Прокалочные печи
//Прокалочные печи
Электропечь с выкатным подом ПВП с 10.80.9/12М для термообработки деталей из стали и сплавов при температуре до 1200ºС в воздушной атмосфереПечи для прокалки — неформализованное и не корректное в технологическом аспекте обозначение большого спектра печей и печных (нагревательных) агрегатов различного целевого назначения и разной конструкции, появлению которого мы обязаны практическому отсутствию четкой классификации печей.
De facto термин «прокалка» в России и странах постсоветского пространства используется, как условное обозначение термических процессов упорядочения кристаллической структуры нефтяных коксов и/или удаления поверхностной и кристаллизационной влаги, летучих соединений из материала/изделий, иногда сопровождающегося рекристаллизацией, но при отсутствии фазовых переходов. Термин не имеет перевода в технических/политехнических иностранных словарях, а зачастую выдаваемый за «прокалку» формализованный английский термин Calcination (кальцинация, сжигание извести — от лат.
На текущий момент под печами для прокалки (или прокалочными печами) подразумеваются промышленные и специальные печи для термической обработки (термические в разных производствах — для закалки, нормализации, отжига, отпуска, цементации, азотирования и т. д.), печи для обжига материалов и изделий (керамики и клинкера, флотационного серного колчедана и извести, алюминиевых концентратов и минерального сырья), нагревательные печи для удаления поверхностной и кристаллизационной влаги (сушила по классификации Бельского В.И.), лабораторные нагревательные печи и т. д.
Т. е. практически все современные печи и агрегаты исключая целевые нагревательные прокатные/кузнечные печи, используемые для повышения пластичности материала перед его обработкой давлением, печи для перегонки нефти, специфические печи химической промышленности, а также плавильные печи, где происходит фазовый переход материалов из твердого состояния в жидкое.
Конструктивные и теплоэнергетические особенности печей для прокалки.
Впечатляющий спектр применения печей для прокалки в аспекте их позиционирования производителями и продающими компаниями определяет чрезвычайно большое количество конструкций печей и агрегатов, причем традиционные формы рабочего пространства печей для прокалки (печи камерные, печи камерные с выкатным подом, многокамерные, карусельные, барабанные, кольцевые, шахтные печи, печи проходные туннельные и т. д.) в совокупности с устройствами механизации/автоматизации загрузки/выгрузки и технологии процессов обусловили появление различных модификаций печей и агрегатов.
Колпаковая электропечь ППК 86.60/8м для нормализации и отпуска сварных конструкций
Предлагаемые методические печи сопротивления (электрические), по сути, противоречат самой концепции методических печей, где нагреваемый материал/изделие и тепловой поток двигаются навстречу друг другу, что реально выполнимо только в пламенных печах, а в шахтных печах для закалки, как правило используемых для нагрева длинномеров с целью экономии пространства цеха, загрузка может осуществляться снизу в подвешенную на опорах камеру.
Вместе с тем, печи для прокалки имеют одно общее свойство — подавляющее их большинство изготавливается на заводах производителей в виде готовых изделий на металлокаркасе или узлов, собираемых на объекте, причем и пламенные (в основном газовые или жидкотопливные) и электрические печи (сопротивления, индуктивные, дуговые, диэлектрические, электронные, плазменные), позиционируемые, как прокалочные не имеют формализованного по верхнему пределу температурного режима.
//Можно классифицировать следующим образом:
- по виду топлива: газовые и электрические
- по способу теплообмена высокотемпературными с превалирующим теплообменом излучением и низкотемпературными с большей долей теплообмена конвекцией в зависимости от их целевого назначения;
Важно: Теплопередача конвекцией зависит от первой степени разности температур между нагревающей средой и нагреваемым материалом, в то время, как теплопередача излучением — от четвертой степени разности температур.Практически превалирование излучение над конвекцией начинается с температур 800–900 градусов Цельсия, хотя на соотношение долей конвекции и излучения в теплообмене влияют химический состав и физические свойства нагревающей среды, степень черноты нагревающей поверхности/объема (факела пламени горелок, атмосферы в рабочей камере, стенок, свода, пода рабочей камеры, механизмов подачи заготовок/материала/изделий и т. д.).
- по режиму работы периодического и непрерывного действия;
- по форме и пространственному расположению рабочего пространства камерными и проходными, туннельными, камерными с выкатным подом, шахтными, карусельными и т. д.;
- по способу нагрева — прямого и косвенного нагрева, при котором нагреваемое изделие/материал и нагревающая среда (дымовые газы, нагревательные элементы) не контактируют друг с другом;
Справка: В пламенных печах косвенного нагрева нагревающие газы из горелок/форсунок уходят в систему теплообменных труб, передающих тепло нагреваемому материалу/изделию конвекцией и излучением в долях, определяемых температурой стенок теплообменной системы. - по способу использования излишков тепла регенеративными и рекуперативными;
- по нагревательной среде рабочего пространства окислительными, восстановительными, безокислительными и вакуумными.
Важно: Вне зависимости от способа установки все печи для прокалки, как и плавильные, нагревательные, химические и т. д. печи имеют металлический каркас, отчасти нивелирующий негативы теплового расширения и риски разрушения теплоизолирующего покрытия рабочего пространства с интегрированными в него нагревательными/нагревающими устройствами/элементами (индукторами и ТЭНами электрических печей, горелками и форсунками пламенных печей и т. д.). Этот демпфирующий тепловые и механические нагрузки каркас может собираться «по кладке» рабочего пространства или же быть основой для теплоизолирующего покрытия, укладываемого/настилаемого изнутри металлического корпуса нагревательной камеры.
В пламенных печах для прокалки тепло отходящих газов используется для нагрева первичного/вторичного воздуха, подаваемого в топливные горелки, подогрева топливной смеси (рекуператоры и регенераторы) и/или нагрева пара/воды для собственных нужд производства в котлах-утилизаторах. В подавляющем большинстве конструкций электрических печей для прокалки полезная тепловая энергия безвозвратно уходит при загрузке/выгрузке, через теплоизоляцию корпуса и по тепловым мостам, формируемым загрузочными механизмами.
Основной задачей разработчиков конструкций печей для прокалки является максимально возможное повышение КПД печи за счет повышения эффективности теплообмена и снижения объемов тепловых потерь.
Важно: Различают коэффициент полезного действия рабочего пространства печи (отношение полезной тепловой энергии ко всей тепловой энергии, вводимой в рабочее пространство), технологический КПД (отношение полезной тепловой энергии в технологическом процесе к общей тепловой энергии, затрачиваемой на выполнение технологического процесса) и энергетический КПД, определяемый отношением тепловой энергии, использованной печью/агрегатом, в том числе энергии, которая аккумулируется/преобразуется в регенераторах, рекуператорах и котлах-утилизаторах, к всей затраченной энергии (электрической, тепловой). КПД печей непрерывного действия, как правило, больше КПД печей периодического действия, КПД электрических печей выше КПД пламенных печей и т. д. В целом печи для прокалки могут иметь КПД от 8–10% до 75%, хотя некоторые производители искусственно завышают эту величину до 85–90% с целью увеличения продаж.
В пламенных печах эффективность и полноту сгорания топлива (жидкого или газового) повышают:
- подогревом топлива используемого для горения воздуха, что позволяет снизить порог потенциальной энергии компонентов топливной смеси, определяющий возможность самопроизвольного протекания окислительных реакций;
Важно: В любых топливных печах подача воздуха для горения строго дозированная, а его нагрев контролируется, причем в ряде случаев при избытке воздуха его не подогревают, чтобы исключить неконтролируемое повышение температуры горения и, как следствие потребность еще в больших объемах подаваемого воздуха. - искусственным повышением степени черноты факела горелок для увеличения доли излучения в теплообмене; формированием турбулентного потока нагревающих газов и нагревательной атмосферы в рабочем пространстве, что повышает интенсивность теплообмена;
- преднагревом теплоизолирующей кладки, которая становится активным участником теплообмена с нагреваемым материалом/изделием;
- повышением давления в рабочем пространстве, что позволяет снизить температуру технологического процесса.
Эффективность электрических печей для прокалки (в основном сопротивления) повышают варьированием давления/температуры, использованием теплоизолирующих материалов за нагревающими элементами с большой отражающей способностью или отражающим покрытием, снижением тепловых потерь при загрузке/выгрузке и т. д.
Огнеупорные материалы печей для прокалки.
Для теплоизоляции рабочих пространств печей для прокалки используют огнеупорные материалы различного химического состава, теплотехнических и механических свойств, определяя приемлемость того или иного материала не по показателю огнеупорности (температуре начала размягчения материала под действием собственной массы), а по температуре начала деформации материала под нагрузкой 2 кгс/мм2. К дополнительным характеристикам, определяющим преимущества/недостатки огнеупорного материала относятся:
- гомогенность и дисперсность микро- и макроструктуры, влияющие на трещиностойкость, механические свойства, пористость, шлакоустойчивость;
- термическая стойкость, определяющая стойкость к нарушению целостности при колебаниях температуры; коэффициент линейного температурного расширения, характеризующий постоянство объема;
- шлакоустойчивость — способность противостоять окислительному воздействию шлаков и нагревающих газов; теплоемкость, характеризующая объемы тепловой энергии, необходимой для разогрева кладки;
- теплопроводность, ответственная за равномерное распределение температур в слое теплоизолятора;
- электропроводность, которая становится весомым критерием при высоких температурах в рабочем пространстве печи;
- технологичность, определяющая не только трудоемкость работ по кладке, расход материала, но и общий объем пустот/несплошностей и проблемных мест, заполняемых или не заполненных огнестойкими растворами/бетонами.
