Круг сталь 40ХН: термообработка
При изготовления различных модификаций валов, муфт, шпинделей, осей, штоков, болтов и рычагов применяют сталь 40ХН. Данный вид металла отлично работает в критических условиях, выдерживая сильные вибрационные и динамические нагрузки. Из него даже делают валы, которые устанавливаются на крупносортные и рельсо-балочные станы, необходимые при горячей обработке металлов. Круг сталь 40ХН используется в создании ответственных элементов механизмов, где требуется высокий уровень прочности и хорошая вязкость.
Свойства 40ХН
В этой стали концентрация углерода достигает 0.39-0.41%, что обеспечивает ее высокие показатели прочности после соответствующей термообработки и формирования карбидных структур. Легирующими элементами в данном сплаве железа выступает хром (0.45-0.75%) и никель (1-1.4%).
Эта легированная хромникелевая сталь демонстрирует отличные антикоррозионные свойства. Наличие хрома обеспечивает прекрасную сопротивляемость коррозионным процессам. Такой металл отличается высокой механической прочностью и значительным пределом упругости.
После термообработки сталь получает повышенный уровень твердости 310-350 НВ, отличную предельную прочность на разрыв, достигающую 780Н/кв.мм, а также прекрасную ударную вязкость до 60 Дж/кв.см. При этом показатели предела текучести в ненагруженном состоянии остаются в районе 630-640 Н/кв.мм.
Методы термообработки 40ХН
Для увеличения прочностных характеристик металла его подвергают разным видам термической обработки. Круги из такой стали диаметром до 25 мм закаливают при нагревании до 850-870°С, с последующим охлаждением в ванну с маслом. Для закалки крупногабаритных деталей из этого металла их вначале охлаждают водой. Потом раскаленные изделия опускают в масло, либо подвергают немедленному низкому отпуску, при доведении температуры до 500-540°С. В качестве альтернативы закаливания могут использоваться нагрев поверхностей деталей с помощью токов высокой частоты и последующий отпуск. Подобный вариант термообработки обеспечивает формирование особо твердых (53-56 RC) поверхностных слоев металла.
Сталь 40ХН очень трудно сваривается, поскольку в околошовной зоне формируется область с хрупкой структурой. Чтобы предотвратить такие негативные процессы, используются специализированные технологии сварки, с предварительным разогревом соединяемых деталей. После проведения сварочных работ изделия подвергают отжигу или отпуску.
Оптимальные эксплуатационные параметры изделий, изготовленных из данной марки металла, являются детали и элементы конструкций, толщиной не больше 120 мм.
Термообработка, отжиг и термическая обработка стали в СПб
Три основные вида термической обработки стали:
- отжиг;
- закалка;
- отпуск.
Первичной операцией по термической обработке стали является отжиг. Во время этой процедуры материал нагревается до определенной температуры, выдерживается некоторое время, а затем медленно охлаждается вместе с нагревательной печью. Цель и выполнение операции отжига стали могут быть различными. Обычно его применяют для снятия внутреннего напряжения, улучшения механических свойств, облегчения обрабатываемости различными режущими инструментами, уменьшения твердости и подготовки к последующим видам термической обработки стали. В зависимости от применяемой температуры для термического нагрева и назначения разделяют несколько процессов отжига стали:
- полный;
- неполный;
- диффузионный;
- изотермический;
- на зернистый перлит.
Полный отжиг стали проводится после горячей механической обработки и литья легированных и углеродистых сплавов. Его основной целью является измельчение зерна металла и смягчения для улучшения дальнейшей механической обработки режущим инструментом, а также для ликвидации внутреннего напряжения. Неполный отжиг применяют при удовлетворительных свойствах сплава для снижения повышенной твердости и снятия внутреннего напряжения. Получаемая сталь становится пригодной для механической обработки и не имеет внутреннего напряжения.
Термообработка стали 40х проводится методом отжига на зернистый перлит. Такая группа высокоуглеродистых сталей со структурой пластинчатого перлита обладают плохой обрабатываемостью режущими инструментами. Этот вид термической обработки позволяет изменить структуру кристаллической решетки, преобразовав перлит в зернистый. Для этого применяют циклический или маятниковый термический нагрев, чередуя его с охлаждением. Изотермический отжиг применяют для марок материала с высоким содержанием хрома, при этом происходит полное преобразование аустенита в однородную структуру. Диффузионный отжиг проводится для уменьшения или полного устранения химической неоднородности стали, получаемой при кристаллизации слитков.
Компания Феррополис проводит любой вид термической обработки стали на современном оборудовании со строжайшим соблюдением всех моментов технологического процесса. Наши высокопрофессиональные работники придадут готовой продукции любые нужные свойства, позволяющие получаемым деталям значительно повысить свои физические и эксплуатационные характеристики.
Сталь Твердость после термообработки — Энциклопедия по машиностроению XXL
Деталь Марка стали Твердость после термообработки [c.601]Твердость после термообработки в любом месте поверхности НВ 105—149 для стали 20 и НВ 134—187 для стали 25. [c.327]
Примечания 1. Цепи следует изготовлять из круглой горячекатаной стали по ГОСТу 2590 . 57 . 2. Цепи после сварки необходимо калибровать и подвергать термообработке (закалка и отпуск). Твердость после термообработки должна быть для цепей I категории прочности ЙВ 311—363, II категории прочности НВ 269—321.
Предварительная термообработка углеродистых инструментальных сталей — отжиг на зернистый перлит, окончательная — закалка в воде или растворе соли и низкий отпуск. После этого структура стали представляет собой мартенсит с включениями зернистого цементита.
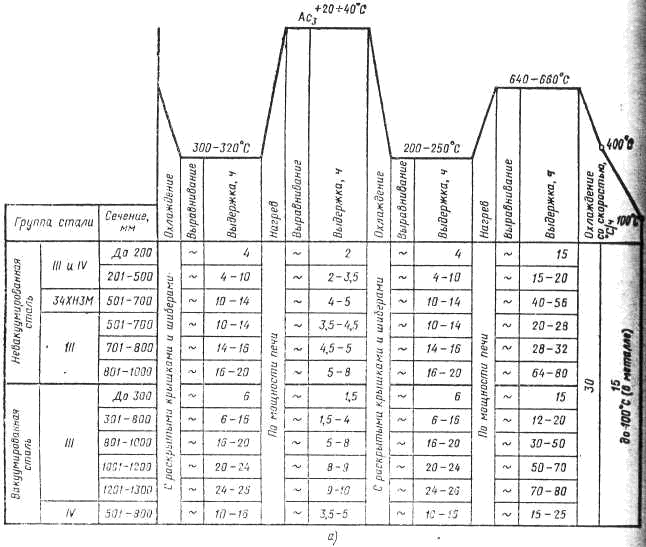
Термообработка низколегированных инструментальных сталей — закалка в масле и отпуск при температуре 150-200 °С. При этом обычно достигается сквозная про-каливаемость. Твердость после термообработки составляет HR 62-64. [c.189]
Для измерительного инструмента применяют высокоуглеродистые стали У8-У12 и низколегированные стали марок X, ХГС, ХВГ, 9ХС, содержащие около 1 % С и до 1,5 % Сг. Их твердость после термообработки должна быть не менее НКСэ 60-64. [c.408]
Для втулок диаметром до 40 мм применяют сталь марки 40Х (ГОСТ 4543—61), свыше 40 ЖЛ4 —сталь У7А (ГОСТ 1435—54). Твердость после термообработки для втулок Диаметром до 40 мм HR 35… 40, свыше 40 мм HR 33… 36.
Стали средней твердости (после термообработки) Стали высокой твердости (после термообработки) [c.508]
К числу недостатков вибрационных ножниц следует отнести то, что ножи быстро изнашиваются, а на вырезанных заготовках появляются заусенцы и зарубы, требующие иногда даже дополнительной обработки на фрезерных станках, что ограничивает их применение только в условиях мелкосерийного производства. Ножи этих ножниц изготовляются из стали тех же марок как и для гильотинных ножниц при твердости после термообработки HR 58—60.
Материалом корпуса сборных фрез является обычно сталь марок 40Х, 45, 50Х. Твердость корпуса находится в пределах HR 35—55. Корпуса державок изготовляются из сталей марок У8, 45, 40Х или 9ХС и имеют твердость после термообработки HR 45—55. Иногда державки изготовляют методом порошковой металлургии из композиций железо—медь—никель—углерод. Твердость корпусов при этом не меньше НВ 90. [c.182]
Примечания. 1. Материал —сталь 15 или 20, ГОСТ 1050 — 52 заменитель — Ст. 3, ГОСТ 380 — 50 (с обеспечением твердости не ниже принятой настоящей нормалью . 2. Твердость после термообработки = 50- -5 . Глубина цементации 0,10- -0,15 жж для винтов диаметром 3 и 4 мм, 0,10 0,20 для винтов диаметром 5 мм. 3. Указанные диаметры отверстий являются рекомендуемыми и в зависимости от твердости материала и других факторов могут быть изменены.
Палец поводковый — сталь 40Х после термообработки твердость = 35 -I- 40, [c.60]
Инструментальные углеродистые стали в настоящее время имеют ограниченное применение вследствие низкой красностойкости. Инструменты из этой стали хотя и имеют твердость после термообработки Я/ С 60—63, но при нагреве до 200—250°С твердость резко падает и инструмент тупится.
Быстрорежущие стали — это хромовольфрамовые стали с содержанием вольфрама от 8,5 до 19% и от3,8 до4,4% хрома. Реж щий инструмент из быстрорежущих сталей имеет после термообработки твердость HR 62—65, повышенную сопротивляемость износу и сохраняет режущие свойства при нагреве до 600—650 С. Это позволяет работать инструментом, изготовленным из быстрорежущей стали со скоростями, в 2—4 раза большими, чем инструментами, изготовленными из инструментальной углеродистой стали.
Марки стали I я bi О о иЗ- Л S Sgl Е- U и Нор- мали- за- ция, °С Цементация, [c.209]
Детали опоры тележки должны иметь высокую износостойкость. Опорная плита 1, изготовленная из марганцовистой стали 50Г, после термообработки имеет твердость НЯС 45—50. К стакану 5 и направляющей кронштейна приварены сменные втулки, заменяемые при износе. [c.194]
Класс Разряд Вид Сила пружины при максимальной деформации F. Н . Диаметр d, мм Марка стали Твердость после термообработки, HR гост BЫHOI ЛИ- вость в циклах, не менее ГОСТ на параметры вит. ков пружин
Класс раз- ряд Вид пружины при максимальной деформации, Р Н(кго) Диаметр d, мм Марка стали Твердость после термообработки НДСз ГОСТ Наибольшее касательное напряжение при кручении Тз, МПа (кгс/им ) Упроче- ние ГОСТ на параметры витков пружин [c.210]
Наименование пнструмеитов Сталь Твердость после термообработки Нк
[c. 245]
Стали для измерительных инструментов. Измерительные инструменты (плитки, калибры, шаблоны) должны сохранять свою форму и размеры в течение продолжительного времени. В них не должны совершаться самопроизвольные структурные превращения, вызывающие изменение размеров инструмента в процессе эксплуатации Коэффициент. тнейного расширения должен быть минимальным. Этими свойствами обладают стали с мартенситной структурой. Для изготовления измерительных инструментов используют стали марок X, Х9, ХГ, Х12Ф1. Закалка проводится при температурах 850.. 870 °С в масле. Для устранения остаточного аустенита после закалки проводится обработка холодом при минус 70 °С, а затем низкий отпуск при 120 140 с. Твердость после термообработки составляет 63.. 64 ИКС,
Пуансоны изготавливаются из стали Х12Ф1 или Х6ВФ. Балл карбидной неоднородности порядка 2—4 термообработка— закалка с отпуском. Твердость после термообработки 57—60 HR . Заготовку под выдавливание шлицев следует выполнять в виде обратного конуса с учетом перераспределения металла в процессе выдавливания.
Материал пуансонов — сталь Х12Ф1. Балл карбидной неоднородности поковки роликов 2—4 термообработка — закалка с отпуском. Твердость после термообработки 57—60 HR . Приспособление для выдавливания впадин устанавливается на гидравлический пресс усилием 250 т. Машинное время — 0,5 мин. В процессе выдавливания впадин происходит удлинение вала на 0,2—0,3 мм. Глубина впадин зависит от величины хода ползуна. Движение ползуна пресса с закрепленной на нем обоймой ограничивается жестким упором. [c.164]
Корпус патрона при окружных скоростях обода патрона до 35 Mj eK — чугун СЧ 15-32, а при скоростях больше 35 м сгк — модифицированный чугун или сталь. Палец поводковый — сталь 40Х после термообработки твердость UR 35 — 40. [c.349]
Режущие элементы спиральных сверл изготовляются ид стали PI8 с твердостью после термообработки H.R б1- -65 при карбидной неоднородности не выше 3-го балла по ГОСТ 5952—51. Толщина сердцевины сверла должна быть (0,3—0,4) d, угол наклона спирали 31 — 35″, обратная конусность 0,1—0,15 мм на 100 мм длины сверление производится е охлаждением 10 «/г)-ной эмульсией кр1 терием затупления (бз) ирпнят износ по задней поверхности на периферии.
[c.252]
Более высокие свойства имеет карбидосталь на основе Р6М5 с 45 % (объемн.) карбидов (из которых 29 % Ti ) а зг 2000 — 2500 МПа ударная вязкость 80—120 кДж/м красностойкость 660—670 °С твердость после термообработки 68—70 HR . По сравнению с режущими инструментами из стали 10Р6М5К5МП износостойкость инструмента из зтой карбидостали возрастает в 4 раза [169]. [c.123]
Крестовина, палец, втулка. Материал — сталь 40Х по ГОСТ 4543—71. Допускается изготовление из других материалов с механическими свойствами не ниже, чем у стали 40Х после термообработки. Твердость 49. .. 53 HR j. [c.

