΅Π·ΠΊΠΎ ΡΠ½ΠΈΠΆΠ°Π΅Ρ Π·Π°ΠΊΠ°Π»ΠΎΡΠ½ΡΠ΅ Π½Π°ΠΏΡΡΠΆΠ΅Π½ΠΈΡ ΠΈΒ ΡΠ΅ΠΌ ΡΠ°ΠΌΡΠΌ ΡΠΌΠ΅Π½ΡΡΠ°Π΅Ρ Π·Π½Π°ΡΠ΅Π½ΠΈΡ Π·Π°ΠΊΠ°Π»ΠΎΡΠ½ΡΡ Π΄Π΅ΡΠΎΡΠΌΠ°ΡΠΈΠΉ ΠΈΒ ΡΠΈΡΠΊ ΠΎΠ±ΡΠ°Π·ΠΎΠ²Π°Π½ΠΈΡ Π·Π°ΠΊΠ°Π»ΠΎΡΠ½ΡΡ ΡΡΠ΅ΡΠΈΠ½. ΠΠ»Π°Π²Π½ΡΡ ΡΠ»ΠΎΠΆΠ½ΠΎΡΡΡ ΠΏΡΠ΅Π΄ΡΡΠ°Π²Π»ΡΠ΅Ρ ΡΠΎΠ±ΠΎΠΉ ΡΠΎΡΠ½ΡΠΉ ΠΏΠΎΠ΄Π±ΠΎΡ Π²ΡΠ΅ΠΌΠ΅Π½ΠΈ Π²ΡΠ΄Π΅ΡΠΆΠΊΠΈ Π²Β ΠΊΠ°ΠΆΠ΄ΠΎΠΉ ΠΈΠ·Β ΡΡΠ΅Π΄ (ΠΎΡΠΎΠ±Π΅Π½Π½ΠΎ Π΄Π»Ρ ΠΈΠ·Π΄Π΅Π»ΠΈΠΉ ΠΏΠ΅ΡΠ΅ΠΌΠ΅Π½Π½ΠΎΠ³ΠΎ ΡΠ΅ΡΠ΅Π½ΠΈΡ).
ΠΠΎΒ ΡΡΠΎΠΉ ΠΏΡΠΈΡΠΈΠ½Π΅ Π²Β ΠΠΠ Β«Π’Π΅Ρ Π½ΠΎΠΏΠ°ΡΠΊ ΠΠΌΠΏΡΠ»ΡΡΒ» Π·Π°ΠΊΠ°Π»ΠΊΠ° ΡΒ ΡΠ°ΠΌΠΎΠΎΡΠΏΡΡΠΊΠΎΠΌ (ΡΒ ΠΎΡ Π»Π°ΠΆΠ΄Π΅Π½ΠΈΠ΅ΠΌ Π²Β ΡΠ°ΡΡΠ²ΠΎΡΠ΅ ΠΏΠΎΠ»ΠΈΠΌΠ΅ΡΠ°) ΠΊΠ°ΠΊ ΠΏΡΠ°Π²ΠΈΠ»ΠΎ, ΠΏΡΠΈΠΌΠ΅Π½ΡΠ΅ΡΡΡ ΡΠΎΠ»ΡΠΊΠΎ Π΄Π»Ρ ΠΈΠ·Π΄Π΅Π»ΠΈΠΉ ΡΡΠ°Π²Π½ΠΈΡΠ΅Π»ΡΠ½ΠΎ ΠΏΡΠΎΡΡΠΎΠΉ ΡΠΎΡΠΌΡ, ΠΏΡΠΈΡΡΠΌ Π²ΡΠ΅ΠΌΡ Π²ΡΠ΄Π΅ΡΠΆΠΊΠΈ Π²Β ΠΊΠ°ΠΆΠ΄ΠΎΠΉ ΠΈΠ·Β ΡΡΠ΅Π΄ Π²ΡΡΡΠΈΡΡΠ²Π°Π΅ΡΡΡ Π΄Π»Ρ ΠΊΠ°ΠΆΠ΄ΠΎΠ³ΠΎ ΠΈΠ·Π΄Π΅Π»ΠΈΡ ΠΈΠ½Π΄ΠΈΠ²ΠΈΠ΄ΡΠ°Π»ΡΠ½ΠΎ ΠΈΒ ΠΈΡΠΏΠΎΠ»ΡΠ·ΠΎΠ²Π°Π½ΠΈΠ΅ΠΌ ΡΠΏΠ΅ΡΠΈΠ°Π»ΠΈΠ·ΠΈΡΠΎΠ²Π°Π½Π½ΠΎΠΉ ΠΏΡΠΎΠ³ΡΠ°ΠΌΠΌΡ, Π°Β ΡΠ΅ΠΌΠΏΠ΅ΡΠ°ΡΡΡΠ° ΡΠ°ΠΌΠΎΠΎΡΠΏΡΡΠΊΠ° ΠΊΠΎΠ½ΡΡΠΎΠ»ΠΈΡΡΠ΅ΡΡΡ ΠΏΠΈΡΠΎΠΌΠ΅ΡΡΠΎΠΌ, ΠΈΒ Π²Β ΡΠ»ΡΡΠ°Π΅ ΠΏΡΠ΅Π²ΡΡΠ΅Π½ΠΈΡ Π·Π°Π΄Π°Π½Π½ΠΎΠΉ ΡΠ΅ΠΌΠΏΠ΅ΡΠ°ΡΡΡΡ ΠΈΠ·Π΄Π΅Π»ΠΈΠ΅ ΠΏΠΎΠ²ΡΠΎΡΠ½ΠΎ ΠΏΠΎΠ³ΡΡΠΆΠ°Π΅ΡΡΡ Π²Β Π·Π°ΠΊΠ°Π»ΠΎΡΠ½ΡΠΉ Π±Π°ΠΊ (ΠΏΡΠΈ ΡΡΠΎΠΌ Π·Π°ΠΊΠ°Π»ΠΊΠ° ΡΠ΅ΡΠ΅Π· Π²ΠΎΠ΄Ρ Π²Β ΠΌΠ°ΡΠ»ΠΎ ΠΏΡΠ΅ΠΈΠΌΡΡΠ΅ΡΡΠ²Π΅Π½Π½ΠΎ ΠΏΡΠΈΠΌΠ΅Π½ΡΠ΅ΡΡΡ Π΄Π»Ρ ΠΈΠ·Π΄Π΅Π»ΠΈΠΉ ΡΡΠ΅Π΄Π½Π΅Π³ΠΎ ΡΠ°Π·ΠΌΠ΅ΡΠ°, Π°Β Π·Π°ΠΊΠ°Π»ΠΊΠ° ΡΒ ΡΠ°ΠΌΠΎΠΎΡΠΏΡΡΠΊΠΎΠΌΒ β Π΄Π»Ρ ΠΊΡΡΠΏΠ½ΠΎΠ³Π°Π±Π°ΡΠΈΡΠ½ΡΡ ΠΈΠ·Π΄Π΅Π»ΠΈΠΉ). - ΠΠ°ΠΊΠ°Π»ΠΊΠ° ΠΊΡΠΏΠ°Π½ΠΈΠ΅ΠΌ ΠΎΡΠ»ΠΈΡΠ°Π΅ΡΡΡ ΠΎΡΒ Π·Π°ΠΊΠ°Π»ΠΊΠΈ ΡΒ ΡΠ°ΠΌΠΎΠΎΡΠΏΡΡΠΊΠΎΠΌ ΡΠ΅ΠΌ, ΡΡΠΎ ΠΈΠ·Π΄Π΅Π»ΠΈΠ΅ ΠΏΠΎΠ³ΡΡΠΆΠ°Π΅ΡΡΡ Π²Β Π·Π°ΠΊΠ°Π»ΠΎΡΠ½ΡΡ ΡΡΠ΅Π΄Ρ Π½Π°Β ΠΎΠ³ΡΠ°Π½ΠΈΡΠ΅Π½Π½ΠΎΠ΅ Π²ΡΠ΅ΠΌΡ ΠΈΒ Π·Π°ΡΠ΅ΠΌ Π²ΡΠ½ΠΎΡΠΈΡΡΡ Π½Π°Β Π²ΠΎΠ·Π΄ΡΡ
Π΄Π»Ρ Π²ΡΡΠ°Π²Π½ΠΈΠ²Π°Π½ΠΈΡ ΡΠ΅ΠΌΠΏΠ΅ΡΠ°ΡΡΡΡ ΠΏΠΎΒ ΡΠ΅ΡΠ΅Π½ΠΈΡ Π½Π΅Β ΠΎΠ΄ΠΈΠ½ ΡΠ°Π·, Π°Β Π½Π΅ΠΎΠ΄Π½ΠΎΠΊΡΠ°ΡΠ½ΠΎ. ΠΠ»Π°Π²Π½ΡΡ ΡΠ»ΠΎΠΆΠ½ΠΎΡΡΡ ΠΏΡΠ΅Π΄ΡΡΠ°Π²Π»ΡΠ΅Ρ ΡΠΎΠ±ΠΎΠΉ ΡΠΎΡΠ½ΡΠΉ ΠΏΠΎΠ΄Π±ΠΎΡ Π²ΡΠ΅ΠΌΠ΅Π½ΠΈ Π²ΡΠ΄Π΅ΡΠΆΠΊΠΈ Π²Β ΠΊΠ°ΠΆΠ΄ΠΎΠΉ ΠΈΠ·Β ΡΡΠ΅Π΄ (ΠΎΡΠΎΠ±Π΅Π½Π½ΠΎ Π΄Π»Ρ ΠΈΠ·Π΄Π΅Π»ΠΈΠΉ ΠΏΠ΅ΡΠ΅ΠΌΠ΅Π½Π½ΠΎΠ³ΠΎ ΡΠ΅ΡΠ΅Π½ΠΈΡ).
ΠΠΎΒ ΡΡΠΎΠΉ ΠΏΡΠΈΡΠΈΠ½Π΅ Π²Β ΠΠΠ Β«Π’Π΅Ρ Π½ΠΎΠΏΠ°ΡΠΊ ΠΠΌΠΏΡΠ»ΡΡΒ» Π·Π°ΠΊΠ°Π»ΠΊΠ° ΠΊΡΠΏΠ°Π½ΠΈΠ΅ΠΌ, ΠΏΡΠΈΠΌΠ΅Π½ΡΠ΅ΡΡΡ ΡΠΎΠ»ΡΠΊΠΎ Π΄Π»Ρ ΠΊΡΡΠΏΠ½ΠΎΠ³Π°Π±Π°ΡΠΈΡΠ½ΡΡ ΠΈΒ ΠΎΡΠ²Π΅ΡΡΡΠ²Π΅Π½Π½ΡΡ ΠΈΠ·Π΄Π΅Π»ΠΈΠΉ, Π΄Π»Ρ ΠΊΠΎΡΠΎΡΡΡ ΠΎΡΠΎΠ±Π΅Π½Π½ΠΎ Π²Π΅Π»ΠΈΠΊ ΡΠΈΡΠΊ ΠΎΠ±ΡΠ°Π·ΠΎΠ²Π°Π½ΠΈΡ Π·Π°ΠΊΠ°Π»ΠΎΡΠ½ΡΡ ΡΡΠ΅ΡΠΈΠ½, ΠΏΡΠΈΡΡΠΌ ΠΊΠΎΠ½ΡΡΠΎΠ»Ρ ΡΠ΅ΠΌΠΏΠ΅ΡΠ°ΡΡΡΡ ΠΈΠ·Π΄Π΅Π»ΠΈΡ ΡΒ ΠΏΠΎΠΌΠΎΡΡΡ ΠΏΠΈΡΠΎΠΌΠ΅ΡΡΠ° ΠΏΡΠΎΠ²ΠΎΠ΄ΠΈΡΡΡ ΠΏΡΠΈ ΠΊΠ°ΠΆΠ΄ΠΎΠΌ Π²ΡΠ½ΠΈΠΌΠ°Π½ΠΈΠΈ ΠΈΠ·Π΄Π΅Π»ΠΈΠΈ ΠΈΠ·Β Π·Π°ΠΊΠ°Π»ΠΎΡΠ½ΠΎΠ³ΠΎ Π±Π°ΠΊΠ°.
- Π‘ΡΡΠΏΠ΅Π½ΡΠ°ΡΠ°Ρ Π·Π°ΠΊΠ°Π»ΠΊΠ° ΡΒ ΠΎΡ
Π»Π°ΠΆΠ΄Π΅Π½ΠΈΠ΅ΠΌ Π²Β Π³ΠΎΡΡΡΠ΅ΠΉ ΡΡΠ΅Π΄Π΅ ΡΒ ΡΠ΅ΠΌΠΏΠ΅ΡΠ°ΡΡΡΠΎΠΉ Π½Π΅ΠΌΠ½ΠΎΠ³ΠΎ Π²ΡΡΠ΅Β ΠΠ (ΠΊΠ°ΠΊ ΠΏΡΠ°Π²ΠΈΠ»ΠΎ, ΡΠ°ΡΠΏΠ»Π°Π²Π΅ ΡΠ΅Π»ΠΈΡΡΡ Π»ΠΈΠ±ΠΎ ΡΠ΅Π»ΠΎΡΠΈ) ΡΒ ΠΊΡΠ°ΡΠΊΠΎΠ²ΡΠ΅ΠΌΠ΅Π½Π½ΠΎΠΉ (Π²ΠΎΒ ΠΈΠ·Π±Π΅ΠΆΠ°Π½ΠΈΠ΅ Π±Π΅ΠΉΠ½ΠΈΡΠ½ΠΎΠ³ΠΎ ΠΏΡΠ΅Π²ΡΠ°ΡΠ΅Π½ΠΈΡ Π°ΡΡΡΠ΅Π½ΠΈΡΠ°) Π²ΡΠ΄Π΅ΡΠΆΠΊΠΎΠΉ Π΄Π»Ρ Π²ΡΡΠ°Π²Π½ΠΈΠ²Π°Π½ΠΈΡ ΡΠ΅ΠΌΠΏΠ΅ΡΠ°ΡΡΡΡ ΠΏΠΎΒ ΡΠ΅ΡΠ΅Π½ΠΈΡ ΠΈΒ ΠΏΠΎΡΠ»Π΅Π΄ΡΡΡΠΈΠΌ ΠΎΡ
Π»Π°ΠΆΠ΄Π΅Π½ΠΈΠ΅ΠΌ Π½Π°Β Π²ΠΎΠ·Π΄ΡΡ
Π΅.
ΠΠ°Π½Π½ΡΠΉ ΡΠΏΠΎΡΠΎΠ± Π·Π°ΠΊΠ°Π»ΠΊΠΈ ΠΎΠ±Π΅ΡΠΏΠ΅ΡΠΈΠ²Π°Π΅Ρ ΠΌΠΈΠ½ΠΈΠΌΠΈΠ·Π°ΡΠΈΡ Π·Π°ΠΊΠ°Π»ΠΎΡΠ½ΡΡ Π΄Π΅ΡΠΎΡΠΌΠ°ΡΠΈΠΉ ΠΈΒ ΡΠΌΠ΅Π½ΡΡΠ΅Π½ΠΈΠ΅ Π²Π½ΡΡΡΠ΅Π½Π½ΠΈΡ Π½Π°ΠΏΡΡΠΆΠ΅Π½ΠΈΠΉ ΠΏΠΎΡΡΠΈ Π΄ΠΎΒ Π½ΡΠ»Ρ, Π½ΠΎΒ ΠΏΡΠΈΠΌΠ΅Π½ΡΠ΅ΡΡΡ Π²Β ΠΠΠ Β«Π’Π΅Ρ Π½ΠΎΠΏΠ°ΡΠΊ ΠΠΌΠΏΡΠ»ΡΡΒ» ΡΠΎΠ»ΡΠΊΠΎ Π΄Π»Ρ ΠΈΠ·Π΄Π΅Π»ΠΈΠΉ Π½Π΅Π±ΠΎΠ»ΡΡΠΎΠ³ΠΎ ΡΠ°Π·ΠΌΠ΅ΡΠ° Π»ΠΈΠ±ΠΎ ΠΈΠ·Β ΡΡΠ°Π»Π΅ΠΉ Π²ΡΡΠΎΠΊΠΎΠΉ ΠΏΡΠΎΠΊΠ°Π»ΠΈΠ²Π°Π΅ΠΌΠΎΡΡΠΈ, ΠΏΠΎΡΠΊΠΎΠ»ΡΠΊΡ ΡΠΊΠΎΡΠΎΡΡΡ ΠΎΡ Π»Π°ΠΆΠ΄Π΅Π½ΠΈΡ Π²Β ΡΠ°ΡΠΏΠ»Π°Π²Π΅ ΡΠ΅Π»ΠΈΡΡΡ Π½Π΅Β Π²ΡΡΠ΅, ΡΠ΅ΠΌ Π²Β ΠΌΠ°ΡΠ»Π΅.
- ΠΠ·ΠΎΡΠ΅ΡΠΌΠΈΡΠ΅ΡΠΊΠ°Ρ Π·Π°ΠΊΠ°Π»ΠΊΠ° ΠΏΡΠΎΠ²ΠΎΠ΄ΠΈΡΡΡ ΠΏΠΎΒ ΡΠΎΠΉΒ ΠΆΠ΅ ΡΡ Π΅ΠΌΠ΅, ΡΡΠΎ ΠΈΒ ΡΡΡΠΏΠ΅Π½ΡΠ°ΡΠ°ΡΒ β ΡΒ Π΅Π΄ΠΈΠ½ΡΡΠ²Π΅Π½Π½ΡΠΌ ΡΠ°Π·Π»ΠΈΡΠΈΠ΅ΠΌ, ΡΡΠΎ Π²ΡΠ΄Π΅ΡΠΆΠΊΠ° Π²Β Π³ΠΎΡΡΡΠ΅ΠΉ ΡΡΠ΅Π΄Π΅ ΠΏΡΠΎΠ²ΠΎΠ΄ΠΈΡΡΡ Π·Π½Π°ΡΠΈΡΠ΅Π»ΡΠ½ΠΎ Π΄ΠΎΠ»ΡΡΠ΅ Π΄Π»Ρ ΠΎΠ±Π΅ΡΠΏΠ΅ΡΠ΅Π½ΠΈΡ Π±Π΅ΠΉΠ½ΠΈΡΠ½ΠΎΠ³ΠΎ ΠΏΡΠ΅Π²ΡΠ°ΡΠ΅Π½ΠΈΡ Π°ΡΡΡΠ΅Π½ΠΈΡΠ°.
- Q-M-B Π·Π°ΠΊΠ°Π»ΠΊΠ° (Π΄Π²ΡΡ
ΡΡΡΠΏΠ΅Π½ΡΠ°ΡΠ°Ρ ΠΌΠ°ΡΡΠ΅Π½ΡΠΈΡΠ½ΠΎ-Π±Π΅ΠΉΠ½ΠΈΡΠ½Π°Ρ) ΠΏΡΠΎΠ²ΠΎΠ΄ΠΈΡΡΡ ΠΏΠΎΒ ΡΠΎΠΉΒ ΠΆΠ΅ ΡΡ
Π΅ΠΌΠ΅, ΡΡΠΎ ΠΈΒ ΠΈΠ·ΠΎΡΠ΅ΡΠΌΠΈΡΠ΅ΡΠΊΠ°ΡΒ β ΡΒ ΡΠ΅ΠΌ ΠΎΡΠ»ΠΈΡΠΈΠ΅ΠΌ, ΡΡΠΎ ΠΎΡ
Π»Π°ΠΆΠ΄Π΅Π½ΠΈΠ΅ ΠΏΡΠΎΠΈΠ·Π²ΠΎΠ΄ΠΈΡΡΡ Π²Β Π³ΠΎΡΡΡΠ΅ΠΉ ΡΡΠ΅Π΄Π΅ ΡΒ ΡΠ΅ΠΌΠΏΠ΅ΡΠ°ΡΡΡΠΎΠΉ Π½Π°Β 10.
..90Β ΠΎΠ‘ Π½ΠΈΠΆΠ΅Β ΠΠ ΡΒ ΡΠ΅Π»ΡΡ ΠΎΠ±ΡΠ°Π·ΠΎΠ²Π°Π½ΠΈΡ Π²Β ΡΡΡΡΠΊΡΡΡΠ΅ ΠΈΠ·Π΄Π΅Π»ΠΈΡ 15…50Β % ΠΌΠ°ΡΡΠ΅Π½ΡΠΈΡΠ°, Π°Β Π·Π°ΡΠ΅ΠΌ ΠΏΠ΅ΡΠ΅Π½ΠΎΡΠΈΡΡΡ Π²Β Π³ΠΎΡΡΡΡΡ ΡΡΠ΅Π΄Ρ ΡΒ ΡΠ΅ΠΌΠΏΠ΅ΡΠ°ΡΡΡΠΎΠΉ Π½Π΅ΠΌΠ½ΠΎΠ³ΠΎ Π²ΡΡΠ΅Β ΠΠ Π΄Π»Ρ ΠΎΠ±Π΅ΡΠΏΠ΅ΡΠ΅Π½ΠΈΡ Π±Π΅ΠΉΠ½ΠΈΡΠ½ΠΎΠ³ΠΎ ΠΏΡΠ΅Π²ΡΠ°ΡΠ΅Π½ΠΈΡ ΠΎΡΡΠ°ΡΠΎΡΠ½ΠΎΠ³ΠΎ Π°ΡΡΡΠ΅Π½ΠΈΡΠ°.
ΠΠΎΒ ΠΌΠ½ΠΎΠ³ΠΈΡ ΡΠ»ΡΡΠ°ΡΡ Π΄Π°Π½Π½Π°Ρ ΡΡΡΡΠΊΡΡΡΠ° ΠΈΠ·Π΄Π΅Π»ΠΈΡ ΡΠ²Π»ΡΠ΅ΡΡΡ ΠΎΠΏΡΠΈΠΌΠ°Π»ΡΠ½ΠΎΠΉ, ΠΎΠ΄Π½Π°ΠΊΠΎ Π²Π²ΠΈΠ΄Ρ ΡΠ΅Ρ Π½ΠΈΡΠ΅ΡΠΊΠΎΠΉ ΡΠ»ΠΎΠΆΠ½ΠΎΡΡΠΈ (Π½Π΅ΠΎΠ±Ρ ΠΎΠ΄ΠΈΠΌΠΎΡΡΠΈ Π½Π°Π»ΠΈΡΠΈΡ Π΄Π²ΡΡ Π·Π°ΠΊΠ°Π»ΠΎΡΠ½ΡΡ Π²Π°Π½Π½ ΡΒ ΡΠ°Π·Π½ΠΎΠΉ ΡΠ΅ΠΌΠΏΠ΅ΡΠ°ΡΡΡΠΎΠΉ) Π΄Π°Π½Π½ΡΠΉ ΡΠΏΠΎΡΠΎΠ± Π·Π°ΠΊΠ°Π»ΠΊΠΈ ΠΏΡΠΈΠΌΠ΅Π½ΡΠ΅ΡΡΡ ΡΠΎΠ»ΡΠΊΠΎ Π΄Π»Ρ ΡΠ°ΠΌΡΡ ΠΎΡΠ²Π΅ΡΡΡΠ²Π΅Π½Π½ΡΡ ΠΈΠ·Π΄Π΅Π»ΠΈΠΉ.