Прокалочные печи, печь для прокалки
Нагрев
В зависимости от требований нагрев в печах для прокалки может быть как газовый так и электрический. Поскольку в России, Беларуси, Украине и Казахстане на абсолютное большинство средних и крупных предприятий газифицированы, сразу оговоримся, что дальше речь пойдёт о газовой системе нагрева. К тому же статистика показывает, что проходные прокалочные печи целесообразно применять на производствах выпускающих более 800 тонн отливок год получаемых с применением технологии ЛВМ. При меньших объёмах производства имеет смысл рассмотреть применение камерных печей для прокалки или печей для нагрева с выкатным подом.
Нагрев в проходных печах для прокалки производится с помощью скоростных импульсных или рекуперативных газовых горелок. Печь делится на несколько температурных зон в зависимости от требований. Первая зона обычно имеет температуру 400-500 °C, а последняя зона 900-1200 °C. В последней зоне обычно находится несколько опок с формами готовыми к одновременной выдаче или последовательной с кратким промежутком времени.
Температура в зонах контролируется автоматически и поддерживается соответствующими интервалами работы горелок и регулированием температуры в каждой зоне. Для правильной пропорции газа и воздуха в случае изменения температуры воздуха предусматривается измерение давления сгорающего воздуха.
Центральный рекуператор нагревает воздух горения приблизительно до 450 °C, в зависимости от нагрузки. При этом необходимо учитывать, что каждые 100 °C подогрева воздуха в рекуператоре снижают расход газа в среднем на 4.82%.
Более старые газовые проходные печи для прокалки, широко применяемые на сегодняшний день на предприятиях постсоветского пространства, и не использующие систему рекуперации, показывают существенно более высокие затраты, которые в конечном итоге чувствительно сказываются на цене продукции. На месте подключения газа к печи устанавливается газораспределительная установка с необходимыми предохранительными элементами, включая счётчик для измерения расхода газа.
Металлическая конструкция
Металлоконструкции прокалочной печи изготовлены из стальных прокатных профилей и стального листа. Части подвергающиеся воздействию высоких температур изготовлены из жаростойкого сплава. В корпусе так же могут предусматриваться уплотняемые технические проемы для технического обслуживания. В зависимости от доступных площадей возможна установка рекуператора на крышу печи.
Изоляция прокалочной печи
Внутренняя поверхность свода и стен печи, заслонок, а так же дымоотводящие каналы изолированы современными материалами из керамических волокон.
Преимущества керамоволокнистых модулей:
— низкое аккумулирование тепла при нагреве и охлаждении;
— низкая теплопроводность;
— практическое отсутствие ремонтов, экономия на затратах;
— быстрый разогрев и остывание, повышение производительности;
— срок службы керамоволокнистых блоков до 20 лет.
Изоляция рабочих тележек выполняется многослойной из современных материалов, которые особенно подходят для высоких температур и больших механических нагрузок: кальций-силикатных плит, лёгкого изолирующего и твёрдого термобетона. Дополнительно для повышения износостойкости пода в рабочей поверхности рабочего слоя футеровки тележек могут использоваться металлические части из жаропрочного металла.
Система транспортировки форм
Система транспортировки форм в проходной печи для прокалки и вне ёё происходит при помощи тележек. Установка форм на тележки производится при помощи крана или может выполнятся промышленным роботом при автоматизации литейного производства. В последнем случае, проходная печь для прокалки форм поставляется обычно в комплекте с двумя промышленными роботами, обеспечивающими синхронизированную работу с печью и подключённые с общей системе управления печью.
В печи для прокалки обычно постоянно находится не менее 12 рабочих тележек. Как минимум три из которых находятся в последней зоне и готовы в любой момент выдать формы под заливку. Вне прокалочной печи обычно находится ещё 6-8 дополнительных рабочих тележек, с которыми производятся работы (загрузка/разгрузка) или которые находятся в камере охлаждения с уже залитыми формами.
Перемещение рабочих тележек в печи обеспечивается с помощью зубчатой рейки и электродвигателя. Движение всех тележек в печи осуществляется одновременно – так, если одна тележка входит в печь, то другая из неё выходит.
На каждой стороне печи установлено по одной вспомогательной тележке, имеющих свой привод с электромотором и своё управление. Рабочие тележки из печи заезжают на вспомогательную тележку. Далее с них либо снимается форма и подаётся на заливку либо заливка происходит сразу на тележке, например в случае автоматизации литейного производства.
После этого тележка с залитыми формами перемещается на позицию перед камерой охлаждения. С помощью транспортёра тележка проходя через камеру охлаждения возвращается на позицию разгрузки и установки на неё новых форм. Вспомогательная тележка транспортирует загруженную рабочую тележку до входа перед печью.
Транспортировка всех тележек автоматизирована и синхронизирована. Оператор имеет возможность настройки такта движения тележек по времени в зависимости от готовности металла к заливке.
Камера охлаждения
Нагретые тележки с опоками или без них охлаждаются в камере установленной параллельно с прокалочной печью. Охлаждение в камере производится при помощи вентиляторов.
Дымоотводящие каналы
Дымоотводящие каналы на печи для покалки изготовлены из стальных профилей и листового металла. На листовой металл прикреплена изоляция. Каналы покрашены термостойкой краской. На соединениях фланцах предусматривается уплотнение керамической ватой.
Дымовые газы при выходе из печи попадают в дымоотводящий канал, в котором находится центральный рекуператор, предварительно нагревающий воздух для горения. Необходимо учитывать, что в формах не должно находиться модельного воска или его содержание должно быть минимальным.
В печи измеряется давление. Сигнал давления преобразуется в измерительном устройстве с преобразователем в сигнал напряжения. Сигнал направляется в регулятор давления в PLC, которого открывает и закрывает клапан в дымоотводящем канале. В печи автоматически поддерживается избыточное давление.
Система управления и контроля
Управление температурой, а так же контроль всех других параметров и функций прокалочной печи выполняется программируемым логическим контроллером (PLC).
Простая в управлении информационная панель, располагается на лицевой стороне главного щита управления и подключена к PLC. Все оборудование для управления и регулирования печи (ручной выключатель, предохранители, входные/выходные контакторы, переключатели, сигнальные лампы, гудок) размещаются в главном электрощите управления, который находится в отдельном помещении в относительной близости от проходной прокалочной печи. Система регулировки имеет возможность от сигнала термоэлементов в своде печи выполнять автоматическую регулировку температуры. Защита от превышения максимальной температуры в печи предусматривается при помощи независимого чувствительного элемента и предохранительного регулятора температуры.
PLC подключается к персональному компьютеру, на котором инсталлирована специальная программа контроля (мониторинга), обеспечивающая визуализацию всего процесса и сохранение данных в специальных файлах. При этом в случае автоматизации участка программа контроля так же обеспечивает управление промышленными роботами и обеспечивает их синхронную работу с проходной прокалочной печью.
Прочее
Смотрите так же по теме:
Камерные печи для прокалки
Печи для нагрева с выкатным подом
Автоматизация литейного производства
печи для просушки и прокалки электродов и флюса печи для просушки и прокалки электродов и флюса
×
Как правильно искать на сайте, рекомендации
Пример: | Как не нужно искать | |
Вводить одно КЛЮЧЕВОЕ СЛОВО |
электрод индикатор центрифуга дозатор |
вместо запроса «комбинированный рН-электрод для измерений в микропланшетах корпус стекло» (!!! Не использовать фразы из нескольких слов / и сложносоставные запросы) |
Водить КОРЕНЬ слова без окончаний |
||
Ввести СИНОНИМ (КОРЕНЬ слова синонима) |
||
оч | вместо запроса «особо чистый» | |
При поиск «Квалификации химических реактивов» использовать сокращения: | хч | вместо запроса «химически чистый» |
Для поиска по «Квалификации химических реактивов» можно перейти к подбору : по характеристикам раздела «Химические реактивы» | чда | вместо запроса «чистые для анализа» |
тех | вместо запроса «технически» | |
На странице категории воспользоваться «Фильтром характеристик, в каждой категории есть вверху кнопка: Перейти к подбору по характеристикам нажимая на которую страница прокручиваться до списка «Характеристик» данной категории.![]() |
||
Прокалочные печи — Справочник химика 21
Расчет барабанной прокалочной печи [c.194]На сушильно-прокалочной установке размещены агрегаты различных конструкций. Применение той или иной конструкции определяется характером вырабатываемой продукции для микросферической — сушильные и прокалочные колонны, для шариковой — конвейерные или шахтные сушилки и шахтные прокалочные печи, для таблетированной — сушильные барабаны. [c.137]
Над прокалочной печью расположен загрузочный. бункер, внизу шахту замыкает распределительное (разгрузочное) устройство.

