Цементация стали — технологический процесс и его описание. Цементация стали в домашних условиях
Сама по себе цементация стали является процессом, в основе которого лежит химико-термическая обработка. Суть ее состоит в осуществлении диффузионного насыщения поверхности указанного материала достаточным количеством углерода при нагревании в определенной среде.
Цементация стали. Цель данного действия
Основной задачей указанного процесса является проведение обогащения верхнего слоя машинных деталей и элементов необходимым количеством углерода, процентное содержание которого в данном случае может составлять 0,8-1,1%. В результате такой операции после осуществления закалки получают высокий уровень твердости материала, при этом его пластичная сердцевина сохраняется. Это немаловажные свойства данного процесса.
Разновидности
По степени прочности образования сердцевины принято выделять три основные группы обрабатываемого материала:
- С неупрочняемой сердцевиной.
В данную группу входят такие марки цементируемых сталей углеродистых, как 10, 15, 20. Используют их в деталях с небольшими размерами и малоответственными функциями. В данном случае под цементируемым слоем при осуществлении закалки происходит превращение аустенита в феррито-перлитную смесь.
- С сердцевиной, упрочняемой слабо. В состав этой группы включают хромистые низколегированные стали таких марок, как 15Х, 20Х. Здесь проведение дополнительного легирования с помощью малых добавок ванадия обеспечивает получение более мелкого зерна, что приводит к улучшению пластичности и вязкости материала.
- С сильно упрочняемой сердцевиной. Стали данной группы применяют при изготовлении деталей, которые обладают большим сечением или сложной конфигурацией, а также испытывают влияние значительных ударных нагрузок или подвергаются воздействию немалых переменных напряжений. В них осуществляют введение никеля (12Х2Н4А, 12ХНЗА, 20ХН). Из-за дефицитности данного материала иногда проводят его замену марганцем, при этом применяют ввод небольшого количества ванадия или титана для дробления зерна.
В основном цементация стали используется для образования высокого процентного соотношения твердости поверхности детали, а также для достижения высокой износоустойчивости, которая создается благодаря применению термической обработки после проведения указанного процесса.
Какие детали подвергаются данной операции
Цементация стали применяется для следующих изделий:
— зубчатых колес;
— «пальцев»;
— валов;
— осей;
— рычагов;
— «червяков»;
— деталей подшипников (крупногабаритных колец и роликов) и др.
Способы цементации
Если существует несколько видов указанного материала, то для каждого из них будет применяться своя собственная методика данного процесса. Как правило, цементированная сталь может создаваться в различных условиях и средах, а также при обязательной температуре от 850 до 950 градусов по Цельсию. Поэтому разделяют несколько методов этого действия:
1. Процесс цементации, происходящий в твердом карбюризаторе. В этом случае возможно использование органических веществ (костей животных, древесины и т.д.) и неорганических (кокса) в сочетании с различными активаторами. Обогащение углеродом будет происходить при проведении химической реакции его окисления. Применение активаторов в данном случае способствует лучшему и быстрому ее протеканию. Такой метод особенно целесообразен для достижения больших глубин науглероживания. Он является эффективным при штучном изготовлении стальных изделий. Однако данный процесс очень трудоемкий, он влечет за собой большие затраты сил, времени и энергии.
2. Процесс цементации, происходящий под воздействием газов. В данном методе принято использовать обогащенные газы (природный, магистральный и др.) или категорию инертных (азот). Все зависит от индивидуального подхода. К тому же цементируемая сталь на основе газов создается с малым процентом алифатических предельных углеводородов, пропана или алканов. Чаще всего этот метод применяется в масштабном производстве, но является очень затратным в плане денежных средств. Похожий способ применяется при термическом производстве. При этом в горячую ротортную печь вводят смеси органических высокомолекулярных соединений (например, скипидара, этилового спирта и т.д.), которые, в свою очередь, обладают способностью распада под влиянием катализаторов (никелевых).
3. Процесс жидкостной цементации. Его применяют в цианидных и бесцианидных ваннах. Каждая из этих сред характеризуется своими особенностями, преимуществами и недостатками. К примеру, цианидные ванны не относятся к категории безвредных. Их принято классифицировать как опасные носители не только для окружающей среды, но и для человека. Поэтому при работе с таким материалом необходимо стараться соблюдать все предписанные меры безопасности, чтобы избежать неблагополучных последствий. А вот метод, основанный на бесцианидной ванне, не рекомендовано применять в силу того, что он ведет к необратимому загрязнению окружающей среды и наносит ей огромный урон. Указанные способы если и применяют на практике, то только лишь для получения небольших глубин науглероживания.
Термообработка цементованных изделий
Данный процесс является также достаточно важным этапом обработки деталей. Ведь даже после цементации изделие не обладает высоким процентом износостойкости и надёжности. Поэтому завершающим шагом в данном случае служит работа по закаливанию и отпуску. Процесс закалки характеризуется рядом особенностей и свойств. Весь процесс цементации проходит под влиянием роста зерна, а его отдача по сечению является неодинаковой и расходуется неравномерно. Поэтому в работе выделяют несколько этапов закалки, каждый из которых происходит в определённых температурных условиях.
Вывод
Ознакомившись с вышесказанным, можно сказать, что организация указанного процесса при изготовлении стальных изделий является очень важной. Данное действие значительно укрепит поверхностный слой детали. При обладании определенными навыками в этой сфере и наличии необходимых материалов и оборудования может быть осуществлена цементация стали в домашних условиях.
Цементация — это.
.. Что такое Цементация?
Этим названием определяется в технике обработки металлов процесс, с помощью которого железным изделиям сообщается способность образовать поверхностный закал, т. е. твердую наружную корку, придающую железу свойства закаленной стали, при чем внутренняя масса металла сохраняет мягкость и вязкость, свойственные железу. Благодаря такой поверхностной осталёвке (цементации) изделие хорошо противостоит давящим и истирающим усилиям и в то же время чуждо хрупкости и ломкости, какими отличаются изделия, состоящие сплошь из закаленной стали. Благодаря этим своеобразным свойствам оцементованных железных частей они получили большое применение в машиностроении, именно в качестве таких машинных частей, которые должны выносить сильное трение на поверхности и в то же время подвергаться ударам и сотрясениям. Таковы, напр., цапфы (пальцы) локомотивных колес, шейки осей и валов, шарнирные валки и проч., а из пассивных машинных частей — гайки, винты, гаечные ключи и т. п. Ц. железного предмета распространяется, как уже было замечено выше, лишь на некоторый слой прилегающей к его поверхности, не проникая далеко в глубь его.
Процесс Ц. состоит собственно в насыщении железа углеродом, т. е. получении сталеватого железа. Твердости собственно этим процессом сообщено быть не может; ее сообщает оцементованному предмету последующая закалка (см.).След., Ц. и закалка, образуют один нераздельный процесс. Для насыщения железа углеродом пользуются свойством его соединяться с углеродом при возвышенной температуре в прикосновении с углем, взятым в виде порошка.
Для этого обыкновенно применяют древесно-угольный порошок (всего лучше из березового угля), или, еще успешнее — измельченный в порошок животный уголь (пережженная кожа, кости, рога и копыта животных).