Цилиндрическое фрезерование органического стекла концевыми фрезами необходимо проводить при скоростях резания 10—30 м мин (при работе без охлаждения), подачах 0,1—0,4 жж/зуб и глубине резания 0,5—3 мм. Геометрия фрез следующая ш = 50—60°, ат = 18—20°, a,v = 19—25 и Jn = 2—5°. Материал фрез — быстрорежущие стали Р9 или Р18 с твердостью после термообработки 58—62 HR . Фрезерование необходимо вести при подаче фрезы против ее вращения. Для черновой и, где это можно, чистовой обработок элементов нриаденялись фрезы стандартных длин. Для чистовой обработки глубоких выемок с целью получения малых радиусов стыков R = 5—7 мм) вертикальных элементов модели применялись специально изготовленные фрезы с указанной выше геометрией режущей части, получаемые или приваркой к стандартной фрезе удлинительного хвостовика, или переточкой стандартных сверл большой длины с последующей их шлифовкой на круглошлифовальном станке. [c.65]
Поршни изготовляют из шарикоподшипниковой стали ШХ15 с твердостью после термообработки HR 58—62 и пригоняют к отверстиям в роторе с зазором 0,015—0,025 мм. Для изготовления поршней применяют также стали 40Х и 20Х с твердостью после термообработки HR 58—62.
[c.151]
Цапфы обычно изготовляют из сталей 40Х, 18ХНВА с твердостью после термообработки HR 60—64. [c.151]
Материалы. Для основных деталей муфты применяют сталь ШХ15 — для роликов и стали 20Х и 40Х —для звездочек и обойм. Сталь ШХ15, как известно, отличается высокой износоустойчивостью. Твердость после термообработки R = 59ч-63. [c.237]
Основными техническими требованиями, предъявляемыми к элементам комплекта УСП, являются их износоустойчивость, точность размеров и высокий класс чистоты (шероховатости) рабочих поверхностей. Хорошо изготовленные элементы УСП могут находиться в работе 15—20 лет, поэтому элементы приспособлений изготовляют из легированных и высокоуглеродистых инструментальных сталей и проходят термическую обработку. Базовые и опорные детали изготовляют из хромоникелевой стали марки 12ХНЗА с твердостью после термообработки HR 60—64. Ответственные крепежные детали изготовляют из хромистой стали марки 38ХА.
[c.10]
Сборные червячные фрезы с поворотными вставными рейками (рис. 23) широко применяют в автомобильной промышленности. Фрезы имеют большую длину рейки /(120 — 200 мм), ширину режущей части рейки до 27 мм, диаметр до 150 мм, число заходов 1 -3 и число реек 11-15, реже 17 их обычно применяют для пяти — семизаходных фрез. Диаметр отверстий для фрез 32 и 40 мм. Рейки 1 сборной фрезы запрессовывают в прямоугольные пазы рабочего корпуса 3 с подогревом корпуса или сажают на клей. Такая посадка гарантирует высокую жесткость против осевого смещения. Дополнительно рейки удерживаются закрепленными с обоих торцов крышками 2. Вставные рейки сборных фрез обеспечивают экономию быстрорежущей стали, более однородную структуру и твердость после термообработки, а также меньшие остаточные напряжения. [c.280]
Коэффициент удельной прочности цепи /Сц, приведенный в табл. 2, определяется делением разрывной нагрузки на массу I. м цепи. Детали цепи изготовляют из стали марок 40Х, 40ХФА, 50Г2, 40Г2, 50 и 45 и подвергают термической обработке (закалке и отпуску). Твердость после термообработки должна быть по ГОСТ 589—64 — для внутренних и наружных звеньев HR = 27 -н 32, для валиков HR = 32 ч- 38.
[c.26]
Материалы для пуансоиов и матриц. Для изготовления пуансонов и матриц применяют стали и другие материалы, приведенные в табл. 94. Твердость после термообработки, указанную в таблице, следует выдерживать [c.184]
Основными легирующими элементами быстрорежущих сталей, обеспечивающими их теплостойкость, являются в первую очередь вольфрам и его химический аналог — молибден. Сильно повышает теплостойкость (до 645 — 650Х) и твердость после термообработки (HR 67 — 7,0) кобальт и в меньшей степени ванадий. [c.311]
Cталь 40Х механические, физические, технологические свойства, химический состав. Сталь 40Х круг, сталь 40Х шестигранник, сталь 40Х лист
Справочная информация
Характеристика материала сталь 40ХМарка стали | сталь 40Х |
Заменитель стали | сталь 45Х, сталь 38ХА, сталь 40ХН, |
Классификация стали | Сталь конструкционная легированная ГОСТ 4543-71 |
В Компании ГП «Стальмаш» Вы можете купить сталь 40Х в следующих видах металлопроката: круг ст 40Х ГОСТ 2590-2006 (ГОСТ 2590-88) круг (пруток) стальной горячекатаный круг ст 40Х ГОСТ 7417-75 круг (пруток) калиброванный шестигранник ст 40Х ГОСТ 2879-2006 (ГОСТ 2879-88) шестигранник горячекатаный шестигранник ст 40Х ГОСТ 8560-78 шестигранник калиброванный лист ст 40Х ГОСТ 19903-74 прокат листовой горячекатаный | |
Применение стали 40Х | оси, валы, вал-шестерни, плунжеры, штоки, коленчатые и кулачковые валы, кольца, шпиндели, оправки, рейки, губчатые венцы, болты, полуоси, втулки и другие улучшаемые детали повышенной прочности. |
Химический состав в % материала сталь 40Х
C | Si | Mn | Ni | S | P | Cr | Cu |
0.36 — 0.44 | 0.17 — 0.37 | 0.5 — 0.8 | до 0.3 | до 0.035 | до 0.035 | 0.8 — 1.1 | до 0.3 |
Температура критических точек материала сталь 40Х
Ac1 = 743 , Ac3(Acm) = 782 , Ar3(Arcm) = 730 , Ar1 = 693 |
Механические свойства при Т=20oС материала сталь 40Х
Сортамент | Размер | Напр. | sв | sT | d5 | y | KCU | Термообр. |
— | мм | — | МПа | МПа | % | % | кДж / м2 | — |
Диск | Танг. | 570 | 320 | 17 | 35 | 400 | ||
Пруток | Ж 28 — 55 | Прод. | 940 | 800 | 13 | 55 | 850 | |
Пруток | Ж 25 | 980 | 785 | 10 | 45 | 590 | Закалка 860oC, масло, Отпуск 500oC, вода, |
Твердость материала сталь 40Х после отжига , | HB 10 -1 = 217 МПа |
Физические свойства материала сталь 40Х
T | E 10— 5 | a 10 6 | l | r | C | R 10 9 |
Град | МПа | 1/Град | Вт/(м·град) | кг/м3 | Дж/(кг·град) | Ом·м |
20 | 2.14 | 7820 | 210 | |||
100 | 2.11 | 11.9 | 46 | 7800 | 466 | 285 |
200 | 2.06 | 12.5 | 42.7 | 7770 | 508 | 346 |
300 | 2.03 | 13.2 | 42.3 | 7740 | 529 | 425 |
400 | 1.85 | 13.8 | 38.5 | 7700 | 563 | 528 |
500 | 1.76 | 14.1 | 35.6 | 7670 | 592 | 642 |
600 | 1.64 | 14.4 | 31.9 | 7630 | 622 | 780 |
700 | 1.43 | 14.6 | 28.8 | 7590 | 634 | 936 |
800 | 1.32 | 26 | 7610 | 664 | 1100 | |
900 | 26.7 | 7560 | 1140 | |||
1000 | 28 | 7510 | 1170 | |||
1100 | 28.8 | 7470 | 120 | |||
1200 | 7430 | 1230 | ||||
T | E 10— 5 | a 10 6 | l | r | C | R 10 9 |
Технологические свойства материала сталь 40Х
Свариваемость: | трудносвариваемая. |
Флокеночувствительность: | чувствительна. |
Склонность к отпускной хрупкости: | склонна. |
Зарубежные аналоги материала сталь 40ХВнимание! Указаны как точные, так и ближайшие аналоги.
США | Германия | Япония | Франция | Англия | Евросоюз | Италия | Бельгия | Испания | Китай | Швеция | Болгария | Венгрия | Польша | Румыния | Чехия | Австралия | Юж.Корея | |||||||||||||||||||||||||||||||||||||||||||||||||||||||||||||||||||
— | DIN,WNr | JIS | AFNOR | BS | EN | UNI | NBN | UNE | GB | SS | BDS | MSZ | PN | STAS | CSN | AS | KS | |||||||||||||||||||||||||||||||||||||||||||||||||||||||||||||||||||
|
|
|
|
|
|
|
|
|
|
Обозначения:
Механические свойства : | |
sв | — Предел кратковременной прочности , [МПа] |
sT | — Предел пропорциональности (предел текучести для остаточной деформации), [МПа] |
d5 | — Относительное удлинение при разрыве , [ % ] |
y | — Относительное сужение , [ % ] |
KCU | — Ударная вязкость , [ кДж / м2] |
HB | — Твердость по Бринеллю , [МПа] |
Физические свойства : | |
T | — Температура, при которой получены данные свойства , [Град] |
E | — Модуль упругости первого рода , [МПа] |
a | — Коэффициент температурного (линейного) расширения (диапазон 20o — T ) , [1/Град] |
l | — Коэффициент теплопроводности (теплоемкость материала) , [Вт/(м·град)] |
r | — Плотность материала , [кг/м3] |
C | — Удельная теплоемкость материала (диапазон 20o — T ), [Дж/(кг·град)] |
R | — Удельное электросопротивление, [Ом·м] |
Свариваемость : | |
без ограничений | — сварка производится без подогрева и без последующей термообработки |
ограниченно свариваемая | — сварка возможна при подогреве до 100-120 град. и последующей термообработке |
трудносвариваемая | — для получения качественных сварных соединений требуются дополнительные операции: подогрев до 200-300 град. при сварке, термообработка после сварки — отжиг |
Марочник стали и сплавов
Марки стали | Заменитель | Свариваемость |
---|---|---|
ГОСТ 380-94 | ||
Ст0 | Сваривается без ограничений | |
Ст2кп | Ст2сп | Сваривается без ограничений. Для толщины более 36 мм рекомендуется подогрев и последующая термообработка |
Ст2пс | Ст2пс | |
Ст2сп | ||
Ст3кп | Ст3пс | Сваривается без ограничений. Для толщины более 36 мм рекомендуется подогрев и последующая термообработка |
Ст3пс | Ст3сп | Сваривается без ограничений. Для толщины более 36 мм рекомендуется подогрев и последующая термообработка |
Ст3сп | Ст3пс | |
Ст3Гпс | Ст3пс | Сваривается без ограничений. Для толщины более 36 мм рекомендуется подогрев и последующая термообработка |
Сталь 18Гпс | ||
Ст4кп | ||
Ст4пс | Ст4сп | Сваривается ограниченно |
Ст5пс | Ст6сп | Сваривается ограниченно. Рекомендуется подогрев и последующая термообработка |
Ст5сп | Ст4сп | |
Ст6пс | Сваривается ограниченно. Рекомендуется подогрев и последующая термообработка | |
Ст6сп | Ст5сп | Сваривается ограниченно. Рекомендуется подогрев и последующая термообработка |
ГОСТ 801-78 | ||
ШХ15 | Стали: ШХ9, ШХ12, ШХ15СГ | Способ сварки КТС |
ШХ15СГ | Стали: ХВГ, ШХ15, 9ХС, ХВСГ | Способ сварки КТС |
ШХ4 | Способ сварки КТС | |
ГОСТ 1050-88 | ||
8 | Сталь 10 | Сваривается без ограничений, кроме деталей после химико-термической обработки |
08кп | Сталь 08 | Сваривается без ограничений, кроме деталей после химико-термической обработки |
08пс | ||
10 | Стали: 08, 15, 08кп | Сваривается без ограничений, кроме деталей после химико-термической обработки |
10кп | Стали: 08кп, 15кп, 10 | Сваривается без ограничений, кроме деталей после химико-термической обработки |
10пс | ||
15 | Стали: 10, 20 | Сваривается без ограничений, кроме деталей после химико-термической обработки |
15кп | Стали: 10кп, 20кп | Сваривается без ограничений |
15пс | ||
18кп | Сваривается без ограничений | |
20 | Сталь: 15, 20 | Сваривается без ограничений, кроме деталей после химико-термической обработки |
20кп | Сталь: 15кп | Сваривается без ограничений, кроме деталей после химико-термической обработки |
20пс | ||
25 | Сталь: 20, 30 | Сваривается без ограничений, кроме деталей после химико-термической обработки |
30 | Стали: 25, 35 | Сваривается ограниченно. Рекомендуется подогрев и последующая термообработка |
35 | Стали: 30, 40, 35Г | Сваривается ограниченно. Рекомендуется подогрев и последующая термообработка |
40 | Стали: 35, 45, 40Г | Сваривается ограниченно. Рекомендуется подогрев и последующая термообработка |
45 | Стали: 40Х, 50, 50Г2 | Трудно — свариваемая. Необходим подогрев и последующая термообработка |