Микросферический силикагель сушат в сушильной колонне — в полете распыляемой суспензии, а шариковый — на ленте конвейерной сушилки. Прокаливание микросфер проводят в прокалочной колонне в кипящем слое, а шариков — в прокалочных печах. [c.121]
Прокалочная печь для прокаливания шариковых катализаторов и адсорбентов представляет собой квадратную шахту из нержавеющей жароупорной стали (рис. 35), разделенную на четыре зоны предварительного подогрева, подогрева, прокаливания и охлаждения. Первая и последняя зоны имеют трубчатое устройство, обе средние (подогрева и прокаливания) — полые. [c.139]
Обезвоживание гидрогеля. Сушат катализатор в непрерывно действующих сушилках микросферический — методом распыления суспензии в вертикальную сушильную колонну, шариковый — на горизонтальной конвейерной сушилке, в которой катализатор движется на сетчатой ленте. Сушка суспензии протекает в восходящем потоке дымовых газов, на лепте конвейерной сушилки — в паровоздушной смеси. Микросферический катализатор прокаливают в периодически действующих прокалочных колоннах, шариковый — в прокалочных печах непрерывного действия. [c.96]
Загрузка прокалочных печей автоматизирована следующим образом. На печах установлен автомат, регулирующий работу элеватора и тем самым поддерживающий постоянный уровень в печах. В загрузочном патрубке подвешен свободно качающийся металлический стержень со скобой. При повышении уровня в патрубке стержень под действием веса катализатора перемещается в верхнее положение до тех пор, пока скоба одним концом не нажмет кнопку стон магнитного пускателя — элеватор останавливается. По мере понижения уровня стержень под действием собственного веса стремится занять вертикальное положение, а скоба другим концом нажимает кнопку пуск — элеватор включается в работу. Таким образом уровень в прокалочных печах все время поддерживается постоянным. [c.151]
Прокаливание шарикового катализатора осуществляют в печах шахтного типа. Высушенный катализатор из бункера сушилок вертикальным элеватором поднимается на верх прокалочной печи печь всегда должна быть заполнена катализатором. С момента поступления катализатора в прокалочную печь до поступления его в зону прокаливания проходит 26 ч. За это время катализатор постепенно нагревается дымовыми газами с 125 —160 до 750° С. В зоне прокаливания при температуре около 780° С катализатор находится 20 ч, в зоне охлаждения и до выхода из печи — 26 ч, постепенно охлаждаясь до 60—75° С. Следовательно, общее время пребывания катализатора в прокалочной печи составляет 72 ч. [c.88]
На третьем этапе составляют тепловой и материальный балансы прокалочной печи, из которых устанавливают требуемое количество горячего и холодного воздуха, а также топлива, подаваемых в прокалочную печь, и другие материальные и тепловые потоки, в том числе потери в окружающую среду в зависимости от производительности печи, влажности и выхода летучих веществ из кокса, толщины слоя кокса на подине, температуры топочного пространства, скорости вращения подины. [c.204]
Пылью называют мелкораздробленные твердые вещества, способные находиться в воздухе длительное время во взвешенном состоянии и проникать в дыхательные органы человека. В производстве катализаторов и адсорбентов пыль образуется при различных производственных процессах а) при разгрузке крытых вагонов п открытых платформ с силикат-глыбой, гидроокисью алюминия п эпсомитом б) при дроблении силикат-глыбы, помоле глинозема и подаче гидроокиси алюминия в реактор в) при помоле алюмосили-катной крошки шарикового катализатора на аэробильной мельнице и транспортировании молотого катализатора или адсорбента г) при загрузке и выгрузке катализаторов и адсорбентов из прокалочных печей и колонн д) во время чистки и ремонта аппаратуры. [c.162]
Сжигание летучих веществ в печи позволяет в значительной степени оградить прокаливаемый материал от угара и сэкономить топливо. Для сжигания летучих веществ предложены следующие способы и конструктивные решения 1) подача воздуха непосредственно в ту область печи, где наблюдается наиболее интенсивное выделение летучих веществ 2) возврат части дымовых газов в прокалочную печь в качестве топлива 3) увеличение диаметра печи в зоне интенсивного выделения летучих веществ 4) применение двух печных барабанов, в одном из которых кокс до температуры начала выделения летучих веществ нагревается путем сжигания топлива, а в другом—дальнейший нагрев осуществляется за счет сжигания летучих веществ при прямоточном движении потоков кокса и дымовых газов. [c.193]
Реакционный объем прокалочной печи V (м= ) вычисляют по формуле [c.195]
Расход воздуха на горение топлива и пыли и дожиг летучих веществ рассчитывают в стехиометрическом соотношении, так как в прокалочной печи среда восстановительная (за исключением топки). [c.196]
Прокалочную печь по длине разделить на зоны а) подогрев кокса до 100 °С б) сушка кокса при температуре 100°С в) подогрев сухого кокса от 100 °С до температуры начала выделения летучих веществ —500 «С г) выделение основной массы летучих веществ при температуре 500—850 °С — зона карбонизации д) прокаливание при нагреве кокса от 850 °С до конечной температуры (приблизительно до 1400 °С в случае игольчатого кокса и до 1200°С в случае рядового кокса) е) топочная зона. [c.196]
Температура предварительного подогрева технологического воздуха, подаваемого в прокалочную печь, по практическим данным не должна превышать 400—500 °С. [c.196]
Часть летучих веществ (в % масс.), сгораемых в той части прокалочной печи, где температура кокса не превышает 850 °С, равна [c.197]
Расчет прокалочной печи с вращающимся подом [c.204]
Определить технологические размеры прокалочной печи с вращающимся подом можно путем ряда поверочных расчетов, которые удобно разбить на три этапа. На первом этапе задаются геометрическими размерами и формой прокалочной печи, числом, размерами и расположением перемешивающих устройств — скребков. [c.204]
В прокалочной печи с вращающимся подом, снабженной скребками, лимитирующей стадией процесса является передача тепла внутри слоя кокса. С некоторыми допущениями можно принять, что температура топочного пространства и температура поверхности слоя кокса одинаковы. [c.206]
Выделившийся сероводород быстро окисляется кислородом воздуха при высоких температурах до сернистого газа, при низких температурах — до элементарной серы. Поэтому в отходящих газах прокалочных печей и электролизных ванн электродных и алюминиевых заводов находится преимущественно сернистый газ и в небольшом количестве сероводород. [c.157]
Прокалка коксовых частич таких размеров в существующих прокалочных агрегатах — вращающихся печах или вертикальных камерных печах — практически невозможна. В связи с этим научно-исследовательские и проектные институты пытаются разработать приемлемые конструкции прокалочных печей, в которых угар кокса будет наименьшим при их высокой производительности. [c.250]
Из низа сушильной колонны катализатор ссыпается в инжекторный тройник и дымовым газом транспортируется в бункер сухого катализатора 22 через циклон 23. Из бункера катализатор пересыпается в прокалочную печь 24. Прокаливание ведется горячим дымовым газом из топки 25. В прокалочной печи газ двинслой катализатора для создания кипящего слоя. Охлажденный до —120° С после прокаливания готовый катализатор затаривается в бочки. [c.232]
Прокаливание — одна из важных операций приготовления контактных масс. При прокаливании, вследствие термической диссоциации, получается собственно активное вещество катализатора. Условия прокаливания (температура, время, среда) в значительной степени определяют средний диаметр пор и величину поверхности, полученной контактной массы [35—37]. Прокаливание обычно проводят при температурах, райны или выше температур проведения каталитической реакции. В крупнотоннажных производствах катализаторов применяют прокалочные печи с непосредственным обогревом катализатора нагретым воздухом или дымовыми газами (в частности, вращающиеся печи), реакторы шахтного типа, взвешенного слоя и др. В малотоннажных производствах катализаторов часто используют муфельные печи с электрическим нагревом. [c.105]
Прокалочная печь —шахта из нержавеющей стали квадратного сечения, снабженная рубашкой и теплоизоляцией. В ней катализатор, медленно опускаясь, проходит также 3 зоны (рис. 46) предварительного подогрева в верхней части печи, прокаливания при 750 °С и охлаждения. С повышением температуры прокаливания механическая прочность катализатора возрастает, одновременно уменьшается его удельная поверхность, а, следовательно, и активность. Оптимальной является температура 750°С., На [c.115]
Прокалка катализатора осуществляется в прокалочпой печи, куда сухой катализатор пересыпается самотеком, путем подогрева его горячими дымовыми газами из топки под давлением. Для поддерншпия заданного температурного режима прокалки часть дымовых газов подается иепосред-ственпо в прокалочную печь под слой катализатора для создания кипящего слоя, а другая часть — в кожух прокалочной печи. По окончании прокалки и и охлаждения до 120 °С катализатор выгружается через разгрузочный патрубок в бочки либо транспортируется с помощью сжатого воздуха из нижнего стояка прокалочной печи в бункер готового катализатора. [c.224]
Катализатор заполняет все пространство прокалочной печи и под действием собственной тяжести медленно движется сверху вниз. Скорость движения регулируется калиброванными кольцами, устанавливаемыми в нижнем распределительном устройстве печи. Зону предварительного нагрева и зону прокаливания нагревают дымовыми газами, всасываемыми вентиляторами из газогенераторной топки. В прокалочную печь дымовые газы поступают с температурой 850— 930° С, а выходят в атмосферу с температурой не выше 180—200° С. Эту температуру поддерживают, подавая на прием дымососа холодный воздух через специальный шибер. В последней зоне катализатор охлаждают холодным воздухом, используемым затем в газогенераторной.топке. Движение дымовых газов и катализатора в прокалоч-ных печах осуществляют по принципу противотока поток шариков движется сверху вниз, а дымовые газы — снизу вверх, распределяясь в слое катализатора при помощи специальных коробов и равномерно пронизывая весь слой. Поддержание постоянного температурного режима в прокалочных печах связано с поддержанием постоянного уровня в них катализатора падение уровня нарушает температурный режим печей. Высокий уровень, при котором загрузочная труба переполняется и катализатор ссыпается в бункер элеватора, приводит к обрыву цепей и поломке ковшей. Поэтому вертикальный элеватор для загрузки прокалочных печей работает периодически его пуск и остановку проводят автоматически, чем и поддерживают постоянный уровень шариков в прокалочных печах. [c.69]
