Расход кислорода при резке металла: нормы расхода пропана
Автор admin На чтение 5 мин. Просмотров 8.1k. Опубликовано
Расход кислорода и пропана на резку металла
Себестоимость процесса резки металла определяет расход кислорода и пропана, суммируемый с оплатой труда резчика. Причем расход окислителя и топлива зависит от технологии термического разделения металлов.
Поэтому мы начнем нашу статью с описания способов резки и дальше рассмотрим расход кислорода при резки труб.
Технологии резки металлов
На сегодняшний день в промышленности используются три типовых технологии термического разделения металлических заготовок:
- Кислородная резка.
- Плазменная резка.
- Лазерная резка.
Первая технология – кислородная резка – используется при разделении заготовок из углеродистой и низколегированной стали. Кроме того, кислородным резаком можно подравнять края кромок уже отрезанных заготовок, подготовить зону раздела стыка перед сваркой и «подчистить» поверхность литой детали. Расход рабочих газов, в данном случае, определяется тратой и топлива (горючего газа), и окислителя (кислорода).
Вторая технология – плазменная резка – используется при разделении сталей всех типов (от конструкционных до высоколегированных), цветных металлов и их сплавов. Для плазменного резака нет недоступных материалов – он режет даже самые тугоплавкие металлы.

Причем качество разделочного шва, в данном случае, значительно выше, чем у конкурирующей технологии. При определении объемов рабочих газов, в данном случае, важен расход кислорода — при резке металла плазмой за горение материала отвечает именно окислитель. А сама плазма используется, как катализатор процесса термического окисления металла.
Третья технология – лазерная резка – используется для разделения тонколистовых заготовок. Соответственно, объемы расходуемых газов, в данном случае, будут существенно меньше, чем у кислородной и плазменной резки, которые рассчитаны на работу с крупными, толстостенными заготовками.
Нормы расчета горючих газов и окислителя
Нормы расхода пропана и кислорода или ацетилена и кислорода или только окислителя рассчитываются следующим образом:
- Норматив
расхода топлива или окислителя на погонный метр разреза (
- После этого к полученной сумме прибавляют произведение все того же норматива расхода (H) на коэффициент потерь (k), связанных с продувкой и настройкой резака.
В итоге, расход кислорода при сварке (или расход горючего газа) считается по формуле:
P = HL x Hk
Причем коэффициент k принимают равным 1,1 (для мелкосерийного производства или штучной резки, когда требуется часто включать и выключать резак) или 1,05 (для крупносерийного производства, когда резак работает почти без перерывов).
Определение норматива расхода газов

Для точного определения объемов расходуемых газов необходимо определить основу формулы — норму, которой определяется расход газа на погонный метр прорезаемого металла, обозначаемую в формуле литерой «H».
Согласно общим рекомендациям нормированный расход равняется частному от допустимого расхода разделяющего аппарата (p) (кислородного, плазменного или лазерного резака) и скорости резания металла (V).
То есть формула, по которой рассчитывается нормированный расход кислорода на резку металла (Н), а равно и любого другого газа, участвующего в процессе термического разделения, выглядит следующим образом:
Н = р/V
Искомый результат подставляют в первую формулу и получают конкретное значение расходуемого объема.
Таблица расхода кислорода при резке труб
Труба (наружный диаметр × толщина стенки), мм | Расход кислорода, м3 |
Ø 14 × 2,0 | 0,00348 |
Ø 16 × 3,5 | |
Ø 20 × 2,5 | 0,00566 |
Ø 32 × 3,0 | 0,0102 |
Ø 45 × 3,0 | 0,0143 |
Ø 57 × 6,0 | 0,0344 |
Ø 76 × 8,0 | 0,0377 |
Ø 89 × 6,0 | 0,0473 |
Ø 108 × 6,0 | 0,0574 |
Ø 114 × 6,0 | 0,0605 |
Ø 133 × 6,0 | 0,0705 |
Ø 159 × 8,0 | 0,119 |
Ø 219 × 12,0 | 0,213 |
Ø 426 × 10,0 | 0,351 |
Ø 530 × 10,0 | 0,436 |
Определение значения допустимого расхода и скорости резания
Используемые во второй формуле операнды p (допустимый расход) и V (скорость резания) зависят от множества факторов.
В частности значение допустимого расхода определяется паспортными данными сварочного аппарата. По сути p равно максимальной пропускной способности форсунки резака в рабочем режиме.
А вот скорость резания – V– определяется исходя из глубины шва, ширины режущей струи окислителя или плазмы, типа разделяемого материала и целой серии косвенных параметров.
В итоге, значение допустимого расхода извлекают из паспорта «резака», а скорость резания находят в справочниках, которые содержат специальные таблицы или диаграммы, связывающие все вводные данные.
И согласно справочным данным допустимый расход кислорода равняется 0,6-25 кубическим метрам в час. А максимальная скорость резания – 5-420 м/час. Причем для лазерной резки характерен минимальный расход (0,6 м3/час) и максимальная скорость (420 м/час): ведь такой резак разделит только 20-миллиметровую заготовку.
А вот плазменный резак «сжигает» до 25 м3/час кислорода и 1,2 м3/час ацетилена. При этом он разделяет даже 30-сантиметровые заготовки, делая разрез на скорости в 5 метров в час.
Словом, в таких расчетах все относительно: чем больше скорость, тем меньше глубина и чем больше расход, тем меньше скорость.
расход кислорода и пропана, технология
Наиболее распространенный способ для осуществления резки металла сегодня – автогенный, его еще называют газовый или кислородный. Его суть сводится к тому, что под воздействием пламени газа, металл нагревается и начинает плавиться, а под воздействием струи кислорода происходит его сгорание, делая узкий паз.
В качестве подогревателя используют ацетилен, пропан-бутан, природный, коксовый газ.
Резка металла может классифицироваться в зависимости от необходимого конечного результата:
Поверхностная газовая резка применяется в случаях, когда необходимо удаление слоев металла, чтобы образовались шлицы, канавки и другие конструктивные элементы.
Разделительный вид предусматривает выполнения сквозного реза, для получения необходимого количества металлических элементов, частей. Прожиг металла для получения глубоких или сквозных отверстий называется резкой копьем.
В независимости от видов резки, технология выполнения данного процесса будет одинаковой. Горение газа обеспечивает температуру от 1000 до 1300 оС, ее достаточно, чтобы расплавить прочную сталь. Во время этого подается сильная струя кислорода, который вступает в реакцию с расплавленными молекулами металла, окисляя их.

В результате этого получается разрез. Кислород подается под большим давлением, Часто оно достигает 12 атмосфер, такая струя даже без подачи огня может разрезать кожу.
Строение режущего аппарата сконструировано таким образом:
- газовая горелка;
- два баллона;
- смеситель;
- регулятор давления;
- шланги.
Газовая горелка состоит из головки с несколькими соплами, в основном достаточно трех. Через два боковых подается горючее вещество, через третий, который размещается посредине, подается кислород. Баллоны предназначены непосредственно для газа и кислорода, в зависимости от объемов предполагаемой работы подбираются соответствующие по вместительности баллоны.

Для обеспечения одного часа непрерывной работы будет расходоваться в среднем 0,7 м3 ацетилена (1 м3 пропана) и 10 м3 кислорода. В целом необходимое количество исходного сырья будет зависеть от плотности металла и необходимой температуры для его нагрева. Сократить расход пропана можно за счет специальных насадок на сопла, которые фиксируют подачу газа в определенном направлении, чем ближе будет подача к кислородной струе, тем возрастет расход топлива.
Шланги необходимы для подачи кислорода и горючего вещества из баллонов в смеситель, их еще называют рукавами. Материал, из которого сделаны шланги – двухслойная резина, между слоями каркас, выполненный из хлопчатобумажной нити. Диаметр – до 12 мм, возможность эксплуатации при температуре воздуха не ниже -35 оС.
Регулятор давления необходим для обеспечения разных режимов и скоростей резки. Подавая меньшее количество топлива можно обеспечить низкую температуру, которая необходима для тонкой стали или металла невысокой прочности, а также сократить расход сырья.
Еще одной важной функцией редуктора является поддержание равномерного уровня давления. Если в процессе резки будет прервана подача газа, металл быстро охладеет и дальнейшая обработка станет невозможной.
Резка металла пропаном и кислородом
Необходимое оборудование

Самым первым резаком было устройство Р1-01, его сконструировали еще в СССР, затем появились более модернизированные модели – Р2 и Р3. Отличаются аппараты размерами сопел и мощностью редуктора. Более современные ручные установки:
- Смена;
- Quicky;
- Орбита;
- Secator.
Они отличаются набором дополнительных функций и производительностью.
Quicky-Е может осуществлять фигурную резку, по заданным чертежам, скорость работы достигает 1000 мм в минуту, максимально допустимая толщина металла до 100 мм. Устройство имеет набор съемных сопел для обеспечения обработки металлических листов или труб различной толщины.

Этот аппарат может работать, используя различные виды горючего газа, в отличие от прототипа Р1-01,который работает только на ацетилене.
Ручной резак Secator имеет более улучшенные характеристики по сравнению с аналогами.

С его помощью можно обрабатывать металл толщиной до 300 мм, это обеспечивают дополнительные насадки, входящие в комплект, они съемные и их можно приобрести дополнительно, по мере износа. Secator может производить следующие виды резки:
- фигурную;
- прямую;
- кольцевую;
- под скосом.
Скорость может регулироваться в диапазоне от 100 1200 мм в минуту, а с помощью встроенной муфты свободного хода обеспечивается плавное перемещение машины по листу металла. Редуктор с воздушным охлаждением обеспечивает более чистую работу и сокращает расход горючего вещества.
Вышеперечисленные модели относятся к ручным, то есть они компактные, управляются с помощью рук мастера. Но для больших объемов обрабатываемого металла работать с такими

установками неудобно и не эффективно. Для промышленного производства применяются стационарные режущие установки — это, по сути, та же технология.
Они представляют собой станок со столешницей, в которую встроен режущий механизм. Работу его обеспечивает электрический
компрессор, для которого необходима электросеть с не менее 380 В и трехфазными розетками. Технология работы моделей стационарных режущих установок ничем, но отличается от ручных. Разница лишь в производительности, максимальной температуре нагрева, и способности обрабатывать металл, толщиной более 300 мм.
Условия для резки металла газом
Газовая резка металла будет эффективна только в том случае, когда температура воспламенения металла будет меньшей, чем температура плавления. Такие пропорции соблюдаются в низкоуглеродистых сплавах, они плавятся при 1500 оС, а процесс воспламенения наступает при 1300 оС.
Для качественной работы установки необходимо обеспечить постоянную подачу газа, поскольку кислороду необходимо постоянное количество теплоты, которая поддерживается в основном (на 70%) за счет сгорания металла и лишь 30% обеспечивает пламя газа. Если его прекратить, металл перестанет вырабатывать тепло и кислород не сможет выполнять возложенные на него функции.
Работа резака, обучение резки металла
Максимальная температура ручных газовых резаков достигает 1300 оС, это достаточная величина для обработки большинства видов металла, однако, есть и такие, которые начинают плавиться при особо высоких температурах, например, окисел алюминия – 2050 оС (это почти в три раза больше чем температура плавления чистого алюминия), сталь с содержанием хрома – 2000 оС, никеля – 1985 оС.
Если металл достаточно не разогрет и не начат процесс плавления, кислород не сможет вытеснить тугоплавкие окислы. Обратная этой ситуация, когда металл имеет низкую температуру плавления, под воздействием горящего газа он может просто расплавиться, так, нельзя применять данный способ резки для чугуна.
Техника безопасности
Осуществление резки металла с помощью газовой установки лучше доверить опытному специалисту, поскольку при неаккуратном обращении последствия могут быть достаточно печальными.
Техника безопасности предполагает выполнения следующих условий:

- хорошая вентиляция в помещении, где будут осуществляться работы;
- на расстоянии 5 метров не должно быть баллонов с газом и прочими горючими веществами;
- работы должны вестись в защитной маске или специальных очках, а также в огнеупорной одежде;
- направлять пламя необходимо в противоположную сторону от источника газа;
- шланги в процессе эксплуатации прибора нельзя перегибать, наступать на них, зажимать ногами;
- если делается перерыв, то следует полностью погасить пламя у горелки и закрутить газовые вентили баллонов.
Соблюдение этих простых условий обеспечит безопасную и эффективную работу по резке металла газовой установкой.
Видео: Работа резака, обучение резки металла
Похожие статьи
Газовая резка металла — технология обработки, устройства, рекомендации
Газовая резка металла (кислородная/автогенная) – процесс разрезания стальных и металлических изделии/заготовок кислородным потоком, который подается из специального аппарата. Суть процедуры раскроя заключается в горении металла, с помощью газовой смеси и кислорода, подаваемых на обрабатываемый элемент. Предварительно изделие нагревается до 1300 градусов открытым пламенем, затем подается кислородная струя, разрезающая металл в соответствии со схемой. Современная технология газовой резки позволяет производить раскрой листа любой конфигурации толщиной до 300 мм, в отдельных случаях до 1000 мм.
Основные методы резки металла газом
Копьевая резка — с помощью данной операции производится обработка нержавейки, чугуна и низкоуглеродистой стали больших диаметров. Суть резки заключается в том, что копье разогревается до температуры плавления и прижимается к разрезаемой заготовке. Метод распространен в области машиностроения и металлургии.
Кислородно-флюсовая резка используется для работы с высоколегированными хромистыми и хромоникелевыми сплавами. Данный способ характеризуется тем, что в струю газа (кислорода) начинает вводится порошкообразный флюс, он служит дополнительным источником тепла.
Воздушно-дуговая резка основана на расплавлении металла посредством электрической дуги. При использовании данного метода газ подается вдоль всего электрода.
Резка пропаном выполняется при необходимости раскроя титана, низколегированных и низкоуглеродистых стальных сплавов.
Оборудование данного типа не может раскроить металл толще 300 мм.
Толщина материала, см | Пробивание, сек. | Ширина реза, см | Расход пропана, м |
Расход кислорода, м3 |
---|---|---|---|---|
0,4 | От 5 до 8 | 0,25 | 0,035 | 0,289 |
1,0 | От 8 до 13 | 0,3 | 0,041 | 0,415 |
2,0 | От 13 до 18 | 0,4 | 0,051 | 0,623 |
4,0 | От 22 до 28 | 0,45 | 0,071 | 1,037 |
6,0 | От 25 до 30 | 0,5 | 0,071 | 1,461 |
Как рассчитать стоимость услуги за метр
При расчете стоимости в рассмотрение принимается: толщина металла, максимальный размер детали, ширина реза, кромка, особенности конфигурации, исходный материал – черный или цветной металл, а также предусмотрена резка под углом. Как правило, формула для расчета принимает во внимание прямой рез, если же она осуществляется по окружности/сектору, тогда используется повышающий коэффициент 2.0. Стоимость одного отверстия = 0,25 стоимости реза 1 п.м. металла.
Расход газа при резке металла
Рабочий диапазон, мм | Резательное сопло NX | Кислород (давление, bar) | Горючий газ (давление, bar) | Кислород (потребление, m3/h) | Горючий газ (потребление, m3/h) |
---|---|---|---|---|---|
3-5 | 000 NX | 1,0-2,0 | 0,5 | 1,5-2,0 | 0,20 |
5-10 | 00 NX | 1,5-2,0 | 0,5 | 2,0-3,0 | 0,30 |
10-15 | 0 NX | 2,0-3,0 | 0,5 | 3,0-3,5 | 0,35 |
15-25 | 1 NX | 2,5-3,5 | 0,5 | 3,5-4,5 | 0,40 |
25-50 | 2 NX | 3,5-4,0 | 0,5 | 4,0-4,8 | 0,40 |
50-75 | 3 NX | 3,0-4,5 | 0,5 | 5,0-6,5 | 0,40 |
75-150 | 4 NX | 3,5-5,5 | 0,5 | 6,5-9,5 | 0,50 |
150-200 | 5 NX | 4,5-5,5 | 0,5 | 10,0-14,0 | 0,60 |
200-300 | 6 NX | 5,5-6,5 | 0,5 | 15,0-19,0 | 0,70 |
Особенности резки в размер
Газовая резка позволяет проводить фигурный раскрой листа. Используя газовый резак, можно получить ровный вертикальный край без рваных швов. Также повысить качество можно применяя трафаретную резку. Среди достоинств метода – мобильность оборудования, благодаря чему можно совершать одинаковые операции по шаблонным задачам.
Преимущества метода газовой резки
- ● быстрота и универсальность
- ● оптимальная стоимость и высокое качество
- ● любой уровень сложности
- ● любая конфигурация реза
- ● возможность работы с металлом разной толщины
Возможность деформации
Деформация — обычное явление, если на металл оказывается термическое воздействие. Исправить дефекты можно с помощью вальцовки, обжига, предварительного закрепления изделия, также не стоит превышать допустимую скорость обработки.
Процесс раскроя металла
● Резка начинается с точки, от которой должен идти разрез.
● Эта точка разогревается до температуры 1000-1300 С. После воспламенения материала пускается узконаправленная струя кислорода.
● Резак плвно ведется по линии (угол — 84-85 градусов), сторона — противоположная от резки.
● Когда линия раскроя достигнет 20 мм, угол наклона меняется на 20-30 градусов.
Устройство ручного газового резака
Устройство инжекторного резака
От чего зависит расход газа:
● квалификации мастера
● технических характеристик оборудования
● вида и толщины разрезаемой детали
● глубины и ширины реза
Расход кислорода и пропана при резке металла
Проверьте исправность манометров. Обратите внимание на герметичность газовых редукторов.Процесс резки- Начинайте резку металла с той точки, от которой должен пойти разрез.
- Разогрейте эту точку до температуры возгорания металла (1000-1300 C). Когда металл воспламенится (поверхность при этом будет выглядеть мокрой) откройте вентиль режущего кислорода и пустите узконаправленную струю.
- Плавно ведите резак кислородный по линии разреза, под углом 84-85° в противоположную сторону от резки. Если толщина метала больше 95 мм, сделайте отклонение на 7-10°.
- После того, как линия разреза достигла 15-20 мм, измените угол наклона на 20-30°.
При правильном выборе скорости перемещения газового резака поток искр и шлака вылетает из разреза прямо вниз, кромки при этом получаются чистыми, отсутствуют подтеки и наплавления.
Если в процессе выполнения работы у вас оборвался кислородный шланг – не паникуйте. Закройте подачу пропана, а затем оба баллона. Исчезнувшее в процессе регулировки пламя нужно разжечь повторно, предварительно закрыв вентили резака.
Техника безопасности при резке и сварке
Разработанные четкие правила техники безопасности позволили сделать процесс контролируемым, жизнь и здоровье резчиков и окружающих стала вне опасности:
- Использование специальной маски с светофильтрами, респиратора и защитного костюма.
- Допуск к работам лиц, достигших возраста 18 лет и прошедших специальный курс по газовому делу, имеющие удостоверение с отметкой на проведение данного вида работ.
- Обмыливание на плотность всех соединений аппаратуры, трубопроводов и арматуры для предотвращения утечки газа.
- Использование специальных тележек и носилок для перемещения отдельных баллонов. Отсутствие ударение баллонов друг о друга при транспортировке.
- Не допускается попадание на кислородный редуктор, вентиль или шланг сжиженного газа, жиров, масла.
- Запрещается открывание замасленными руками редуктора и вентиля кислородного баллона.
- Перед началом работ необходимо выпускать через резак смесь газа и воздуха, образующуюся в шланге. Таким образом предотвращаем появление обратного удара в шланг и редуктор.
- Прогрев металла только сжиженным газом без кислорода строго запрещается.
Класс арматуры. А-IА-III
Диаметр стержней, мм. 12-25
§ 59. Ручная дуговая сварка валиковыми швами
Тип соединения 21 (рис. 60)
Норма на 10 соединений
Диаметр стержней, мм
Масса наплавленного металла, кг
Расход электродов, кг
Класс арматуры. А-I A-II А-III
Диаметр стержней, мм. 8-40 10-40 8-40
Раздел IV. ГАЗОВАЯ РЕЗКА
1. Производственные нормы предусматривают ручную и механизированную резку.
2. Нормы даны для резки листовой стали в нижнем положении, труб – в неповоротном положении. При резке труб в поворотном положении к нормам расхода следует применять поправочный коэффициент 0,87.
3. Нормы разработаны для резки с применением кислорода чистотой 99,5%. При применении кислорода другой чистоты нормы необходимо умножить на поправочные коэффициенты:
Чистота кислорода, % 99,8 99,5 99 98,5 98
Поправочный коэффициент 0,9 1,0 1,1 1,2 1,25
4. При резке одним резаком со снятием кромок за толщину стали следует принимать толщину кромки, кроме случаев, указанных в примечаниях табл. 106 и 113.
5. При резке листовой стали с радиусом кривизны менее 300 мм к нормам необходимо применять поправочный коэффициент 1,1.
6. В § 68 представлены нормы на вырезку отверстий или обрезку концов патрубков, при вварке которых расположение к оси трубы предусмотрено под углом 90°. При вырезке косых патрубков расположение которых к оси трубы будет составлять 45 и 60°, необходимо применять поправочные коэффициенты соответственно 1,2 и 1,16.
7. В табл. 106, 112 даны нормы расхода материалов на 1 м реза. При отсутствии в табл. 107 и 113 необходимого диаметра трубы норма расхода рассчитывается по формуле
НТР=Н1 м шва??lШВА,
где НТР – норма расхода материалов на резку трубы необходимого диаметра, л;
Н1 м шва – норма расхода материалов на 1 м реза определенной толщины, л;
lШВА – длина окружности трубы необходимого диаметра, м.
При отсутствии в табл. 108 и 109 необходимого диаметра трубы норма расхода рассчитывается по указанной формуле с применением поправочных коэффициентов соответственно 1,23 и 1,05.
8. В табл. 99-113 нормы расхода газов приведены в литрах (л). При необходимости получения нормы расхода газов в килограммах (кг) должны быть применены следующие поправочные коэффициенты: для кислорода – 0,00133; для ацетилена – 0,00109; для пропан-бутановой смеси – 0,00194; для природного газа – 0,008.
Глава 9. РУЧНАЯ ГАЗОВАЯ РЕЗКА
§ 60. Резка листовой стали
Норма на 1 м реза
Толщина металла, мм
Расход материалов, л, по видам резки с использованием
Расход кислорода на 1 метр реза
Разновидности термической резки металла.
Рассмотрим три основных способа терморезки. Первый по распространению тип – это кислородно-автогенная резка. Область применения – раскрой листового и сортового углеродистого, низколегированного металлопроката, обрезка лишних выступов и кромок, которые образовались во время литья, подготовка деталей под сварку, разделка металлолома и прочее. Данный способ не применяется для разделения нержавеющих высоколегированных сталей, цветных металлов и чугуна.
Следующий тип – это плазменно-дуговая резка. Область применения – это также раскрой, но в данном случае низко- и высоколегированных сталей, а также алюминия, меди и их сплавов.
И последний тип, который мы рассмотрим в данной статье – это лазерная резка, которая является одним из инновационных методов резки металлов. Этот способ значительно расширяет область применения газовой резки и, благодаря этому, можно эффективно разделять тонколистный прокат, специальный профильный прокат, тонкостенные трубы, как из металлических, так и не из металлических деталей. Расход газового топлива в различных способах (кислород, ацетилен, пропан) на разделение определяется по специализированным таблицам в зависимости от режима резки, а также от толщины разрезаемого металла.
При вышеупомянутых типах резки по видам топлива номинируется расход газов, которые используются для разогрева разрезаемой конструкции, для резки, а также для образования плазмы. Повторим, что к таким относятся: кислород, газы-заменители (пропан- бутан, природный газ и др.), ацетилен, а также азот. Кроме этих газов, используются водород и аргон, но их область и популярность применения не значительна, поэтому включать в содержание статьи мы их не будем.
Во время работы с плазменно-дуговым прибором важно заранее планировать количество сменных специальных электродов (катодов), с циркониевыми или гафниевыми вставками. Нормы расхода данных электродов меняются в зависимости от интенсивности рабочего процесса и в общем, не превышают 4 стержней за одну смену. Более точное нормирование расхода стержней будет указано в инструкции по эксплуатации данного агрегата.
Расход газов на резку металла: нормы.
Расхода кислорода на резку металла, как и расход других газов, рассчитывается по специальной формуле:
Рдет = HL + HКh
И в этом уравнении Н – это нормативы расхода во время рабочего процесса, кубический метр газа на метр реза. L – величина разреза или вырезаемой детали, метр. Kh – это коэффициент, который учитывает множество особенностей рабочего процесса: расход газа на начальном этапе резке, продувка и регулировка, зажигание плазменной дуги, на прогрев металла, и, как правило, он равняется 1.1 при единичном производстве, или 1.05 – при промышленном производстве.
Норма расхода кислорода на резку металла и прочих газов (Н, кубический метр на один метр разреза) во время разделения в зависимости от мощностей оборудования и режима резки, высчитывается по следующей формуле:
H = Р/V
Где Р – это допустимый расход газов, который указан в технических характеристиках используемого оборудования, метр кубический на час, а V – это скорость разделения метр на час.
Основные значения газового расхода по различным диапазонам скорости резки для некоторых типов оборудования, которые можно применять для расчётов крупного масштаба в промышленном производстве, приведены в следующей таблице.
Как происходит резка металла газом
Основные сведения
Наиболее распространенный способ для осуществления резки металла сегодня – автогенный, его еще называют газовый или кислородный. Его суть сводится к тому, что под воздействием пламени газа, металл нагревается и начинает плавиться, а под воздействием струи кислорода происходит его сгорание, делая узкий паз.
В качестве подогревателя используют ацетилен, пропан-бутан, природный, коксовый газ.
Резка металла может классифицироваться в зависимости от необходимого конечного результата:
- поверхностная;
- разделительная;
- резка копьем.
Поверхностная газовая резка применяется в случаях, когда необходимо удаление слоев металла, чтобы образовались шлицы, канавки и другие конструктивные элементы.
Разделительный вид предусматривает выполнения сквозного реза, для получения необходимого количества металлических элементов, частей. Прожиг металла для получения глубоких или сквозных отверстий называется резкой копьем.
Технологический процесс
Строение режущего аппарата сконструировано таким образом:
- газовая горелка;
- два баллона;
- смеситель;
- регулятор давления;
- шланги.
Газовая горелка состоит из головки с несколькими соплами, в основном достаточно трех. Через два боковых подается горючее вещество, через третий, который размещается посредине, подается кислород. Баллоны предназначены непосредственно для газа и кислорода, в зависимости от объемов предполагаемой работы подбираются соответствующие по вместительности баллоны.
Для обеспечения одного часа непрерывной работы будет расходоваться в среднем 0,7 м 3 ацетилена (1 м 3 пропана) и 10 м 3 кислорода. В целом необходимое количество исходного сырья будет зависеть от плотности металла и необходимой температуры для его нагрева. Сократить расход пропана можно за счет специальных насадок на сопла, которые фиксируют подачу газа в определенном направлении, чем ближе будет подача к кислородной струе, тем возрастет расход топлива.
Регулятор давления необходим для обеспечения разных режимов и скоростей резки. Подавая меньшее количество топлива можно обеспечить низкую температуру, которая необходима для тонкой стали или металла невысокой прочности, а также сократить расход сырья.
Еще одной важной функцией редуктора является поддержание равномерного уровня давления. Если в процессе резки будет прервана подача газа, металл быстро охладеет и дальнейшая обработка станет невозможной.
Необходимое оборудование
Самым первым резаком было устройство Р1-01, его сконструировали еще в СССР, затем появились более модернизированные модели – Р2 и Р3. Отличаются аппараты размерами сопел и мощностью редуктора. Более современные ручные установки:
Они отличаются набором дополнительных функций и производительностью.
Quicky-Е может осуществлять фигурную резку, по заданным чертежам, скорость работы достигает 1000 мм в минуту, максимально допустимая толщина металла до 100 мм. Устройство имеет набор съемных сопел для обеспечения обработки металлических листов или труб различной толщины.
Этот аппарат может работать, используя различные виды горючего газа, в отличие от прототипа Р1-01,который работает только на ацетилене.
Ручной резак Secator имеет более улучшенные характеристики по сравнению с аналогами.
С его помощью можно обрабатывать металл толщиной до 300 мм, это обеспечивают дополнительные насадки, входящие в комплект, они съемные и их можно приобрести дополнительно, по мере износа. Secator может производить следующие виды резки:
Скорость может регулироваться в диапазоне от 100 1200 мм в минуту, а с помощью встроенной муфты свободного хода обеспечивается плавное перемещение машины по листу металла. Редуктор с воздушным охлаждением обеспечивает более чистую работу и сокращает расход горючего вещества.
Вышеперечисленные модели относятся к ручным, то есть они компактные, управляются с помощью рук мастера. Но для больших объемов обрабатываемого металла работать с такими
установками неудобно и не эффективно. Для промышленного производства применяются стационарные режущие установки — это, по сути, та же технология.
Они представляют собой станок со столешницей, в которую встроен режущий механизм. Работу его обеспечивает электрический
компрессор, для которого необходима электросеть с не менее 380 В и трехфазными розетками. Технология работы моделей стационарных режущих установок ничем, но отличается от ручных. Разница лишь в производительности, максимальной температуре нагрева, и способности обрабатывать металл, толщиной более 300 мм.
Условия для резки металла газом