- Q-n-P Π·Π°ΠΊΠ°Π»ΠΊΠ° (Π·Π°ΠΊΠ°Π»ΠΊΠ° ΡΒ ΠΏΠ΅ΡΠ΅ΡΠ°ΡΠΏΡΠ΅Π΄Π΅Π»Π΅Π½ΠΈΠ΅ΠΌ ΡΠ³Π»Π΅ΡΠΎΠ΄Π°) ΠΏΡΠΎΠ²ΠΎΠ΄ΠΈΡΡΡ ΠΏΠΎΒ ΡΠΎΠΉΒ ΠΆΠ΅ ΡΡ
Π΅ΠΌΠ΅, ΡΡΠΎ ΠΈΒ Q-M-B Π·Π°ΠΊΠ°Π»ΠΊΠ°Β β ΡΒ ΡΠ΅ΠΌ ΠΎΡΠ»ΠΈΡΠΈΠ΅ΠΌ, ΡΡΠΎ ΠΎΡ
Π»Π°ΠΆΠ΄Π΅Π½ΠΈΠ΅ ΠΏΡΠΎΠΈΠ·Π²ΠΎΠ΄ΠΈΡΡΡ Π²Β Π³ΠΎΡΡΡΠ΅ΠΉ ΡΡΠ΅Π΄Π΅ ΡΒ ΡΠ΅ΠΌΠΏΠ΅ΡΠ°ΡΡΡΠΎΠΉ Π½Π°Β 80…120Β ΠΎΠ‘ Π½ΠΈΠΆΠ΅Β ΠΠ ΡΒ ΡΠ΅Π»ΡΡ ΠΎΠ±ΡΠ°Π·ΠΎΠ²Π°Π½ΠΈΡ Π²Β ΡΡΡΡΠΊΡΡΡΠ΅ ΠΈΠ·Π΄Π΅Π»ΠΈΡ 75…80Β % ΠΌΠ°ΡΡΠ΅Π½ΡΠΈΡΠ°.
ΠΠ°ΡΠ΅ΠΌ ΠΏΡΠΎΡΠ΅ΡΡ ΠΏΠ΅ΡΠ΅Π½ΠΎΡΠΈΡΡΡ Π²Β ΠΎΡΠΏΡΡΠΊΠ½ΡΡ ΠΏΠ΅ΡΡ ΡΒ ΡΠ΅ΠΌΠΏΠ΅ΡΠ°ΡΡΡΠΎΠΉ Π½Π΅ΠΌΠ½ΠΎΠ³ΠΎ Π²ΡΡΠ΅Β ΠΠ Π΄Π»Ρ ΠΎΠ±Π΅ΡΠΏΠ΅ΡΠ΅Π½ΠΈΡ ΠΏΠ΅ΡΠ΅ΡΠ°ΡΠΏΡΠ΅Π΄Π΅Π»Π΅Π½ΠΈΡ ΡΠ³Π»Π΅ΡΠΎΠ΄Π° (ΠΈΠ·Β ΠΌΠ°ΡΡΠ΅Π½ΡΠΈΡΠ° Π²Β ΠΎΡΡΠ°ΡΠΎΡΠ½ΡΠΉ Π°ΡΡΡΠ΅Π½ΠΈΡ) ΠΈΒ ΡΡΠ°Π±ΠΈΠ»ΠΈΠ·Π°ΡΠΈΠΈ ΠΎΡΡΠ°ΡΠΎΡΠ½ΠΎΠ³ΠΎ Π°ΡΡΡΠ΅Π½ΠΈΡΠ° ΠΈΒ Π²ΡΠ΄Π΅ΡΠΆΠΈΠ²Π°Π΅ΡΡΡ Π²Β ΡΠ΅ΡΠ΅Π½ΠΈΠ΅ Π½Π΅ΠΏΡΠΎΠ΄ΠΎΠ»ΠΆΠΈΡΠ΅Π»ΡΠ½ΠΎΠ³ΠΎ Π²ΡΠ΅ΠΌΠ΅Π½ΠΈ (5…30Β ΠΌΠΈΠ½ΡΡ).
ΠΠ°ΠΆΠ½ΡΠΌ ΠΏΡΠ΅ΠΈΠΌΡΡΠ΅ΡΡΠ²ΠΎΠΌ ΠΏΠ΅ΡΠ΅Π΄ Q-M-B Π·Π°ΠΊΠ°Π»ΠΊΠΎΠΉ ΡΠ²Π»ΡΠ΅ΡΡΡ Π²ΠΎΠ·ΠΌΠΎΠΆΠ½ΠΎΡΡΡ ΠΏΡΠΈΠΌΠ΅Π½Π΅Π½ΠΈΡ Π²ΠΌΠ΅ΡΡΠΎ ΡΠ°ΡΠΏΠ»Π°Π²Π»Π΅Π½Π½ΠΎΠΉ ΡΠ΅Π»ΠΈΡΡΡ Π³ΠΎΡΡΡΠ΅Π³ΠΎ ΠΌΠ°ΡΠ»Π°, Π°Β ΡΠ°ΠΊΠΆΠ΅ ΡΡΡΠ΅ΡΡΠ²Π΅Π½Π½ΠΎΠ΅ ΡΠΎΠΊΡΠ°ΡΠ΅Π½ΠΈΠ΅ Π΄Π»ΠΈΡΠ΅Π»ΡΠ½ΠΎΡΡΠΈ ΠΏΡΠΎΠΈΠ·Π²ΠΎΠ΄ΡΡΠ²Π΅Π½Π½ΠΎΠ³ΠΎ ΡΠΈΠΊΠ»Π°.ΠΠ΅ΡΠ΅ΡΠ°ΡΠΏΡΠ΅Π΄Π΅Π»Π΅Π½ΠΈΠ΅ ΡΠ³Π»Π΅ΡΠΎΠ΄Π° ΠΏΡΠΈ Π²ΡΠ΄Π΅ΡΠΆΠΊΠ΅ Π²Β ΠΎΡΠΏΡΡΠΊΠ½ΠΎΠΉ ΠΏΠ΅ΡΠΈ ΠΎΠ±Π΅ΡΠΏΠ΅ΡΠΈΠ²Π°Π΅ΡΡΡ ΡΠΎΠ»ΡΠΊΠΎ Π΄Π»Ρ ΠΊΡΠ΅ΠΌΠ½ΠΈΡΡΡΡ ΡΡΠ°Π»Π΅ΠΉ, ΠΏΠΎΡΡΠΎΠΌΡ Π²Β ΠΠΠ Β«Π’Π΅Ρ Π½ΠΎΠΏΠ°ΡΠΊ ΠΠΌΠΏΡΠ»ΡΡΒ» Q-n-P Π·Π°ΠΊΠ°Π»ΠΊΠ° ΠΏΡΠΈΠΌΠ΅Π½ΡΠ΅ΡΡΡ ΠΎΠ³ΡΠ°Π½ΠΈΡΠ΅Π½Π½ΠΎ (ΡΠΎΠ»ΡΠΊΠΎ Π΄Π»Ρ ΠΈΠ·Π΄Π΅Π»ΠΈΠΉ ΠΈΠ·Β ΡΡΠ°Π»Π΅ΠΉ 30Π₯ΠΠ‘Π, 6Π₯Π‘ ΠΈΒ Ρ.ΠΏ. ΠΌΠ°ΡΠΎΠΊ).
- ΠΠ°ΠΊΠ°Π»ΠΊΠ° ΡΒ ΠΎΠ±ΡΠ°Π±ΠΎΡΠΊΠΎΠΉ Ρ
ΠΎΠ»ΠΎΠ΄ΠΎΠΌ (ΠΊΡΠΈΠΎΠ³Π΅Π½Π½Π°Ρ ΠΎΠ±ΡΠ°Π±ΠΎΡΠΊΠ°) Π·Π°ΠΊΠ»ΡΡΠ°Π΅ΡΡΡ Π²Β ΡΠΎΠΌ, ΡΡΠΎ ΠΏΠΎΡΠ»Π΅ ΠΎΡ
Π»Π°ΠΆΠ΄Π΅Π½ΠΈΡ ΡΡΠ°Π»ΠΈ Π΄ΠΎΒ ΠΊΠΎΠΌΠ½Π°ΡΠ½ΠΎΠΉ ΡΠ΅ΠΌΠΏΠ΅ΡΠ°ΡΡΡΡ ΠΏΡΠΎΠΈΠ·Π²ΠΎΠ΄ΠΈΡΡΡ Π΅Π΅Β Π΄ΠΎΠΏΠΎΠ»Π½ΠΈΡΠ΅Π»ΡΠ½ΠΎΠ΅ ΠΎΡ
Π»Π°ΠΆΠ΄Π΅Π½ΠΈΠ΅ Π΄ΠΎΒ ΡΠ΅ΠΌΠΏΠ΅ΡΠ°ΡΡΡ Π½ΠΈΠΆΠ΅ 0Β Β°Π‘ (ΠΏΠΎΒ Π²ΠΎΠ·ΠΌΠΎΠΆΠ½ΠΎΡΡΠΈΒ β Π½ΠΈΠΆΠ΅ ΠΠ).
ΠΠ°Π½Π½ΡΠΉ ΡΠΏΠΎΡΠΎΠ± ΡΠ΅ΡΠΌΠΎΠΎΠ±ΡΠ°Π±ΠΎΡΠΊΠΈ ΠΏΡΠΈΠΌΠ΅Π½ΡΠ΅ΡΡΡ Π΄Π»Ρ Π²ΡΡΠΎΠΊΠΎΡΠ³Π»Π΅ΡΠΎΠ΄ΠΈΡΡΡΡ ΠΈ/ΠΈΠ»ΠΈ Π²ΡΡΠΎΠΊΠΎΠ»Π΅Π³ΠΈΡΠΎΠ²Π°Π½Π½ΡΡ ΡΡΠ°Π»Π΅ΠΉ, ΡΒ ΠΊΠΎΡΠΎΡΡΡ ΡΠΎΡΠΊΠ°Β ΠΠ Π»Π΅ΠΆΠΈΡ Π·Π½Π°ΡΠΈΡΠ΅Π»ΡΠ½ΠΎ Π½ΠΈΠΆΠ΅ Π½ΡΠ»Ρ, ΡΒ ΡΠ΅Π»ΡΡ ΠΌΠ°ΠΊΡΠΈΠΌΠ°Π»ΡΠ½ΠΎ ΠΏΠΎΠ»Π½ΠΎΠ³ΠΎ ΠΏΡΠ΅Π²ΡΠ°ΡΠ΅Π½ΠΈΡ ΠΎΡΡΠ°ΡΠΎΡΠ½ΠΎΠ³ΠΎ Π°ΡΡΡΠ΅Π½ΠΈΡΠ°.ΠΒ ΠΠΠ Β«Π’Π΅Ρ Π½ΠΎΠΏΠ°ΡΠΊ ΠΠΌΠΏΡΠ»ΡΡΒ» Π·Π°ΠΊΠ°Π»ΠΊΠ° ΡΒ ΠΎΠ±ΡΠ°Π±ΠΎΡΠΊΠΎΠΉ Ρ ΠΎΠ»ΠΎΠ΄ΠΎΠΌ (Π²Β ΠΆΠΈΠ΄ΠΊΠΎΠΌ Π°Π·ΠΎΡΠ΅ Π»ΠΈΠ±ΠΎ ΡΠΌΠ΅ΡΠΈ ΡΠΏΠΈΡΡΠ° ΡΒ ΡΠ²Π΅ΡΠ΄ΠΎΠΉ ΡΠ³Π»Π΅ΠΊΠΈΡΠ»ΠΎΡΠΎΠΉ) ΠΏΡΠΈΠΌΠ΅Π½ΡΠ΅ΡΡΡ ΠΎΠ³ΡΠ°Π½ΠΈΡΠ΅Π½Π½ΠΎ (ΡΠΎΠ»ΡΠΊΠΎ Π΄Π»Ρ ΠΈΠ·Π΄Π΅Π»ΠΈΠΉ ΠΈΠ·Β ΠΈΠ½ΡΡΡΡΠΌΠ΅Π½ΡΠ°Π»ΡΠ½ΡΡ ΡΡΠ°Π»Π΅ΠΉ ΡΠΈΠΏΠ° Π₯ΠΠ ΠΈΒ Π¨Π₯15, Π°Β ΡΠ°ΠΊΠΆΠ΅ Π΄Π»Ρ ΠΎΡΠΎΠ±ΠΎ ΠΎΡΠ²Π΅ΡΡΡΠ²Π΅Π½Π½ΡΡ ΡΠ΅ΠΌΠ΅Π½ΡΠΈΡΠΎΠ²Π°Π½Π½ΡΡ ΠΈΠ·Π΄Π΅Π»ΠΈΠΉ).
Π Π°Π·Π»ΠΈΡΠΈΡ ΠΌΠ΅ΠΆΠ΄Ρ Π·Π°ΠΊΠ°Π»ΠΊΠΎΠΉ ΠΈΒ ΠΎΡΠΆΠΈΠ³ΠΎΠΌ
ΠΡΠΈΠ½ΡΠΈΠΏΠΈΠ°Π»ΡΠ½ΠΎΠ΅ ΡΠ°Π·Π»ΠΈΡΠΈΠ΅ ΠΌΠ΅ΠΆΠ΄Ρ Π·Π°ΠΊΠ°Π»ΠΊΠΎΠΉ ΠΈΒ ΠΎΡΠΆΠΈΠ³ΠΎΠΌ Π·Π°ΠΊΠ»ΡΡΠ°Π΅ΡΡΡ Π²Β ΡΠΎΠΌ, ΡΡΠΎ Π΄Π»Ρ ΡΠΈΠΊΡΠ°ΡΠΈΠΈ ΡΡΡΡΠΊΡΡΡΠ½ΠΎ-Π½Π΅ΡΡΡΠΎΠΉΡΠΈΠ²ΠΎΠ³ΠΎ ΡΠΎΡΡΠΎΡΠ½ΠΈΡ ΠΎΡ
Π»Π°ΠΆΠ΄Π΅Π½ΠΈΠ΅ ΠΏΡΠΈ Π·Π°ΠΊΠ°Π»ΠΊΠ΅ Π΄ΠΎΠ»ΠΆΠ½ΠΎ ΠΎΡΡΡΠ΅ΡΡΠ²Π»ΡΡΡΡΡ ΡΠΎΒ ΡΠΊΠΎΡΠΎΡΡΡΡ Π±ΠΎΠ»ΡΡΠ΅ ΠΊΡΠΈΡΠΈΡΠ΅ΡΠΊΠΎΠΉ.
ΠΡΠΈΡΠΈΡΠ΅ΡΠΊΠ°Ρ ΡΠΊΠΎΡΠΎΡΡΡ Π·Π°ΠΊΠ°Π»ΠΊΠΈΒ β ΠΌΠΈΠ½ΠΈΠΌΠ°Π»ΡΠ½Π°Ρ ΡΠΊΠΎΡΠΎΡΡΡ ΠΎΡ Π»Π°ΠΆΠ΄Π΅Π½ΠΈΡ, ΠΏΡΠΈ ΠΊΠΎΡΠΎΡΠΎΠΉ ΠΏΠΎΠ΄Π°Π²Π»ΡΡΡΡΡ Π΄ΠΈΡΡΡΠ·ΠΈΠΎΠ½Π½ΡΠ΅ ΠΏΡΠ΅Π²ΡΠ°ΡΠ΅Π½ΠΈΡ, ΠΈΒ Π°ΡΡΡΠ΅Π½ΠΈΡ ΠΏΡΠ΅Π²ΡΠ°ΡΠ°Π΅ΡΡΡ Π²Β ΠΌΠ°ΡΡΠ΅Π½ΡΠΈΡ. ΠΡΠΈΡΠΈΡΠ΅ΡΠΊΠ°Ρ ΡΠΊΠΎΡΠΎΡΡΡ Π·Π°ΠΊΠ°Π»ΠΊΠΈ Π·Π°Π²ΠΈΡΠΈΡ ΠΏΡΠ΅ΠΆΠ΄Π΅ Π²ΡΠ΅Π³ΠΎ ΠΎΡΒ Ρ ΠΈΠΌΠΈΡΠ΅ΡΠΊΠΎΠ³ΠΎ ΡΠΎΡΡΠ°Π²Π° ΡΠΏΠ»Π°Π²Π°Β ΠΈ, Π²Β ΠΎΠΏΡΠ΅Π΄Π΅Π»Π΅Π½Π½ΠΎΠΉ ΡΡΠ΅ΠΏΠ΅Π½ΠΈ, ΠΎΡΒ ΡΠ΅ΠΌΠΏΠ΅ΡΠ°ΡΡΡΡ Π·Π°ΠΊΠ°Π»ΠΊΠΈ.
ΠΠ»Ρ Π½Π΅ΠΊΠΎΡΠΎΡΡΡ Π²ΡΡΠΎΠΊΠΎΠ»Π΅Π³ΠΈΡΠΎΠ²Π°Π½Π½ΡΡ ΡΡΠ°Π»Π΅ΠΉ (Π½Π°ΠΏΡΠΈΠΌΠ΅Ρ, Π±ΡΡΡΡΠΎΡΠ΅ΠΆΡΡΠΈΡ ΠΈΠ»ΠΈ ΡΠ΅ΠΌΠ΅Π½ΡΠΈΡΠΎΠ²Π°Π½Π½ΡΡ ) ΠΊΡΠΈΡΠΈΡΠ΅ΡΠΊΠ°Ρ ΡΠΊΠΎΡΠΎΡΡΡ ΡΡΠΎΠ»Ρ ΠΌΠ°Π»Π°, ΡΡΠΎ Π·Π°ΠΊΠ°Π»ΠΊΠ° ΠΏΡΠΎΡΠ΅ΠΊΠ°Π΅Ρ Π΄Π°ΠΆΠ΅ ΠΏΡΠΈ ΠΎΡ Π»Π°ΠΆΠ΄Π΅Π½ΠΈΠΈ Π½Π°Β ΡΠΏΠΎΠΊΠΎΠΉΠ½ΠΎΠΌ Π²ΠΎΠ·Π΄ΡΡ Π΅Β β ΠΈΒ Π²Β ΡΡΠΎΠΌ ΡΠ»ΡΡΠ°Π΅ ΠΏΡΠΎΡΠ΅ΡΡ ΠΈΠΌΠ΅Π½ΡΠ΅ΡΡΡ Π½Π΅Β Π½ΠΎΡΠΌΠ°Π»ΠΈΠ·Π°ΡΠΈΠ΅ΠΉ (ΠΊΠΎΡΠΎΡΠ°Ρ ΡΠ²Π»ΡΠ΅ΡΡΡ ΡΠ°Π·Π½ΠΎΠ²ΠΈΠ΄Π½ΠΎΡΡΡΡ ΠΎΡΠΆΠΈΠ³Π°), Π°Β Π²ΠΎΠ·Π΄ΡΡΠ½ΠΎΠΉ Π·Π°ΠΊΠ°Π»ΠΊΠΎΠΉ.
ΠΡΠΏΡΡΠΊ Π²Β ΡΠ΅ΡΠΌΠΎΠΎΠ±ΡΠ°Π±ΠΎΡΠΊΠ΅: ΠΎΡΠΎΠ±Π΅Π½Π½ΠΎΡΡΠΈ ΠΈΒ Π²ΠΈΠ΄Ρ
ΠΡΠΏΡΡΠΊΒ β Π½Π°Π³ΡΠ΅Π² Π·Π°ΠΊΠ°Π»Π΅Π½Π½ΠΎΠ³ΠΎ (ΡΒ ΠΏΠΎΠ»ΠΈΠΌΠΎΡΡΠ½ΡΠΌ ΠΏΡΠ΅Π²ΡΠ°ΡΠ΅Π½ΠΈΠ΅ΠΌ) ΡΠΏΠ»Π°Π²Π° Π΄ΠΎΒ ΡΠ΅ΠΌΠΏΠ΅ΡΠ°ΡΡΡΡ Π½Π΅Β Π²ΡΡΠ΅ ΡΠΎΡΠΊΠΈ ΠΏΠΎΠ»ΠΈΠΌΠΎΡΡΠ½ΠΎΠ³ΠΎ ΠΏΡΠ΅Π²ΡΠ°ΡΠ΅Π½ΠΈΡ Π΄Π»Ρ ΠΏΠΎΠ»ΡΡΠ΅Π½ΠΈΡ Π±ΠΎΠ»Π΅Π΅ ΡΠ΅ΡΠΌΠΈΡΠ΅ΡΠΊΠΈ ΡΡΠ°Π±ΠΈΠ»ΡΠ½ΠΎΠ³ΠΎ ΡΠΎΡΡΠΎΡΠ½ΠΈΡ.
ΠΠΎΡΠ»Π΅ Π·Π°ΠΊΠ°Π»ΠΊΠΈ ΡΡΠ°Π»Ρ ΠΏΡΠΈΠΎΠ±ΡΠ΅ΡΠ°Π΅Ρ ΡΡΡΡΠΊΡΡΡΡ, ΡΠΎΡΡΠΎΡΡΡΡ ΠΈΠ·Β ΠΌΠ°ΡΡΠ΅Π½ΡΠΈΡΠ° ΠΈΒ ΠΎΡΡΠ°ΡΠΎΡΠ½ΠΎΠ³ΠΎ Π°ΡΡΡΠ΅Π½ΠΈΡΠ° (Π²Β ΡΡΠ΄Π΅ ΡΠ»ΡΡΠ°Π΅Π²Β β ΡΠ°ΠΊΠΆΠ΅ Π±Π΅ΠΉΠ½ΠΈΡΠ°), ΠΊΠΎΡΠΎΡΡΠ΅ ΡΠ²Π»ΡΡΡΡΡ Π½Π΅ΡΠ°Π²Π½ΠΎΠ²Π΅ΡΠ½ΡΠΌΠΈ ΡΠ°Π·Π°ΠΌΠΈ ΠΈΒ ΠΏΡΠΈ ΠΏΠΎΡΠ»Π΅Π΄ΡΡΡΠ΅ΠΌ Π½Π°Π³ΡΠ΅Π²Π΅ ΠΏΡΠ΅ΡΠ΅ΡΠΏΠ΅Π²Π°ΡΡ ΠΏΡΠ΅Π²ΡΠ°ΡΠ΅Π½ΠΈΡ. ΠΡΠΎΠΌΠ΅ ΡΠΎΠ³ΠΎ, Π²Β Π·Π°ΠΊΠ°Π»Π΅Π½Π½ΡΡ
Π·Π°ΡΠ²ΡΠ΅ΠΊΡΠΎΠΈΠ΄Π½ΡΡ
ΡΡΠ°Π»ΡΡ
ΠΏΡΠΈΡΡΡΡΡΠ²ΡΠ΅Ρ Π²ΡΠΎΡΠΈΡΠ½ΡΠΉ ΡΠ΅ΠΌΠ΅Π½ΡΠΈΡ, ΠΊΠΎΡΠΎΡΡΠΉ Π½Π΅Β ΠΈΡΠΏΡΡΡΠ²Π°Π΅Ρ ΠΏΡΠ΅Π²ΡΠ°ΡΠ΅Π½ΠΈΠΉ.
ΠΒ ΡΠ΅ΡΠΌΠΎΠΎΠ±ΡΠ°Π±ΠΎΡΠΊΠ΅ Π²ΡΠ΄Π΅Π»ΡΡΡ ΡΡΠΈ Π²ΠΈΠ΄Π° ΠΎΡΠΏΡΡΠΊΠ°.