Прокаленный и охлажденный катализатор на выходе из прокалочной печи наклонным элеватором подают в тройник, из которого он распределяется по ситообразным вращаюпщмся барабанным грохотам для просеивания. Стандартные шарики размерами 2,5—5,0 мм [c.69]
Процессы обезвоживания шариковых силикагелей включают три стадии с постепенным увеличением температуры обработка вытеснителем (104—120° С), высушивание на конвейерной сушилке (135—150° С) и прокаливание (450—500° С) в прокалочных колоннах (мелкошариковых) или в прокалочных печах (крупношариковых). Кроме кислой среды тормозящим условием при созревании силикагеля является также выбор применяемого вытеснителя. Для [c.123]
I — аппарат для обессеривания носителя 2, 5—сушилки 3—бак с мешайкой и паровой рубашкой 4—прямоточный барабанный смеситель 6 — прокалочная печь. [c.149]
Зона предварительного подогрева 1 состоит из шести рядов трубок, в которые входят дымовые газы из газогенераторной топки, а между ними сверху вниз сплошным потоком движется катализатор или адсорбент. Под трубками расположены 64 воронки 2, образующие выравниватель потока, назначение которого заключается в создании равномерного потока движения шариков по всему сечению прокалочной печи. Зона нрокаливания 3 имеет восемь газораспределительных желобов 3. Дымовые газы поступают в них, проходят снизу вверх через слой шариков и отсасываются вентилятором из-под воронок выравнивателя потока. Эта зона снабжена люком 4 для внутреннего осмотра печи. Зона охлаждения 6 состоит из шести рядов трубок, через которые вентилятором прокачивают холодный воздух. Под ней расположен второй выравниватель потока, состоящий из четырех рядов воронок 7 в нервом ряду 64, [c. 139]
Температура зоны предварительного подогрева (верхний змеевик) от 170—175 до 650—700 С, в зоне прокаливания 750—780″ С, в зоне охлаждения (нижний змеевпк) 50—75 С. Суточная выгрузка прокалочной печи 3—3,5 т, общая загрузка — 9 т, время движення шариков от начала загрузкп до выгрузки 3 суток, охлаждение печи для ремонта 2,5—3 суток, загрузка п пуск 1.5—2 суток. Для запуска прокалочную печь предварительно заполняют шариками, затем температуру начинают повышать. [c.140]
Установка для определения стабильности катализатора состоят из электрической печи, реактора, бюретки для подачи воды, холодильника, приемника и пароперегревателя. Перед началом работы прокалочной печи проверяют распределение температуры по ее длине. Затем выбирают площадку для загрузки -катализатора, на которой перепад температуры не превышает 5° С. Констрзтащя печи должна обеспечить длину площадки, достаточную для загрузки 150 лл катализатора. В испытуемом образце предварительно определяют насыпную плотность и каталитическую активность. При загрузке катализатора в реактор определяют его массу и объем. Весь прокаливаемый катализатор должен разместиться в зоне выбранной прокалочной площадки. Реактор вставляют в печь и соединяют с пароперегревателем и холодильником. Зазор между реактором п печью сверху и снизу закрывают асбестовой ватой. В карман реактора вставляют термопару и печь разогревают до 750° С в течение 75—90 мин. [c.161]
На рис. 3.8 показана принципиальная схема установки прокаливания, снабженной барабанной печью. Установка включает блоки прокаливания и охлаждения кокса, пылеулавливания и утилизации тепла и склад готового продукта. На установке предусмотрены полный дожиг пыли и летучих веществ, утилизация тепла с получением водяного пара. Важным элементом технологической схемы установки является предварительный подогрев воздуха до 400—450 °С, позволяющий уменьшить потери кокса от угара. Этому также способствует предварительная сушка или обезвоживание исходного сырья. Подготовленный к прокаливанию кокс из сырьевого бункера с помощью ковшового элеватора подают в загрузочный бункер 4, откуда кокс самотеком через дозатор 5 ссыпается в прокалочную печь 3 барабанного типа навстречу потоку горячих дымовых газов. Дымовые газы образуются за счет подачи в печь жидкого либо газообразного топлива и воздуха. Из печи газовый поток, несущий в себе недогоревшие летучие вещества и коксовую пыль, сразу поступает в иылеосадительную камеру 7, а далее проходит котел-утилизатор 5 и с помощью дымососа 9 подается в [c.192]
Сырой кокс из сырьевого бункера 3 в прокалочную печь 5 загружается по лручной регулировкой толщины слоя кокса. Дымовые газы отводятся через дымоход 4, расиоложен-ный над сводом печи. Загружаемый кокс сразу попадает в зону с высокой температурой — около 1000 °С. Благодаря этому из кокса в течение нескольких минут удаляется влага, а потом происходит пиролитическое разложение смолистых веществ, выделяющихся из кокса при температуре 500 °С и выше. Время пребывания кокса в зоне иагрева составляет примерно 1 ч. Перепад температур мел(ду отходящими дымовыми газами и прокаленным коксом достигает 85—100 °С и более. Топливо извне для нагрева кокса практически не расходуется, если готовый продукт имеет истинную плотность не более 2060 кг/м . [c.194]
При составлении общего теплового баланса прокалочной печи задаются расходом топлива из расчета примерно 2,5% (масс.) от производительности печи по сырью, отдельно определяют количество сгорающих в печи летучих веществ и количест1зо выделяю цегося при этом тепла. Из теплового баланса находят расход технологического воздуха. [c.197]
Во избежание сильного уноса пыли важно обратить внимание на то, что линейная скорость дымовых газов в прокалочной печи не должна превышать 0,2 м/с. Внутренние размеры печи — диаметр и высоту рекомендуется ориентировочно принимать, исходя из условия, что удельный съем кокса с 1 м площади пода и с 1 м печного пространства не превышает значений, указанных ниже [c.204]
Таким образом, в данном пособии изложены методы расчетов основных технологических процессов нефтепереработки, включая подготовку газовых потоков с целью их дальнейшего использования, а также рассмотрены некоторые вопросы охраны природы. Особенностью пособия является то, что дан не полный расчет всей технологической цепочки любого вторичного процесса, а лишь расчеты основных аппаратов — реакторов экстракторов, прокалочных печей и т. д. Подобный подход поз волил достаточно полно излолшть важные элементы расчетов что существенно при организации самостоятельной работы сту дентов над курсовыми и дипломными проектами. Методы рас чета ректификационных колонн и оборудования, предназначен ных для блоков регенерации растворителей (при очистке мае ляных фракций) или для блоков разделения продуктов реакции аналогичны для любых систем и в достаточной степени рассмотрены в главе 1. [c.326]
Пропитку гранулированного носителя осуществляют различными способами. Часто применяют метод пропитки в избытке раствора. В этом случае предварительно определяют адсорбционное равновесие между раствором разных концентраций и носителем. Особо следует обратить внимание на возможность избирательЦой адсорбции компонентов из раствора носителем. Пропитывающий раствор готовят такой концентрации, чтобы поглощенное по расчету количество солей создавало в готовом катализаторе нужную концентрацию активного компонента. Пропитку гранул (в том числе и таблеток) носителя можно осуществлять достаточно примитивно в чанах или чашах с последующим отделением избытка раствора на нутч-фильтрах или центрифугах. Более рациональным, однако, является применение специальных пропиточных машин [13], представляющих собою, движущуюся бесконечную ленту, на которой подвешены сетчатые корзины из нержавеющей стали или другого материала. Носитель загружают из бункера в корзины. При движении ленты корзины опускаются на некоторое время в короб с пропитывающим раствором, а затем приподнимаются и перемещаются в обратном направлении над коробом, давая раствору стечь в него. Далее лента машины с подвешенными корзинами может, например, последовательно проходить тоннельные сушилку и прокалочную печь. [c.183]
зачем нужны, производители, модели печек для сушки и прокаливания
Для сушки и прокаливания отсыревших сварочных электродов применяется печь для прокалки электродов. Кроме того для хранения ранее прокаленных электродов активно применяются термопеналы. Процесс просушки и прокалки сварочных электродов позволяет восстановить качественные свойства для гарантированной работы сварщика и требуемых показателей сварного шва.
Сегодня рынок предлагает такое оборудования в большом ассортименте, это и электропечи и термопеналы для сушки и прокаливания сварочных электродов производства России, а также пеналы-термосы для хранения ранее прокаленных электродов. Этот товар может быть самых разнообразных моделей и образцов. Поэтому при выборе необходимо внимательно подходить к вопросу соответствия соотношения цена – качество.
Электропечь и термопенал для сушки, прокаливания и для хранения электродов для ручной дуговой сварки обеспечивают высокие качественные показатели электродов при сварочном процессе на особо ответственных участках и объектах. Они с успехом применяются при ремонте и изготовлении ответственных конструкций, а также при сваривании различных трубопроводов. Печь для прокалки электродов может использоваться в качестве камеры для сушки или для других необходимых целей. Установки для сушки могут быть, как стационарные, так и переносные.
Производители
Одним из ведущих российских производителей печей для прокалки электродов является завод сварочного оборудования “ТЭН и К”, город Миасс. С 1998 года предприятие обзавелось значительным опытом в сфере изготовления и продажи профессионального оснащения для сварки. Продукция компании пользуется высоким спросом. Электропечи отлично зарекомендовали себя на рынке, основными характеристиками являются улучшенная теплоизоляция и равномерный нагрев материалов по всему рабочему пространству прибора. Агрегаты оснащены визуальным контролем температуры и времени, что гарантирует удобство работы. При этом аппараты активно применяются в различных областях промышленности.