Для качественной работы установки необходимо обеспечить постоянную подачу газа, поскольку кислороду необходимо постоянное количество теплоты, которая поддерживается в основном (на 70%) за счет сгорания металла и лишь 30% обеспечивает пламя газа. Если его прекратить, металл перестанет вырабатывать тепло и кислород не сможет выполнять возложенные на него функции.
Максимальная температура ручных газовых резаков достигает 1300 о С, это достаточная величина для обработки большинства видов металла, однако, есть и такие, которые начинают плавиться при особо высоких температурах, например, окисел алюминия – 2050 о С (это почти в три раза больше чем температура плавления чистого алюминия), сталь с содержанием хрома – 2000 о С, никеля – 1985 о С.
Если металл достаточно не разогрет и не начат процесс плавления, кислород не сможет вытеснить тугоплавкие окислы. Обратная этой ситуация, когда металл имеет низкую температуру плавления, под воздействием горящего газа он может просто расплавиться, так, нельзя применять данный способ резки для чугуна.
Техника безопасности
Осуществление резки металла с помощью газовой установки лучше доверить опытному специалисту, поскольку при неаккуратном обращении последствия могут быть достаточно печальными.
Техника безопасности предполагает выполнения следующих условий:
Соблюдение этих простых условий обеспечит безопасную и эффективную работу по резке металла газовой установкой.
Расход кислорода и пропана на резку металла
Поэтому мы начнем нашу статью с описания способов резки.
Технологии резки металлов
На сегодняшний день в промышленности используются три типовых технологии термического разделения металлических заготовок:
- Кислородная резка.
- Плазменная резка.
- Лазерная резка.
Первая технология – кислородная резка – используется при разделении заготовок из углеродистой и низколегированной стали. Кроме того, кислородным резаком можно подравнять края кромок уже отрезанных заготовок, подготовить зону раздела стыка перед сваркой и «подчистить» поверхность литой детали. Расход рабочих газов, в данном случае, определяется тратой и топлива (горючего газа), и окислителя (кислорода).
Вторая технология – плазменная резка – используется при разделении сталей всех типов (от конструкционных до высоколегированных), цветных металлов и их сплавов. Для плазменного резака нет недоступных материалов – он режет даже самые тугоплавкие металлы.
Третья технология – лазерная резка – используется для разделения тонколистовых заготовок. Соответственно, объемы расходуемых газов, в данном случае, будут существенно меньше, чем у кислородной и плазменной резки, которые рассчитаны на работу с крупными, толстостенными заготовками.
Нормы расчета горючих газов и окислителя
Нормы расхода пропана и кислорода или ацетилена и кислорода или только окислителя рассчитываются следующим образом:
- Норматив расхода топлива или окислителя на погонный метр разреза (H) умножается на длину разделочного шва (L).
- После этого к полученной сумме прибавляют произведение все того же норматива расхода (H) на коэффициент потерь (k), связанных с продувкой и настройкой резака.
В итоге, расход кислорода при сварке (или расход горючего газа) считается по формуле:
Причем коэффициент k принимают равным 1,1 (для мелкосерийного производства или штучной резки, когда требуется часто включать и выключать резак) или 1,05 (для крупносерийного производства, когда резак работает почти без перерывов).
Определение норматива расхода газов
Согласно общим рекомендациям нормированный расход равняется частному от допустимого расхода разделяющего аппарата (p) (кислородного, плазменного или лазерного резака) и скорости резания металла (V).
То есть формула, по которой рассчитывается нормированный расход кислорода на резку металла (Н), а равно и любого другого газа, участвующего в процессе термического разделения, выглядит следующим образом:
Искомый результат подставляют в первую формулу и получают конкретное значение расходуемого объема.
Определение значения допустимого расхода и скорости резания
Используемые во второй формуле операнды p (допустимый расход) и V (скорость резания) зависят от множества факторов.
В частности значение допустимого расхода определяется паспортными данными сварочного аппарата. По сути p равно максимальной пропускной способности форсунки резака в рабочем режиме.
А вот скорость резания – V– определяется исходя из глубины шва, ширины режущей струи окислителя или плазмы, типа разделяемого материала и целой серии косвенных параметров.
В итоге, значение допустимого расхода извлекают из паспорта «резака», а скорость резания находят в справочниках, которые содержат специальные таблицы или диаграммы, связывающие все вводные данные.
И согласно справочным данным допустимый расход кислорода равняется 0,6-25 кубическим метрам в час. А максимальная скорость резания – 5-420 м/час. Причем для лазерной резки характерен минимальный расход (0,6 м3/час) и максимальная скорость (420 м/час): ведь такой резак разделит только 20-миллиметровую заготовку.
А вот плазменный резак «сжигает» до 25 м3/час кислорода и 1,2 м3/час ацетилена. При этом он разделяет даже 30-сантиметровые заготовки, делая разрез на скорости в 5 метров в час.
Словом, в таких расчетах все относительно: чем больше скорость, тем меньше глубина и чем больше расход, тем меньше скорость.
Кислородная резка стали средних толщин
Установки для автоматической сварки продольных швов обечаек – в наличии на складе!
Высокая производительность, удобство, простота в управлении и надежность в эксплуатации.
Сварочные экраны и защитные шторки – в наличии на складе!
Защита от излучения при сварке и резке. Большой выбор.
Доставка по всей России!
При кислородной разделительной резке стали в соответствии с технологическими особенностями различают резку металла малых толщин (до 5 мм), средних толщин (5—300 мм) и больших толщин (свыше 300 мм). Такое, деление довольно условно, однако для каждого диапазона разрезаемых толщин существуют общие закономерности.
Наиболее важными технологическими параметрами кислородной резки являются расход режущего кислорода, мощность подогревающего пламени, скорость резки.
Для расчетов расходов режущего кислорода может быть рекомендована следующая формула, полученная на основании результатов обработки данных ВНИИавтогенмаш и зарубежных фирм,
где Vкр — расход «режущего» кислорода, м 3 /с; k2 — коэффициент, учитывающий состояние металла перед резкой (k2 = 0,3 — для проката; k2=0,6 — для литья и поковок толщиной от 0,3 до 0,6 м), kр, kп, kм — см. табл. 26.1.
Подогревающее пламя нагревает поверхностные слои металла до температуры воспламенения в начале резки, а в процессе резки — фронтальную поверхность металла. Мощность подогревающего пламени возрастет с увеличением толщины разрезаемого металла, расстояния между торцом резака и металлом. При резке загрязненного металла мощность пламени необходимо увеличивать. Мощность пламени определяется расходом горючего газа, его родом и соотношением расхода горючего газа и подогревающего кислорода. При кислородной резке в качестве горючего используются газообразные и жидкие углеводороды. При сгорании указанных горючих в смеси с кислородом образуется высокотемпературное пламя.
В табл. 26.2 приведены сведения об основных свойствах горючих газов.
Расходы горючего газа и подогревающего кислорода при резке могут быть определены из нижеследующих зависимостей:
где Vr.r — расход горючего газа, м 3 /с; Vк.п — расход подогревающего кислорода, м 3 /с; δ — толщина разрезаемого металла, м. Значения входящих в приведенные уравнения коэффициентов для разных условий резки приведены в табл. 26.1 и 26.2. Расход железного порошка (qф, кг/с) при резке высоколегированных сталей определяется по формуле:
qф = 0,025δ 1,5 + 0,0017. (26.10)
При заданных расходах газов скорость резки уменьшается по экспоненциальному закону с увеличением толщины разрезаемого металла, так как динамическое воздействие струи на расплав резко сокращается по мере удаления от среза сопла. Скорость резки увеличивается с ростом температуры подогрева металла вследствие возрастания толщины жидкой прослойки металла в разрезе, чистоты кислорода и давления кислорода перед соплом. Повышение давления «режущего» кислорода перед соплом способствует увеличению скорости его потока и его динамического воздействия на окисляемый металл. Наибольшее увеличение скорости потока кислорода (до 90%) наблюдается в интервале давления на входе в сопло от 98 до 2940 кПа, дальнейшее повышение давления кислорода перед соплом от 2940 до 9800 кПа позволяет увеличить скорость кислородного потока лишь на 8 %.
На основании обобщения экспериментальных данных получена следующая зависимость для определения скорости резки:
где v — скорость резки, м/с; δ — толщина разрезаемого металла, м; kд — коэффициент скорости резки, зависящий от давления «режущего» кислорода,
где рk — давление «режущего» кислорода, кПа; кч — коэффициент скорости резки, зависящий oт чистоты кислорода,
где ε — чистота кислорода, %; kт, kм, kр выбираются в соответствии с табл 26.1.
Меньшие скорости резки выбираются при точной вырезке фигурных деталей, наибольшие при прямолинейной разделительной кислородной резке металла в скрап (табл, 26.3).
Волченко В.Н. “Сварка и свариваемые материалы”.
Методика расчета расхода материалов при термической резке
Рассмотрим три способа термической резки металла: газокислородная, плазменная и лазерная как наиболее распространенные.
Кислородно-разделительная резка применяется для раскроя сортового и листового углеродистого и низколегированного метал-лопроката, обрезки прибылей стального литья, обработки кромок под сварку и др. Не применяется для резки нержавеющих и высоколегированных сталей, чугуна и цветных металлов.
Плазменно-дуговая резка применяется для раскроя проката как низкоуглеродистых, так и высоколегированных сталей, а также алюминия, меди и их сплавов.
Лазерная резка значительно расширяет область применения термической резки и является эффективным способом резки тонколистового проката, тонкостенных труб и специального профильного проката из металлических и неметаллических материалов.
Каждый из способов имеет свои технически и экономически обоснованные области применения, но для всех способов существует общая технологическая схема расходования технических газов.
При упомянутых выше способах резки нормируются расходные газы, используемые для подогрева металла, собственно резки или плазмообразования. К таким газам относятся: кислород, ацетилен или его заменители (пропан-бутан, природный газ) и азот. Применение водорода и аргона при резке весьма ограничено и в статье не рассматривается.
При плазменно-дуговой резке необходимо планировать расход специальных сменных электродов (катодов) с гафниевыми или циркониевыми вставками. Нормы расхода таких электродов зависят от интенсивности их эксплуатации и составляют 1-4 шт./смену. Для более точного нормирования их расхода необходимо исходить из требований руководства по эксплуатации соответствующего оборудования. В общем случае норма расхода газа на рез или вырезку детали (Рдет) определяется по формуле:
где Н — норматив расхода газа в процессе резки, м3 на 1 м ре-за; L — длина реза (вырезаемого контура), м; Кн — коэффициент, учитывающий расход газов на начальных этапах резки, на подогрев, зажигание плазменной дуги, продувки и регулировки, может быть принят равным 1,1 при единичном производстве и 1,05 — при серийном.
Норматив расхода газа (H, м3 на 1 м реза) в процессе резки в зависимости от характеристик оборудования и режимов резки определяется по формуле:
где Р — номинальный расход газов согласно техническим характеристикам применяемого оборудования, м3/ч; V — скорость резки, м/ч.
Значения номинальных расходов газов в диапазоне скоростей резки для некоторых видов оборудования, которые можно использовать для укрупненных расчетов, приведены в таблице ниже.
Использование того или иного газа обуславливается требованиями технологического процесса и применяемым оборудованием.
Зависимость номинального расхода газа от толщины и скорости резки практически линейная пропорциональная и необходимое значение легко определяется интерполированием.
Таким образом, при необходимости можно укрупненно, оценочно определить расход газов при различных видах термической резки расчетным путем, исходя из используемого вида оборудования, разрезаемого материала и его толщины.
“>
Резка металла
Сколько баллонов кислорода нужно на резку данного объема металла? Данный вопрос является основополагающим, как при вычислении общих затрат в течение трудового процесса, так и при вычислении себестоимости изготовления детали и производства определённых видов работ. Так как кислород является топливом для резки детали, то норма расхода кислорода на резку металла приобретает ключевое значение, наряду с расходом электроэнергии. Существует несколько способов термического разделения металлов, которые подразделяются в зависимости от способа и вида используемого топлива. Поэтому наряду с кислородной резкой металлов мы в данной статье обратим внимание и на другие способы резки металлических конструкций. Итак, приступим.
Разновидности термической резки металла.
Рассмотрим три основных способа терморезки. Первый по распространению тип – это кислородно-автогенная резка. Область применения – раскрой листового и сортового углеродистого, низколегированного металлопроката, обрезка лишних выступов и кромок, которые образовались во время литья, подготовка деталей под сварку, разделка металлолома и прочее. Данный способ не применяется для разделения нержавеющих высоколегированных сталей, цветных металлов и чугуна.
Следующий тип – это плазменно-дуговая резка. Область применения – это также раскрой, но в данном случае низко- и высоколегированных сталей, а также алюминия, меди и их сплавов.
И последний тип, который мы рассмотрим в данной статье – это лазерная резка, которая является одним из инновационных методов резки металлов. Этот способ значительно расширяет область применения газовой резки и, благодаря этому, можно эффективно разделять тонколистный прокат, специальный профильный прокат, тонкостенные трубы, как из металлических, так и не из металлических деталей. Расход газового топлива в различных способах (кислород, ацетилен, пропан) на разделение определяется по специализированным таблицам в зависимости от режима резки, а также от толщины разрезаемого металла.
При вышеупомянутых типах резки по видам топлива номинируется расход газов, которые используются для разогрева разрезаемой конструкции, для резки, а также для образования плазмы. Повторим, что к таким относятся: кислород, газы-заменители (пропан- бутан, природный газ и др.), ацетилен, а также азот. Кроме этих газов, используются водород и аргон, но их область и популярность применения не значительна, поэтому включать в содержание статьи мы их не будем.
Во время работы с плазменно-дуговым прибором важно заранее планировать количество сменных специальных электродов (катодов), с циркониевыми или гафниевыми вставками. Нормы расхода данных электродов меняются в зависимости от интенсивности рабочего процесса и в общем, не превышают 4 стержней за одну смену. Более точное нормирование расхода стержней будет указано в инструкции по эксплуатации данного агрегата.
Расход газов на резку металла: нормы.
Расхода кислорода на резку металла, как и расход других газов, рассчитывается по специальной формуле:
Рдет = HL + HКh
И в этом уравнении Н – это нормативы расхода во время рабочего процесса, кубический метр газа на метр реза. L – величина разреза или вырезаемой детали, метр. Kh – это коэффициент, который учитывает множество особенностей рабочего процесса: расход газа на начальном этапе резке, продувка и регулировка, зажигание плазменной дуги, на прогрев металла, и, как правило, он равняется 1.1 при единичном производстве, или 1.05 — при промышленном производстве.
Норма расхода кислорода на резку металла и прочих газов (Н, кубический метр на один метр разреза) во время разделения в зависимости от мощностей оборудования и режима резки, высчитывается по следующей формуле:
H = Р/V
Где Р – это допустимый расход газов, который указан в технических характеристиках используемого оборудования, метр кубический на час, а V – это скорость разделения метр на час.
Основные значения газового расхода по различным диапазонам скорости резки для некоторых типов оборудования, которые можно применять для расчётов крупного масштаба в промышленном производстве, приведены в следующей таблице.
Таблица. Номинальный расход газов в диапазоне скоростей резки для некоторых видов оборудования. | |||||||
Виды оборудования | Оптимальный диапазон разрешенных толщин мм | Диапазон скоростей резки м/ч | Номинальный расход газа, м3/ч | ||||
Кислород | Ацетилен | Азот | Природный газ | Воздух | |||
Ручной кислородный резак | 4-60 | 30-6 | 5,0-10,0 | 0,12-0,45 | — | 0,21-0,75 | — |
Машинный кислородный резак | 5-300 | 40-5 | 2,5-25,0 | 0,2-1,2 | — | 0,32-2,04 | — |
Плазменный резак | 1-60 | 200-6 | — | — | 2,5-5,0 | — | 3,0-9,0 |
Лазерная режущая головка | 1-20* | 420-50 | 0,6-3,0 | — | 2,1-12,6 | — | — |
Для низкоуглеродистых, легированных сталей и цветных металлов диапазон 1-10 мм. |
Применение различных газов в качестве топлива для разделительных машин по металлу обусловлено требованиями к применяемому оборудованию и в зависимости от технологического процесса. Зависимость толщины и скорости резки от допустимого расхода газа является прямо пропорциональной и данное значение можно легко и просто определить интерполированием. И поэтому можно укрупнено, оценочно совершить вычисление расхода различных газов независимо от вида термической резки металлов, исходя из размеров разреза, толщины металла, а также мощности оборудования.
В конце важно отметить, что нормирование расхода газов – это одна из важных особенностей, от которых зависит эффективность и скорость рабочего процесса, поэтому не стоит забывать про нормативы расхода, особенно во время разделения металла в огромных масштабах.
как правильно пользоваться пропан-кислород, сварка для начинающих, настроить температуру – Расходники и комплектующие на Svarka.guru