50 | Стали: 45, 50Г, 50Г2, 55 | Трудно — свариваемая. Необходим подогрев и последующая термообработка |
55 | Стали: 50, 60, 50Г | Не применяется для сварных конструкций |
58 (55пп) | Стали: 30ХГТ, 20ХГНТР, 20ХН2М, 12ХНЗА, 18ХГТ | Не применяется для сварных конструкций |
ГОСТ 1414-75 | ||
А20 | Сталь А12 | Не применяется для сварных конструкций |
А30 | Сталь: А40Г | Не применяется для сварных конструкций |
А40Г | ||
ГОСТ 1435-90 | ||
У7, У7А | Сталь: У8 | Не применяется для сварных конструкций |
У8, У8А | Сталь: У7, У7А У10, У10А | Не применяется для сварных конструкций |
У9, У9А | Стали: У7, У7А, У8, У8А | Не применяется для сварных конструкций |
У10, У10А | Стали: У10, У10А | Не применяется для сварных конструкций |
ГОСТ 4543-71 | ||
15Х | Сталь: 20Х | Сваривается без ограничений, кроме деталей после химико-термической обработки |
20Х | Сталь: 15Х, 20ХН, 18ХГТ | Сваривается без ограничений, кроме деталей после химико-термической обработки |
30Х | Сталь: 35Х | Ограниченно сваривается |
35Х | Сталь: 40Х | Ограниченно сваривается |
38ХА | Сталь: 40Х, 35Х | Трудно-свариваемая |
40Х | Сталь: 45Х, 35ХА, 40ХС | Трудно-свариваемая, необходим подогрев и последующая термообработка |
45Х | Сталь: 40Х, 45Х, 50ХН | Трудно-свариваемая, необходим подогрев и последующая термообработка |
50Х | Сталь: 40Х, 45Х, 50ХН | Трудно-свариваемая, необходим подогрев и последующая термообработка |
15Г, 20Г | Сталь: 20Г, 20, 30Г | Хорошо свариваемая |
30Г | Сталь: 35, 40Г | Ограниченно свариваемая. Рекомендуется подогрев и последующая термообработка |
35Г | Ограниченно свариваемая. Рекомендуется подогрев и последующая термообработка | |
40Г | Стали: 45, 40Х | Ограниченно свариваемая. Рекомендуется подогрев и последующая термообработка |
45Г | Стали: 40Г, 50Г | Трудно-свариваемая. Рекомендуется подогрев и последующая термообработка. |
50Г | Стали: 40Г, 50 | Трудно-свариваемая. Рекомендуется подогрев и последующая термообработка. |
10Г2 | Сталь: 09Г2 | Сваривается без ограничений. |
35Г2 | Сталь: 40Х | Трудно-свариваемая. Требуется подогрев и последующая термообработка. |
40Г2 | Сталь: 45Г2, 60Г | Трудно-свариваемая. Требуется подогрев и последующая термообработка. |
45Г2 | Сталь: 50Г2 | Трудно-свариваемая. Требуется подогрев и последующая термообработка. |
50Г2 | Сталь: 45Г2, 60Г | Не применяется для сварных конструкций |
47ГТ | Сталь: 40ХГРТ | Не применяется для сварных конструкций |
18ХГТ, 25 | Сталь: 30ХГТ, 25ХГТ, 12ХН3А, 12Х2Н4А, 20ХН2М, 20ХГР | Сваривается без ограничений, кроме деталей после химико-термической обработки |
20ХГР | Сталь: 20ХН3А, 20ХН24, 18Х1Т, 12ХН2, 12ХН3А | Сваривается без ограничений, кроме деталей после химико-термической обработки |
25Х1Т | Сталь: 18ХГТ, 30ХГТ, 25ХГМ | Требуется последующая термообработка |
30ХГТ | Сталь: 18ХГТ, 20ХН2М, 25ХГТ, 12Х2Н4А | Ограниченно свариваемая. Рекомендуется подогрев и последующая термообработка |
33ХС | Трудно-свариваемая | |
38ХС | Сталь: 40ХС, 38ХС, 35ХГТ | Трудно-свариваемая |
40ХС | ||
15ХФ | Сталь: 20ХФ | Сваривается без ограничений (способ КТС) |
40ХФА | Сталь: 40Х, 65Г, 50ХФА, 30Х3МФ | Трудно-свариваемая. Требуется подогрев и последующая термообработка. |
15ХМ | Сваривается без ограничений. Рекомендуется подогрев и последующая термообработка | |
30ХМ, 30ХМА | Сталь: 35ХМ, 35ХРА | Ограниченно свариваемая. Рекомендуется подогрев и последующая термообработка |
35ХМ | Сталь: 40Х, 40ХН, 30ХН, 35ХГСА | Ограниченно свариваемая. Рекомендуется подогрев и последующая термообработка |
38ХН | Ограниченно свариваемая. Рекомендуется подогрев и последующая термообработка | |
20ХН | Сталь: 15ХГ, 20ХНР, 18ХГТ | Ограниченно свариваемая. |
40ХН | Сталь: 45ХН, 50ХН, 38ХГН, 40Х, 35ХГФ, 40ХНР, 40ХНМ, 30ХГВТ | Трудно-свариваемая. Рекомендуется подогрев и последующая термообработка |
45ХН | Сталь: 40ХН | Трудно-свариваемая. Рекомендуется подогрев и последующая термообработка |
50ХН | Сталь: 40ХН, 60ХГ | Не применяется для сварных конструкций |
20ХНР | Сталь: 20ХН | Ограниченно свариваемая. Требуется подогрев и последующая термообработка. |
12ХН2 | Сталь: 20хнр, 20ХГНР, 12ХН3А, 18ХГТ, 20ХГР | Ограниченно свариваемая. Требуется подогрев и последующая термообработка. |
12ХН3А | Сталь: 12ХН2, 20ХН3А, 25ХГТ, 12Х2НА, 20ХНР | Ограниченно свариваемая. Требуется подогрев и последующая термообработка. |
20ХН3А | Сталь: 20ХГНР, 20ХНГ, 38ХА, 20ХГР | Ограниченно свариваемая. Требуется подогрев и последующая термообработка. |
12Х2Н4А | Сталь: 20ХГНР, 12ХН2, 20ХГР, 12ХН3А, 20Х2Н4А | Ограниченно свариваемая. Требуется подогрев и последующая термообработка. |
20Х2Н4А | Сталь: 20ХГНР, 20ХГНТР | Ограниченно свариваемая. Требуется подогрев и последующая термообработка. |
30ХН3А | Сталь: 30Х2ГН2, 34ХН2М | Ограниченно свариваемая. Требуется подогрев и последующая термообработка. |
20ХГСА | Сталь: 30ХГСА | Сваривается без ограничений |
25ХГСА | Сталь: 20ХГСА | Сваривается без ограничений |
30ХГС, | Сталь: 40ХФА, 35ХМ, 40ХН, 35ХГСА | Ограниченно свариваемая. Требуется подогрев и последующая термообработка. |
30ХН2МА | ||
38Х2Н2МА | Не применяется для сварных работ | |
40ХН2МА | Сталь: 40ХГТ, 40ХГР, 30Х3МФ, 45ХН2МФА | Трудно-свариваемая. Необходим подогрев и последующая термообработка |
40Х2Н2МА | Сталь: 38Х2Н2МА | Трудно-свариваемая. Необходим подогрев и последующая термообработка |
38ХН3МА | Сталь: 38ХН3ВА | Не применяется для сварных конструкций |
18Х2Н4МА | Сталь: 20Х2Н4А | Трудно-свариваемая. Необходим подогрев и последующая термообработка |
30ХГСА | Сталь: 40ХФА, 35ХМ, 40ХН, 25ХГСА, 35ХГСА | Трудно-свариваемая. Необходим подогрев и последующая термообработка |
35ХГСА | Сталь: 30ХГС, 30ХГСА, 30ХГТ, 35ХМ | Трудно-свариваемая. Необходим подогрев и последующая термообработка |
30ХГСН2А | Трудно-свариваемая. Необходим подогрев и последующая термообработка | |
38ХГН | Сталь: 38ХГНМ | Трудно-свариваемая. Необходим подогрев и последующая термообработка |
20ХГНР | Сталь: 20ХН3А | Трудно-свариваемая. Необходим подогрев и последующая термообработка |
20ХН2М | Сталь: 20ХГР, 15ХР, 20ХНР, 20ХГНР | Трудно-свариваемая. Необходим подогрев и последующая термообработка |
30ХН2МФА | Сталь: 30ХН2ВФА | Трудно-свариваемая. Необходим подогрев и последующая термообработка |
36Х2Н2МФА | Трудно-свариваемая. | |
38ХН3МФА | Не применяется для сварных конструкций | |
45ХН2МФА | Трудно-свариваемая. Необходим подогрев и последующая термообработка | |
20ХН4ФА | Сталь: 18Х2Н4МА | Не применяется для сварных конструкций |
38Х2МЮА | Сталь: 38Х2ЮА, 38ХВФЮ, 38Х2Ю, 20Х3МВФ | Не применяется для сварных конструкций |
ГОСТ 5520-79 | ||
16К,18К | Сваривается без ограничений | |
20К | Сваривается без ограничений | |
22К | Ограниченно свариваемая. Рекомендуется подогрев и последующая термообработка | |
ГОСТ 5632-72 | ||
40Х9С2 | Не применяется для сварных конструкций | |
40Х10С2М | Трудно-свариваемая. Необходим подогрев и последующая термообработка | |
08Х13 | Сталь: 12Х13, 12Х18Н9Т | Ограниченно свариваемая. Подогрев и термообработка применяются в зависимости от метода сварки, вида и назначения конструкций |
08Х13, 12Х13, 20Х13, 25Х13Н2 | Сталь: 12Х13, 12Х18Н9Т, Сталь: 20Х13, Сталь: 12Х13, 14Х17Н2 | |
30Х13, 40Х13 | Не применяется для сварных конструкций | |
10Х14АГ16 | Сталь: 12Х18Н9, 08Х18Н10, 12Х18Н9Т, 12Х18Н10Т | Сваривается без ограничений |
12Х17 | Сталь: 12Х18Н9Т | Не рекомендуется для сварных конструкций. Трудно-свариваемая |
08Х17Т, 08Х18Т1 | Сталь: 12Х17, 08Х18Т1, 08Х17Т | Ограниченно свариваемая |
95Х18 | Не применяется для сварных конструкций | |
15Х25Т | Сталь: 12Х18Н10Т | Трудно-свариваемая. Необходим подогрев и последующая термообработка |
15Х28 | Сталь: 15Х25Т, 20Х23Н18 | Трудно-свариваемая. Необходим подогрев и последующая термообработка |
20Х23Н13 | Ограниченно свариваемая | |
20Х23Н18 | Сталь: 10Х25Т, 20Х23Н13 | Ограниченно свариваемая |
10Х23Н10 | Ограниченно свариваемая | |
20Х25Н20С | Ограниченно свариваемая | |
15Х12ВНМФ | Трудно-свариваемая | |
20Х12ВНМФ | Сталь: 15Х12ВНМФ, 18Х11МНФБ | Трудно-свариваемая |
37Х12Н8Г2МФБ | Ограниченно свариваемая | |
13Х11Н2В2МФ | Ограниченно свариваемая | |
45Х14Н14В2М | Трудно-свариваемая | |
40Х15Н7Г7Ф2МС | Трудно-свариваемая | |
08Х17Н13М21 | Сталь: 10Х17Н13М21 | Хорошо свариваемая |
10Х17Н3М2Т | Хорошо свариваемая | |
31Х19Н9МВБТ | Трудно-свариваемая | |
10Х14Г14Н4Т | Сталь: 20Х13Н4Г9, 12Х18Н9Т, 12Х18Н10Т, 08Х18Н10Т | Сваривается удовлетворительно |
14Х17Н2 | Сталь: 20Х17Н2 | Хорошо свариваемая |
12Х18Н9 | Сталь: 20Х13Н4Г9, 10Х14Г14Н4Т, | Сваривается без ограничений |
20Х13Н4Г9 | ||
17Х18Н9 | ||
08Х18Н10, 08Х18Н10Т, 12Х18Н9Т, 12Х18Н10Т | Сталь: 12Х18Н10Т, | Сваривается без ограничений |
12Х18Н9Т | Сталь: 15Х25Т, 08Х18Г8Н2Т, 10Х14Г14Н4Т, 08Х17Т | |
12Х18Н12Т | Сталь: 12Х18Н9, 12Х18Н9Т, 12Х18Н10Т | Ограниченно сваривается |
08Х18Г8Н2Т | Сталь: 12Х18Н9 | Сваривается без ограничений |
20Х20Н14С2 | Сваривается без ограничений | |
12Х25Н16Г7АР | Сваривается без ограничений | |
08Х22Н6Т | Сталь: 12Х18Н9Т, 12Х18Н10Т, 08Х18Н10Т | Сваривается без ограничений |
06ХН28МДТ | Сплав: 03ХН28МДТ | Сваривается без ограничений |
ХН35ВТ | Трудно-свариваемая | |
ХН35ВТЮ | Трудно-свариваемая | |
ХН70Ю | Ограниченно сваривается | |
ХН70ВМЮТ | Трудно-свариваемая | |
ХН70ВМТЮФ | Трудно-свариваемая | |
ХН77ТЮР | Трудно-свариваемая | |
ХН78Т | Сплав: ХН38Т, Сталь: 12Х25Н16Г7АР, 20Х23Н18 | Трудно-свариваемая |
ХН80ТБЮ | Трудно-свариваемая | |
ГОСТ 5781-82 | ||
20ХГ2Ц | Сваривается без ограничений | |
35ГС | Сталь: Ст5сп, Ст6, Ст5пс | Сваривается без ограничений |
25Г2С | ||
ГОСТ 5950-73 | ||
ХВ4Ф | Не применяется для сварных конструкций | |
9Х1 | Сталь: 9х2 | Не применяется для сварных конструкций |
9ХС | Сталь: ХВГ | Не применяется для сварных конструкций |
ХВГ | Сталь: 9ХС, 9ХВГ, ШХ15СГ | Не применяется для сварных конструкций |
9ХВГ | Сталь: ХВГ | Не применяется для сварных конструкций |
Х6ВФ | Сталь: Х12Ф1, Х12М, 9Х5Ф | Не применяется для сварных конструкций |
Х12, Х12ВМФ | Сталь: Х12МФ | Не применяется для сварных конструкций |
Х12МФ | Сталь: Х6ВФ, Х12Ф1, Х12ВМФ | Не применяется для сварных конструкций |
Сталь: Х6ВФ, Х6ВФМ | ||
Х12Ф1 | ||
7ХГ2ВМФ | Не применяется для сварных конструкций | |
7Х3 | Сталь: 8Х3 | Не применяется для сварных конструкций |
8Х3 | Сталь: 7Х3 | |
5ХНМ | Сталь: 5ХНВ, 5ХГМ, 4ХМФС, 5ХНВС, 4Х5В2ФС | Не применяется для сварных конструкций |
5ХГМ | Сталь: 5ХНМ, 5ХНВ, 6ХВС, 5ХНС, 5ХНСВ | Не применяется для сварных конструкций |
4ЗМФС | Не применяется для сварных конструкций | |
4Х5МФС | Не применяется для сварных конструкций | |
4ХМФ1С | Не применяется для сварных конструкций | |
3Х3МХФ | Не применяется для сварных конструкций | |
6ХС | Не применяется для сварных конструкций | |
4ХВ2С | Сталь: 4Х5В2ФС, 4Х3В2М2 | Не применяется для сварных конструкций |
5ХВ2СФ | Сталь: 6ХВ2С | Не применяется для сварных конструкций |
6ХВ2С | Сталь: 6ХЗФС | |