Компания “ЛИНГАС” – изготовитель широкого спектра специализированного оборудования, основана в 1992 году. Востребованной категорией являются печи для хранения, сушки и прокалки электродов. Производимая продукция разработана на уровне лучших зарубежных аналогов, обладает всеми необходимыми сертификатами. Квалифицированные сотрудники самостоятельно занимаются усовершенствованием существующих аппаратов и разработкой новых машин. Ежегодно в производство внедряются новые современные модели. Поставка оснащения осуществляется по территории России и странам СНГ.
Ещё одним крупным производителем электродных печей является ЗАО “НОВЭЛ”. История предприятия началась в 1989 году, в 1995 был выпущена первая партия ТЭНов. В следующие несколько лет завод значительно увеличил собственный ассортимент. Сегодня клиентам предлагается электротепловое, вентиляционное, сварочное и другое профессиональное оборудование. Каждое изделие проходит обязательную сертификацию, поэтому продукция характеризуется высоким качеством, удобством и простотой управления. Реализация технического оснащения проводится через дилерскую сетью, охватывающую все регионы России и страны СНГ.
[ads-pc-2][ads-mob-2]
Производственно-коммерческое предприятие “Плазер” было основано в середине 90-х годов, располагает подразделениями в трех городах. Компания специализируется на изготовлении сварочного оборудования. Одной из актуальных категорий широкого ассортимента являются печи для сушки и прокаливания электродов, а также для хранения уже обработанных материалов. Печи выпускаются под маркировкой “ЭТП”. Организация производит продукцию, адаптированную к российским условиям эксплуатации и с применением новейших технологий. Также фирма реализует обширный спектр сварочных материалов, аксессуаров и вспомогательных средств для профессионального выполнения работ.
“Lincoln Electric” – один из мировых производителей сварочного оборудования и материалов. Компания была основана в 1895 году, располагает офисами продаж более чем в 160 странах мира. Предприятие предлагает широкий ассортимент технически современного оснащения. Востребованной продукцией являются печи для прокаливания электродов. Конструкция данных агрегатов тщательно продумана и разработана с применением современных технологий. Аппараты обладают оптимальными характеристиками и обеспечивают качественную термообработку. Электродные печи от американского концерна способны намного повысить эффективность работы.
Печи для прокалки электродов – популярные модели
Электронагревательные печи ЭПСЭ предназначаются для прокаливания и просушки сварочных электродов при температурах от 100 до 400 градусов по Цельсию. Последние модели печей оборудованы электронными блоками управления с цифровыми индикаторами, которые позволяют отслеживать оставшееся время прокалки (сушки) и текущую температуру.
Повышенный эксплуатационный ресурс, достигнут благодаря применению трубчатых электронагревателей (ТЭН) вместо нихромовой проволоки, которые обладают большим сроком службы и при ремонте легко меняются.
ЭПСЭ-10/400
Наиболее популярной моделью из серии электродных печей ЭПСЭ является модель ЭПСЭ-10/400. ЭПСЭ-10/400 – печка для электродов электронагревательного типа, используется для сушки и прокалки. В ходе термообработки поддерживается автоматическое поддержание температуры в границах 100-400 градусов. Модель оснащена блоком управления с терморегулятором для настройки параметров.
Основные технические характеристики:
- Масса загружаемых электродов – 10 кг.
- Вес – 15 кг.
- Напряжение – 220 В.
- Мощность – 100 Вт/ч.
- Габариты – 222 мм. х 720 мм. х 265 мм.
- Время разогрева до номинальной температуры с полной загрузкой – 100 мин.
ЭПСЭ-50/400
Печи для сушки электродов ЭПСЭ-50/400 имеют близкую к максимальной загрузку в 50 кг. (для мобильных устройств). Это позволяет использовать агрегат для прокалки материалов как в стационарных условиях, так и при выезде сварщика на объект.
Основные технические характеристики:
- Масса загружаемых электродов – 50 кг.
- Вес – 40 кг.
- Напряжение – 220 В.
- Мощность – 250 Вт/ч.
- Габариты – 605 мм. х 470 мм. х 680 мм.
ПСПЭ-10/400
ПСПЭ-10/400 – печь предназначена для прокаливания электродов при температуре от 100 до 400 градусов. Модель обладает компактными размерами, оснащена ручным терморегулятором и двумя ТЭНами. Внутри прибора расположены две выдвижные полки, на каждую из которых можно расположить по 5 кг. материалов. Небольшие параметры печи позволяет сварщикам брать аппарат с собой на объект.
Основные технические характеристики:
- Масса загружаемых электродов – 10 кг.
- Вес – 15 кг.
- Напряжение – 220 В.
- Мощность – 100 Вт/ч.
- Габариты – 222 мм. х 710 мм. х 305 мм.
Видео
СШО 3,2.
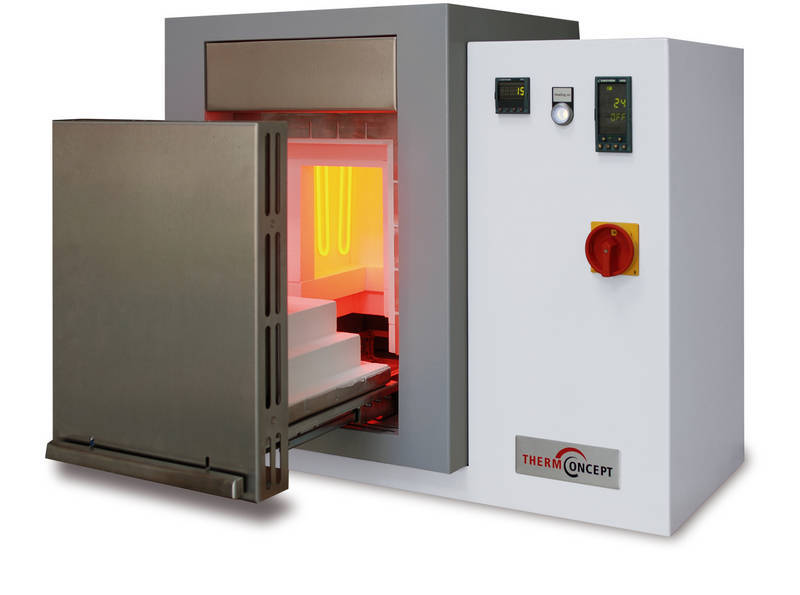
СШО 3,2.3,2.5/4,0 – печь для сушки и прокалки электродов при температуре до 400 градусов.
Основные технические характеристики:
- Масса загружаемых электродов – максимум 90 кг.
- Вес – 80 кг.
- Напряжение – 220 или 380 В.
- Мощность – 600 Вт/ч.
- Габариты – 765 мм. х 640 мм. х 850 мм.
HydroGuard Bench 240
HydroGuard Bench 240 – печь для прокалки электродов, работает в диапазоне температур от 38 до 288 градусов, оснащена терморегулятором. Круглая форма агрегата гарантирует правильную циркуляцию воздуха. Полки внутри прибора съемные, это позволяет использовать печь для нагревания рабочих изделий.
Основные технические характеристики:
- Масса загружаемых электродов – 159 кг.
- Напряжение – 240/480 В.
- Два нагревательных элемента суммарной мощностью 1000 Вт.
Радуга-34
Печь для прокалки электродов «Радуга-34» устроена по модульному принципу и состоит из пяти пятиметровых модулей, которые одновременно являются зонами температурного нагрева. Контроль температуры осуществляется с точностью до одного градуса при помощи термопары.
Основные технические характеристики:
- Масса загружаемых электродов – 2 тонны электродов диаметром 4 мм. за 7 часов работы.
- Габариты печи – 27000 мм. х 920 мм. х 1200 мм.
- Длина нагревательной камеры, ориентировочно – 25500 мм.
- Количество управляемых зон нагрева – 12 ( 6 – сверху, 6 – снизу).
- Максимальная температура нагрева изделия – 450 °С.
- Каждая зона нагрева имеет щелевидную трубу для удаления влаги.
- Ширина туннеля нагревательной камеры – 540 мм.
- Максимальная потребляемая мощность – 23500 Вт.
- Средняя потребляемая мощность – 6000 Вт.
- Тип конвейера составной (тефлоновая лента + сетка).
[ads-pc-3][ads-mob-3]
Функционал
Рассмотрим подробнее функционал печей для прокаливания. Печи для сушки и прокалки электродов делятся на стационарные и мобильные. Также встречается деление на простые приборы с функцией сушки и комбинированные – для сушки и прокалки.
Независимо от классификации аппараты обладают схожей конструкцией и внутренним наполнением.
Электропечь представляет собой металлический шкаф/ящик со специальными лотками/полками для электродов. Для поддержания необходимой температура стенки с внутренней стороны отделаны термоизолирующими материалами. Прибор снабжен термостатом, который работает в диапазоне от 60 до 500 градусов. В зависимости от модели агрегата варьируется размер и количество лотков, а, следовательно, разнится масса загружаемых электродов – от 10 до 250 кг.
Некоторые модели, применяемые для термообработки большого объема материалов, снабжены микропроцессорным программируемым регулятором и тепловыми экранами для лучшей теплоизоляции.
Как выбирать
И несколько советов о том, как выбирать прокалочные печи. При выборе печи для сушки и прокаливания электродов следует обратить внимание на несколько важных параметров.