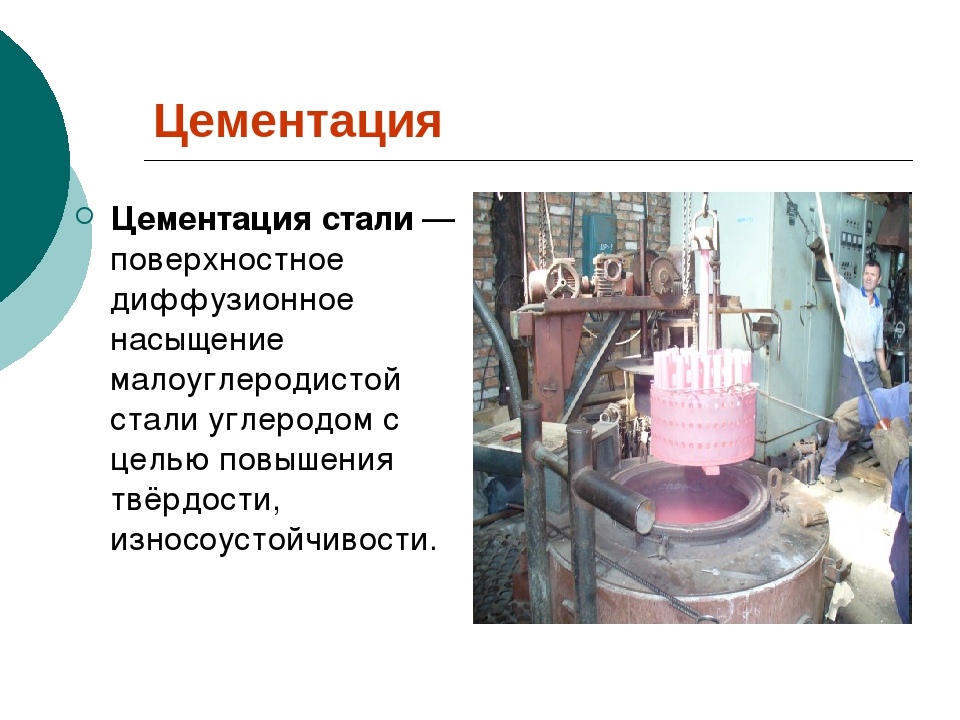

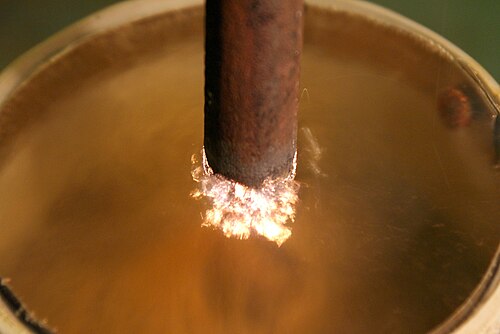


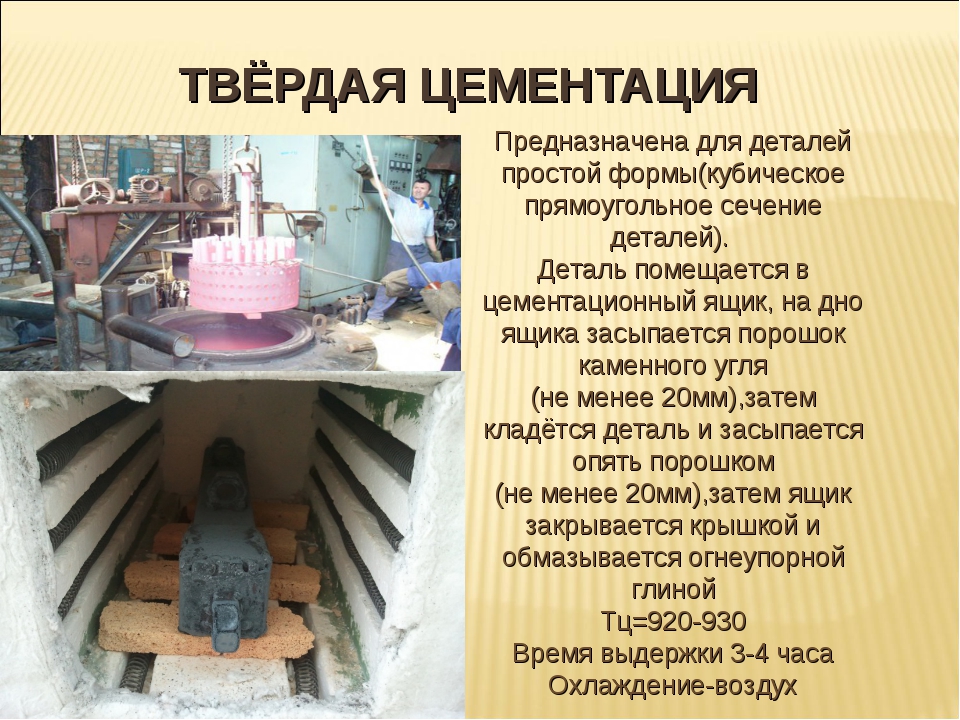
Цементовальная печь.
В сводчатой внутренней камере этой печи помещаются два (иногда 3—4) прямоугольного сечения корыта аа, охватываемые снизу и с боков пламенем. Корыта эти отформованы из огнеупорной глины или из шамотной массы и служат для помещения в них цементуемых железных полос. Корытам сообщается длина, на 1 м большая против длины железных полос. Стенки их вделаны в наружные поперечные стенки печи. Последние имеют в местах, соответствующих внутренней полости корыт, отверстия для раскладывания через них полос. Во время хода операции эти отверстия герметически закупориваются. На рисунке изображены: bb — боковые, массивные стенки печи; с — ее свод; d — топочная решетка; ее — пламенные пролеты. Корыта имеют ширину в 600—800 мм и такую же высоту. Приступая к загрузке печи, прежде всего выстилают дно корыт слоем угольного порошка, а поверх его укладывают ряд железных полос, оставляя между соседними полосами промежутки не менее 10 мм, которые затем также забиваются угольным порошком. Поверх железных полос насыпается снова порошок, слоем в 20—30 мм толщины, а поверх его укладывается второй ряд железных полос, снова перекрываемый слоем угольного порошка. Таким образом продолжают загрузку, пока не достигнут уровня на 150 мм ниже верхнего края стенок корыта. Тогда остающееся пространство в корыте заполняют тонким песком.
Одна печь может вместить в себе от 3 до 20 тонн железа. Нагрузив корыта, заделывают и замазывают наглухо глиной загрузочные отверстия и приступают к растопке печи. Сначала поддерживается лишь слабый огонь, который постепенно все более и более усиливается, пока внутренняя поверхность стенок печи не раскалится добела (это достигается на шестые или седьмые сутки). В этом жару печь поддерживается еще в продолжение 5—9 суток. К концу этого срока железо вполне превращается в сталь. На Ц. берутся лишь отборные сорта железа; у нас на уральских заводах — кричное, древесно-угольное железо; в Англии — шведское древесно-угольное. Цементная сталь носит еще названия «морянки» и «томленки». Для улучшения ее качеств она обыкновенно еще проваривается или переплавляется. О Ц. броневых плит — см. Плиты броневые.
В. Кнаббе. Δ.
Цементация стали: тонкости процесса
Posted by Менеджер in Теория металлаЦементация — процесс химико-термической обработки, заключающийся в диффузионном насыщении поверхностного слоя стали углеродом при нагреве в соответствующей среде.
Цель цементации — обогащение поверхностного слоя деталей машин углеродом до концентрации 0,8—1,1% и получение после закалки высокой твердости при сохранении пластичной сердцевины. Цементации подвергаются детали, изготовленные из низкоуглеродистых сталей (0,1—0,2% С) марок 15, 20 или легированных низкоуглеродистых сталей марок 20Г, 20Х, 20ХФ, 12ХНЗА, 20Х2Н4А, 18ХГТ, 18Х2Н4ВА, 20ХГНР и др.
Цементация может проводиться в твердых, газообразных и жидких углеродсодержащих средах, которые называются карбюризаторами.
Цементация в твердом карбюризаторе. Наиболее старым способом является цементация в твердой среде (в твердом карбюризаторе). При этом способе цементации карбюризатором служит смесь древесного угля и углекислых солей (углекислого бария — ВаС03, углекислого натрия (соды) — Na2C03 и др.). Углекислые соли добавляются к древесному углю в количестве 10—40%. В практике цементации применяют различные составы карбюризаторов.
Для цементации в твердом карбюризаторе детали помещают в цементационный (стальной) ящик и засыпают карбюризатором. Упаковка деталей в ящик с карбюризатором должна производиться таким образом, чтобы детали со всех сторон были окружены карбюризатором и не соприкасались друг с другом, со стенками и дном ящика. Ящик закрывают крышкой и замазывают огнеупорной глиной. Через отверстия в крышке в ящик вставляют стержни из такой же низкоуглеродистой стали, из которой изготовлены цементуемые детали. Эти стержни называются «свидетелями» и служат они для контроля цементации. Ящик с упакованными в нем в карбюризаторе деталями (рис. 152) помещают в печь и нагревают до 900—950° С.
При нагреве протекают следующие процессы. Углерод угля соединяется с кислородом воздуха, находящимся в ящике, и образуется окись углерода (СО). Этот процесс можно представить следующей реакцией:
2С + 02 = 2СО
Окись углерода разлагается на углекислый газ (С02) и углерод, образующийся в виде атомов (атомарный углерод):
2СО-С02 + С
Атомарный углерод проникает (диффундирует) в поверхностный слой детали. Так как детали нагреты до 900—950° С, т. е. выше верхней критической точки Ас3у и в стали при такой температуре образуется 7-железо, углерод, проникая в сталь, растворяется в v-железе с образованием аустенита:
Fe.. + C = Fe,(C).
Цементация стали — Слесарное дело
Цементация (науглероживание) – это технология термообработки сталей. Она применяется для подготовки стали к другому виду термообработки, закалке. Цементация предназначена для тех марок стали, которые из-за низкого содержания в них углерода не поддаются или плохо поддаются закалке. Суть этой технологии состоит в том, что заготовка из такой стали насыщается углеродом (науглероживается) до такой степени, чтобы обеспечить возможность её закалки. Чаще всего науглероживанию подвергают только верхний слой металла, чтобы в нем образовалось больше мартенсита, чем в сердцевине, и сформировался твердый поверхностный слой. При этом сердцевина стальной заготовки чаще всего должна оставаться вязкой и мягкой.
