самодельный пневматический или механический молот для ковки
На чтение 7 мин. Просмотров 5.6k. Опубликовано Обновлено
В кузнечном деле мастеру не обойтись без ряда специальных инструментов, в том числе и без кузнечного молота. Такой агрегат способен деформировать металлозаготовку, придавая ей определенную форму.
Особенности эксплуатации подобного оборудования на практике определяются его видом, возможностями и особенностями строения.
Принцип работы кузнечного молота
Кузнечные молоты актуальны для небольших кузниц, которые специализируются на заказах по изготовлению изделий из металла:
- элементы для мебели, созданные путем художественной ковки;
- мелкий инвентарь для охоты, рыбалки;
- памятные сувениры и т.
Устройство рычажного кузнечного молота.Принцип работы данного оборудования основывается на использовании динамических ударов рабочего органа ‒ штока, соединенного с ударной частью машины ‒ бабой, а также устройствами для контроля силы воздействия.
Иные обязательные конструктивные элементы рессорного кузнечного молота описаны ниже:
- баба, соединенная с поршнем;
- основание, закрепленное на основании;
- станина с зафиксированными на ней направляющими для подвижных узлов;
- приводное оборудование;
- щитовое ограждение, обеспечивающее оператору высокий уровень безопасности;
- электрооборудование;
- у пневматических молотов в конструкции также присутствует компрессорный цилиндр.
Первые модели подобного оборудования оснащались ножным или ручным приводом, современные изделия имеют удобную систему управления, минимизирующую усилие со стороны кузнеца.
Опишем принцип функционирования устройства:
- заготовку помещают в нижнюю часть молота;
- устройство настраивается на актуальную частоту удара и приводится в движение;
- при активации молота ведомая верхняя часть конструкции бьет по металлозаготовке;
- динамическое воздействие на металлозаготовку осуществляется до того момента, пока она не приобретет актуальную форму.
Принцип работы дизель молота заключается в преобразовании возвратно-поступательного движения, который совершается кривошипно-шатунным механизмом, в аналогичное движение поршня. Это предоставляет мастеру возможность совершить с его помощью множество операций.
Виды молотов
Продольный разрез молота МА4132.По типу вещества, применяемого в компрессорном цилиндре, различают следующие ковочные молоты:
- паровоздушные агрегаты работают за счет пара или атмосферного воздуха;
- гидравлические и гидростатические модели используют силу жидкости под давлением;
- бензиновые молоты функционируют по принципу ДВС;
- газовые используют сжиженный газ;
- молоты электромагнитного типа для ковки используют энергии электрических и магнитных полей;
- механические молоты запускаются физическим усилием мастера, используются мало в сравнении с иными моделями подобного оборудования;
- рессорно-пружинные модели работают за счет того, что рессора ускоряет падение поршня вниз;
- пневматические используют силу газа под давлением в процессе функционирования.
Отдельно стоит отметить кузнечный пневмомолот с пневмоцилиндром. Такое строение избавляет мастера от необходимости применять дополнительные источники энергии и утяжелять конструкцию. При ударе кузнечного молота по заготовке ее форма меняется согласно запланированной рабочей схеме.
Механический
Механический кузнечный молот представляет собой старое по принципу функционирования устройство, разработанное и применяемое на практике еще несколько веков назад.
Основой его конструкции является механизм, подающий усилие от мускулов человека на молот. И только спустя многие годы были сконструированы первые модели с приводами на силе воды и пара.
Основная рабочая часть механического молота сконструирована из рычага с молотом с одной стороны и массивным противовесом с другой. Его устанавливают на вал, способный качаться под воздействием на педаль или рычаг.
[box type=”fact”]Механические молоты имеют ручной способ управления, поэтому такие модели можно изготовить своими силами.
Однако стоит помнить, что КПД такого оборудования в сравнении с более современными моделями довольно низкое. А габариты механики при этом довольно внушительны, что не позволяет использовать их в крохотных кузницах.
Пневматический

Молоты устанавливаются в единичном количестве и снабжаются индивидуальной компрессорной установкой. Они не отличаются большой массой падающих частей, потому могут применяться для ковки малых по размеру изделий.
Зачастую, пневмомолот оснащается С-образной станиной, скрепляющейся для жесткости посредством боковых стоек. Штамповочная зона пневматического молота открыта с трех сторон, что значительно упрощает его обслуживание.
Молот пневматический кузнечный управляется с помощью ручного рычага или педали и может применяться в двух направлениях:
- для выполнения ковки художественного типа подойдут агрегаты, масса которых не превышает 75 кг;
- в производстве: МПЧ 150-2000 кг.
Достоинства оборудования такого типа заключаются в следующем:
- энергоемкость;
- высокая чувствительность при регулировке рабочих режимов;
- простое управление;
- долгий срок службы.
Недостатки пневматических молотов ‒ приличные габариты, существенный вес, сложность транспортировки.
https://youtu.be/mq8UQp9oc04
Молот самодельный: супермолот
Смастерить самодельный кузнечный молот для ковки металлоизделий будет легче, если разделить все операции на несколько этапов в следующей последовательности:
- подготовка основания для монтажа кузнечного пресс молота;
- конструирование рамы с рессорами;
- сборка рабочего механизма;
- установка самодельного устройства.
Чертежи
Изготовить кузнечный молот своими руками можно в условиях мастерской или гаражной постройки. Но перед работой важно определить актуальные размеры агрегата, описать все его составляющие детали, что в последствие позволит определить вес изделия и его функциональные возможности.
Для этого потребуется составить самостоятельно или найти в интернете чертежи и схему сборки такой конструкции с детальным описанием всех ее частей.
[box type=”fact”]На заметку! Легче изготовить своими руками кузнечные молоты механического типа, исходя из классификации подобных агрегатов, по характеру применяемой силы.[/box]Фундамент
После создания чертежа устройства для ковки переходят к формированию фундамента. Самодельный кузнечный молот нужно установить на ровную площадку, подготовленную заранее. Это необходимо для нормальной работы устройства и устранение риска его опрокидывания при эксплуатации.