1. В зависимости от объема производства сварщику может понадобиться разное количество сварочных материалов. Поэтому главной технической характеристикой при выборе печи является масса загружаемых электродов.
2. Ещё одним существенным свойством является мощность, величина которой охватывает широкий диапазон от 100 до 6000 Вт.
3. Напряжение питающей сети имеет стандартное значение для всех печей, произведенных отечественными заводами.
4. Вес и габариты агрегата для прокаливания варьируются в значительных величинах. Если в обязанности сварщика не входит выезд на объект, то масса и размеры оборудования не играет большой роли.
5. Компактные переносные печи поддерживает только функцию сушки электродов, стационарные – и прокаливают, и сушат сварочные материалы.
Обжиговые печи. Барабанные печи. Печи для прокалки
Назначение барабанной печи
Назначение данной вращающейся обжиговой печи – нагревание подаваемого материала до максимальной температуры 950 °C. Конструкция оборудования основана на изложенных ниже условиях процесса, протекающего во вращающейся обжиговой печи.
Материал нагревается в следующих режимах теплопередачи, перечисленных в порядке возрастания их значимости:
1. Теплота излучения.
2. Теплота от прямого контакта с внутренней поверхностью барабана.
Необходимое количество тепла определяется с учетом следующих требований:
1. Тепло для увеличения температуры твердых компонентов.
2. Тепло для нагрева влажного подаваемого материала до температуры испарения.
3. Тепло для выпаривания влажного подаваемого материала.
4. Тепло для увеличения температуры струи воздуха.
Описание процесса работы барабанной печи
Влажный кек (UO4.2H2O) помещают на загрузочный конвейер обжиговой печи. Загрузочная сторона барабана оборудована винтовыми пластинами и подающей накладкой, с большой скоростью отводящей материал от данной стороны барабана. Сразу же после схода с винтовых пластин материал под действием силы тяжести стекает вдоль продольной оси барабана. В печной секции обжиговой печи гидратированный пероксид урана (UO4.2H2O) подогревается при помощи электронагревательных элементов печи. Электрическая печь разделена на три зоны температурного контроля, что обеспечивает гибкость температурной характеристики. В первых двух зонах пероксид урана (UO4.2H2O) поэтапно нагревается до температуры около 680 °C. В третьей зоне температура повышается примерно до 880 °C, причем происходит превращение пероксида урана (UO4.2H2O) в закись-окись урана (U3O8).
Полностью прореагировавший желтый урановый кек (U3O8) подается в охлаждающую секцию барабана. Тепло отводится от твердых компонентов, за счет высокой теплопроводности, через стенку барабана обжиговой печи и удаляется с охлаждающей водой, разбрызгиваемой на внешнюю часть барабана. Температура материала уменьшается приблизительно до 60 °C, затем материал подается в разгрузочный трубопровод, через который под действием силы тяжести попадает в транспортную систему. Через разгрузочный трубопровод во вращающуюся обжиговую печь подается мощный поток воздуха, проходящий через барабан навстречу потоку материала, чтобы удалить водяной пар, образовавшийся на нагревательной стадии процесса. Влажный воздух отводится из загрузочного трубопровода при помощи вентиляции.
Компоненты обжиговой барабанной печи
Барабан вращающейся обжиговой печи
Сварные секции барабана имеют швы, располагающиеся попеременно под углами 90° и 180° один к другому и полученные сваркой с полным проплавлением основного металла. Бандажи и зубчатые венцы смонтированы на механически обработанных поверхностях, отделенных от барабана распорными элементами, чтобы учесть различия в радиальном тепловом расширении. Конструкция барабана учитывает любые тепловые и механические нагрузки и поэтому обеспечивает надежную работу. На загрузочной стороне барабана расположены удерживающие материал накладки, преграждающие обратный поток материала в трубопровод и винтовые пластины для подачи материала в нагретые секции.
Открытые секции барабана на загрузочной и разгрузочной стороне оборудованы экранами тепловой защиты персонала.
Бандаж
Барабан имеет два бандажа без сварных швов и стыков из кованой стали. Каждый бандаж имеет цельную прямоугольную секцию и упрочнен для увеличения срока службы.
Опорные колеса
Барабан печи вращается на четырех опорных колесах изготовленных из кованой стали. Опорные колеса упрочнены для увеличения срока службы. Колеса установлены с натягом на высокопрочный вал, установленный между двумя подшипниковыми опорами, имеющими срок службы не менее 60000 часов. Основание колес оснащено нажимными винтами для горизонтального выравнивания и регулировки колес.
Упорные ролики
Установка содержит два упорных ролика, состоящих из двух стальных колес с уплотненными сферическими роликоподшипниками, срок службы которых составляет не менее 60000 часов. Упорные ролики упрочнены для увеличения их срока службы.
Узел привода
Барабан рассчитан на вращение с частотой 1-5 об/мин при мощности 1,5 кВт от электродвигателя с частотой вращения 1425 об/мин, работающего от трехфазной сети переменного тока напряжением 380 В, частотой 50 Гц и выполненного в герметичном исполнении с воздушным охлаждением. Вал электродвигателя напрямую соединен с входным валом главного редуктора через гибкую муфту.
Циклоидный главный редуктор имеет точное понижающее передаточное отношение 71:1 с одной ступенью понижения. Низкоскоростной вал редуктора рассчитан на необходимый момент и предельные нагрузки.
Предотвращение деформации барабана обжиговой печи
Для предотвращения деформации барабана печи, во время сбоев в системе энергоснабжения электродвигателя, предусмотрен дополнительный дизельный двигатель для продолжения вращения барабана. Дизельный двигатель имеет регулируемую частоту вращения (1500-3000 об/мин) и номинальную мощность на выходе 1,5 – 3,8 кВт. Дизельный двигатель запускается вручную или электрическим стартером постоянного тока и напрямую соединен с валом электрического двигателя через муфту.
Барабанная обжиговая печь»>
Зубчатый венец
Зубчатый венец выполнен из углеродистой стали. Каждая звездочка имеет 96 закаленных зубьев, смонтирована на барабане и имеет разъемы для упрощения демонтажа.
Приводная шестерня
Изготовлена из углеродистой стали. Каждая шестерня имеет 14 закаленных зубьев и установлена на низкоскоростном валу редуктора.
Приводная цепь
Применяется цепь с наклоном для обеспечения вращения барабана обжиговой печи.
Система обжиговой печи
Кожух печи охватывает барабан и изготовлен из углеродистой стали. Стены и пол кожухов выполнены как одна полная секция. Крыша печи состоит из трех секций, по одной на каждую зону нагрева, и может быть снята с целью технического обслуживания печи или барабана.
Характеристики камеры/нагревательных элементов:
Форсуночный водоохладитель
Форсуночный водоохладитель — уменьшает температуру продукта печи. Корпус охладителя изготовлен из углеродистой стали с внутренними поверхностями, покрытыми эпоксидной смолой (для уменьшения действия коррозии). Корпус оборудован двумя смонтированными в верхней части трубопроводами, имеющими распылительные сопла, впускные и выпускные вращающиеся лабиринтные уплотнения, верхнее сопло для выпуска пара, нижнее дренажное сопло, боковое перепускное сопло, дверцы для доступа и смотровые отверстия. Вода подается в распылительные сопла по трубопроводу, а выпуск осуществляется под действием силы тяжести через нижний дренажный фланец.
Трубопроводы обжиговой печи
Загрузочный трубопровод выполнен из стали нержавеющей стали. Комплектация: монтажная крышка, смотровое отверстие, качающееся сопло для выпуска газа, дверца для выпуска обратных утечек через барабан и узел вращающегося уплотнения.
Разгрузочный трубопровод выполнен из нержавеющей стали. Комплектация: желоб для разгрузки продукта, монтажную крышку, смотровое отверстие и узел вращающегося уплотнения. Разгрузочное уплотнение – температурный компенсатор сильфонного типа.
Винтовой питатель
Обжиговая печь оборудована загрузочным винтовым конвейером для подачи в барабан кека пероксида урана, представляет собой шнек, расположенный под нулевым углом к горизонтали, подвергшийся чистовой обработке.
Термопары обжиговой печи
Предусмотрены термопары для непрерывного контроля температуры в зонах печи и температур выгружаемого продукта.
Выключатели по нулевой частоте вращения
Обжиговая печь поставляется с двумя выключателями по нулевой частоте вращения, один из которых непрерывно контролирует вращение барабана, другой – вращение загрузочной винтовой линии. Узлы выключателей по частоте вращения смонтированы на концах валов и имеют тип дисковых генераторов импульсов, создающих переменное магнитное поле, регистрируемое измерительным устройством.
Прокалочные печи — SchumacherTech — Машиностроение и торговля
Koe 135
Для вытопки воска и равномерной прокалки опок. Возможность программирования 9 программ с 30 шагами нагрева, выдерживания температуры и медленым охлаждением. Высокая камера позволяет работать с опоками больших размеров.
Мощность | 9 КВт |
---|---|
Температура | до 1200 °C |
Размер камеры | 410x600x555 мм. |
Электропитание | 3×400В |
Габариты | 760x1050x1530 мм. |
Вес | 415 кг. |
Ruf AO 500
Для вытопки воска и равномерной прокалки опок. Возможность программирования 6 программ с 30 шагами нагрева, выдерживания температуры и медленым охлаждением. Высокая камера позволяет работать с опоками высоты до 440 мм.