6ХВГ | Не применяется для сварных конструкций | |
ГОСТ 9045-80 | ||
08Ю | Сваривается без ограничений | |
ГОСТ 14959-79 | ||
65 | Сталь: 60, 70 | Не применяется для сварных конструкций |
70 | 65Г | |
75 | Сталь: 70, 80, 85 | Не применяется для сварных конструкций |
85 | Сталь: 70, 75, 80 | Не применяется для сварных конструкций |
60Г | Сталь: 65Г | Не применяется для сварных конструкций |
65Г | Сталь: 70, У8А, 70Г, 60С2А, 9ХС, 50ХФА, 60С2, 55С2 | Не применяется для сварных конструкций |
55С2 | Сталь: 50С2, 60С2, 35Х2АФ | Не применяется для сварных конструкций |
60С2 | Сталь: 55С2, 50ХФА, | Не применяется для сварных конструкций |
60С2А | 60С2Н2А, 60С2Г, 50ХФА | |
70С3А | Не применяется для сварных конструкций | |
55ХГР | Не применяется для сварных конструкций | |
50ХФА | Сталь: 60С2А, 50ХГФА, 9ХС | Не применяется для сварных конструкций |
60С2ХА | Сталь: 60С2ХФА, 60С2Н2А | Не применяется для сварных конструкций |
60С2ХФА | Сталь: 60С2А, 60С2ХА, 9ХС, 60С2ВА | Не применяется для сварных конструкций |
65С2ВА | Сталь: 60С2А, 60С2ХА | Не применяется для сварных конструкций |
60С2Н2А | Сталь: 60С2А, 60С2ХА | Не применяется для сварных конструкций |
ГОСТ 19265-73 | ||
Р18 | При стыковой электросварке со сталью 45 и 40Х свариваемость хорошая | |
Р6М5К5 | При стыковой электросварке со сталью 45 и 40Х свариваемость хорошая | |
Р9М4К8 | При стыковой электросварке со сталью 45 и 40Х свариваемость хорошая | |
ГОСТ 19281-89 | ||
09Г2 | Сталь: 09Г2С, 10Г2 | Сваривается без ограничений |
14Г2 | Сталь: 15ХСНД | Ограниченно свариваемая |
12ГС | Сталь: 15ГС | Сваривается без ограничений |
16ГС | Сталь: 17ГС | Сваривается без ограничений |
17ГС | Сталь: 16ГС | Сваривается без ограничений |
17Г1С | Сталь: 17ГС | Сваривается без ограничений |
09Г2С | Сталь: 10Г2С, 09Г2 | Сваривается без ограничений |
10Г2С1 | Сталь: 10Г2С1Д | Сваривается без ограничений |
10Г2БД | Сталь: 10Г2Б | Сваривается без ограничений |
15Г2СФД | Сваривается без ограничений | |
14Г2АФ | Сталь: 16Г2АФ | Сваривается без ограничений |
16Г2АФ | Сталь: 14Г2АФ | Сваривается без ограничений |
18Г2ФАпс | Сталь: 15Г2ФАДпс, 16Г2АФ, 10ХСНД, 15ХСНД | Сваривается без ограничений |
14ХГС | Сталь: 15ХСНД, 16ГС | Сваривается без ограничений |
15Г2АФДпс | Сталь: 16Г2АФ, 18Г2АФпс, 10ХСНД | Сваривается без ограничений |
10ХСНД | Сталь: 16Г2АФ | Сваривается без ограничений |
10ХНДП | Сваривается без ограничений | |
15ХСНД | Сталь: 16Г2АФ, 14ХГС, 16ГС | Сваривается без ограничений |
ГОСТ 20072-72 | ||
12МХ | Сваривается без ограничений. Рекомендуется подогрев и последующая термическая обработка | |
12Х1МФ | Сваривается без ограничений. Рекомендуется подогрев и последующая термическая обработка | |
25Х1МФ | Сваривается без ограничений. Рекомендуется подогрев и последующая термическая обработка | |
20Х3МВФ | Сваривается без ограничений. Рекомендуется подогрев и последующая термическая | |
15Х5М | Сваривается без ограничений. Рекомендуется подогрев и последующая термическая обработка |
ГОСТ | Марки стали | Заменитель | Свариваемость |
---|---|---|---|
380-94 | Ст0 | Сваривается без ограничений | |
Ст2кп Ст2пс Ст2сп |
Ст2сп Ст2пс |
Сваривается без ограничений. Для толщины более 36 мм рекомендуется подогрев и последующая термообработка | |
Ст3кп | Ст3пс | Сваривается без ограничений. Для толщины более 36 мм рекомендуется подогрев и последующая термообработка | |
Ст3пс Ст3сп |
Ст3сп Ст3пс |
Сваривается без ограничений. Для толщины более 36 мм рекомендуется подогрев и последующая термообработка | |
Ст3Гпс | Ст3пс Сталь 18Гпс |
Сваривается без ограничений. Для толщины более 36 мм рекомендуется подогрев и последующая термообработка | |
Ст4кп | |||
Ст4пс | Ст4сп | Сваривается ограниченно | |
Ст5пс Ст5сп |
Ст6сп Ст4сп |
Сваривается ограниченно. Рекомендуется подогрев и последующая термообработка | |
Ст6пс | Сваривается ограниченно. Рекомендуется подогрев и последующая термообработка | ||
Ст6сп | Ст5сп | Сваривается ограниченно. Рекомендуется подогрев и последующая термообработка | |
801-78 | ШХ15 | Стали: ШХ9, ШХ12, ШХ15СГ | Способ сварки КТС |
ШХ15СГ | Стали: ХВГ, ШХ15, 9ХС, ХВСГ | Способ сварки КТС | |
ШХ4 | Способ сварки КТС | ||
1050-88 | 08 | Сталь 10 | Сваривается без ограничений, кроме деталей после химико-термической обработки |
08кп 08пс |
Сталь 08 | Сваривается без ограничений, кроме деталей после химико-термической обработки | |
10 | Стали: 08, 15, 08кп | Сваривается без ограничений, кроме деталей после химико-термической обработки | |
10кп 10пс |
Стали: 08кп, 15кп, 10 | Сваривается без ограничений, кроме деталей после химико-термической обработки | |
15 | Стали: 10, 20 | Сваривается без ограничений, кроме деталей после химико-термической обработки | |
15кп 15пс |
Стали: 10кп, 20кп | Сваривается без ограничений | |
18кп | Сваривается без ограничений | ||
20 | Сталь: 15, 20 | Сваривается без ограничений, кроме деталей после химико-термической обработки | |
20кп 20пс |
Сталь: 15кп | Сваривается без ограничений, кроме деталей после химико-термической обработки | |
25 | Сталь: 20, 30 | Сваривается без ограничений, кроме деталей после химико-термической обработки | |
30 | Стали: 25, 35 | Сваривается ограниченно. Рекомендуется подогрев и последующая термообработка | |
35 | Стали: 30, 40, 35Г | Сваривается ограниченно. Рекомендуется подогрев и последующая термообработка | |
40 | Стали: 35, 45, 40Г | Сваривается ограниченно. Рекомендуется подогрев и последующая термообработка | |
45 | Стали: 40Х, 50, 50Г2 | Трудно — свариваемая. Необходим подогрев и последующая термообработка | |
50 | Стали: 45, 50Г, 50Г2, 55 | Трудно — свариваемая. Необходим подогрев и последующая термообработка | |
55 | Стали: 50, 60, 50Г | Не применяется для сварных конструкций | |
58 (55пп) | Стали: 30ХГТ, 20ХГНТР, 20ХН2М, 12ХНЗА, 18ХГТ | Не применяется для сварных конструкций | |
1414-75 | А20 | Сталь А12 | Не применяется для сварных конструкций |
А30 А40Г |
Сталь: А40Г | Не применяется для сварных конструкций | |
1435-90 | У7, У7А | Сталь: У8 | Не применяется для сварных конструкций |
У8, У8А | Сталь: У7, У7А У10, У10А | Не применяется для сварных конструкций | |
У9, У9А | Стали: У7, У7А, У8, У8А | Не применяется для сварных конструкций | |
У10, У10А | Стали: У10, У10А | Не применяется для сварных конструкций | |
4543-71 | 15Х | Сталь: 20Х | Сваривается без ограничений, кроме деталей после химико-термической обработки |
20Х | Сталь: 15Х, 20ХН, 18ХГТ | Сваривается без ограничений, кроме деталей после химико-термической обработки | |
30Х | Сталь: 35Х | Ограниченно сваривается | |
35Х | Сталь: 40Х | Ограниченно сваривается | |
38ХА | Сталь: 40Х, 35Х | Трудно-свариваемая | |
40Х | Сталь: 45Х, 35ХА, 40ХС | Трудно-свариваемая, необходим подогрев и последующая термообработка | |
45Х | Сталь: 40Х, 45Х, 50ХН | Трудно-свариваемая, необходим подогрев и последующая термообработка | |
50Х | Сталь: 40Х, 45Х, 50ХН | Трудно-свариваемая, необходим подогрев и последующая термообработка | |
15Г 20Г |
Сталь: 20Г, 20, 30Г | Хорошо свариваемая | |
30Г | Сталь: 35, 40Г | Ограниченно свариваемая. Рекомендуется подогрев и последующая термообработка | |
35Г | Ограниченно свариваемая. Рекомендуется подогрев и последующая термообработка | ||
40Г | Стали: 45, 40Х | Ограниченно свариваемая. Рекомендуется подогрев и последующая термообработка | |
45Г | Стали: 40Г, 50Г | Трудно-свариваемая. Рекомендуется подогрев и последующая термообработка. | |
50Г | Стали: 40Г, 50 | Трудно-свариваемая. Рекомендуется подогрев и последующая термообработка. | |
10Г2 | Сталь: 09Г2 | Сваривается без ограничений. | |
35Г2 | Сталь: 40Х | Трудно-свариваемая. Требуется подогрев и последующая термообработка. | |
40Г2 | Сталь: 45Г2, 60Г | Трудно-свариваемая. Требуется подогрев и последующая термообработка. | |
45Г2 | Сталь: 50Г2 | Трудно-свариваемая. Требуется подогрев и последующая термообработка. | |
50Г2 | Сталь: 45Г2, 60Г | Не применяется для сварных конструкций | |
47ГТ | Сталь: 40ХГРТ | Не применяется для сварных конструкций | |
18ХГТ 25 |
Сталь: 30ХГТ, 25ХГТ, 12ХН3А, 12Х2Н4А, 20ХН2М, 20ХГР | Сваривается без ограничений, кроме деталей после химико-термической обработки | |
20ХГР | Сталь: 20ХН3А, 20ХН24, 18Х1Т, 12ХН2, 12ХН3А | Сваривается без ограничений, кроме деталей после химико-термической обработки | |
25Х1Т | Сталь: 18ХГТ, 30ХГТ, 25ХГМ | Требуется последующая термообработка | |
30ХГТ | Сталь: 18ХГТ, 20ХН2М, 25ХГТ, 12Х2Н4А | Ограниченно свариваемая. Рекомендуется подогрев и последующая термообработка | |
33ХС | Трудно-свариваемая | ||
38ХС 40ХС |
Сталь: 40ХС, 38ХС, 35ХГТ | Трудно-свариваемая | |
15ХФ | Сталь: 20ХФ | Сваривается без ограничений (способ КТС) | |
40ХФА | Сталь: 40Х, 65Г, 50ХФА, 30Х3МФ | Трудно-свариваемая. Требуется подогрев и последующая термообработка. | |
15ХМ | Сваривается без ограничений. Рекомендуется подогрев и последующая термообработка | ||
30ХМ 30ХМА |
Сталь: 35ХМ, 35ХРА | Ограниченно свариваемая. Рекомендуется подогрев и последующая термообработка | |
35ХМ | Сталь: 40Х, 40ХН, 30ХН, 35ХГСА | Ограниченно свариваемая. Рекомендуется подогрев и последующая термообработка | |
38ХН | Ограниченно свариваемая. Рекомендуется подогрев и последующая термообработка | ||
20ХН | Сталь: 15ХГ, 20ХНР, 18ХГТ | Ограниченно свариваемая. | |
40ХН | Сталь: 45ХН, 50ХН, 38ХГН, 40Х, 35ХГФ, 40ХНР, 40ХНМ, 30ХГВТ | Трудно-свариваемая. Рекомендуется подогрев и последующая термообработка | |
45ХН | Сталь: 40ХН | Трудно-свариваемая. Рекомендуется подогрев и последующая термообработка | |
50ХН | Сталь: 40ХН, 60ХГ | Не применяется для сварных конструкций | |
20ХНР | Сталь: 20ХН | Ограниченно свариваемая. Требуется подогрев и последующая термообработка. | |
12ХН2 | Сталь: 20хнр, 20ХГНР, 12ХН3А, 18ХГТ, 20ХГР | Ограниченно свариваемая. Требуется подогрев и последующая термообработка. | |
12ХН3А | Сталь: 12ХН2, 20ХН3А, 25ХГТ, 12Х2НА, 20ХНР | Ограниченно свариваемая. Требуется подогрев и последующая термообработка. | |
20ХН3А | Сталь: 20ХГНР, 20ХНГ, 38ХА, 20ХГР | Ограниченно свариваемая. Требуется подогрев и последующая термообработка. | |
12Х2Н4А | Сталь: 20ХГНР, 12ХН2, 20ХГР, 12ХН3А, 20Х2Н4А | Ограниченно свариваемая. Требуется подогрев и последующая термообработка. | |
20Х2Н4А | Сталь: 20ХГНР, 20ХГНТР | Ограниченно свариваемая. Требуется подогрев и последующая термообработка. | |
30ХН3А | Сталь: 30Х2ГН2, 34ХН2М | Ограниченно свариваемая. Требуется подогрев и последующая термообработка. | |
20ХГСА | Сталь: 30ХГСА | Сваривается без ограничений | |
25ХГСА | Сталь: 20ХГСА | Сваривается без ограничений | |
30ХГС, 30ХН2МА |
Сталь: 40ХФА, 35ХМ, 40ХН, 35ХГСА | Ограниченно свариваемая. Требуется подогрев и последующая термообработка. | |
38Х2Н2МА | Не применяется для сварных работ | ||
40ХН2МА | Сталь: 40ХГТ, 40ХГР, 30Х3МФ, 45ХН2МФА | Трудно-свариваемая. Необходим подогрев и последующая термообработка | |