Электрическая схема кузнечного молота.В месте монтажа конструкции нужно выкопать яму актуальных размеров. Ее дно тщательно посыпают песком со щебнем, поливают водой и трамбуют. Поверх осуществленного слоя песчаной подушки монтируют армирующий каркас, для чего применяется арматура с диаметром 12-14 мм.
Крайне важно не забыть при этом про перевязку, которую осуществляют каждые 250-300 мм.
Раствор бетона готовят в пропорции 1:2:3, для чего потребуются следующие материалы:
- цемент марки м400;
- щебенка фракции 10-20;
- песок.
Заливку следует осуществлять за один раз, постоянно уплотняя массу. Это позволит избежать образования пустот внутри фундамента.
На завершающем этапе изготовления основания под самодельный молот в незастывший бетон стоит установить анкерные болты, на которые впоследствии дополнительно зафиксируется агрегат.
Рама
Самодельный кузнечный молот при сборке требует наличия сварочного аппарата, с помощью которого собирается рама конструкции. Ее изготавливают из профильных труб или иного вида металлопроката, обладающего высокой прочностью.
Для дополнительной устойчивости изделия нужно установить распорки, а также поперечные балки.
Сборка молота
В начале работы потребуется собрать раму агрегата и выполнить ее монтаж на подготовленное основание. Нижние салазки фиксируются анкерными болтами с гайками, а остальные направляющие и перемычки привариваются к ним с помощью сварочного аппарата.
Вал вставляется в стойки, а потом на него крепят рычаг с молотом. Аналогично собирают привода с педалью или рычагом.
Самодельный кузнечный молот оснащается наковальней. Она выполняет крайне важную функцию, поэтому ее монтаж нужно осуществлять со всей ответственностью. Фиксируют наковальню точно под нижним положением бока, а под ней располагают чурбак из дерева.
Он выполнит функции амортизатора при ударах молота . Наковальня изготавливается из обрезка рельсы или швеллера, но желательно с закаленной лицевой частью. После осуществления сборки конструкции ее красят.
Подведем итоги
В кузнице стоит иметь молот разного рода металлоизделий. Среди разных видов такого оборудования выделяются механические модели, потому что они легко изготавливаются своими силами. С помощью таких самоделок можно создавать простые и сложные металлические изделия.
Кузнечный молот своими руками. Как и зачем?
Возможно, вас это удивит, но кузнечное дело еще живо и популярно. И многие занимаются этим и даже делают кузнечные молоты своими руками!
Для чего предназначен кузнечный молот?
Если такой молот хочет сделать не кузнечных дел мастер в каком-нибудь поколении, то тогда, возможно, это делается с целью создания красивых кованых элементов декора или мебели, изготовленной методом ковки (например, стулья и столы).
В большинстве случаев кузнечный молот — устройство, которое применяют на заводах и в мастерских, работающих с художественной штамповкой металла, изготавливающих и ремонтирующих инструменты. Его применение зависит от модели.
Для использования в домашних условиях данное устройство часто делается самостоятельно, и за счет своего ударного механизма применяется не только для изготовления кованых элементов, но и для работы с металлическими листами (для их деформации).
Кузнечный молот своими руками: что потребуется?
Данное приспособление очень увесистое. Изготовление требует затрат времени и сил, но обойдется дешевле, если делать своими руками. Чаще всего за эту процедуру берутся любители ручной работы и обладатели умелых рук.
Как самому сделать кузнечный молот с минимальными затратами сил и денег?
Итак, начнем с простой модели (кузнечный молот с ножным приводом). Потребуется для его создания:
- Сварочный аппарат, болгарка (абразивный и отрезной круги).
- Швеллер 100-120. Размер 5000 мм.
- Полоса стали (70 на 25). Размер 3300 мм.
- 2 шт. профильных трубы (70 на 40 (2000 мм) и 80 на 80 (400мм)).
- Труба Д нар. 48. Рамер 1000 мм.
- Прут Д 8.150 мм.
Делаем кузнечный молот
После приобретения инструментов выбирается точное место расположения молота. Равняем с помощью уровня поверхность, на которой он будет стоять (лучше всего залить этот участок бетоном).
Берем швеллер, два отрезка по 2 м и три — по метру. Свариваем метровые отрезки в виде короба. Это передняя деталь поперечной рамы, которая во время работы молота несет большую нагрузку. На ней будет крепиться наковальня.
Последний метровый отрезок швеллера будет задней поперечиной, а два отрезка по 2 метра укладываются параллельно и станут основой продольной рамы.
Все элементы между собой свариваются. Вот и готова рама конструкции молота.
Следующим шагом будет сборка рычага кузнечного молота. На нем на одной стороне будет закреплен боек, а на второй – противовес.
Для защиты от деформации при изготовлении и применении в работе этой детали рекомендуется полоса стали именно 25 мм по толщине и по ширине 70 мм. Длина всей полосы — 2000 мм.
В 700 мм от края стали сварочным аппаратом сделать отверстие 56 мм в диаметре, в которое вставится обрезок трубы 80 мм длинной и диаметром 48 мм. Трубу приварить со всех сторон к полосе стали, отслеживая ее симметричность и перпендикулярность относительно листа. Этот отрезок будет выполнять функцию подшипника.
Следующим шагом отрезки стали 9000 и 100 мм сваркой усиливают рычаг.
Затем кусок круглой трубы с наружным диаметром в 48 мм и метр длинной используют как ось рычага.
Рычаг же устанавливается по центру оси молота и фиксируется от продольных передвижений с помощью приваривания на ось двух отрезков прута по 75 мм и диаметром в 8 мм.
Для бойка можно использовать болванку из инструментальной стали (можно и круглого или квадратного сечения 80 на 80, 100 на 100).
