Технология выплавки чугуна в индукционной электропечи
Загрузка и расплавление.
В крупных зарубежных литейных цехах, где смонтированы индукционные установки для плавки чугуна, как уже указывалось выше, операции загрузки шихты в печи механизированы и автоматизированы.
Подача материалов в печь производится в определённой последовательности. Например, через каждые 20 минут в печь загружается 200 кг стального скрапа, 160 кг возврата и чушкового чугуна, через каждые 40 минут в печь вводится 22 кг кокса до тех пор, пока в чугуне не будет обеспечено требуемое содержание углерода.
Шихта не должна падать в тигель с большей высоты во избежание его повреждения. Лучше, если шихта сползает. Сползание шихты может быть обеспечено с помощью склизов, вибрационных конвейеров, бадьёй специальных конструкций. Удар шихты о футеровку должен быть боковым, а не верхним, так как в первом случае футеровка работает на сжатие, а во втором на срез, причём при этом ударной нагрузке подвергается наиболее хрупкая ошлакованная часть футеровки.
Большое значение при плавке чугуна в индукционной печи имеет правильный выбор режима в зависимости от ёмкости печи, производительности, величины кусков шихты, потребности в металле и т.д.
При выборе частоты тока в индукционной печи необходимо учитывать ёмкость печи, величину кусков шихты и т.д. Так, например, печь малой ёмкости имеет лучшее показатели при высоких частотах, а печь большей ёмкости – при низких. Если же печь работает на частотах меньших, чем оптимальная (при данных размерах печи), то будет наблюдаться сильное перемешивание металла, что может привести к увеличению количества неметаллических включений в металле. Кроме того, наблюдается большая потеря металла за счёт его окисления. В этом случае некоторые виды скрапа (например, стружка, если в печи нет жидкого металла) не могут быть применены, а срок службы футеровки сокращается втрое. При частоте, выше оптимальной, перемешивание ванны металла очень слабое, что отражается на гомогенности металла, находящегося в печи.
С повышением частоты можно применять более мелкие куски шихты. Если, однако, в печи есть жидкий металл, то это условие можно не соблюдать. При данной требуемой производительности печи с понижением частоты тока потребляемая мощность становится меньше. С увеличением ёмкости эта разность увеличивается. Удельный расход энергии у печей промышленной частоты меньше, чем у высокочастотных печей . Исключением являются печи ёмкостью менее 1т.
Перегрев металла в печах промышленной и промежуточной частоты протекает быстро. Скорость перегрева в первых 10°С /мин, во вторых — 30°С/мин. После достижения в печи необходимой температуры металла следует подавать ток небольшой силы. В печах большой ёмкости (10-15т) для поддержания температуры металла постоянной требуется 20-30 кВт•ч на тонну жидкого металла в час. Для нагрева чугуна до 1200°С необходимо 410-430 кВт•ч на тонну.
Получение синтетического чугуна.
Синтетическим называют чугун, получаемый в индукционных печах путём переплавки стружки, стальной обрези и других малоценных отходов с дальнейшим науглероживанием расплава и доведением его химсостава до заданного. В работе приведены результаты исследований процесса получения синтетического чугуна из стружки в индукционной высокочастотной печи с кислым тиглем ёмкостью 150кг.
Установлено, что общий угар металла определяется номенклатурой шихтовых материалов и их окисленностью, способом ввода ферросплавов и карбюризатора, температурой нагрева и выдержкой металла. При выплавке чугунов из стальной стружки угар металла меньше по сравнению с выплавкой из чугунной в 2-2,5 раза; при вводе ферросплавов и карбюризатора в завалку он меньше примерно в 1,5 раза, чем при вводе в жидкий металл. Так как стружка всегда в какой-то степени загрязнена, различают весовой и истинный угар металла. Для определения последнего весь образующийся шлак собирали, взвешивали и анализировали. По этим данным рассчитывали количество в нём окислов Fe,Mn,Cr,Si, вносимых шихтой, а разницу относили на засоренность шихты. Истинный угар металла меньше весового на 20-25%. Истинный угар при выплавке синтетических чугунов из стальной стружки составлял от 0,3 до 6,2%, а из чугунной 5,3-9,0%. Авторы это объясняют большей поверхностью и окисленностью чугунной стружки по сравнению со стальной, что подтверждается и количеством образующегося шлака и содержанием в нём окислов Fe, Mn, Si.
Степень и скорость усвоения ферросплавов и карбюризатора, равно как и угар элементов, зависят от способа их ввода, температуры нагрева и выдержки металла. В качестве карбюризатора использовали бой графитовых электродов. Степень и скорость усвоения углерода зависят ещё от размера кусков карбюризатора: если они больше 40мм-скорость усвоения углерода уменьшается на 20-25%. Скорость усвоения углерода жидким металлом с 1,3-1,62%С, 0,15-0,46%Si при 1400-1470°С достигает 0,12% в минуту, в среднем 0,09%, продолжительность науглероживания до 3,2-3,6%С составляет 22-34 минуты, усвояемость углерода из электродного боя – 80-85%.
Для ввода в расплав Si использовали Cu45. Угар Si при вводе Cu45 в жидкий металл выше, чем при вводе в завалку, в 1,4-1,5 раза, он почти не зависит от выдержки металла, но изменяется с нагревом. Кремний выгорает только до 1420-1450°С, а при дальнейшем нагреве восстанавливается углеродом, и при 1500-1550°С наблюдается его пригар с образованием окиси углерода. Скорость усвоения Si малоуглеродистым жидким чугуном с 1,3-1,62%С 0,15-0,46%Si при 1420-1460°C составляет в среднем 0,1% в минуту, а высокоуглеродистым чугуном при этой же температуре – только 0,04% в минуту.
Марганец усваивается из Mn 1 на 80-90% со скоростью (при 1460°С) 0,1% в минуту; угар Mn для большинства плавок не превышает 18% и зависит от способа ввода ферромарганца, от температуры нагрева и почти не зависит от выдержки. При вводе ферромарганца в жидкий металл одновременно с ферросилицием и боем электродов Mn горит меньше, чем при вводе в заливку. Степень и скорость усвоения Cr жидким чугуном определяется температурой и при 1365°С составляет 0,08%, а при 1470°С-0,18% в минуту, угар равен 31,5 и 5,5% соответственно.
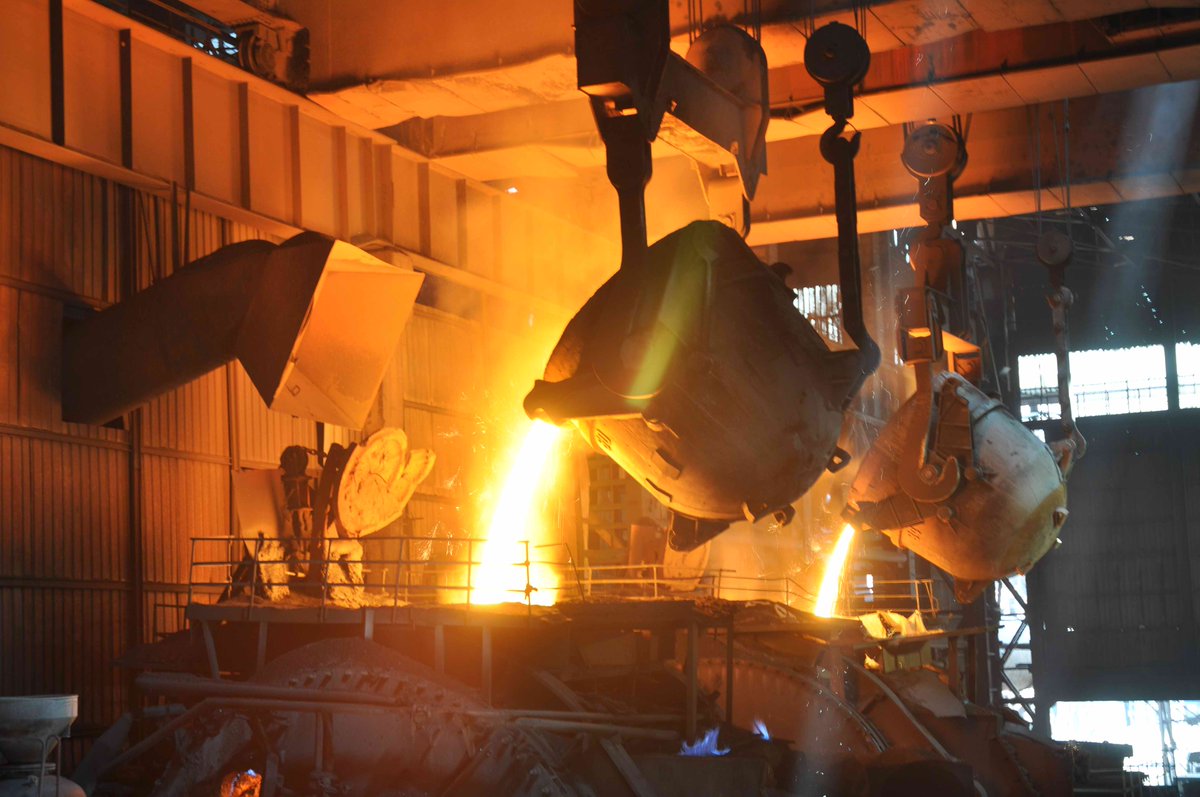
Механические свойства синтетических чугунов несколько выше ваграночных с равным углеродным эквивалентом C_э, зависят от исходных шихтовых материалов, состава, температуры нагрева и выдержки металла. Структура синтетических чугунов при близких температурах заливки зависит не только от их состава, но и от исходных шихтовых материалов. У чугунов с равным C_э структура металлической основы примерно одинаковая, но форма и количество графита зависят от исходных шихтовых материалов. Так, у чугунов, полученных из стальной стружки, включения графита крупные, изолированные и компактные, либо это очень длинные слабо завихренные пластины с притупленными окончаниями. Напротив, у чугунов, полученных из чугунной стружки, пластины графита мелкие и средние, сильно завихренные, пересекающиеся между собой. Разница в количестве и форме графита при равном C_э и близких температурах заливки сказывается на механических свойствах: у чугунов, выплавленных из стальной стружки, они более высокие, чем у чугунов из чугунной стружки.
Содержание азота в чугунах из стальной стружки несколько выше, чем в ваграночных и синтетических, выплавленных из чугунной стружки. Это объясняется болеем высоким процентом азота в самой стружке и внесением его ферросплавами, которых при этом вводится в несколько раз больше. Кислорода во всех синтетических чугунах почти столько же, сколько и в ваграночных, а в некоторых случаях даже значительно меньше. Содержание водорода несколько выше.
Наиболее важным металлургическим процессом при плавке синтетического чугуна в индукционной электропечи является науглероживание расплава, так как вся технико-экономическая целесообразность применения индукционных электропечей основана на применении в качестве шихтовых материалов стружки и других малоценных отходов. Науглероживание металла можно производить загрузкой углеродосодержащих добавок прямо в шихту, что, например, часто наблюдается в американской практике. На одном из заводов науглероживание проводится коксом, загружаемым или в шихту, или непосредственно в жидкий металл. При науглероживании коксом усвоение углерода в металле ниже требуемого, то в ванну металла вводят графит, а если оно завышено – добавляется стальной скрап. Дополнительное науглероживание, как правило, приходится производить в среднем для одной плавки из десяти. При надлежащем уровне шихтовки обеспечивается постоянный состав чугуна с заданным содержанием углерода в течение всей смены независимо от остатка металла в печи. Рекомендуется также вводить пылевидный графит в струе газа на зеркало металла с последующей продувкой газа. Можно вводить углеродосодержащие добавки в специальном встряхивающем ковше. После того как содержание углерода поднялось до необходимого значения, целесообразно довести и содержание кремния до желаемого.
Усвоение углерода металла в значительной степени зависит от времени его растворения, температуры металла и химического состава исходного металла. Растворение углерода – процесс, идущий с поглощением тепла. Поэтому в период науглероживания необходимо поддерживать температуру металла. Если науглероживание вещества вводятся на ванну жидкого металла, то предварительно необходимо тщательно очистить зеркало металла от шлака.
Большая работа по изучению процессов науглероживания проведена в институте проблем литья АН УССР.
Экспериментальная работа большей частью проводилась в литейном цехе каунасского завода «Центролит » . Опытные плавки вели в тигельных индукционных электропечах с кислой футеровкой ИЧМ-1А, ИЧТ-6, ASEA-8, ёмкостью 1,6, и 8т. В качестве шихтовых материалов применяли дроблёную стальную и чугунную стружку, ферросилиций Cu45 и Cu75, науглероживающие реагенты: бой электродов, электродный порошок, сланцевый кокс, графит.
Электромагнитное перемешивание жидкого сплава в электропечах промышленной частоты оказывает сильное влияние на процесс науглероживания. Установлено, что высокая интенсивность перемешивания в значительной степени способствует быстрому и полному усвоению карбюризатора(рис. 1а). науглероживание является эндотермическим процессом. Поэтому происходит падение температуры в среднем на 50°С на 1% усвоенного углерода.
Индукция.
В результате исследования четырёх карбюризаторов: боя электродов, сланцевого кокса, тигельного графита, электродного порошка – и обработки опубликованных данных по растворимости углеродосодержащих материалов установлена общая для карбюризаторов зависимость усвоения углерода жидким сплавом от содержания углерода в реагенте (рис. 1б). усвоение науглероживателя в печах промышленной частоты вследствие электромагнитного перемешивания на 7-8% выше, чем в высокочастотных печах. Размер частиц реагента для печей ёмкостью 6-8т рекомендуется в пределах 5-10мм, так как более мелкие частицы и пылевидная фракция подвергаются распылению и окислению, а крупные частицы растворяются в металле длительное время.
Сравнение технологических режимов загрузки карбюризатора по двум вариантам: 1 — периодическое введение вместе с шихтой и 2 — введение карбюризатора в конце плавки – показало, что периодическое добавление науглероживателя сокращает продолжительность плавки в среднем на 5 минут на 1т выплавляемого чугуна, снижает расход электроэнергии в среднем на 38 кВт•ч/т, хотя даёт несколько меньшее усвоение реагента жидким сплавом (3,71% против 3,85%). Способ периодического введения карбюризатора признан более экономичным.
Десульфурация чугуна.
Если чугун из индукционной печи идёт на переработку в высокопрочный, то необходимо проводить десульфурацию металла. Десульфурация ведётся различными реагентами, вводимыми в металл в струе газа, или другими способами. Весьма эффективно, как уже отмечалось, вести десульфурацию карбидом кальция CaC2, вводимым в металл. Рекомендуется также в металл вводить соду в парообразном или измельчённом состоянии. После обработки металла десульфурирующими реагентами содержание серы в печи снижается до 0,001-0,015%. Степень десульфурации увеличивается с повышением температуры металла, что объясняется уменьшением его вязкости и увеличением скорости диффузии. При очень высоких температурах, около 1600°С, наблюдается частичное снижение степени десульфурации как вследствие реакции карбида кальция с кислородом воздуха и с футеровкой тигля, так и вследствие спекания карбида кальция при 1550°С.
Степень десульфурации зависит и от первоначального содержания серы в чугуне, с понижением которого требуется относительно большой расход карбида кальция. Если серы в исходном чугуне менее 0,04%, то расход обессеривающей добавки очень велик. Чем выше содержание углерода в чугуне, теми лучше обессеривающие действие карбида кальция. Образующийся под действием карбида кальция свободный углерод растворяется в жидком чугуне или выделяется из него в зависимости от его эвтектичности и температуры; практически науглероживание чугуна не наблюдается или эффект его невелик.
В ванну индукционной печи карбид кальция вводится порциями. Крупные зёрна обессеривают чугун лучше, чем мелкие, в противоположность другим способам десульфурации. При постоянном применении карбида кальция следует учитывать понижение стойкости кислой футеровки.
Плавка чугуна в индукционных печах
Плавка чугуна в индукционных печах
Категория:
Литейные цеха
Плавка чугуна в индукционных печах
В индукционных тигельных печах начали плавить чугун около четверти века назад. Однако из-за дефицита электроэнергии, несовершенства печей и кладки широкого применения такая плавка не получила. Основным плавильным агрегатом оставалась вагранка.