ΠΠΈΠ·ΠΊΠΈΠΉ ΠΎΡΠΏΡΡΠΊ
Π’Π°ΠΊ Π½Π°Π·ΡΠ²Π°Π΅ΡΡΡ ΠΏΡΠΎΡΠ΅ΡΡ Π½Π°Π³ΡΠ΅Π²Π° Π·Π°ΠΊΠ°Π»Π΅Π½Π½ΠΎΠΉ ΡΡΠ°Π»ΠΈ Π΄ΠΎΒ 150Β β 350Β Β°Π‘, ΠΏΡΠΈ ΠΊΠΎΡΠΎΡΠΎΠΌ ΠΏΡΠΎΠΈΡΡ ΠΎΠ΄ΠΈΡ Π²ΡΠ΄Π΅Π»Π΅Π½ΠΈΠ΅ ΡΠ³Π»Π΅ΡΠΎΠ΄Π° ΠΈΠ·Β ΠΌΠ°ΡΡΠ΅Π½ΡΠΈΡΠ° (ΠΎΠ±ΡΠ°Π·ΠΎΠ²Π°Π½ΠΈΠ΅ ΠΌΠ°ΡΡΠ΅Π½ΡΠΈΡΠ° ΠΎΡΠΏΡΡΠΊΠ°), ΠΎΠ±ΡΠ°Π·ΠΎΠ²Π°Π½ΠΈΠ΅ ΠΊΠ°ΡΠ±ΠΈΠ΄Π½ΠΎΠΉ ΡΠ°Π·Ρ (Ξ΅-ΠΊΠ°ΡΠ±ΠΈΠ΄Π° ΠΈ/ΠΈΠ»ΠΈ ΡΠ΅ΠΌΠ΅Π½ΡΠΈΡΠ°), ΠΏΡΠ΅Π²ΡΠ°ΡΠ΅Π½ΠΈΠ΅ ΠΎΡΡΠ°ΡΠΎΡΠ½ΠΎΠ³ΠΎ Π°ΡΡΡΠ΅Π½ΠΈΡΠ° Π²Β Π½ΠΈΠΆΠ½ΠΈΠΉ Π±Π΅ΠΉΠ½ΠΈΡ ΠΈΒ ΡΠ°ΡΡΠΈΡΠ½ΠΎΠ΅ ΡΠ½ΡΡΠΈΠ΅ Π²Π½ΡΡΡΠ΅Π½Π½ΠΈΡ Π½Π°ΠΏΡΡΠΆΠ΅Π½ΠΈΠΉ.
ΠΠ°Π½Π½ΡΠΉ Π²ΠΈΠ΄ ΠΎΡΠΏΡΡΠΊΠ° ΠΏΡΠΈΠΌΠ΅Π½ΡΠ΅ΡΡΡ Π΄Π»Ρ ΠΈΠ·Π΄Π΅Π»ΠΈΠΉ, ΠΎΡΒ ΠΊΠΎΡΠΎΡΡΡ ΡΡΠ΅Π±ΡΠ΅ΡΡΡ ΡΠΎΡ ΡΠ°Π½Π΅Π½ΠΈΠ΅ Π²ΡΡΠΎΠΊΠΎΠΉ ΡΠ²ΡΡΠ΄ΠΎΡΡΠΈ ΠΈΒ ΠΏΡΠΎΡΠ½ΠΎΡΡΠΈ (Π²Β ΠΠΠ Β«Π’Π΅Ρ Π½ΠΎΠΏΠ°ΡΠΊ ΠΠΌΠΏΡΠ»ΡΡΒ» ΠΎΠ½Β ΠΏΡΠΈΠΌΠ΅Π½ΡΠ΅ΡΡΡ Π³Π»Π°Π²Π½ΡΠΌ ΠΎΠ±ΡΠ°Π·ΠΎΠΌ Π΄Π»Ρ ΠΏΠΈΠΊ ΠΈΒ Π±ΠΎΠΉΠΊΠΎΠ²).
Π‘ΡΠ΅Π΄Π½ΠΈΠΉ ΠΎΡΠΏΡΡΠΊ
ΠΡΠΎ ΠΏΡΠΎΡΠ΅ΡΡ Π½Π°Π³ΡΠ΅Π²Π° Π·Π°ΠΊΠ°Π»Π΅Π½Π½ΠΎΠΉ ΡΡΠ°Π»ΠΈ Π΄ΠΎΒ 350Β β 500Β Β°Π‘, Π²Β ΡΠ΅Π·ΡΠ»ΡΡΠ°ΡΠ΅ ΠΊΠΎΡΠΎΡΠΎΠ³ΠΎ ΠΏΡΠΎΠΈΡΡ ΠΎΠ΄ΠΈΡ ΡΠ°ΡΠΏΠ°Π΄ ΠΌΠ°ΡΡΠ΅Π½ΡΠΈΡΠ° Π½Π°Β ΡΠ΅ΡΡΠΈΡΠΎ-ΡΠ΅ΠΌΠ΅Π½ΡΠΈΡΠ½ΡΡ ΡΠΌΠ΅ΡΡ (ΡΡΠΎΠΎΡΡΠΈΡ ΠΎΡΠΏΡΡΠΊΠ°) ΠΈΒ Π±ΠΎΠ»Π΅Π΅ Π³Π»ΡΠ±ΠΎΠΊΠΎΠ΅ ΡΠ½ΡΡΠΈΠ΅ Π²Π½ΡΡΡΠ΅Π½Π½ΠΈΡ Π½Π°ΠΏΡΡΠΆΠ΅Π½ΠΈΠΉ.
ΠΠ°Π½Π½ΡΠΉ Π²ΠΈΠ΄ ΠΎΡΠΏΡΡΠΊΠ° ΠΏΡΠΈΠΌΠ΅Π½ΡΠ΅ΡΡΡ Π΄Π»Ρ ΠΈΠ·Π΄Π΅Π»ΠΈΠΉ, ΠΎΡΒ ΠΊΠΎΡΠΎΡΡΡ
ΡΡΠ΅Π±ΡΠ΅ΡΡΡ ΡΠΎΡ
ΡΠ°Π½Π΅Π½ΠΈΠ΅ Π²ΡΡΠΎΠΊΠΎΠΉ ΠΏΡΠΎΡΠ½ΠΎΡΡΠΈ ΠΈΒ ΡΠΏΡΡΠ³ΠΎΡΡΠΈ ΠΏΡΠΈ Π½Π°Π»ΠΈΡΠΈΠΈ ΡΠΌΠ΅ΡΠ΅Π½Π½ΠΎΠΉ ΠΏΠ»Π°ΡΡΠΈΡΠ½ΠΎΡΡΠΈ (Π²Β ΠΠΠ Β«Π’Π΅Ρ
Π½ΠΎΠΏΠ°ΡΠΊ ΠΠΌΠΏΡΠ»ΡΡΒ» ΠΎΠ½Β ΠΏΡΠΈΠΌΠ΅Π½ΡΠ΅ΡΡΡ Π³Π»Π°Π²Π½ΡΠΌ ΠΎΠ±ΡΠ°Π·ΠΎΠΌ Π΄Π»Ρ ΠΏΠ°Π»ΡΡΠ΅Π², ΡΡΡΠΆΠ΅ΠΊ ΠΈΒ Ρ. ΠΏ. ΠΊΡΠ΅ΠΏΠ΅ΠΆΠ° ΡΒ ΠΊΠ»Π°ΡΡΠΎΠΌ ΠΏΡΠΎΡΠ½ΠΎΡΡΠΈ 10.9 ΠΈΒ 12.9).
ΠΡΡΠΎΠΊΠΈΠΉ ΠΎΡΠΏΡΡΠΊ
ΠΡΠΎΡ ΠΏΡΠΎΡΠ΅ΡΡ ΠΏΠΎΠ΄ΡΠ°Π·ΡΠΌΠ΅Π²Π°Π΅Ρ Π½Π°Π³ΡΠ΅Π² Π·Π°ΠΊΠ°Π»Π΅Π½Π½ΠΎΠΉ ΡΡΠ°Π»ΠΈ Π΄ΠΎΒ 500Β β 700Β Β°Π‘, ΠΊΠΎΡΠΎΡΡΠΉ ΡΠΎΠΏΡΠΎΠ²ΠΎΠΆΠ΄Π°Π΅ΡΡΡ ΡΠ°ΡΠΏΠ°Π΄ΠΎΠΌ ΠΌΠ°ΡΡΠ΅Π½ΡΠΈΡΠ° Π½Π°Β ΡΠ΅ΡΡΠΈΡΠΎ-ΡΠ΅ΠΌΠ΅Π½ΡΠΈΡΠ½ΡΡ ΡΠΌΠ΅ΡΡ (ΡΠΎΡΠ±ΠΈΡ ΠΎΡΠΏΡΡΠΊΠ°), Π΄ΠΈΡΠΏΠ΅ΡΡΠΈΠΎΠ½Π½ΡΠΌ ΡΠ²Π΅ΡΠ΄Π΅Π½ΠΈΠ΅ΠΌ ΡΡΠ°Π»Π΅ΠΉ, ΠΏΡΠ°ΠΊΡΠΈΡΠ΅ΠΊΠΈ ΠΏΠΎΠ»Π½ΡΠΌ ΡΠ½ΡΡΠΈΠ΅ΠΌ Π²Π½ΡΡΡΠ΅Π½Π½ΠΈΡ Π½Π°ΠΏΡΡΠΆΠ΅Π½ΠΈΠΉ.
ΠΠ°Π½Π½ΡΠΉ Π²ΠΈΠ΄ ΠΎΡΠΏΡΡΠΊΠ° ΠΏΡΠΈΠΌΠ΅Π½ΡΠ΅ΡΡΡ Π΄Π»Ρ ΠΈΠ·Π΄Π΅Π»ΠΈΠΉ, ΠΎΡΒ ΠΊΠΎΡΠΎΡΡΡ ΡΡΠ΅Π±ΡΠ΅ΡΡΡ Π½Π°Π»ΠΈΡΠΈΠ΅ Π²ΡΡΠΎΠΊΠΎΠΉ ΠΏΠ»Π°ΡΡΠΈΡΠ½ΠΎΡΡΠΈ ΠΈΒ ΡΠ΄Π°ΡΠ½ΠΎΠΉ Π²ΡΠ·ΠΊΠΎΡΡΠΈ ΠΏΡΠΈ ΡΠΎΡ ΡΠ°Π½Π΅Π½ΠΈΠΈ ΡΡΠ°Π²Π½ΠΈΡΠ΅Π»ΡΠ½ΠΎ Π²ΡΡΠΎΠΊΠΎΠΉ ΠΏΡΠΎΡΠ½ΠΎΡΡΠΈ (Π²Β ΠΠΠ Β«Π’Π΅Ρ Π½ΠΎΠΏΠ°ΡΠΊ ΠΠΌΠΏΡΠ»ΡΡΒ» ΠΎΠ½Β ΠΏΡΠΈΠΌΠ΅Π½ΡΠ΅ΡΡΡ Π³Π»Π°Π²Π½ΡΠΌ ΠΎΠ±ΡΠ°Π·ΠΎΠΌ Π΄Π»Ρ Π²ΡΡΠ»ΠΎΠΊ, Π³ΠΈΠ»ΡΠ· ΠΈΒ ΠΊΡΠ΅ΠΏΠ΅ΠΆΠ° ΡΒ ΠΊΠ»Π°ΡΡΠΎΠΌ ΠΏΡΠΎΡΠ½ΠΎΡΡΠΈ 8.8 ΠΈΒ 9.8).
ΠΡΠΎΠ±Π΅Π½Π½ΠΎΡΡΠΈ Π·Π°ΠΊΠ°Π»ΠΊΠΈ Π±Π΅Π· ΠΏΠΎΠ»ΠΈΠΌΠΎΡΡΠ½ΠΎΠ³ΠΎ ΠΏΡΠ΅Π²ΡΠ°ΡΠ΅Π½ΠΈΡ
ΠΠ°ΠΊΠ°Π»ΠΊΠ° Π±Π΅Π· ΠΏΠΎΠ»ΠΈΠΌΠΎΡΡΠ½ΠΎΠ³ΠΎ ΠΏΡΠ΅Π²ΡΠ°ΡΠ΅Π½ΠΈΡΒ β Π½Π°Π³ΡΠ΅Π² Π΄ΠΎΒ ΡΠ΅ΠΌΠΏΠ΅ΡΠ°ΡΡΡ, Π²ΡΠ·ΡΠ²Π°ΡΡΠΈΡ ΡΡΡΡΠΊΡΡΡΠ½ΡΠ΅ ΠΈΠ·ΠΌΠ΅Π½Π΅Π½ΠΈΡ (ΡΠ°ΡΠ΅ Π²ΡΠ΅Π³ΠΎ Π΄Π»Ρ ΡΠ°ΡΡΠ²ΠΎΡΠ΅Π½ΠΈΡ ΠΈΠ·Π±ΡΡΠΎΡΠ½ΠΎΠΉ ΡΠ°Π·Ρ) ΡΒ ΠΏΠΎΡΠ»Π΅Π΄ΡΡΡΠΈΠΌ Π±ΡΡΡΡΡΠΌ ΠΎΡ Π»Π°ΠΆΠ΄Π΅Π½ΠΈΠ΅ΠΌ Π΄Π»Ρ ΠΏΠΎΠ»ΡΡΠ΅Π½ΠΈΡ ΡΡΡΡΠΊΡΡΡΠ½ΠΎ-Π½Π΅ΡΡΡΠΎΠΉΡΠΈΠ²ΠΎΠ³ΠΎ ΡΠΎΡΡΠΎΡΠ½ΠΈΡΒ β ΠΏΠ΅ΡΠ΅ΡΡΡΠ΅Π½Π½ΠΎΠ³ΠΎ ΡΠ²Π΅ΡΠ΄ΠΎΠ³ΠΎ ΡΠ°ΡΡΠ²ΠΎΡΠ°.
ΠΠ°ΠΊΠ°Π»ΠΊΠ° Π±Π΅Π· ΠΏΠΎΠ»ΠΈΠΌΠΎΡΡΠ½ΠΎΠ³ΠΎ ΠΏΡΠ΅Π²ΡΠ°ΡΠ΅Π½ΠΈΡ ΠΏΡΠΈΠΌΠ΅Π½ΡΠ΅ΡΡΡ ΠΏΡΠ΅ΠΈΠΌΡΡΠ΅ΡΡΠ²Π΅Π½Π½ΠΎ Π΄Π»Ρ ΡΠΏΠ»Π°Π²ΠΎΠ² ΡΠ²Π΅ΡΠ½ΡΡ
ΠΌΠ΅ΡΠ°Π»Π»ΠΎΠ² (Π°Π»ΡΠΌΠΈΠ½ΠΈΠ΅Π²ΡΡ
, ΠΌΠ΅Π΄Π½ΡΡ
, Π½ΠΈΠΊΠ΅Π»Π΅Π²ΡΡ
, ΡΠΈΡΠ°Π½ΠΎΠ²ΡΡ
ΠΈΒ Π΄Ρ. ) ΠΈΒ Π»ΠΈΡΡ Π΄Π»Ρ Π½Π΅ΠΌΠ½ΠΎΠ³ΠΈΡ
ΠΌΠ°ΡΠΎΠΊ ΡΡΠ°Π»ΠΈ (ΠΏΡΠ΅ΠΈΠΌΡΡΠ΅ΡΡΠ²Π΅Π½Π½ΠΎ Π°ΡΡΡΠ΅Π½ΠΈΡΠ½ΡΡ
Β β Π½Π΅ΡΠΆΠ°Π²Π΅ΡΡΠΈΡ
Ρ
ΡΠΎΠΌΠΎΠ½ΠΈΠΊΠ΅Π»Π΅Π²ΡΡ
ΡΠΈΠΏΠ° Π₯18Π8 ΠΈΒ ΠΈΠ·Π½ΠΎΡΠΎΡΡΠΎΠΉΠΊΠΈΡ
Π²ΡΡΠΎΠΊΠΎΠΌΠ°ΡΠ³Π°Π½ΡΠ΅Π²ΡΡ
ΡΠΈΠΏΠ° 110Π13). ΠΒ ΠΠΠ Β«Π’Π΅Ρ
Π½ΠΎΠΏΠ°ΡΠΊ ΠΠΌΠΏΡΠ»ΡΡΒ» ΠΎΠ½Β ΠΏΡΠΈΠΌΠ΅Π½ΡΠ΅ΡΡΡ Π³Π»Π°Π²Π½ΡΠΌ ΠΎΠ±ΡΠ°Π·ΠΎΠΌ ΠΈΠ·Π΄Π΅Π»ΠΈΠΉ ΠΈΠ·Β Π½Π΅ΡΠΆΠ°Π²Π΅ΡΡΠΈΡ
ΡΡΠ°Π»Π΅ΠΉ ΡΠΈΠΏΠ° Π₯18Π8, Π₯18Π10Π’ ΠΈΒ Ρ.ΠΏ., Π°Β ΡΠ°ΠΊΠΆΠ΅ ΠΈΠ·Π΄Π΅Π»ΠΈΠΉ ΠΈΠ·Β ΠΌΠ΅Π΄Π½ΡΡ
ΠΈΒ Π°Π»ΡΠΌΠΈΠ½ΠΈΠ΅Π²ΡΡ
ΡΠΏΠ»Π°Π²ΠΎΠ².
Π‘ΡΠ°ΡΠ΅Π½ΠΈΠ΅ Π²Β ΡΠ΅ΡΠΌΠΎΠΎΠ±ΡΠ°Π±ΠΎΡΠΊΠ΅: ΡΡΠΎ ΡΡΠΎ ΠΈΒ Π΄Π»Ρ ΡΠ΅Π³ΠΎ?
Π‘ΡΠ°ΡΠ΅Π½ΠΈΠ΅Β β Π½Π°Π³ΡΠ΅Π² ΠΈΠ»ΠΈ Π΄Π»ΠΈΡΠ΅Π»ΡΠ½Π°Ρ Π²ΡΠ΄Π΅ΡΠΆΠΊΠ° ΠΏΡΠΈ ΠΊΠΎΠΌΠ½Π°ΡΠ½ΠΎΠΉ ΡΠ΅ΠΌΠΏΠ΅ΡΠ°ΡΡΡΠ΅Β β Ρ.Π½. Π΅ΡΡΠ΅ΡΡΠ²Π΅Π½Π½ΠΎΠ΅ ΡΡΠ°ΡΠ΅Π½ΠΈΠ΅, Π²ΡΠ·ΡΠ²Π°ΡΡΠΈΠΉ ΠΏΡΠ΅Π²ΡΠ°ΡΠ΅Π½ΠΈΡ Π²Β Π·Π°ΠΊΠ°Π»Π΅Π½Π½ΠΎΠΌ Π±Π΅Π· ΠΏΠΎΠ»ΠΈΠΌΠΎΡΡΠ½ΠΎΠ³ΠΎ ΠΏΡΠ΅Π²ΡΠ°ΡΠ΅Π½ΠΈΡ ΡΠΏΠ»Π°Π²Π΅ ΡΒ ΡΠ΅Π»ΡΡ Π»ΠΈΠ±ΠΎ ΡΠΏΡΠΎΡΠ½Π΅Π½ΠΈΡ ΡΠΏΠ»Π°Π²ΠΎΠ² (Π·Π°Β ΡΡΡΡ Π΄ΠΈΡΠΏΠ΅ΡΡΠΈΠΎΠ½Π½ΠΎΠ³ΠΎ ΡΠ²Π΅ΡΠ΄Π΅Π½ΠΈΡ), Π»ΠΈΠ±ΠΎ ΡΠ°Π·ΡΠΏΡΠΎΡΠ½Π΅Π½ΠΈΡ (Π·Π°Β ΡΡΡΡ ΠΏΡΠΈΠ±Π»ΠΈΠΆΠ΅Π½ΠΈΡ ΡΠΏΠ»Π°Π²Π° ΠΊΒ Π±ΠΎΠ»Π΅Π΅ ΡΠ°Π²Π½ΠΎΠ²Π΅ΡΠ½ΠΎΠΌΡ ΡΠΎΡΡΠΎΡΠ½ΠΈΡ.
ΠΒ ΠΠΠ Β«Π’Π΅Ρ Π½ΠΎΠΏΠ°ΡΠΊ ΠΠΌΠΏΡΠ»ΡΡΒ» ΡΠ°ΠΊΠΎΠΉ ΡΠΏΠΎΡΠΎΠ± ΠΏΡΠΈΠΌΠ΅Π½ΡΠ΅ΡΡΡ Π³Π»Π°Π²Π½ΡΠΌ ΠΎΠ±ΡΠ°Π·ΠΎΠΌ Π΄Π»Ρ ΠΈΠ·Π΄Π΅Π»ΠΈΠΉ ΠΈΠ·Β ΠΌΠ΅Π΄Π½ΡΡ ΠΈΒ Π°Π»ΡΠΌΠΈΠ½ΠΈΠ΅Π²ΡΡ ΡΠΏΠ»Π°Π²ΠΎΠ².
Π§ΡΠΎ ΡΠ°ΠΊΠΎΠ΅ Ρ ΠΈΠΌΠΈΠΊΠΎ-ΡΠ΅ΡΠΌΠΈΡΠ΅ΡΠΊΠ°Ρ ΠΎΠ±ΡΠ°Π±ΠΎΡΠΊΠ°?
Π₯ΠΈΠΌΠΈΠΊΠΎ-ΡΠ΅ΡΠΌΠΈΡΠ΅ΡΠΊΠ°Ρ ΠΎΠ±ΡΠ°Π±ΠΎΡΠΊΠ° (Π₯Π’Π) Π·Π°ΠΊΠ»ΡΡΠ°Π΅ΡΡΡ Π²Β ΡΠΎΡΠ΅ΡΠ°Π½ΠΈΠΈ ΡΠ΅ΡΠΌΠΈΡΠ΅ΡΠΊΠΎΠ³ΠΎ ΠΈΒ Ρ
ΠΈΠΌΠΈΡΠ΅ΡΠΊΠΎΠ³ΠΎ Π²ΠΎΠ·Π΄Π΅ΠΉΡΡΠ²ΠΈΡ ΡΒ ΡΠ΅Π»ΡΡ ΠΈΠ·ΠΌΠ΅Π½Π΅Π½ΠΈΡ Ρ
ΠΈΠΌΠΈΡΠ΅ΡΠΊΠΎΠ³ΠΎ ΡΠΎΡΡΠ°Π²Π°, ΡΡΡΡΠΊΡΡΡΡ ΠΈΒ ΡΠ²ΠΎΠΉΡΡΠ² ΠΏΠΎΠ²Π΅ΡΡ
Π½ΠΎΡΡΠ½ΠΎΠ³ΠΎ ΡΠ»ΠΎΡ ΠΈΠ·Π΄Π΅Π»ΠΈΡ.
ΠΠ½Π° Π²ΠΊΠ»ΡΡΠ°Π΅Ρ Π΄ΠΈΡΡΡΠ·ΠΈΠΎΠ½Π½ΠΎΠ΅ Π½Π°ΡΡΡΠ΅Π½ΠΈΠ΅ Π½Π΅ΠΌΠ΅ΡΠ°Π»Π»Π°ΠΌΠΈ (ΡΠ³Π»Π΅ΡΠΎΠ΄ΠΎΠΌ, Π°Π·ΠΎΡΠΎΠΌ, Π±ΠΎΡΠΎΠΌ, ΡΠ΅ΡΠΎΠΉ, ΠΊΡΠ΅ΠΌΠ½ΠΈΠ΅ΠΌ ΠΈΒ ΠΊΠΈΡΠ»ΠΎΡΠΎΠ΄ΠΎΠΌ), Π΄ΠΈΡΡΡΠ·ΠΈΠΎΠ½Π½ΠΎΠ΅ Π½Π°ΡΡΡΠ΅Π½ΠΈΠ΅ ΠΌΠ΅ΡΠ°Π»Π»Π°ΠΌΠΈ (Π΄ΠΈΡΡΡΠ·ΠΈΠΎΠ½Π½Π°Ρ ΠΌΠ΅ΡΠ°Π»Π»ΠΈΠ·Π°ΡΠΈΡΒ β Π°Π»ΡΠΌΠΈΠ½ΠΈΠ΅ΠΌ, Ρ ΡΠΎΠΌΠΎΠΌ, Π±Π΅ΡΠΈΠ»Π»ΠΈΠ΅ΠΌ, ΡΠΈΡΠ°Π½ΠΎΠΌ, ΡΠΈΠ½ΠΊΠΎΠΌ, ΠΌΠ΅Π΄ΡΡ ΠΈΒ Π΄Ρ.), Π΄ΠΈΡΡΡΠ·ΠΈΠΎΠ½Π½ΠΎΠ΅ ΡΠ΄Π°Π»Π΅Π½ΠΈΠ΅ ΠΏΡΠΈΠΌΠ΅ΡΠ΅ΠΉ (ΡΠ³Π»Π΅ΡΠΎΠ΄Π°, ΠΊΠΈΡΠ»ΠΎΡΠΎΠ΄Π°, Π²ΠΎΠ΄ΠΎΡΠΎΠ΄Π°).