Профильную трубу 70 на 40 делим пополам — и выходят две вертикальные метровые стойки, которые привариваются на раме. На этих стойках крепится ось рычага.
Для основы наковальни нужно взять профильную трубу 80 на 80 мм и 400 мм в длину, к которой привариваются два куска стальной полосы 70 на 25 мм и 150 мм в длину. Так получится стол 150 на 140 мм по размеру, который приваривается на переднюю поперечину рамы.
Для противовеса подойдет любой металлический кусок, но при этом стоит учесть, что нужно обеспечить для рычага с бойком возврат в исходное местоположение после проведенного удара.
На каждом этапе работы нужно уровнем проверять горизонтальность всей конструкции и каждой ее части по отдельности, чтобы молот не был перекошенным. От горизонтальности конструкции молота зависит качество его работы.
Интересные моменты при самостоятельной сборке молота
Самодельный молот кузнечный можно немного видоизменить при наличии другого материала. Но главное, чтобы суть его работы не поменялась.
Можно усовершенствовать и сделать пневматический молот кузнечный, как и гидро- или электроприводной. Такие конструкции хорошо подойдут не просто для улучшения своего быта, а для собственного бизнеса по производству кованой мебели или инструмента. Но потребуют больше усилий, времени и материала для изготовления.
Самодельный кузнечный молот можно изготовить и с помощью пошагового толкования, благодаря многочисленным видео на просторах Интернета. Но это еще не все! Там множество других видеопримеров, как сделать разные кузнечные молоты своими руками.
Что можно изготовить кузнечным молотом?
Некоторые мужчины не понимают, для чего применяются кузнечные молоты, своими руками сделанные или покупные.
С их помощью можно сделать у себя в гараже или мастерской кованные красивые ворота или забор, решетки на окна или столы и стулья, что-нибудь для дизайна в саду, инструмент и множество других полезных вещей.
В сельских местностях есть потомки кузнечных мастеров, которые продолжают дело своих предков, делают кузнечные молоты своими руками, различные наковальни, куют инструмент и декоративное оружие. Это для них не только хобби, но и дело всей жизни.
Кроме того, в качестве хобби каждому желающему можно сделать миникузницу и проводить экскурсии для детей старших классов, чтобы прививать у них интерес к работе, кузнечному делу, да и просто показать, как много можно сделать своими руками.
В чем плюсы самодельного кузнечного молота?
Самый главный плюс — это экономия, ведь некоторые материалы для его изготовления могут уже иметься в хозяйстве, а какие-то можно заменить идентичными, да и купить пару отрезков стали и трубы дешевле, чем уже готовый механический кузнечный молот.
Только при самостоятельном изготовлении можно полностью разобраться в механизме и принципе работы устройства.
Можно изменить конструкции и сделать усовершенствованную модель более подходящих размеров и т. д.
Да и похвастать самостоятельным изготовлением кузнечного молота перед друзьями, своим умельством и мастерством будет приятно каждому мужчине.
Механический привод для кувалды
При занятии кузнечным делом большой трудностью является первичная грубая расковка заготовки. Эту работу можно существенно облегчить самодельным механическим приводом ударяющим молотом по наковальне. Он бьет тяжелой кувалдой с высокой частотой и всегда с одинаковой силой, что позволяет расковывать деталь за один нагрев гораздо больше чем вручную.Основные материалы:
- электрический мотор со шкивом;
- большой шкив с осью;
- приводной ремень;
- натяжной шкив или ролик с осью и подшипниками;
- кувалда;
- мебельное колесико;
- наковальня или рессора;
- 2 натяжные пружины;
- талреп;
- рейки и доски;
- алюминиевая полоса 40 мм;
- фанера 20 мм;
- 2 корпусных подшипника на лапках под ось большого шкива;
- квадратная труба 20х20 мм.
Изготовление механической кувалды
Основанием станка служит деревянный верстак, собранный из бруса и доски. Он состоит из трех опор для закрепления деталей механизма. Они соединены внизу общим основанием и имеют верхнюю связь парой брусков.
На боковой полке первой опоры верстака закрепляется электродвигатель с небольшим шкивом на валу.
На него одет приводной ремень, натянутый на большой шкив, зафиксированный на центральной опоре. Он насажен на длинную ось, удерживаемую двумя корпусными подшипниками на лапках.
Большой ведомый шкив намного больше относительно ведущего, что снижает передаточное число от электродвигателя, но обеспечивает мощность.
На оси большого шкива закрепляется самодельный эксцентрик из 2-х сращенных листов фанеры. Для защиты от износа он покрыт алюминиевой полосой.
Эксцентрик зафиксирован на валу наглухо, поэтому вращается вместе с большим шкивом.
Вверху первой опоры с помощью подшипника закреплен конец ручки кувалды, что позволяет ей двигаться в одной плоскости.