Технический прогресс в машиностроении, связанный с повышением надежности и долговечности машин, уменьшением их веса, предъявляет все большие требования к качеству чугунных отливок, что ведет к усовершенствованию конструкций вагранок. Вагранки оборудуются рекуператорами для подогрева воздуха, мощными вентиляторами и др. Появляются коксогазовые и газовые вагранки. Однако несмотря на существенное изменение конструкции вагранок, преимущества горячего дутья, во многих случаях ваграночный чугун все же не удовлетворяет требованиям относительно пределов колебания химического состава, содержания вредных примесей и степени перегрева металла.
Для плавки чугуна все большее распространение получают индукционные печи промышленной частоты. Начиная с конца пятидесятых годов плавка чугуна в электропечах и особенно в индукционных печах в промышленно развитых странах начинает вытеснять ваграночную плавку. За период с 1963 по 1968 г. в США количество работающих электропечей для плавки чугуна возросло до 4000. Из них около 70% составляют индукционные печи промышленной частоты. За последние 6—7 лет в США число вагранок сократилось почти вдвое, а число электропечей возросло в 2,5 раза. В Западной Европе также идет процесс замены вагранок электропечами.
В СССР первый блок цехов с индукционными печами промышленной частоты вместо вагранок начал работать в 1963 г. на Каунасском чугунолитейном заводе. Институт «Ленгипротяжмаш» в течение ряда лет в проектах литейных цехов предусматривает индукционные печи промышленной частоты.
Главное преимущество индукционной плавки чугуна перед ваграночной состоит в возможности управлять процессом перегрева чугуна в широком интервале по температуре и времени, осуществлять более глубокую металлургическую обработку расплава, точно выдерживать химический состав и получать чугун высокого качества. К преимуществам этих печей относится возможность переплава небрикетированной чугунной стружки до 40% веса металлической завалки, отходов тонколистового железа, что снижает расход чушкового чугуна и лома. Допустимо использование и компактных отходов металла большого веса и крупных размеров, существенно ограниченного при плавке в вагранке. При плавке снижается угар Si и Мп, удешевляются шихтовые материалы, общий угар находится в пределах 2—0,6%, сокращается штат обслуживающего персонала и на 30% — потребность в кубатуре помещения за счет высоты здания.
При плавке чугуна в индукционных печах резко снижается содержание S в расплаве, что облегчает получение чугуна с шаровидным графитом. Существенно улучшаются санитарно-гигиенические условия труда, так как обслуживающий персонал не подвергается вредным воздействиям тепла, пыли, шума, газов от сжигания топлива. Последний фактор особенно важен в черте города и населенных пунктах, так как при работе индукционных печей воздушный бассейн засоряется во много раз меньше, чем при ваграночном процессе, при котором требуются громоздкие, дорогостоящие средства очистки. Снижается удельный расход огнеупорных материалов — для индукционной печи он составляет 3 кг/т, дуговой печи с кислой футеровкой — 17,6 и для вагранки — 27 кг/т.
Индукционные печи гибки в работе, обеспечивают отбор металла большими порциями или непрерывно в зависимости от условий производства при высокой стабильности состава жидкого чугуна.
Расчеты, зарубежная практика и практика Каунасского завода «Центролит» подтверждают полную целесообразность широкого применения индукционных печей вместо вагранок. При использовании дешевой шихты себестоимость тонны жидкого металла может снижаться на 30—40%. По сравнению с простыми вагранками ин-
Аукционные печи более капиталоемки (на 10 руб/т жидкого металла в год) вследствие высокой стоимости оборудования. Однако при использовании дешевой шихты срок окупаемости капитальных затрат не превышает полугода. При наличии у вагранок установок для подогрева дутья, очистки газов, охлаждения футеровки, автоматического управления режимов плавки и прочего разницы в стоимости установок нет.
Рис. 1. Схема вариантов установки индукционных печей: 1 — основной трансформатор; 2 — вспомогательный трансформатор; 3 — конденсаторные батареи; т/п — трансформаторная подстанция
Действительная производительность печей принята равной 70% от теоретической с учетом времени на загрузку шихты, выпуск металла из печи и подготовку тигля к плавке.
На рис. 1, а показана установка из двух тиглей и одного основного трансформатора, где один тигель является разервным; на рис. 4.22, в — установка из трех тиглей и двух основных трансформаторов, два тигля работают одновременно, а один резервный; на рис. 1, б — установка, которая имеет два тигля и один вспомогательный трансформатор. Дополнительный трансформатор позволяет переключать любую из двух печей на работу в миксерном режиме и вести плавку и раздачу металла непрерывно. Производительность печей такой установки увеличивается и определяется умножением нормативной на коэффициент 1,3. Установка печей на рис. 1, г имеет три тигля, два основных и один вспомогательный трансформатор. Каждый из тиглей может работать в миксерном режиме. Мощность установки также определяется умножением нормативной на коэффициент 2,6—2,7. Плавка и выдача металла ведется непрерывно. При проектировании литейных цехов с применением индукционных печей возможны и другие схемы компоновки печей и электрооборудования.
При разработке проектов с применением индукционных печей необходимо предусматривать специальные средства для удаления влаги, масла, эмульсии и других жиросодержащих веществ в стружке и других отходах, направляемых на плавку. По данным Каунасского завода «Центролит», использующего в качестве шихты чугунную стружку россыпью, в 1 т стружки содержится более 30 кг масла и эмульсии.
Плавка необработанной шихты загрязняет цех копотью, при загрузке возможны возгорания и хлопки, щелочные составляющие эмульсии ускоряют разрушение футеровки, а сернистые составляющие масла насыщают металл серой. В итоге качество отливок ухудшается и снижаются технико-экономические показатели.
Подготовку шихты можно производить тепловым методом в печи при 500—700 °С, где удаляются практически все летучие и горючие вещества. Чтобы избежать окисления стружки, создают в печи нейтральную или восстановительную атмосферу.
Для обезжиривания легковесных металлоотходов применяют также промывку слабощелочными растворами едкого натра (40— 50% NaOH и 0,5—1% ДС-РАС — поверхностно-активное вещество). Операция промывки производится методом душирования сверху в специальной емкости. Продолжительность обезжиривания составляет 5—10 мин. Раствор подогревают до 60—80 °С, что облегчает последующую сушку шихты за счет собственного тепла.
Серьезным резервом в снижении стоимости плавки и повышения производительности индукционных печей промышленной частоты является предварительный подогрев шихты более дешевым топливом — мазутом или газом. Загрузка шихты, имеющей температуру 650—700 °С, обеспечивает повышение производительности печи на 40 и снижение расхода электроэнергии на 30%.
Выплавка металла в чугунолитейных цехах может осуществляться различными плавильными агрегатами или их сочетанием, однако в большинстве случаев вопрос стоит о выборе между вагранкой, индукционной и электродуговой печью. От выбора плавильного агрегата во многом зависят технико-экономические показатели работы плавильного отделения.
Для установления оптимального варианта применения плавильных печей В. М. Шестопалом и И. А. Иоффе было проведено сравнительное технико-экономическое исследование семи основных плавильных агрегатов применительно к типовым плавильным участкам мощностью 15 000—140 000 т для пяти основных марок серого чугуна по трем наиболее характерным для большинства районов СССР условиям стоимости 1 кВт установленной мощности (38 р. 8 к., 43 р. 10 к., 53 р.).
Исследование показало следующее.
1. Наиболее перспективным плавильным агрегатом для плавки чугуна в настоящее время является индукционная тигельная печь промышленной частоты с установкой для подогрева шихты и мик-серным режимом, причем особенно высокие технико-экономические показатели — при выплавке синтетических чугунов на дешевой шихте. При использовании дорогой шихты, рассчитанной для плавки в коксовой вагранке, приведенные затраты будут выше, чем при плавке в коксовых и газовых вагранках и дуплекс-процессах на их основе. Однако, учитывая такие факторы, как качество жидкого чугуна (особенно при выплавке специальных марок), гибкость в работе при выплавке различных марок чугуна, условия труда на плавильном агрегате (газы, пыль, шум), целесообразно применять индукционные тигельные печи промышленной частоты с установками для подогрева шихты и миксерным режимом.
2. Без дешевой шихты и при высокой стоимости электроэнергии, когда нет необходимости в выплавке высоких и специальных марок чугуна, целесообразно применять дуплекс-процессы: коксовая вагранка + индукционная печь промышленной частоты и газовая вагранка + индукционная печь промышленной частоты.
3. Двухчастотные индукционные печи (плавка на высокой или средней частоте, доводка и выдержка металла на промышленной частоте) хотя и имеют приведенные затраты на 1 т жидкого чугуна больше, чем индукционные тигельные печи промышленной частоты, однако дают ряд преимуществ: занимают меньше площади, ускоряют плавку на холодной завалке и мелкой шихте, дают возможность плавить наряду с чугуном и сталь. Поэтому двухчастот-ные печи целесообразно устанавливать при реконструкции цехов, имеющих минимальные площади для установки плавильных агрегатов, а также в цехах, выпускающих ремонтное литье с частой сменой марок выплавляемого чугуна и кратковременным использованием плавильных печей в течение суток и в смешанных чугуно-сталелитейных цехах.
4. Дуплекс-процесс дуговая печь + индукционная печь промышленной частоты ввиду высоких приведенных затрат целесообразно применять в чугунолитейных цехах только в случаях плавки хромистых чугунов с особо низким содержанием фосфора и серы, на загрязненной другими металлами и неизвестного состава шихте и в смешанных чугуносталелитейных цехах.
При сравнении вариантов плавильных агрегатов необходимо учитывать наряду с экономической эффективностью и такие технологические факторы, как качество жидкого чугуна, гибкость в работе при выплавке последовательно различных марок чугуна, условия работы на плавильном агрегате, которые в отдельных случаях могут иметь решающее значение при выборе плавильного агрегата.
При выплавке жидкого металла для ковкого чугуна наибольшее распространение получили дуплекс-процессы вагранка ‘электродуговая или индукционная печь. Например, по схеме вагранка’ электродуговая печь работают литейные цехи Горьковского автозавода и Тульского комбайнового завода, по схеме вагранка + индукционная тигельная печь — литейный цех ковкого чугуна Кутаисского автомобильного завода и др.
Однако и здесь индукционные печи промышленной частоты имеют преимущества. Опыт работы литейного цеха Запорожского арматурного завода, оборудованного индукционными тигельными печами промышленной частоты, специализирующегося на массовом выпуске арматуры из ковкого чугуна, оценивается положительно, особенно при использовании в составе шихты стружки.
В промышленно развитых странах, кроме индукционных печей, для плавки чугунов широко применяется дуплекс-процесс вагранка + -риндукционная печь, который решает проблему плавки различных марок синтетического чугуна с низким содержанием серы, пригодным для получения высокопрочных чугунов.
В ФРГ применяется дуплекс-процесс вагранка + индукционная печь, где используются 10-тонные вагранки с подогревом дутья и 5-тонная индукционная печь. На заводе «Вольво» в Швеции используется дуплекс-процесс вагранка + канальная печь для отливок блоков цилиндров, головок блоков. В 10-тонной вагранке с подогревом дутья до 500°С выплавляется синтетический чугун на шихте из стального лома, возврата и 10% доменного чугуна. Металл из вагранки в 20-тонную канальную печь поступает по желобу и подогревается до 1450—1470°С. Стойкость футеровки ванны — три года. По такой же схеме вагранка + канальная печь работают литейные цехи шведских фирм «Эббес Брук» и «Скания Вабис».
На автомобильной фирме «Крейслер» в США две вагранки производительностью по 50 т/ч с подогревом дутья до 750°С работают в дуплекс-процессе с тремя канальными печами емкостью до 100 т, одна из которых — резервная. Чугун из вагранки в канальную печь поступает по желобу непрерывно и перегревается до 1530—1550°С. Он используется для отливок блоков цилиндров, головок блоков и других деталей. В литейном цехе фирмы «Atlas Foundry Со» (США) чугун с низким содержанием серы выплавляется в индукционных печах, а затем подается в индукционную тигельную печь, где он дополнительно науглероживается, а на заводе фирмы ASEA для получения чугуна с шаровидным графитом используется дуплекс-процесс индукционная тигельная печь + индукционная канальная печь, где две 8-тонные тигельные печи работают с одной 10-тонной канальной.
На Горьковском автозаводе для выплавки магниевого чугуна применяется дуплекс-процесс индукционная тигельная печь промышленной частоты + электродуговая печь. В проекте реконструкции литейных цехов завода для синтетического чугуна запроектирован дуплекс-процесс индукционная тигельная печь-канальная печь. Ваграночный процесс и дуплекс-процесс вагранка + дуговая печь заменяют дуплекс-процессом металлургическая вагранка+” + канальная печь, где будут выплавляться чугуны марки КЧ35-10, СЧ24-44, СЧ18-36.
Рис. 2. Типовая схема организации дуплекс-процесса металлургическая вагранка + индукционная канальная печь: 1 — индукционные канальные печи; 2 — металлургические вагранки
Типовая схема организации дуплекс-процесса металлургическая вагранка + канальная печь представлена на рис. 3. Из вагранки производительностью 30 т/ч с подогревом дутья до 500 — 600 °С чугун поступает по желобу в канальную печь полезной емкостью 45 т. Вагранка плавит без выбивки в течение недели.
При выплавке чугуна индукционные печи могут работать в различных режимах.
Если идут плавки одного химического состава, в печи может оставаться «болото» жидкого металла. Отбор металла производится определенными порциями. После каждого отбора печь загружается таким же количеством холодной шихты.
На рис. 4., в показана диаграмма для скользящего химического состава, когда расплав одного состава может использоваться для приготовления другой марки сплава. В этом случае печь может работать с «болотом» жидкого металла. Величина «болота» зависит от расчетного химического состава.
Печи, обеспечивающие работу конвейеров, должны работать по графику. Для этого на все работающие печи составляется график работы печей и выдачи металла на конвейер.
Дуплекс-процесс вагранка-индукционная печь может быть двух типов. Первый тип — две печи тигельные, работающие попеременно: одна — на заполнение, другая — на выдачу жидкого металла. По данным В. Трещалина, емкость миксеров, обеспечивающих стабилизацию химического состава, главным образом по кремнию составляет 0,8 q каждый (q — часовая производительность вагранки). При использовании канальных миксеров, где обычно остается до 30% жидкого металла, емкость миксера увеличивается на 30%.
При организации второго типа вагранка оборудуется одним миксером, в который чугун поступает непрерывно и раздается на заливку.
Реклама:
Читать далее:
Плавка стали в электродуговых печах
Статьи по теме:
Плавка чугуна в электрических печах
Плавка чугуна в электрических печах
Категория:
Литейное производство
Плавка чугуна в электрических печах
Высокопрочные марки серого чугуна СЧ35-56, СЧ40-60, СЧ44-64 могут быть получены модифицированием и только при плавке в электропечах.
Преимущества электроплавки заключаются в возможностях проведения металлургической обработки сплава, легкой регулировки ее теплового режима, получения чугуна высокого качества, с заданным химическим составом, любой марки. Очень важное значение имеет и возможность использования при электроплавке Дешевых шихтовых материалов в виде легковесных отходов металлообработки (выштамповка, стружка), отходов кузнечного производства, лома и т. п., высвобождение дефицитного кокса, улучшение состояния воздушного бассейна.
При шихтовке следует учитывать, что содержание углерода чугунной стружке из-за выкрашивания его в виде графита всегда : еньще, чем в обрабатываемой отливке.
Пуск индукционной печи осуществляют с помощью пусковой болванки. Для этого отливают чугунную болванку требуемого химического состава массой около 1/2 общей емкости тигля и формой, соответствующей форме тигля, но с несколько меньшим диаметром. Болванку помещают в тигель и расплавляют. После этого приступают к загрузке в определенной последовательности составляющих шихты. Печь в это время должна быть отключена. На зеркало расплавленного металла сначала загружают электродную, а затем стальную стружку и выштамповку, после этого чугунную стружку и в последнюю очередь возврат собственного производства. После полного расплавления шихты в печь вводят ферросплавы.