ΠΠΈΡΡΡΠ·ΠΈΠΎΠ½Π½ΠΎΠ΅ Π½Π°ΡΡΡΠ΅Π½ΠΈΠ΅ ΠΊΠ»Π°ΡΡΠΈΡΠΈΡΠΈΡΡΠ΅ΡΡΡ ΠΏΠΎΒ Π½Π°ΡΡΡΠ°ΡΡΠ΅ΠΌΡ ΡΠ»Π΅ΠΌΠ΅Π½ΡΡΒ β ΡΠ³Π»Π΅ΡΠΎΠ΄Ρ (ΡΠ΅ΠΌΠ΅Π½ΡΠ°ΡΠΈΡ), Π°Π·ΠΎΡΡ (Π°Π·ΠΎΡΠΈΡΠΎΠ²Π°Π½ΠΈΠ΅), Π±ΠΎΡΡ (Π±ΠΎΡΠΈΡΠΎΠ²Π°Π½ΠΈΠ΅) ΠΈΒ Ρ.ΠΏ. ΠΒ ΡΡΠ΄Π΅ ΡΠ»ΡΡΠ°Π΅Π² ΠΏΡΠΈΠΌΠ΅Π½ΡΠ΅ΡΡΡ ΠΎΠ΄Π½ΠΎΠ²ΡΠ΅ΠΌΠ΅Π½Π½ΠΎΠ΅ Π½Π°ΡΡΡΠ΅Π½ΠΈΠ΅ Π½Π΅ΡΠΊΠΎΠ»ΡΠΊΠΈΠΌΠΈ ΡΠ»Π΅ΠΌΠ΅Π½ΡΠ°ΠΌΠΈ (Π½Π°ΠΏΡΠΈΠΌΠ΅Ρ, Ρ ΡΠΎΠΌΠΎΠ°Π»ΠΈΡΠΈΡΠΎΠ²Π°Π½ΠΈΠ΅Β β Π½Π°ΡΡΡΠ΅Π½ΠΈΠ΅ Ρ ΡΠΎΠΌΠΎΠΌ ΠΈΒ Π°Π»ΡΠΌΠΈΠ½ΠΈΠ΅ΠΌ, ΡΠΈΠ°Π½ΠΈΡΠΎΠ²Π°Π½ΠΈΠ΅ ΠΈΒ Π½ΠΈΡΡΠΎΡΠ΅ΠΌΠ΅Π½ΡΠ°ΡΠΈΡΒ β Π½Π°ΡΡΡΠ΅Π½ΠΈΠ΅ ΡΠ³Π»Π΅ΡΠΎΠ΄ΠΎΠΌ ΠΈΒ Π°Π·ΠΎΡΠΎΠΌ). Π₯Π’Π ΠΌΠΎΠΆΠ΅Ρ ΠΏΡΠΈΠΌΠ΅Π½ΡΡΡΡΡ ΠΊΠ°ΠΊ ΠΎΠΊΠΎΠ½ΡΠ°ΡΠ΅Π»ΡΠ½Π°Ρ ΠΈΠ»ΠΈ ΠΊΠ°ΠΊ ΠΏΡΠ΅Π΄Π²Π°ΡΠΈΡΠ΅Π»ΡΠ½Π°Ρ ΠΎΠΏΠ΅ΡΠ°ΡΠΈΡ ΠΏΠ΅ΡΠ΅Π΄ ΠΏΠΎΡΠ»Π΅Π΄ΡΡΡΠ΅ΠΉ ΡΠΏΡΠΎΡΠ½ΡΡΡΠ΅ΠΉ ΡΠ΅ΡΠΌΠΈΡΠ΅ΡΠΊΠΎΠΉ ΠΎΠ±ΡΠ°Π±ΠΎΡΠΊΠΎΠΉ.
ΠΠ°ΠΊ ΠΏΡΠ°Π²ΠΈΠ»ΠΎ, ΡΠΊΠΎΡΠΎΡΡΡ Π΄ΠΈΡΡΡΠ·ΠΈΠΈ Π½Π΅ΠΌΠ΅ΡΠ°Π»Π»ΠΎΠ² ΡΡΡΠ΅ΡΡΠ²Π΅Π½Π½ΠΎ Π²ΡΡΠ΅, ΡΠ΅ΠΌ ΠΌΠ΅ΡΠ°Π»Π»ΠΎΠ², ΠΏΠΎΡΡΠΎΠΌΡ Π²Β ΡΠ΅Ρ
ΡΠ»ΡΡΠ°ΡΡ
, ΠΊΠΎΠ³Π΄Π° ΡΡΠ΅Π±ΡΠ΅ΡΡΡ ΠΏΠΎΠ»ΡΡΠ΅Π½ΠΈΠ΅ Π΄ΠΎΡΡΠ°ΡΠΎΡΠ½ΠΎ ΡΠΎΠ»ΡΡΡΡ
Π΄ΠΈΡΡΡΠ·ΠΈΠΎΠ½Π½ΡΡ
ΡΠ»ΠΎΡΠ², ΠΎΠ±ΡΡΠ½ΠΎ ΠΈΡΠΏΠΎΠ»ΡΠ·ΡΠ΅ΡΡΡ Π½Π°ΡΡΡΠ΅Π½ΠΈΠ΅ Π½Π΅ΠΌΠ΅ΡΠ°Π»Π»Π°ΠΌΠΈ. ΠΠΎΒ ΡΡΠΎΠΉ ΠΏΡΠΈΡΠΈΠ½Π΅ ΠΒ ΠΠΠ Β«Π’Π΅Ρ
Π½ΠΎΠΏΠ°ΡΠΊ ΠΠΌΠΏΡΠ»ΡΡΒ» ΠΏΡΠΈΠΌΠ΅Π½ΡΡΡΡΡ, Π³Π»Π°Π²Π½ΡΠΌ ΠΎΠ±ΡΠ°Π·ΠΎΠΌ, Π½Π°ΠΈΠ±ΠΎΠ»Π΅Π΅ ΡΠ°ΡΠΏΡΠΎΡΡΡΠ°Π½Π΅Π½Π½ΡΠ΅ ΠΈΠ·Β ΠΌΠ΅ΡΠΎΠ΄ΠΎΠ² Π₯Π’ΠΒ β ΡΠ΅ΠΌΠ΅Π½ΡΠ°ΡΠΈΡ, Π½ΠΈΡΡΠΎΡΠ΅ΠΌΠ΅Π½ΡΠ°ΡΠΈΡ, Π°Π·ΠΎΡΠΈΡΠΎΠ²Π°Π½ΠΈΠ΅ ΠΈΒ ΠΊΠ°ΡΠ±ΠΎΠ½ΠΈΡΡΠ°ΡΠΈΡ. ΠΠ°Π½Π½ΡΠ΅ Π²ΠΈΠ΄Ρ Π₯Π’Π ΡΡΡΠ΅ΡΡΠ²Π΅Π½Π½ΠΎ ΠΏΠΎΠ²ΡΡΠ°ΡΡ ΡΠ²Π΅ΡΠ΄ΠΎΡΡΡ, ΠΈΠ·Π½ΠΎΡΠΎΡΡΠΎΠΉΠΊΠΎΡΡΡ ΠΈΒ Π·Π°Π΄ΠΈΡΠΎΡΡΠΎΠΉΠΊΠΎΡΡΡ ΠΈΠ·Π΄Π΅Π»ΠΈΠΉ.
ΠΠ΅ΡΠΎΡΠΌΠ°ΡΠΈΠΎΠ½Π½ΠΎ-ΡΠ΅ΡΠΌΠΈΡΠ΅ΡΠΊΠ°Ρ ΠΎΠ±ΡΠ°Π±ΠΎΡΠΊΠ°: ΠΎΡΠΎΠ±Π΅Π½Π½ΠΎΡΡΠΈ ΠΈΒ Π²ΠΈΠ΄Ρ
Π Π°Π·Π½ΡΠ΅ Π²ΠΈΠ΄Ρ Π΄Π΅ΡΠΎΡΠΌΠ°ΡΠΈΠΎΠ½Π½ΠΎ-ΡΠ΅ΡΠΌΠΈΡΠ΅ΡΠΊΠΎΠΉ ΠΎΠ±ΡΠ°Π±ΠΎΡΠΊΠΈ ΡΠ°Π·Π΄Π΅Π»ΡΡΡΡΡ Π²Β Π·Π°-Π²ΠΈΡΠΈΠΌΠΎΡΡΠΈ ΠΎΡΒ Ρ Π°ΡΠ°ΠΊΡΠ΅ΡΠ° ΡΠ°Π·ΠΎΠ²ΡΡ ΠΏΡΠ΅Π²ΡΠ°ΡΠ΅Π½ΠΈΠΉ ΠΈΒ ΡΠΏΠΎΡΠΎΠ±Π° Π΄Π΅ΡΠΎΡΠΌΠ°ΡΠΈΠΈ, ΠΏΡΠΈΡΠ΅ΠΌ ΡΡΡΠ΅ΡΡΠ²Π΅Π½Π½ΠΎΠ΅ Π·Π½Π°ΡΠ΅Π½ΠΈΠ΅ ΠΈΠΌΠ΅Π΅Ρ, Π΄ΠΎΒ ΠΈΠ»ΠΈ ΠΏΠΎΡΠ»Π΅ Π΄Π΅ΡΠΎΡΠΌΠ°ΡΠΈΠΈ ΠΏΡΠΎΠΈΡΡ ΠΎΠ΄ΠΈΡ ΠΏΡΠ΅Π²ΡΠ°ΡΠ΅Π½ΠΈΠ΅, Π°Β ΡΠ°ΠΊΠΆΠ΅ Π²ΡΡΠ΅ ΠΈΠ»ΠΈ Π½ΠΈΠΆΠ΅ ΡΠ΅ΠΌΠΏΠ΅ΡΠ°ΡΡΡΡ ΡΠ΅ΠΊΡΠΈΡΡΠ°Π»Π»ΠΈΠ·Π°ΡΠΈΠΈ ΠΏΡΠΎΠΈΠ·Π²ΠΎΠ΄ΠΈΠ»Π°ΡΡ Π΄Π΅ΡΠΎΡΠΌΠ°ΡΠΈΡ.
ΠΡΠ»ΠΈ ΡΠ°Π·ΠΎΠ²ΠΎΠ΅ ΠΏΡΠ΅Π²ΡΠ°ΡΠ΅Π½ΠΈΠ΅ ΠΏΡΠΎΠΈΡΡ ΠΎΠ΄ΠΈΡ Π΄ΠΎΒ Π΄Π΅ΡΠΎΡΠΌΠ°ΡΠΈΠΈ, ΡΠ°ΠΊΠΎΠΉ Π²ΠΈΠ΄ ΠΎΠ±ΡΠ°Π±ΠΎΡΠΊΠΈ ΠΈΠΌΠ΅Π½ΡΠ΅ΡΡΡ ΠΌΠ΅Ρ Π°Π½ΠΎΡΠ΅ΡΠΌΠΈΡΠ΅ΡΠΊΠΎΠΉ ΠΎΠ±ΡΠ°Π±ΠΎΡΠΊΠΎΠΉ (ΠΠ’Π). ΠΠ΄Π½ΠΈΠΌ ΠΈΠ·Β Π½Π°ΠΈΠ±ΠΎΠ»Π΅Π΅ ΡΠ°ΡΠΏΡΠΎΡΡΡΠ°Π½ΡΠ½Π½ΡΡ Π²ΠΈΠ΄ΠΎΠ² ΠΠ’Π ΡΠ²Π»ΡΠ΅ΡΡΡ Ρ ΠΎΠ»ΠΎΠ΄Π½ΠΎΠ΅ Π²ΠΎΠ»ΠΎΡΠ΅Π½ΠΈΠ΅ ΠΏΡΠΎΠ²ΠΎΠ»ΠΎΠΊΠΈ ΠΏΠΎΡΠ»Π΅ ΠΏΠ°ΡΠ΅Π½ΡΠΈΡΠΎΠ²Π°Π½ΠΈΡ. ΠΒ ΠΠΠ Β«Π’Π΅Ρ Π½ΠΎΠΏΠ°ΡΠΊ ΠΠΌΠΏΡΠ»ΡΡΒ» ΠΈΠ·Β ΠΌΠ΅ΡΠΎΠ΄ΠΎΠ² ΠΠ’Π ΠΏΡΠΈΠΌΠ΅Π½ΡΠ΅ΡΡΡ ΠΏΡΠ΅ΠΈΠΌΡΡΠ΅ΡΡΠ²Π΅Π½Π½ΠΎ Π°Π»ΠΌΠ°Π·Π½ΠΎΠ΅ Π²ΡΠ³Π»Π°ΠΆΠΈΠ²Π°Π½ΠΈΠ΅.
ΠΡΠ»ΠΈΒ ΠΆΠ΅ ΠΏΡΠ΅Π²ΡΠ°ΡΠ΅Π½ΠΈΠ΅ ΠΏΡΠΎΠΈΡΡ
ΠΎΠ΄ΠΈΡ Π²ΠΎΒ Π²ΡΠ΅ΠΌΡ ΠΈΠ»ΠΈ ΠΏΠΎΡΠ»Π΅ Π΄Π΅ΡΠΎΡΠΌΠ°ΡΠΈΠΈ, ΡΠ°ΠΊΠΎΠΉ Π²ΠΈΠ΄ ΠΎΠ±ΡΠ°Π±ΠΎΡΠΊΠΈ ΠΈΠΌΠ΅Π½ΡΠ΅ΡΡΡ ΡΠ΅ΡΠΌΠΎΠΌΠ΅Ρ
Π°Π½ΠΈΡΠ΅ΡΠΊΠΎΠΉ ΠΎΠ±ΡΠ°Π±ΠΎΡΠΊΠΎΠΉ (Π’ΠΠ). ΠΒ Π·Π°Π²ΠΈΡΠΈΠΌΠΎΡΡΠΈ ΠΎΡΒ ΡΠ΅ΠΌΠΏΠ΅ΡΠ°ΡΡΡΡ Π΄Π΅ΡΠΎΡΠΌΠ°ΡΠΈΠΈ, ΡΠ°Π·Π»ΠΈΡΠ°ΡΡ Π²ΡΡΠΎΠΊΠΎΡΠ΅ΠΌΠΏΠ΅ΡΠ°ΡΡΡΠ½ΡΡ Π’ΠΠ (ΠΠ’ΠΠ), ΠΏΡΠΈ ΠΊΠΎΡΠΎΡΠΎΠΉ Π΄Π΅ΡΠΎΡΠΌΠ°ΡΠΈΡ ΠΏΡΠΎΠΈΠ·Π²ΠΎΠ΄ΠΈΡΡΡ Π²ΡΡΠ΅ ΡΠ΅ΠΌΠΏΠ΅ΡΠ°ΡΡΡΡ ΠΏΠΎΠ»ΠΈΠΌΠΎΡΡΠ½ΠΎΠ³ΠΎ ΠΏΡΠ΅Π²ΡΠ°ΡΠ΅Π½ΠΈΡ, ΠΈΒ Π½ΠΈΠ·ΠΊΠΎΡΠ΅ΠΌΠΏΠ΅ΡΠ°ΡΡΡΠ½ΡΡ Π’ΠΠ (ΠΠ’ΠΠ).
ΠΡΠΈ ΡΡΠΎΠΌ Π΄Π΅ΡΠΎΡΠΌΠ°ΡΠΈΡ ΠΏΡΠΎΠΈΠ·Π²ΠΎΠ΄ΠΈΡΡΡ Π½ΠΈΠΆΠ΅ ΡΠ΅ΠΌΠΏΠ΅ΡΠ°ΡΡΡΡ ΠΏΠΎΠ»ΠΈΠΌΠΎΡΡΠ½ΠΎΠ³ΠΎ ΠΏΡΠ΅Π²ΡΠ°ΡΠ΅Π½ΠΈΡ, Π½ΠΎΒ Π²ΡΡΠ΅ ΡΠ΅ΠΌΠΏΠ΅ΡΠ°ΡΡΡΡ ΠΌΠ°ΡΡΠ΅Π½ΡΠΈΡΠ½ΠΎΠ³ΠΎ ΠΏΡΠ΅Π²ΡΠ°ΡΠ΅Π½ΠΈΡ. ΠΒ ΠΠΠ Β«Π’Π΅Ρ Π½ΠΎΠΏΠ°ΡΠΊ ΠΠΌΠΏΡΠ»ΡΡΒ» Π’ΠΠ Π½Π΅Β ΠΏΡΠΈΠΌΠ΅Π½ΡΠ΅ΡΡΡ, ΠΏΠΎΡΡΠΎΠΌΡ Π½Π΅Ρ ΡΠΌΡΡΠ»Π° ΠΎΡΡΠ°Π½Π°Π²Π»ΠΈΠ²Π°ΡΡΡΡ Π½Π°Β Π½Π΅ΠΌ Π±ΠΎΠ»Π΅Π΅ ΠΏΠΎΠ΄ΡΠΎΠ±Π½ΠΎ.
ΠΡΒ ΠΌΠΎΠΆΠ΅ΡΠ΅ Π·Π°Π΄Π°ΡΡ ΡΠΏΠ΅ΡΠΈΠ°Π»ΠΈΡΡΠ°ΠΌ ΠΊΠΎΠΌΠΏΠ°Π½ΠΈΠΈ Π’Π΅Ρ Π½ΠΎΠΏΠ°ΡΠΊ Β«ΠΠΌΠΏΡΠ»ΡΡΒ» Π»ΡΠ±ΠΎΠΉ ΠΈΠ½ΡΠ΅ΡΠ΅ΡΡΡΡΠΈΠΉ Π²Π°Ρ Π²ΠΎΠΏΡΠΎΡ
ΠΠ°ΠΊΠ°Π»ΠΊΠ°, Π·Π°ΠΊΠ°Π»ΠΊΠ°, ΠΎΡΠΏΡΡΠΊ Π² ΠΠ΅ΡΠ»Π°Π±Π΅ Π£ΠΈΠ½Π΄ΠΌΡΡΠ°, ΠΠ΅Π½ΡΠΈΠ»ΡΠ²Π°Π½ΠΈΡ.
(Π½Π°ΠΆΠΌΠΈΡΠ΅ Π½Π° ΠΌΠΈΠ½ΠΈΠ°ΡΡΡΡ, ΡΡΠΎΠ±Ρ ΡΠ²Π΅Π»ΠΈΡΠΈΡΡ)
ΠΠ°ΠΊΠ°Π»ΠΊΠ° ΠΌΠ΅ΡΠ°Π»Π»Π° / ΠΠ°ΠΊΠ°Π»ΠΊΠ° ΠΌΠ΅ΡΠ°Π»Π»Π° / ΠΡΠΏΡΡΠΊ ΠΌΠ΅ΡΠ°Π»Π»Π°
Π’ΡΠΈ Π±ΠΎΠ»ΡΡΠΈΡ ΠΊΠΎΠΌΠΏΠ»Π΅ΠΊΡΠ° ΠΏΠΎΠ΄ΡΠΈΠΏΠ½ΠΈΠΊΠΎΠ² ΠΈΠ·Π²Π»Π΅ΠΊΠ°ΡΡΡΡ ΠΈΠ· ΠΏΠ΅ΡΠΈ Π½Π°ΡΠ³Π»Π΅ΡΠΎΠΆΠΈΠ²Π°Π½ΠΈΡ Metlab Π΄ΠΈΠ°ΠΌΠ΅ΡΡΠΎΠΌ 180 Π΄ΡΠΉΠΌΠΎΠ² ΠΈ Π²ΡΡΠΎΡΠΎΠΉ 156 Π΄ΡΠΉΠΌΠΎΠ² ΠΏΠΎΡΠ»Π΅ ΡΠ΅ΠΌΠΏΠ΅ΡΠ°ΡΡΡΡ Π·Π°ΠΊΠ°Π»ΠΊΠΈ (1550Β°F) Π΄Π»Ρ ΠΏΠΎΡΠ»Π΅Π΄ΡΡΡΠ΅ΠΉ Π·Π°ΠΊΠ°Π»ΠΊΠΈ Π² ΠΏΠ΅ΡΠ΅ΠΌΠ΅ΡΠΈΠ²Π°Π΅ΠΌΠΎΠΌ Π³ΠΎΡΡΡΠ΅ΠΌ ΠΌΠ°ΡΠ»Π΅. ΠΠ΅ΡΠ°Π»ΠΈ Π±ΡΠ»ΠΈ Π½Π°ΡΠ³Π»Π΅ΡΠΎΠΆΠ΅Π½Ρ Π΄ΠΎ Π³Π»ΡΠ±ΠΈΠ½Ρ ΠΊΠΎΡΠΏΡΡΠ° Π±ΠΎΠ»Π΅Π΅ 0,200 Π΄ΡΠΉΠΌΠ° ECD. ΠΠ΅Ρ ΠΏΡΠΈΡΠΏΠΎΡΠΎΠ±Π»Π΅Π½ΠΈΡ ΠΈ ΠΊΠΎΠΌΠΏΠΎΠ½Π΅Π½ΡΠΎΠ² ΡΠΎΡΡΠ°Π²Π»ΡΠ΅Ρ ΠΎΠΊΠΎΠ»ΠΎ 40 000 ΡΡΠ½ΡΠΎΠ².