Цементация проводится в различных средах при температурах от 850°C до 950°C. По типу среды различаются следующие методы:
1) цементация в твердом карбюризаторе, при которой применяются неорганические (кокс) и органические вещества (древесина, кости животных и т.п.) с добавлением активаторов. Насыщение углеродом происходит в результате химической реакции окисления углерода. Активаторы способствуют протеканию этой реакции.
2) газовая цементация, при которой используются специально обогащенные газы (природный газ, магистральный газ и др.) или инертный газ (азот). При этом к газу, применяемому для цементации, добавляются небольшие количества алифатических предельных углеводородов, алканов, чаще всего пропана.
Аналогичный метод все чаще внедряется в термических производствах. В этом случае в горячие ретортные печи вводятся смеси высокомолекулярных органических соединений (скипидара, этилового спирта и др.), которые затем разлагаются под действием никелевых катализаторов.
3) жидкостная цементация двух типов: в цианидных и в бесцианидных ваннах.
Однако, поскольку в соляной ванне помимо прочего также содержится азот, может происходить его поглощение сталью. А это может неблагоприятно сказаться на последующей обработке заготовки резанием.
Кроме того, цианидные ванны опасны для окружающей среды и человека. Поэтому при использовании жидкостной цементации в цианидных ваннах необходимо соблюдать предписанные меры безопасности. В этой связи более целесообразным является применение бесцианидных ванн. В наши дни жидкостная цементация, даже в бесцианидных ваннах, почти не применяется в связи с высоким уровнем загрязнения окружающей среды.
Преимущества и недостатки различных методов цементации:
1) Цементация в твердом карбюризаторе особенно целесообразна для достижения большой глубины науглероживания, а также при штучном производстве изделий из стали. Недостатком этого метода являются высокая трудоемкость и плохая варьируемость условий науглероживания.
2) В серийном или массовом производстве целесообразно применять газовую цементацию, так как этот метод позволяет достаточно широко варьировать условия науглероживания. Единственным недостатком является высокая себестоимость.
3) Жидкостную цементацию применяют для получения небольшой глубины науглероживания, так как уже при незначительной продолжительности погружения заготовки в ванну происходит достаточно большое насыщение углеродом её поверхностного слоя. Поэтому слишком большая продолжительность погружения ведет к коррозии заготовки.
< Предыдущая | Следующая > |
---|
Цементация стали — Википедия. Что такое Цементация стали
Цемента́ция ста́ли — поверхностное диффузионное насыщение стали углеродом с целью повышения твёрдости, износоустойчивости.
Цементации подвергают низкоуглеродистые (обычно до 0,25 % C) и легированные стали, процесс в случае использования твёрдого карбюризатора проводится при температурах 900—950 °С, при газовой цементации (газообразный карбюризатор) — при 850—900 °С.
После цементации изделия подвергают термообработке, приводящей к образованию мартенситной фазы в поверхностном слое изделия (закалка на мартенсит) с последующим отпуском для снятия внутренних напряжений.
Способы цементации:
- в твёрдом карбюризаторе
- в газовом карбюризаторе
- в кипящем слое
- в растворах электролитов
- в пастах
Цементация в твёрдом карбюризаторе
Цементовальная печь XIX векаВ этом процессе насыщающей средой является древесный уголь в зёрнах поперечником 3,5—10 мм или каменноугольный полукокс и торфяной кокс, к которым добавляют активизаторы. Этот процесс известен по крайней мере с XII века[1].
Технология процесса состоит в следующем: Загрузка деталей в стальной ящик с герметичным песчаным затвором. Укладка деталей производится таким образом, чтобы они были покрыты карбюризатором со всех сторон, не соприкасались друг с другом и стенками ящика. Далее ящик герметично закрывается песчаным затвором или замазывается огнеупорной глиной и загружается в печь.
Стандартный режим: 900—950 °С, 1 час выдержки (после прогрева ящика) на 0,1 мм толщины цементированного слоя. Для получения 1 мм слоя — выдержка 10 часов.
При «ускоренном» режиме цементация производится при 980 градусах. Выдержка уменьшается в два раза, и для получения слоя 1 мм требуется 5 часов. Но при этом образуется цементитная сетка, которую придётся убирать многократной нормализацией металла.
Цементация в газовом карбюризаторе
Этот процесс осуществляют в среде газов, содержащих углерод. Газовая цементация имеет ряд преимуществ по сравнению с цементацией в твёрдом карбюризаторе, поэтому её широко применяют на заводах, изготовляющих детали массовыми партиями.
В случае с газовой цементацией можно получить заданную концентрацию углерода в слое; сокращается длительность процесса, так как отпадает необходимость прогрева ящиков, наполненных малотеплопроводным карбюризатором; обеспечивается возможность полной механизации и автоматизации процессов, и значительно упрощается последующая термическая обработка деталей, так как закалку можно проводить непосредственно из цементационной печи.
Цементация в кипящем слое
Процесс цементации в кипящем слое проходит в атмосфере эндогаза с добавкой метана. Кипящий слой представляет собой гетерогенную систему, в которой за счёт проходящего потока газа через слои мелких (0,05-0,20 мм) частиц (чаще корунда) создаётся их интенсивное перемешивание, что внешне напоминает кипящую жидкость. Частицы корунда располагаются на газораспределительной решётке печи. При определённой скорости прохождения восходящего потока газа (выше критической скорости) частицы становятся подвижными, и слой приобретает некоторые свойства жидкости (псевдоожиженный слой). В этом состоянии сцепление между частицами нарушено, они становятся подвижными и опираются не на решётку, а на поток газа. Достоинствами процесса цементации в кипящем слое являются: сокращение длительности процесса вследствие большой скорости нагрева и высокого коэффициента массоотдачи углерода; возможность регулирования углеродного потенциала атмосферы в рабочей зоне печи; уменьшение деформации и коробления обрабатываемых деталей за счёт равномерного распределения температуры по всему объёму печи. Процесс цементации в кипящем слое может быть использован на заводах мелкосерийного и единичного производства.
Цементация в растворах электролитов
Использование анодного эффекта для диффузионного насыщения обрабатываемой поверхности углеродом в многокомпонентных растворах электролитов — один из видов скоростной электрохимико-термической обработки (анодный электролитный нагрев) малогабаритных изделий. Анод-деталь при наложении постоянного напряжения в диапазоне от 150 до 300 В разогревается до температур 450—1050°С. Достижение таких температур обеспечивает сплошная и устойчивая парогазовая оболочка, отделяющая анод от электролита. Для обеспечения цементации в электролит, кроме электропроводящего компонента, вводят углеродсодержащие вещества-доноры (глицерин, ацетон, этиленгликоль, сахароза и другие).
Цементация в пастах
Цементация с нанесением на науглероживаемую металлическую поверхность С-содержащих материалов в виде суспензии, обмазки или шликера, сушкой и последующим нагревом изделия ТВЧ или током промышленной частоты. Толщина слоя пасты должна быть в 6—8 раз больше требуемой толщины цементованного слоя. Температуру цементации устанавливают 910—1050 °С.