Металл в печи перегревается до температуры 1350—1400 °С. После достижения этой температуры печь выключают и отбирают пробы на отбел, твердость и на химический состав. При выключенной печи металл выдерживают 10—20 мин. В это время производят все анализы. Если металл не отвечает требованиям по отбелу, твердости и химическому составу, производят корректировку его состава. Для повышения содержания углерода добавляют электродную стружку, кремния — ферросилиций и марганца — ферромарганец.
По окончании корректировки отбирают пробы для повторных исследований. После получения удовлетворительных результатов температуру металла доводят до 1450—1470 °С. Замер ее в печи производят оптическим пирометром или термопарой погружения-
Из печи металл выдается в ковши разной емкости (в зависимости от емкости печи и весовой характеристики отливок). Во всех случаях в печи должен оставаться жидкий металл в количестве 25—30% от общей емкости, на который вновь загружают шихт) в указанной выше последовательности.
При выплавке чугуна высоких марок (СЧ28-48, СЧ32-52 и др.) металл подвергается модифицированию ферросилицием ФС75 в количестве 0,7—0,8% от массы металла в ковше. Модификатор подается на струю при выдаче металла в ковш после заполнения 1/3 его емкости. Модификатор должен быть сухим и просеянным через сита с ячейками 10 и 2,5 мм.
Тигельные индукционные печи. Для электроплавки наибольшее распространение в нашей стране и за рубежом получили электрические индукционные печи промышленной частоты. В зависимости назначения они подразделяются на индукционные тигельные (ИЧТ), тигельные миксеры (ИЧТМ) ц канальные миксеры (ИЧКМ).
Рис. 1. Индукционная тигельная печь.
Стоимость индукционных печей и современных вагранок практически одинакова, однако срок окупаемости первых приблизительно в 2 раза меньше благодаря более низкой стоимости шихтовых материалов и самих отливок. Все это дает основание полагать, то электроплавка в индукционных печах уже в ближайшее время получит самое широкое распространение.
Индукционные тигельные печи работают как трансформатор без железного сердечника, первичной обмоткой которого является многовитковая катушка индуктор, а вторичной и одновременно нагрузкой — расплавляемый металл. Принцип работы печи основан на поглощении электромагнитной энергии металлической шихтой, которая заложена в тигель, помещенный в переменное магнитное поле. Нагрев и расплавление шихты происходят в результате наведения электрического тока и выделения тепла в кусках шихты.
Индукционная тигельная печь (ИЧТ) емкостью 6 т представлена на рис. 1. Она состоит из металлического каркаса, тигля, индуктора, крышки с механизмами подъема, рабочей площадки, токо- и водоподводящих устройств, заключенных в кожухе. Каркас печи представляет собой сварную конструкцию из листовой стали. Под сливным носком расположена ось поворота печи. Посредством гидравлического механизма осуществляется наклон печи в одну сторону на любой угол до 100° для выдачи металла.
Главной частью печи является индуктор, представляющий собой медную водоохлаждаемую трубку. Воротник печи вместе с рабочей площадкой составляет съемную сварную конструкцию. Воротник футеруется шамотными кирпичами, а для отвода дымовых газов предусмотрен канал, расположенный непосредственно под площадкой. Плавильным пространством печи является тигель. Тигель изготовляется из специальной огнеупорной массы. Операции его набивки непосредственно в печи должны выполняться с особой
тщательностью и с применением химически чистых материалов. Высокие требования к качеству изготовления тигля объясняются тем что он работает в неблагоприятных условиях: внутренняя поверхность его обогревается жидким металлом и имеет высокую температуру, а наружная соприкасается с индуктором, охлаждаемым водой.
Для футеровки индукционных тигельных печей применяется кварцевый песок либо молотый кварцит. В качестве связующей добавки используется борная кислота, которая, являясь плавнем, обеспечивает быстрое спекание футеровки.
Рис. 2. Индукционная канальная печь-миксер: 1 — индукционные единицы; 2— механизм вращения; 3 — токопро-вод; 4 — кожух; 5 —футеровка.
Канальные индукционные печи со стальным сердечником получили широкое применение для плавки медных сплавов (бронз, латуней). Из литературы известно и об использовании их для плавки чугуна на твердой завалке.
Однако наибольшее распространение имеют канальные печи-миксеры, работающие по Дуплекс-процессу: вагранка — индукционный канальный миксер или индукционная тигельная печь — канальный миксер.
Реклама:
Читать далее:
Разливка чугуна
Статьи по теме:
Плавильное отделение. Плавка чугуна на предприятии «Металит».
Плавильное отделение компании Metalyt
Компания Металит предлагает услуги по плавке чугуна. При этом используются двухтигельные индукционные печи с загрузкой 5 тонн. Плавка чугуна осуществляется в огнеупорных тигле, который нагревается посредством катушки переменного тока.
Компания имеет все необходимое оборудование для плавки чугуна, загрузка шихты осуществляется с помощью магнитной шайбы, которая перемещается с помощью крана. Такое устройство позволяет сделать загрузку материалов для плавления быстрой и простой.
Использование магнитной шайбы для загрузки позволяет существенно продлить эксплуатацию футеровки. Именно она позволяет снизить затраты на ремонт футеровки или на ее восстановление.
Особенности плавки чугуна
Плавильные печи литейного производства Металит осуществляется в тигле. Особенностью этого процесса является то, что в то время, как в одном тигле осуществляется плавка с поддержанием определенной температуры, второй имеет возможность осуществлять заливку. Такой подход позволяет существенно снизить денежные затраты на выплавку чугуна и его производство.
Компания Металит имеет современные печи для плавления чугуна, а также оборудование. Это позволяет получить такие основные преимущества:
- Быстрый нагрев металла.
- Возможность контролировать температуру плавления и поддерживать ее на необходимом уровне длительное время.
- Наличие мощных установок позволяет получить высокий уровень производительности.
- Низкое и эффективное энергопотребление – это достигается за счет использования двух тиглей, а также правильной организации всего процесса выплавки и заливки.
- Использование оборудования для плавления чугуна достаточно удобно, а ремонтные работы можно проводить в любое удобное время.
- Автоматизированный процесс плавки позволяет получить высококачественные слитки для дальнейшего использования.
Использование двухтигельных индукционных печей – это лучшее решение для выплавки чугуна, которое с успехом используется на производственной компании Металит.
Технические характеристики двухтигельных индукционных печей «OTTO JUNKER»
Эксплуатация в литейной промышленности в Украине и европейских странах двухтигельных индукционных печей «OTTOJUNKER» обусловлено значимыми преимуществами данного оборудования, такими как:
- быстрый нагрев металла;
- возможность контролировать температуру расплава и весь процесс плавки;
- высокий уровень производительности за счет мощности установки;
- низкое энергопотребление;
- легкая настройка на определенный тип и марку металла;
- удобство эксплуатации и технического обслуживания установки;
- автоматизация плавки.
Также оборудование индукционного типа «OTTOJUNKER», которое содержит плавильное отделение завода «Металит» в Украине, отвечает всем установленным положениям и требованиям по безопасности экологичности. Печи изготовлены согласно нормам по защите экологии, в них не используются опасные токсичные материалы, такие как PCB и асбест.
Двухтигельные индукционные печи «OTTOJUNKER» – универсальное металлургическое оборудование для плавки, выдержки и разливки чугуна разных марок.
Технические характеристики установки
Плавильное отделение завода «Металит» содержит оборудование с такими характеристиками:
Мощность печи | 3000 кВт |
Частота тока | 250 Гц |
Диаметр тигля | 860 мм |
Глубина тигля | 1665 мм |
Температурный диапазон плавления чугуна | 1250 – 1550 °С |
Использование индукционных плавильных печей OTTOJUNKER обеспечивает высокую производительность при минимальном потреблении электроэнергии. Таким образом, производственный процесс изготовления отливок становится эффективным и не затратным, по сравнению с традиционными методами производства чугунных заготовок.
Индукционные плавильные печи фирмы OTTO JUNKER – надежная, проверенная система плавки металлов с высокой производительностью. У нее много преимуществ и особенностей, благодаря которым наше предприятие поставляет своим клиентам отливки высокого качества.
Сотрудничество с компанией Металит
Если вам необходимы чугунные заготовки для дельнейшего использования, вы всегда можете заказать их у нас. Наша компания готова сотрудничать с сельскохозяйственными, машиностроительными, автомобильными компаниями и многими другими. Мы готовы выполнить ваши заказы в самое короткое время.
Если у вас есть нестандартный заказ, например, с использованием определенной марки чугуна, мы всегда готовы вас выслушать и предложить оптимальный вариант для сотрудничества. Наши цены вас приятно удивят и порадуют, ведь современное двухтигельное оборудование позволяет сэкономить на электроэнергии, а соответственно и устанавливать цену ниже, чем у конкурентов.
Мы готовы работать по индивидуальному заказу, обращайтесь и вы непременно будете рады взаимовыгодному сотрудничеству. Мы предоставляем полный цикл выплавки чугуна по требованиям, которые указывает заказчик.
Плавка чугуна — Энциклопедия по машиностроению XXL
Процесс модифицирования чугуна магнием сопровождается понижением температуры металла (на 80—90 °С) вследствие затраты большого количества теплоты на плавление и испарение магния, поэтому температура чугуна при выпуске из печи должна быть 1420—1450 С. Для плавки чугуна применяют водоохлаждаемые вагранки с основ- [c.161]В целях осуществления комплекса мероприятий по улучшению санитарно-гигиенических условий труда и оздоровлению окружающей среды для плавки чугуна широко внедряются современные вагранки закрытого типа, в которых отходящие газы полностью отбираются, подвергаются эффективной очистке, дожигаются, а теплота утилизируется. Эффективно работают установки для очистки дымовых газов от хлоридов, внедряются новые нетоксичные связующие материалы и технологические процессы изготовления стержней, более широкое применение получает литье в металлические формы,
[c. 173]
Однако плавка чугуна в вагранках имеет свои преимущества [c.239]
Плавка чугуна в вагранке. В процессе плавки происходят следующие физико-металлургические процессы плавление металлической шихты и флюса науглероживание расплава образование шлака изменение состава и температуры чугуна. [c.257]
Расчет шлакообразующих. Расчет шихты при плавке сплавов в металлургических агрегатах, как правило, производят на 1000 кг сплава. При плавке чугуна в вагранках расчетным путем определяют количество вводимого известняка. При этом [c.259]
Плавка чугуна. Основным металлургическим процессом при индукционной плавке является процесс науглероживания чугуна. Процесс науглероживания стального расплава с углеродом протекает при сильном индукционном перемешивании, т.е. при более благоприятных условиях. [c.265]
В конце плавки чугуна необходимо температуру довести до 1550°С для более интенсивного распределения графита и увеличения количества связанного углерода. Чем выше содержание углерода в чугуне, тем до более высоких температур допустим перегрев его без образования междендритного графита. Перегрев до определенных пределов является одним из эффективных методов повышения прочности чугуна.
[c.266]
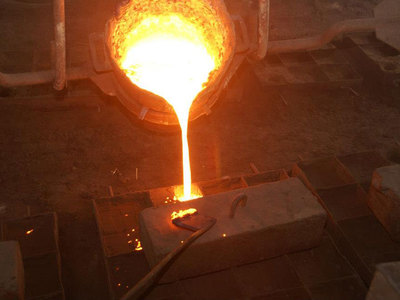
Печи для плавки чугуна. Канальные печи используются при плавке чугуна в качестве миксеров в дуплекс-процессе с вагранками, дуговыми и индукционными тигельными печами, позволяя повысить температуру, осуществить легирование и обеспечить однородность чугуна перед разливкой. Емкость канальных миксеров лежит в пределах от 0,5 до 250 т. Коэффициент мощности печей для плавки чугуна составляет 0,6—0,8 срок службы футеровки ванны достигает года, а подового камня 4—6 мес допустимая удельная мощность в каналах из условия перегрева металла (40 — 50). 10 Вт/м [c.278]
В промышленности строительных материалов ВЭР образуются при обжиге цементного клинкера, варке стекла, обжиге керамических изделий, выплавке термоизоляционных материалов, при плавке чугуна в вагранках и в других термохимических процессах. [c.70]
В Советском Союзе разработаны различные методы применения природного газа для плавки чугуна в литейных цехах. В связи с тем, что в некоторых зарубежных странах в последние годы обнаружены большие запасы природного газа (в частности, в Голландии и Англии), эти страны глубоко изучают достижения СССР с целью перенесения его опыта.
[c.105]
Прогрессивные процессы в литейном производстве осуществляются в результате модернизации существующих вагранок и установки электропечей во вновь строящихся цехах. При этом технология плавки в вагранках совершенствуется путем автоматизации операций набора, взвешивания и загрузки шихты, контроля и регулирования процесса плавки, подогрева дутья, применения природного газа и новых материалов для футеровки (угольные блоки) водоохлаждаемых вагранок. При плавке чугуна в электропечах обеспечивается высокое качество металла путем снижения в нем содержания серы и фосфора и идеального перемешивания, что делает его однородным по химическому составу и температуре. Это позволяет получать отливки хорошего качества любой конфигурации, снижать брак и угар металла до 1,5% вместо в вагранке).
[c.189]
Разрабатываются предложения по внедрению индукционной плавки чугуна и дуплекс-процесса, электрошлакового литья, смесей холодного твердения на основе синтетических смол для изготовления форм и стержней, базовых отливок станкостроения в облицованных кокилях. Усовершенствуется процесс непрерывного литья фасонных профилей, разрабатываются составы чугунов для станкостроения и режимов их обработки, исключающих или сокращающих цикл старения отливок. Исследуются возможности и проводятся экспериментальные работы по переводу единичных отливок станкостроения с литого на сварное исполнение, по повышению размерной точности отливок. [c.288]
Реализуются мероприятия по усовершенствованию плавки чугуна в вагранках с использованием низкосортной шихты и защиты окружающей среды. [c.288]
Плавка чугуна (дуплекс-процесс) 1 т жидкого чугуна 95—100 [c.243]
Плавка чугуна (твердая завалка) 1 т жидкого чугуна 640—660
[c. 243]
Дуплекс-процесс плавки чугуна 6—182 Дуралюмин 4—178 [c.74]
Струбцины 3—137 5 — 250, 268 Струбцины-домкраты 5 — 459 Струги экскаваторные 9—1156 Стружка брикетная — Содержание в шихте при плавке стали 14—ГЗ — Содержание в шихте при плавке чугуна [c.290]
Содержание в шихте при плавке чугун 4— 13 [c.319]
Плавка — см. Плавка чугуна [c.341]
И —ЧИСЛО молей металла, вступающих в реакцию с 1 молем Од. Следовательно, уменьшение концентрации металла в растворе ведёт к увеличению упругости диссоциации его окисла. При плавке чугуна и стали концентрация железа в ванне Ср обычно мало [c.168]
ПЛАВКА ЧУГУНА Отливки из чугуна первичной плавки [c.174]
Применение шамотовых тиглей для плавки чугуна нерационально вследствие их малой прочности. [c.175]
Плавка чугуна в пламенных печах требует непрерывного контроля за его составом и температурой средствами экспресс-анализа и отбором специальных проб. Как только металл достиг заданного химического состава и температуры, его следует немедленно выпустить из печи, так как иначе состав металла будет изменяться вследствие окисления.
[c.176]
Дуплекс-процесс при плавке чугунов [c.182]
М а р и е н б а X Л. М., Применение местных топлив и заменителей кокса при плавке чугуна в вагранке, Машгиз, 19 3. [c.198]
Технологические пробы обеих групп дают возможность объективного, но относительного суждения о составе металла. Поэтому необходимо в каждом конкретном случае устанавливать связь между составом чугуна и показателями технологической пробы. Технологические пробы для оценки состава металла особенно важны при процессах непрерывной выплавки (плавка чугуна в вагранке), не позволяющих ожидать ответа из экспресс-лаборатории. [c.245]
Продукты доменной плавки. Чугун — основной продукт доменной плавки. В доменных печах получают чугуи различного химического состава в зависимости от его назначения.