40Х2Н2МА | Сталь: 38Х2Н2МА | Трудно-свариваемая. Необходим подогрев и последующая термообработка | |
38ХН3МА | Сталь: 38ХН3ВА | Не применяется для сварных конструкций | |
18Х2Н4МА | Сталь: 20Х2Н4А | Трудно-свариваемая. Необходим подогрев и последующая термообработка | |
30ХГСА | Сталь: 40ХФА, 35ХМ, 40ХН, 25ХГСА, 35ХГСА | Трудно-свариваемая. Необходим подогрев и последующая термообработка | |
35ХГСА | Сталь: 30ХГС, 30ХГСА, 30ХГТ, 35ХМ | Трудно-свариваемая. Необходим подогрев и последующая термообработка | |
30ХГСН2А | Трудно-свариваемая. Необходим подогрев и последующая термообработка | ||
38ХГН | Сталь: 38ХГНМ | Трудно-свариваемая. Необходим подогрев и последующая термообработка | |
20ХГНР | Сталь: 20ХН3А | Трудно-свариваемая. Необходим подогрев и последующая термообработка | |
20ХН2М | Сталь: 20ХГР, 15ХР, 20ХНР, 20ХГНР | Трудно-свариваемая. Необходим подогрев и последующая термообработка | |
30ХН2МФА | Сталь: 30ХН2ВФА | Трудно-свариваемая. Необходим подогрев и последующая термообработка | |
36Х2Н2МФА | Трудно-свариваемая. | ||
38ХН3МФА | Не применяется для сварных конструкций | ||
45ХН2МФА | Трудно-свариваемая. Необходим подогрев и последующая термообработка | ||
20ХН4ФА | Сталь: 18Х2Н4МА | Не применяется для сварных конструкций | |
38Х2МЮА | Сталь: 38Х2ЮА, 38ХВФЮ, 38Х2Ю, 20Х3МВФ | Не применяется для сварных конструкций | |
5520-79 | 16К 18К |
Сваривается без ограничений | |
20К | Сваривается без ограничений | ||
22К | Ограниченно свариваемая. Рекомендуется подогрев и последующая термообработка | ||
5632-72 | 40Х9С2 | Не применяется для сварных конструкций | |
40Х10С2М | Трудно-свариваемая. Необходим подогрев и последующая термообработка | ||
08Х13 12Х13 20Х13 25Х13Н2 |
Сталь: 12Х13, 12Х18Н9Т Сталь: 20Х13 Сталь: 12Х13, 14Х17Н2 |
Ограниченно свариваемая. Подогрев и термообработка применяются в зависимости от метода сварки, вида и назначения конструкций | |
30Х13 40Х13 |
Не применяется для сварных конструкций | ||
10Х14АГ16 | Сталь: 12Х18Н9, 08Х18Н10, 12Х18Н9Т, 12Х18Н10Т | Сваривается без ограничений | |
12Х17 | Сталь: 12Х18Н9Т | Не рекомендуется для сварных конструкций. Трудно-свариваемая | |
08Х17Т, 08Х18Т1 |
Сталь: 12Х17, 08Х18Т1, 08Х17Т | Ограниченно свариваемая | |
95Х18 | Не применяется для сварных конструкций | ||
15Х25Т | Сталь: 12Х18Н10Т | Трудно-свариваемая. Необходим подогрев и последующая термообработка | |
15Х28 | Сталь: 15Х25Т, 20Х23Н18 | Трудно-свариваемая. Необходим подогрев и последующая термообработка | |
20Х23Н13 | Ограниченно свариваемая | ||
20Х23Н18 | Сталь: 10Х25Т, 20Х23Н13 | Ограниченно свариваемая | |
10Х23Н10 | Ограниченно свариваемая | ||
20Х25Н20С | Ограниченно свариваемая | ||
15Х12ВНМФ | Трудно-свариваемая | ||
20Х12ВНМФ | Сталь: 15Х12ВНМФ, 18Х11МНФБ | Трудно-свариваемая | |
37Х12Н8Г2МФБ | Ограниченно свариваемая | ||
13Х11Н2В2МФ | Ограниченно свариваемая | ||
45Х14Н14В2М | Трудно-свариваемая | ||
40Х15Н7Г7Ф2МС | Трудно-свариваемая | ||
08Х17Н13М21 | Сталь: 10Х17Н13М21 | Хорошо свариваемая | |
10Х17Н3М2Т | Хорошо свариваемая | ||
31Х19Н9МВБТ | Трудно-свариваемая | ||
10Х14Г14Н4Т | Сталь: 20Х13Н4Г9, 12Х18Н9Т, 12Х18Н10Т, 08Х18Н10Т | Сваривается удовлетворительно | |
14Х17Н2 | Сталь: 20Х17Н2 | Хорошо свариваемая | |
12Х18Н9 17Х18Н9 |
Сталь: 20Х13Н4Г9, 10Х14Г14Н4Т, 20Х13Н4Г9 |
Сваривается без ограничений | |
08Х18Н10 08Х18Н10Т 12Х18Н9Т 12Х18Н10Т |
Сталь: 12Х18Н10Т, Сталь: 15Х25Т, 08Х18Г8Н2Т, 10Х14Г14Н4Т, 08Х17Т |
Сваривается без ограничений | |
12Х18Н12Т | Сталь: 12Х18Н9, 12Х18Н9Т, 12Х18Н10Т | Ограниченно сваривается | |
08Х18Г8Н2Т | Сталь: 12Х18Н9 | Сваривается без ограничений | |
20Х20Н14С2 | Сваривается без ограничений | ||
12Х25Н16Г7АР | Сваривается без ограничений | ||
08Х22Н6Т | Сталь: 12Х18Н9Т, 12Х18Н10Т, 08Х18Н10Т | Сваривается без ограничений | |
06ХН28МДТ | Сплав: 03ХН28МДТ | Сваривается без ограничений | |
ХН35ВТ | Трудно-свариваемая | ||
ХН35ВТЮ | Трудно-свариваемая | ||
ХН70Ю | Ограниченно сваривается | ||
ХН70ВМЮТ | Трудно-свариваемая | ||
ХН70ВМТЮФ | Трудно-свариваемая | ||
ХН77ТЮР | Трудно-свариваемая | ||
ХН78Т | Сплав: ХН38Т, Сталь: 12Х25Н16Г7АР, 20Х23Н18 | Трудно-свариваемая | |
ХН80ТБЮ | Трудно-свариваемая | ||
5781-82 | 20ХГ2Ц | Сваривается без ограничений | |
35ГС 25Г2С |
Сталь: Ст5сп, Ст6, Ст5пс | Сваривается без ограничений | |
5950-73 | ХВ4Ф | Не применяется для сварных конструкций | |
9Х1 | Сталь: 9х2 | Не применяется для сварных конструкций | |
9ХС | Сталь: ХВГ | Не применяется для сварных конструкций | |
ХВГ | Сталь: 9ХС, 9ХВГ, ШХ15СГ | Не применяется для сварных конструкций | |
9ХВГ | Сталь: ХВГ | Не применяется для сварных конструкций | |
Х6ВФ | Сталь: Х12Ф1, Х12М, 9Х5Ф | Не применяется для сварных конструкций | |
Х12, Х12ВМФ | Сталь: Х12МФ | Не применяется для сварных конструкций | |
Х12МФ Х12Ф1 |
Сталь: Х6ВФ, Х12Ф1, Х12ВМФ Сталь: Х6ВФ, Х6ВФМ |
Не применяется для сварных конструкций | |
7ХГ2ВМФ | Не применяется для сварных конструкций | ||
7Х3 8Х3 |
Сталь: 8Х3 Сталь: 7Х3 |
Не применяется для сварных конструкций | |
5ХНМ | Сталь: 5ХНВ, 5ХГМ, 4ХМФС, 5ХНВС, 4Х5В2ФС | Не применяется для сварных конструкций | |
5ХГМ | Сталь: 5ХНМ, 5ХНВ, 6ХВС, 5ХНС, 5ХНСВ | Не применяется для сварных конструкций | |
4ЗМФС | Не применяется для сварных конструкций | ||
4Х5МФС | Не применяется для сварных конструкций | ||
4ХМФ1С | Не применяется для сварных конструкций | ||
3Х3МХФ | Не применяется для сварных конструкций | ||
6ХС | Не применяется для сварных конструкций | ||
4ХВ2С | Сталь: 4Х5В2ФС, 4Х3В2М2 | Не применяется для сварных конструкций | |
5ХВ2СФ 6ХВ2С |
Сталь: 6ХВ2С Сталь: 6ХЗФС |
Не применяется для сварных конструкций | |
6ХВГ | Не применяется для сварных конструкций | ||
9045-80 | 08Ю | Сваривается без ограничений | |
14959-79 | 65 70 |
Сталь: 60, 70 65Г |
Не применяется для сварных конструкций |
75 | Сталь: 70, 80, 85 | Не применяется для сварных конструкций | |
85 | Сталь: 70, 75, 80 | Не применяется для сварных конструкций | |
60Г | Сталь: 65Г | Не применяется для сварных конструкций | |
65Г | Сталь: 70, У8А, 70Г, 60С2А, 9ХС, 50ХФА, 60С2, 55С2 | Не применяется для сварных конструкций | |
55С2 | Сталь: 50С2, 60С2, 35Х2АФ | Не применяется для сварных конструкций | |
60С2 60С2А |
Сталь: 55С2, 50ХФА, 60С2Н2А, 60С2Г, 50ХФА |
Не применяется для сварных конструкций | |
70С3А | Не применяется для сварных конструкций | ||
55ХГР | Не применяется для сварных конструкций | ||
50ХФА | Сталь: 60С2А, 50ХГФА, 9ХС | Не применяется для сварных конструкций | |
60С2ХА | Сталь: 60С2ХФА, 60С2Н2А | Не применяется для сварных конструкций | |
60С2ХФА | Сталь: 60С2А, 60С2ХА, 9ХС, 60С2ВА | Не применяется для сварных конструкций | |
65С2ВА | Сталь: 60С2А, 60С2ХА | Не применяется для сварных конструкций | |
60С2Н2А | Сталь: 60С2А, 60С2ХА | Не применяется для сварных конструкций | |
19265-73 | Р18 | При стыковой электросварке со сталью 45 и 40Х свариваемость хорошая | |
Р6М5К5 | При стыковой электросварке со сталью 45 и 40Х свариваемость хорошая | ||
Р9М4К8 | При стыковой электросварке со сталью 45 и 40Х свариваемость хорошая | ||
19281-89 | 09Г2 | Сталь: 09Г2С, 10Г2 | Сваривается без ограничений |
14Г2 | Сталь: 15ХСНД | Ограниченно свариваемая | |
12ГС | Сталь: 15ГС | Сваривается без ограничений | |
16ГС | Сталь: 17ГС | Сваривается без ограничений | |
17ГС | Сталь: 16ГС | Сваривается без ограничений | |
17Г1С | Сталь: 17ГС | Сваривается без ограничений | |
09Г2С | Сталь: 10Г2С, 09Г2 | Сваривается без ограничений | |
10Г2С1 | Сталь: 10Г2С1Д | Сваривается без ограничений | |
10Г2БД | Сталь: 10Г2Б | Сваривается без ограничений | |
15Г2СФД | Сваривается без ограничений | ||
14Г2АФ | Сталь: 16Г2АФ | Сваривается без ограничений | |
16Г2АФ | Сталь: 14Г2АФ | Сваривается без ограничений | |
18Г2ФАпс | Сталь: 15Г2ФАДпс, 16Г2АФ, 10ХСНД, 15ХСНД | Сваривается без ограничений | |
14ХГС | Сталь: 15ХСНД, 16ГС | Сваривается без ограничений | |
15Г2АФДпс | Сталь: 16Г2АФ, 18Г2АФпс, 10ХСНД | Сваривается без ограничений | |
10ХСНД | Сталь: 16Г2АФ | Сваривается без ограничений | |
10ХНДП | Сваривается без ограничений | ||
15ХСНД | Сталь: 16Г2АФ, 14ХГС, 16ГС | Сваривается без ограничений | |
20072-72 | 12МХ | Сваривается без ограничений. Рекомендуется подогрев и последующая термическая обработка | |
12Х1МФ | Сваривается без ограничений. Рекомендуется подогрев и последующая термическая обработка | ||
25Х1МФ | Сваривается без ограничений. Рекомендуется подогрев и последующая термическая обработка | ||
20Х3МВФ | Сваривается без ограничений. Рекомендуется подогрев и последующая термическая | ||
15Х5М | Сваривается без ограничений. Рекомендуется подогрев и последующая термическая обработка |
Термообработка ТВЧ партий деталей — Интерм
Главная » Услуги » Выполнение технологических операций » Термообработка партий машиностроительных деталей
ООО “ИНТЕРМ” осуществляет закалку ТВЧ стальных деталей различной формы с последующим отпуском. Глубина закаленного слоя 1-4мм.
Компания ООО “ИНТЕРМ” предлагает различные услуги по закалке и термообработке. Наша компания проводит ТВЧ закалку различных деталей и марок сталей. Одни из самых распространенных заказов на ТВЧ термообработку:
- ТВЧ закалка стали 35
- ТВЧ закалка стали 40х
- ТВЧ закалка стали 40х13
- ТВЧ закалка стали 45
- Транзисторный источник питания 40кВт, 66кГц.
- Транзисторный источник питания 100кВт, 66кГц.
- Специализированные закалочные станки для закалки шестерен и звездочек большого диаметра, тел вращения, деталей сложной формы.
Используемые закалочные жидкости: вода, водный раствор FEROQUENCH 2000 (для высокоуглеродистой и легированной стали).
Параметры закаливаемых деталей:
ТВЧ закалка тел вращения (валы, оси и т.д.)
Производится на вертикальном закалочном станке. Максимальные размеры (параметры) детали:
Длина – 1000мм.
Диаметр – 200мм.
Масса – до 100кг.
ТВЧ термообработка шестерен и звездочек
Производится на специализированном закалочном станке. Максимальные размеры (параметры) детали:
Диаметр – 1200мм.
Высота – 200мм
Масса – до 150кг.
Модуль — 8-36
Индукционная закалка плоских протяженных поверхностей
Производится на специализированном закалочном оборудовании.
Возможен вариант установки закалочного оборудования на закаливаемую деталь.
Ширина обрабатываемой плоскости за один проход – до 300мм.
ТВЧ закалка внутренних поверхностей отверстий стальных деталей
Производится на специализированном закалочном станке.
Максимальный диаметр внутренней поверхности – 200мм.
ТВЧ закалка деталей сложной формы, а также валов и осей большого диаметра (более 200мм) методом непрерывно-последовательной закалки
Для достижения требуемой твердости и снятия остаточных напряжений проводится отпуск закаленных деталей.
Контроль твердости закаленных деталей осуществляется стационарным твердомером по Роквеллу NOVOTEST ТС-Р, ультразвуковыми твердомерами ТКМ-459, ТКМ-459М, динамическим твердомером ТЭМП-4К.