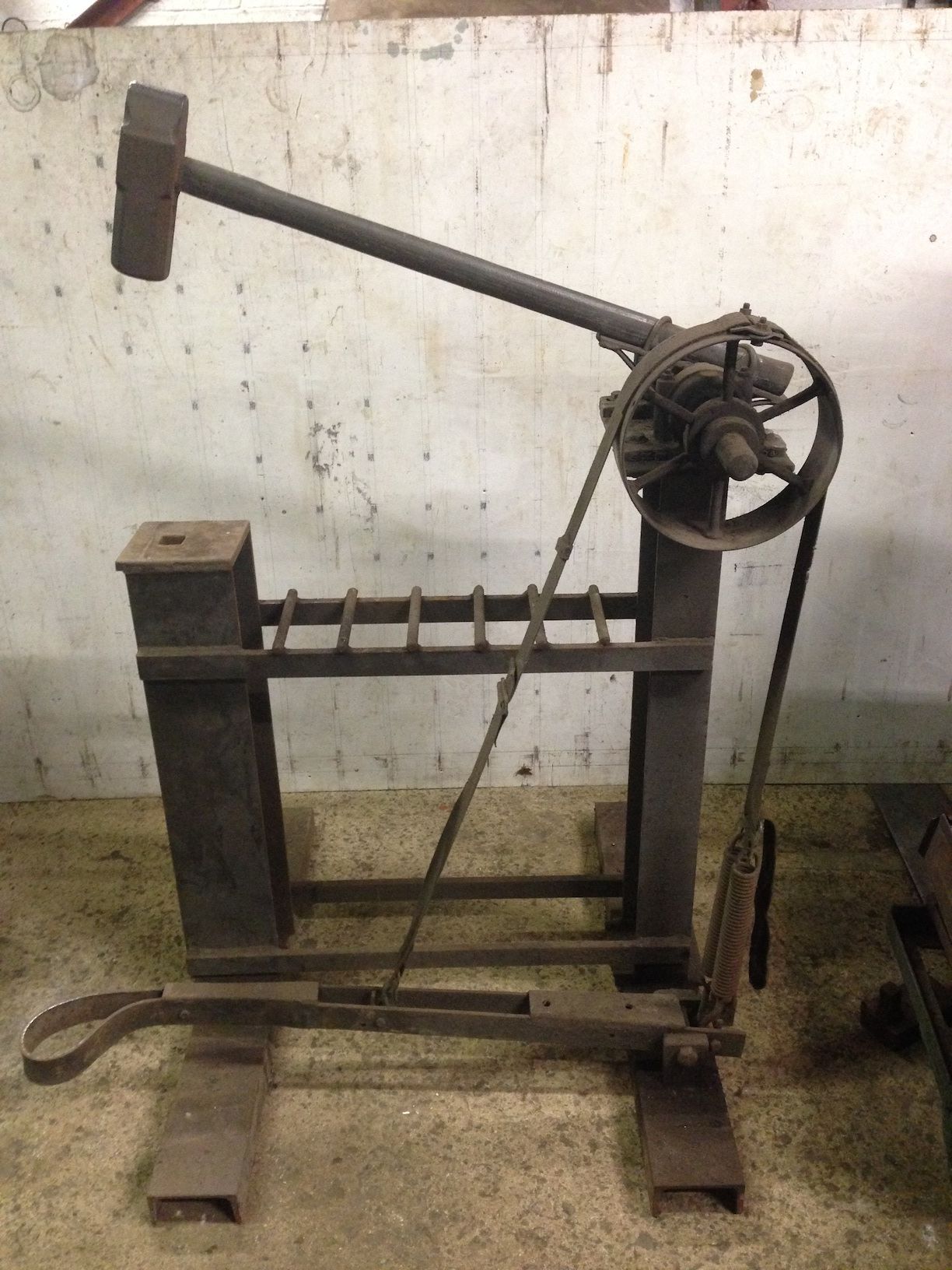
Над началом третьей опоры верстака на ручке кувалды закрепляется жесткий хомут с пружиной, притягивающей молот вниз.
Также предусмотрена деревянная рамка для ограничения верхнего хода кувалды.
На третьей опоре устанавливается наковальня или рельса. Ее высота подбирается так, чтобы молот, упертый мебельным колесом на самую низкую точку эксцентрика, доставал до наковальни с зазором в пару миллиметров.
К верхней части центральной опоры на одно крепление присоединяется рейка так, чтобы ее крепеж использовался как ось вращения всего плеча. На краю рейки у двигателя закрепляется натяжной ролик или шкив, задача которого в подтяжке провисающего приводного ремня. Второй конец плеча с помощью талрепа связывается с почти параллельным к ней квадратным металлопрофилем, расположенным внизу. Тот также благодаря одному крепежу работает как плечо. Его ось вращения располагается тоже на центральной опоре, но ниже.

С помощью талрепа проводится регулировка расстояния между рейкой и квадратом таким образом, чтобы получить при прижатии ногой к полу квадратной трубы натяжение приводного ремня на моторе.
Для использования молота нужно запустить двигатель. После этого нажав ногой на стальной квадрат можно натянуть ремень, после чего кувалда подбрасываемая эксцентриком и ускоряемая пружиной обратно начнет бить по наковальне. Как только отпустить ногу, то ремень провиснет, и удары прекратятся.
Смотрите видео
Молот в работе:
Ковка молотком | QForm
Пример моделирования ковки с молотком в QForm Молотки ковочные — одни из самых распространенных машин, используемых для ковки. Наиболее важные вопросы, возникающие при разработке технологии ковки с молотком:
- Разработка бездефектных поковок (т.е. отсутствие недозаливки и дефектов сплошности в полости штампа, а также благоприятная микроструктура)
- Достижение хорошего срока службы штампа
- Выбор правильного оборудования и расчет необходимого количества ударов
Преимущества
- Быстрое развитие технологий
- Прогноз свойств кованых деталей
- Улучшение рабочих свойств и качества поковки
- Повышение стойкости инструмента за счет уменьшения растрескивания и износа матрицы
- Прогноз распределения температуры в инструменте и заготовке
Распределение эффективных напряжений в поковке. Моделирование в QFormForged Моделирование автомобильных деталей в QForm. Красными точками обозначены круги
Специальные функции QForm, которые помогают имитировать ударную ковку
- Очень удобный интерфейс позволяет пользователю работать с разными вариантами одной технологии и быстро переключаться между ними
- Пакетный режим включен для автоматического решения нескольких вариантов технологии
- Простая настройка параметров оборудования
- Анализ нескольких графиков в одном окне
- Материал может быть удален из моделируемой поковки, чтобы показать свойства обработанной детали
- Специальная вкладка для операций многоударной ковки позволяет легко настроить любое количество ударов за одну операцию, включая все движения (вращение и смещение) заготовки перед проходом и изменение энергии удара для каждого удара
- Прогноз количества необходимых ударов
Пример
В этом видео показана оптимизация технологии ковки с использованием молотка с использованием программного обеспечения для моделирования QForm. Технология ковки цапфы состоит из 4 операций ударной ковки: волочения, высадки, правки и окончательной ковки.