Примечания
Литература
Ссылки
Цементация структура цементованного слоя — Энциклопедия по машиностроению XXL
Сталь для цементации должна обладать минимальной склонностью к перенасыщению углеродом, сохранению остаточного аустенита, карбидообразованию, внутреннему окислению легирующих элементов и анормальности структуры цементованного слоя. Она должна быть мелкозернистой, обладать узкой полосой прокаливаемости, обеспечивающей стабильную деформацию при цементации и последующей термической обработке и хорошо обрабатываться резанием. [c.151]Это обеспечивает измельчение зерна и полную закалку цементованного слоя и частичную перекристаллизацию и измельчение зерна сердцевины. После газовой цементации часто применяют закалку без повторного нагрева, а непосредственно из печи после подстуживания изделий до 840—860 °С для уменьшения коробления обрабатываемых изделий. Такая обработка не исправляет структуры цементованного слоя и сердцевины, поэтому непосредственную закалку применяют только в том случае, когда изделия изготовлены из наследственно мелкозернистой стали. Для уменьшения деформации пементованных изделий выполняют также ступенчатую закалку в горячем масле (160—180 °С). [c.237]
При газовой цементации часто применяют закалку без повторного нагрева, а непосредственно из цементационной печи после подстуживания изделий до 840—860 °С. Такая обработка не исправляет структуру цементованного слоя и сердцевины, поэтому ее применяют только для изделий, изго-тoвJilшшx из наследственно мелкозернистых сталей. [c.123]
Цементации подвергают углеродистые и низкоуглеродистые стали с низким содержанием углерода (0,1-0,2 %). В результате на поверхности концентрация углерода возрастает до 0,8-1,1 %. Толщина цементованного слоя составляет 1-2,5 мм. Концентрация углерода убывает по толщине слоя по мере удаления от поверхности. Поэтому в структуре цементованного слоя можно выделить три зоны заэвтектоидную, состоящую из перлита и расположенного по границам зерен вторичного цементита эвтек-тоидную зону состоящую из перлита доэвтектоидную, состоящую из перлита и феррита. При этом количество феррита по мере приближения к сердцевине возрастает. [c.144]
После цементации детали подвергают термической обработке для обеспечения высокой твердости поверхности, исправления структуры перегрева и устранения карбидной сетки в цементированном слое. Закалку производят при 780-850 С с последующим отпуском при 150-200 °С. При этом происходит измельчение зерна цементированного слоя и частично зерна сердцевины. После цементации в твердом карбюризаторе в целях получения мелкозернистой структуры поверхностного слоя и сердцевины выполняют двойную закалку (рис. 10.6). В процессе первой закалки деталь нагревают выше температуры точки на 30-50 °С, в результате чего измельчается структура сердцевины и устраняется цемен-титная сетка в поверхностном слое. При второй закалке деталь нагревают выше температуры точки на 30-50 °С, вследствие чего измельчается структура цементованного слоя, обеспечивается высокая твердость. Двойная закалка способствует повышению механических свойств деталей, но увеличивает их коробление, окисление и обезуглероживание. Окончательной операцией термической обработки является низкий отпуск при 150-200 °С, уменьшающий остаточные напряжения и не снижающий твердости стали. После [c.222]
Типичная структура цементованного слоя на поверхности низкоуглеродистой стали после медленного охлаждения от температуры цементации показана на рис. 7.3. Обычно ее сопоставляют со схемами, представленными на рис. 7.4. Наружная часть слоя, содержащая > 0,8% С, имеет структуру заэвтектоидных сталей — перлит и вторичный цементит, который при медленном охлаждении выделяется на границах аустенитных зерен в виде оболочек (на шлифе сетка). Средняя часть слоя, имеющая эв-тектоидную концентрацию, состоит из перлита. Далее по направлению к сердцевине концентрация углерода уменьшается, структура соответствует доэвтектоидной стали, причем количество перлита уменьшается при приближении к сердцевине. [c.200]
Однако чрезмерно высокое содержание легирующих элементов (в особенности дефицитных) в сталях для цементуемых изделий, например шестерен, не рекомендуется ибо при этом затрудняется применение наиболее экономически и технически выгодного метода непосредственной закалки их после цементации. Непосредственная закалка высоколегированных сталей неприемлема из-за опасности образования в структуре цементованного слоя чрезмерно большого количества остаточного аустенита, вследствие чего может значительно снизиться прочность изделия, например шестерен. [c.304]
При одинарной закалке высоколегированных сталей в структуре цементованного слоя сохраняется большое количество (до Ю—60% и более) остаточного аустенита, снижающего твердость. Для разложения остаточного аустенита после цементации чаще применяют высокий отпуск при температуре 600—640° С, затем закалку с пониженной температуры и низкий отпуск (см. табл. 170). Иногда стали, содержащие большое количество остаточного аустенита, после закалки обра батывают при температуре—70н —80° С это превращает большую часть [c.334]
При одинарной закалке высоколегированных сталей в структуре цементованного слоя сохраняется большое количество (до 50—60% и более) остаточного аустенита, снижающего твердость. Такие стали после закалки обрабатывают холодом это переводит большую часть остаточного аустенита в мартенсит в результате значительно повышается твердость. Например, твердость хромоникелевой стали после цементации и закалки составила HR 52, а после обработки холодом возросла до HR 59—60. [c.253]
В отдельных случаях более, целесообразно вместо охлаждения на воздухе после цементации производить первую закалку в масле и затем, для улучшения структуры цементованного слоя, вторую закалку при 820° С (схема IV). При этом в наружном слое снижается количество остаточного аустенита из-за понижения концентрации легирующих элементов и углерода в аустените в процессе повторного нагрева до более низкой температуры закалки. [c.633]
На фиг. 2 показана структура цементованного слоя стали Ст. 3, подвергавшейся цементации при температуре 950° С и выдержке в течение 4 час. при подаче масла 60 капель в минуту. Глубина слоя 0,8 мл1, структура перлит мелкого сложения. [c.16]
Цементация при указанных температурах является трудоемкой операцией, требующей большого расхода энергии для нагрева, длительной выдержки при этих температурах, боль-июй затраты рабочей силы при малоэффективном использовании оборудования. Между тем известно, что одним из основных факторов, определяющих скорость диффузии углерода и структуру цементованного слоя, является температура процесса. Повышение температуры процесса цементации увеличивает скорость диффузии углерода, позволяет значительно повысить производительность процесса и снизить себестоимость обработки. Однако до сих пор внедрение высокотемпературной газовой цементации в практику работы заводов тормозилось рядом причин [c.44]
Однако одно из основных возражений остается в силе — это ухудшение структуры и механических свойств цементованных сталей. Вопрос о получении доброкачественной структуры сердцевины изделий и цементованного слоя во многом зависит от режима цементации прп высоких температурах, состава карбюризатора, состава цементованных сталей и последующего режима термической обработки. От комплекса этих условий и будет, по нашему мнению, зависеть качество структуры цементованного слоя и сердцевины и механические свойства. сталей. [c.45]
Дефекты цементации. Основной дефект цементации — увеличение зерна стали вследствие высоких температур нагрева и длительных выдержек. При газовой цементации в случае неправильно выбранного соотношения скоростей абсорбции и диссоциации (когда абсорбция отстает от диссоциации) на поверхности изделий возможно появление плотной сажистой пленки, затрудняющей диффузию. Иногда вместо нормальной заэвтектоидной структуры цементованного слоя наблюдается выделение цементита в виде крупных включений, окруженных ферритом, что приводит к образованию в изделиях мягких пятен после закалки. Для устранения этого дефекта повышают температуру и производят резкое охлаждение при закалке. Большое значение имеет также прочная связь поверхностного слоя с сердцевиной изделий при резком изменении концентрации углерода по сечению возможно отслаивание или растрескивание цементированного слоя. [c.151]
Толщина цементованного слоя определяется размерами детали, условиями ее работы, содержанием углерода и легирующих элементов в стали. После цементации и последующей термической обработки требуемая структура цементованного слоя (на глубине 0,2 мм) — мелкоигольчатый мартенсит (углеродистая сталь) или мелкоигольчатый мартенсит с включениями дисперсных карбидов (легированная сталь) (рис. 98, а). Наличие в цементованном слое структурно свободных карбидов в виде сетки приводит при шлифовании к получению трещин (из-за хрупкости слоя). Кроме того, крупные включения карбидов, выходя на поверхность, могут выкрашиваться в процессе работы. Если детали работают при больших знакопеременных давлениях, в структуре цементованного слоя недопустимо наличие большого количества остаточного аустенита, который превращается в неотпущенный мартенсит, имеющий большую хрупкость. Присутствие больших количеств остаточного аустенита (более 10—15%) приводит к усталостному разрушению слоя. [c.127]
Следовательно, при ступенчатых режимах цементации даже при оптимальной концентрации углерода на поверхности происходит перераспределение легирующих элементов между фазами цементованного слоя. В результате при последующей закалке в масле в структуре цементованного слоя появляется трооститная сетка (в связи с понижением прокаливаемости), снижаются поверхностная твердость и долговечность деталей. Для предотвращения образования трооститной сетки в цементованном слое в связи с образованием карбидов не следует осуществлять ступенчатые режимы цементации для деталей из сталей, склонных к образованию стойких карбидов, или применять стали, менее склонные к образованию карбидной фазы при ступенчатой цементации (по экспериментальным данным это стали, содержащие не менее 0,5% Мо и не более 0,5% Сг). [c.131]
Зубчатые колеса из хромоникелевых сталей 12Х2Н4А, 20Х2Н4А и других непосредственной закалке не подвергают — получается большое количество остаточного аустенита, что снижает твердость поверхности зуба. Поэтому зубчатые колеса из этих сталей после цементации охлаждают на воздухе, подвергают высокому отпуску при 600—650° С (для подготовки структуры цементованного слоя под закалку во время отпуска происходит распад остаточного аустенита и мартенсита и выделяются карбиды), закаливают в масле от 800—820° С и подвергают низкому отпуску при 180—200° С. Для уменьшения деформации зубчатые колеса после высокого отпуска до закалки иногда подвергают шевингованию. [c.224]