Достоинства и минусы
Газовая резка и сварка металлов обладает многими преимуществами, но нас интересует только резка, имеющая такие плюсы:
- Востребована, когда разрезается металл большой толщины или нужна вырезка по трафарету, а болгарка с криволинейными участками не справляется.
- Газовый аналог гораздо удобнее для работы, имеет малый вес, действует в два раза быстрее, чем оборудование с бензиновым двигателем.
- Пропан по стоимости ниже ацетилена и бензина, так что его использование рентабельнее.
- Кромка среза намного уже, а структура чище, нежели от болгарки или бензинового оборудования.
Недостатки — узкий круг металлов, подверженных аналогичной обработке.
Особенности применения
Чтобы понимать, как правильно резать металл резаком, надо изучить конструкцию и знать, что подобное оборудование не используется для резки сталей с высоким содержанием углерода, т. к. нет возможности создать температуру, способную обеспечить устойчивое плавление. При резке чугунных заготовок или конструкций происходит концентрация графита между зерен металла, что затрудняет работу.


Резак нельзя использовать для разрезания изделий, состоящих из алюминия, меди и сплавов на её основе.
Резка по поверхности
Пользователей, конечно же, интересует такой вопрос — как пользоваться резаком во время фигурной резки. Такая методика выполняется соплом инструмента, при этом расплавленный шлак разогревает металл, но, не превышая температуру плавления. Резак располагается под углом до 80 градусов, а после подачи кислорода угол изменяется в пределах 18—450.
Канавки образуются при регулировке скорости резки, если нужен их больший размер, то меняют угол мундштука и немного замедляют скорость резки, регулируя подачу кислорода. Ширину канавок изменяют путём настройки подачи струи горящего газа через сопло, этот параметр приравнивается как 1 к 6, при этом надо следить, чтобы не было затоков.