Формирование нахлестов происходит в исходной технологии, как показано на первом этапе видео. Затем была увеличена высота осадки и сплющивания, чтобы избежать образования дефектов. Второй этап видео показывает, что кованая деталь после оптимизации не имеет дефектов.
МАШИНОСТРОЕНИЕ: Поковка
Ковка — это самый старый процесс формования, используемый для изготовления небольших изделий, для которых точность размера не так важна.Детали формуются путем нагревания их на открытом огне или в очаге кузнецом и придания им формы путем приложения усилий сжатия с помощью молотков. Таким образом, ковка определяется как пластическая деформация металлов при повышенных температурах до заданного размера или формы с использованием сжимающих сил, прилагаемых некоторыми средствами ручных молотков, молотов малой мощности, штампа, пресса или машины для осадки. Суть его состоит в изменении или изменении формы и сечения металла путем удара молотком при температуре около 980 ° C, при которой металл полностью пластичен и может легко деформироваться или формироваться под давлением.
Преимущества ковки
Некоторые общие преимущества ковки приведены ниже.
1. Кованые детали обладают высокой пластичностью и обладают большой устойчивостью к ударным и усталостным нагрузкам.
2. Ковка улучшает структуру металла.
3. Это приводит к значительной экономии времени, труда и материалов по сравнению с производством аналогичного изделия путем вырезания из цельного материала и последующего придания ему формы.
4. Ковка деформирует ранее созданное однонаправленное волокно, создаваемое прокаткой, и увеличивает прочность, задавая направление зерен.
5. Из-за интенсивной работы недоработки обнаруживаются редко, поэтому следует иметь хорошую надежность.
6. Достаточная степень точности может быть получена при ковке.
7. Кованые детали легко свариваются.
Недостатки ковки
Ниже приведены некоторые недостатки ковки.
1. Быстрое окисление при ковке поверхности металла при высокой температуре приводит к образованию окалины, изнашивающей штампы.
2. Трудно соблюдать жесткие допуски при ковке.
3. Ковка ограничена простыми формами и ограничена деталями, имеющими поднутрения и т. Д.
4. Некоторые материалы трудно поддаются ковке.
5. Первоначальная стоимость штампов поковок и стоимость их обслуживания высока.
6. Металлы растрескиваются или деформируются при работе при температуре ниже указанного предела.
7. Стоимость обслуживания штампованных штампов также очень высока.
Области применения ковки
Ковке можно подвергать почти все металлы и сплавы.Низкоуглеродистые и среднеуглеродистые стали легко поддаются горячей штамповке, но высокоуглеродистые и легированные стали труднее ковать и требуют более тщательного ухода. Ковка обычно выполняется для углеродистых легированных сталей, кованого железа, сплавов на основе меди, алюминиевых сплавов и сплавов магния. Нержавеющая сталь, суперсплавы на основе никеля и титан выкованы специально для использования в аэрокосмической отрасли. Хорошим примером изготовления коленчатого вала из легированной стали является ковка. Процессы ковки являются одними из наиболее важных производственных технологий, широко используемых при производстве небольших инструментов, оборудования для железных дорог, автомобилей и грузовиков, а также компонентов для авиационной промышленности.Эти процессы также широко используются при производстве деталей тракторов, судостроении, велосипедной промышленности, железнодорожных компонентов, сельскохозяйственной техники и т. Д.
ПРОИЗВОДИМОСТЬ
Легкость ковки называется ковкой. Ковкость материала также может быть определена как способность материала подвергаться деформации при сжатии без разрыва. Ковкость увеличивается с повышением температуры до точки, при которой появляется вторая фаза, например, от феррита до аустенита в стали, или если рост зерна становится чрезмерным. Основная структура кристаллической решетки металлов и их сплавов, по-видимому, является хорошим показателем их относительной ковкости. На определенные механические свойства также влияет ковкость. Металлы с низкой пластичностью имеют пониженную ковкость при более высокой скорости деформации, тогда как на металлы с высокой пластичностью не так сильно влияет увеличение скорости деформации. Чистые металлы обладают хорошей пластичностью и, следовательно, хорошими ковочными свойствами. Металлы, обладающие высокой пластичностью при холодной рабочей температуре, обладают хорошей ковкостью.
Основными сплавами для холодной или горячей штамповки являются сплавы алюминия и меди, включая относительно чистые металлы. Углеродистые стали с содержанием углерода 0,25% или менее легко поддаются горячей ковке или холодной головке. Высокоуглеродистые и высоколегированные стали почти всегда подвергаются горячей ковке. Магний, обладающий гексагональной плотноупакованной структурой (HCP), имеет низкую пластичность при комнатной температуре, но легко подвергается горячей ковке. Алюминиевые сплавы кованы при температуре от 385 ° C до 455 ° C, что примерно на 400 ° C ниже температуры затвердевания.Алюминиевые сплавы не образуют окалины во время операций горячей штамповки, поэтому срок службы штампа очень высок. Медь и латунь с содержанием цинка 30% или менее имеют отличную ковкость при холодной обработке. Латуни с высоким содержанием цинка можно подвергать холодной ковке в ограниченной степени, но они являются отличными сплавами для горячей ковки. Ковка магниевых сплавов осуществляется на прессах при температуре выше 400 ° C. При более высоких температурах магний должен быть защищен от окисления или воспламенения инертной атмосферой диоксида серы.