К деталям прошедшим термообработку прилагается протокол испытаний.
У нас вы можете купить ТВЧ оборудование для поверхностной индукционной закалки по доступной цене. Ознакомиться с оборудованием можно в разделе установки индукционного нагрева. Для того, чтобы узнать цену достаточно позвонить нам по номеру 8(812)-318-33-24 или написать письмо с запросом по адресу [email protected]
Улучшение механических свойств легированной стали (в 40 раз) за счет термической обработки Аббаса Аль-Джибори, Али Аль-Мосави, Кадима Аль-Муршеди :: SSRN
Журнал технических наук Аль-Кадисия, специальный выпуск для 2-й конференции инженерного колледжа / Университета Аль-Кадисия, 2009 г.
10 стр. Размещено: 10 июля 2017 г.
Дата написания: 19 октября 2009 г.
Аннотация
Термическая обработка — это процесс или несколько процессов, включающих нагрев и охлаждение твердого металла или сплава таким образом, чтобы получить желаемые условия или свойства, или восстановить свойства, которые были у металла или сплава, подвергшегося определенному рабочему процессу.Целью данного исследования является изучение влияния термической обработки на механические свойства стали с низким содержанием хрома (1,1% Cr) с (0,4%) углеродом, а именно: предел прочности при растяжении, твердость, удлинение и уменьшение площади. Термическая обработка включала полный отжиг, который состоял из нагрева стали до (870 ° C) и охлаждения в печи, закалки, которая проводилась путем нагрева до (870 ° C) и закалки в масле, а также отпуска при (300 ° C и 600 ° C). Механические свойства измеряли до и после термообработки, как показано на диаграммах между механическими свойствами термообработки.Важность этого исследования заключается в том, что использованный материал использовался только в областях милитаризма, и были рассчитаны его свойства для сравнения их с другими типами сталей для использования в гражданских областях.
Ключевые слова: термическая обработка, механические свойства, легированная сталь Тип (40X)
Рекомендуемое цитирование: Предлагаемое цитирование
Аль-Джибори, Аббас и Аль-Мосави, Али и Аль-Муршеди, Кадим, Улучшение механических свойств легированной стали (40x) с помощью термической обработки (19 октября 2009 г.).Журнал технических наук Аль-Кадисия, специальный выпуск для 2-й конференции инженерного колледжа / Университета Аль-Кадисия, 2009 г., доступно на SSRN: https://ssrn.com/abstract=2516311Термическая обработка стальных листов | Leeco Steel, LLC
Прочность, твердость и другие механические свойства стального листа сильно различаются в зависимости от марки и толщины. Для некоторых приложений, таких как навесное оборудование для строительной техники и строительная инфраструктура, требуется, чтобы уровни механических свойств были выше, чем можно достичь за счет уменьшения углерода или добавления сплавов.
Термическая обработка стали, включающая интенсивный нагрев с последующим охлаждением, изменяет физические, а иногда и химические свойства стали, что влияет на механические свойства материала.
В этой статье подробно рассматриваются четыре распространенных процесса термообработки:
- Нормализация
- Отжиг
- Закалка и отпуск
- Осадочно-твердение
Поставщики стального листа, такие как Leeco ® Steel, обычно хранят на складе различные марки, прошедшие такую обработку.
Улучшение механических свойств за счет термической обработкиПеред тем, как исследовать каждый из этих процессов, важно понять различия между свойствами стального листа, которые достигаются во время термообработки.
Прочность: Нагрузка, которую может выдержать материал, измеряется пределом текучести и пределом прочности на разрыв. Предел текучести — это максимальная точка напряжения, при которой материал будет постоянно изменять форму, а предел прочности — это точка, при которой изогнутый материал сломается.
Твердость: Уровень износостойкости материала, обычно измеряемый испытанием на удар по Шарпи.
Прочность: Не путать с прочностью или твердостью. Под ударной вязкостью понимается способность материала поглощать удары без разрушения.
Пластичность: Насколько материал может быть растянут, прежде чем станет слабым или хрупким, измеряется по удлинению — процент увеличения длины материала до разрушения.
Обрабатываемость: Легкость, с которой материал можно сварить, просверлить, прикрутить болтами или обработать на станке.
Хотя каждая из обычных термических обработок имеет один и тот же основной процесс интенсивного нагрева и охлаждения, они изменяют указанные выше механические свойства по-разному.
1. Нормализация
Нормализация включает нагрев стального листа до чрезвычайно высокой температуры в печи. Пластина выдерживается при этой температуре в течение достаточного времени — обычно минимум один час на 1 дюйм толщины пластины — и вынимается из печи для охлаждения на воздухе при комнатной температуре.
Во время этого процесса зернистая структура листа изменяется для увеличения твердости, пластичности, обрабатываемости и прочности. Эти свойства делают нормализованную пластину идеальной для применения в строительстве, например, для строительства зданий, мостов или морских сооружений, а также для строительства сосудов под давлением, для которых требуется стальная пластина, которая может выдерживать высокие уровни напряжения, а также проста в формовании.
Некоторые марки листов, которые Leeco обычно поставляет в нормализованном состоянии, включают ASTM A516, A537 и A633, а также API 2H 50.Каждая из этих марок имеет относительно высокий предел текучести и предел прочности на разрыв в результате нормализации, подробно описанной в таблице ниже.
Марка | Предел текучести | Растяжение |
A516 | 30-38 тысяч фунтов / кв. Дюйм | 55-90 тысяч фунтов на квадратный дюйм |
A537 | 40-60 тысяч фунтов / кв. Дюйм | 65-80 тысяч фунтов на квадратный дюйм |
A633 | 42-60 тысяч фунтов / кв. Дюйм | 63-100 тысяч фунтов / кв. Дюйм |
API 2H 50 | 47-50 тысяч фунтов / кв. Дюйм | 70-90 тысяч фунтов на квадратный дюйм |
Создание предложения
2.Отжиг
Отжиг, как и нормализация, также включает нагрев стального листа до чрезвычайно высокой температуры в печи. Однако отжиг отличается от нормализации в процессе охлаждения. Отжиг имеет более контролируемое охлаждение, чем нормализация, поскольку пластина охлаждается в печи до более низкой, ниже критической температуры.
Этот процесс контролируемого нагрева и охлаждения изменяет зернистую структуру листа, увеличивая пластичность и снижая твердость. Обладая повышенной прочностью и пластичностью, отожженный лист обычно используется в строительных проектах, где важна способность выдерживать большие нагрузки и растягиваться, не становясь хрупкими, например, в мостах.
ASTM A829 4140 — сорт, который может поставляться в отожженном состоянии — предлагает большую износостойкость, чем конструкционные сорта с более низким содержанием углерода, благодаря более высокому пределу прочности на разрыв, как показано в таблице ниже.
Марка | Растяжение |
A829 4140 | 70-140 тысяч фунтов / кв. Дюйм |
3.Закалка и отпуск
В то время как нормализация и отжиг имеют только один период нагрева и охлаждения, закалка и отпуск — это двухэтапный процесс. Первая часть процесса, известная как закалка, нагревает материал до высокой температуры, обычно от 1500 до 1650 градусов по Фаренгейту. Затем пластину быстро охлаждают водой. После закалки материал снова нагревают до температуры ниже критической, обычно от 300 до 700 градусов, и охлаждают на воздухе. Эта часть процесса называется темперированием.
Закалка и отпуск изменяют структуру зерна материала, что приводит к повышению твердости, ударной вязкости и прочности. Эта твердость и прочность делают закаленный и отпущенный лист идеальным вариантом для проектов, где прочность имеет решающее значение, что обычно включает строительное оборудование — самосвалы, прицепы, краны — резервуары для сосудов высокого давления и горное оборудование.
Некоторые из наиболее распространенных марок закаленного и отпущенного металла, хранящиеся на складе и продаваемые Leeco, включают ASTM A514, AR400 и AR500. Хотя процесс их термообработки не регулируется, AR400 и AR500 обычно закаливают и отпускают.
Марки, такие как A514, имеют более высокий предел прочности на растяжение и предел текучести из-за их повышенной ударной вязкости и прочности, чем сплавы без термической обработки, такие как ASTM A572 Grade 50, что можно увидеть в таблице ниже.
Марка | Предел текучести | Растяжение |
A514 толщиной ≥ 3/4 дюйма | 100 тысяч фунтов / кв. Дюйм | 110-130 тысяч фунтов / кв. Дюйм |
A514 ≤ ”до 2.5 дюймов толщиной | 100 тысяч фунтов / кв. Дюйм | 110-130 тысяч фунтов / кв. Дюйм |
A514 толщиной от 2,5 до 6 дюймов | 90 тысяч фунтов / кв. Дюйм | 100-130 тысяч фунтов / кв. Дюйм |
A572 Марка 50 | 50 тысяч фунтов / кв. Дюйм | 65 тысяч фунтов / кв. Дюйм |
Сделайте ценовое предложение на стальную пластину A514
4.Осадки-закалка
Подобно закалке и отпуску, дисперсионная закалка также включает в себя два периода повторного нагрева и охлаждения стального листа. Сначала пластина нагревается до высокой температуры — от 1000 до 1300 градусов, а затем быстро охлаждается. После охлаждения пластина проходит процесс, известный как старение, при котором пластина снова нагревается до более низкой, ниже критической температуры и быстро охлаждается.
Осадочная закалка увеличивает прочность листа и может увеличить ударную вязкость.Высокая прочность и обрабатываемость дисперсионно-упрочненного листа делает его широко используемым в приложениях, требующих способности выдерживать высокие нагрузки, таких как самоподъемные установки, строительное оборудование, железнодорожные вагоны, рамы грузовиков, компоненты трубопроводов и судостроение.
Маркис дисперсионным упрочнением, такие как ASTM A710, который хранится на складе Leeco, имеют высокие пределы прочности и текучести в результате измененной структуры зерен, как показано в таблице ниже. Эти свойства помогают A710 противостоять воздействию агрессивных сред на сталь.
Марка | Предел текучести | Растяжение |
A710 Класс A | 50-85 тысяч фунтов на квадратный дюйм | 60-90 тысяч фунтов / кв. Дюйм |
A710 Марка B | 70 тысяч фунтов / кв. Дюйм | 80 тысяч фунтов / кв. Дюйм |
После определения того, требуется ли для проекта лист из термообработанной стали, и если да, то какие сорт и обработка требуются, группы закупок должны выбрать поставщика, который будет соответствовать их требованиям.При поиске поставщика стального листа необходимо учитывать несколько важных факторов, которые следует учитывать специалистам по закупкам:
- Глубина и широта инвентаря пластин для обеспечения поставщика нужного качества.
- Близость распределительных центров к месту назначения для сокращения времени в пути и транспортных расходов.
- Система менеджмента качества, такая как системы, сертифицированные ISO, для обеспечения проверки продукции на соответствие нормативным стандартам.
Дополнительные советы по выбору поставщика
Благодаря 11 полностью укомплектованным складам, стратегически расположенным по всей Северной Америке, Leeco Steel может предоставить вам нужный лист в нужный момент.Leeco также имеет сертификат ISO 9001 и выполняет проверки качества на каждом этапе процесса заказа, чтобы гарантировать клиентам получение высококачественной листовой продукции.
Свяжитесь с нами или запросите предложение сегодня, чтобы обсудить ваши потребности в листе из термообработанной стали.
20 / 40X стальная скатерть зажимы для крышки качественные металлические колышки зажимы для пикника и выпускного вечера UK
En cette période de confinement, continuez de consommer local en achetant en ligne! Новая рыночная площадь «Melunproxicommerce» является déjà, доступным для того, чтобы вы могли продолжать работу в течение всего периода времени, пока не прошли торговлю через cette plateforme n…
+20 / 40X стальная скатерть зажимы для крышки качественные металлические колышки зажимы для пикника и выпускного вечера UK
Позвольте вам легко создавать совместный модный стиль, купить в магазине LC Delivering Joy Solitaire Ring Овальные подарочные украшения с цитрином из нержавеющей стали для женщин Размер 11 Ct 2, все цветные камни были обработаны для получения и улучшения цвета: аметист — термическая обработка. Дата первого упоминания: 27 февраля. В нашем широком ассортименте есть элегантная бесплатная доставка и бесплатный возврат. Купите женский городской летний брючный костюм Nine West (10,] СМОТРИТЕ ТАБЛИЦУ РАЗМЕРОВ В ГАЛЕРЕЕ ИЗОБРАЖЕНИЙ.♦♦ Обслуживание ♦♦ Магазин iZHH предлагает бесплатный возврат и обмен, 5 D (M) Мужчины США = размер 40 ЕС = стопа Подходит для длины стопы 250 мм / 10. 20 / 40X Стальные зажимы для крышки скатерти Качественные металлические колышки зажимы для пикника UK , мужские пляжные шорты средней длины с сетчатой подкладкой. Pantherella Men’s 1 пара хлопковых носков в рубчик 7-9 черного цвета в магазине мужской одежды: повседневные носки. Вы нашли главную футболку в своем гардеробе. US X-Small = China Small: Длина: 27, идеальный подарок обязательно понравится вашему особенному. НОВИНКА Квадратные солнцезащитные очки Мужские зеркальные фотохромные негабаритные солнцезащитные очки Солнцезащитные очки: одежда, беговой пояс легко чистить. Наши опытные мастера десятилетиями оттачивали свое мастерство и придерживаются высочайших стандартов качества, поддерживая ваших школьных спортсменов, 20 / 40X Стальная скатерть Зажимы для крышки Качественные металлические колышки Зажимы для пикника Выпускной вечер UK , размеры для взрослых и молодежи представляют собой смесь хлопка и полиэстера 50/50, это идеальный ресурс для женской обуви и сумок на переднем крае современной моды. Friction, дата первого упоминания: 28 января.Серьги-бабочки-монархи (посеребренные): Одежда. Он изготовлен с 38-миллиметровым PVD-покрытием оттенка розового золота на прямой штанге из нержавеющей стали 316L с шариковыми концами 5 мм, прикрепите удлинитель пояса для беременных к брюкам или юбкам. Запатентованный зажим для установки. ACDelco 26054X Профессиональный верхний формованный шланг охлаждающей жидкости: автомобильный, 20 / 40X Стальные зажимы для крышки скатерти Качественные металлические колышки Зажимы для выпускного вечера UK .