ΠΠ°ΠΊΠ°Π»ΠΊΠ° ΠΌΠ΅ΡΠ°Π»Π»Π°
ΠΡΠΏΠΎΠ»ΡΠ·ΠΎΠ²Π°Π½ΠΈΠ΅ ΡΡΠΎΠΉ ΠΎΠ±ΡΠ°Π±ΠΎΡΠΊΠΈ ΠΏΡΠΈΠ²Π΅Π΄Π΅Ρ ΠΊ ΡΠ»ΡΡΡΠ΅Π½ΠΈΡ ΠΌΠ΅Ρ
Π°Π½ΠΈΡΠ΅ΡΠΊΠΈΡ
ΡΠ²ΠΎΠΉΡΡΠ², Π° ΡΠ°ΠΊΠΆΠ΅ ΠΊ ΠΏΠΎΠ²ΡΡΠ΅Π½ΠΈΡ ΡΡΠΎΠ²Π½Ρ ΡΠ²Π΅ΡΠ΄ΠΎΡΡΠΈ, Π² ΡΠ΅Π·ΡΠ»ΡΡΠ°ΡΠ΅ ΡΠ΅Π³ΠΎ ΠΈΠ·Π΄Π΅Π»ΠΈΠ΅ ΡΡΠ°Π½Π΅Ρ Π±ΠΎΠ»Π΅Π΅ ΠΏΡΠΎΡΠ½ΡΠΌ ΠΈ Π΄ΠΎΠ»Π³ΠΎΠ²Π΅ΡΠ½ΡΠΌ. Π‘ΠΏΠ»Π°Π²Ρ Π½Π°Π³ΡΠ΅Π²Π°ΡΡ Π²ΡΡΠ΅ ΠΊΡΠΈΡΠΈΡΠ΅ΡΠΊΠΎΠΉ ΡΠ΅ΠΌΠΏΠ΅ΡΠ°ΡΡΡΡ ΠΏΡΠ΅Π²ΡΠ°ΡΠ΅Π½ΠΈΡ ΠΌΠ°ΡΠ΅ΡΠΈΠ°Π»Π°, Π° Π·Π°ΡΠ΅ΠΌ Π΄ΠΎΡΡΠ°ΡΠΎΡΠ½ΠΎ Π±ΡΡΡΡΠΎ ΠΎΡ
Π»Π°ΠΆΠ΄Π°ΡΡ, ΡΡΠΎΠ±Ρ ΠΌΡΠ³ΠΊΠΈΠΉ ΠΈΡΡ
ΠΎΠ΄Π½ΡΠΉ ΠΌΠ°ΡΠ΅ΡΠΈΠ°Π» ΠΏΡΠ΅Π²ΡΠ°ΡΠΈΠ»ΡΡ Π² Π³ΠΎΡΠ°Π·Π΄ΠΎ Π±ΠΎΠ»Π΅Π΅ ΡΠ²Π΅ΡΠ΄ΡΡ ΠΈ ΠΏΡΠΎΡΠ½ΡΡ ΡΡΡΡΠΊΡΡΡΡ. Π‘ΠΏΠ»Π°Π²Ρ ΠΌΠΎΠ³ΡΡ ΠΎΡ
Π»Π°ΠΆΠ΄Π°ΡΡΡΡ Π½Π° Π²ΠΎΠ·Π΄ΡΡ
Π΅ ΠΈΠ»ΠΈ ΠΎΡ
Π»Π°ΠΆΠ΄Π°ΡΡΡΡ Π·Π°ΠΊΠ°Π»ΠΊΠΎΠΉ Π² ββΠΌΠ°ΡΠ»Π΅, Π²ΠΎΠ΄Π΅ ΠΈΠ»ΠΈ Π΄ΡΡΠ³ΠΎΠΉ ΠΆΠΈΠ΄ΠΊΠΎΡΡΠΈ, Π² Π·Π°Π²ΠΈΡΠΈΠΌΠΎΡΡΠΈ ΠΎΡ ΠΊΠΎΠ»ΠΈΡΠ΅ΡΡΠ²Π° Π»Π΅Π³ΠΈΡΡΡΡΠΈΡ
ΡΠ»Π΅ΠΌΠ΅Π½ΡΠΎΠ² Π² ΠΌΠ°ΡΠ΅ΡΠΈΠ°Π»Π΅. ΠΠ°ΠΊΠ°Π»Π΅Π½Π½ΡΠ΅ ΠΌΠ°ΡΠ΅ΡΠΈΠ°Π»Ρ ΠΎΠ±ΡΡΠ½ΠΎ ΠΏΠΎΠ΄Π²Π΅ΡΠ³Π°ΡΡ ΠΎΡΠΏΡΡΠΊΡ ΠΈΠ»ΠΈ ΡΠ½ΡΡΠΈΡ Π½Π°ΠΏΡΡΠΆΠ΅Π½ΠΈΡ Π΄Π»Ρ ΡΠ»ΡΡΡΠ΅Π½ΠΈΡ ΠΈΡ
ΡΠ°Π·ΠΌΠ΅ΡΠ½ΠΎΠΉ ΡΡΠ°Π±ΠΈΠ»ΡΠ½ΠΎΡΡΠΈ ΠΈ ΡΠ΄Π°ΡΠ½ΠΎΠΉ Π²ΡΠ·ΠΊΠΎΡΡΠΈ.
Π‘ΡΠ°Π»ΡΠ½ΡΠ΅ Π΄Π΅ΡΠ°Π»ΠΈ ΡΠ°ΡΡΠΎ ΡΡΠ΅Π±ΡΡΡ ΡΠ΅ΡΠΌΠΈΡΠ΅ΡΠΊΠΎΠΉ ΠΎΠ±ΡΠ°Π±ΠΎΡΠΊΠΈ Π΄Π»Ρ ΠΏΠΎΠ»ΡΡΠ΅Π½ΠΈΡ ΡΠ»ΡΡΡΠ΅Π½Π½ΡΡ
ΠΌΠ΅Ρ
Π°Π½ΠΈΡΠ΅ΡΠΊΠΈΡ
ΡΠ²ΠΎΠΉΡΡΠ², ΡΠ°ΠΊΠΈΡ
ΠΊΠ°ΠΊ ΠΏΠΎΠ²ΡΡΠ΅Π½ΠΈΠ΅ ΡΠ²Π΅ΡΠ΄ΠΎΡΡΠΈ ΠΈΠ»ΠΈ ΠΏΡΠΎΡΠ½ΠΎΡΡΠΈ. ΠΡΠΎΡΠ΅ΡΡ Π·Π°ΠΊΠ°Π»ΠΊΠΈ ΡΠΎΡΡΠΎΠΈΡ ΠΈΠ· Π½Π°Π³ΡΠ΅Π²Π° ΠΊΠΎΠΌΠΏΠΎΠ½Π΅Π½ΡΠΎΠ² Π²ΡΡΠ΅ ΠΊΡΠΈΡΠΈΡΠ΅ΡΠΊΠΎΠΉ (Π½ΠΎΡΠΌΠ°Π»ΠΈΠ·ΡΡΡΠ΅ΠΉ) ΡΠ΅ΠΌΠΏΠ΅ΡΠ°ΡΡΡΡ, Π²ΡΠ΄Π΅ΡΠΆΠΊΠΈ ΠΏΡΠΈ ΡΡΠΎΠΉ ΡΠ΅ΠΌΠΏΠ΅ΡΠ°ΡΡΡΠ΅ Π² ΡΠ΅ΡΠ΅Π½ΠΈΠ΅ ΠΎΠ΄Π½ΠΎΠ³ΠΎ ΡΠ°ΡΠ° Π½Π° Π΄ΡΠΉΠΌ ΡΠΎΠ»ΡΠΈΠ½Ρ, ΠΎΡ
Π»Π°ΠΆΠ΄Π΅Π½ΠΈΡ ΡΠΎ ΡΠΊΠΎΡΠΎΡΡΡΡ, Π΄ΠΎΡΡΠ°ΡΠΎΡΠ½ΠΎΠΉ Π΄Π»Ρ ΡΠΎΠ³ΠΎ, ΡΡΠΎΠ±Ρ ΠΌΠ°ΡΠ΅ΡΠΈΠ°Π» ΠΏΡΠ΅Π²ΡΠ°ΡΠΈΠ»ΡΡ Π² Π³ΠΎΡΠ°Π·Π΄ΠΎ Π±ΠΎΠ»Π΅Π΅ ΡΠ²Π΅ΡΠ΄ΡΡ ΠΈ ΠΏΡΠΎΡΠ½ΡΡ ΡΡΡΡΠΊΡΡΡΡ, Π° Π·Π°ΡΠ΅ΠΌ ΠΎΡΠΏΡΡΠΊΠ°. . Π‘ΡΠ°Π»Ρ ΠΏΠΎ ΡΡΡΠ΅ΡΡΠ²Ρ ΠΏΡΠ΅Π΄ΡΡΠ°Π²Π»ΡΠ΅Ρ ΡΠΎΠ±ΠΎΠΉ ΡΠΏΠ»Π°Π² ΠΆΠ΅Π»Π΅Π·Π° ΠΈ ΡΠ³Π»Π΅ΡΠΎΠ΄Π°; Π΄ΡΡΠ³ΠΈΠ΅ ΡΡΠ°Π»ΡΠ½ΡΠ΅ ΡΠΏΠ»Π°Π²Ρ ΠΈΠΌΠ΅ΡΡ Π΄ΡΡΠ³ΠΈΠ΅ ΠΌΠ΅ΡΠ°Π»Π»ΠΈΡΠ΅ΡΠΊΠΈΠ΅ ΡΠ»Π΅ΠΌΠ΅Π½ΡΡ Π² ΡΠ°ΡΡΠ²ΠΎΡΠ΅. ΠΠ°Π³ΡΠ΅Π² ΠΌΠ°ΡΠ΅ΡΠΈΠ°Π»Π° Π²ΡΡΠ΅ ΠΊΡΠΈΡΠΈΡΠ΅ΡΠΊΠΎΠΉ ΡΠ΅ΠΌΠΏΠ΅ΡΠ°ΡΡΡΡ ΠΏΡΠΈΠ²ΠΎΠ΄ΠΈΡ ΠΊ ΡΠΎΠΌΡ, ΡΡΠΎ ΡΠ³Π»Π΅ΡΠΎΠ΄ ΠΈ Π΄ΡΡΠ³ΠΈΠ΅ ΡΠ»Π΅ΠΌΠ΅Π½ΡΡ ΠΏΠ΅ΡΠ΅Ρ
ΠΎΠ΄ΡΡ Π² ΡΠ²Π΅ΡΠ΄ΡΠΉ ΡΠ°ΡΡΠ²ΠΎΡ. ΠΠ°ΠΊΠ°Π»ΠΊΠ° Β«Π·Π°ΠΌΠΎΡΠ°ΠΆΠΈΠ²Π°Π΅ΡΒ» ΠΌΠΈΠΊΡΠΎΡΡΡΡΠΊΡΡΡΡ, Π²ΡΠ·ΡΠ²Π°Ρ Π½Π°ΠΏΡΡΠΆΠ΅Π½ΠΈΡ. ΠΠ΅ΡΠ°Π»ΠΈ Π²ΠΏΠΎΡΠ»Π΅Π΄ΡΡΠ²ΠΈΠΈ Π·Π°ΠΊΠ°Π»ΡΡΡΡΡ Π΄Π»Ρ ΠΏΡΠ΅ΠΎΠ±ΡΠ°Π·ΠΎΠ²Π°Π½ΠΈΡ ΠΌΠΈΠΊΡΠΎΡΡΡΡΠΊΡΡΡΡ, Π΄ΠΎΡΡΠΈΠΆΠ΅Π½ΠΈΡ ΡΠΎΠΎΡΠ²Π΅ΡΡΡΠ²ΡΡΡΠ΅ΠΉ ΡΠ²Π΅ΡΠ΄ΠΎΡΡΠΈ ΠΈ ΡΡΡΡΠ°Π½Π΅Π½ΠΈΡ Π½Π°ΠΏΡΡΠΆΠ΅Π½ΠΈΠΉ.
ΠΠ°ΠΊΠ°Π»ΠΊΠ° ΠΌΠ΅ΡΠ°Π»Π»Π°
ΠΠ°ΡΠ΅ΡΠΈΠ°Π» Π½Π°Π³ΡΠ΅Π²Π°Π΅ΡΡΡ Π΄ΠΎ ΠΏΠΎΠ΄Ρ ΠΎΠ΄ΡΡΠ΅ΠΉ ΡΠ΅ΠΌΠΏΠ΅ΡΠ°ΡΡΡΡ, Π° Π·Π°ΡΠ΅ΠΌ Π·Π°ΠΊΠ°Π»ΠΈΠ²Π°Π΅ΡΡΡ Π² Π²ΠΎΠ΄Π΅ ΠΈΠ»ΠΈ ΠΌΠ°ΡΠ»Π΅ Π΄Π»Ρ Π·Π°ΡΠ²Π΅ΡΠ΄Π΅Π²Π°Π½ΠΈΡ Π΄ΠΎ ΠΏΠΎΠ»Π½ΠΎΠΉ ΡΠ²Π΅ΡΠ΄ΠΎΡΡΠΈ Π² Π·Π°Π²ΠΈΡΠΈΠΌΠΎΡΡΠΈ ΠΎΡ ΡΠΈΠΏΠ° ΡΡΠ°Π»ΠΈ.
ΠΠ°ΡΠ΅ΡΠΈΠ°Π» Π½Π°Π³ΡΠ΅Π²Π°ΡΡ Π΄ΠΎ ΡΠ΅ΠΌΠΏΠ΅ΡΠ°ΡΡΡΡ, ΠΏΠΎΠ΄Ρ ΠΎΠ΄ΡΡΠ΅ΠΉ Π΄Π»Ρ Π·Π°ΡΠ²Π΅ΡΠ΄Π΅Π²Π°Π½ΠΈΡ, Π·Π°ΡΠ΅ΠΌ Π±ΡΡΡΡΠΎ ΠΎΡ Π»Π°ΠΆΠ΄Π°ΡΡ, ΠΏΠΎΠ³ΡΡΠΆΠ°Ρ Π³ΠΎΡΡΡΡΡ ΡΠ°ΡΡΡ Π² Π²ΠΎΠ΄Ρ, ΠΌΠ°ΡΠ»ΠΎ ΠΈΠ»ΠΈ Π΄ΡΡΠ³ΡΡ ΠΏΠΎΠ΄Ρ ΠΎΠ΄ΡΡΡΡ ΠΆΠΈΠ΄ΠΊΠΎΡΡΡ, ΡΡΠΎΠ±Ρ ΠΏΡΠ΅ΠΎΠ±ΡΠ°Π·ΠΎΠ²Π°ΡΡ ΠΌΠ°ΡΠ΅ΡΠΈΠ°Π» Π² ΠΏΠΎΠ»Π½ΠΎΡΡΡΡ Π·Π°ΡΠ²Π΅ΡΠ΄Π΅Π²ΡΡΡ ΡΡΡΡΠΊΡΡΡΡ. ΠΠ΅ΡΠ°Π»ΠΈ, ΠΏΠΎΠ΄Π²Π΅ΡΠ³Π°ΡΡΠΈΠ΅ΡΡ Π·Π°ΠΊΠ°Π»ΠΊΠ΅, ΠΎΠ±ΡΡΠ½ΠΎ Π΄ΠΎΠ»ΠΆΠ½Ρ Π±ΡΡΡ ΡΠΎΡΡΠ°ΡΠ΅Π½Ρ, ΠΎΡΠΏΡΡΠ΅Π½Ρ ΠΈΠ»ΠΈ ΡΠ½ΡΡΡ Π½Π°ΠΏΡΡΠΆΠ΅Π½ΠΈΡ Π΄Π»Ρ Π΄ΠΎΡΡΠΈΠΆΠ΅Π½ΠΈΡ Π½Π°Π΄Π»Π΅ΠΆΠ°ΡΠ΅ΠΉ ΡΠ΄Π°ΡΠ½ΠΎΠΉ Π²ΡΠ·ΠΊΠΎΡΡΠΈ, ΠΎΠΊΠΎΠ½ΡΠ°ΡΠ΅Π»ΡΠ½ΠΎΠΉ ΡΠ²Π΅ΡΠ΄ΠΎΡΡΠΈ ΠΈ ΡΡΠ°Π±ΠΈΠ»ΡΠ½ΠΎΡΡΠΈ ΡΠ°Π·ΠΌΠ΅ΡΠΎΠ².
Π‘ΠΏΠ»Π°Π²Ρ ΠΌΠΎΠ³ΡΡ ΠΎΡ
Π»Π°ΠΆΠ΄Π°ΡΡΡΡ Π½Π° Π²ΠΎΠ·Π΄ΡΡ
Π΅ ΠΈΠ»ΠΈ ΠΎΡ
Π»Π°ΠΆΠ΄Π°ΡΡΡΡ Π·Π°ΠΊΠ°Π»ΠΊΠΎΠΉ Π² ββΠΌΠ°ΡΠ»Π΅, Π²ΠΎΠ΄Π΅ ΠΈΠ»ΠΈ Π΄ΡΡΠ³ΠΎΠΉ ΠΆΠΈΠ΄ΠΊΠΎΡΡΠΈ, Π² Π·Π°Π²ΠΈΡΠΈΠΌΠΎΡΡΠΈ ΠΎΡ ΠΊΠΎΠ»ΠΈΡΠ΅ΡΡΠ²Π° Π»Π΅Π³ΠΈΡΡΡΡΠΈΡ
ΡΠ»Π΅ΠΌΠ΅Π½ΡΠΎΠ² Π² ΠΌΠ°ΡΠ΅ΡΠΈΠ°Π»Π΅ ΠΈ ΡΡΠ΅Π±ΡΠ΅ΠΌΡΡ
ΠΊΠΎΠ½Π΅ΡΠ½ΡΡ
ΠΌΠ΅Ρ
Π°Π½ΠΈΡΠ΅ΡΠΊΠΈΡ
ΡΠ²ΠΎΠΉΡΡΠ². ΠΠ°ΠΊΠ°Π»Π΅Π½Π½ΡΠ΅ ΠΌΠ°ΡΠ΅ΡΠΈΠ°Π»Ρ Π·Π°ΠΊΠ°Π»ΡΡΡΡΡ Π΄Π»Ρ ΡΠ»ΡΡΡΠ΅Π½ΠΈΡ ΠΈΡ
ΡΠ°Π·ΠΌΠ΅ΡΠ½ΠΎΠΉ ΡΡΠ°Π±ΠΈΠ»ΡΠ½ΠΎΡΡΠΈ ΠΈ ΡΠ΄Π°ΡΠ½ΠΎΠΉ Π²ΡΠ·ΠΊΠΎΡΡΠΈ.
ΠΠ°ΠΊΠ°Π»ΠΊΠ° ΠΌΠ΅ΡΠ°Π»Π»Π°
ΠΡΠΏΡΡΠΊ ΠΏΡΠΎΠ²ΠΎΠ΄ΠΈΡΡΡ Π΄Π»Ρ ΠΏΠΎΠ»ΡΡΠ΅Π½ΠΈΡ ΡΡΠ΅Π±ΡΠ΅ΠΌΠΎΠ³ΠΎ ΡΠΎΡΠ΅ΡΠ°Π½ΠΈΡ ΡΠ²Π΅ΡΠ΄ΠΎΡΡΠΈ, ΠΏΡΠΎΡΠ½ΠΎΡΡΠΈ ΠΈ ΡΠ΄Π°ΡΠ½ΠΎΠΉ Π²ΡΠ·ΠΊΠΎΡΡΠΈ ΠΈΠ»ΠΈ Π΄Π»Ρ ΡΠ½ΠΈΠΆΠ΅Π½ΠΈΡ Ρ ΡΡΠΏΠΊΠΎΡΡΠΈ ΠΏΠΎΠ»Π½ΠΎΡΡΡΡ Π·Π°ΠΊΠ°Π»Π΅Π½Π½ΡΡ ΡΡΠ°Π»Π΅ΠΉ. Π‘ΡΠ°Π»ΠΈ Π½ΠΈΠΊΠΎΠ³Π΄Π° Π½Π΅ ΠΈΡΠΏΠΎΠ»ΡΠ·ΡΡΡΡΡ Π² Π·Π°ΠΊΠ°Π»Π΅Π½Π½ΠΎΠΌ ΡΠΎΡΡΠΎΡΠ½ΠΈΠΈ. Π‘ΠΎΡΠ΅ΡΠ°Π½ΠΈΠ΅ Π·Π°ΠΊΠ°Π»ΠΊΠΈ ΠΈ ΠΎΡΠΏΡΡΠΊΠ° Π²Π°ΠΆΠ½ΠΎ Π΄Π»Ρ ΠΈΠ·Π³ΠΎΡΠΎΠ²Π»Π΅Π½ΠΈΡ ΠΏΡΠΎΡΠ½ΡΡ Π΄Π΅ΡΠ°Π»Π΅ΠΉ.
ΠΡΠ° ΠΎΠ±ΡΠ°Π±ΠΎΡΠΊΠ° ΡΠ»Π΅Π΄ΡΠ΅Ρ Π·Π° Π·Π°ΠΊΠ°Π»ΠΊΠΎΠΉ ΠΈΠ»ΠΈ ΠΎΡ Π»Π°ΠΆΠ΄Π΅Π½ΠΈΠ΅ΠΌ Π½Π° Π²ΠΎΠ·Π΄ΡΡ Π΅. ΠΡΠΏΡΡΠΊ ΠΎΠ±ΡΡΠ½ΠΎ ΡΡΠΈΡΠ°Π΅ΡΡΡ ΡΡΡΠ΅ΠΊΡΠΈΠ²Π½ΡΠΌ Π΄Π»Ρ ΡΠ½ΡΡΠΈΡ Π½Π°ΠΏΡΡΠΆΠ΅Π½ΠΈΠΉ, Π²ΡΠ·Π²Π°Π½Π½ΡΡ Π·Π°ΠΊΠ°Π»ΠΊΠΎΠΉ, Π² Π΄ΠΎΠΏΠΎΠ»Π½Π΅Π½ΠΈΠ΅ ΠΊ ΡΠ½ΠΈΠΆΠ΅Π½ΠΈΡ ΡΠ²Π΅ΡΠ΄ΠΎΡΡΠΈ Π΄ΠΎ ΠΎΠΏΡΠ΅Π΄Π΅Π»Π΅Π½Π½ΠΎΠ³ΠΎ Π΄ΠΈΠ°ΠΏΠ°Π·ΠΎΠ½Π° ΠΈΠ»ΠΈ ΡΠ΄ΠΎΠ²Π»Π΅ΡΠ²ΠΎΡΠ΅Π½ΠΈΡ ΠΎΠΏΡΠ΅Π΄Π΅Π»Π΅Π½Π½ΡΡ ΡΡΠ΅Π±ΠΎΠ²Π°Π½ΠΈΠΉ ΠΊ ΠΌΠ΅Ρ Π°Π½ΠΈΡΠ΅ΡΠΊΠΈΠΌ ΡΠ²ΠΎΠΉΡΡΠ²Π°ΠΌ.
ΠΡΠΏΡΡΠΊ β ΡΡΠΎ ΠΏΡΠΎΡΠ΅ΡΡ ΠΏΠΎΠ²ΡΠΎΡΠ½ΠΎΠ³ΠΎ Π½Π°Π³ΡΠ΅Π²Π° ΡΡΠ°Π»ΠΈ ΠΏΡΠΈ ΠΎΡΠ½ΠΎΡΠΈΡΠ΅Π»ΡΠ½ΠΎ Π½ΠΈΠ·ΠΊΠΎΠΉ ΡΠ΅ΠΌΠΏΠ΅ΡΠ°ΡΡΡΠ΅, ΠΏΡΠΈΠ²ΠΎΠ΄ΡΡΠΈΠΉ ΠΊ ΠΎΡΠ°ΠΆΠ΄Π΅Π½ΠΈΡ ΠΈ ΡΡΠ΅ΡΠΎΠΈΠ΄ΠΈΠ·Π°ΡΠΈΠΈ ΠΊΠ°ΡΠ±ΠΈΠ΄ΠΎΠ², ΠΏΡΠΈΡΡΡΡΡΠ²ΡΡΡΠΈΡ
Π² ΠΌΠΈΠΊΡΠΎΡΡΡΡΠΊΡΡΡΠ΅. Π’Π΅ΠΌΠΏΠ΅ΡΠ°ΡΡΡΠ° ΠΈ Π²ΡΠ΅ΠΌΡ ΠΎΡΠΏΡΡΠΊΠ° ΠΎΠ±ΡΡΠ½ΠΎ ΠΊΠΎΠ½ΡΡΠΎΠ»ΠΈΡΡΡΡΡΡ Π΄Π»Ρ ΠΏΠΎΠ»ΡΡΠ΅Π½ΠΈΡ ΠΎΠΊΠΎΠ½ΡΠ°ΡΠ΅Π»ΡΠ½ΡΡ
ΡΠ²ΠΎΠΉΡΡΠ², ΡΡΠ΅Π±ΡΠ΅ΠΌΡΡ
ΠΎΡ ΡΡΠ°Π»ΠΈ. Π ΡΠ΅Π·ΡΠ»ΡΡΠ°ΡΠ΅ ΠΏΠΎΠ»ΡΡΠ°Π΅ΡΡΡ ΠΊΠΎΠΌΠΏΠΎΠ½Π΅Π½Ρ Ρ ΠΏΠΎΠ΄Ρ
ΠΎΠ΄ΡΡΠΈΠΌ ΡΠΎΡΠ΅ΡΠ°Π½ΠΈΠ΅ΠΌ ΡΠ²Π΅ΡΠ΄ΠΎΡΡΠΈ, ΠΏΡΠΎΡΠ½ΠΎΡΡΠΈ ΠΈ ΡΠ΄Π°ΡΠ½ΠΎΠΉ Π²ΡΠ·ΠΊΠΎΡΡΠΈ Π΄Π»Ρ ΠΏΡΠ΅Π΄ΠΏΠΎΠ»Π°Π³Π°Π΅ΠΌΠΎΠ³ΠΎ ΠΏΡΠΈΠΌΠ΅Π½Π΅Π½ΠΈΡ. ΠΡΠΏΡΡΠΊ ΡΠ°ΠΊΠΆΠ΅ ΡΡΡΠ΅ΠΊΡΠΈΠ²Π΅Π½ Π΄Π»Ρ ΡΠ½ΡΡΠΈΡ Π½Π°ΠΏΡΡΠΆΠ΅Π½ΠΈΠΉ, Π²ΡΠ·Π²Π°Π½Π½ΡΡ
Π·Π°ΠΊΠ°Π»ΠΊΠΎΠΉ.