КОВАННЫЕ МАТЕРИАЛЫ
Чтобы быть ковким металлом, он должен обладать необходимой пластичностью.Под пластичностью понимается способность материала деформироваться при растяжении без разрыва. Ковочные работы требуют материалов, которые должны обладать свойством, описываемым как пластичность, то есть способностью выдерживать значительную высокую пластическую деформацию без разрушения даже при наличии растягивающих напряжений. Если во время ковки происходит разрушение, это связано с механизмом вязкого разрушения и вызвано растягивающими напряжениями. Материал данной пластичности может по-разному разрушаться в различных процессах, в зависимости от наложенных на него условий деформации.Поковки закупаются в виде горячекатаного проката или заготовок круглого или прямоугольного сечения. Ковочные материалы должны обладать необходимой пластичностью и должной прочностью.
Некоторые кованые металлы указаны в порядке возрастания сложности ковки.
1. Алюминиевые сплавы 2. Магниевые сплавы
3. Медные сплавы. 4. Углеродистые и низколегированные стали
5. Мартенситные нержавеющие стали 6. Аустенитные нержавеющие стали
7.Никелевые сплавы 8. Титановые сплавы
9. Колумбиевые сплавы 10. Танталовые сплавы
11. Молибденовые сплавы 12. Вольфрамовые сплавы
13. Бериллий.
ТЕМПЕРАТУРА КОВКИ
Металл должен быть нагрет до температуры, при которой он будет обладать высокими пластическими свойствами для выполнения процесса ковки. Металлическая заготовка нагревается до надлежащей температуры, так что перед деформацией она приобретает требуемые пластические свойства, которые необходимы для удовлетворительной ковки.Повышенная температура может привести к возгоранию металла. Недостаточная температура не приведет к приданию металлу достаточной пластичности, чтобы придать ему правильную форму путем обработки молотком и т. Д. Более того, в этих условиях в продукте могут возникнуть дефекты холодной обработки, такие как закалка
и растрескивание. Температура начала ковки для мягкой низкоуглеродистой стали составляет от 1250 до 1300 ° C, температура окончательной ковки составляет от 800 до 840 ° C. Соответствующие температуры для твердоуглеродистых и легированных сталей составляют от 1100 до 1140 ° C и от 830 до 870 ° C.Кованое железо лучше всего ковать при температуре чуть ниже 1290 ° C. Цветные сплавы, такие как бронза и латунь, нагреваются примерно до 600–930 ° C, алюминиевые и магниевые сплавы — примерно до 340–500 ° C. Для получения хороших результатов температура ковки должна быть соответствующей. Чрезмерная температура может привести к возгоранию металла, что нарушит сцепление металла. Недостаточная температура не придаст металлу достаточной пластичности. Операция ковки в металле, если она закончена при более низкой температуре, может привести к холодному закалке и появлению трещин.Однако чрезмерный нагрев кованной детали может привести к окислению и, следовательно, к потере материала. Температуру нагрева стали для ручной ковки можно оценить по цвету нагрева и по цвету света, излучаемого нагретой сталью. Для точного определения температуры ковки нагретой детали обычно используются оптические пирометры.
ПРЕИМУЩЕСТВА ПОВКОВКИ ПО СРАВНЕНИЮ ЛИТЬЯ И ОБРАБОТКИ
Из-за присущего улучшения размера зерна и введения непрерывного потока зерна в структуру готовой кованой детали поковка имеет следующие преимущества по сравнению с литьем и механической обработкой.Некоторые из таких преимуществ приведены ниже.
(i) Повышенная прочность и жесткость.
(ii) Уменьшение веса готовой детали.
(iii) Экономия в материале.
(iv) Устранение внутренних дефектов, таких как трещины, пористость, раковины и т. Д.
(v) Способность выдерживать непредсказуемые нагрузки во время эксплуатации.
(vi) Минимальная машинная обработка детали, особенно если она выкована в штампах.
ВЛИЯНИЕ ПОВКОВКИ НА ХАРАКТЕРИСТИКИ МЕТАЛЛА
Обычно ковочный материал выбирается на основе определенных желаемых механических свойств, присущих композиции и / или тех, которые могут быть получены путем ковки.Таких свойств может быть одно или несколько, например прочность, сопротивление усталости, ударам или изгибу, хорошие характеристики обработки, долговечность и т. Д. Непрерывный и непрерывный поток зерна в кованой детали приводит к более высокой прочности и ударной вязкости. В литой детали нет растекания зерна. Литая деталь имеет беспорядочную ориентацию зерен, поэтому она имеет слабую кристаллическую структуру. В прокатанном или механически обработанном компоненте существует прерывистый поток зерна. Катаная деталь имеет лучшую пластичность в направлении, параллельном направлению пластического удлинения, из-за эффекта ориентации зерен.Когда деталь обрабатывается, обработка прерывает непрерывный поток зерна. В кованых деталях волокнистые линии потока компонента являются непрерывными. Ковка приводит к изменению расположения волокон, поскольку обработка проводится при температуре выше рекристаллизации. Исходные кристаллы деформируются во время операции ковки, и многие компоненты осаждаются при высоких температурах, которые снова становятся растворимыми в твердом железе при замерзании, таким образом увеличивая локальную однородность металла. Такие свойства, как предел упругости, предел прочности металла при растяжении, не доказаны из-за потока зерна.Если кованую заготовку зубчатого колеса вырезать в плоскости, выровненной по направлению, а поверхность отшлифовать до гладкости и вдоль зубьев заготовки зубчатого колеса и погрузить в раствор кислоты, невооруженным глазом обнаженный металл будет казаться имеющим структуру, подобную волокну, показаны на фиг.
1 и фиг.2.