Чтобы кромки выемки были чистыми, надо увеличить подачу кислорода.


Соотношение пропана и кислорода
Чтобы правильно резать металлы кислородно-пропановым резаком, надо отрегулировать подачу газов к соплу. Такая регулировка осуществляется по рекомендациям справочников, где имеются таблицы и диаграммы, при отсутствии нужной литературы надо свериться с технологией, указанной в документах на изделие. При отсутствии нормативной документации, используют соотношение одна часть пропана к десяти частям кислорода.
Комплект оборудования
До начала газовой резки или сварки следует тщательно подготовить оборудование:
- Емкости с газами.
- Шланги для подключения.
- Резак.
- Мундштук, имеющий определенные размеры.
- Редукторы регулировки и контроля объема.
Оборудование не зависит от производителя, маркировка вентилей стандартная.
Подготовительные работы
Как надо настраивать резак для резки металла — прежде всего, нужно удостовериться, что изделие находится в исправном состоянии, готово к работе, затем выполняется следующий порядок действий:
- Шланги от баллонов подключаются к резаку, предварительно продув изделие для удаления изнутри посторонних вкраплений.
- Кислород подсоединяется к штуцеру с правой резьбой, а пропан — к штуцеру с левосторонней резьбой.
- Уровень подачи пропана выставить на 0,5, а кислорода — на 5,0 атмосфер.
- Проверяем соединения на предмет утечки, а также работу редукторов и манометров.
Если обнаружены утечки газов, то подтягиваются гайки или меняются прокладки.

Начало работы
Как нужно резать металл газовым резаком — выполнив подготовку, исполнитель приоткрывает вентиль пропана, зажигает струю газа, при этом сопло изделия упирается в поверхность металла. Теперь нужно произвести настройку силы пламени, попеременно добавляя пропан и кислород. После установки оптимальной силы струи горящей смеси, изделие располагается под прямым углом к поверхности детали, сопло располагается не ближе 5 мм.
Если разрез начинается в середине листа, то точку старта устанавливают в начале разреза. Поверхность разогревается до температуры не менее 1000 0C, с виду она как бы намокает, затем увеличивается подача кислорода для образования мощной узконаправленной струи.
Особенности резки
Резак надо вести плавно вдоль линии разреза и следить за углом наклона, который отклоняется на 5—6 градусов против движения инструмента. При толщине металла более 0,95 м отклонение увеличивают, прорезав металл на глубину около 20 мм, угол отклонения опять уменьшается. Как резать резаком, чтобы срез был ровным, мы уже подробно объясняли в предыдущем разделе.
Сколько расходуется газа
Расход газов при резке металла пропаново-кислородным резаком, зависит от толщины конструкции и конфигурации разреза. Для наглядности приводим расположенную ниже таблицу:
Размер заготовки (толщина), мм | Время на отверстие, сек | Размер разреза (ширина), мм | Расход, на м3 реза | |
пропана | кислорода | |||
4,0 | 5—8 | 2,5 | 0,035 | 0,289 |
10,0 | 8—13 | 3,0 | 0,041 | 0,415 |
20,0 | 13—18 | 4,0 | 0,051 | 0,623 |
40,0 | 22—28 | 4,5 | 0,071 | 1,037 |
60,0 | 25—30 | 5,0 | 0,087 | 1,461 |
Расход газов существенно снижается, когда выполняется наплавка или пайка.
Нюансы
Главная задача исполнителя — правильно выдерживать скорость:
- нормальный режим — искры летят под прямым углом относительно поверхности заготовки;
- малая скорость — разлет от исполнителя и угол менее 85 градусов.
После окончания процесса вначале перекрывается подача кислорода, а пропан — отключают в последнюю очередь.