[c.27]
Футероака индукционных печей. Футеровка индукционной печи может быть выполнена из кислых, ооюаных и нейтральных огнеупорных материалов (см. табл. 57). Кислая футеровка хорошо освоена, ее выполняют из кварцита, содержащего не менее 95% S1O2 и борной кислоты в качестве связующего. Гранулометрический состав кварцита 35% фракции от 1,5 до 3,5 мм и 65% — от О до 1,5 мм. К смеси добавляют 1,5% технической борной кислоты и ее применяют при плавке чугунов и стали. Стойкость кислой футеровки на печи емкостью 1,4 т составляет 150 плавок, а при основной футеровке — колеблется в пределах только 10 — 100 плавок. Недостатком является что при кислой футеровке невозможно получить вязкость горячих и подвижных шлаков, равную 0,1 -0,3 Па С, т.е. бороться с вредными примесями — серой и фосфором. В процессе плавки образуются длинные шлаки вязкостью 0,8 - [c.251]
В металлургии магний используется в качестве раскнслителя при плавке чугуна, для раскисления и десульфуризации медных и никелевых сплавов, а также в качестве восстановителя при получении некоторых металлов — ванадия, хрома, бериллия, титана, циркония и др. трудновосстанавливаемых металлов.
[c.123]
Статистическая обработка полученных результатов и анализ кривых распределения твердости большой партии серийных отливок показали, что среднестатистическое значение твердости отливок из чугуна ИЧХ28Н2, дополнительно легированного ванадием из мазутного шлака, повышается по сравнению с твердостью отливок, изготавливаемых по заводской технологии, с 46,ЗЯ J до 49,5Я/гс- Содержание ванадия в выплавляемом чугуне составляло 0,25—0,50%. В металлическом шлаке, образующемся при плавке чугуна, среднее содержание ванадия составляло 0,3%. В промышленных плавках средняя величина усвоения ванадия составляет 70—75%. [c.242]
В начале 1896 г. М. А. Павлов получает письмо от владельца Сул инского завода Пастухова. Ему предлагается занять место управляющего доменным производством завода. Им был нужен опытный и знающий доменный инженер для того, чтобы поставить но-современному плавку чугуна на антраците , писал Пастухов. Сулинский завод находился невдалеке от Ростова-на-Дону, возле антрацитовых месторождений. Этим объяснялось стремление его хозяина вести плавку не на каксе, а на антраците. Однако особенно стей такой плавки никто в Европе не знал. Она применялась только на заводах Восточной Пенсильвании. Павлов согласился заведовать доменным цехом завода лишь афи условии предшарительной командировки в США для ознакомления с новым процессом.
[c.191]
Расчеты показывают, что на 1 т прироста выпуска стальных отливок требуется на 35% больше капитальных вложений, чем на 1 т прироста выпуска чугунных отливок, поэтому предпочтение в машиностроении отдается применению высококачественных чу-гунов взамен литой и кованой стали. Уменьшает эффективность плавка чугуна в маломощных вагранках, имеющих относительно низкий технический уровень и не обеспечивающих возможностей выплавлять высококачественные литейные сплавы. Совершенствование литейного производства осуществляется путем улучшения ваграночных процессов и применения электроплавки (последнее позволяет получать высококачественный синтетический чугун), внедрения мероприятий по утонению стенок отливок путем замены углеродистой стали легированной (в результате удельный расход металла уменьшается примерно в 2 раза, а надежность и долговечность машин увеличивается в 1,5—2 раза).
[c.181]
Шихтовка производится полукозловыми кранами 14, снабженными магнитными шайбами, подъемная сила которых регулируется крановщиками из кабины. Набранная калоша поступает в бадьи скипового подъемника и выгружается в вагранки. Плавка чугуна происходит в двух парах коксогазовых вагранок, работа которых полностью автоматизирована. Расплавленный чугун поступает в поворотные копильники 15 и выливается в ковши монорельсовой тележки 16, доставляющей его к заливочным устройствам 17 литейных конвейеров 18, 19 и 20. Заливка форм производится с заливочных площадок 21, движущихся синхронно с литейными конвейерами. [c.400]
Для поршневых колец, работающих при повышенных температурах (примерно до 250°), в условиях полусухого трения, наиболее пригодной является перлитная или сорбитная (после термообработки) структура с минимальным количеством феррита. Эта структура сообщает кольцу необходимую прочность, вязкость и хорошие антифрикционные свойства. Составы колец зависят от способа изготовления, определяющего скорость остывания отливок. При отливке индивидуальных колец в сырые формы обычный перлитный состав (№ 31) имеет повышенное содержание и до 3,0% 51 (для колец толщиной в 3—4 мм). Это обеспечивает перлитную структуру в тонких отливках и отсутствие как местных отбе-лов, так и феррито-графитной псевдоэвтектики, снижающих упругие и антифрикционные свойства. Повышенное количество фосфора, помимо необходимой жидкотекучести, способствует распределению фосфидов в виде разорванной сетки. Сера назначается до 0,07% для обеспечения хорошей заполняемости формы, хотя содержание до 0,1% 5 не оказывает вредного влияния на работу колец. Плавка чугуна для колец обычно производится дуплекс-процессом (вагранкагэлектропечь), что обеспечивает однородность состава и высокий перегрев. Оптимальная твёрдость колец, обладающих нормальной упругостью и прочностью, лежит в пределах 97 — 103.
[c.50]
Плавка чугуна нирезист производится в пламенных печах или в вагранках. По коррозио-стойкости и механическим свойствам (см. табл. 64 — 66) отливки близки к латуням и бронзам и превышают последние по износостойкости. Благодаря аустенито-графитной структуре в сплаве удачно сочетаются коррозиостойкость с жароупорностью и сохраняются прочность и плотность при длительных нагревах до высоких температур (при температуре 450° С предел прочности при растяжении падает всего на 3 кг мм , при 700° С — примерно на 50%).
[c.56]
Плавиковый шпат (ручного обогащения по ОСТ НКТП 7633-655). Плавиковый шпат, или флюорит, представляет собой минерал кристаллического строения, содержащий в основной своей массе СаРз. Удельный вес в твёрдом состоянии — 3,18, температура плавления 1378° С. Применяется в качестве флюса а) 2-й и 3-й сорта — при плавке чугуна и стали б) 1-й сорт—при илавке магниевых и алюминиевых сплавов, а также бронз. При плавке магниевых и алюминиевых сплавов может быть использован только в сухом состоянии, получаемом путём сушки и прокаливания. По содержанию составных частей плавиковый шиат ручного обогащения должен отвечать требованиям, приведённым в табл. 26.
[c.7]
Для плавки чугуна, стали и медных сплавов применяются графитовые (фиг. 278) и шамотные тигли для плавки алюминиевых и цинковых сплавов — металлические. Сверху тигель закрывается крышкой (фиг. 279), защищающей металл от окислительного действия атмосферы печи. Размеры тиглей — по ОСТ 2J154-39 и 2015.5-3 -). [c.146]
Вся печь заключена в железный кожух. Камера сгорания может быть снята для ремонта. Загрузка производится через рабочее окно, выпуск металла — через лётку. Емкость печей— 160, 320 и 800 кг. Удельный расход мазута — 12 — 15% к весу металла на первую плавку и 7 — IQO/o—на последующие. Продолжительность плавки—1 — и/г часа. При плавке чугуна расход топлива повышается до 25—,300/о, а время плавки — до U/a — 21/г час. Угар металла (меди и чугуна) составляет в среднем 7%. [c.150]
Большое распространение на советских заводах получил модифицированный чугун Большевик» (Киевского завода Большевик»), сущность производства которого заключается а) в повышении устойчивости цементита путём выбора соответствующего химического состава (сумма С + Si определяется по формуле С + Si = 5,4— Ig s, где s — толщина отливки) и б) в последующем увеличении скорости распада цементита за счёт раскисления чугуна. Содержание кремния должно быть ниже критического», т. е. ниже концентрации, вызывающей энергичное графитообразование, и графит при плавке чугуна должен полностью раствориться в жидком металле. Количество вводимого модификатора зависит от качества последнего, толщины стенок отливки и химического состава чугуна. В табл. 188 приведены нормы расхода модификаторов.
[c.206]
Индукционные печи для плавки чугуна
Индукционные печи для плавки чугунаТакое оборудование промышленные предприятия используют для плавки чёрных металлов. На серийных и массовых производствах наиболее эффективен индукционный метод нагрева, который предполагает выделение теплоты изнутри самого металла. Процесс протекает следующим образом: на небольшой объём металла подаётся значительная концентрация электрической энергии, благодаря чему с большой скоростью начинает выделяться тепло.
Печи для выплавки чугуна ИТПЭ от компании «Термолит» также могут быть использованы для изготовления высококачественных стальных отливок.
По вопросам приобретения оборудования и обращайтесь в отдел маркетинга ООО «Термолит»
Тел./Ф.: (0619) 42-40-12; 42-02-19; 42-03-14
Моб.: (095)040-75-17; (098)63-502-63;
E-mail: [email protected];
Устройство оборудования для литья чугунаОсновной состав печи для выплавки чугуна представлен:
- плавильным агрегатом;
- тиристорным преобразователем частоты;
- конденсаторной батареей.
Первый перечисленный компонент состоит из каркаса и двух стоек с плунжерами.[
Плавильное пространство индукционной печи для плавки чугуна представлено диэлектрической футеровкой(кварцевая, магнезитовая) расположенной внутри индуктора. Шихта (смесь материалов для создания сплава) загружается в тигель сверху. В основу тигля входят футеровочные массы.
Опорами для индукционной печи для плавки чугуна являются две стойки — сварные конструкции. Стойки крепятся на фундаменте анкерными болтами. Верхняя часть каждой стойки располагает шарнирными креплениями каркаса электропечи. Каркас может быть прямоугольным или цилиндрическим. Элемент представлен сварной конструкцией из углеродистой или нержавеющей стали.
Электромагнитное поле создаёт такой компонент оборудования для литья чугуна, как индуктор. С помощью него шихта нагревается и расплавляется. Индуктор в электропечах от «Термолита» — это однофазный, однослойный элемент из медной трубки. Благодаря тому, что индуктор является водоохлаждаемым, значительно снижаются тепловые электрические потери.
Электропечь наклоняется для слива металла благодаря нагнетанию масла через гидрораспределитель в нижние полости двух плунжеров. Возвращается в исходное состояние печи для выплавки чугуна с помощью собственного веса.
Система водоохлаждения снижает температуру таких компонентов, как преобразователь частоты конденсаторы, трубошины, элементы индуктора и кабели питания, идущие к нему.
Управление рабочим процессом осуществляется посредством комплекта электрооборудования, состоящего из пульта управления, тиристорного преобразователя частоты.
Питает печь тиристорный преобразователь частоты.
Индукционные плавильные печи в работе
Индукционная плавильная печь ООО Термолит, в работе/ Induction melting furnace in operation
Испытания Индукционной печи ИТПЭ-0.03/0.03 ТрМ1 Система охлаждения с теплообменником вода-воздух.
Плавильная печь ИТПЭ-0. 25/0.25 в работе
Плавка бронзы на печи ИТПЭ-0.06 / Bronze melting at furnace ICMEF-0.06
Плавка латуни на печи ИТПЭ-0.06 / Brass smelting on a furnace ICMEF-0.06
Плавка стали на печи ИТПЭ-0.65 / Steel melting at furnace ICMEF-0,65
Преимущества оборудования для литья чугуна от «Термолита»
При изготовлении техники наша компания использует самые эффективные методы и качественное оборудование. Мы с ответственностью относимся к своей работе. Нам удаётся изготавливать надёжные и производительныеиндукционные печи для плавки чугуна.
Среди основных преимуществ нашего оборудования для литья чугунастоит выделить:
- Высокое качество исполнения и экологичность. Мы не применяем асбест при изготовлении оборудования.
- Использование надёжных комплектующих. Помимо всего прочего в наших электропечах применяются среднечастотные конденсаторы чешского и немецкого производства.
- Применение надёжных тиристорных преобразователей частоты нового поколения с автоподстройкой частоты во время процесса плавки.
- Повышенная мощность плавки.
- Рассчитанная и оптимально подобранная ёмкость конденсаторных батарей, индуктивность индукторов и соединительных линий. Благодаря этим моментам наша техника отличается высокой производительностью, большей эффективностью в расходе электроэнергии, большим коэффициентом полезного действия.
- Использование современных передовых технологий.
- Эффективная защита штоков гидроцилиндров от брызг металла.
- Существенно повышенная надёжность и безотказность работы.
- Повышенная безопасность при эксплуатации.