Рис. 1 Волокнистая кованая структура заготовки шестерни
Рис. 2
Ковка обычно применяется для тех компонентов, которые требуют высокой прочности и устойчивости к ударам или вибрации. Он придает металлу мелкокристаллическую структуру, улучшает физические свойства, закрывает все пустоты и придает металлу формы.Он улучшает механические свойства металлов и улучшает поток зерна, что, в свою очередь, увеличивает прочность и ударную вязкость кованого компонента. Но также могут быть определенные дефекты, такие как включения окалины на поверхности, перекос штампов, трещины и т. Д. Эти дефекты можно контролировать. Преимущества процессов ковки заключаются в том, что, хотя металлическую деталь необходимо нагреть до правильной температуры ковки перед формованием, будет использовано меньше металла, чем если бы форма была выточена из цельного металлического блока.Все поковки покрыты окалиной, поэтому их необходимо очистить. Это делается путем травления в кислоте, дробеструйной обработки или галтовки в зависимости от размера и состава поковок. Если при ковке произошла некоторая деформация, может потребоваться калибровка или правка. Для больших поковок обычно предусматривается контролируемое охлаждение. Также может потребоваться термообработка для обеспечения определенных физических свойств. Однако некоторые общие характеристики кованых деталей приведены ниже.
(i) Кованые детали обладают направленными свойствами и, следовательно, обладают хорошей прочностью.
(ii) Улучшены механические свойства материалов, такие как относительное удлинение, устойчивость к деформации и вибрациям.
(iii) Процесс ковки ограничивает структуру металла, закрывая полости.
(iv) В кованных деталях минимизированы трещины и выбоины.
ОБЫЧНЫЙ РУЧНОЙ КОВКОВОЙ ИНСТРУМЕНТ
Для выполнения ковочных операций вручную используются некоторые обычные ручные кузнечные инструменты. Их также называют кузнечными инструментами, потому что кузнец — это тот, кто занимается ковкой металлов в горячем состоянии.Основные инструменты ручной ковки такие же, как показано ниже.
1. Клещи 2. Фланец
3. Обжимка 4. Фуллер
5. Пуансон 6. Заглушка
7. Горячее долото 8. Молотки
9. Наковальня 10. Обжимной блок
11. Выколотка 12. Ударник
14. Латунная шкала 15. Латунь
16. Калибр Блэка кузнеца 17.Заголовок инструмент
Некоторые из ручных кузнечных инструментов изображены на рис. 3-1, а их применение описано ниже.
Ключи
Клещи обычно используются для удержания при ковке. На рис. 3 показаны различные виды клещей.
1. Клещи плоские используются в основном для зажимных работ прямоугольного сечения.
2. Рифленые клещи с прямой кромкой обычно используются для удержания прутков квадратного, круглого и шестигранного сечения.
3.Заклепочные или кольцевые ключи широко используются для удержания болтов, заклепок и других работ круглого сечения.
4. Гиг-клещи используются для удержания общих подбирающих работ, прямых или конических.
Флаттер
Флаттер показан на рис. 3. Он обычно используется в кузнечном цехе для придания гладкости и точности изделиям, которые уже были сформированы с помощью долбиков и обжимных прессов.
Swage .
Прессовка (рис. 3) используется для ковки, которую необходимо уменьшить или довести до круглой, квадратной или шестиугольной формы.Он выполнен с половинными канавками, размер которых соответствует сокращаемой работе. Он состоит из двух частей: верхней части с ручкой и нижней части с квадратным стержнем, который входит в отверстие для крепления на лицевой поверхности наковальни.
Fuller
Fuller (3) используется в кузнечном цехе для заточки кузнечного изделия. Он состоит из верхних и нижних инструментов, как и в случае обжимных прессов. Фуллер изготавливается различных форм и размеров в соответствии с потребностями, размер обозначает ширину более широкой кромки
Пуансон
Пуансон (рис.3) используется в кузнечном цехе для проделывания отверстий в металлической детали при нагреве ковки.
Рис. 3 Ручной кузнечный инструмент
Заклепочная головка
Заклепочная головка (рис. 3) применяется в кузнечно-прессовом цехе для изготовления головок заклепок на деталях.
Зубила
Зубила используются для резки металла и надрезания перед ломкой. Они могут быть горячими или холодными в зависимости от того, горячий или холодный металл нужно резать. Горячее долото, обычно используемое в кузнечном цехе, показано на рис.14.7. Основное различие между ними — край. Кромка холодного долота закалена и отпущена под углом около 60 °, в то время как кромка горячего долота составляет 30 °, и закалка не требуется. Кромка сделана слегка закругленной для лучшего резания.
Ручные молотки
В ручной ковке используются два основных вида молотов: (1) ручной молоток, используемый самим кузнецом, и (2) кувалда, используемая ударником. Ручные молотки (рис. 4) могут быть далее классифицированы как (а) ударно-ударные молотки, (б) молотки с прямым ударным ударом и (в) молотки с поперечным ударным ударом. Кувалды (рис. 4) могут быть далее классифицированы как (а) двусторонний молоток, (б) прямой ударный молоток и (в) поперечно-ударный молоток. Головки молотов изготовлены из литой стали, их концы закалены и отпущены. Эффектное лицо выполнено слегка выпуклым. Вес ручного молотка варьируется от 0,5 до 2 кг, тогда как вес
кувалды варьируется от 4 до 10 кг.
Рис. 4 Типы молотков
Набор молотков
Набор молотков, обычно используемых в кузнечном цехе, показан на рис.5. Используется для отделки углов при работе с заплечиками, где плоская поверхность была бы неудобной. Он также используется для растягивания работ по заглатыванию.
Рис. 5 Установочный молоток
Наковальня Наковальня — это наиболее часто используемый инструмент в кузнечном цехе, который показан на Рис.6. Он служит опорой для работы кузнеца во время ковки. Корпус наковальни изготовлен из низкоуглеродистой стали с лицевой стороной из инструментальной стали, приваренной к корпусу, но клюв или выступ, используемые для изгиба кривых, не имеют стальной поверхности. Круглое отверстие в опоре, называемое отверстием притчеля, обычно используется для гибки стержней небольшого диаметра и в качестве штампа для операций горячей штамповки.Квадратное или жесткое отверстие используется для крепления квадратных стержней различных фитингов. Наковальни в кузнечном цехе могут варьироваться от 100 до 150 кг, и они всегда должны стоять так, чтобы их верхняя поверхность составляла около 0,75 метра. с пола. Этой высоты можно достичь, поставив наковальню на деревянную или чугунную основу в кузнечно-прессовом цехе.