Цементация производится. обычно твердым карбуризатором. Для улучшения структуры цементованного слоя и получения вязкой сердцевины сильно нагруженных пальцев иногда вводятся дополнительные операции в термообработку в зависимости от сорта стали (предварительная закалка из ящика, нормализация или отжиг после цементации, двойная закалка и т. д.). После термообработки твердость цементованного слоя ио [c.213]
Повышение концентрацин углерода выше этого предела снижает предел выносливости, предел прочности при износе (на 10—15%), при кручении (на 15—20%) и ударную вязкость 8]. Типичная структура цементованного слоя углеродистой стали после медленного охлаждения с температуры цементации приведена на фиг. 49. [c.79]
Марка стали Термическая обработка после цементации (основной вариант) Температура отпуска °С Структура цементованного слоя [c.379]
После газовой цементации используют закалку без повторного нагрева, а непосредственно из цементационной печи после подстуживания изделий до 840—860 °С. Такая обработка не исправляет структуры цементованного слоя и сердцевины и не приводит к измельче- [c.197]
Для разложения остаточного аустенита после цементации применяют высокий отпуск при 630—640 °С, после чего следует закалка с пониженной температуры и низкий отпуск. Такая обработка также обеспечивает высокую твердость цементованного слоя. Структура сердцевины должна состоять из низкоуглеродистого мартенсита или нижнего бейнита. Низкоуглеродистый мартенсит обеспечивает повышенную прочность и достаточную вязкость сердцевины. Сохранение обособленных участков или сетки феррита нежелательно, так как это сопровождается значительным снижением ирочности, пластичности и вязкости цементованных деталей Твердость сердцевины для различных сталей составляет HR 20—40, [c.238]
После цементации и закалки детали из легированной стали рекомендуется подвергать поверхностному наклепу, в результате поверхностного деформирования остаточный аустенит превращается в мартенсит. После термообработки цементованный слой имеет структуру игольчатого мартенсита с мелкими глобулями карбидов и неболь-П1ИМ количеством остаточного мартенсита. Эта структура отличается высокой износостойкостью. [c.238]
Анализ причин брака должен производиться по документам экспресс-лаборатории. Например, установлено, что структурный анализ цементованного слоя систематически отмечает наличие в структуре цементитной сетки при глубине слоя в пределах чертежных допусков. Для выяснения причины, вызывающей этот брак, необходимо изучить анализы газа, применяемого для цементации. Наличие в газе избытка предельных углеводородов и будет причиной такого брака. В случае же нормы по содержанию активной части газа карбюризатора причиной брака будет нарушение технологического процесса либо в отношении температуры, либо в отношении дозировки газа. [c.503]
Для цементации применяют низкоуглеродистую нелегированную и легированную сталь с содержанием углерода 0,08—0,30% (табл. 26). К цементуемой качественной стали предъявляются требования по чистоте металла, структуре, механическим свойствам, закаливаемости цементованного слоя, обрабатываемости резанием и др. [c.96]
Термическая обработка стали после цементации и свойства цементованных деталей. Окончательные свойства цементованных деталей достигаются в результате термической обработки, выполняемой после цементации. Этой обработкой можно исправить структуру и измельчить зерно сердцевины и цементованного слоя, неизбежно увеличивающееся во время длительной выдержки при высокой температуре цементации, получить высокую твердость в цементованном слое и хорошие механические свойства сердцевины устранить карбидную сетку в цементованном слое. [c.236]
После цементации термическая обработка иногда сострит из двойной закалки и отпуска. Первую закалку (или нормализацию) с нагревом до 880—900 °С (выше точки Ас сердцевины) назначают для исправления структуры сердцевины. Кроме того, при нагреве в поверхностном слое в аустените растворяется цемен-гитная сетка, которая уже вновь при быстром охлаждении не образуется. Вторую закалку проводят с нагревом до 760—780 °С для устранения перегрева цементованного слоя и придания ему высокой твердости. Недостаток такой термической обработки заключается в сложности технологического процесса, повышенном короблении, возникающем в изделиях сложной формы, и возможности окисления и обезуглероживания. [c.237]
Окончательные свойства цементованные изделия приобретают в результате термической обработки после цементации. Эта обработка необходима для того, чтобы исправить структуру и измельчить зерно сердцевины и цементованного слоя, неизбежно увеличивающееся во время длительной выдержки при высокой температуре цементации, получить высокую твердость в цементованном слое и хорошие механические свойства сердцевины. [c.123]
После цементации термическая обработка иногда состоит из двойной закалки и отпуска. Первую закалку (или нормализацию) с нагревом до 880— 900 °С (выше точки Асз сердцевины) назначают для исправления структуры сердцевины. Вторую закалку проводят с нагревом до 760—780 С для устранения перегрева цементованного слоя и придания ему высокой твердости. Недостаток такой термообработки — сложность технологического процесса, возможность окисления и обезуглероживания. [c.123]
После цементации для получения высокой твердости цементованного слоя проводят закалку. Температура закалки 780— 810° С. Такая температура является оптимальной для стали, содержащей 0,75—0,85% углерода (обычное содержание углерода в цементованном слое). Малоуглеродистая сердцевина не воспринимает закалку и она имеет структуру феррита с перлитом. Чтобы предотвратить скалывание цементованного закаленного слоя при больших контактных напряжениях и ударах, необходим низкий отпуск. [c.154]
Содержание углерода в поверхностном слое при данной температуре определяется пределом растворимости углерода в аустените (линия SE диаграммы Fe—F j ). Так как температура цементации выще температуры /4 j, углерод поглощается аустенитом (рис. 4.1, а). Предельное содержание углерода в аустените в непосредственной близости от поверхности обычно составляет 1,1… 1,2 % и быстро убывает по толщине детали. При охлаждении детали происходят фазовые 11ревращения в поверхностном слое, а поскольку цементованный слой имеет переменную концентрацию, то его структура различна по глубине. [c.70]
С с целью измельчения структуры сердцевины и устранения цементитной сейгки в поверхностном слое. Вторую закалку проводят с нагревом до 760…780 °С для устранения перегрева цементованного слоя и придания ему высокой твердости. Для наследственно мелкозернистых сталей применяют закалку с температур выще Асу После газовой цементации такие изделия часто закаливают без повторного нагрева, непосредственно из печи с температур 840…860 °С после подстуживания с целью уменьшения коробления обрабатываемых изделий. [c.70]
Под цементацией принято понимать процесс высокотемпературного насыщения поверхностного слоя стали углеродом. Так как углерод в а-фазе практически нерастворим, то процесс цементации осуществляется в интервале температур 930-950 °С — т. е. выще а у-превращения. Структура поверхностного слоя цементованного изделия представляет собой структуру заэвтектоидной стали (перлит и цементит вторичный), поэтому для придания стали окончательных — эксплуатационных — свойств после процесса цементации необходимо выполнить режим термической обработки, состоящий в закалке и низком отпуске температурно-временные параметры режима термической обработки назначаются в зависимости от химического состава стали, ответственности, назначения и геометрических размеров цементованного изделия. Обычно применяется закалка с температуры цементации непосредственно после завершения процесса химико-термической обработки или после подстуживания до 800-850 °С и повторного нагрева выше точки Ас центральной (нецементованной) части изделия. После закалки следует отпуск при температурах 160-180 °С. [c.470]
Качество процесса цементации оценивается по эффективной толщине цементованного слоя, которая определяется по одному из двух показателей — твердости или структ>ре слоя. Структура поверхностного слоя цементованной стали состоит из нескольких зон поверхностной — заэвтектоидной (перлит + цементит), эвтектоидной — перлитной и доэвтектоидной — перлито-ферритной. Эффективную толщину цементованного слоя по структуре принято измерять на металлографических шлифах в отожженном состоянии при увеличениях от 100 до 500 раз. Границей цементованной зоны считается структура состоящая из 50 % перлита и 50 % феррита, что соответствует концентрации углерода равной 0,4 масс. %. [c.472]
Рис. 7.4. Участок диаграммы состояния Fe — ГезС, а также изменение содержания углерода и структуры по толщине цементованного слоя h (схема) ta — температура цементации U i Ui — температура нагрева при первой и второй закалке соответственно |
В соответствии с распределением углерода по глубине цементованного слоя изменяются микроструктура и твердость (рис. 2). После закалки с температуры цементации структура состоит из аустенита, мартенсита и избыточных карбидов (Fe, Сг)зС. Твердость на поверхности равна HR 20—30, далее твердость постепенно увеличивается с понижением содержания углерода. [c.600]
Окончательные свойства цементованные изделия приобретают в результате термической обработки, выполняемой после цементации (табл. 170). Эта обработка необходима для исправления структуры, а нередко и измельчения зерна сердцевины и цементованного слря получения высокой твердости цементованного слоя и хороших механических свойств сердцевины устранения карбидной сетки в цементованном слое, которая может возникнуть при пересыщении его углеродом. [c.334]
Науглероживание — Изготовленные на заказ, кованые, литые и плакированные детали — ООО «Бунти»
Науглероживание относится к производственному процессу, в ходе которого стальные или железные детали упрочняются за счет пропитки поверхности атомами углерода. Этот процесс способствует «поверхностному упрочнению» или «упрочнению поверхности», при котором внутренняя часть металла остается сравнительно мягкой, а внешний слой затвердевает в прочную защитную оболочку. Науглероживание обычно основывается на строго контролируемых процессах термообработки для ускорения переноса атомов углерода.
Металлурги нашего века используют множество методов для получения поверхностей из закаленной стали. Наряду с индукционной закалкой и азотированием науглероживание стало одним из самых популярных производственных процессов.