Структура условного обозначения ИТПЭ — ХХ/ХХХ ТГ Пример- ИТПЭ-0,4/0,35 ТГ1
И — метод нагрева- индукционный | 0,4 — номинальная емкость тигля, т |
T — конструктивный признак- тигельная | 0,35 — мощность преобразователя, МВт |
П — плавильная | Т — тиристорный преобразователь частоты |
Э -электропечь | Г — гидравлический наклон |
1 — один плавильный агрегат |
Структура условного обозначения ИТПЭ — ХХ/ХХХ ТрМ Пример- ИТПЭ-0,03/0,05 ТрМ1
И — метод нагрева- индукционный | 0,03 — номинальная емкость тигля, т |
T — конструктивный признак- тигельная | 0,05 — мощность генератора, МВт |
П — плавильная | Тр — транзисторный генератор |
Э -электропечь | М — механический наклон |
1 — один плавильный агрегат |
№ | Наименование | С одним тиглем | С двумя тиглями |
1 | Плавильный агрегат ИТПЭ* | 1 | 2 |
2 | Тиристорный преобразователь частоты ТПЧ | 1 | 1 |
3 | Батарея конденсаторная ИТПЭ | 1 | 1 |
4 | Кабель водоохлаждаемый ИТПЭ | 2 | 4 |
5 | Пульт управления и сигнализации ШУС с гидростанцией | 1 | 1 |
6 | Шкаф теплообменный ИМ | 1 | 1 |
7 | Комплект трубошин ИТПЭ | 1 | 2 |
8 | ЗиП к ТПЧ | 1 | 1 |
9 | Комплект монтажных принадлежностей | 1 | 1 |
10 | Комплект эксплуатационной документации | 1 | 1 |
* возможна комплектация двумя и тремя плавильными агрегатами
В комплект поставки ИТПЭ — ХХ/ХХ ТрМ* входит:№ | Наименование | С одним тиглем | С двумя тиглями |
1 | Плавильный агрегат ИТПЭ* | 1 | 2 |
2 | Транзисторный генератор ВТГ | 1 | 1 |
3 | Кабель водоохлаждаемый ИТПЭ | 2 | 4 |
4 | Комплект монтажных принадлежностей | 1 | 1 |
5 | Комплект эксплуатационной документации | 1 | 1 |
Технические характеристики
№ | Тип печи | Емкость в тоннах | Мощность питающего преобразователя, кВт | Скорость расплавления и перегрева металла, т/ч | Напряжение питающей сети, В | Расход воды на охлаждение (общий), куб.![]() | Удельный расход эл. энергии, квт.ч/т | Тип источника питания |
1 | ИТПЭ-0,005/0,01 ТрМ* | 0,005 | 10 | 0,01 | 380 | 1,3 | 540 | ВТГ-5-22 |
2 | ИТПЭ-0,01/0,02 ТрМ* | 0,01 | 20 | 0,02 | 380 | 1,5 | 540 | ВТГ-20-22 |
3 | ИТПЭ-0,03/0,05 ТрМ* | 0,03 | 50 | 0,04 | 380 | 3,5 | 540 | ВТГ-50-2,4/8,0/10,0 |
4 | ИТПЭ-0,03/0,1 ТрМ* | 0,03 | 100 | 0,06 | 380 | 3,8 | 540 | ВТГ-100-2,4/4,0 |
5 | ИТПЭ-0,06/0,05 ТрМ* | 0,06 | 50 | 0,07 | 380 | 3,3 | 550 | ВТГ-50-6,0 |
6 | ИТПЭ-0,06/0,1 ТрМ* | 0,06 | 100 | 0,11 | 380 | 4,5 | 530 | ВТГ-100-2,4 |
7 | ИТПЭ-0,1/0,1 ТрМ* | 0,10 | 100 | 0,16 | 380 | 5,0 | 540 | ВТГ-100-8,0 |
8 | ИТПЭ-0,1/0,1 ТГ* | 0,10 | 100 | 0,16 | 380 | 6,0 | 540 | ТПЧ-100-2,4 |
9 | ИТПЭ-0,16/0,16 ТГ* | 0,16 | 160 | 0,23 | 380 | 8,5 | 550 | ТПЧ-160-2,4 |
10 | ИТПЭ-0,16/0,25 ТГ* | 0,16 | 160 | 0,36 | 380 | 8,7 | 530 | ТПЧ-250-2,4 |
11 | ИТПЭ-0,25/0,25 ТГ* | 0,25 | 250 | 0,38 | 380 | 8,9 | 550 | ТПЧ-250-1,0 |
12 | ИТПЭ-0,25/0,35 ТГ* | 0,25 | 350 | 0,4 | 380 | 9,0 | 530 | ТПЧ-350-1,0 |
13 | ИТПЭ-0,4/0,35 ТГ* | 0,40 | 350 | 0,58 | 380 | 9,8 | 540 | ТПЧ-350-1,0 |
14 | ИТПЭ-0,4/0,4 ТГ* | 0,40 | 400 | 0,61 | 380 | 9,8 | 530 | ТПЧ-400-1,0 |
15 | ИТПЭ-0,4/0,5 ТГ* | 0,40 | 500 | 0,76 | 380 | 10,0 | 520 | ТПЧ-500-1,0 |
16 | ИТПЭ-0,5/0,4 ТГ* | 0,50 | 400 | 0,58 | 380 | 10,3 | 550 | ТПЧ-400-1,0 |
17 | ИТПЭ-0,5/0,5 ТГ* | 0,50 | 500 | 0,60 | 380 | 10,5 | 530 | ТПЧ-500-1,0 |
18 | ИТПЭ-0,65/0,5 ТГ* | 0,65 | 500 | 0,65 | 380 | 11,5 | 550 | ТПЧ-500-1,0 |
19 | ИТПЭ-0,8/0,65 ТГ* | 0,8 | 650 | 1,0 | 380 | 18,0 | 560 | ТПЧ-650-1,0 |
20 | ИТПЭ-1,0/0,8 ТГ* | 1,00 | 800 | 1,3 | 6000/10000 | 21,2 | 570 | ТПЧ-800-1,0 |
21 | ИТПЭ-1,5/1,2 ТГ* | 1,50 | 1200 | 1,3 | 6000/10000 | 24,0 | 570 | ТПЧ-1200-1,0 |
22 | ИТПЭ-2,5/1,6 ТГ* | 2,5 | 1600 | 2,3 | 6000/10000 | 27,2 | 570 | ТПЧ-1600-0,5 |
23 | ИТПЭ-3,0/1,6 ТГ* | 3,0 | 1600 | 2,8 | 6000/10000 | 32,0 | 590 | ТПЧ-1600-0,5 |
24 | ИТПЭ-5,0/3,2 ТГ* | 5,0 | 3200 | 5,2 | 6000/10000 | 41,0 | 590 | ТПЧ-3200-0,25 |
Заказать печь для выплавки чугуна
Компания «Термолит» уже оснастила большое количество предприятий оборудованием для литья чугуна. Также мы осуществляем обслуживание поставляемого нами оборудования. Мы поставляем технику в страны СНГ, а также в страны ближнего зарубежья вроде Польши, Финляндии, Израиля, Германии, Италии. Если Вы закажите печь для выплавки чугуна в «Термолите», то, несомненно, останетесь довольны приобретением.
13Декабрь
Плавка металла дуплекс-процессом на индукционной печи ИТПЭ-1,0/0,8-0,4 ТГ2
В 2017 г. ООО «Термолит» была произведена индукционная печь ИТПЭ-1,0/0,8-0,4 ТГ2 с двумя плавильными агрегатами и запущена на предприятие ООО…
Узнать больше11Ноябрь
Отгрузка плавильной печи ИТПЭ-2,0/1,6 ТГ2 в Грузию
В конце прошлой недели ООО «Термолит» осуществило отгрузку индукционной плавильной печи ИТПЭ-2,0/1,6 ТГ2 для предприятия в Грузии. Ранее Заказчики приезжали…
Узнать больше
Плавка чугуна в электрических печах
Плавка чугуна в электрических печах. В связи с расширением производства отливок из высокопрочных, модифицированных и других чугунов высокого качества все более широкое применение для плавки получают электрические индукционные и дуговые печи.
Плавка чугуна в электрических печах — индукционных и дуговых — приобретает все большее значение в связи с развитием производства модифицированных, высокопрочных и других качественных чугунов. [c.444]
ПЛАВКА ЧУГУНА В ЭЛЕКТРИЧЕСКИХ ПЕЧАХ [c.326]
Плавка в электрических печах может производиться как на твердой, так и на жидкой завалке. Второй способ является более экономичным и применяется чаще (предварительно чугун [c.44]
Плавка баббита. Стальные или чугунные тигли, предварительно подогретые, загружают кусками баббита весом 1—2 кГ и нагревают в электрической печи до температуры 400—500° (в зависимости от марки баббита).
[c.210]
Плавка чугуна в индукционных электрических печах [c.390]
В литейных цехах для плавки стали применяют электрические дуговые печи, небольшие конверторы с боковым дутьем и мартеновские печи для плавки чугуна — вагранки, электрические индукционные печи промышленной частоты для плавки цветных сплавов — различные электрические и пламенные печи. [c.209]
Индукционные печи имеют ряд преимуществ перед другими плавильными агрегатами. В них люжно нагревать металл до очень высоких температур без местного перегрева (что наблюдается иногда в электрических дуговых печах), регулировать состав газовой атмосферы или создавать вакуум. Емкость индукционных печей изменяется от нескольких килограммов (лабораторные печи) до 6—10 т. В современной практике находят широкое применение индукционные печи промышленной частоты, их используют для плавки обычного и синтетического чугуна. В таких печах можно успешно вести плавку стружки и высечки без их брикетирования. Одновременно такой процесс очень мобилен (плавка длится не более 40 мин), резко улучшаются условия труда, не нужно расходовать дефицитный литейный чугун. Применение этих печей позволяет с минимальными затратами получать металл высокого качества.
[c.213]
Плавка чугуна. В литейном производстве более 90% чугуна выплавляют в вагранках. Они имеют простую конструкцию, высокую производительность экономически выгодны. В связи с появлением новых марок модифицированных, высокопрочных, легированных чугунов начинают применять электрические индукционные и дуговые печи. [c.320]
Получение синтетического чугуна имеет еще меньшее применение и заключается в плавке в электрических печах стального лома с углеродсодержащими материалами. [c.13]
Плавку металла для ферритного чугуна ведут дуплекс-процес-сом, расплавление — в вагранке, а перегрев и доводку — в электрической печи. При малом масштабе плавку ведут в пламенной печи.

Плавка чугуна. В литейном производстве более 90% чугуна выплавляют в вагранках. За последние годы очень быстрое развитие получила плавка в электрических печах (индукционных и дуговых), обеспечивающая получение чугунов высокого качества. Быстро развивается также дуплекс-процесс, в особенности вариант вагранка — индукционная печь. [c.442]
Выбор способа плавки определяется масштабом производства и требованиями к деталям. Ваграночный чугун применяется для производства отливок групп Б, Г и Д (см. табл. 9, 10 и 13), отливки остальных групп, согласно указанным таблицам производятся из чугуна, получаемого в электрических печах или дуплекс-процессом. [c.317]
ПЛАВКА ЧУГУНА В ПЛАМЕННЫХ И ЭЛЕКТРИЧЕСКИХ ПЕЧАХ [c.278]
Плавку чугуна чаще всего Производят в вагранках и реже в электрических печах главным образом в индукционных тигельных промьшшенной частоты типа ИЧТ-6 и ИЧТ-10 и др. В современных литейных цехах вместо старых вагранок применяют ваграночные комплексы моделей 95111—95115 с часовой производительностью расплава соответственно от 4—6 до 25—50 т. В состав таких комплексов входит коксогазовая вагранка закрытого типа, которая снабжена системой подогрева дутья до 673-873 К за счет рекуперации отходящих газов, а также системой очистки отходящих ваграночных газов. Однако использование электроагрегатов более предпочтительно, так как они позволяют получать расплав точного химического состава с минимальным содержанием серы (вредной примеси). Для плавки в электроагрегатах можно использовать дешевую металлическую стружку и другие легковесные металлоотходы, а также металлизованные окатыши, не содержащие вредных примесей (серу и фосфор).
[c.21]
Печи промышленной частоты не требуют преобразователей и просты по устройству. Электрический коэффициент полезного действия их при плавке чугуна может достигать 75%. Эти печи впервые были применены в 1943—1944 гг. для плавки магния. В 1950 г. сконструированы печи для плавки алюминия. Высокое качество металла и экономичность плавки способствовали внедрению печей промышленной частоты в литейных цехах для выплавки чугуна и стали. Капитальные затраты при уста-
[c.8]
Плавка чугуна для фасонного литья может производиться в печах различной конструкции. Могут быть использованы печи тигельные, отражательные, мартеновские, электрические (дуговые, печи сопротивления, индукционные), вагранки различной конструкции, вагранка в сочетании с пламенной печью или электропечью (двойные процессы). [c.387]
Обычно для плавки стали в дуговых электрических печах применяют шихтовые материалы в твердом состоянии. Шихта состоит из стального лома, чугуна, железной руды, флюсов, ферросплавов. В качестве флюсов применяют в основных печах — известь, в кислых — кварцевый песок. Плавка шихты происходит за счет тепла трех электрических дуг, образующихся между электродами и металлом. Температура дуги более 3000° С. Тепло передается металлической ванне излучением.
[c.33]
Оборудование для разливки стали. Готовая сталь после окончания процесса плавки выпускается в разливочный ковш и разливается при помощи крана. Из конвертора сталь выпускается в ковш путем наклона, а из мартеновских и электрических печей — по выпускному желобу. Из ковша сталь разливают в чугунные изложницы (для получения слитков) и в земляные или металлические формы (для получения фасонных отливок). [c.89]
Шихтовые материалы для чугунного литья и шихтовка. Материалы, загружаемые в плавильные печи, называются шихтовыми материалами. При плавке в электрических и пламенных печах загружаемую шихту составляют из металла и флюсов, а при плавке в вагранке к ним добавляют еще топливо. [c.216]
Плавку чугуна можно производить в пламенных и электрических печах. [c.276]
Нелегированная (углеродистая) сталь отличается от чугуна меньшим содержанием углерода, кремния, марганца, серы и фосфора, что достигается окислением этих элементов ю время плавки в различных металлургических агрегатах. В настоящее время сталь производят в трех типах плавильных агрегатов — конверторах, мартеновских и электрических печах.
[c.25]
Электрические печи, так же как и пламенные, применяются в тех случаях, когда требуется получить высокую температуру жидкого чугуна и особо ответственное литье из серого чугуна (например, поршневые кольца, цилиндры и др.). Преимущества этих печей особенно значительны при плавке легированного чу- [c.102]
Электрические печи. В литейных цехах электрические печи применяются для плавки углеродистых и легированных сталей, сплавов цветных металлов, ковкого чугуна и специальных марок серого чугуна. Их преимущества перед другими печами возможность получения высококачественного металла достижение максимальной температуры и легкость ее регулирования возможность очистки металла от вредных примесей минималь-ньш угар металла незначительность изменений химического состава металла и удобство обслуживания. [c.231]
Разработка конструктивно-технологических вариантов применения природного газа для плавки чугуна в вагранках, основанная на изучении многочисленных попыток решения этого вопроса, продолжается до настоящего времени. На ряде предприятий Харькова, Ростова и других городов в вагранках производительностью от 1,5 до 7 т/ч успешно осуществлена частичная замена кокса природным газом. Туннели газовых горелок рекомендуется размещать в этом случае над фурменным поясом, но ниже уровня коксовой колоши [Л. 143]. Применение коксогазовых вагранок позволяет удешевить плавильный процесс при очень небольших ка1Питаловло-жениях, но не решает вопроса повышения температуры выплавляемого чугуна. Чисто газовые вагранки производительностью до 10 г/ч успешно эксплуатируются на ряде бакинских заводов. Однако широкое распространение чисто газовых вагранок (особенно высокотемпературных) сдерживается жесткостью требований, предъявляемых к огне-и шлакоупорности футеровки и силикатной колоши, а также трудностями перегрева расплавленного металла, поверхность которого покрыта малотеплопроводным жидким шлаком. В связи с этим газовую плавку некоторых сортов чугуна (например, используемых лля тонкостенного и качественного литья) приходится комбинировать с электрическим перегревом.
Применительно к этим случаям возникают предложения об осуществлении плавки металла в сравнительно простой печи на дешевом топливе
[c.171]
Особенности производства титана обусловлены его высокой химической активностью и большим сродством к кислороду, азоту, водороду и другим элементам. Титановые руды подвергаются электромагнитному, электростатическому, флотационному, гравитационному и другим видам обогащения, в результате которых получаются концентраты, содержащие до 60% TiOj. Рациональным способом переработки железотитановых концентратов является плавка в электрических печах. Восстановительной плавкой получают чугун, легированный титаном (0,6—2,0% Ti), и шлаки, содержащие около 80% TiOg и 1,5—3,0% FeO, используемые в качестве сырья для получения титана. [c.51]
Исходными материалами для плавки в электрических печах являются стальной лом, отходы и специальные заготовки с повышенными требованиями к вредным примесям, сортировке, загрязненности, габаритности и пр. Передельный чугун изредка применяется для высокоуглеродистых сталей, но чаще заменяется электродным боем или малосернистым коксом.
[c.40]
Обычно ильменитовый концентрат в виде ильменитоугольных брикетов плавят в электрических печах с закрытым колошником. В результате восстановительной плавки получают малоуглеродистый легированный чугун и высокотитанистый шлак с содержанием 80% и более двуокиси титана Т10г. Этот шлак служит сырьем для получения четыреххлористого титана. Измельченный шлак смешивают с углем и каменноугольным пеком, а затем брикетируют. Брикеты нагревают без доступа воз- [c.118]
Этому способствует наличие в чугуне кремния. Поэтому шихтовка всегда производится в первую очередь на кремний. Штыковой чугун, лом и скрап. д. б. перед плавкой предварительно подготовлены, разбиты до определенного размера кусков, а брак отливок и литники очищены от пригоревшей формовочной земли. В качестве топлива для наибо,11ее распространенных плавильных приборов — вагра-пок (см. ) употребляется кокс или антрацит. В процессе плавки в вагранке от загрязнений в шихте, оплавления футеровки, золы топлива и окисления примесей образуется шлак. Чтобы сделать шлак легкоплавким, в вагранку добавляют флюсы. Наиболее распространенным флюсом является известняк (СаСОз) и плавиковый шпат (СаК ). Кроме вагралок для плавки чугуна примеряются электрические и пламенные печи. Сырыми материалами для изготовления форм и стержней являются кварцевые пески, глины, естественные глинистые пески, различные связующие вещества и припылы. Из этих материалов приготовляются формовочные и стержневые смеси определенного состава и свойства в зависимости от сплава и характера отливок (см. Формовочные материалы). Модели и ящики при индивидуальном производстве делаются обычно из дерева. При серийном и массовом производстве модели отливаются из металла, т. к. деревянная модель очень недолговечна (см. Модельное дело). При формовке на формовочных машинах (см. Формовочные и стержневые машины) употребляются почти исключительно металлич.
модели. Готовые формы и стержни непосредственно собираются под заливку или предварительно высушиваются в специальных сушилах.