Рис. 6 Упор
Обжимной блок
Обжимной блок, обычно используемый в кузнечном цехе, показан на рис. 7. Он в основном используется для операций загибки, гибки, прямоугольной формы, калибровки и формовки при ковке.Это 0,25 тн. или даже шире. Его можно использовать как на подставке, так и на ребре.
Рис. 7 Пресс-блок
Выколотка
Выколотка, обычно используемая в кузнечном цехе, показана на Рис.8. Это коническая штанга из инструментальной стали. Отверстия открываются с помощью более крупного конического пуансона, называемого выколоткой.
Рис. 8 Выколотка
Hardie
Hardie — это тип долота, используемого в кузнечном цехе. Он показан на рис. 9. Его коническая головка закреплена в отверстии для крепления наковальни режущей кромкой вверх.Обрезаемая часть держится над режущей кромкой закрепленного на опоре выноса, другое долото помещается над работой, и резка выполняется молотком.
Рис. 9 Hardie
Лопата
Лопата, обычно используемая в кузнечном цехе, показана на рис. 10. Она используется для загрузки угля или кокса в печь. Он также используется для установки кусков угля в топку и удаления золы из топки.
Покер
Покер (Рис. 10) используется для удаления клинкера из печи и разрыхления кусков угля в печи.
Грабли
Грабли (рис. 10) служат для укладки углей на фурмы.
Клювое железо
Клювое железо, обычно используемое в кузнечном цехе, показано на рис. 11. Оно также известно как небольшая наковальня из кованой стали. Его передний верхний конец состоит из рога, а верхний задний конец — из плоского хвоста. Его конический хвостовик вставляется в отверстие наковальни. Его обычно используют в качестве наковальни для небольших кузнечных работ.
Рис.11 Клюв
СПОСОБЫ КОВКИМетоды ковки, обычно используемые для изменения формы сырья в готовую форму в кузнечном цехе, обычно подразделяются на две категории: ручная ковка и механическая ковка.Это обсуждается, так как под номером
Ручная ковка выполняется в кузнечной мастерской. Изделие нагревается до температуры ковки в поде, а затем с помощью клещей помещается на наковальню. Затем его выковывают с помощью ручных молотков и других инструментов ручной ковки для придания особой формы.
Ручная ковка (рис. 12)
1. Осадка 2. Гибка
3. Рисование 4. Резка
5. Установка 6. Пробивка
7. Сплющивание 8.Фуллеринг
9. Кузнечная сварка 10. Обжимка
Рис. 12 Ручная ковка
Некоторые важные операции ручной ковки описаны ниже.
(i) Вытяжка
Вытяжка используется для уменьшения толщины стержня и увеличения его длины. Это может быть выполнено путем обработки металла над выступом наковальни, как показано на рис. 13, а затем путем ударов молотком по поверхности наковальни. Закругленный выступ наковальни действует как тупой край, заставляя металл течь в продольном направлении при ударе молотка.Для опускания очень тяжелых работ можно использовать фуллер для опускания бруска через рог (круглую часть) наковальни.
Профессия Кузнечный молоток
Рабочие, занимающиеся ковкой с ударной ковкой, используют кузнечные машины и оборудование, в частности, обработанные молотки, для придания заготовкам из черных и цветных металлов желаемой формы.Они заботятся о кузнечных молотках, которые падают на заготовку, чтобы изменить ее форму по форме штампа, который может быть закрытым или открытым, полностью закрывая заготовку или нет.
Хотите знать, какая профессия и профессия вам больше всего подходят? Пройдите наш бесплатный тест на карьерный код Голландии и узнайте.
Тип личности
Знание
- Типы ударных отбойных молотков
Различные типы молотов, используемые в процессе ковки, такие как противоударный молот, отбойный молоток, отбойный молоток для досок, отбойный молоток с ремнем, отбойный молоток и другие.
- Процессы ковки
Различные процессы штамповки металла при ковке, такие как обжимка, ковка в открытых штампах, автоматическая горячая штамповка, зубчатая штамповка, штамповочная штамповка, валковая штамповка, высадка, штамповка и другие.
Навыки
- Удалить окалину с металлической детали
Удалите скопившуюся окалину или металлические «чешуйки» на поверхности металлической заготовки, образовавшиеся в результате окисления после извлечения из печи, путем распыления на нее жидкости на масляной основе, которая вызовет отслаивание во время процесса ковки.
- Обеспечить правильную температуру металла
Обеспечивает необходимую, обычно постоянную температуру обрабатываемых металлических деталей в процессе их изготовления.
- Ключи кузнечные
Безопасно используйте соответствующие кузнечные инструменты и оборудование, включая кузнечные ключи для перемещения и перемещения горячих металлических заготовок во время процессов ковки.
- Молот для ковки с отводом
Стрелец ковочный молот, предназначенный для формовки горячего или холодного металла с использованием большой силы энергии, отслеживание и управление им в соответствии с правилами.
Дополнительные знания и навыки
изготовление металлической тары работать в команде в опасной среде изготовление инструментов умирает использование пыли для ковки работать эргономично горячая ковка производство парогенераторов производство стальных бочек и аналогичных емкостей заменить умирают изготовление дверей из металла обработка черных металлов выполнить тестирование продукта производство отопительного оборудования виды процессов производства металла изготовление металлоконструкций вести учет хода работ технологии обработки металлов управлять подъемным оборудованием конвейерная лента монитора записывать производственные данные для контроля качества удерживайте металлическую заготовку в машине холодная ковка обратитесь к техническим ресурсам машина для встречного удара настроить контроллер машины обработка цветных металлов эксплуатировать печь выполнять техническое обслуживание машины консультировать техников .