ΠΠ±ΡΠ΅ΠΊΡΡ
ΠΡΠΊΡΡΡΠ°Ρ ΠΈΠ»ΠΈ Π·Π°ΠΊΡΡΡΠ°Ρ ΠΏΠ΅ΡΡ β Π·Π°ΠΊΠ°Π»ΠΊΠ°, ΠΎΡΠΆΠΈΠ³, Π½ΠΎΡΠΌΠ°Π»ΠΈΠ·Π°ΡΠΈΡ, ΠΎΠ±ΡΠ°Π±ΠΎΡΠΊΠ° Π½Π° ΡΠ²Π΅ΡΠ΄ΡΠΉ ΡΠ°ΡΡΠ²ΠΎΡ ΠΈ Ρ. Π΄. Π΄ΠΎ 2200Β°F
- Π¨Π°Ρ ΡΠ½Π°Ρ ΠΏΠ΅ΡΡ — Π΄ΠΈΠ°ΠΌΠ΅ΡΡ 144 Π΄ΡΠΉΠΌΠ° ΠΈ Π²ΡΡΠΎΡΠ° 96 Π΄ΡΠΉΠΌΠΎΠ²
- Π¨Π°Ρ ΡΠ½Π°Ρ ΠΏΠ΅ΡΡ — Π΄ΠΈΠ°ΠΌΠ΅ΡΡ 180 Π΄ΡΠΉΠΌΠΎΠ² ΠΈ Π²ΡΡΠΎΡΠ° 156 Π΄ΡΠΉΠΌΠΎΠ²
- Π¨Π°Ρ ΡΠ½Π°Ρ ΠΏΠ΅ΡΡ (2) β Π΄ΠΈΠ°ΠΌΠ΅ΡΡ 54 Π΄ΡΠΉΠΌΠ° ΠΈ Π²ΡΡΠΎΡΠ° 180 Π΄ΡΠΉΠΌΠΎΠ²
- ΠΠΎΠ»ΠΏΠ°ΠΊΠΎΠ²ΡΠ΅ ΠΏΠ΅ΡΠΈ (4) β Π΄ΠΈΠ°ΠΌΠ΅ΡΡ 72 Π΄ΡΠΉΠΌΠ° ΠΈ Π²ΡΡΠΎΡΠ° 84 Π΄ΡΠΉΠΌΠ°
- ΠΡΡΡΠΎΠ΅Π½Π½ΡΠ΅ ΠΏΠ΅ΡΠΈ Π΄Π»Ρ Π·Π°ΠΊΠ°Π»ΠΊΠΈ Π² ΠΌΠ°ΡΠ»Π΅ — Π²ΡΡΠΎΡΠ° 24″ x 36″ x 24″, Π²ΡΡΠΎΡΠ° 18″ x 24″ x 18″
- ΠΠ΅ΡΡ Ρ Π²ΡΠ°ΡΠ°ΡΡΠΈΠΌΡΡ ΠΏΠΎΠ΄ΠΎΠΌ ΠΈ Π·Π°ΠΊΠ°Π»ΠΎΡΠ½ΡΠΉ ΠΏΡΠ΅ΡΡ β ΠΠ΅ΡΠ°Π»ΠΈ Π΄ΠΈΠ°ΠΌΠ΅ΡΡΠΎΠΌ Π΄ΠΎ 16 Π΄ΡΠΉΠΌΠΎΠ²
- ΠΠ°ΠΊΡΡΠΌΠ½Π°Ρ ΠΏΠ΅ΡΡ — Π²Π½Π΅ΡΠ½ΠΈΠΉ Π΄ΠΈΠ°ΠΌΠ΅ΡΡ 24 Π΄ΡΠΉΠΌΠ° x Π³Π»ΡΠ±ΠΈΠ½Π° 24 Π΄ΡΠΉΠΌΠ°
Π²Π΅ΡΠ½ΡΡΡΡΡ ΠΊ Π½Π°ΡΠ°Π»Ρ
ΠΌΠ΅ΡΠ°Π»Π»ΡΡΠ³ΠΈΡ | ΠΠΏΡΠ΅Π΄Π΅Π»Π΅Π½ΠΈΠ΅ ΠΈ ΠΈΡΡΠΎΡΠΈΡ
ΠΌΠ΅ΡΠ°Π»Π»ΡΡΠ³ΠΈΡ
Π‘ΠΌΠΎΡΡΠ΅ΡΡ Π²ΡΠ΅ Π‘ΠΠ
- ΠΠ»ΡΡΠ΅Π²ΡΠ΅ Π»ΡΠ΄ΠΈ:
- ΠΠΈΡ
Π°ΠΈΠ» ΠΠΎΠΌΠΎΠ½ΠΎΡΠΎΠ²
ΠΠ΅ΠΎΡΠ³ΠΈΡΡ ΠΠ³ΡΠΈΠΊΠΎΠ»Π°
ΠΡΠ½ΠΈΠ΅Π» ΠΠΎΡΡΠ½ ΠΠΆΠ΅ΠΊΠ»ΠΈΠ½Π³
Π‘ΡΡ ΠΠ»Π°Π½ ΠΠΎΡΡΡΠ΅Π»Π»
ΠΡΠ΄Π΅Π½ Π.
ΠΠ΅ΠΌΠ΅Π½Ρ-ΠΌΠ»Π°Π΄ΡΠΈΠΉ
- ΠΠΎΡ ΠΎΠΆΠΈΠ΅ ΡΠ΅ΠΌΡ:
- ΠΌΠ΅ΡΠ°Π»Π»ΠΎΠΊΠΎΠ½ΡΡΡΡΠΊΡΠΈΠΈ ΠΏΠ΅ΡΠ΅ΡΠ°Π±ΠΎΡΠΊΠ° ΠΏΠΎΠ»Π΅Π·Π½ΡΡ ΠΈΡΠΊΠΎΠΏΠ°Π΅ΠΌΡΡ ΠΌΠ΅ΡΠ°Π»Π»ΠΎΠ³ΡΠ°ΡΠΈΡ ΡΠΈΠ·ΠΈΡΠ΅ΡΠΊΠ°Ρ ΠΌΠ΅ΡΠ°Π»Π»ΡΡΠ³ΠΈΡ ΡΠ΅Ρ Π½ΠΎΠ»ΠΎΠ³ΠΈΡΠ΅ΡΠΊΠ°Ρ ΠΌΠ΅ΡΠ°Π»Π»ΡΡΠ³ΠΈΡ
ΠΡΠΎΡΠΌΠΎΡΡΠ΅ΡΡ Π²Π΅ΡΡ ΡΠ²ΡΠ·Π°Π½Π½ΡΠΉ ΠΊΠΎΠ½ΡΠ΅Π½Ρ β
Π Π΅Π·ΡΠΌΠ΅
ΠΡΠΎΡΡΠΈΡΠ΅ ΠΊΡΠ°ΡΠΊΠΈΠΉ ΠΎΠ±Π·ΠΎΡ ΡΡΠΎΠΉ ΡΠ΅ΠΌΡ
ΠΌΠ΅ΡΠ°Π»Π»ΡΡΠ³ΠΈΡ ΠΡΠΊΡΡΡΡΠ²ΠΎ ΠΈ Π½Π°ΡΠΊΠ° ΠΏΠΎ ΠΈΠ·Π²Π»Π΅ΡΠ΅Π½ΠΈΡ ΠΌΠ΅ΡΠ°Π»Π»ΠΎΠ² ΠΈΠ· ΡΡΠ΄ ΠΈ ΠΌΠΎΠ΄ΠΈΡΠΈΠΊΠ°ΡΠΈΠΈ ΠΌΠ΅ΡΠ°Π»Π»ΠΎΠ² Π΄Π»Ρ ΠΈΡΠΏΠΎΠ»ΡΠ·ΠΎΠ²Π°Π½ΠΈΡ. ΠΠ΅ΡΠ°Π»Π»ΡΡΠ³ΠΈΡ ΠΎΠ±ΡΡΠ½ΠΎ ΠΎΡΠ½ΠΎΡΠΈΡΡΡ ΠΊ ΠΊΠΎΠΌΠΌΠ΅ΡΡΠ΅ΡΠΊΠΈΠΌ, Π° Π½Π΅ ΠΊ Π»Π°Π±ΠΎΡΠ°ΡΠΎΡΠ½ΡΠΌ ΠΌΠ΅ΡΠΎΠ΄Π°ΠΌ. ΠΡΠΎ ΡΠ°ΠΊΠΆΠ΅ ΠΊΠ°ΡΠ°Π΅ΡΡΡ Ρ ΠΈΠΌΠΈΡΠ΅ΡΠΊΠΈΡ , ΡΠΈΠ·ΠΈΡΠ΅ΡΠΊΠΈΡ ΠΈ Π°ΡΠΎΠΌΠ½ΡΡ ΡΠ²ΠΎΠΉΡΡΠ² ΠΈ ΡΡΡΡΠΊΡΡΡΡ ΠΌΠ΅ΡΠ°Π»Π»ΠΎΠ², Π° ΡΠ°ΠΊΠΆΠ΅ ΠΏΡΠΈΠ½ΡΠΈΠΏΠΎΠ², ΠΏΠΎ ΠΊΠΎΡΠΎΡΡΠΌ ΠΌΠ΅ΡΠ°Π»Π»Ρ ΠΎΠ±ΡΠ΅Π΄ΠΈΠ½ΡΡΡΡΡ Π² ΡΠΏΠ»Π°Π²Ρ.
ΠΡΡΠΎΡΠΈΡ ΠΌΠ΅ΡΠ°Π»Π»ΡΡΠ³ΠΈΠΈ
Π‘ΠΎΠ²ΡΠ΅ΠΌΠ΅Π½Π½ΠΎΠ΅ ΠΈΡΠΏΠΎΠ»ΡΠ·ΠΎΠ²Π°Π½ΠΈΠ΅ ΠΌΠ΅ΡΠ°Π»Π»ΠΎΠ² ΡΠ²Π»ΡΠ΅ΡΡΡ ΠΊΡΠ»ΡΠΌΠΈΠ½Π°ΡΠΈΠ΅ΠΉ Π΄ΠΎΠ»Π³ΠΎΠ³ΠΎ ΠΏΡΡΠΈ ΡΠ°Π·Π²ΠΈΡΠΈΡ, ΡΠ°ΡΡΡΠ½ΡΠ²ΡΠ΅Π³ΠΎΡΡ ΠΏΡΠΈΠΌΠ΅ΡΠ½ΠΎ Π½Π° 6500 Π»Π΅Ρ. ΠΡΠΈΠ½ΡΡΠΎ ΡΡΠΈΡΠ°ΡΡ, ΡΡΠΎ ΠΏΠ΅ΡΠ²ΡΠΌΠΈ ΠΈΠ·Π²Π΅ΡΡΠ½ΡΠΌΠΈ ΠΌΠ΅ΡΠ°Π»Π»Π°ΠΌΠΈ Π±ΡΠ»ΠΈ Π·ΠΎΠ»ΠΎΡΠΎ, ΡΠ΅ΡΠ΅Π±ΡΠΎ ΠΈ ΠΌΠ΅Π΄Ρ, Π½Π°Ρ
ΠΎΠ΄ΠΈΠ²ΡΠΈΠ΅ΡΡ Π² ΡΠ°ΠΌΠΎΡΠΎΠ΄Π½ΠΎΠΌ ΠΈΠ»ΠΈ ΠΌΠ΅ΡΠ°Π»Π»ΠΈΡΠ΅ΡΠΊΠΎΠΌ ΡΠΎΡΡΠΎΡΠ½ΠΈΠΈ, ΠΈΠ· ΠΊΠΎΡΠΎΡΡΡ
ΡΠ°ΠΌΡΠΌΠΈ ΡΠ°Π½Π½ΠΈΠΌΠΈ, ΠΏΠΎ Π²ΡΠ΅ΠΉ Π²Π΅ΡΠΎΡΡΠ½ΠΎΡΡΠΈ, Π±ΡΠ»ΠΈ ΡΠ°ΠΌΠΎΡΠΎΠ΄ΠΊΠΈ Π·ΠΎΠ»ΠΎΡΠ°, Π½Π°ΠΉΠ΄Π΅Π½Π½ΡΠ΅ Π² ΠΏΠ΅ΡΠΊΠ°Ρ
ΠΈ Π³ΡΠ°Π²ΠΈΠΈ Π² ΡΡΡΠ»Π°Ρ
ΡΠ΅ΠΊ. Π’Π°ΠΊΠΈΠ΅ ΡΠ°ΠΌΠΎΡΠΎΠ΄Π½ΡΠ΅ ΠΌΠ΅ΡΠ°Π»Π»Ρ ΡΡΠ°Π»ΠΈ ΠΈΠ·Π²Π΅ΡΡΠ½Ρ ΠΈ ΡΠ΅Π½ΠΈΠ»ΠΈΡΡ Π·Π° ΠΈΡ
Π΄Π΅ΠΊΠΎΡΠ°ΡΠΈΠ²Π½ΡΡ ΠΈ ΡΡΠΈΠ»ΠΈΡΠ°ΡΠ½ΡΡ ΡΠ΅Π½Π½ΠΎΡΡΡ Π²ΠΎ Π²ΡΠΎΡΠΎΠΉ ΠΏΠΎΠ»ΠΎΠ²ΠΈΠ½Π΅ ΠΊΠ°ΠΌΠ΅Π½Π½ΠΎΠ³ΠΎ Π²Π΅ΠΊΠ°.
Π‘Π°ΠΌΠ°Ρ ΡΠ°Π½Π½ΡΡ ΡΠ°Π·ΡΠ°Π±ΠΎΡΠΊΠ°
ΠΠΎΠ»ΠΎΡΠΎ ΠΌΠΎΠΆΠ½ΠΎ Π°Π³Π»ΠΎΠΌΠ΅ΡΠΈΡΠΎΠ²Π°ΡΡ Π² Π±ΠΎΠ»Π΅Π΅ ΠΊΡΡΠΏΠ½ΡΠ΅ ΠΊΡΡΠΊΠΈ ΠΏΡΡΠ΅ΠΌ Ρ
ΠΎΠ»ΠΎΠ΄Π½ΠΎΠΉ ΠΊΠΎΠ²ΠΊΠΈ, Π½ΠΎ ΡΠ°ΠΌΠΎΡΠΎΠ΄Π½Π°Ρ ΠΌΠ΅Π΄Ρ Π½Π΅ ΠΌΠΎΠΆΠ΅Ρ, ΠΈ ΡΡΡΠ΅ΡΡΠ²Π΅Π½Π½ΡΠΌ ΡΠ°Π³ΠΎΠΌ Π½Π° ΠΏΡΡΠΈ ΠΊ ΠΠ΅ΠΊΡ ΠΌΠ΅ΡΠ°Π»Π»ΠΎΠ² ΡΡΠ°Π»ΠΎ ΠΎΡΠΊΡΡΡΠΈΠ΅ ΡΠΎΠ³ΠΎ, ΡΡΠΎ ΡΠ°ΠΊΠΈΠ΅ ΠΌΠ΅ΡΠ°Π»Π»Ρ, ΠΊΠ°ΠΊ ΠΌΠ΅Π΄Ρ, ΠΌΠΎΠ³ΡΡ Π±ΡΡΡ ΠΏΡΠ΅ΠΎΠ±ΡΠ°Π·ΠΎΠ²Π°Π½Ρ Π² ΡΠΎΡΠΌΡ ΠΏΡΡΠ΅ΠΌ ΠΏΠ»Π°Π²Π»Π΅Π½ΠΈΡ ΠΈ ΠΎΡΠ»ΠΈΠ²ΠΊΠΈ Π² ΡΠΎΡΠΌΡ; ΡΡΠ΅Π΄ΠΈ ΡΠ°ΠΌΡΡ
ΡΠ°Π½Π½ΠΈΡ
ΠΈΠ·Π²Π΅ΡΡΠ½ΡΡ
ΠΈΠ·Π΄Π΅Π»ΠΈΠΉ ΡΡΠΎΠ³ΠΎ ΡΠΈΠΏΠ° β ΠΌΠ΅Π΄Π½ΡΠ΅ ΡΠΎΠΏΠΎΡΡ, ΠΎΡΠ»ΠΈΡΡΠ΅ Π½Π° ΠΠ°Π»ΠΊΠ°Π½Π°Ρ
Π² 4-ΠΌ ΡΡΡΡΡΠ΅Π»Π΅ΡΠΈΠΈ Π΄ΠΎ Π½. Ρ. ΠΡΠ΅ ΠΎΠ΄Π½ΠΈΠΌ ΡΠ°Π³ΠΎΠΌ ΡΡΠ°Π»ΠΎ ΠΎΡΠΊΡΡΡΠΈΠ΅ ΡΠΎΠ³ΠΎ, ΡΡΠΎ ΠΌΠ΅ΡΠ°Π»Π»Ρ ΠΌΠΎΠΆΠ½ΠΎ ΠΈΠ·Π²Π»Π΅ΠΊΠ°ΡΡ ΠΈΠ· ΠΌΠ΅ΡΠ°Π»Π»ΠΎΡΠΎΠ΄Π΅ΡΠΆΠ°ΡΠΈΡ
ΠΌΠΈΠ½Π΅ΡΠ°Π»ΠΎΠ². ΠΠ½ΠΈ Π±ΡΠ»ΠΈ ΡΠΎΠ±ΡΠ°Π½Ρ, ΠΈ ΠΈΡ
ΠΌΠΎΠΆΠ½ΠΎ Π±ΡΠ»ΠΎ ΠΎΡΠ»ΠΈΡΠΈΡΡ ΠΏΠΎ ΡΠ²Π΅ΡΡ, ΡΠ΅ΠΊΡΡΡΡΠ΅, Π²Π΅ΡΡ, ΡΠ²Π΅ΡΡ ΠΏΠ»Π°ΠΌΠ΅Π½ΠΈ ΠΈ Π·Π°ΠΏΠ°Ρ
Ρ ΠΏΡΠΈ Π½Π°Π³ΡΠ΅Π²Π°Π½ΠΈΠΈ. ΠΠ°ΠΌΠ΅ΡΠ½ΠΎ Π±ΠΎΠ»ΡΡΠΈΠΉ Π²ΡΡ
ΠΎΠ΄, ΠΏΠΎΠ»ΡΡΠ΅Π½Π½ΡΠΉ ΠΏΡΠΈ Π½Π°Π³ΡΠ΅Π²Π°Π½ΠΈΠΈ ΡΠ°ΠΌΠΎΡΠΎΠ΄Π½ΠΎΠΉ ΠΌΠ΅Π΄ΠΈ Ρ ΡΠΎΠΏΡΡΡΡΠ²ΡΡΡΠΈΠΌΠΈ ΠΎΠΊΡΠΈΠ΄Π½ΡΠΌΠΈ ΠΌΠΈΠ½Π΅ΡΠ°Π»Π°ΠΌΠΈ, ΠΌΠΎΠ³ ΠΏΡΠΈΠ²Π΅ΡΡΠΈ ΠΊ ΠΏΡΠΎΡΠ΅ΡΡΡ ΠΏΠ»Π°Π²ΠΊΠΈ, ΠΏΠΎΡΠΊΠΎΠ»ΡΠΊΡ ΡΡΠΈ ΠΎΠΊΡΠΈΠ΄Ρ Π»Π΅Π³ΠΊΠΎ Π²ΠΎΡΡΡΠ°Π½Π°Π²Π»ΠΈΠ²Π°ΡΡΡΡ Π΄ΠΎ ΠΌΠ΅ΡΠ°Π»Π»Π° Π² ΡΠ»ΠΎΠ΅ Π΄ΡΠ΅Π²Π΅ΡΠ½ΠΎΠ³ΠΎ ΡΠ³Π»Ρ ΠΏΡΠΈ ΡΠ΅ΠΌΠΏΠ΅ΡΠ°ΡΡΡΠ°Ρ
Π²ΡΡΠ΅ 700 Β° C (1300 Β° F) Π² ΠΊΠ°ΡΠ΅ΡΡΠ²Π΅ Π²ΠΎΡΡΡΠ°Π½ΠΎΠ²ΠΈΡΠ΅Π»Ρ. , ΡΠ³Π°ΡΠ½ΡΠΉ Π³Π°Π·, ΡΡΠ°Π½ΠΎΠ²ΠΈΡΡΡ Π²ΡΠ΅ Π±ΠΎΠ»Π΅Π΅ ΡΡΠ°Π±ΠΈΠ»ΡΠ½ΡΠΌ. Π§ΡΠΎΠ±Ρ ΠΎΡΡΡΠ΅ΡΡΠ²ΠΈΡΡ Π°Π³Π»ΠΎΠΌΠ΅ΡΠ°ΡΠΈΡ ΠΈ ΠΎΡΠ΄Π΅Π»Π΅Π½ΠΈΠ΅ ΡΠ°ΡΠΏΠ»Π°Π²Π»Π΅Π½Π½ΠΎΠΉ ΠΈΠ»ΠΈ Π²ΡΠΏΠ»Π°Π²Π»Π΅Π½Π½ΠΎΠΉ ΠΌΠ΅Π΄ΠΈ ΠΎΡ ΡΠΎΠΏΡΡΡΡΠ²ΡΡΡΠΈΡ
ΠΌΠΈΠ½Π΅ΡΠ°Π»ΠΎΠ², Π½Π΅ΠΎΠ±Ρ
ΠΎΠ΄ΠΈΠΌΠΎ Π±ΡΠ»ΠΎ Π²Π²Π΅ΡΡΠΈ ΠΎΠΊΡΠΈΠ΄ ΠΆΠ΅Π»Π΅Π·Π° Π² ΠΊΠ°ΡΠ΅ΡΡΠ²Π΅ ΡΠ»ΡΡΠ°. ΠΡΠΎΡ Π΄Π°Π»ΡΠ½Π΅ΠΉΡΠΈΠΉ ΡΠ°Π³ Π²ΠΏΠ΅ΡΠ΅Π΄ ΠΌΠΎΠΆΠ½ΠΎ ΠΎΠ±ΡΡΡΠ½ΠΈΡΡ Π½Π°Π»ΠΈΡΠΈΠ΅ΠΌ ΠΌΠΈΠ½Π΅ΡΠ°Π»ΠΎΠ² ΠΎΠΊΡΠΈΠ΄Π° ΠΆΠ΅Π»Π΅Π·Π° Π³ΠΎΡΡΠ°Π½ Π² Π²ΡΠ²Π΅ΡΡΠ΅Π»ΡΡ
Π²Π΅ΡΡ
Π½ΠΈΡ
Π·ΠΎΠ½Π°Ρ
ΠΌΠ΅ΡΡΠΎΡΠΎΠΆΠ΄Π΅Π½ΠΈΠΉ ΡΡΠ»ΡΡΠΈΠ΄ΠΎΠ² ΠΌΠ΅Π΄ΠΈ.