[c.84]
Также весьма редко применяются электрические дуговые однофазные печи типа ДМК (фиг. 142, б). Возможна также плавка чугуна в индукционных бессердечниковых печах повышенной частоты (фиг. 142, е) однако широкого промышленного применения индукционные печи для плавки чугуна пока не получили. [c.272]
При заливке вкладышей производят подгоговку вкладыша к лужению, его лужение, плавку баббита и заливку вк/ адыша. Баббит плавят в электрических печах, в стальном или чугунном тигле, который предварительно нагревают и загружают кусками баббита массой 1—2 кг, затем нагревают в печи до 400—500° С в зависимости от марки баббита. [c.244]
Учение о теплообмене очень быстро развивалось в течение последних 30 лет. В эту науку наряду с зарубежными исследованиями большой вклад внесли и отечественные ученые. Особенно следует отметить работы акад. М. В. Кирпичева и его школы в области теории подобия теплофизических процессов и конвективного теплообмена, работы М. А. Михеева, Г. М. Кондратьева, А. В. Лыкова и многих других. Тепловые процессы лежат в основе многих важнейших производств металла, машин, строительных материалов, химических и пищевых продуктов и др. Достаточно вспомнить, что на выплавку в доменной печи 1 т чугуна из железных руд расходуется 600—750 кг каменноугольного ко кса. Плавка стали в мартеновских печах происходит при очень высокой температуре жидкая сталь выпускается из печи при 1500° С и выше. Тепло выделяется в печах при интенсивном сжигании газообразного или жидкого то плива. В Советском Союзе примерно 80% всей электрической энергии вырабатывается на тепловых электрических станциях, где в тепловых двигателях теплота преобразовывается в механическую работу.
[c.169]
Работы в СССР по охране окружающей среды применительно к литейному производству ведутся в направлении уменьшения токсичности используемых материалов, сокращения выбросов в атмосферу различных вредных газов, очистки и вторичного использования стоков промьшшенных вод, уменьшения и более полного использования отходов производства. Например, для реконструируемых и вновь построенных литейных цехов и центролитов предусматривается процесс плавки только в электрических плавильных агрегатах. Для плавки чугуна взамен вагранок, которые сильно загрязняют атмосферу, используют индукционные плавильные печи промышленной частоты ИЧТ6, ИЧТ 10 и более мощные. Там, где по ряду причин невозможно в реконструируемом цехе поставить электрические плавильные агрегаты для плавки чугуна, открытые вагранки заменяют закрытыми с рекуперацией теплоты отходящих газов, с дожиганием и очисткой их.
[c.217]
Плавку металла выполняют в различных плавильных устройствах. Чугун плавят в (загранках, сталь — в конвертерах и электропечах, цветные металлы и их сплавы — в электрических печах и тиглях. Температуру расплавленного мет1тла доводят до температуры заливки. В среднем температура заливки на 100-150 С выше температуры плавления сплава. [c.125]
Распространённость железа в земной коре 4,2 /о. Чистое железо получают обычно путём восстановления окиси РегОз водородом. Полученный таким образом порошок железа обладает пирофорностью, т. е. самовозгорается на воздухе. Промышленный способ получения железа основан на промежуточном получении чугуна доменным процессом с последующей плавкой в мартеновских печах, конвертере или электрических печах. Со многими элементами (Сг, Ni, Со, W, Мп, V и т. п.) железо образует сплавы, имеющие огромное значение в технике. Роль железа и его сплавов для человека неизмеримо велика.
[c.366]
Цинковые сплавы широко применяются для литья под давлением. Плавка их чаще всего производится в чугунных или стальных котлах, отапливаемых мазутом или газом, или в электрических индукционных печах типа Аякс. Цинк загружают в предварительно нагретые котлы. Легкоплавкие свинец, кадмий и олово вводят в сплав в виде чистых металлов, медь присаживают в виде тонких латунных обрезков. Плавка цинковых сплавов, содержащих медь и алюминий, даёт наилучшие результаты, если добавить эти металлы в виде лигатуры Си —А1 (БОО/о 50/о). При наличии в шихте отходов (лом, возврат) первыми загружают в печь отходы, затем
[c.197]
При изготовлении чугунных втулок применяется центробежное литье. Чугун берется определенного состава, проверяемого анализом. Для плавки вместо вагранок применяются качающиеся электрические печи. Это позволяет обеспечить лучшие условия для контроля за ходом плавки и более равномерного распределения легирующих элементов, а также создать температуру, достаточно высокую для растворения всего графита, чтобы при охлаждении он принимал шаровидную форму, что придает металлу прочность и однородность. Взвешенные порции металла разливаются в стальные подогретые формы, вращающиеся до тех пор, пока металл не затвердеет. Скорость вращения составляет 1500— 3000 об1мин в зависимости от размера втулки. После извлечения из форм втулки отжигаются в течение часа при температуре 954° С, а затем охлаждаются с понижением температуры на 38° С в час до прохождения нижней критической точки. Структура чугуна отливок — шаровидный графит плюс перлитпо-ферритовая металлическая основа. Втулки, полученные из отливок механической обработкой, подвергаются закалке. Предел прочности втулок на растяжение составляет более 35 кГ/см . Химический состав чугуна (в %) никеля — 1,25 молибдена — 0,50 кремния — 2,00—2,20 серы — 0,04—0,07 фосфора — 0,20 общего углерода — 2,85—3,00 связанного углерода — 0,40—0,60 в отожженных втулках и 0,70—0,80 в закаленных втулках. Твердость закаленных втулок составляет HRG 40—44.
[c.270]
Сталь выплавляют из жидкого чугуна в конверторах (бессемеровский, томасовский и кислородно-конверторный способы) или переплавляют в пла.менных (мартеновский способ) и электрических печах. Бессемеровский способ основан на продувке жидкого чугуна, находящегося в конверторе (реторте) с динасовой (кислой) кладкой, холодным воздухом. Из чугуна при продувке через днище конвертора выгорает углерод, кремний, марганец, сера и фосфор, вследствие чего чугун превращается в сталь. Если конвертор имеет кладку (футеровку) из доломита (основную) и для плавки добавляют известь, способ называют томасовским. Кислородно-конверторный способ заключается в продувке чугуна технически чистым кислородом. Мартеновский способ—это процесс получения стали из чугуна и железного лома переплавкой их на поду мартеновской печи. Переплавка металлов в печах, нагреваемых электрическим током, называется электрической плавкой.
[c.18]
Для плавки чугуна применяются вагранки, пламенные и электрические печи. К основным особенностям плавки в вагранках относятся непрерывность процесса, относительно низкий расход топлива и сравнительно высокий к. п. д. (40—45%). Стоимость плавки ниже, чем в пламенных или электрических печах. Производительность вагранок обычно равна 1—20 т/ч, а в отдельных случаях до 30 тп1ч. [c.102]
В кр шных механизированных цехах, изготовляюш,их литье из серого и ковкого чугуна, пламенные и электрические печи применяются в сочетании с вагранками. Расплавление чугуна производится в более экономичном агрегате — вагранке, а доводка по составу и температуре — в пламенной или электрической печи. Такой процесс плавки называется дуплекс-процессом.
[c.103]
Обзор литья металлов для начинающих — плавка, плавка, литье и литье
Привет всем, решил, что сделаю свой первый пост чем-то полезным, а не вопросом. Я знаю о литье больше, чем о кузнечном деле, поэтому решил, что помогу немного добавить в раздел литья, предоставив общий обзор того, как начать литье, справочники, необходимое оборудование, меры безопасности и т. Д. Надеюсь, это будет что-то, на что можно сослаться, чтобы дать какое-то направление людям, спрашивающим «как мне начать лить металл» или «могу ли я отлить свою собственную наковальню» и т. д., поскольку, похоже, таких сообщений довольно много.Я только что пролил бронзу и в итоге неоднократно объяснял процесс всем своим соседям по дому, где я живу и работаю, так что все это в любом случае было у меня в голове на этой неделе. Перед всей информацией я покажу несколько фотографий заливки, так как это всегда выглядит довольно круто.
Вид работающей печи с паковочными формами на переднем плане:
Я что-то проверяю или тыкаю:
Вынимаю тигель из печи:
Заливка:
Заливка:
Вот что было внутри (16 желудей + стробоскоп):
Acorn TIG, приваренный к стальному оголовку (будет прикреплен к кованой ветке на воротах):
Пучок желудей, готовый к прикреплению к воротам:
БЕЗОПАСНОСТЬ
Не делайте этого, если не выполнили надлежащую проверку.В идеале вы должны учиться у кого-то лично, но если это невозможно, вам следует прочитать несколько книг (рекомендации в конце этого поста) и посмотреть несколько видеороликов о разливке домашнего металла в Интернете. Расплавленный металл в любом количестве, превышающем сварочную лужу, чрезвычайно опасен, и несоблюдение этого требования может привести к серьезной аварии. Если есть вопросы, задавайте. Не вини меня, если ты поранишься.
РАСПЛАВЛЕННЫЙ МЕТАЛЛ
Если у вас есть какое-либо количество расплавленного металла, влага становится чрезвычайно опасной. Капля расплавленного металла на бетон (который удерживает влагу) превратит воду в порах в пар, вызывая небольшой взрыв, который выбрасывает жидкий металл и крошку бетона в воздух. А теперь подумайте, что было бы, если бы вы пролили целый тигель. ВСЕГДА ПЕРЕНОСИТЕ МЕТАЛЛ НА СУХИЙ ПЕСК.
Если вы воткнете что-нибудь — палочку для перемешивания, скиммер, еще кусочки металла для плавления — в тигель, когда в нем есть расплавленный металл, этот объект должен быть DRY .Это так же просто, как предварительный нагрев металла на верхней части печи во время ее работы и удерживание конца любых инструментов в вытяжном пламени в течение нескольких секунд, но если вы забудете, вы заставите расплавленный металл взорваться, пока вы стоите там. с вашим лицом над ним. Точно так же ваши изложницы (в которые вы заливаете оставшийся металл после заполнения форм) необходимо предварительно нагреть в печи, иначе произойдет взрыв. ПРЕДПОЛАГАЕМ, ЧТО, ЕСЛИ ЧТО-ТО НЕ СЛИШКОМ ГОРЯЧЕ, ЧТО ЭТО ВЛАЖНОЕ
ПРЕДОХРАНИТЕЛЬНОЕ ОБОРУДОВАНИЕ
Очки и маска для лица, а не одно или другое. Плотная кожаная куртка, сварочные перчатки, джинсы и толстые кожаные ботинки. Это то, что я ношу. Прекрасно работает, защищая от случайных брызг, и, по крайней мере, не тает на вашей коже в случае бедствия. Всегда держите под рукой ведро с сухим песком и лопату на случай разлива, а также охлаждающую штангу (кусок тяжелого углового железа, приваренный к концу трехфутового стержня), чтобы задержать поток в случае разрыва формы или течь.
ДОМАШНИЕ ТИГИ
Из-за серьезных опасностей, связанных с работой с расплавленным металлом, я настоятельно рекомендую НЕ использовать самодельные тигли для чего-либо более горячего, чем алюминий (например, любых медных сплавов и чугуна). Подходящие тигли будут описаны ниже для каждого отдельного металла, а также будет объяснен подходящий самодельный тигель для алюминия и других низкотемпературных сплавов.
Правильные тигли необходимы, даже если вы выполняете все остальные настройки:
—————————— ————-
Сначала я дам краткий обзор различных металлов, которые вы, возможно, захотите отлить, а затем расскажу некоторые подробности об общем оборудовании, которое вам нужно будет сделать. для небольшого литейного производства.
——————————————-
МЕТАЛЛЫ
СТАЛЬ
Хорошо, во-первых, вы, вероятно, никогда не собираетесь лить сталь дома, и вы определенно никогда не собираетесь делать стальную отливку размером с наковальню. Это просто реальность. Довести тигельную печь до температуры, необходимой для разливки стали, можно, но это превратит вашу печь в расходный материал. Я коснусь этого в первую очередь, поскольку похоже, что многие люди интересуются литьем стали.
Вот приблизительные температуры плавления некоторых металлов (все температуры в F):
Мягкая сталь: 2750
Чугун: 2100
Кремниевая бронза: 1800
Алюминий: 1200
Свинец: 680
Имейте в виду, что вам нужно, чтобы металл был перегрет на несколько сотен градусов выше этих температур, чтобы его успешно разлить, так, например, железо будет разливаться около 2300-2500 (горячее для более тонких отливок). Температура в вашей печи должна быть еще выше, а это значит, что внутренняя температура печи будет близка к 3000. Огнеупор, который я использовал для своей печи, рассчитан на 3000, а поскольку низкоуглеродистая сталь плавится около 2750, вы можете понять, почему его плавление быстро разрушит вашу печь. Вот картина огнеупорной футеровки на моей печи, где капли расплавленного железа высадились на него:
бронзы и алюминий будет просто прилипает к поверхности, но расплавленное железо буквально съедает прямо в него. Печь настолько нагревается, что вам понадобится одна из зеленых оксиацетиленовых масок, чтобы увидеть ее с открытой крышкой. Он просто не выдерживает температуры, необходимой для плавления стали.
ЧУГУН
Тем не менее, с правильно построенной печью плавление чугуна совсем не сложно, однако вам необходимо использовать песчаные формы, так как формы для выплавки, которые вы делаете дома (обсуждаются ниже), не выдерживают температуры расплавленного металла. железо (пробовал). Формование из песка — это само по себе искусство, и для его правильного выполнения потребуется немало практики. В конце поста есть несколько хороших книг по этому поводу. Наконец, для чугуна вам необходимо приобрести графитовый тигель на глиняной связке. НЕ ПЛАВАЙТЕ ЖЕЛЕЗ В ЧТО-ТО ВЫ САМИ СДЕЛАНО . Тигель обойдется вам в 50-100 долларов. Это очень дешевый страховой полис, который стоит каждого пенни. Серьезно. Без шуток. Практически все литейное оборудование, которое у меня есть, — самодельное, кроме тиглей для бронзы и железа.
BRONZE
Хорошо, перейдем к цветным металлам. Лично я использую только кремниевую бронзу для отливок из медного сплава по ряду причин. Во-первых, это состав: 96% меди, 3% кремния и 1% марганца.Вот почему это важно: латунь и другая бронза обычно содержат значительное количество цинка, олова и / или свинца помимо меди. Чтобы расплавить эти сплавы, их нужно нагреть выше температуры, при которой легирующие элементы испаряются. Это означает, что некоторое количество цинка, свинца, олова и т. Д. Улетучится с поверхности в виде газа, особенно когда вы перемешиваете или снимаете слой расплава. Это означает, что вы не только подвергаете себя воздействию токсичных паров, но и меняете состав металла каждый раз, когда его плавите.Кремниевая бронза не меняет состав даже после плавления в течение нескольких десятков раз (если вы держите тигель только для этого сплава), что делает ее идеальной для домашнего использования, где мы не можем проверить состав наших сплавов и где мы хотим немедленно повторно используйте металл, из которого состоит система ворот. Кроме того, вы можете купить прутки из кремнистой бронзы у большинства поставщиков сварочных материалов, что означает, что вы можете сварить их с помощью кислородно-ацетиленовой горелки или сварочного аппарата TIG и получить идеальное цветовое соответствие (особенно хорошо для фиксации небольших ямок в отливках и сварки двух отливок вместе и смешивание сварного шва).По этим причинам я считаю целесообразным покупать кремниевую бронзу вместо того, чтобы использовать куски лома неизвестного состава.
Что касается бронзы, вы действительно действительно хотите купить тигель, а не делать его. В частности, купите тигель из карбида кремния — опять же, около 50–100 долларов, и снова он того стоит. Я использовал самодельный тигель описанного ниже типа для плавления чистой меди, так как я не хотел загрязнять свой тигель для кремниевой бронзы и не хотел тратить 100 долларов на одноразовый эксперимент.Все шло хорошо, медь плавилась, я снял ее, а затем закрыл крышку печи, чтобы нагреть ее еще минуту, так как отливка должна была быть довольно тонкой, и я хотел, чтобы она была действительно горячей. Когда я снова открыл крышку, чтобы вынуть тигель, она вышла из строя, и дно печи было озером расплавленной меди. Если бы я не решил нагреть его еще на минуту, он бы вышел из строя, когда я поднимал его из печи. Это было бы примерно полгаллона расплавленного металла на моих ногах и ботинках.