Мощность | 13 КВт |
---|---|
Температура | до 900 °C |
Размер камеры | 550x450x450 мм. |
Электропитание | 3×400В |
Габариты | 800x1200x1750 мм.![]() |
Вес | 450 кг. |
Ruf RDO 500/2
Вращающаяся прокалочная печь для вытопки воска и равномерной прокалки опок. Возможность программирования 6 программ с 30 шагами нагрева, выдерживания температуры и медленым охлаждением. Два этажа позволяют прокалку большое количество опок одновременно. Оснащена специальным выходом для подключения вытяжки с дросельным клапаном
Мощность | 13 КВт |
---|---|
Температура | до 850 °C |
Диаметр камеры | 500 мм. |
Электропитание | 3×400В |
Диаметр тарелок | 440 мм |
Растояние между тарелок | 220 мм |
Кол.во опок Ø100 мм с фланцем | 20 шт. |
Габариты | 780x1100x1700 мм. |
Вес | 680 кг. |
Как работает печь для обжига?
Прокаливание (также известное как прокаливание) можно определить как нагревание до высоких температур в присутствии кислорода или воздуха, или это может быть процесс термической обработки, вызывающий термическое разложение. Термическое разложение достигается с помощью прокаливания, помещая образец в отсутствие или ограниченную подачу воздуха или кислорода.
Основными задачами печи для обжига являются отвод воды, которая присутствует в виде абсорбированной влаги, удаление летучих компонентов, таких как двуокись углерода, или окисление части или всего вещества.Прокаливание проводится на различных устройствах, в том числе в промышленных печах. В этом сообщении в блоге будет описан принцип работы печи для обжига.
Типы печей обжигаВ зависимости от требований применения печи для обжига могут использовать в качестве источника топлива электричество, газ или масло.
Обычно для прокаливания используются три типа печей. В отражательной печи образец вступает в прямой контакт с пламенем и горячими газами источника тепла, но топливо, используемое для питания источника тепла, является отдельным.
В муфельной печи ни топливо, ни газы от источника тепла не вступают в прямой контакт с образцом при термообработке.
В шахтной печи образец находится в тесном контакте с источником топлива, что приводит к некоторому загрязнению образующейся золой. Однако в некоторых более поздних конструкциях шахтных печей источник топлива размещается на отдельной решетке, что обеспечивает достижение пробы только газом и пламенем и устраняет риск загрязнения пробы.
Печи для обжига от ThermcraftThermcraft разрабатывает и производит ряд промышленных печей на протяжении более 40 лет и имеет возможность создавать печи для обжига для различных применений. Мы производим стандартные конструкции быстрой отгрузки для немедленных решений, или, если вам требуется что-то более конкретное, мы можем построить специальные печи для обжига в соответствии с точными спецификациями.
Мы заработали репутацию производителя высококачественных печей и всегда обеспечиваем высокий уровень обслуживания клиентов.Наша команда рада предоставить поддержку и рекомендации всем, кто хочет приобрести печь для обжига.
Если вам нужна дополнительная информация о наших решениях, свяжитесь с нами.
Печь для обжига| Различные типы промышленных печей
Прокаливание — это процесс термообработки, при котором руды или другие твердые материалы нагреваются ниже точки плавления при отсутствии или ограниченном поступлении воздуха. Этот процесс выполняется, чтобы вызвать термическое разложение, удаление летучей фракции или фазовый переход.
Обычно печи для обжига нагреваются до рабочих температур от 800 o C до 1300 o C, в зависимости от области применения. Другие параметры процесса прокаливания могут включать жесткие термические профили со строгими допусками.
Печи для обжига могут различаться по своей конфигурации, но обычно это муфельные, отражательные, шахтные или обжиговые печи. Когда образец прокаливается, его часто перемешивают, чтобы обеспечить однородность конечного продукта.
муфельных печей построены таким образом, что источник тепла не вступает в контакт с образцом, который в настоящее время кальцинированной, они часто изготовлены из железа, кирпичной кладки или огня глины. В печи отражательного обжига источник тепла находится в прямом контакте с образцом.
Шахтные печи или печи бывают периодическими или непрерывными. Печи периодического обжига охлаждают перед отбором образца, в то время как образец отводится в печи непрерывного обжига без какого-либо охлаждения.Печи непрерывного действия являются более популярным выбором из-за экономии энергии и времени.
Применение печи для обжигаОбщие области применения печей для обжига включают удаление воды из образца, которая присутствует в виде абсорбированной влаги; удаление летучих компонентов, таких как диоксид углерода или диоксид серы; или окислить часть или все вещество.
Печи обжига чаще всего используются для производства цемента.Это достигается путем разложения карбоната кальция на оксид кальция и диоксид углерода.
Эти печи также используются при синтезе цеолитов для удаления ионов аммония и расстекловании стекла, материалов, влияющих на фазовые превращения.
Thermcraft производит и поставляет широкий спектр промышленных печей, которые можно использовать для кальцинации. Наша продукция варьируется от стандартных конструкций, которые можно быстро отгрузить, до решений, которые можно настроить в соответствии с точными спецификациями.
Мы гордимся нашим высоким уровнем обслуживания и поддержки клиентов, и наша команда будет рада дать любой совет при выборе правильной печи для обжига для вашего применения.
Если вы хотите приобрести печь для обжига, но не уверены, какие характеристики подходят для ваших требований, свяжитесь с нами, и один из наших сотрудников будет рад помочь.
Печь для обжига, печь для обжига Поставщики и производители на Alibaba.com
Ознакомьтесь с широким спектром высококачественных, эффективных и надежных. печь для обжига на Alibaba.com для различных коммерческих и промышленных требований к плавке.
Профессиональное и оптимальное качество. Печь для обжига на объекте изготовлена из высококачественных материалов, таких как металлы, с длительным сроком службы и устойчивостью к любым видам использования. Эти продукты доступны с различными типами печей и оснащены точным контролем температуры. Файл. Печь для обжига на этом участке оборудована прочным корпусом, имеет водяное охлаждение, функции распылительного охлаждения и автоматическую систему управления ПЛК. Купите это. печь для кальцинирования здесь, чтобы максимизировать производительность и при этом энергоэффективными способами.
Alibaba.com предлагает несколько вариантов. печь для обжига различных размеров, форм, цветов, характеристик и типов печей, таких как дуговая печь, сушильная печь, печь отжига и многие другие. Эти прибыльные и продуктивные. Печь для обжига идеальна для сталелитейных заводов и отдельных производственных компаний благодаря своей эффективности и экологичности. Эти продукты просты в установке и недороги в обслуживании. Эти. Печь для обжига оснащена мощными термостойкими двигателями, которые обеспечивают оптимальную производительность и сокращают затраты на рабочую силу.
Просмотрите отдельные категории. Печь для кальцинирования доступна на сайте Alibaba.com, и покупайте эти продукты в рамках своего бюджета и требований. Эти продукты имеют сертификаты ISO, CE и доступны как OEM-заказы при оптовых закупках. При покупке этих продуктов предлагается квалифицированное послепродажное обслуживание.
печи для обжига, печи для обжига Поставщики и производители на Alibaba.com
Ознакомьтесь с широким спектром высококачественных, эффективных и надежных. печь для кальцинации на Alibaba.com для различных коммерческих и промышленных требований к плавке. Эти эффективные продукты на объекте не только эффективны, но и чрезвычайно надежны и достаточно прочны, чтобы прослужить долгое время. Файл. Печь для обжига — это термостойкие импровизированные модернизированные процедуры плавки для выполнения точных качественных работ, которые также широко популярны среди торговцев золотом. Эти. Печь для кальцинации предлагается на сайте ведущими поставщиками и оптовиками по конкурентоспособным ценам и предложениям. Профессиональное и оптимальное качество. Печь для обжига на месте изготовлена из высококачественных материалов, таких как металлы, с длительным сроком службы и устойчивостью к любым видам использования. Эти продукты доступны с различными типами печей и оснащены точным контролем температуры. Файл. Печь для обжига на этой площадке оснащена прочным корпусом, имеет водяное охлаждение, функции распылительного охлаждения и автоматическую систему управления ПЛК. Купите это. печь для обжига здесь, чтобы максимизировать вашу производительность и это тоже с точки зрения энергоэффективности.
Alibaba.com предлагает несколько вариантов. печь для обжига различных размеров, форм, цветов, характеристик и типов печей, таких как дуговая печь, сушильная печь, печь отжига и многие другие. Эти прибыльные и продуктивные. Печь для кальцинации идеальна для сталелитейных заводов и отдельных производственных компаний благодаря своей эффективности и экологичности. Эти продукты просты в установке и недороги в обслуживании. Эти. Печь для обжига оснащена мощными термостойкими двигателями, которые обеспечивают оптимальную производительность и снижают стоимость рабочей силы.
Просмотрите отдельные категории. Печь для обжига доступна на сайте Alibaba.com, и покупайте эти продукты в рамках своего бюджета и требований. Эти продукты имеют сертификаты ISO, CE и доступны как OEM-заказы при оптовых закупках. При покупке этих продуктов предлагается квалифицированное послепродажное обслуживание.
Этот сайт использует файлы cookie для повышения производительности. Если ваш браузер не принимает файлы cookie, вы не можете просматривать этот сайт.
Настройка вашего браузера для приема файлов cookie
Есть много причин, по которым cookie не может быть установлен правильно. Ниже приведены наиболее частые причины:
- В вашем браузере отключены файлы cookie. Вам необходимо сбросить настройки своего браузера, чтобы он принимал файлы cookie, или чтобы спросить вас, хотите ли вы принимать файлы cookie.