Негативная деформация
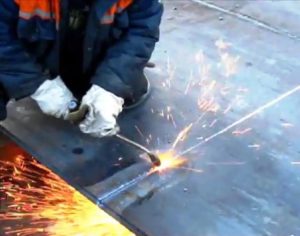
- при неравномерном нагреве поверхности;
- была выбрана высокая скорость движения резака;
- произошло резкое охлаждение места нагревания.
Чтобы исключить возникновение перечисленных факторов на заготовки, их предварительно надежно закрепляют и прогревают, а скорость наращивают постепенно. Если же коробление всё-таки произошло, то вернуть первоначальную форму можно при помощи обжига или отпуска, а листы править на вальцах.
Опасность обратного удара
При неправильном режиме горения струи происходит хлопок и пламя втягивается вовнутрь изделия, что приводит к взрыву, т. к. огонь распространяется по шлангам и доходит до емкостей с газами. Чтобы предотвратить опасную ситуацию, резак оборудуется обратным клапаном, который отсекает пламя и не допускает его распространения.
Правила использования
Они аналогичны технике безопасности при проведении сварки, но имеют специфические дополнения:
- Средствами защиты пренебрегать не рекомендуется, т. к. это приводит к получению травм в виде ожога кожи или повреждения роговицы глаз разлетающимися искрами, поэтому обязательны очки и перчатки с длинными раструбами до локтя.
- Одежда и обувь исполнителя изготавливается из негорючего материала.
- Баллоны с газами располагаются не ближе пяти метров от места проведения резки.
- Пламя резака направляется только в противоположную от шлангов сторону.
- Резка производится в помещениях, оборудованных сильной вентиляцией или на открытых площадках.
При длительном простое оборудования нужно провести профилактические работы, прежде чем использовать резак по назначению.
Техника безопасности
Оборудование относится к категории взрывоопасных, поэтому место выполнения работ нужно снабдить следующими принадлежностями:
- огнетушитель;
- ящик с песком;
- пожарный стенд с соответствующими инструментами.
Каждый исполнитель должен иметь комплект защитной одежды.
Не допускается наличие под защитой одежды из легко возгораемого материала, например, из синтетик, а края рукавов должны плотно облегать тело, чтобы внутрь не попали искры.
Выводы
Перед началом работы исполнители обязаны пройти инструктаж с записью в специальный журнал, к работе допускаются только лица, сдавшие зачеты по знанию теории процесса и практического исполнения резки.
Резка металла газом: основные технические нюансы
Вопросы, рассмотренные в материале:
- Что собой представляет процесс резки металла газом
- Преимущества и недостатки технологии резки металла газом
- Какие газы используются для резки металла
- Основные правила резки толстого металла газом
- Условия резки металла газом и кислородом
Резка металла газом – метод металлообработки, применяемый не только на крупном производстве, но также в быту, сельском хозяйстве, мелкосерийном выпуске. Это по-настоящему универсальный, простой и быстрый способ разрезать толстую металлическую заготовку без длительной настройки оборудования и больших затрат.
Для того чтобы резка металла газом выполнялась правильно, необходимо соблюдать правила, подобрать оборудование и расходные материалы, выполнить остальные условия. О том, как это сделать лучше, читайте в нашем материале.
Что собой представляет процесс резки металла газом
Газовая резка металлов в настоящее время – это достаточно простая технология, при которой работа идет без применения сложной аппаратуры и дополнительных источников энергии. Данный метод используют специалисты для проведения работ в сельском хозяйстве, строительстве и различных видах ремонта. Оборудование для газовой резки металла мобильно, быстро перевозится для использования на другом объекте.
Рассмотрим основной принцип резки с помощью кислорода. Вначале происходит разогрев материала нагревателем в среднем до температуры +1 100 °С. После чего кислород начинает подаваться в зону реза, соприкасается с раскаленной поверхностью и загорается. Стабильная подача кислорода дает мощную струю горящего газа, которая с легкостью режет лист металла.
Для успешной резки газом необходимо, чтобы материал имел температуру горения меньшую, чем плавления. Иначе расплавленный металл будет тяжело убрать из зоны реза, в отличие от сгоревшего.
Следовательно, можно сделать вывод о том, что резка металла газом происходит вследствие его выгорания в зоне действия газовой струи. Основной частью оборудования для резки газом является резак. В нем происходит создание смеси воздуха с газом за счет дозирования и последующее смешивание кислорода с парами жидкого топлива или газами. После чего резак воспламеняет получаемую смесь и дополнительно обеспечивает подачу кислорода в зону реза.
Газовая резка является одним из температурных методов обработки материалов. Ее достоинством стала большая производительность и возможность обрабатывать заготовки практически любой толщины. Один сварщик за смену в состоянии произвести резку нескольких тонн материала. Работники указывают на одно из главных преимуществ – возможность работать вне зависимости от источников энергии. Это особенно важно, когда работа ведется в полевых условиях, где отсутствует какой-либо источник питания.
Рекомендовано к прочтению
В списке металлов, в работе с которыми используется газокислородная резка, есть исключения: алюминий, нержавейка, медь и латунь.
Преимущества и недостатки технологии резки металла газом
Резка кислородом имеет большое количество преимуществ перед иными видами. Они делают ее эффективнее экономически. Но существует ряд ситуаций, когда она просто незаменима.
Достоинствами газокислородной резки являются:
- Возможность обрабатывать заготовки большой толщины.
- Высокая сложность выполняемых резов, например, таких как многоступенчатый.
- Удобство выполнения фасонной обработки материалов, т. е. на заданную глубину, а не только сквозного реза.
- Хорошее качество реза при невысокой себестоимости обработки.
- Высокая производительность.
- Автономность и мобильность оборудования позволяет применять ее в труднодоступных местах, в том числе при сборке/разборке корпусов судов, а также сложных производственных конструкций.
Описываемая технология резки газом, помимо достоинств, имеет и недостатки, к примеру:
- Для ее осуществления сварщику требуется достаточный опыт. Специалистам с низкой квалификацией доступны только простые виды реза, например, прямая обработка тонкого листа металла.
- Опасность возникновения пожара или взрыва. Технология требует тщательных подготовительных мероприятий и последующего соблюдения правил техники безопасности при проведении работ.
- Точность реза не слишком высокая, в особенности при ручной обработке. После его выполнения заготовку, как правило, необходимо дополнительно механически доводить до соответствия ее формы и размеров чертежу.
- Термическое воздействие на заготовку иногда приводит к разным формам деформации, таким как кручение, коробление и пр. Это особенно рискованно при раскрое материала и в меньшей степени при демонтаже конструкций.
Эти недостатки способен решить иной метод – плазменная резка с помощью автоматизированных стационарных аппаратов. Однако они не мобильны и не дают возможности выполнять операции в труднодоступных местах.
Какие газы используются для резки металла
Существует несколько методов классификации газовой резки. Она происходит в зависимости от применяемых газов и прочих особенностей. Из них можно выбрать оптимальный для выполнения той или иной операции или задачи. К примеру, электродуговая резка с кислородом возможна в случае подключения аппаратуры к электрической сети. А обрабатывать низкоуглеродистые стали удобнее газовоздушной смесью с пропаном.
Среди профессионалов наиболее востребованными методами являются:
- Резка пропаном. Резка металла газом, например, пропаном, а также кислородом – пожалуй, самый популярный, но имеющий свои ограничения. Он применяется для низколегированных и низкоуглеродистых сталей, титановых сплавов. В случае наличия в составе материала легирующего компонента или углерода в количестве более 1 %, требуется применение иного метода. Резка возможна и с другими газами: ацетиленом, метаном и пр.
- Воздушно-дуговая резка. Довольно эффективным методом резки является кислородно-электрическая дуговая резка. Плавка происходит при помощи электрической дуги. Остатки же расплава убираются воздушной струей. При выполнении операции таким образом подача кислорода происходит вдоль электрода. К недостаткам этого метода можно отнести неглубокие резы. Впрочем, они компенсируются практически любой шириной заготовки.
- Кислородно-флюсовая резка. Ее особенностью является подача в зону реза дополнительного компонента – порошкообразного флюса. Он дает возможность обрабатываемому металлу стать более податливым в процессе флюсовой кислородной резки. Данный метод применяется для металлов, которые образуют твердоплавкие окислы. В процессе его применения создается добавочный тепловой эффект, при котором струя газа эффективно режет металл. Применяется кислородно-флюсовая металлическая резка для обработки меди и медных сплавов, легированных сталей, железобетона и зашлакованных металлов.
- Копьевая резка. Данный метод применяется для работы с промышленными технологическими отходами, большими массивами стали и аварийными скрапами. Особенностью является увеличивающаяся скорость выполнения работ. Технология включает применение высокоэнергетичной струи газа, что приводит к значительной экономии стальных копьев. Скорость же работы увеличивается быстрым, полным сгоранием обрабатываемого материала.
Расход газов при резке металла можно увидеть в таблице:
На показатель зависимости расхода газа от объемов работ сильное влияние оказывает выбранный метод резки. Нормы резки металла газом при использовании кислородно-флюсового метода содержат информацию о несравнимо меньшем использовании газа, чем при воздушно-дуговом.
Помимо способа обработки, расход газа и кислорода при резке металла зависит от ряда параметров, таких как:
- квалификация сварщика – неопытному специалисту потребуется большее количество газа на один метр заготовки, чем мастеру;
- параметры оборудования и его целостность;
- толщина и марка металла, из которого сделана заготовка;
- характеристики реза – ширина и глубина.
В нижеследующей таблице представлена информация, необходимая для специалиста при выполнении реза пропаном:
Основные правила резки толстого металла газом
Газокислородная резка применяется для раскроя сплавов стали толщиной от 0,5 до 6 см. Вследствие реакции окисления выделяется тепло, которое нагревает и расплавляет металл. А продукты, образующиеся из-за сгорания материала, убираются из зоны реза потоками газа.
Существует ряд требований, которые надо соблюдать в процессе подготовки и выполнения газокислородной резки материалов:
- Перед началом работ необходимо аккуратно очистить поверхность вдоль будущей линии реза на расстояние до 10–15 см. Удалению подлежат остатки старой краски, смазок, масложировых пленок. Если их оставить, то во время резки газом может произойти возгорание, а иногда и взрыв. Помимо них, необходимо избавиться от ржавчины, поскольку ее присутствие замедляет работу по причине теплоизоляционных свойств последней.
- В нижней части заготовки должно быть свободное пространство для выхода струи газа. Размер его невелик – 5–10 см. Однако его отсутствие может привести к турбулентности потока газа из-за его отражения, что крайне нежелательно, к тому же отрицательно влияет на скорость выполнения работы, а также вызывает температурную деформацию изделия.
- Угол отклонения резака от вертикали не должен превышать 5°. В противном случае форма факела искажается, точность падает, качество поверхности реза ухудшается.
- Для выполнения работ сварщику необходимы высокая квалификация и достаточный опыт. Выполнение данного требования будет гарантировать высокую производительность и точность реза.
Газ в зону реза подается с помощью запорных вентилей: одним общим и двумя запорными. Использование двух разных запорных вентилей помогает быстро управлять составом смеси и перенастраивать оборудование для резки металла газом.
На рукоятке резака находятся три патрубка с разъемами. Именно с их помощью в зону реза попадают газ для сварки и резки металла: ацетилен или пропан, кислород, а также жидкость для охлаждения. Давление газов при резке металла устанавливается на редукторе баллона. Оно должно быть ≤ 12 атм.