ΠΠΎ ΠΌΠ½ΠΎΠ³ΠΈΡ ΡΠ΅Π³ΠΈΠΎΠ½Π°Ρ Π² ΠΏΠΎΡΠ»Π΅Π΄ΡΡΡΠΈΠΉ ΠΏΠ΅ΡΠΈΠΎΠ΄ ΠΏΡΠΎΠΈΠ·Π²ΠΎΠ΄ΠΈΠ»ΠΈΡΡ ΠΌΠ΅Π΄Π½ΠΎ-ΠΌΡΡΡΡΠΊΠΎΠ²ΡΠ΅ ΡΠΏΠ»Π°Π²Ρ, ΠΎΠ±Π»Π°Π΄Π°ΡΡΠΈΠ΅ ΠΏΡΠ΅Π²ΠΎΡΡ ΠΎΠ΄Π½ΡΠΌΠΈ ΡΠ²ΠΎΠΉΡΡΠ²Π°ΠΌΠΈ ΠΏΠΎ ΡΡΠ°Π²Π½Π΅Π½ΠΈΡ Ρ ΠΌΠ΅Π΄ΡΡ ΠΊΠ°ΠΊ Π² Π»ΠΈΡΠΎΠΌ, ΡΠ°ΠΊ ΠΈ Π² Π΄Π΅ΡΠΎΡΠΌΠΈΡΡΠ΅ΠΌΠΎΠΌ Π²ΠΈΠ΄Π΅. Π‘Π½Π°ΡΠ°Π»Π° ΡΡΠΎ ΠΌΠΎΠ³Π»ΠΎ Π±ΡΡΡ ΡΠ»ΡΡΠ°ΠΉΠ½ΡΠΌ ΠΈΠ·-Π·Π° ΡΡ ΠΎΠ΄ΡΡΠ²Π° ΠΏΠΎ ΡΠ²Π΅ΡΡ ΠΈ ΡΠ²Π΅ΡΡ ΠΏΠ»Π°ΠΌΠ΅Π½ΠΈ ΠΌΠ΅ΠΆΠ΄Ρ ΡΡΠΊΠΎ-Π·Π΅Π»Π΅Π½ΡΠΌ ΠΌΠ΅Π΄Π½ΠΎ-ΠΊΠ°ΡΠ±ΠΎΠ½Π°ΡΠ½ΡΠΌ ΠΌΠΈΠ½Π΅ΡΠ°Π»ΠΎΠΌ ΠΌΠ°Π»Π°Ρ ΠΈΡΠΎΠΌ ΠΈ ΠΏΡΠΎΠ΄ΡΠΊΡΠ°ΠΌΠΈ Π²ΡΠ²Π΅ΡΡΠΈΠ²Π°Π½ΠΈΡ ΡΠ°ΠΊΠΈΡ ΠΌΠ΅Π΄Π½ΠΎ-ΠΌΡΡΡΡΠΊΠΎΠ²ΡΡ ΡΡΠ»ΡΡΠΈΠ΄Π½ΡΡ ΠΌΠΈΠ½Π΅ΡΠ°Π»ΠΎΠ², ΠΊΠ°ΠΊ ΡΠ½Π°ΡΠ³ΠΈΡ, Π° ΠΏΠΎΠ·Π΄Π½Π΅Π΅ Π·Π° ΡΡΠΈΠΌ ΠΌΠΎΠ³ ΠΏΠΎΡΠ»Π΅Π΄ΠΎΠ²Π°ΡΡ ΡΠ΅Π»Π΅Π½Π°ΠΏΡΠ°Π²Π»Π΅Π½Π½ΡΠΉ ΠΎΡΠ±ΠΎΡ ΡΠΎΠ΅Π΄ΠΈΠ½Π΅Π½ΠΈΠΉ ΠΌΡΡΡΡΠΊΠ° Π½Π° ΠΎΡΠ½ΠΎΠ²Π΅ ΠΈΡ ΡΠ΅ΡΠ½ΠΎΡΠ½ΠΎΠ³ΠΎ Π·Π°ΠΏΠ°Ρ Π° ΠΏΡΠΈ Π½Π°Π³ΡΠ΅Π²Π°Π½ΠΈΠΈ.
Π‘ΠΎΠ΄Π΅ΡΠΆΠ°Π½ΠΈΠ΅ ΠΌΡΡΡΡΠΊΠ° Π²Π°ΡΡΠΈΡΠΎΠ²Π°Π»ΠΎΡΡ ΠΎΡ 1 Π΄ΠΎ 7 ΠΏΡΠΎΡΠ΅Π½ΡΠΎΠ², ΠΎΠ»ΠΎΠ²Π° Π΄ΠΎ 3 ΠΏΡΠΎΡΠ΅Π½ΡΠΎΠ². ΠΡΠ°ΠΊΡΠΈΡΠ΅ΡΠΊΠΈ Π½Π΅ ΡΠΎΠ΄Π΅ΡΠΆΠ°ΡΠΈΠ΅ ΠΌΡΡΡΡΠΊΠ° ΠΌΠ΅Π΄Π½ΡΠ΅ ΡΠΏΠ»Π°Π²Ρ Ρ Π±ΠΎΠ»Π΅Π΅ Π²ΡΡΠΎΠΊΠΈΠΌ ΡΠΎΠ΄Π΅ΡΠΆΠ°Π½ΠΈΠ΅ΠΌ ΠΎΠ»ΠΎΠ²Π° β Π΄ΡΡΠ³ΠΈΠΌΠΈ ΡΠ»ΠΎΠ²Π°ΠΌΠΈ, Π½Π°ΡΡΠΎΡΡΠ°Ρ Π±ΡΠΎΠ½Π·Π° β ΠΏΠΎ-Π²ΠΈΠ΄ΠΈΠΌΠΎΠΌΡ, ΠΏΠΎΡΠ²ΠΈΠ»ΠΈΡΡ ΠΌΠ΅ΠΆΠ΄Ρ 3000 ΠΈ 2500 Π³ΠΎΠ΄Π°ΠΌΠΈ Π΄ΠΎ Π½Π°ΡΠ΅ΠΉ ΡΡΡ, Π½Π°ΡΠΈΠ½Π°Ρ Ρ Π΄Π΅Π»ΡΡΡ Π’ΠΈΠ³ΡΠ° ΠΈ ΠΠ²ΡΡΠ°ΡΠ°. ΠΡΠΊΡΡΡΠΈΠ΅ Π·Π½Π°ΡΠ΅Π½ΠΈΡ ΠΎΠ»ΠΎΠ²Π° ΠΌΠΎΠ³Π»ΠΎ ΠΏΡΠΎΠΈΠ·ΠΎΠΉΡΠΈ Π±Π»Π°Π³ΠΎΠ΄Π°ΡΡ ΠΈΡΠΏΠΎΠ»ΡΠ·ΠΎΠ²Π°Π½ΠΈΡ ΡΡΠ°Π½Π½ΠΈΡΠ°, ΡΠΌΠ΅ΡΠ°Π½Π½ΠΎΠ³ΠΎ ΡΡΠ»ΡΡΠΈΠ΄Π° ΠΌΠ΅Π΄ΠΈ, ΠΆΠ΅Π»Π΅Π·Π° ΠΈ ΠΎΠ»ΠΎΠ²Π°, Ρ
ΠΎΡΡ ΡΡΠΎΡ ΠΌΠΈΠ½Π΅ΡΠ°Π» Π½Π΅ ΡΠ°ΠΊ ΡΠΈΡΠΎΠΊΠΎ Π΄ΠΎΡΡΡΠΏΠ΅Π½, ΠΊΠ°ΠΊ ΠΎΡΠ½ΠΎΠ²Π½ΠΎΠΉ ΠΌΠΈΠ½Π΅ΡΠ°Π» ΠΎΠ»ΠΎΠ²Π°, ΠΊΠ°ΡΡΠΈΡΠ΅ΡΠΈΡ, ΠΊΠΎΡΠΎΡΡΠΉ, Π΄ΠΎΠ»ΠΆΠ½ΠΎ Π±ΡΡΡ, Π±ΡΠ» ΠΊΠΎΠ½Π΅ΡΠ½ΡΠΌ ΠΈΡΡΠΎΡΠ½ΠΈΠΊΠΎΠΌ. ΠΌΠ΅ΡΠ°Π»Π»Π°. ΠΠ°ΡΡΠΈΡΠ΅ΡΠΈΡ ΠΏΠΎΡΠ°Π·ΠΈΡΠ΅Π»ΡΠ½ΠΎ ΠΏΠ»ΠΎΡΠ½ΡΠΉ ΠΈ Π²ΡΡΡΠ΅ΡΠ°Π΅ΡΡΡ Π² Π²ΠΈΠ΄Π΅ Π³Π°Π»ΡΠΊΠΈ Π² Π°Π»Π»ΡΠ²ΠΈΠ°Π»ΡΠ½ΡΡ
ΠΎΡΠ»ΠΎΠΆΠ΅Π½ΠΈΡΡ
Π²ΠΌΠ΅ΡΡΠ΅ Ρ Π°ΡΡΠ΅Π½ΠΎΠΏΠΈΡΠΈΡΠΎΠΌ ΠΈ Π·ΠΎΠ»ΠΎΡΠΎΠΌ; ΡΡΠΎ ΡΠ°ΠΊΠΆΠ΅ ΠΏΡΠΎΠΈΡΡ
ΠΎΠ΄ΠΈΡ Π² ΠΎΠΏΡΠ΅Π΄Π΅Π»Π΅Π½Π½ΠΎΠΉ ΡΡΠ΅ΠΏΠ΅Π½ΠΈ Π² Π³ΠΎΡΡΠ°Π½Π°Ρ
ΠΎΠΊΡΠΈΠ΄Π° ΠΆΠ΅Π»Π΅Π·Π°, ΡΠΏΠΎΠΌΡΠ½ΡΡΡΡ
Π²ΡΡΠ΅.
Π₯ΠΎΡΡ Π±ΡΠΎΠ½Π·Π° ΠΌΠΎΠ³Π»Π° ΡΠ°Π·Π²ΠΈΠ²Π°ΡΡΡΡ Π½Π΅Π·Π°Π²ΠΈΡΠΈΠΌΠΎ Π² ΡΠ°Π·Π½ΡΡ
ΠΌΠ΅ΡΡΠ°Ρ
, Π½Π°ΠΈΠ±ΠΎΠ»Π΅Π΅ Π²Π΅ΡΠΎΡΡΠ½ΠΎ, ΡΡΠΎ Π±ΡΠΎΠ½Π·ΠΎΠ²Π°Ρ ΠΊΡΠ»ΡΡΡΡΠ° ΡΠ°ΡΠΏΡΠΎΡΡΡΠ°Π½ΠΈΠ»Π°ΡΡ ΡΠ΅ΡΠ΅Π· ΡΠΎΡΠ³ΠΎΠ²Π»Ρ ΠΈ ΠΌΠΈΠ³ΡΠ°ΡΠΈΡ Π½Π°ΡΠΎΠ΄ΠΎΠ² Ρ ΠΠ»ΠΈΠΆΠ½Π΅Π³ΠΎ ΠΠΎΡΡΠΎΠΊΠ° Π² ΠΠ³ΠΈΠΏΠ΅Ρ, ΠΠ²ΡΠΎΠΏΡ ΠΈ, Π²ΠΎΠ·ΠΌΠΎΠΆΠ½ΠΎ, ΠΠΈΡΠ°ΠΉ. ΠΠΎ ΠΌΠ½ΠΎΠ³ΠΈΡ
ΡΠΈΠ²ΠΈΠ»ΠΈΠ·Π°ΡΠΈΡΡ
ΠΏΡΠΎΠΈΠ·Π²ΠΎΠ΄ΡΡΠ²ΠΎ ΠΌΠ΅Π΄ΠΈ, ΠΌΡΡΡΡΠΊΠΎΠ²ΠΎΠΉ ΠΌΠ΅Π΄ΠΈ ΠΈ ΠΎΠ»ΠΎΠ²ΡΠ½Π½ΠΎΠΉ Π±ΡΠΎΠ½Π·Ρ ΠΊΠ°ΠΊΠΎΠ΅-ΡΠΎ Π²ΡΠ΅ΠΌΡ ΠΏΡΠΎΠ΄ΠΎΠ»ΠΆΠ°Π»ΠΎΡΡ ΠΎΠ΄Π½ΠΎΠ²ΡΠ΅ΠΌΠ΅Π½Π½ΠΎ. ΠΠΎΠ·ΠΌΠΎΠΆΠ½ΠΎΠ΅ ΠΈΡΡΠ΅Π·Π½ΠΎΠ²Π΅Π½ΠΈΠ΅ ΠΌΠ΅Π΄Π½ΠΎ-ΠΌΡΡΡΡΠΊΠΎΠ²ΡΡ
ΡΠΏΠ»Π°Π²ΠΎΠ² ΡΡΡΠ΄Π½ΠΎ ΠΎΠ±ΡΡΡΠ½ΠΈΡΡ. ΠΡΠΎΠΈΠ·Π²ΠΎΠ΄ΡΡΠ²ΠΎ ΠΌΠΎΠ³Π»ΠΎ Π±ΡΡΡ ΠΎΡΠ½ΠΎΠ²Π°Π½ΠΎ Π½Π° ΠΏΠΎΠ»Π΅Π·Π½ΡΡ
ΠΈΡΠΊΠΎΠΏΠ°Π΅ΠΌΡΡ
, ΠΊΠΎΡΠΎΡΡΠ΅ Π½Π΅ Π±ΡΠ»ΠΈ ΡΠΈΡΠΎΠΊΠΎ Π΄ΠΎΡΡΡΠΏΠ½Ρ ΠΈ ΡΡΠ°Π»ΠΈ Π΄Π΅ΡΠΈΡΠΈΡΠ½ΡΠΌΠΈ, Π½ΠΎ ΠΎΡΠ½ΠΎΡΠΈΡΠ΅Π»ΡΠ½Π°Ρ Π½Π΅Ρ
Π²Π°ΡΠΊΠ° ΠΌΠΈΠ½Π΅ΡΠ°Π»ΠΎΠ² ΠΎΠ»ΠΎΠ²Π° Π½Π΅ ΠΌΠ΅ΡΠ°Π»Π° Π·Π½Π°ΡΠΈΡΠ΅Π»ΡΠ½ΠΎΠΉ ΡΠΎΡΠ³ΠΎΠ²Π»Π΅ ΡΡΠΈΠΌ ΠΌΠ΅ΡΠ°Π»Π»ΠΎΠΌ Π½Π° Π·Π½Π°ΡΠΈΡΠ΅Π»ΡΠ½ΡΡ
ΡΠ°ΡΡΡΠΎΡΠ½ΠΈΡΡ
. ΠΠΎΠ·ΠΌΠΎΠΆΠ½ΠΎ, ΠΎΠ»ΠΎΠ²ΡΠ½Π½ΡΠ΅ Π±ΡΠΎΠ½Π·Ρ Π² ΠΊΠΎΠ½Π΅ΡΠ½ΠΎΠΌ ΠΈΡΠΎΠ³Π΅ ΡΡΠ°Π»ΠΈ ΠΏΡΠ΅Π΄ΠΏΠΎΡΠΈΡΠ°ΡΡΡΡ ΠΈΠ·-Π·Π° Π²ΠΎΠ·ΠΌΠΎΠΆΠ½ΠΎΡΡΠΈ ΠΎΡΡΠ°Π²Π»Π΅Π½ΠΈΡ ΠΌΡΡΡΡΠΊΠΎΠΌ ΠΎΡ ΠΏΠ°ΡΠΎΠ², ΠΎΠ±ΡΠ°Π·ΡΡΡΠΈΡ
ΡΡ ΠΏΡΠΈ ΠΎΠΊΠΈΡΠ»Π΅Π½ΠΈΠΈ ΠΌΡΡΡΡΠΊΠΎΡΠΎΠ΄Π΅ΡΠΆΠ°ΡΠΈΡ
ΠΌΠΈΠ½Π΅ΡΠ°Π»ΠΎΠ².
ΠΡΠΎΡΠΌΠΈΡΠ΅ ΠΏΠΎΠ΄ΠΏΠΈΡΠΊΡ Britannica Premium ΠΈ ΠΏΠΎΠ»ΡΡΠΈΡΠ΅ Π΄ΠΎΡΡΡΠΏ ΠΊ ΡΠΊΡΠΊΠ»ΡΠ·ΠΈΠ²Π½ΠΎΠΌΡ ΠΊΠΎΠ½ΡΠ΅Π½ΡΡ. ΠΠΎΠ΄ΠΏΠΈΡΠΈΡΠ΅ΡΡ ΡΠ΅ΠΉΡΠ°Ρ
ΠΠΎ ΠΌΠ΅ΡΠ΅ ΡΠ°Π·ΡΠ°Π±ΠΎΡΠΊΠΈ Π²ΡΠ²Π΅ΡΡΠ΅Π»ΡΡ ΠΌΠ΅Π΄Π½ΡΡ ΡΡΠ΄ Π² ΠΎΠΏΡΠ΅Π΄Π΅Π»Π΅Π½Π½ΡΡ ΠΌΠ΅ΡΡΠ°Ρ , Π±ΠΎΠ»Π΅Π΅ ΡΠ²Π΅ΡΠ΄ΡΠ΅ ΡΡΠ»ΡΡΠΈΠ΄Π½ΡΠ΅ ΡΡΠ΄Ρ ΠΏΠΎΠ΄ Π½ΠΈΠΌΠΈ Π΄ΠΎΠ±ΡΠ²Π°Π»ΠΈΡΡ ΠΈ ΠΏΠ»Π°Π²ΠΈΠ»ΠΈΡΡ. ΠΡΠΏΠΎΠ»ΡΠ·ΡΠ΅ΠΌΡΠ΅ ΠΌΠΈΠ½Π΅ΡΠ°Π»Ρ, ΡΠ°ΠΊΠΈΠ΅ ΠΊΠ°ΠΊ Ρ Π°Π»ΡΠΊΠΎΠΏΠΈΡΠΈΡ, ΡΡΠ»ΡΡΠΈΠ΄ ΠΌΠ΅Π΄ΠΈ ΠΈ ΠΆΠ΅Π»Π΅Π·Π°, Π½ΡΠΆΠ΄Π°Π»ΠΈΡΡ Π² ΠΎΠΊΠΈΡΠ»ΠΈΡΠ΅Π»ΡΠ½ΠΎΠΌ ΠΎΠ±ΠΆΠΈΠ³Π΅ Π΄Π»Ρ ΡΠ΄Π°Π»Π΅Π½ΠΈΡ ΡΠ΅ΡΡ Π² Π²ΠΈΠ΄Π΅ Π΄ΠΈΠΎΠΊΡΠΈΠ΄Π° ΡΠ΅ΡΡ ΠΈ ΠΏΠΎΠ»ΡΡΠ΅Π½ΠΈΡ ΠΎΠΊΡΠΈΠ΄Π° ΠΌΠ΅Π΄ΠΈ. ΠΡΠΎ Π½Π΅ ΡΠΎΠ»ΡΠΊΠΎ ΡΡΠ΅Π±ΠΎΠ²Π°Π»ΠΎ Π±ΠΎΠ»ΡΡΠΈΡ ΠΌΠ΅ΡΠ°Π»Π»ΡΡΠ³ΠΈΡΠ΅ΡΠΊΠΈΡ Π½Π°Π²ΡΠΊΠΎΠ², Π½ΠΎ ΡΠ°ΠΊΠΆΠ΅ ΠΎΠΊΠΈΡΠ»ΡΠ»ΠΎ ΡΠ΅ΡΠ½ΠΎ ΡΠ²ΡΠ·Π°Π½Π½ΠΎΠ΅ ΠΆΠ΅Π»Π΅Π·ΠΎ, ΡΡΠΎ Π² ΡΠΎΡΠ΅ΡΠ°Π½ΠΈΠΈ Ρ ΠΈΡΠΏΠΎΠ»ΡΠ·ΠΎΠ²Π°Π½ΠΈΠ΅ΠΌ ΡΠ»ΡΡΠΎΠ² ΠΈΠ· ΠΎΠΊΡΠΈΠ΄Π° ΠΆΠ΅Π»Π΅Π·Π° ΠΈ Π±ΠΎΠ»Π΅Π΅ ΡΠΈΠ»ΡΠ½ΡΠΌΠΈ Π²ΠΎΡΡΡΠ°Π½ΠΎΠ²ΠΈΡΠ΅Π»ΡΠ½ΡΠΌΠΈ ΡΡΠ»ΠΎΠ²ΠΈΡΠΌΠΈ, ΡΠΎΠ·Π΄Π°Π²Π°Π΅ΠΌΡΠΌΠΈ ΡΡΠΎΠ²Π΅ΡΡΠ΅Π½ΡΡΠ²ΠΎΠ²Π°Π½Π½ΡΠΌΠΈ ΠΏΠ»Π°Π²ΠΈΠ»ΡΠ½ΡΠΌΠΈ ΠΏΠ΅ΡΠ°ΠΌΠΈ, ΠΏΡΠΈΠ²ΠΎΠ΄ΠΈΠ»ΠΎ ΠΊ Π±ΠΎΠ»Π΅Π΅ Π²ΡΡΠΎΠΊΠΎΠΌΡ ΡΠΎΠ΄Π΅ΡΠΆΠ°Π½ΠΈΡ ΠΆΠ΅Π»Π΅Π·Π° Π² Π±ΡΠΎΠ½Π·Π΅.