Процесс цементации
Производитель выполняет науглероживание, стараясь упрочить внешнюю поверхность железа или низкоуглеродистой стали за счет добавления углерода. Этот процесс изменяет химический состав поверхности железных или стальных деталей.Заготовки обычно проходят этот процесс после обработки. Инструмент с науглероживанием будет менее легко ломаться и более эффективно противостоит царапинам и другим истиранию при нормальном использовании. Производители используют измерения глубины корпуса, чтобы оценить толщину этого внешнего защитного слоя.
Во время науглероживания атомы углерода диффундируют из источника углерода в поверхность металлической заготовки. Они остаются постоянно прикрепленными к структуре металла, пока деталь остывает.Углерод увеличивает твердость одним из двух способов: либо он становится частью внешней структуры самого металла, образуя внешний мартенситный или перлитный стальной слой, либо в некоторых случаях он образует карбиды после объединения с другими элементами сплава. . В обоих случаях образуются прочно закаленные стальные поверхности.
Способы науглероживания
Четыре метода науглероживания стали популярными в производственных условиях. У каждого есть свои преимущества и недостатки:
Жидкое науглероживание
Производители иногда вводят атомы углерода на поверхность низкоуглеродистой стали, погружая металл при высоких температурах в ванны с высокоуглеродистыми жидкостями.
Подробности процесса
В прошлом жидкости, используемые для этого процесса, часто включали цианид, сильную кислоту, которая помогала шлифовать поверхность для подготовки металла к осаждению углерода. Сегодня производители обычно используют более экологически чистые и менее токсичные кислоты в процессе науглероживания жидкости. Сетчатые корзины или проволока позволяют всей заготовке оставаться подвешенной в ванне с жидкостью в течение желаемого периода времени, обеспечивая равномерное науглероживание.
Преимущества
Этот процесс упрощает производство внешних металлических корпусов с высоким содержанием углерода. Обычно для его завершения требуется сравнительно немного времени. Жидкая цементация очень эффективна для упрочнения поверхностей деталей малых и средних размеров; производители могут легко автоматизировать этот процесс.
Примеры
Производители, производящие мелкие детали, такие как шарикоподшипники, часто используют науглероживание жидкостью.
Науглероживание газом
В этом широко популярном методе науглероживания используются такие газы, как метан или окись углерода, чтобы вызвать отложение углерода на поверхности низкоуглеродистых сталей или чугунов.
Подробности процесса
Сегодня производители тщательно контролируют температуру для достижения оптимального уровня науглероживания. Этот процесс обычно происходит в больших печах. Это часто происходит в сочетании с автоматизацией и предлагает отличный контроль над глубиной упрочнения.
Преимущества
Науглероживание газом позволяет производителям легче работать с очень большими деталями. Кроме того, это может позволить компании эффективно упрочнять большие объемы материала.
Примеры
Этот процесс позволяет науглероживать коммерческие сейфы и хранилища, а также большие промышленные лезвия и другие тяжелые предметы.
Пакет науглероживания
Этот производственный процесс, открытый много лет назад, включает упаковку низкоуглеродистой стали или железа древесным углем или коксом и нагревание материала при очень высоких температурах.
Подробности процесса
Образуется газообразный оксид углерода, который помогает переносить углерод на поверхность металла. Производители часто сталкиваются с трудностями при поддержании однородной температуры по всей поверхности с помощью этого метода, поэтому уровни углерода в науглероженной поверхности могут варьироваться. Этот процесс имеет тенденцию генерировать несколько тонкие (от 1 мм до 1,5 мм) слои твердого сплава.
Преимущества
Методы науглероживанияPack позволяют производственным компаниям науглероживать как крупные детали, так и большие объемы мелких деталей.
Примеры
Производители иногда производят недорогие потребительские инструменты, такие как садовые лопатки и грабли, используя этот метод.
Вакуумная цементация
Обычно используется в сочетании с закалкой в масле или газе под высоким давлением, в вакууме
цементировочная закалка | цементация стали
науглероживание стали для цементации обычно имеют содержание основного углерода около 0,2%, с содержанием углерода в науглероженном слое обычно регулируется на уровне от 0,8 до 1% C. Однако поверхностный углерод часто ограничивается 0,9% из-за слишком высокого содержание углерода может привести к остаточному аустениту и хрупкости мартенсит. Мост науглероженные стали — это раскисленные стали (раскисленные добавление алюминия), которые поддерживают мелкий размер зерна до температуры около 1040 ° C.Стали грубые зерна могут быть науглерожены, если двойная закалка обеспечивает измельчение зерна. Двойная закалка обычно состоит из прямой закалить, а затем повторно охладить при более низкой температуре. Многие легированные стали для цементации теперь указываются на основе прокаливаемости сердечника. Хотя те же соображения в целом применимы к выбору немецентрированных марок, есть некоторые особенности науглероживания. Первый, в цементированной стали закаливаемость как гильзы, так и ядро нужно учитывать. Из-за разницы в углероде содержимое, корпус и ядро имеют совершенно разную жесткость, и эта разница для некоторых сталей намного больше, чем для другие. Кроме того, у этих двух регионов разные служебные функции.До появления бедных легированных сталей, таких как 86xx серии, с бором и без него, было мало необходимости беспокоит способность к упрочнению, поскольку содержание сплава в сочетании с высоким содержанием углерода всегда обеспечивает адекватное прокаливаемость. Это все еще верно, когда стали закаливаются непосредственно после науглероживания, так что углерод и легирующие элементы находятся в растворе в случае аустенита.В детали, которые повторно нагреваются для закалки, а также в тяжелых секциях детали, однако, требования к упрочняемости как корпуса, так и сердечника следует тщательно оценить. The взаимосвязь между температурным градиентом и углеродным градиентом во время закалки науглероженной детали может дать измеримый разница в глубине корпуса, измеренная по твердости.Что то есть увеличение прокаливаемости основы может дать более высокую доля мартенсита для данного уровня углерода, дающая увеличенная измеренная глубина корпуса. Следовательно, более мелкий углерод профиль и более короткое время науглероживания можно использовать для достижения желаемый результат в правильно подобранной стали. Ядро Твердость.Распространенной ошибкой является указание слишком узкого диапазона твердости сердечника. Когда окончательная закалка происходит от температуры достаточно высокий, чтобы позволить развитию полной твердости сердечника, изменение твердости в любом месте будет полоса прокаливаемости стали в соответствующем положении на закаленном в конце образце на прокаливаемость. В стандартные стали закупаются по химическому составу вместо прокаливаемости диапазон может составлять 20 или более Очки HRC; например, 8620 может варьироваться от 20 до 45 HRC при 4/16 дюйма(6,35 мм) положение. Диапазон из 25 пунктов подчеркивает преимущество покупки до характеристик закаливаемости чтобы избежать недопустимых колебаний в диапазонах для стандартных химических сталей. Другой способ контролировать ядро твердость в узких пределах, не прибегая к использованию высоколегированных сталей заключается в использовании окончательной закалки из нижнего температура так, чтобы в корпусе развилась полная твердость без недостатка чрезмерной твердости сердечника. Шестерни почти всегда закаливаются в масле, потому что держится на самом низком уровне. Поэтому легированные стали обычно выбираются, и ведется много споров о том, какие именно сплав. Низколегированные стали, такие как 4023, 5120, 4118, 8620, и 4620, с содержанием углерода от 0,15 до 0,25%, являются широко используется и в целом удовлетворительно.Обычно первые выбор — одна из двух последних упомянутых сталей, любая из который должен быть безопасным для всех обычных приложений. Финал выбор, основанный на опыте эксплуатации или динамометрических испытаниях, должна быть самая дешевая сталь, которая будет выполнять эту работу. Для тяжелых условий эксплуатации используются более высоколегированные марки, такие как 4320, 4817 и 9310 оправданы, если основаны на фактических характеристиках тесты.