- Ваш браузер спрашивает вас, хотите ли вы принимать файлы cookie, и вы отказались.
Чтобы принять файлы cookie с этого сайта, используйте кнопку «Назад» и примите файлы cookie.
- Ваш браузер не поддерживает файлы cookie. Если вы подозреваете это, попробуйте другой браузер.
- Дата на вашем компьютере в прошлом. Если часы вашего компьютера показывают дату до 1 января 1970 г., браузер автоматически забудет файл cookie. Чтобы исправить это, установите правильное время и дату на своем компьютере.
- Вы установили приложение, которое отслеживает или блокирует установку файлов cookie. Вы должны отключить приложение при входе в систему или уточнить у системного администратора.
Почему этому сайту требуются файлы cookie?
Этот сайт использует файлы cookie для повышения производительности, запоминая, что вы вошли в систему, когда переходите со страницы на страницу. Чтобы предоставить доступ без файлов cookie
потребует от сайта создания нового сеанса для каждой посещаемой страницы, что замедляет работу системы до неприемлемого уровня.
Что сохраняется в файле cookie?
Этот сайт не хранит ничего, кроме автоматически сгенерированного идентификатора сеанса в cookie; никакая другая информация не фиксируется.
Как правило, в файле cookie может храниться только информация, которую вы предоставляете, или выбор, который вы делаете при посещении веб-сайта. Например, сайт не может определить ваше имя электронной почты, пока вы не введете его. Разрешение веб-сайту создавать файлы cookie не дает этому или любому другому сайту доступа к остальной части вашего компьютера, и только сайт, который создал файл cookie, может его прочитать.
Оптимизация прокалки антрацита в электропечах
Чалых Е.Ф., Технология и оборудование электродных и электроугольных предприятий, , М .: Металлургия, 1972.
Google ученый
Данцис Я.Б., Ершов В.А., Жилов Г.М., и др. Электротермические процессы в химической технологии, , Москва: Химия, 1984.
Google ученый
Солдатов, А. и Мочалов В.В., Производство электрокальцинированного антрацита с особыми свойствами // Технологические процессы и оборудование электродного производства . М .: Гос. Научно-исслед. Inst. Хим. Пром-сти, 1989, с. 43–49.
Google ученый
Гасик М.И., Электроды рудовосстановительных электропечей, , М .: Металлургия, 1984.
Google ученый
Солдатов А.И. и Рогожина Т.В., Современная технология электродных масс, , Челябинск: Фрегат, 1997.
. Google ученый
Селезнев А.Н., Углеродистое сырье для электродной промышленности, , М .: Профиздат, 2000.
Google ученый
Кашлев И.М., Елкин К.С., Страхов В.М., Производство электродной массы из антрацитов, VII Международный конгресс «Цветные металлы и минералы», Тезисы доклады (VII Международный конгресс «Цветные металлы и минералы»). , Тез. Докл.) , Красноярск, 2015, гл. 4. С. 220–221.
Google ученый
Кашлев, И.М., Солдатов А.И., Якушевич Н.Ф., Страхов В.М. Использование угля в качестве углеродного наполнителя при производстве электродной массы // Кокс хим. Химии. , 2000, нет. 1. С. 20–23.
Google ученый
Кашлев И.М., Солдатов А.И., Рогожина Т.В., Страхов В.М. Сырье для производства электродной массы // Труды заводской научно-технической конференции «Совершенствование производства.Завод Научно-техн. Конф. «Оптимизация производства ферросилиция». Новокузнецк, , 1997, № 4, с. 3. С. 106–115.
Google ученый
Кравцов К.И., Астахова И.С., Ходырев А.А. Выбор сырья для производства электродной массы, Труды заводской научно-технической конференции «Фабрика совершенствования науки и техники». Конф. «Оптимизация производства ферросилиция», Новокузнецк, , 1997, № 4, с.3. С. 126–131.
Google ученый
Гилязов У.Ш., Юрковский И.М., Константинова Д.С., Рогалин М.И. Графитизация антрацита, Химия. Тверь. Топл. (Москва) , 1984, вып. 4. С. 84–87.
Google ученый
Атманский А.И., Кондрашенкова Н.Ф., Осташевская Н.С. и др. Трансформация структуры и свойств антрацита Горловской впадины в процессе высокотемпературной обработки // Хим.Тверь. Топл. (Москва) , 1977, вып. 4. С. 43–46.
Google ученый
Фиалков А.С., Гилязов У.Ш., Самойлов В.С. и др. Изменение пористости антрацитов в процессе их термообработки // Химия. Тверь. Топл. (Москва) , 1983, вып. 4. С. 71–74.
Google ученый
Гасик М.И. , Гриншпунт А.Г. Влияние термической обработки на структуру и свойства термоантрацита для углеродных масс самоотжигающихся электродов.Тверь. Топл. (Москва) , 1981, вып. 4. С. 76–83.
Google ученый
Солдатов А.И., Кашлев И.М., Сидоров А.Н., Кузин В.В. Подготовка листвянского антрацита для производства электродной массы в Антрациты Горловского бассейна (Антрациты Горловского бассейна) , Новосибирск, 1996 г. С. 79–82.
Google ученый
Страхов, В.М., Кашлев И.М., Анализ качества горловского антрацита как сырья для производства термоантрацита в электрокальцинаторе в Антрацитах Горловского бассейна (Антрациты Горловского бассейна) , Новосибирск, 1996, с. 82–86.
Google ученый
Страхов В.М., Кашлев И.М., Павлов С.Ф., Кравцов К.И. Термическая обработка листвянского антрацита как наполнителя для производства электродной массы на Кузнецком заводе ферросплавов, в Проблемы и перспективы развития ферросплавного производства. (Проблемы и перспективы развития производства ферросплавов) , Актобе, 2003, с.396–401.
Google ученый
Брыляков В.И., Бондарев А.А., Гребенев В.С. и др. Патент РФ 2234037, 2004.
. Google ученый
Павлов С.Ф., Кашлев И.М., Астахов А.В. Энергосбережение на Кузнецком заводе ферросплавов, Вестн. ТЭК Ресур. Кузбасса , 2004 г., вып. 7. С. 34–36.
Google ученый
Хитрик С.И., Гасик М.И., Кушнарев В.Г., Лагунов Ю.В. Удельное электрическое сопротивление самоспекающихся электродов при высоких температурах // Электротермия . 1966. 54, стр. 11, 12.
Google ученый
Воробьев И.П., Электротермия восстановительных процессов , Екатеринбург: Урал. Отд., Росс. Акад. Наук, 2009.
. Google ученый
Мизин В.Г., Уканаков П.М., Серов Г.В. Контактное электрическое сопротивление углеродсодержащих восстановителей // Кокс хим. Химии. , 1975, нет. 2. С. 22–25.
Google ученый
(PDF) Моделирование потока газ-твердое тело в печи для прокаливания
Моделирование потока газа и твердых веществ в печи
Хайян Ло
Кафедра машиностроения, Гонконгский политехнический университет
Хунг Хом, Коулун , Гонконг
электронная почта: luohust @ hotmail.com
Поступила в редакцию: 10 сентября 2010 г., принята в печать: 24 января 2011 г.
Реферат
В данной статье исследуется двухфазный поток газа и твердого вещества в обжиговой печи. Турбулентная жидкая фаза
рассчитывается с использованием модели с двумя уравнениями RNG k-
ε
в системе Эйлера
, в то время как твердая фаза, обрабатываемая с помощью стохастической траекторной модели частиц
, рассчитывается в рамках лагранжевой системы. Схема потока
характеристики жидкой фазы и траектории частиц твердой фазы были предсказаны
в зависимости от диапазона условий потока и различных размеров частиц. Результаты расчетов
предоставили полезную информацию при предварительном просмотре регулирования кинетики
, двухфазного газо-твердого вещества в печи для обжига.
Ключевые слова: печь обжига; Модель стохастической траектории частиц
1. ВВЕДЕНИЕ
В цементной промышленности существует множество видов производственных технологий. В процессе обжига клинкерного цемента
основная система управляется печью обжига [1].
Для качественно выполненной печи обжига она должна иметь ряд важных характеристик, таких как эффективность
, эксплуатационная надежность, скорость растворения сырья, скорость сжигания угля, выработка и контроль
загрязняющих веществ, постоянство горения. и способность антифлуктуации.В обжиговой печи
поток газа оказывает глубокое и продолжительное воздействие на горение угля и разложение сырьевой муки,
, что обусловлено следующими факторами. Во-первых, однородность распределения и время пребывания сырой муки
зависят от основных характеристик потока. Во-вторых, правильное расположение дымовых газов, выходящих
из задней части печи для обжига, и третичного воздуха имеет огромное влияние на стабилизацию и
, поддерживая высокую эффективность сгорания.Таким образом, организация газового потока в печи для обжига
стала в последние годы важной проблемой в цементной промышленности.
На сегодняшний день общепринятые методологии определения характеристик печи для обжига включают теоретический анализ
, холодные испытания и испытания на месте. Чтобы получить представление, предпочтительно использовать вычислительные методы
для точного моделирования двухфазного потока твердое тело-газ в печи для обжига
.Численные исследования двухфазного потока твердое тело-газ в печи для обжига были довольно ограничены из-за присущей ему сложности физики потока. Giddings et. др. [2–3], Ye et. [4–6]
и Ван [7] выполнили некоторые работы по кинетике и аэродинамике горения в различных типах печи для обжига
, но их работа не предоставила достаточной информации о кинетике
твердого газа.