АЛЮМИНИЙ
Алюминий отлично работает с ломом, но для достижения наилучших результатов используйте литой (не экструдированный) алюминий. Это означает, что автомобильные колеса, детали велосипеда и т. Д. Идеальны, но не так много трубок, листов, пивных банок и т. Д. Поскольку алюминий плавится при такой низкой температуре, вы можете безопасно использовать стальной тигель ИДЕАЛЬНОЙ КОНСТРУКЦИИ или, что еще лучше, чугунный тигель. Чтобы сделать стальной тигель, достаточно приварить кусок толстостенной трубы к более толстой пластине. Я с большим успехом использовал стенку 1/4 дюйма и 4-дюймовую трубу высотой около 10 дюймов, приваренную к куску пластины 3/8 дюйма.Сбоку приварил проушины для захвата клещами. Если вы не являетесь квалифицированным сварщиком, попросите кого-нибудь сварить его для вас, это не тот сварной шов, который вы хотите испортить. Кроме того, как и в случае с любым тиглем, вам нужно специально изготовить щипцы, которые очень хорошо подходят без люфта.
LEAD
Свинец плавится при такой низкой температуре, что вам даже не понадобится печь, только подходящий стальной или чугунный контейнер и несколько горелок. Мой сосед недавно отлил свинцовый киль весом 1100 фунтов для лодки, которую он строит, поместив свинец в модифицированную чугунную ванну, расплавив его несколькими кровельными горелками и выколов его снизу в деревянную форму с песчаным покрытием. Я не рекомендую деревянные формы — обработка поверхности не самая лучшая из-за влаги в форме, а пожарная часть была вызвана из-за чрезмерного копчения. Все вышеперечисленные меры безопасности применяются даже без печи, и помните, что свинец чрезвычайно токсичен.
ОБОРУДОВАНИЕ
Помимо тиглей для бронзы и / или железа, а также воздуходувки, вы можете легко сделать все, что вам нужно, самостоятельно. Вся моя литейная стоимость легко составляла менее 1000 долларов, включая несколько хороших книг (купленных новых, перечисленных ниже), два тигля, мою печь (материалы стоили около 300 долларов), гончарную печь (60 долларов на Craigslist и необходимые только для потерянного воска литье), электрическая воздуходувка (25 долларов на Craigslist) и множество самодельного оборудования, в основном сделанного из лома стали.Моя печь надстроена и, вероятно, больше, чем могло бы понадобиться многим здесь людям. Вы можете гораздо меньше потратить на простую настройку. Вот весь мой литейный цех, запакованный в углу моего цеха (выходит только время от времени):
ПЕЧЬ
Центральным оборудованием в литейном цехе является печь. Что касается масштабов, о которых мы говорим, тигельная печь — безусловно, самая разумная вещь для строительства, так что это все, что я буду обсуждать. Вы можете построить относительно печь, работающую на пропане или природном газе, которая в основном представляет собой вертикальную газовую кузницу с крышкой.Однако этим печам будет трудно плавить железо, если они вообще смогут это сделать. Я настоятельно рекомендую купить у Колина Пека (в Англии) руководство под названием «Печь для отработанного масла от литья чугуна искусного Боджера». Это то, что я сделал, и никогда не стал бы строить печь другого стиля. Конструкция корпуса печи проста и легко модифицируется для использования имеющегося у вас лома, и он усовершенствовал конструкцию горелки, в которой для сжигания отработанного масла используется гравитационная подача (отработанное растительное масло, отработанное моторное масло и дизельное топливо работают хорошо. ).На горелке есть форсунка, поэтому топливо не распыляется, что означает, что вы можете использовать отработанное масло (свободное, но загрязненное частицами), не забивая горелку.
Кроме того, поскольку оно подается под действием силы тяжести, нет необходимости в насосе, а масло при атмосферном давлении НАМНОГО безопаснее, чем сжатый газ, когда вы работаете с расплавленным металлом. Кроме того, он выделяет намного больше тепла, чем пропан или природный газ — я могу расплавить 30 фунтов бронзы при холодном запуске менее чем за 45 минут. Правильно построенный, он очень чисто горит (не дымится) и может легко плавить чугун.Он определенно может расплавить сталь, если вы захотите, но это быстро испортит футеровку печи. Используя в основном подручные материалы, я потратил около 300 долларов на свою печь. Стоимость — это, прежде всего, литой огнеупор с температурой 3000 градусов (очень рекомендуется), который, как мне кажется, стоил 65 долларов за мешок весом 50 фунтов (я использовал 3) около 5 лет назад. Я не буду вдаваться в подробности о конструкции печи, поскольку Колин пытается продать свою книгу, поэтому вам придется купить ее у него, если вам нужны планы (обратите внимание, я никоим образом не извлекаю выгоду из этого, и я не даже знаю Колина.
Просто это такой хороший дизайн, что это все, что я хочу порекомендовать).
РУЧНЫЕ ИНСТРУМЕНТЫ
Вам понадобятся различные простые инструменты, которые вы легко можете изготовить самостоятельно. Здесь изображены разливочный стержень (длинная вещь, которая удерживает тигель во время разливки), щипцы для тигля (для подъема тигля в печь и из печи), скиммер (угловая сталь, приваренная к стержню, изогнутая на конце, чтобы соответствовать моему тиглю, используется для снятия шлака перед разливкой) и изложницы (угловой чугун с закрытыми концами и рукояткой для выливания остатков металла после заполнения изложниц).Другие инструменты, не изображенные на рисунке, включают стальной стержень 1/2 дюйма для перемешивания, охлаждающую штангу (описанную выше в разделе «Оборудование для обеспечения безопасности»), пару щипцов для загрузки предварительно нагретого металла в тигель. Действительно простые вещи. Также обратите внимание, что для измерения температуры вам не нужен пирометр. Просто возьмите стержень диаметром 1/2 дюйма, который вы используете для перемешивания, воткните его на секунду в расплав, а затем вытащите. Если расплавленный металл соскользнет с конца, вы готовы к заливке. Если он на нем слипается, значит, он недостаточно горячий. Этот метод никогда не подводил меня для алюминия, бронзы и железа.
ИНСТРУМЕНТЫ ДЛЯ ФОРМЫ
Это зависит от того, выполняете ли вы литье в песчаные формы или по выплавляемым моделям. Я не делал форм для песка несколько лет, и у меня больше нет инструментов для этого, поэтому я не буду пытаться перечислять то, что вам нужно, это просто простые ручные инструменты и мюллер, если вам повезет, чтобы скрестить дорожки с одним. Я бы порекомендовал новичкам использовать Petrobond (песок на масляной основе), а не песок на водной основе, так как с ним легче работать и поддерживать его.
Я не буду вдаваться в подробности фактического процесса литья под давлением, но если вам интересно, вы должны купить последнюю книгу, указанную в конце этого поста.Я скажу, однако, что «микрокристаллический воск» — это то, что вы хотите купить, если делаете скульптурные изделия. Он становится очень мягким при нагревании от ваших рук, а затем может выдерживать любое скручивание или изгиб, не трескаясь, и очень плавно перетекает в себя. Подобно кремниевой бронзе, этот продукт настолько превосходен, что стоит своих денег. Паковочные формы легко сделать из 1 части воды, 1 части гончарного гипса и 2 частей грубого песка.
Для этого процесса вам нужно будет выжечь формы в печи, чтобы расплавить, сжечь и, наконец, испарить воск, а также прокалить формы.Вам нужно запустить его в течение нескольких дней и медленно повышать температуру, в конечном итоге поддерживая формы на уровне 1200 в течение дня и заполняя их расплавленным металлом, когда они остынут примерно до 800. Стандартная гончарная печь работает нормально, но будьте готовы проснуться вставайте один или два раза каждую ночь, чтобы проверить температуру, если у вас нет цифрового контроллера. Кроме того, вы можете выжечь другие органические предметы (овощи, палки и т. Д.) Вместо того, чтобы лепить что-то воском.
ПОСТАВЩИКИ / МАТЕРИАЛЬНЫЕ РЕСУРСЫ
Budget Casting Supply — ваш лучший выбор для покупок в Интернете, но если вы живете в большом городе или рядом с ним, вам действительно следует искать местных поставщиков.Если вы не знаете ни одного, попробуйте поискать в ThomasNet. Если вы не знакомы, этот веб-сайт представляет собой базу данных производителей и поставщиков с возможностью поиска, что очень полезно. Часто предприятия, поставляющие литейное оборудование или огнеупоры, никогда не имеют случайных клиентов, и если вы объясните, чем вы занимаетесь, они часто будут очень заинтригованы и постараются помочь вам. Мне еще предстоит заплатить за изоляцию из керамического волокна, хотя я получил ее в большом количестве между различными кузницами и моей печью — крупный поставщик огнеупоров обычно может предоставить вам «образец», которого более чем достаточно для того, что вы работаете на.
——————————————-
Вот и все У меня есть для вас, не написав об этом книги. Надеюсь, это будет полезно для некоторых из вас, кто хочет добавить литье в свои навыки работы с металлом. Я буду более чем счастлив ответить на любые ваши вопросы, и если кто-то находится в районе Филадельфии и хочет увидеть разлив, просто дайте мне знать, и я приглашаю вас к следующему.
——————————————-
РЕКОМЕНДУЕМЫЕ ЧТЕНИЯ
— «Печь для отработанного масла при отливке чугуна искусного Боджера» Колина Пека
… Доступно у автора по адресу http: //www.artfulbod…alcasting.com/. Это руководство — то, что я использовал, чтобы построить свою печь, описанную выше. Не думаю, что когда-либо построил бы тигельную печь, не основанную на этой конструкции. Ужасно написано, никогда даже не корректируется, но тем не менее бесценно.
— «Библия литейщика» К. В. Аммена
— «Полное руководство по литью в песчаные формы» также К. В. Аммен
… Книги Аммена очень удобочитаемы и понятны. Получите их независимо от того, делаете ли вы формы из песка или паковочные массы.
— «США. Руководство Navy Foundry », перепечатанное Lindsay Publications
.
… бесценный ресурс, но не из тех книг, которые вы читаете насквозь (например, скучное техническое руководство). Опять же, хотя он написан, в частности, для литья в песчаные формы, большая часть информации также имеет отношение к литью по выплавляемым моделям.
— «Литейный уголь» Дэйва Джинджери
… отлично подходит для начала, это песочное литье в наиболее упрощенной форме. Идеально подходит для супер-недорогой установки, чтобы залить немного алюминия, чтобы узнать, нравится ли он вам.
— «Литье металла: руководство по литью в песчаные формы для малых литейных производств» Стива Честейна
… есть два тома. Хорошие книги, но не обязательно, если вас интересует только литье по выплавляемым моделям.
— «Студийное литье из бронзы: метод потерянного воска» Джона Миллса и Майкла Гиллеспи
… для литья по выплавляемым моделям.
Также проверьте Lindsay Publications, чтобы узнать о других книгах по кастингу, включая некоторые из перечисленных выше.
Чугун | Металлургия для чайников
Чугун получают из чушкового чугуна, и хотя он обычно относится к серому чугуну, он также определяет большую группу сплавов железа, которые затвердевают с эвтектикой.По цвету изломанной поверхности можно идентифицировать сплав. Белый чугун назван в честь его белой поверхности при разрушении из-за его карбидных примесей, которые позволяют трещинам проходить сквозь них. Серый чугун назван в честь его серой изломанной поверхности, которая возникает из-за того, что чешуйки графита отклоняют проходящую трещину и инициируют бесчисленные новые трещины по мере разрушения материала.
Чугун Автозапчасти
Углерод (C) и кремний (Si) являются основными легирующими элементами, количество которых варьируется от 2.От 1 до 4 мас.% И от 1 до 3 мас.% Соответственно. Сплавы железа с меньшим содержанием углерода известны как сталь.
Хотя это технически делает эти базовые сплавы тройными сплавами Fe-C-Si, принцип затвердевания чугуна понятен из бинарной фазовой диаграммы железо-углерод. Поскольку состав большинства чугунов находится в районе эвтектической точки системы железо-углерод, температуры плавления тесно коррелируют, обычно в диапазоне от 1150 до 1200 ° C (от 2102 до 2192 ° F), что составляет около 300 ° C (572 ° F). F) ниже точки плавления чистого железа.
Фазовая диаграмма Сталь и чугун
Чугун имеет тенденцию к хрупкости, за исключением ковкого чугуна. Обладая относительно низкой температурой плавления, хорошей текучестью, литейными качествами, отличной обрабатываемостью, устойчивостью к деформации и износостойкостью, чугуны стали конструкционным материалом с широким спектром применения и используются в трубах, машинах и деталях автомобильной промышленности, таких как цилиндры. головки (снижение использования), блоки цилиндров и коробки передач (снижение использования).Он устойчив к разрушению и разрушению в результате окисления (ржавчины).
Чугунные украшения
Чугун получают путем переплавки передельного чугуна, часто вместе с значительным количеством железного лома и стального лома, и принятия различных мер по удалению нежелательных загрязняющих веществ, таких как фосфор и сера. В зависимости от области применения содержание углерода и кремния снижается до желаемого уровня, который может составлять от 2 до 3,5% и от 1 до 3% соответственно. Затем в расплав добавляются другие элементы, прежде чем окончательная форма будет произведена путем литья.[необходима цитата] Железо иногда плавят в доменной печи особого типа, известной как вагранка, но чаще плавят в электрических индукционных печах. [необходима цитата] После завершения плавки расплавленное железо выливается в печь для выдержки или ковш.
Чугун Art
Свойства чугуна изменяются за счет добавления различных легирующих элементов или легирующих добавок. После углерода кремний является наиболее важным легирующим агентом, поскольку он вытесняет углерод из раствора. Вместо этого углерод образует графит, в результате чего чугун становится более мягким, уменьшается усадка, прочность и плотность.Сера при добавлении образует сульфид железа, который предотвращает образование графита и увеличивает твердость.
Проблема с серой заключается в том, что она делает расплавленный чугун вялым, что приводит к краткосрочным дефектам. Чтобы противодействовать воздействию серы, добавляют марганец, потому что они превращаются в сульфид марганца вместо сульфида железа. Сульфид марганца легче расплава, поэтому он имеет тенденцию всплывать из расплава в шлак. Количество марганца, необходимое для нейтрализации серы, равно 1.7 × содержание серы + 0,3%. Если добавить больше этого количества марганца, то образуется карбид марганца, который увеличивает твердость и охлаждение, за исключением серого чугуна, где до 1% марганца увеличивает прочность и плотность.
Фазовая диаграмма железа и углерода
Никель является одним из наиболее распространенных легирующих добавок, поскольку он улучшает структуру перлита и графита, улучшает ударную вязкость и выравнивает разницу в твердости между толщиной сечения. Хром добавляется в ковш в небольших количествах для уменьшения содержания свободного графита, получения холода и потому, что он является мощным стабилизатором карбида; никель часто добавляют вместе.Можно добавить небольшое количество олова вместо 0,5% хрома. Медь добавляется в ковш или в печь в количестве от 0,5 до 2,5% для уменьшения охлаждения, очистки графита и увеличения текучести.
Кухонный гарнитур из чугуна
Молибден добавляется от 0,3 до 1% для увеличения охлаждения и улучшения структуры графита и перлита; его часто добавляют в сочетании с никелем, медью и хромом для получения высокопрочных чугунов. Титан добавляют в качестве дегазатора и раскислителя, но он также увеличивает текучесть.От 0,15 до 0,5% ванадия добавляют в чугун для стабилизации цементита, увеличения твердости и повышения устойчивости к износу и нагреванию. Цирконий от 0,1 до 0,3% способствует образованию графита, раскислению и увеличению текучести. В расплавы ковкого чугуна добавляют висмут в диапазоне от 0,002 до 0,01%, чтобы увеличить количество кремния, которое можно добавить. В белое железо бор добавлен, чтобы способствовать производству ковкого чугуна, он также снижает эффект огрубления висмута.
Машинный блок из чугуна
Серый чугун
Серый чугун характеризуется своей графитовой микроструктурой, из-за которой изломы материала приобретают серый цвет.Это наиболее часто используемый чугун и наиболее широко используемый литой материал в зависимости от веса.