ΠΠ΅Π²ΠΎΠ·ΠΌΠΎΠΆΠ½ΠΎ ΠΏΡΠΎΠ²Π΅ΡΡΠΈ ΡΠ΅ΡΠΊΡΡ Π³ΡΠ°Π½ΠΈΡΡ ΠΌΠ΅ΠΆΠ΄Ρ Π±ΡΠΎΠ½Π·ΠΎΠ²ΡΠΌ Π²Π΅ΠΊΠΎΠΌ ΠΈ ΠΆΠ΅Π»Π΅Π·Π½ΡΠΌ Π²Π΅ΠΊΠΎΠΌ. ΠΠ΅Π±ΠΎΠ»ΡΡΠΈΠ΅ ΠΊΡΡΠΊΠΈ ΠΆΠ΅Π»Π΅Π·Π° Π΄ΠΎΠ»ΠΆΠ½Ρ Π±ΡΠ»ΠΈ ΠΏΡΠΎΠΈΠ·Π²ΠΎΠ΄ΠΈΡΡΡΡ Π² ΠΌΠ΅Π΄Π΅ΠΏΠ»Π°Π²ΠΈΠ»ΡΠ½ΡΡ
ΠΏΠ΅ΡΠ°Ρ
, ΠΏΠΎΡΠΊΠΎΠ»ΡΠΊΡ ΠΈΡΠΏΠΎΠ»ΡΠ·ΠΎΠ²Π°Π»ΠΈΡΡ ΡΠ»ΡΡΡ ΠΎΠΊΡΠΈΠ΄Π° ΠΆΠ΅Π»Π΅Π·Π° ΠΈ ΠΆΠ΅Π»Π΅Π·ΠΎΡΠΎΠ΄Π΅ΡΠΆΠ°ΡΠΈΠ΅ ΡΡΠ»ΡΡΠΈΠ΄Π½ΡΠ΅ ΡΡΠ΄Ρ ΠΌΠ΅Π΄ΠΈ. ΠΡΠΎΠΌΠ΅ ΡΠΎΠ³ΠΎ, Π±ΠΎΠ»Π΅Π΅ Π²ΡΡΠΎΠΊΠΈΠ΅ ΡΠ΅ΠΌΠΏΠ΅ΡΠ°ΡΡΡΡ ΠΏΠ΅ΡΠΈ ΡΠΎΠ·Π΄Π°Π»ΠΈ Π±Ρ ΡΡΠ»ΠΎΠ²ΠΈΡ Π΄Π»Ρ Π±ΠΎΠ»Π΅Π΅ ΡΠΈΠ»ΡΠ½ΠΎΠ³ΠΎ Π²ΠΎΡΡΡΠ°Π½ΠΎΠ²Π»Π΅Π½ΠΈΡ (ΡΠΎ Π΅ΡΡΡ Π±ΠΎΠ»Π΅Π΅ Π²ΡΡΠΎΠΊΠΎΠ΅ ΡΠΎΠ΄Π΅ΡΠΆΠ°Π½ΠΈΠ΅ ΠΌΠΎΠ½ΠΎΠΎΠΊΡΠΈΠ΄Π° ΡΠ³Π»Π΅ΡΠΎΠ΄Π° Π² Π³Π°Π·Π°Ρ
ΠΏΠ΅ΡΠΈ). Π Π°Π½Π½ΠΈΠΉ ΠΊΡΡΠΎΠΊ ΠΆΠ΅Π»Π΅Π·Π° Ρ Π΄ΠΎΡΠΎΠ³ΠΈ Π² ΠΏΡΠΎΠ²ΠΈΠ½ΡΠΈΠΈ ΠΡΠ΅Π½ΡΠ΅, ΠΠΈΠ΄Π΅ΡΠ»Π°Π½Π΄Ρ, Π±ΡΠ» Π΄Π°ΡΠΈΡΠΎΠ²Π°Π½ 1350 Π³ΠΎΠ΄ΠΎΠΌ Π΄ΠΎ Π½Π°ΡΠ΅ΠΉ ΡΡΡ, Π΄Π°ΡΠΎΠΉ, ΠΊΠΎΡΠΎΡΡΡ ΠΎΠ±ΡΡΠ½ΠΎ ΠΏΡΠΈΠ½ΠΈΠΌΠ°ΡΡ Π·Π° ΡΡΠ΅Π΄Π½ΠΈΠΉ Π±ΡΠΎΠ½Π·ΠΎΠ²ΡΠΉ Π²Π΅ΠΊ Π΄Π»Ρ ΡΡΠΎΠΉ ΠΎΠ±Π»Π°ΡΡΠΈ. Π‘ Π΄ΡΡΠ³ΠΎΠΉ ΡΡΠΎΡΠΎΠ½Ρ, Π² ΠΠ½Π°ΡΠΎΠ»ΠΈΠΈ ΠΆΠ΅Π»Π΅Π·ΠΎ ΠΈΡΠΏΠΎΠ»ΡΠ·ΠΎΠ²Π°Π»ΠΎΡΡ ΡΠΆΠ΅ Π² 2000 Π³. Π΄ΠΎ Π½. Ρ. ΠΡΡΡ ΡΠ°ΠΊΠΆΠ΅ ΡΠ»ΡΡΠ°ΠΉΠ½ΡΠ΅ ΡΡΡΠ»ΠΊΠΈ Π½Π° ΠΆΠ΅Π»Π΅Π·ΠΎ ΠΈ Π² Π±ΠΎΠ»Π΅Π΅ ΡΠ°Π½Π½ΠΈΠ΅ ΠΏΠ΅ΡΠΈΠΎΠ΄Ρ, Π½ΠΎ ΡΡΠΎΡ ΠΌΠ°ΡΠ΅ΡΠΈΠ°Π» ΠΈΠΌΠ΅Π» ΠΌΠ΅ΡΠ΅ΠΎΡΠΈΡΠ½ΠΎΠ΅ ΠΏΡΠΎΠΈΡΡ
ΠΎΠΆΠ΄Π΅Π½ΠΈΠ΅.
ΠΠ°ΠΊ ΡΠΎΠ»ΡΠΊΠΎ Π±ΡΠ»Π° ΡΡΡΠ°Π½ΠΎΠ²Π»Π΅Π½Π° ββΠ²Π·Π°ΠΈΠΌΠΎΡΠ²ΡΠ·Ρ ΠΌΠ΅ΠΆΠ΄Ρ Π½ΠΎΠ²ΡΠΌ ΠΌΠ΅ΡΠ°Π»Π»ΠΎΠΌ, Π½Π°ΠΉΠ΄Π΅Π½Π½ΡΠΌ Π² ΠΌΠ΅Π΄Π½ΡΡ
ΠΏΠ»Π°Π²ΠΊΠ°Ρ
, ΠΈ ΡΡΠ΄ΠΎΠΉ, Π΄ΠΎΠ±Π°Π²Π»Π΅Π½Π½ΠΎΠΉ Π² ΠΊΠ°ΡΠ΅ΡΡΠ²Π΅ ΡΠ»ΡΡΠ°, Π΅ΡΡΠ΅ΡΡΠ²Π΅Π½Π½ΡΠΌ ΠΎΠ±ΡΠ°Π·ΠΎΠΌ ΠΏΠΎΡΠ»Π΅Π΄ΠΎΠ²Π°Π»Π° ΡΠ°Π±ΠΎΡΠ° ΠΏΠ΅ΡΠ΅ΠΉ Π΄Π»Ρ ΠΏΡΠΎΠΈΠ·Π²ΠΎΠ΄ΡΡΠ²Π° ΡΠΎΠ»ΡΠΊΠΎ ΠΆΠ΅Π»Π΅Π·Π°. ΠΠ΅ΡΠΎΠΌΠ½Π΅Π½Π½ΠΎ, ΠΊ 1400 Π³. Π΄ΠΎ Π½. Ρ. Π² ΠΠ½Π°ΡΠΎΠ»ΠΈΠΈ Π±ΠΎΠ»ΡΡΠΎΠ΅ Π·Π½Π°ΡΠ΅Π½ΠΈΠ΅ ΠΏΡΠΈΠΎΠ±ΡΠ΅Π»ΠΎ ΠΆΠ΅Π»Π΅Π·ΠΎ, Π° ΠΊ 1200β1000 Π³Π³. Π΄ΠΎ Π½. Ρ. ΠΈΠ· Π½Π΅Π³ΠΎ Π² Π±ΠΎΠ»ΡΡΠΈΡ
ΠΌΠ°ΡΡΡΠ°Π±Π°Ρ
ΠΈΠ·Π³ΠΎΡΠ°Π²Π»ΠΈΠ²Π°Π»ΠΈ ΠΎΡΡΠΆΠΈΠ΅, ΠΏΠ΅ΡΠ²ΠΎΠ½Π°ΡΠ°Π»ΡΠ½ΠΎ Π»Π΅Π·Π²ΠΈΡ ΠΊΠΈΠ½ΠΆΠ°Π»ΠΎΠ². ΠΠΎ ΡΡΠΎΠΉ ΠΏΡΠΈΡΠΈΠ½Π΅ 1200 Π³. Π΄ΠΎ Π½.Ρ. Π±ΡΠ» ΠΏΡΠΈΠ½ΡΡ Π·Π° Π½Π°ΡΠ°Π»ΠΎ ΠΆΠ΅Π»Π΅Π·Π½ΠΎΠ³ΠΎ Π²Π΅ΠΊΠ°. ΠΠ°Π½Π½ΡΠ΅ ΡΠ°ΡΠΊΠΎΠΏΠΎΠΊ ΡΠΊΠ°Π·ΡΠ²Π°ΡΡ Π½Π° ΡΠΎ, ΡΡΠΎ ΠΈΡΠΊΡΡΡΡΠ²ΠΎ ΠΈΠ·Π³ΠΎΡΠΎΠ²Π»Π΅Π½ΠΈΡ ΠΆΠ΅Π»Π΅Π·Π° Π·Π°ΡΠΎΠ΄ΠΈΠ»ΠΎΡΡ Π² Π³ΠΎΡΠΈΡΡΠΎΠΉ ΠΌΠ΅ΡΡΠ½ΠΎΡΡΠΈ ΠΊ ΡΠ³Ρ ΠΎΡ Π§Π΅ΡΠ½ΠΎΠ³ΠΎ ΠΌΠΎΡΡ, Π³Π΄Π΅ Π΄ΠΎΠΌΠΈΠ½ΠΈΡΠΎΠ²Π°Π»ΠΈ Ρ
Π΅ΡΡΡ. ΠΠΎΠ·ΠΆΠ΅ ΡΡΠΎ ΠΈΡΠΊΡΡΡΡΠ²ΠΎ, ΠΏΠΎ-Π²ΠΈΠ΄ΠΈΠΌΠΎΠΌΡ, ΡΠ°ΡΠΏΡΠΎΡΡΡΠ°Π½ΠΈΠ»ΠΎΡΡ ΡΡΠ΅Π΄ΠΈ ΡΠΈΠ»ΠΈΡΡΠΈΠΌΠ»ΡΠ½, ΠΏΠΎΡΠΊΠΎΠ»ΡΠΊΡ Π² ΠΠ΅ΡΠ°ΡΠ΅ Π±ΡΠ»ΠΈ ΠΎΠ±Π½Π°ΡΡΠΆΠ΅Π½Ρ Π³ΡΡΠ±ΡΠ΅ ΠΏΠ΅ΡΠΈ, Π΄Π°ΡΠΈΡΡΠ΅ΠΌΡΠ΅ 1200 Π³. Π΄ΠΎ Π½. Ρ., Π²ΠΌΠ΅ΡΡΠ΅ Ρ ΡΡΠ΄ΠΎΠΌ ΠΆΠ΅Π»Π΅Π·Π½ΡΡ
ΠΏΡΠ΅Π΄ΠΌΠ΅ΡΠΎΠ².
ΠΠ»Π°Π²ΠΊΠ° ΠΎΠΊΡΠΈΠ΄Π° ΠΆΠ΅Π»Π΅Π·Π° Ρ Π΄ΡΠ΅Π²Π΅ΡΠ½ΡΠΌ ΡΠ³Π»Π΅ΠΌ ΡΡΠ΅Π±ΠΎΠ²Π°Π»Π° Π²ΡΡΠΎΠΊΠΎΠΉ ΡΠ΅ΠΌΠΏΠ΅ΡΠ°ΡΡΡΡ, ΠΈ, ΠΏΠΎΡΠΊΠΎΠ»ΡΠΊΡ ΡΠ΅ΠΌΠΏΠ΅ΡΠ°ΡΡΡΠ° ΠΏΠ»Π°Π²Π»Π΅Π½ΠΈΡ ΠΆΠ΅Π»Π΅Π·Π° 1540 Β°C (2800 Β°F) ΡΠΎΠ³Π΄Π° Π±ΡΠ»Π° Π½Π΅Π΄ΠΎΡΡΠΈΠΆΠΈΠΌΠ°, ΠΏΡΠΎΠ΄ΡΠΊΡ ΠΏΡΠ΅Π΄ΡΡΠ°Π²Π»ΡΠ» ΡΠΎΠ±ΠΎΠΉ ΠΏΡΠΎΡΡΠΎ Π³ΡΠ±ΡΠ°ΡΡΡ ΠΌΠ°ΡΡΡ ΠΏΠ°ΡΡΠΎΠΎΠ±ΡΠ°Π·Π½ΡΡ Π³Π»ΠΎΠ±ΡΠ» ΠΌΠ΅ΡΠ°Π»Π»Π°, ΡΠΌΠ΅ΡΠ°Π½Π½ΡΡ Ρ ΠΏΠΎΠ»ΡΠΆΠΈΠ΄ΠΊΠΈΠΉ ΡΠ»Π°ΠΊ. ΠΡΠΎΡ ΠΏΡΠΎΠ΄ΡΠΊΡ, ΠΏΠΎΠ·ΠΆΠ΅ ΠΈΠ·Π²Π΅ΡΡΠ½ΡΠΉ ΠΊΠ°ΠΊ Π±Π»ΡΠΌ, Π²ΡΡΠ΄ Π»ΠΈ ΠΌΠΎΠΆΠ½ΠΎ Π±ΡΠ»ΠΎ ΠΈΡΠΏΠΎΠ»ΡΠ·ΠΎΠ²Π°ΡΡ Π² ΡΠΎΠΌ Π²ΠΈΠ΄Π΅, Π² ΠΊΠ°ΠΊΠΎΠΌ ΠΎΠ½ Π±ΡΠ», Π½ΠΎ ΠΏΠΎΠ²ΡΠΎΡΠ½ΡΠΉ Π½Π°Π³ΡΠ΅Π² ΠΈ Π³ΠΎΡΡΡΠ°Ρ ΠΊΠΎΠ²ΠΊΠ° ΡΡΡΡΠ°Π½ΠΈΠ»ΠΈ Π±ΠΎΠ»ΡΡΡΡ ΡΠ°ΡΡΡ ΡΠ»Π°ΠΊΠ°, ΡΠΎΠ·Π΄Π°Π² ΠΊΠΎΠ²Π°Π½ΠΎΠ΅ ΠΆΠ΅Π»Π΅Π·ΠΎ, ΠΏΡΠΎΠ΄ΡΠΊΡ Π³ΠΎΡΠ°Π·Π΄ΠΎ Π»ΡΡΡΠ΅Π³ΠΎ ΠΊΠ°ΡΠ΅ΡΡΠ²Π°.
ΠΠ° ΡΠ²ΠΎΠΉΡΡΠ²Π° ΠΆΠ΅Π»Π΅Π·Π° ΡΠΈΠ»ΡΠ½ΠΎ Π²Π»ΠΈΡΠ΅Ρ ΠΏΡΠΈΡΡΡΡΡΠ²ΠΈΠ΅ Π½Π΅Π±ΠΎΠ»ΡΡΠΎΠ³ΠΎ ΠΊΠΎΠ»ΠΈΡΠ΅ΡΡΠ²Π° ΡΠ³Π»Π΅ΡΠΎΠ΄Π°, ΠΏΡΠΈ ΡΡΠΎΠΌ Π·Π½Π°ΡΠΈΡΠ΅Π»ΡΠ½ΠΎΠ΅ ΡΠ²Π΅Π»ΠΈΡΠ΅Π½ΠΈΠ΅ ΠΏΡΠΎΡΠ½ΠΎΡΡΠΈ ΡΠ²ΡΠ·Π°Π½ΠΎ Ρ ΡΠΎΠ΄Π΅ΡΠΆΠ°Π½ΠΈΠ΅ΠΌ ΠΌΠ΅Π½Π΅Π΅ 0,5 ΠΏΡΠΎΡΠ΅Π½ΡΠ°. ΠΡΠΈ Π΄ΠΎΡΡΠΈΠΆΠΈΠΌΡΡ
ΡΠΎΠ³Π΄Π° ΡΠ΅ΠΌΠΏΠ΅ΡΠ°ΡΡΡΠ°Ρ
— ΠΎΠΊΠΎΠ»ΠΎ 1200 Β° C (2200 Β° F) — Π²ΠΎΡΡΡΠ°Π½ΠΎΠ²Π»Π΅Π½ΠΈΠ΅ Π΄ΡΠ΅Π²Π΅ΡΠ½ΡΠΌ ΡΠ³Π»Π΅ΠΌ Π΄Π°Π²Π°Π»ΠΎ ΠΏΠΎΡΡΠΈ ΡΠΈΡΡΠΎΠ΅ ΠΆΠ΅Π»Π΅Π·ΠΎ, ΠΊΠΎΡΠΎΡΠΎΠ΅ Π±ΡΠ»ΠΎ ΠΌΡΠ³ΠΊΠΈΠΌ ΠΈ ΠΈΠΌΠ΅Π»ΠΎ ΠΎΠ³ΡΠ°Π½ΠΈΡΠ΅Π½Π½ΠΎΠ΅ ΠΏΡΠΈΠΌΠ΅Π½Π΅Π½ΠΈΠ΅ Π΄Π»Ρ ΠΎΡΡΠΆΠΈΡ ΠΈ ΠΈΠ½ΡΡΡΡΠΌΠ΅Π½ΡΠΎΠ². Ρ ΠΈΠ·ΠΎΠ±ΡΠ΅ΡΠ΅Π½ΠΈΠ΅ΠΌ Π»ΡΡΡΠΈΡ
ΠΌΠ΅Ρ
ΠΎΠ² ΠΆΠ΅Π»Π΅Π·ΠΎ ΠΏΠΎΠ³Π»ΠΎΡΠ°Π»ΠΎ Π±ΠΎΠ»ΡΡΠ΅ ΡΠ³Π»Π΅ΡΠΎΠ΄Π°. ΠΡΠΎ ΠΏΡΠΈΠ²Π΅Π»ΠΎ ΠΊ ΡΠ²Π΅ΡΠ΅Π½ΠΈΡ ΠΈ ΠΆΠ΅Π»Π΅Π·Π½ΡΠΌ ΠΈΠ·Π΄Π΅Π»ΠΈΡΠΌ Ρ ΡΠ°Π·Π»ΠΈΡΠ½ΡΠΌ ΡΠΎΠ΄Π΅ΡΠΆΠ°Π½ΠΈΠ΅ΠΌ ΡΠ³Π»Π΅ΡΠΎΠ΄Π°, ΡΡΠΎ Π·Π°ΡΡΡΠ΄Π½ΡΠ»ΠΎ ΠΎΠΏΡΠ΅Π΄Π΅Π»Π΅Π½ΠΈΠ΅ ΠΏΠ΅ΡΠΈΠΎΠ΄Π°, Π² ΡΠ΅ΡΠ΅Π½ΠΈΠ΅ ΠΊΠΎΡΠΎΡΠΎΠ³ΠΎ ΠΆΠ΅Π»Π΅Π·ΠΎ ΠΌΠΎΠ³Π»ΠΎ Π±ΡΡΡ ΠΏΡΠ΅Π΄Π½Π°ΠΌΠ΅ΡΠ΅Π½Π½ΠΎ ΡΠΏΡΠΎΡΠ½Π΅Π½ΠΎ ΠΏΡΡΠ΅ΠΌ Π½Π°ΡΠ³Π»Π΅ΡΠΎΠΆΠΈΠ²Π°Π½ΠΈΡ ΠΈΠ»ΠΈ ΠΏΠΎΠ²ΡΠΎΡΠ½ΠΎΠ³ΠΎ Π½Π°Π³ΡΠ΅Π²Π°Π½ΠΈΡ ΠΌΠ΅ΡΠ°Π»Π»Π° Π² ΠΊΠΎΠ½ΡΠ°ΠΊΡΠ΅ Ρ ΠΈΠ·Π±ΡΡΠΊΠΎΠΌ Π΄ΡΠ΅Π²Π΅ΡΠ½ΠΎΠ³ΠΎ ΡΠ³Π»Ρ.
Π£Π³Π»Π΅ΡΠΎΠ΄ΠΎΡΠΎΠ΄Π΅ΡΠΆΠ°ΡΠ΅Π΅ ΠΆΠ΅Π»Π΅Π·ΠΎ ΠΈΠΌΠ΅Π»ΠΎ Π΅ΡΠ΅ ΠΎΠ΄Π½ΠΎ Π±ΠΎΠ»ΡΡΠΎΠ΅ ΠΏΡΠ΅ΠΈΠΌΡΡΠ΅ΡΡΠ²ΠΎ, Π·Π°ΠΊΠ»ΡΡΠ°Π²ΡΠ΅Π΅ΡΡ Π² ΡΠΎΠΌ, ΡΡΠΎ, Π² ΠΎΡΠ»ΠΈΡΠΈΠ΅ ΠΎΡ Π±ΡΠΎΠ½Π·Ρ ΠΈ Π±Π΅Π·ΡΠ³Π»Π΅ΡΠΎΠ΄ΠΈΡΡΠΎΠ³ΠΎ ΠΆΠ΅Π»Π΅Π·Π°, Π΅Π³ΠΎ ΠΌΠΎΠΆΠ½ΠΎ Π±ΡΠ»ΠΎ ΡΠ΄Π΅Π»Π°ΡΡ Π΅ΡΠ΅ Π±ΠΎΠ»Π΅Π΅ ΡΠ²Π΅ΡΠ΄ΡΠΌ ΠΏΡΡΠ΅ΠΌ Π·Π°ΠΊΠ°Π»ΠΊΠΈ, Ρ. Π΅. Π±ΡΡΡΡΠΎΠ³ΠΎ ΠΎΡ
Π»Π°ΠΆΠ΄Π΅Π½ΠΈΡ ΠΏΡΡΠ΅ΠΌ ΠΏΠΎΠ³ΡΡΠΆΠ΅Π½ΠΈΡ Π² Π²ΠΎΠ΄Ρ. ΠΠ΅Ρ Π½ΠΈΠΊΠ°ΠΊΠΈΡ
ΡΠ²ΠΈΠ΄Π΅ΡΠ΅Π»ΡΡΡΠ² ΠΈΡΠΏΠΎΠ»ΡΠ·ΠΎΠ²Π°Π½ΠΈΡ ΡΡΠΎΠ³ΠΎ ΠΏΡΠΎΡΠ΅ΡΡΠ° Π·Π°ΠΊΠ°Π»ΠΊΠΈ Π² ΡΠ°Π½Π½Π΅ΠΌ ΠΆΠ΅Π»Π΅Π·Π½ΠΎΠΌ Π²Π΅ΠΊΠ΅, ΡΠ°ΠΊ ΡΡΠΎ ΠΎΠ½ Π΄ΠΎΠ»ΠΆΠ΅Π½ Π±ΡΠ» Π±ΡΡΡ Π»ΠΈΠ±ΠΎ Π½Π΅ΠΈΠ·Π²Π΅ΡΡΠ΅Π½ ΡΠΎΠ³Π΄Π°, Π»ΠΈΠ±ΠΎ Π½Π΅ ΡΡΠΈΡΠ°Π»ΡΡ Π²ΡΠ³ΠΎΠ΄Π½ΡΠΌ, ΠΏΠΎΡΠΊΠΎΠ»ΡΠΊΡ Π·Π°ΠΊΠ°Π»ΠΊΠ° Π΄Π΅Π»Π°Π΅Ρ ΠΆΠ΅Π»Π΅Π·ΠΎ ΠΎΡΠ΅Π½Ρ Ρ
ΡΡΠΏΠΊΠΈΠΌ ΠΈ Π΄ΠΎΠ»ΠΆΠ½Π° ΡΠΎΠΏΡΠΎΠ²ΠΎΠΆΠ΄Π°ΡΡΡΡ ΠΎΡΠΏΡΡΠΊΠΎΠΌ ΠΈΠ»ΠΈ ΠΏΠΎΠ²ΡΠΎΡΠ½ΡΠΌ Π½Π°Π³ΡΠ΅Π²ΠΎΠΌ ΠΏΡΠΈ Π±ΠΎΠ»Π΅Π΅ Π½ΠΈΠ·ΠΊΠ°Ρ ΡΠ΅ΠΌΠΏΠ΅ΡΠ°ΡΡΡΠ°, ΡΡΠΎΠ±Ρ Π²ΠΎΡΡΡΠ°Π½ΠΎΠ²ΠΈΡΡ ΡΠ΄Π°ΡΠ½ΡΡ Π²ΡΠ·ΠΊΠΎΡΡΡ. Π’ΠΎ, ΡΡΠΎ, ΠΏΠΎ-Π²ΠΈΠ΄ΠΈΠΌΠΎΠΌΡ, Π±ΡΠ»ΠΎ ΡΡΡΠ°Π½ΠΎΠ²Π»Π΅Π½ΠΎ Π½Π° ΡΠ°Π½Π½Π΅ΠΌ ΡΡΠ°ΠΏΠ΅, Π±ΡΠ»ΠΎ ΠΏΡΠ°ΠΊΡΠΈΠΊΠΎΠΉ ΠΌΠ½ΠΎΠ³ΠΎΠΊΡΠ°ΡΠ½ΠΎΠΉ Ρ
ΠΎΠ»ΠΎΠ΄Π½ΠΎΠΉ ΠΊΠΎΠ²ΠΊΠΈ ΠΈ ΠΎΡΠΆΠΈΠ³Π° ΠΏΡΠΈ 600β700 Β° C (1100β1300 Β° F), ΡΠ΅ΠΌΠΏΠ΅ΡΠ°ΡΡΡΠ°, Π΅ΡΡΠ΅ΡΡΠ²Π΅Π½Π½ΠΎ Π΄ΠΎΡΡΠΈΠ³Π°Π΅ΠΌΠ°Ρ ΠΏΡΠΈ ΠΏΡΠΎΡΡΠΎΠΌ ΠΎΠ³Π½Π΅.