Подача кислорода в факел резака начинается после поджога последнего. Пропан, сгорая, выделяет тепло, которое нагревает изделие, и начинается его окисление. Процесс происходит достаточно быстро. Заготовка режется (прожигается) струей раскаленного газа (кислорода), одновременно этот же поток выметает частицы расплава в образовывающийся рез.
Условия резки металла газом и кислородом
Рассмотрим обязательные условия успешной обработки материалов методом газокислородной резки:
- Температура горения металла в среде кислорода, которая также обозначается как Твоспл, должна быть ниже Тплав (температуры плавления). Разница температур не должна быть ниже 50 °С. В противном случае возможно вытекание расплава, а также увеличение ширины реза. Например, конструкционные сплавы имеют Твоспл, равную +1 150 °С, в то время как Тплав равна +1 540 °С. Температура плавления снижается с возрастанием количества углерода, что затрудняет обработку высокоуглеродистых сплавов, а также чугуна простым резаком.
- Температура плавления заготовки должна быть выше температуры плавления поверхностных оксидных пленок. Такая пленка является тугоплавкой и не дает кислороду достигнуть поверхности металла, в результате чего его горение не может начаться. Например, температура плавления оксида хрома равна +2 270 °С, а конструкционной стали – +1 540 °С. Специалисты рекомендуют в таком случае использовать порошок флюса. Между ним и поверхностной пленкой начинается реакция, превращающая последнюю в продукт с пониженной температурой плавления.
- Появляющиеся в ходе резки газом оксиды должны иметь высокий показатель жидкотекучести. Иначе расплав будет облеплять края реза, мешая работе и не давая основному материалу гореть. Повысить текучесть оксидов можно с помощью специально подобранных флюсов. Однако такое вмешательство делает резку газом существенно дороже.
- Обрабатываемая заготовка должна иметь невысокую теплопроводность – иначе не будет происходить возгорания материала в зоне реза из-за отведения из него тепла. Работу либо вообще нельзя будет вести, либо она будет постоянно прерываться, из-за чего норма расхода газов при резке металла повысится, а следом снизится качество реза и его точность.
Перед тем как начнется резка металла природным газом, необходимо подготовить следующую аппаратуру:
- Емкости, содержащие газ.
- Шланги для подключения газа.
- Резак.
- Определенного размера мундштук.
- Редукторы, контролирующие объем и регулировку.
Перечисленная аппаратура не зависит от ее производителя и имеет стандартную маркировку вентилей.
До работы допускаются только сварщики, прошедшие инструктаж, о чем произведена запись в специальном журнале, и успешно сдавшие зачеты о знании теории и практики резки.
Почему следует обращаться именно к нам
Мы с уважением относимся ко всем клиентам и одинаково скрупулезно выполняем задания любого объема.
Наши производственные мощности позволяют обрабатывать различные материалы:
- цветные металлы;
- чугун;
- нержавеющую сталь.
При выполнении заказа наши специалисты применяют все известные способы механической обработки металла. Современное оборудование последнего поколения дает возможность добиваться максимального соответствия изначальным чертежам.
Для того чтобы приблизить заготовку к предъявленному заказчиком эскизу, наши специалисты используют универсальное оборудование, предназначенное для ювелирной заточки инструмента для особо сложных операций. В наших производственных цехах металл становится пластичным материалом, из которого можно выполнить любую заготовку.
Преимуществом обращения к нашим специалистам является соблюдение ими ГОСТа и всех технологических нормативов. На каждом этапе работы ведется жесткий контроль качества, поэтому мы гарантируем клиентам добросовестно выполненный продукт.
Благодаря опыту наших мастеров на выходе получается образцовое изделие, отвечающее самым взыскательным требованиям. При этом мы отталкиваемся от мощной материальной базы и ориентируемся на инновационные технологические наработки.
Мы работаем с заказчиками со всех регионов России. Если вы хотите сделать заказ на металлообработку, наши менеджеры готовы выслушать все условия. В случае необходимости клиенту предоставляется бесплатная профильная консультация.
Выбор газа для кислородной резки
Топливные газы издавна использовались для резки и нагрева металла, но что на самом деле производители металла знают об этой очень распространенной части производственного процесса? Достаточно ли мы осведомлены, чтобы сделать лучший выбор топливного газа для кислородной резки?
Кислородная резка — это процесс резки стали в результате химической реакции кислорода с основным металлом при повышенной температуре. Как только кислород смешивается с топливным газом, температура быстро повышается до точки, достаточно высокой, чтобы плавиться и смыть сталь.Процесс кислородной резки — это не что иное, как быстрое окисление, также известное как горение.
Конечно, изготовители всегда беспокоятся о стоимости, а стоимость топливного газа — ацетилена, пропилена или пропана — обычно составляет от 20 до 25 процентов от общих затрат на резку. Но безопасность — это не только стоимость, но и важнее всего.
OSHA Subpart Q 29 CFR 1910.253 содержит ряд жестких и жестких требований к газовой резке и сварке с кислородом. Если рабочие не знают и не понимают этих требований, возможны серьезные ожоги и взрывы.Стандарт 51 Национальной ассоциации противопожарной защиты (NFPA), Кислородно-топливные газовые системы для сварки, резки и Стандарт NFPA 58, Хранение сжиженных углеводородных газов и обращение с ними также охватывают топливные газы. OSHA 49 CFR 195 распространяется на автомобильную транспортировку баллонов со сжатым газом — правила, соблюдение которых обеспечивается министерствами транспорта штата.
Следующее сравнение трех топливных газов применимо к их использованию для резки углеродистой стали, которая плавится при температуре около 2760 градусов по Фаренгейту.Чтобы точно сравнить газы, изготовители должны учитывать их свойства теплопередачи, температуру пламени, потребление кислорода, распределение тепла, безопасное рабочее давление, транспортировку и обращение. И производители должны убедиться, что у них есть правильный размер и стиль наконечника, газовый шланг и настройки регулятора для применения.
Ацетилен
Ацетилен, впервые обнаруженный в 1836 году профессором химии Эдмундом Дэви, используется для резки более 100 лет. В сочетании с надлежащим количеством кислорода (1: 1) он имеет самую высокую температуру пламени — свыше 5 800 градусов по Фаренгейту при температуре нейтрального пламени 5 580 градусов — и самую низкую температуру вторичного пламени.Работа вторичного пламени — большей внешней колбы (обычно синей), окружающей внутренний столб белого пламени — заключается в предварительном нагреве стали для плавления или резания внутреннего (первичного) пламени.
Теплосодержание ацетилена, 1470 БТЕ на кубический фут, является самым низким из всех топливных газов, кроме природного газа. При низкой температуре вторичного пламени газу может потребоваться значительное время для предварительного нагрева при тяжелой резке.
Чем ацетилен так отличается от других топливных газов? Во-первых, газовый баллон — это не открытый баллон.Ацетилен — нестабильный газ, чувствительный к ударам. Цилиндр, наполненный сырым ацетиленом, разлетелся бы на части, если бы его не стабилизировали. Цилиндр изнутри заполнен абсорбентом во время изготовления цилиндра. Обычно этот абсорбент в новых цилиндрах представляет собой силикат кальция, похожий на песок.
Перед операцией заправки ацетиленом цилиндр примерно на 80 процентов заполняется ацетоном, стабилизирующим агентом. Затем цилиндр подключается к коллекторной системе, и газ ацетилен образуется, когда карбид кальция подвергается воздействию воды и медленно вводится в цилиндр для поглощения ацетоном.Ацетон удерживает газ в растворе — жидкости, поглощающей газ.
Ацетон чрезвычайно огнеопасен, поэтому ацетилен никогда не должен превышать 15 фунтов. Если скорость вывода ацетилена составляет более 15 фунтов, ацетон не может выделять газ достаточно быстро, поэтому процесс высасывает ацетон в дополнение к ацетилену. Это серьезная проблема безопасности; ацетон будет медленно растворять шланг топливного газа изнутри, плюс из горелки будет падать пламя. По этой причине никогда не кладите баллон для использования.Перед использованием он должен стоять примерно два часа, чтобы содержимое стабилизировалось.
Безопасный отбор из баллона с ацетиленом составляет не более 1/7 объема баллона; некоторые эксперты снизили это значение до 1/10. Более высокая скорость отбора нарушит баланс ацетона в цилиндре и увеличит возможность отвода ацетона через регулятор и шланг топливного газа.
Когда эти правила не соблюдаются, ацетилен становится вторым по опасности газом в промышленности после кислорода.Это имеет тенденцию к обратным результатам. Если пламя заземлено на основной металл, оно будет казаться погасшим, но на самом деле оно горит внутри факела — явление, известное как ретроспективное воспроизведение. Новые факелы обычно имеют встроенные пламегасители, предотвращающие обратное попадание пламени в шланг, но вспышка горит очень быстро и является очень серьезным заболеванием.
Как и все горючие газы, давление в баллоне ацетилена зависит от температуры окружающей среды. Полный цилиндр при температуре 0 градусов по Фаренгейту имеет манометрическое давление около 85 фунтов на квадратный дюйм; при 60 градусах по Фаренгейту манометрическое давление составляет в среднем 225 фунтов.; при 100 градусах по Фаренгейту манометрическое давление составляет 355 фунтов. Давление выше 300 фунтов. неприемлемо, поэтому баллоны не следует хранить под прямыми солнечными лучами.
Несмотря на эти опасения, ацетилен обладает рядом хороших качеств, которых нет у других топливных газов. Даже с очень экономичным потреблением кислорода (1: 1) он обеспечивает более горячее нейтральное пламя, чем пропилен и пропан. Ацетилен — единственный топливный газ, который можно использовать для газовой сварки. Он отлично подходит для напыления пламенем, наплавки, предварительного нагрева и мягкой пайки меди.Ацетилен лучше работает в мини- и микролаках, чем два других газа, и его можно использовать в горелке с аспиратором воздуха с одним шлангом. Свяжитесь с вашим поставщиком газа для получения информации о требуемом классе топливного газа.
Пропилен
Пропилен быстро стал наиболее предпочтительным кислородным топливом в промышленности. Пропилен, встречающийся в природе как побочный продукт нефтепереработки и переработки природного газа, используется в металлообрабатывающей промышленности с начала 1970-х годов.
Наконечники горелки и регулятор топливного газа для пропилена отличаются от наконечников для ацетилена.Гайка и ниппель изготовлены из CGA-510 (стандарт соединительного фитинга Ассоциации сжатого газа), но манометр не имеет значения 15 фунтов на квадратный дюйм. Два регулятора также подключены по-разному. Пропилен и пропан можно использовать при давлении в баллоне, но манометр должен быть настроен на давление, необходимое для предполагаемого использования. Больше не лучше; это влияет на качество резки.
Пропилен имеет высокое тепловыделение в первичном и вторичном пламени. Вторичное пламя содержит более чем в два раза больше БТЕ, чем ацетилен, и составляет 1 960 БТЕ / фут. 3 Первичное пламя имеет 440 БТЕ / фут. 3 — аналог ацетилена. Общее содержание БТЕ в пламени составляет около 2400 БТЕ, что вдвое больше, чем у ацетилена.
Срок службы пропилена в пять раз дольше, чем у ацетилена. Пропилен при любой температуре имеет самое высокое давление пара и скорость отвода из всех жидких топливных газов. Температура пламени нейтрального кислородного топлива составляет около 5280 градусов по Фаренгейту, что примерно на 300 градусов по Фаренгейту ниже, чем у ацетилена.
Как и в случае с ацетиленом, для пропилена и пропана требуются баллоны, соединенные коллектором, для выполнения больших работ, требующих больших нагревательных головок с большим объемом топливного газа.Жидкое топливо в цилиндре не может выкипеть достаточно быстро, если скорость откачки превышает 90 футов. 3 / час.