Испытание на ресурс шестерен в тех же креплениях на службе, чтобы подтвердить как дизайн, так и выбор стали особенно важно. В другие приложения, когда искажения не являются основным фактором, углеродистые стали, описанные выше, закаленные в воде, могут быть используется диаметром до 50 мм (2 дюйма). В больших размерах, низколегированный стали, закаленные в воде, такие как 5120, 4023 и 6120, могут быть используется, но необходимо учитывать возможные деформации и трещины при закалке. избегали. науглероживание Методы. При этом основной принцип науглероживания остался без изменений с момента первого применения науглероживания, метод использовался для введения углерода в сталь. непрерывной эволюции. В в его самом раннем применении детали просто помещались в подходящие контейнер и покрытый толстым слоем угольного порошка (пакетная науглероживание).Хотя эффективен для введения углерода, этот метод был чрезвычайно медленным, и, поскольку спрос на большее производство росло, новый процесс с использованием газовой атмосферы был развит. В науглероживание газом, детали окружены углеродсодержащим атмосферу, которую можно постоянно пополнять, чтобы может поддерживаться высокий углеродный потенциал.Хотя скорость науглероживание существенно увеличивается в газовой атмосфере, метод требует использования многокомпонентной атмосферы состав которых необходимо очень тщательно контролировать, чтобы избежать вредные побочные эффекты, например, поверхностные и межзеренные. оксиды. Кроме того, требуется отдельное оборудование. для создания атмосферы и управления ее составом.Несмотря на Эта повышенная сложность науглероживания газа стала самый эффективный и широко используемый метод цементации стали запчасти в большом количестве. В усилия, необходимые для упрощения атмосферы, науглероживания в бескислородная среда при очень низком давлении (вакуумная цементация) был изучен и превратился в жизнеспособный и важный альтернатива.Хотя кожух печи в некоторых отношениях усложняется, атмосфера сильно упрощается. Однокомпонентная атмосфера, состоящая исключительно из простого можно использовать газообразный углеводород, например метан. Более того, потому что детали нагреваются в бескислородной среде, температура науглероживания может быть значительно увеличена без риска поверхностного или межзеренного окисления.В допустимая более высокая температура увеличивает не только твердое растворимость углерода в аустените, но также и его скорость диффузия, так что время, необходимое для достижения глубины корпуса желаемое уменьшается. Хотя вакуумная цементация устраняет некоторые сложности, связанные с газом карбунзирование, это создает новую серьезную проблему, которая должна быть адресованным.Поскольку вакуумная цементация проводится при очень высокой низкое давление и скорость потока науглероживающего газа в печь очень низкий, углеродный потенциал газ в глубоких нишах и глухих отверстиях быстро истощается. Если не пополнить этот газ, в случае глубина по поверхности детали. Если, чтобы решить эту проблему, давление газа значительно увеличился, возникает другая проблема, проблема свободного углерода образование или образование сажи. Таким образом, чтобы получить случаи достаточно равномерной глубины на деталь сложной формы, давление газа необходимо увеличивать периодически для пополнения обедненной атмосферы в нишах а затем снова снизили до рабочего давления. Ясно, В вакуумной науглероживании существует тонкий баланс: процесс условия должны быть скорректированы для достижения наилучшего компромисса между однородностью корпуса, риском образования сажи и науглероживанием показатель. А метод, который преодолевает обе эти основные проблемы, но сохраняет желательные черты простой атмосферы и допустимые рабочая температура — плазменная или ионная науглероживание. Кому Подведем итог, методы науглероживания включают: Газ
науглероживание Процесс характеристики вышеупомянутых методов цементации делятся на две общие группы: Обычный
методы, вводящие углерод через газовую атмосферу, соляные ванны
или угольные пачки В Обычно при обычных методах угарный газ разрушается вниз по стальной поверхности: 2CO ? CO2 + C The высвободившийся углерод легко растворяется аустенитной фазой и проникает в стальной корпус. Для какого-то процесса методы (газовая и пакетная науглероживание), производимый диоксид углерода может реагировать с углеродной атмосферой или древесным углем с образованием новый окись углерода обратной реакцией. науглероживание чаще всего выполняется при температуре от 850 до 950 ° C (1550 и 1750 ° F), но иногда используются более высокие температуры для сокращения времени цикла и / или получения большей глубины высокоуглеродистый поверхностный слой. А комплексная модель науглероживания газа должна включать алгоритмы которые описывают: Углерод
диффузия |
Науглероживание и упрочнение — Metlab of Wyndmoor PA
(нажмите на миниатюру, чтобы увеличить)
1.) Вал двойной спиральной шестерни весом 19 000 фунтов, науглероженный до эффективной глубины корпуса 0,250 дюйма, закаленный в 20 000 галлонов перемешиваемого теплого масла. Шестерня была подвергнута термообработке вертикально одной из двух Metlab диаметром 54 дюйма на 180 дюймов печи с глубоким шахтным карьером.Его контрольно нагревали до 1750 ° F, выдерживали при температуре почти 200 часов, затем медленно охлаждали, повторно нагревали до температуры закалки, закалку, отпуск, глубокую заморозку и повторный отпуск. | Науглероживание |
2.) 26 000 фунтов плоской проволоки из низкоуглеродистой стали подготавливаются для сфероидального отжига. Отжиг сфероидальной формы — это промежуточный этап обработки, позволяющий катать проволоку до меньшего калибра без образования трещин. | Науглероживание |
Науглероживание | Удобства
Науглероживание
Науглероживание, также называемое закалкой, представляет собой процесс термообработки, при котором образуется поверхность, устойчивая к износу, при сохранении ударной вязкости и прочности сердечника.Эта обработка применяется к деталям из низкоуглеродистой стали после механической обработки, а также к подшипникам, зубчатым колесам и другим компонентам из высоколегированной стали.
Науглероживание увеличивает прочность и износостойкость за счет диффузии углерода в поверхность стали, образуя каркас, сохраняя при этом значительно меньшую твердость в сердечнике. Эта обработка применяется к низкоуглеродистой стали после механической обработки.
Прочные и очень твердые детали сложной и сложной формы могут быть изготовлены из относительно недорогих материалов, которые легко подвергаются механической обработке или формованию перед термообработкой.
Большая часть науглероживания осуществляется путем нагрева компонентов в шахтной печи или печи с герметичной атмосферой и введением науглероживающих газов при определенной температуре. Науглероживание газом позволяет точно контролировать как температуру процесса, так и атмосферу науглероживания (углеродный потенциал). Науглероживание — это процесс время / температура; науглероживающая атмосфера вводится в печь на необходимое время для обеспечения правильной глубины корпуса. Углеродный потенциал газа можно снизить, чтобы обеспечить диффузию, избегая избытка углерода в поверхностном слое.
После науглероживания изделие либо медленно охлаждается для последующего закалки, либо закаливается непосредственно в масло. Выбор закалки производится для достижения оптимальных свойств с приемлемыми уровнями изменения размеров. Для минимальной деформации можно использовать закалку в горячем масле, но ее применение может быть ограничено требованиями к прочности продукта. В качестве альтернативы кольца подшипников могут быть подвергнуты закалке под давлением для сохранения допусков на их размеры, что сводит к минимуму необходимость чрезмерного шлифования после термообработки.В некоторых случаях продукт подвергают отпуску, затем криогенно обрабатывают для преобразования остаточного аустенита в мартенсит, а затем повторно отпускают.
Metlab может науглероживать и упрочнять шестерни и другие компоненты, которые достаточно малы, чтобы их можно было держать в руке, до 14 футов в диаметре и 16 футов в высоту, а их вес составляет до 50 000 фунтов. Мелкие корпуса только 0,002–0,005 дюйма и глубокие корпуса до 0,350 дюйма были определены и легко достигаются.
Закалочный пресс, расположенный на предприятии, позволяет контролировать размеры, что обеспечивает точную закалку шестерен и подшипников диаметром до 16 дюймов.