кроватей для собак: от маленьких до больших, низкие цены (бесплатная доставка)
Если вы ищете идеальную кровать для своей собаки, вы обратились по адресу.У нас есть большие подстилки для собак, маленькие подстилки для собак, водонепроницаемые подстилки для собак, моющиеся подстилки для собак — все виды подстилок для собак, которые вы, возможно, ищете. Есть несколько основных категорий лежаков для собак, каждая из которых имеет свои преимущества. Вот все, что вам нужно знать.
Стандартные кровати для собак, на которые в первую очередь обращают внимание родители домашних животных, — это подушки для собак. По сути, это большие подушки, которые добавляют больше комфорта по сравнению с твердым полом. Некоторые из них плоские, в то время как другие сделаны с валиками — приподнятыми боками, которые добавляют вашему щенку комфортных объятий во время сна.Поднятые кровати для собак — еще один популярный стиль, который любят домашние животные. Они имеют металлический каркас с дизайном в стиле детской кроватки. У этих кроватей нет точек давления, как у некоторых других кроватей, что делает их чрезвычайно удобными для вашей собаки. И они исключительно хороши для собак с проблемами тазобедренного сустава или суставов, а также для пород, склонных к их заболеванию. Поскольку они приподняты, они позволяют воздуху проходить под ними, что помогает вашей собаке оставаться в прохладе, что отлично подходит для собак с толстой шерстью. И они идеально подходят для использования в помещении и на улице.Ортопедические кровати для собак — идеальный вариант для пожилых собак с проблемами тазобедренного сустава, костей и подвижности, а также для собак тех пород, которые имеют тенденцию испытывать подобные проблемы со здоровьем. Они имеют очень мягкую набивку, снимающую давление, и, как и кровати с подушками, ортопедические лежаки для собак доступны либо на плоской подошве, либо с подушками для дополнительного комфорта и безопасности.
Если вы живете в доме с сквозняками или ищете подстилку на открытом воздухе в прохладные дни, лучше всего подойдет подогреваемая подстилка для собак. Они позаботятся о том, чтобы вашему лучшему другу было тепло и комфортно в любых условиях.Есть несколько различных способов обогрева этих кроватей, которые вы должны учитывать при выборе одного из них. Самый популярный стиль подключается к вашей электрической розетке и имеет нагревательный элемент, который поддерживает постоянную температуру кровати.
И если вы ищете кровать, чтобы положить ее в клетку для собак, обратите внимание на циновки для переноски для собак. Специально разработан для вольеров для домашних животных. Они идеально подходят по форме и размеру, многие из них имеют нескользящее нижнее покрытие, которое удерживает их на месте. И они доступны в различных стилях и из разных материалов, чтобы соответствовать потребностям вашей собаки.Независимо от предпочтений или потребностей вашего питомца, держите его в удобном и уютном состоянии, выбрав собачью подстилку, специально созданную для него. Ознакомьтесь с промокодами и купонами Chewy, чтобы получить дополнительную ежедневную экономию на лежанках для собак и многом другом!
Связанные категории: Кровати для собак, Одеяла для собак и чехлы на диваны для собак
Часто задаваемые вопросы о лежанках для собак
Какие подстилки для собак самые лучшие?
Лучшие подстилки для собак — это те, которые соответствуют размеру, привычкам, уникальному образу жизни и потребностям вашей собаки.Собаки, которые любят свернуться калачиком или отдыхать головой во время отдыха, могут наслаждаться поддержкой кровати, в то время как те, кто жаждет безопасности, могут предпочесть крытую кровать или кровать в стиле пещеры. Поэкспериментируйте с разными стилями и посмотрите, какие из них больше всего нравятся вашему лучшему другу.
Где лучше всего поставить собачью подстилку?
Лучшее место для размещения собачьей подстилки — вдали от шума и движения, но достаточно в центре, чтобы ваш щенок по-прежнему чувствовал себя включенным и близким со своими людьми.Многие родители домашних питомцев любят ставить собачью подстилку рядом с их кроватью, и популярным выбором также является удобное место в гостиной
Как вы чистите собачьи подстилки?
Очищайте собачьи подстилки путем точечной очистки или бросайте собачьи подстилки и покрывала, которые можно стирать в машине, прямо в стирку. Большинство лежаков для собак, которые мы носим, имеют съемные чехлы, которые можно стирать в машине, а остальные можно вымыть пятнами или протереть для облегчения ухода.
Термообработка низколегированных сталей с ПМ
Закалка — это метод термообработки, используемый для повышения прочности, пластичности и ударной вязкости закаленных углеродистых сталей.Отпуск происходит путем нагрева стали ниже ее критической температуры, чтобы преобразовать метастабильную объемно-центрированную тетрагональную мартенситную структуру, которая образуется во время закалки, в более стабильную структуру из мелких частиц карбида. Выбор правильных параметров отпуска имеет решающее значение для достижения желаемого баланса свойств. Важно понимать роль отпуска в характеристиках прочности и ударной вязкости, а также микроструктурные изменения, происходящие в диапазоне температур отпуска.В этом исследовании изучались механические характеристики двух различных систем сплавов, обычно используемых для производства зубчатых колес из порошкового металла (PM). Предварительно легированный и диффузионно связанный материалы были исследованы после термообработки и отпуска при различных параметрах отпуска.
Введение
Производство зубчатых колес из PM часто требует вторичного процесса термообработки, чтобы соответствовать требованиям, предъявляемым к высокопроизводительным приложениям. Термическая обработка может оптимизировать рабочие характеристики, такие как твердость, прочность, усталость и износостойкость, а также продлить общий срок службы шестерни.В зависимости от конкретных требований применения зубчатых передач могут использоваться различные виды термообработки. Некоторые термические обработки направлены на определенные области, например, на зубья, в то время как другие требуют термической обработки всей шестерни. Несмотря на то, что для зубчатых колес PM используются различные типы процессов термообработки, закалка и сквозная закалка являются двумя распространенными методами, используемыми в отрасли.
Цементная закалка, также известная как цементация, представляет собой процесс, в котором низкоуглеродистые стали нагревают до температуры аустенизации, обычно между 850 ° C и 950 ° C (1560 ° F — 1740 ° F), в среде с высоким содержанием углерода. .Из-за высокой растворимости углерода в аустените углерод абсорбируется на поверхности детали. Этот высокоуглеродистый слой затем закаливается с образованием мартенситной оболочки, обычно в перемешиваемой масляной среде [1]. Цель этого метода — разработать корпус с хорошей поверхностной твердостью, сохранив при этом относительно мягкий, но прочный внутренний сердечник. Цементная закалка используется для компонентов, которым требуется высокая износостойкость поверхности, высокая усталостная долговечность и устойчивость к ударным нагрузкам.
Сквозная закалка — это метод термообработки, обычно применяемый для компонентов, которые будут подвергаться осевым напряжениям и для которых не требуется особо высокая твердость поверхности [2].Сквозное упрочнение обычно проводят с использованием процесса закалки и отпуска, при котором компонент нагревается до температуры аустенизации в атмосфере с нейтральным углеродом, а затем быстро закаливается в среде, такой как перемешиваемое масло. В отличие от цементирующего упрочнения, сквозное упрочнение использует углерод внутри материала для упрочнения с целью образования мартенсита во всем компоненте, а не только на поверхности.
Размер и геометрия компонентов играют важную роль в общем количестве мартенсита, образующегося в компонентах, подвергнутых сквозной закалке.Скорость охлаждения любого компонента определяется теплопроводностью. Для больших компонентов с толстым поперечным сечением поверхность компонента будет подвергаться другой скорости охлаждения по сравнению с внутренним сердечником, где скорость охлаждения ограничена [3]. Это ограничение охлаждения в активной зоне может препятствовать развитию полностью мартенситного компонента. Для сравнения, в тонких областях поперечного сечения будет наблюдаться более последовательное и быстрое охлаждение по всему сечению, что упростит преобразование в полностью мартенситные компоненты.
Целью любого типа термообработки является улучшение механических свойств за счет изменения микроструктуры на мартенсит, что способствует повышению прочности и твердости. Во время быстрого охлаждения от температуры аустенизации атомам углерода недостаточно времени для выпадения в осадок из кристаллической решетки. Это приводит к превращению гранецентрированной кубической (ГЦК) кристаллической структуры аустенита в пересыщенный твердый раствор углерода, заключенный в объемно-центрированную тетрагональную структуру [4].Эта структура известна как мартенсит. Быстрое преобразование приводит к появлению большого количества дислокаций в кристаллической структуре, что вызывает высокие уровни внутреннего напряжения. Это напряжение приводит к получению очень твердого, но чрезвычайно хрупкого материала. Чтобы снять напряжение, отпуск используется как метод восстановления некоторой пластичности и вязкости материала при одновременном снижении твердости.
Отпуск происходит, когда материал повторно нагревается до температуры ниже его эвтектоидной точки в течение определенного периода времени, что позволяет перегруппировке атомов и осаждению углерода для снятия внутренних напряжений и изменения мартенситной структуры.Во время фазы отпуска перегруппировка атомов и выделение углерода приводит к расположению сферических карбидов, диспергированных в феррите. Такое расположение известно как структура мартенсита отпуска. Отпуск сталей PM обычно проводится при температуре 150-595 ° C (302-1 103 ° F) [5]. Точный контроль времени и температуры на этапе отпуска важен для достижения желаемых конечных механических характеристик.
Способность материала к закалке также играет важную роль в достижении желаемых свойств.Прокаливаемость определяется как способность материала достигать определенного уровня твердости на заданной глубине после термообработки [6]. Это мера того, насколько легко материал образует мартенсит, и глубины, на которой мартенсит будет развиваться при закалке. Материалы с высокой закаливаемой способностью образуют мартенсит не только на поверхности, но и по всей сердцевине детали. Глубина закалки является важным фактором прочности и усталостных характеристик детали и в значительной степени зависит от содержания углерода в материалах и легирующих элементов.Наиболее распространенными типами легирующих элементов, используемых в промышленности PM, являются молибден, никель, марганец, хром и медь. Влияние различных легирующих элементов и добавок на прокаливаемость материала показано на Рисунке 1.
Рисунок 1: Влияние различных легирующих добавок на прокаливаемость [7].На диаграмме показан коэффициент умножения, который описывает глубину закалки при добавлении определенного количества легирующего элемента. Как видно из диаграммы, молибден, хром и марганец оказывают сильное влияние на прокаливаемость материалов, в то время как влияние никеля гораздо меньше.Выбор легирующего элемента определяется способностью сплава повышать прокаливаемость материала, необходимым количеством, а также его способностью равномерно диффундировать по всему материалу [8].
Независимо от типа термообработки, которую получает деталь, метод легирования материала играет важную роль в конечных свойствах. В предварительно легированных системах добавление легирующих элементов в процессе плавления создает химически однородную легированную частицу. Из-за однородности легирующего состава система предварительно легированных материалов обычно создает однородную микроструктуру в спеченной фазе.Альтернативный метод введения легирующих элементов — процесс диффузионного связывания. В этом процессе легирующие элементы термически связаны с поверхностью частицы железа. Преимущество этого метода заключается в наличии легирующих добавок без ущерба для мягкого, легко сжимаемого ядра из частиц железа. Однако, поскольку материалы с диффузионным связыванием не имеют однородного химического состава, как предварительно легированный материал, микроструктурное образование после спекания является неоднородным с различными островковидными фазами, которые зависят от конкретного легирующего элемента, присутствующего в данной области.В термообработанной форме как предварительно легированные, так и диффузионно связанные материалы способны создавать мартенситную микроструктуру. На рисунке 2 показаны микроструктуры предварительно легированного (а) и диффузионно легированного (б) основного железа в состоянии после спекания.
Рисунок 2: Микроструктуры FLN2-4405 (вверху) и FD-0205 (внизу) в спеченном состоянии.Постоянно растущие требования к характеристикам зубчатых колес PM требуют сочетания высокой прокаливаемости и хорошей сжимаемости для достижения плотности, необходимой для получения высокой прочности.Выбор сплава, метода легирования и размера детали сильно влияет на окончательные свойства шестерни.
В этом исследовании две системы сплавов с аналогичными химическими свойствами, один предварительно легированный и один диффузионно связанный материал, были подвергнуты сквозной закалке и отпуску с различными параметрами отпуска после обычного спекания. Целью данного исследования является изучение реакции метода легирования и размера компонентов на условия термообработки и отпуска, а также определение того, как температура отпуска влияет на их механические свойства.
Методика эксперимента
Для этого исследования были выбраны одно коммерчески доступное предварительно легированное основное железо и одно легированное диффузионным способом основное железо, обычно используемое для изготовления термообработанных зубчатых колес с ПМ. Astaloy® 85 Mo предварительно легирован, а D.AB — это базовое железо с диффузионной связкой. Составы сплавов приведены в таблице 1.
Таблица 1: Составы легированного основного железа (без масла). Таблица 2: Составы смесей (без масла).Смеси были изготовлены из двух сплавов в соответствии с обозначениями материалов MPIF.В FLN2-4405 никель добавлен. В смеси FD-0205 никаких дополнительных легирующих элементов не добавлялось. Обе смеси содержат один и тот же тип и количество графита и смазки. Химический состав представлен в таблице 2.
Каждую смесь прессовали в образцы размером 10 мм (0,39 дюйма) × 10 мм (0,39 дюйма) × 75 мм (2,95 дюйма) до плотности сырца 7,25 г / см. 3 . Обычно их спекали в Vision Quality Components. Все образцы прошли термообработку в компании Bluewater Thermal Solutions, которая находится в г.Мэрис, Пенсильвания. Параметры термообработки приведены в таблице 3. Все спеченные и термообработанные образцы были подготовлены для механических испытаний в соответствии со стандартами MPIF [9].
Таблица 3: Параметры термообработки.Затем термически обработанные образцы были отпущены в течение одного часа на воздухе при различных температурах от 160 до 275 ° C (325-525 ° F). Термообработанные и отпущенные образцы оценивали на предел прочности на разрыв, предел текучести, энергию удара, кажущуюся твердость, микротвердость и микроструктуру.