Пропилен — очень стабильный газ с небольшой тенденцией к обратному воспламенению. Использование кислорода для нейтрального пламени составляет 3: 1. Благодаря более высокотемпературному вторичному пламени пропилен режется быстрее, чем ацетилен, и обычно образует меньше шлака.
A 100 фунтов. баллон пропилена составляет около 23,4 галлона, или 922 фута. 3 газа при температуре 70 градусов по Фаренгейту
Пропан
Впервые идентифицировано в 1910 г.S. Bureau of Mines, пропан является побочным продуктом переработки природного газа и нефтепереработки. Он более широко используется, чем два других промышленных топливных газа, в таких областях, как автомобильное топливо, домашнее отопление, кухонные плиты, газовые грили и сушка зерна.
Стандарт США для коммерческого пропана — 90 процентов пропана и 10 процентов наполнителей (этан, бутан, этилмеркаптан и пропилен). Одна из его наиболее желательных черт — продукт процесса горения — водяной пар и углекислый газ.
Пропан расширяется на 1,5 процента при повышении температуры окружающей среды на 10 градусов по Фаренгейту. Другими словами, пропан расширится на 15 процентов от 0 до 100 градусов по Фаренгейту. Следовательно, пропановый баллон не может быть заполнен более чем на 80 процентов его внутреннего пространства; ему требуется свободное пространство над жидким пропаном в цилиндре для температурного расширения. Жидкому пропану также требуется место, когда пары пропана отводятся для газа, потребляемого при горении горелки. Сжиженный газ в цилиндре превратится в газовый пар, необходимый для образования пламени.Это непрерывное действие, поскольку давление пара снижается. Как и в случае с пропиленом, горелка сжигает пар, а не жидкость.
Если нагревательный наконечник потребляет более 85 футов газа. 3 / час, два баллона необходимо соединить вместе. Выкипает недостаточно газа, чтобы обеспечить расход, необходимый для скорости горения горелки. Если горелка голодать, она может перегреться.
Нагревательные горелки, в которых от регулятора до горелки используется один шланг, обычно используются с пропаном.Эти факелы могут производить 1 миллион БТЕ. Кислород не нужен. Это очень экономичный способ предварительного нагрева толстых листов и отливок на 900 градусов по Фаренгейту или более за очень короткий период времени.
Пропан продается фунтами в коммерческих баллонах. Он имеет соотношение кислорода к топливу 4: 1 при нейтральном пламени. Температура единственного пламени пропана составляет 1750 градусов по Фаренгейту, а температура его кислородного пламени — 4820 градусов по Фаренгейту.
Этот газ имеет лишь небольшую тенденцию к обратному воспламенению. Его первичное пламя содержит 255 БТЕ / фут. 3 ; вторичное пламя — 2240 БТЕ. Как и пропилен, для пропана требуется режущий наконечник, состоящий из двух частей; наконечники горелки не такие, как для ацетилена, и не подлежат замене.
Только основы
Обратите внимание, что мы рассмотрели только основы. Для сравнения обычных топливных газов на техническом уровне необходимо учитывать множество переменных. Но фундаментальная информация, представленная здесь — своего рода Топливные газы 101 — по крайней мере, должна дать производителям начало.
.Кислородная резка | Статья о кислородной резке в Free Dictionary
(также газовая резка), метод резки металлических деталей, основанный на свойствах металлов, нагретых до температуры воспламенения, при горении в промышленном кислороде. Кислородная резка выполняется путем предварительного нагрева металла до 1200-1300 ° C и направления на него потока кислорода, который прожигает металл и рассекает его. Образующиеся оксиды железа вытекают в расплавленном состоянии и выдуваются из области реза.Метод применяется для резки изделий из низколегированных и среднеуглеродистых сталей толщиной обычно от 1 мм до 200–300 мм (возможна резка стали толщиной до 2 м).
Кислородная резка производится резаком — специальной сварочной горелкой, оснащенной дополнительным устройством для подачи кислорода. Различают ручную и машинную ацетилено-кислородную, водородно-кислородную и бензин-кислородную резку в зависимости от газа, используемого для предварительного нагрева металла. Машинная резка с кислородом обеспечивает высокую точность и чистоту реза с высокой производительностью.Вырезание по трафаретам, специальным направляющим и чертежам, которые можно копировать в любом масштабе, выполняется на станках. Также можно использовать несколько фрез для одновременной резки нескольких лекал. Кислородную резку можно автоматизировать с помощью фотоэлектрических устройств.
Разновидностью кислородной резки является кислородно-флюсовая резка, которая используется для разделения труднообрабатываемых металлов (высокохромистых и хромоникелевых сталей), а также чугуна и алюминиевых сплавов. В этом случае процесс может быть облегчен путем вдувания порошкообразных флюсов в зону резания вместе с кислородом.Помимо сепарационной кислородной резки, при которой поток кислорода почти перпендикулярен поверхности металла, также используется кислородная обработка. В этом случае струя направлена под небольшим углом (почти параллельно) к поверхности металла.
Кислородная резка широко применяется в машиностроении, судостроении, черной и цветной металлургии, строительстве. Помимо кислородной резки, в промышленности широко применяется плазменная резка.
СПРАВКА
Хренов Н.К. Сварка, резка и пайка металлов, 4 изд. Москва, 1973.Большая Советская Энциклопедия, 3-е издание (1970-1979). © 2010 The Gale Group, Inc. Все права защищены.
.Информация о режущих газах,
Хотя
некоторые из вас могут знать Эда как старого пердуна и думать, что это Эд слева, на самом деле он тот, кто находится справа в своем списке, как
канадский менеджер по обучению для Linde (Praxair, Union Carbide, ESAB). Также, когда Эд работал менеджером по сварке в компаниях AGA и Airfgas, США, Эд поставлял кислородное топливо,
от цехов ручной и механизированной резки до многочисленных сварочных цехов в Северной Америке
в восьмидесятые и девяностые годы.В тех цехах представлены сравнения кислородно-топливного оборудования и различия
между имеющимися топливными газами. Эд опубликовал много статей
как на сварку, так и на процессы резки, и он переписал термическую резку лазерно-плазменной
— Раздел Oxy Fuel Cutting в Руководстве по ASM. Девятое издание.
1988.
ТОПЛИВНЫЕ ГАЗЫ БЫЛИ И ЕЩЕ ОСТАВЛЯЮТСЯ, В ОКРЕСТНОСТИ ПРОДАЖИ БОЛЬШОГО ФЕКАЛА, КАК СМЕСИ МИГ-ГАЗА.
Когда оценивая множество различных доступных топливных газов, компании часто смотреть на цену топливного газа, а не на переменные, которые влияют на заявление.
Задавая правильные вопросы помогает решить выбор
правильный топливный газ. Есть пять глобальных топливных газов, которые заслуживают оценки.
[1] Ацетилен.
[2] Пропилен.
[3] Пропан.
[4] Природный газ.
[5] Mapp Gas.
Доступны и другие топливные газы, например, MIG.
сварочные газовые смеси, , вы обнаружите, что эта информация больше связана с маркетинговой рекламой продукции.
чем реальные преимущества БТЕ при резке стали
10 РЕЗКА
ГАЗОВЫЕ ВОПРОСЫ, НАПРАВЛЯЕМЫЕ ПРИ ПРЕДОСТАВЛЕНИИ РЕШЕНИЙ ДЛЯ
ОБРАБОТКИ РЕЗКИ, ПРОИЗВОДСТВА РЕЗКИ И БЕЗОПАСНОСТИ:
[1] Выполните пересчет веса рассматриваемого топливного газа.При оценке удельной стоимости топливного газа проверьте, сколько кубических футов газа фунт топлива, которое доставляет топливный газ. (см. данные о топливе ниже).
[2] Потребление кислорода — важная часть сокращения затрат. Изучите сокращение потребности в кислороде необходимо для выбранного топливного газа. Узнайте, сколько кубических футов кислорода вам понадобится за кубический фут топливного газа?
[3] Вас интересуют детали, которые вы режете искажение.если искажение является проблемой, вы с меньшей вероятностью захотите топливный газ с высоким нагревом во вторичном пламени?
[4] В зависимости от толщины резки время начала резки может съесть трудозатраты. Большое влияние на производство крупносерийной резки, особенно толстых деталей, оказывает время начала. требуется для создания разреза. Имея это в виду, вы должны смотреть на доступное концентрированное тепло. в первичном пламени.
[5] Вы часто будете терять порезы из-за недостатка тепла.Резка этих сталей толщиной более 1 дюйма,> 25 мм, и вы можете ослабьте разрез, потому что во вторичном пламени недостаточно тепла.
[6] Некоторые заводы выполняют и кислородную резку, и сварку. Оцените топливный газ на его способность выполнять сварку и резку.
[7] Возможно, вас беспокоит безопасность хранения топливного газа на вашем предприятии. Изучите, как температура влияет на этот топливный газ.Также изучите возможность возникновения ретроспективных кадров и как некоторые виды топлива разлагаются при относительно низких рабочих давлениях.
[8] Возможно, вы будете резать в изолированном помещении с плохой вентиляцией, и вы хотите знать, насколько опасен топливный газ. Вы всегда должны беспокоиться о утечки из вашего оборудования и шлангов, и очень важно знать, какие топливные газы легче или тяжелее воздуха.
[9] Если вы этого не сделаете много резки и дешевый природный газ доступен в здании, хорошо выбор топливного газа может быть и ежу понятно.Однако, если природный газ замедляет вашу добычу, возможно, пришло время провести анализ затрат на другой топливный газ.
[10} Если вы разговариваете с торговым представителем плазменного или лазерного оборудования, они могут быть предвзятые в своих рекомендациях по резке для приложений на ваш объект. Обычно эти представители и, к сожалению, слишком много компаний, занимающихся резкой, не знают, какой кислород с конкретным топливом. газы и специальные режущие наконечники и рабочее давление.
При резке и Я, конечно, не собираюсь покрывать их все. Это менеджеры или инженеры обязаны просматривать данные о топливном газе на этом и других сайтах. Также важно учитывать различия кислородно-топливного наконечника, поскольку конструкция наконечника будет играть большую роль в производительности и качестве резки. Как и в большинстве процессов, связанных с сваркой, руководство сварочно-резкой несет ответственность за резку. из-за ажиотажа, охватившего эту важную тему.T
Просто подумайте о вопросах, которые вам нужно задать, и вы на пути к выбору экономичный топливный газ, соответствующий вашему бюджету, производственным требованиям и требованиям безопасности.
.Расход газа, станок для лазерной резки, кислород, азот
Расход газа
В Китае один баллон кислорода стоит 8 долларов за баллон, азот — 16 долларов за баллон.
Стандартный баллон с кислородом или азотом — 40 л / баллон.
1. Для резки углеродистой стали мы в основном используем кислород.
Для резки углеродистой стали, чем толще, тем меньше требуется давление кислорода.
Материал | Толщина | Расход воздуха |
CS | 1 мм | 40 л / 40 минут |
CS | 2 мм | 40 л / 50 минут |
CS | 3 мм | 40 л / 60 минут |
CS | 4 мм | 40 л / 70 минут |
CS | 6 мм | 40 л / 80 минут |
CS | 8 мм | 40 л / 90 минут |
CS | 10 мм | 40 л / 110 минут |
CS | 12 мм | 40 л / 180 минут |
CS | 14 мм | 40 л / 200 минут |
CS | 16 мм | 40 л / 220 минут |
CS | 20 мм | 40 л / 220 минут |
2.Для резки нержавеющей стали в основном используйте азот.
Чем толще нержавеющая сталь, тем выше необходимое давление азота.
Материал | Толщина | Расход воздуха |
SS | 1 мм | 40 л / 80 минут |
SS | 2 мм | 40 л / 40 минут |
SS | 3 мм | 40 л / 30 минут |
SS | 4 мм | 40 л / 30 минут |
SS | 6 мм | 40 л / 30 минут |
SS | 8 мм | 40 л / 30 минут |
3.Что касается газа, клиенты в основном используют кислород и азот, также некоторые выбирают компрессорный воздух.
При использовании компрессора воздуха, мы должны убедиться, что компрессор под давлением 13 бар,
нужно иметь в виду:
Во-первых, убедитесь, что в ваших газовых баллонах достаточно воздуха.
Обычно достаточно воздушного резервуара высотой 1,8 м.
Во-вторых, компрессор воздух должен быть сухим и чистым,
без воды и пыли.
В-третьих, тоже нужен осушитель и фильтр
4. Прочие меры предосторожности при использовании станка для лазерной резки
Станок для лазерной резки с волоконным лазером Источник лазера — генератор волоконного лазера,
при резке выделяет отходящие газы, некоторые из них вредны.
Значит, при резке этих специальных материалов нужно иметь дело с отходящими газами, а затем сдавать их.
Источник волоконного лазера относится к категории 4, лазерный луч вреден для человека-мальчика, особенно для глаз.
Работники должны защитить себя, также должны предотвратить пожар.
.