Услуги
Газовая науглероживание / карбонитрирование (1500 ° — 1850 ° F)
Максимальные размеры нагрузки
|
|
наверх
науглероживание — Найдите производителей и дистрибьюторов в онлайн-справочнике покупателя Gear Technology
ECM USA
Компания ECM Technologies начала производство печей для термообработки в 1928 году.С того времени персонал ECM всегда был полностью привержен расширению своих знаний в области контроля температуры, высокого давления, вакуума и поведения материалов. Этот опыт в промышленном масштабе всегда обогащался нашим тесным партнерством с пользователями печей, инженерами, инженерами по термообработке и разработчиками. Сегодня наша база знаний лежит в основе производственных линий всех наших клиентов. Именно эта забота о внимании и внимании, в сочетании с нашей страстью к своей профессии, сформировала ECM Technology и признанный дух инноваций в ECM USA.Подробнее Или посетите www.ecm-usa.com
Gleason Corporation
Миссия Gleason Corporation — предоставить Total Gear Solutions своей глобальной клиентской базе. Gleason — мировой лидер в разработке, производстве и продаже оборудования для производства зубчатых колес и сопутствующего оборудования. Продукция компании используется клиентами в автомобильной, грузовой, авиационной, сельскохозяйственной, горнодобывающей, энергетической, строительной, электроинструментальной и морской отраслях, а также широким кругом клиентов, обслуживающих различные рынки промышленного оборудования.Gleason имеет производственные предприятия в Рочестере, штат Нью-Йорк; Рокфорд, штат Иллинойс; Дейтон, Огайо; Мюнхен и Людвигсбург, Германия; Студен, Швейцария; Бангалор; Индии и Сучжоу, Китай, и имеет офисы продаж и обслуживания в Северной и Южной Америке, Европе и Азиатско-Тихоокеанском регионе. Подробнее Или посетите www.gleason.com
Solar Atmospheres
Solar Atmospheres специализируется на вакуумной термообработке, вакуумном азотировании, вакуумной пайке, а также услугах по науглероживанию в вакууме.Обладая опытом обработки и индивидуальным обслуживанием, компания Solar эффективно обработает ваши мелкие и крупные детали с помощью нашего уникального ассортимента, включающего более 60 вакуумных печей. Размеры варьируются от лабораторных печей до самой большой в мире коммерческой вакуумной печи. Подробнее Или посетите www.solaratm.com
науглероживание — WordReference Dicţionar englez-român
- Изменение ‘ науглероживание ‘ (v): (⇒ сопряженное)
- науглероживание
- v 3-е лицо в единственном числе (США и Великобритания)
- науглероживание
- ver. настоящее причастие : глагол -ing используется описательно или для образования прогрессивного глагола — например, « поет, птица», «Это поет, .«(США и Великобритания)
- науглероженный
- v прошедший глагол , прошедшее простое : прошедшее время — например,« Он видел человека ».« Она засмеялась »(США и UK)
- науглероженный
- v прошедшее p глагол, причастие прошедшего времени : форма глагола, используемая описательно или для образования глаголов — например, « заперта дверь », «дверь была заперта . «(США и Великобритания)
WordReference Англо-румынский словарь © 2020:
Traduceri Principale | ||
carburize [sth], также UK: carburise [sth] ⇒ vtr переходный глагол : объект, принимающий глагол, принимающий переходный элемент. — например, « Скажи что-нибудь .«Она нашла кошку.» | (металл: обработать углеродом) ( aliaje ) | a carbura vb.tranz. глагол tranzitiv : Verb a cărui acțiune se răsfrâi unctrange direct asuprange construindu-se cu ajutorul complementului direct: a deschide geamul ( geamul fiind complementul direct). Pentru a verifica dacă un глагол este sau nu tranzitiv, i se pune întrebarea pe cine? . pe cine? , . ? Ce citesc? Pe cine întreb? |
a trata cu carbon expr. expresie : Grup de mai multe cuvinte care nu sunt suficient sudate cât să formeze o locuțiune, exprimând in mod concis o idee: a se lua cu mâinile de păr , Nu mai spune! . |
Română:
определение науглероживания и синонимы науглероживания (английский)
Современная компьютеризированная печь газового науглероживания
науглероживание [1] или науглероживание (в основном британский английский) — это процесс термообработки, при котором железо или сталь поглощают углерод, выделяющийся при нагревании металла в присутствии углеродсодержащего материала, такого как древесный уголь или углерод. монооксид, чтобы сделать металл тверже.В зависимости от времени и температуры пораженный участок может варьироваться по содержанию углерода. Более длительное время науглероживания и более высокие температуры приводят к большей диффузии углерода в деталь, а также к увеличению глубины диффузии углерода. Когда чугун или сталь быстро охлаждают закалкой, более высокое содержание углерода на внешней поверхности становится твердым в результате превращения аустенита в мартенсит, в то время как сердцевина остается мягкой и жесткой, как ферритная и / или перлитная микроструктура. [2]
Этот производственный процесс можно охарактеризовать следующими ключевыми моментами: он применяется к заготовкам с низким содержанием углерода; детали контактируют с высокоуглеродистым газом, жидкостью или твердым телом; образует твердую поверхность детали; сердечники заготовок в значительной степени сохраняют свою вязкость и пластичность; и обеспечивает глубину твердости корпуса до 0.25 дюймов (6,4 мм).
Метод
Науглероживание стали включает термическую обработку металлической поверхности с использованием источника углерода. [3] Науглероживание можно использовать для увеличения твердости поверхности низкоуглеродистой стали. [4]
На ранних этапах науглероживания использовалось прямое нанесение древесного угля на металл (первоначально называемое цементацией), но современные методы применяют углеродсодержащие газы или плазму (например, диоксид углерода или метан).Процесс зависит в первую очередь от состава окружающего газа и температуры печи, которые необходимо тщательно контролировать, поскольку тепло также может повлиять на микроструктуру остального материала. Для применений, в которых желателен большой контроль над составом газа, науглероживание может происходить при очень низких давлениях в вакуумной камере.
Плазменное науглероживание все чаще используется в основных промышленных режимах для улучшения характеристик поверхности (таких как износостойкость и коррозионная стойкость, твердость и несущая способность, в дополнение к параметрам, зависящим от качества) различных металлов, особенно нержавеющих сталей.Этот процесс используется как экологически чистый (по сравнению с газовым или твердым науглероживанием). Он также обеспечивает равномерную обработку компонентов со сложной геометрией (плазма может проникать в отверстия и узкие зазоры), что делает его очень гибким с точки зрения обработки компонентов.
Процесс науглероживания заключается в имплантации атомов углерода в поверхностные слои металла. Поскольку металлы состоят из атомов, прочно связанных в металлическую кристаллическую решетку, имплантированные атомы углерода проникают в кристаллическую структуру металла и либо остаются в растворе (растворяются в кристаллической матрице металла — это обычно происходит при более низких температурах), либо реагируют с основным металлом с образованием керамических карбидов (обычно при более высоких температурах из-за более высокой подвижности атомов основного металла).Оба этих механизма упрочняют поверхность металла, первый — за счет деформации решетки из-за того, что атомы оказываются зажатыми между атомами основного металла, а второй — за счет образования очень твердых частиц, стойких к истиранию. Однако каждый разный механизм упрочнения приводит к разным решениям исходной проблемы: первый механизм, известный как упрочнение твердым раствором, улучшает устойчивость основного металла к коррозии, одновременно увеличивая его твердость; последнее, известное как дисперсионное упрочнение, значительно улучшает твердость, но, как правило, в ущерб коррозионной стойкости основного металла.Инженеры, использующие плазменную науглероживание, должны решить, какой из двух механизмов соответствует их потребностям.
Науглероживание газом обычно проводят при температуре от 900 до 950 ° C.
При кислородно-ацетиленовой сварке пламя науглероживания — это пламя с низким содержанием кислорода, которое дает сажистое пламя с более низкой температурой. Его часто используют для отжига металла, что делает его более пластичным и гибким в процессе сварки.
Основная цель при производстве обугленных деталей — обеспечить максимальный контакт между поверхностью детали и элементами, богатыми углеродом.При науглероживании газом и жидкостью детали часто поддерживаются в сетчатых корзинах или подвешиваются на проволоке. При науглероживании в упаковке заготовка и уголь помещаются в контейнер, чтобы гарантировать, что контакт сохраняется на максимально возможной площади поверхности. Пакет науглероживание контейнеры, как правило, изготовлены из углеродистой стали, покрытая алюминием или Жаростойкие никель-хромовый сплав и запечатаны на все отверстия с огнеупорной глиной.
Отвердители
Существуют различные типы элементов или материалов, которые могут использоваться для выполнения этого процесса, но в основном они состоят из материала с высоким содержанием углерода.Некоторые типичные отвердители включают газообразный оксид углерода (CO), цианид натрия и хлорид бария или древесный уголь из твердых пород древесины. При науглероживании газа CO выделяется пропаном или природным газом. При жидкой науглероживании CO образуется из расплавленной соли, состоящей в основном из цианида натрия (NaCN) и хлорида бария (BaCl 2 ). При науглероживании в пакетах окись углерода выделяется коксом или древесным углем твердых пород.
Геометрические возможности
Существует множество видов деталей, которые можно обугливать, что означает практически безграничные возможности для формы материалов, которые можно обугливать.Однако следует внимательно относиться к материалам, которые содержат неоднородные или несимметричные участки. Различные поперечные сечения могут иметь разную скорость охлаждения, что может вызвать чрезмерные напряжения в материале и привести к поломке. [5]
Изменение размеров
Науглероживание детали практически невозможно без каких-либо изменений размеров. Количество этих изменений зависит от типа используемого материала, процесса науглероживания, которому подвергается материал, а также от исходного размера и формы заготовки.Однако изменения невелики по сравнению с операциями термической обработки. [5]
Свойства рабочего материала | Эффекты науглероживания |
---|---|
Механический |
|
Физический |
|
Химическая промышленность |
|
Материал заготовки
Обычно карбонизируемые материалы представляют собой низкоуглеродистые и легированные стали с начальным содержанием углерода от 0.От 2 до 0,3%. На поверхности заготовки не должно быть загрязнений, таких как оксиды масла, щелочные растворы, которые предотвращают или препятствуют диффузии углерода в поверхность заготовки. [5]
Сравнение различных методов
В целом, пакетное науглероживание может работать с более крупными деталями, чем оборудование для науглероживания жидкостью или газом, но методы науглероживания жидким или газовым газом быстрее и подходят для механизированной обработки материалов. Также преимущества науглероживания перед нитроцементацией заключаются в большей глубине гильзы (глубина гильзы больше 0.3 дюйма), меньше искажений и лучше ударопрочность. Это делает его идеальным для применения в высокопрочных и износостойких материалах (например, ножницы или мечи). К недостаткам можно отнести дополнительные расходы, более высокие рабочие температуры и увеличенное время. [5]
Выбор оборудования
Обычно науглероживание газом используется для больших деталей.