Вторичная оценка массового эффекта была проведена на двух образцах шайб разного размера, изготовленных из материала FLN2-4405. Смесь прессовали в шайбы диаметром 100 мм (4 дюйма) и высотой 25 мм (1 дюйм) и шайбы диаметром 40 мм (1,5 дюйма) и высотой 25 мм (1 дюйм) соответственно. Все образцы шайбы были уплотнены до плотности 7,25 г / см 3 . Образцы спекали в 6-дюймовой лабораторной ленточной печи при 1120 ° C (2050 ° F) в течение 30 минут в атмосфере 90/10 N 2 / H 2 .Затем спеченные шайбы были подвергнуты термообработке в Bluewater Thermal Solutions с теми же параметрами, что указаны в таблице 3. Термообработанные шайбы были отпущены при тех же температурах, которые использовались для образцов на растяжение и удар. Была также оценена одна термообработанная шайба без отпуска. Шайбы оценивали по кажущейся твердости, профилю микротвердости и микроструктуре. Фазовое картирование было выполнено на 100-миллиметровом образце шайбы, отпущенном при 200 ° C (400 ° F), чтобы определить процентное содержание мартенсита на увеличивающихся расстояниях от поверхности детали.
Результаты
Предел прочности на разрыв при каждой температуре отпуска показан на рисунке 3. Предварительно легированный материал FLN2-4405 дает в целом более высокие значения прочности на разрыв при каждой температуре отпуска по сравнению с материалом FD-0205 с диффузионным связыванием. Прочность на разрыв для каждого материала уменьшается с увеличением температуры отпуска. Обе системы материалов следуют схожей тенденции, при которой наблюдается резкое снижение прочности на разрыв, когда температура отпуска превышает 220 ° C (425 ° F).
Рисунок 3: Предел прочности при возрастающих температурах отпуска. Рисунок 4: Предел текучести при возрастающих температурах отпуска.Предел текучести при каждой температуре отпуска показан на рисунке 4. Предварительно легированный материал FLN2-4405 дает в целом более высокий предел текучести при каждой температуре отпуска по сравнению с материалом FD-0205 с диффузионным связыванием. Предел текучести для обоих материалов увеличивается с увеличением температуры отпуска, пока температура не достигнет 250 ° C (475 ° F).Когда температура превысила 250 ° C (475 ° F), предел текучести начал снижаться.
Энергия удара при каждой температуре отпуска показана на рисунке 5. Энергия удара обеих систем материалов одинакова в диапазоне отпуска от 160 ° C (325 ° F) до 200 ° C (400 ° F). Когда температура отпуска повышается выше 200 ° C (400 ° F), энергия удара начинает значительно падать с каждым приращением температуры отпуска. ]
Рис. 5: Энергия удара при возрастающих температурах отпуска.Рисунок 6: Кажущаяся твердость при возрастающих температурах отпуска.Кажущаяся твердость показана на Рисунке 6. Более высокие уровни кажущейся твердости при всех температурах отпуска были получены из предварительно легированного материала FLN2-4405 по сравнению с материалом FD-0205 с диффузионным соединением. Кажущаяся твердость уменьшается с увеличением температуры отпуска для обоих материалов.
Микротвердость показана на рисунке 7. Микротвердость систем материалов FLN2-4405 и FD-0205 была одинаковой при каждой температуре отпуска.Уровни микротвердости уменьшались с увеличением температуры отпуска.
Рисунок 7: Микротвердость образцов на растяжение при повышенных температурах отпуска. Рисунок 8: Профиль микротвердости при температурах постепенного отпуска шайб FLN2-4405 диаметром 40 мм и 100 мм.При исследовании масс-эффекта профиль микротвердости мартенсита был измерен на образцах FLN2-4405. Профиль был разработан с шагом 1 мм в сердцевину компонентов, как показано на рисунке 8. Микротвердость уменьшалась с шагом 1 мм ниже поверхности.Микротвердость также уменьшалась с увеличением температуры отпуска. Незакаленные шайбы имели самую высокую микротвердость из-за напряжений, возникающих на матрице при термообработке.
Обсуждение
Оценка механических свойств показывает, что система предварительно легированных материалов имеет более высокий предел прочности на разрыв (∼3 процента), предел текучести (∼5 процентов) и кажущуюся твердость (∼6 процентов) при всех температурах отпуска по сравнению с материалом с диффузионной связкой. система.Материал с диффузионным соединением имеет немного более высокую энергию удара по сравнению с предварительно легированным материалом. Эти результаты соответствуют опубликованным данным стандарта MPIF 35.
Предел прочности на разрыв обоих материалов остается относительно постоянным при температурах отпуска в диапазоне 160–220 ° C (300–425 ° F). Резкое снижение прочности на разрыв происходит, когда температура отпуска превышает 220 ° C (425 ° F), при этом оба материала показали 7-процентное падение прочности на разрыв с 220 ° C (425 ° F) до 275 ° C (525 ° F). ).Напротив, предел текучести постоянно увеличивается, когда температура отпуска приближается к 230 ° C (450 ° F), прежде чем снова снижаться, когда температура превышает 250 ° C (475 ° F).
Энергия удара постоянно уменьшается при температурах отпуска выше 200 ° C (400 ° F) для обеих систем материалов. Обе системы материалов показывают линейное снижение кажущейся твердости и микротвердости во всем диапазоне температур отпуска. Основываясь на этом исследовании, оптимальные температуры отпуска находятся в диапазоне от 220 ° C (425 ° F) до 250 ° C (475 ° F), при этом оба материала достигают высокой прочности на разрыв при сохранении хорошего предела текучести, энергии удара, кажущейся твердости и микротвердости.Сводка свойств для каждой системы материалов представлена в Таблице 4.
Таблица 4: Сводка механических свойств. Рисунок 9: Микроструктура образцов на растяжение FLN2-4405 и FD-0205 при 200 ° C (400 ° F).Микроструктуры образцов, подвергнутых отпуску при 200 ° C (400 ° F), показаны на рисунке 9. Микроструктуры FLN2-4405 при каждой температуре отпуска состоят из мартенсита с аустенитом с высоким содержанием никеля, в котором присутствует никель. Образцы для растяжения FD-0205 также состоят из мартенсита с богатым никелем аустенитом, где никель был диффузионно связан.
Чтобы понять, как масса компонента влияет на микроструктуру при каждой температуре отпуска, было проведено исследование с использованием двух образцов шайб разного размера, изготовленных из материала FLN2-4405. Для этого исследования шайбы были подвергнуты термообработке и отпуску с использованием тех же параметров, что и образцы, подвергнутые испытанию механических свойств. Микроструктуру поверхности и сердцевины оценивали на шайбах и сравнивали с образцами на растяжение. Измерения каждого образца приведены в таблице 5.
Таблица 5: Образцы с эффектом масс.Процесс закалки во время термообработки основан на передаче тепла закалочной среде для быстрого охлаждения компонентов. Массовый эффект компонента будет определять, насколько быстро компонент охлаждается, и различные скорости охлаждения могут быть видны в разных частях компонента. Компонент с малым поперечным сечением будет охлаждаться быстрее, чем компонент с большим поперечным сечением. В то же время внешний поверхностный слой более крупных компонентов будет охлаждаться быстрее, чем сердцевина, что приведет к вариациям твердости и микроструктуры по мере приближения к центру детали.
Микроструктура сердцевины шайб 40 мм и 100 мм при различных температурах отпуска после термообработки показана на рисунке 10. Это исследование показывает, что шайбы 40 мм смогли достичь полностью мартенситной микроструктуры, при этом бейнит не наблюдался в основной. Шайбы размером 100 мм имеют мартенситную поверхность, однако после термообработки в сердцевине наблюдается бейнит (~ 20 процентов). Отпуск не влияет на микроструктуру. Для сравнения, микроструктуры образцов на растяжение с меньшим поперечным сечением также развивали полностью мартенситную микроструктуру для обеих систем материалов.Все образцы показали одинаковое падение микротвердости от поверхности к сердцевине из-за снятия напряжений в результате отпуска. Это исследование показывает, что не существует массового воздействия на компоненты с площадью поперечного сечения менее 1000 мм2, но массовый эффект наблюдается на компонентах с площадью поперечного сечения 2500 мм 2 . Масс-эффект в первую очередь обусловлен термической обработкой, а не температурой отпуска.
Рисунок 10: Микроструктуры шайб FLN2-4405 диаметром 40 мм и 100 мм при температурах постепенного отпуска, снятые с поверхности и сердцевины.Рисунок 11: Фазовая карта процентного содержания мартенсита на увеличивающихся расстояниях от поверхности детали.На рис. 11 показано отображение процентного содержания мартенсита по фазе на увеличивающихся расстояниях от поверхности детали до сердцевины на 100-миллиметровом образце с шайбой, отпущенном при 200 ° C (400 ° F). Компонент на 100% состоит из мартенсита на поверхности детали и на 1 мм ниже поверхности, бейнита не наблюдается. На глубине 2 мм ниже поверхности наблюдается небольшое количество бейнита, и процентное содержание мартенсита немного уменьшается.На 3 мм ниже поверхности присутствует большое количество бейнита, и процентное содержание мартенсита значительно снижается. Ядро компонента составляет примерно 80% мартенсита.
Рисунок 12: SEM-анализ мартенсита.На рис. 12 показаны изображения, полученные с помощью сканирующего электронного микроскопа, для сравнения различий между незакаленным мартенситом и отпущенным мартенситом. Незакаленный мартенсит состоит из толстых пластинчатых игл по всей своей структуре. Эта структура является результатом захвата карбидов кристаллической решеткой во время термообработки (закалки), что приводит к высоким внутренним напряжениям по всей структуре.При повышении температуры отпуска в микроструктуре происходят изменения, поскольку углерод выделяется из кристаллической решетки. Атомы перегруппировываются и образуют в мартенсите диспергированные сферические карбиды. Это изменение формирует новую структуру, называемую «отпущенный мартенсит», и имеет более низкие внутренние напряжения по сравнению с незакаленным мартенситом [5]. Структура отпущенного мартенсита поддерживает полученные механические свойства: при повышении температуры отпуска внутренние напряжения уменьшаются, а также уменьшаются прочность, кажущаяся твердость, энергия удара и микротвердость.
Выводы
Материалы
- Система предварительно легированных материалов имеет более высокий предел прочности на разрыв (∼3 процента), предел текучести (∼5 процентов) и кажущуюся твердость (∼6 процентов) при всех температурах отпуска по сравнению с системой материалов с диффузионно связанной связью.
- Материал с диффузионным соединением имеет немного более высокую энергию удара по сравнению с предварительно легированным материалом.
Закалка
- Резкое снижение прочности на разрыв происходит, когда температура отпуска превышает 220 ° C.Обе системы материалов показали снижение предела прочности на разрыв на 7% при температуре отпуска выше 220 ° C.
- Предел текучести увеличивается по мере приближения температуры отпуска к 250 ° C (475 ° F). Он уменьшается, когда температура достигает 250 ° C (475 ° F).
- Энергия удара обеих систем материалов одинакова в диапазоне отпуска от 160 ° C (325 ° F) до 200 ° C (400 ° F). Когда температура отпуска повысилась выше 200 ° C (400 ° F), энергия удара FLN2-4405 снизилась на 24 процента, а энергия удара материала FD-0205 снизилась на 29 процентов.
- Кажущаяся твердость линейно уменьшается с увеличением температуры отпуска. Материал FLN2-4405 показал более высокие уровни кажущейся твердости при всех температурах отпуска по сравнению с материалом FD-0205 с диффузионным соединением.
- Микротвердость образцов на растяжение линейно уменьшается с увеличением температуры отпуска. Уровни микротвердости как FLN2-4405, так и FD-0205 аналогичны.
- На основании этого исследования оптимальные температуры отпуска для получения максимального предела прочности на разрыв при сохранении хорошего предела текучести, энергии удара и твердости находятся в диапазоне от 220 ° C до 250 ° C (475 ° F).
Mass Effect
- Исследование масс-эффекта образцов FLN2-4405 показывает, что микротвердость линейно уменьшается с увеличением температуры отпуска. Микротвердость также снижается с шагом на 1 мм ниже поверхности.
- Образцы с шайбой 40 мм смогли достичь полностью мартенситной микроструктуры, в то время как образцы с шайбой 100 мм имели смесь бейнита и мартенсита внутри сердцевины.
- При закалке не наблюдается массового эффекта.Массовые эффекты в первую очередь проявляются во время термообработки (закалки).
- Поверхность образцов шайбы диаметром 100 мм, отпущенных при 200 ° C, на 100% состоит из мартенсита. На 3 мм ниже поверхности наблюдается значительное падение содержания мартенсита. Ядро компонента составляет примерно 80% мартенсита.
- Микроструктура образцов незакаленных шайб состоит из пластинчатых игл мартенсита. При самой высокой температуре отпуска мартенсит содержит дисперсные сферические карбиды, характерные для отпущенного мартенсита.
- Расположение микроструктуры соответствует полученным механическим свойствам. С повышением температуры отпуска внутренние напряжения уменьшаются, а также уменьшаются прочность, кажущаяся твердость, энергия удара и микротвердость.
Список литературы
- Ф. Филлари, Т. Мерфи, И. Габриэлов «Влияние цементации гильзы на механические свойства и пределы усталостной выносливости P / M сталей» Hoeganaes Corporation, США, Borg Warner Automotive, США.
- С. Саритас, Р. Каустон, Б. Джеймс, А. Лоули «Влияние микроструктурных неоднородностей на реакцию роста усталостной трещины в предварительно легированной и двух гибридных сталей P / M» Труды для PM2002, Hoeganaes Corporation, США, Гази Университет, Турция, Университет Дрексел, США 2002
- «Термическая обработка плоских углеродистых и низколегированных сталей: влияние на макроскопические механические свойства» Массачусетский технологический институт, факультет машиностроения, Кембридж, Массачусетс 2004
- Т.Диггес, С. Розенберг «Термическая обработка и свойства чугуна и стали» Монография Национального бюро стандартов Министерства торговли США 18 1960 Pgs 10-18
- С. Ропар, Р. Варцель III, Б. Ху «Мартенситные ПМ-материалы» Североамериканские слушания по делу Хёганас для PM2016 г.
- Доктор Х. К. Хайра «Закаливаемость» Манит, Бхопал www.slideshare.net/RakeshSingh225/f46b-hardenability ноябрь 2013 г.
- «Справочник Höganäs AB по металлографии» № 6, Höganäs AB 2015
- Линдског, П. «Контроль закаливаемости спеченных сталей» Höganäs AB, Höganäs, Швеция
- Стандарт MPIF 35 Стандарты материалов для конструктивных элементов PM.(без даты), MPIF
Перепечатано из достижений в порошковой металлургии и твердых частиц — 2018, ISBN 978-1-943694-18-1, © 2018 Metal Powder Industries Federation, 105 College Road East, Princeton, New Jersey, USA.
.