Микроструктура серого чугуна
Большинство чугунов имеют химический состав от 2,5 до 4,0% углерода, от 1 до 3% кремния, а остальное — железо. Серый чугун имеет меньшую прочность на разрыв и ударопрочность, чем сталь, но его прочность на сжатие сопоставима с низко- и среднеуглеродистой сталью.
Белый чугунПри более низком содержании кремния и более быстром охлаждении углерод в белом чугуне выделяется из расплава в виде цементита метастабильной фазы, Fe3C, а не графита.Цементит, который выделяется из расплава, образует относительно крупные частицы, обычно в эвтектической смеси, где другой фазой является аустенит (который при охлаждении может превратиться в мартенсит).
Белый чугун — это нелегированный чугун с низким содержанием углерода и кремния, так что структура представляет собой твердый хрупкий карбид железа без свободного графита. Белый чугун широко используется при абразивном износе, включая дробление, шлифование, фрезерование и обращение с абразивными материалами
Эти эвтектические карбиды слишком велики, чтобы обеспечить дисперсионное твердение (как в некоторых сталях, где выделения цементита могут препятствовать пластической деформации, препятствуя движению дислокаций через ферритную матрицу).
Скорее, они увеличивают объемную твердость чугуна просто за счет своей собственной очень высокой твердости и значительной объемной доли, так что объемная твердость может быть аппроксимирована правилом смесей. В любом случае они предлагают твердость за счет прочности. Поскольку карбид составляет значительную долю материала, белый чугун с полным основанием можно отнести к кермету.
Микроструктура белого чугуна
Белый чугун слишком хрупкий для использования во многих конструктивных элементах, но с хорошей твердостью и стойкостью к истиранию и относительно низкой стоимостью он находит применение в таких областях применения, как износостойкие поверхности (рабочее колесо и спиральная камера) шламовых насосов, гильзы корпуса и подъемные стержни шаровые мельницы и мельницы автогенного помола, шары и кольца в измельчителях угля, а также зубья ковша экскаватора (хотя для этого применения более распространена литая среднеуглеродистая мартенситная сталь).
Ковкий чугунКовкий чугун сначала представляет собой отливку из белого чугуна, которую затем подвергают термообработке при температуре около 900 ° C (1650 ° F). В этом случае графит отделяется гораздо медленнее, так что поверхностное натяжение успевает превратить его в сфероидальные частицы, а не хлопья. Из-за их более низкого соотношения сторон сфероиды относительно короткие и далеко друг от друга, и имеют меньшее поперечное сечение по сравнению с распространяющейся трещиной или фононом.
Микроструктура ковкого чугуна
Деталь фитинга из ковкого чугуна
У них также есть тупые границы, в отличие от чешуек, что снижает проблемы концентрации напряжений, с которыми сталкивается серый чугун.В целом ковкий чугун по своим свойствам больше похож на низкоуглеродистую сталь. Существует предел того, насколько большая деталь может быть отлита из ковкого чугуна, поскольку она сделана из белого чугуна.
Детали из ковкого чугуна
Ковкий чугунБолее поздняя разработка — чугун с шаровидным графитом или высокопрочный чугун. Незначительные количества магния или церия, добавленные к этим сплавам, замедляют рост выделений графита за счет связывания с краями графитовых плоскостей.
Микроструктура чугуна с шаровидным графитом
Наряду с тщательным контролем других элементов и времени, это позволяет углю отделяться в виде сфероидальных частиц по мере затвердевания материала.Свойства аналогичны ковкому чугуну, но можно отливать детали с большим сечением.
Вам нужны ссылки на книги о чугуне? здесь…
Возможно вам понравится
Случайные сообщения
- Как производится алюминий
Производство алюминия осуществляется в два этапа: процесс Байера по переработке бокситовой руды для получения оксида алюминия … - Глоссарий по металлургии
Активность: функция химического потенциала системы.Сплав: Металлическое вещество, состоящее из двух или более … - Композиционных материалов
Композиционные материалы образуются путем объединения двух или более материалов, которые имеют совершенно разные свойства. Различные ма … - Биоматериалы
Биоматериал — это любой материал, поверхность или конструкция, которые взаимодействуют с биологическими системами. Разработка биоматериалов … - Ковкий чугун с закалкой (ADI)
Ковкий чугун с закалкой, или ADI, представляет собой тип ковкого чугуна, который характеризуется повышенной прочностью и прочностью на разрыв…
Контроль химического состава расплавленного чугуна и текучести металла | Mastermelt
Ингредиенты шихты, будь то электрическая печь или вагранка, разработаны для получения окончательного химического состава, необходимого для разливки отливок. К сожалению, составление шихты не определяет окончательный химический состав или качество расплавленного чугуна. Плавление — это не просто процесс переплавки существующих металлических материалов: шлаковые воздействия во время процесса плавления — вызванные или вызванные химической реакцией шлака / металла — играют важную роль в химии железа и качестве готового металла
Химия расплавленного железа вариации происходят из двух основных источников:
(1) Точность веса отдельных металлических и легированных ингредиентов в загрузке; и,
(2) Химические реакции (реакции шлака / металла), которые происходят в процессе плавления и вызывают непредсказуемые и широко варьирующие потери C, Si, MN и других необходимых элементов.
Потери в результате окисления вызывают 99% всех изменений химического состава расплавленного чугуна. Нежелательные изменения веса ингредиентов загрузки, которые, как часто предполагается, приводят к изменениям химического состава, на самом деле оказывают незначительное влияние на большинство операций плавления. Вы должны испытать плавление без потерь при окислении, чтобы оценить важность этого.
Значительные различия в химическом составе металлов, с которыми сталкиваются некоторые литейные предприятия по производству черных металлов, вызваны потерей основных элементов при окислении. Это простое аналитическое сравнение: химический состав будет отличаться на 50% при 50% потере окисления.Окисление необходимо контролировать, чтобы достичь «прямолинейного» химического состава.
Можно ли контролировать углерод для получения химии с прямой линией? Однозначно да. Купольные печи производительностью 100 тонн в час работали в течение всего дня с изменением содержания углерода 0,01% C, и такой исключительный контроль химического состава возможен при любой плавильной операции.
Впрыск фурмы можно использовать для противодействия потерям на окисление в вагранке, в дополнение к добавлению углерода и кремния в расплавленный металл, выходящий из вагранки.Во-первых, нужно решить проблему окисления. Затем можно ввести кремний и углерод в любых количествах, необходимых для уменьшения химического состава.
Вводимые материалы должны быть «пригодными для инъекций» и «качества для инъекций»: карбид кремния (SiC) и графит стандартного качества не подходят. Просто материалы более низкого качества не работают, и их использование дискредитирует фурменный впрыск как надежный инструмент плавления.
SiC должен обладать высокой скоростью растворения в жидком чугуне, и только несколько марок SiC подходят.Углерод должен обладать столь же высокой скоростью растворения в расплавленном чугуне, и ни один из широко доступных графитовых концентраторов углерода не соответствует этому квалификационному стандарту.
Химия для обрезки — Для обрезки химического состава купола металла можно вводить как углерод, так и карбид кремния. Инженеры Mastermelt потратили два года на разработку технологии и навыков, необходимых для определения конкретных материалов, которые можно эффективно вводить.
Бессмысленно вводить SiC и углеродные материалы, которые не обеспечивают полное извлечение углерода или кремния.Без полного восстановления химический контроль еще больше ухудшается.
И углерод, и SiC обычно вводятся через фурму, и оба материала уникальны: они не плавятся, а попадают в расплавленное железо посредством атомного обмена на границе расплавленный металл. Управляющие силы, управляющие скоростью поступления этих материалов в расплавленное железо, сложны, и их лучше оставить ученым и кристаллографам. Скорость проникновения углерода и карбида кремния в расплавленный чугун — неотъемлемые свойства материала.Свойства развиваются в процессе производства материала и сбрасываются по завершении производства.
Когда компания Mastermelt впервые представила систему впрыска SiC в фурму, многие поставщики и литейные предприятия последовали ее примеру и начали вводить газ; ни одна из конкурирующих систем впрыска SiC не оказалась успешной. Многие из этих систем вводили «инжекционный уголь», который оказался коксовой мелочью. К сожалению, многие (если не все) из этих пользователей однозначно доказали, что коксовая мелочь неэффективна для контроля химического состава железа, хотя некоторые поставщики по-прежнему рекомендуют ее.
Когда впрыскиваемый углерод или карбид кремния обеспечивает полное восстановление расплавленного чугуна, плавильный персонал получает очень эффективный инструмент для точной очистки химического состава. Один из руководителей плавления сообщил, что впрыск фурмы Mastermelt DeOX переводит купол в режим «круиз-контроля» для химического контроля на протяжении всей кампании плавления.
Непонимание химии — Многие объяснения появляются, когда химический состав расплавленного железа не соответствует техническим требованиям. При плавлении в вагранке классическим оправданием низкого уровня углерода и кремния является «сегодня в вагранке происходит окисление» или «должен был произойти двойной заряд».«При плавлении в электропечи« бедный углерод »или« карбид кремния низкой чистоты »являются стандартными объяснениями.
Ни одно из этих оправданий не является точным. Вариации химического состава, тепло в тепло, возникают в результате окислительных потерь. DeOX останавливает окисление углерода и кремния за счет стабилизации химического состава как в EF, так и в вагранке. Нейтрализация всего оксида железа в покровном шлаке стабилизирует химический состав, поскольку оксид железа превращается в инертные побочные продукты. Окислительные процессы остановлены.
Небольшие количества оксида железа (например,g., 1,5% FeO) кажутся несущественными для отрицательного воздействия на расплавленное железо, но это далеко не так: содержание FeO должно быть менее 0,2% FeO.
Типичный допустимый уровень 1,5% FeO в вагранках приводит к потере оксида кремния 20-30%, что неприемлемо. При уровне 0,2% FeO исключаются потери, связанные с окислением кремния, и достигается невообразимое качество железа.
Содержание оксида железа должно быть снижено почти до нуля для прекращения потерь от окисления. Многие литейные заводы проверяют химический состав шлака, но мало кто понимает, что оксид железа необходимо контролировать на уровне ниже 0.2% FeO.
Цвет шлака указывает на уровень загрязнения оксидом железа: типичный черный или очень темный шлак указывает на проблему. Зеленоватый цвет, указывающий на более низкие уровни FeO, начинает появляться на уровне 1,0% и переходит в светло-зеленый при содержании FeO 0,2%.
Цвет шлака представляет собой отличную систему оценок для оценки процессов плавления. При плавлении EF цвет шлака указывает на произошедшие потери от окисления. При вагранке цвет шлака указывает на склонность дутьевого воздуха к образованию оксида железа в дополнение к серьезности происходящих потерь от окисления.Проверка цвета шлака является неотъемлемой частью всех систем контроля качества жидкого чугуна.
Текучесть металла — Раньше текучесть металла обычно регулировалась регулировкой температуры разливки. Добавление «перегрева», означающего, что температура чугуна превышает температуру затвердевания, увеличило текучесть металла. Когда повышение температуры оказалось недостаточным для контроля текучести, в железо добавили небольшие количества феррофосфора.
Плохая текучесть создает много проблем для литейного производства.Повышение температуры разливки вызывает множество проблем с качеством в процессе литья. Такие вещи, как пригорание и повышенная усадка, приводят к большим проблемам.
Химический состав металла важен для определения текучести расплава. Железо образует эвтектику, самую низкую температуру плавления, поскольку химический состав приближается к 4,3% CE (процентное содержание углерода и кремния рассчитано уникальным способом). Химический состав железа выше и ниже 4,3% CE имеет более высокие температуры затвердевания. Иногда незначительные изменения химического состава могут снизить текучесть в достаточной степени, чтобы вызвать дефекты «неправильного хода».
До сих пор контроль или изменение химического состава и добавление фосфора, наряду с повышением температуры заливки, были единственными инструментами, доступными инженерам по литью для решения проблемы неправильного запуска. Теперь DeOX представляет собой совершенно новый и эффективный способ улучшения текучести металла.
Как отмечалось в предыдущем отчете, удаление свободных атомов кислорода из расплавленного железа останавливает процесс окисления. В процессе окисления образуются «оксиды», которые в конечном итоге взвешиваются в металлической матрице.Твердые оксиды, такие как SiO 2 и MNO, и газообразный оксид CO, накапливаются в матрице и в конечном итоге объединяются с другими подобными оксидами, достигая критической массы, которая позволяет частице оксида «всплывать» из расплава.
Свободного кислорода больше нет — Этот процесс коалесценции осажденных оксидов дает более чистый металл. Важное открытие инженеров Mastermelt заключалось в том, что после прекращения подачи свободных атомов кислорода взвешенным оксидам требуется около двух минут, чтобы всплыть из ванны расплавленного железа.Этот факт коррелирует с практикой плавки стали, которая допускает одинаковый двухминутный интервал между раскислением и разливкой.
Одной из важных особенностей гораздо более чистого металла с низким содержанием оксидов является то, что его текучесть значительно улучшается. Когда металл очищается, происходит почти невероятное увеличение текучести: это почти дневная разница. Добавки фосфора исключены, температура разливки может быть снижена, а дефекты неправильной работы исчезнут.
В одной заявке на литье, производящей чугунную трубу диаметром два дюйма, которая отливается длинными тонкостенными секциями, неправильный ход или отсутствие заполнения металлической формы по всей длине были устранены как брак, связанный с браком.Мастер заливки пола не поверил своим глазам. Отливка двухдюймовых труб на всю длину производилась на постоянной основе.
Нет необходимости в испытании «спирали текучести» при отливке чугунной трубы диаметром два дюйма в вращающейся металлической форме. Применение литья служит лучшим тестом из всех, но при плохой текучести оно обходится дорого.
Улучшенная текучесть чугунных труб диаметром два дюйма используется также для производства труб из высокопрочного чугуна.В течение многих лет директор завода по производству труб на Среднем Западе рекламировал улучшенную текучесть вагранки Mastermelt с фурмовым литьем во всех размерах труб из ковкого чугуна.
В другом применении необходимость в добавке фосфора была устранена с помощью впрыска Mastermelt SiC в фурму. Когда эта техника впрыска прекратилась через семь лет и был введен другой инъекционный материал, сразу же появились дефекты неправильной работы и возобновились добавления фосфора. Замещающий материал SiC не нейтрализовал оксид железа в вагранке, следовательно, уровни свободного кислорода были выше, что приводило к более высоким уровням взвешенных оксидов и снижению текучести.
Таким образом, чистота металла становится новым и очень важным свойством расплавленного чугуна.
Изучив, как ваш любимый повар готовит соус, можно имитировать чистоту металла. Соус начинается с прозрачного, очень жидкого и жидкого бульона, в который добавлен загуститель. Конечный результат — загустевшая медленно движущаяся жидкость. Наноразмерные оксиды, взвешенные в матрице расплавленного железа, являются загустителем в расплавленном железе. Чистота металла связана с его текучестью. «Грязный» чугун трудно успешно отливать, но когда подача свободных атомов кислорода прекращается, чистота может улучшиться в 10 раз и более; соответственно стремительно растет текучесть.
Чистоту металла можно измерить и сравнить, определив содержание кислорода в затвердевшем образце металла. Все оксиды содержат атом кислорода с общим содержанием кислорода, представляющим общий уровень оксида. Результаты по общему содержанию кислорода могут быть скомпилированы для создания системы оценки текучести для конкретных применений литья в литейном производстве.
Необходимо определить уровень оксидного загрязнения расплавленного металла, который приводит к дефектам, связанным с текучестью. Содержание кислорода напрямую связано с текучестью чугуна, и ему могут быть назначены пределы, аналогичные химическому составу и температуре металла, в общей программе контроля качества литейного производства.
Теперь температура, химический состав металла и чистота могут быть использованы для определения текучести расплавленного чугуна, что существенно снижает потенциальный риск отливки лома. Программа качества каждого чугунолитейного завода должна учитывать эту технологию в своих общих методах контроля качества.
Рон Бейерстедт — президент Mastermelt LLC . Свяжитесь с ним по телефону [email protected]
Это третий в серии отчетов, посвященных влиянию кислорода на плавление железа.
- Вредные эффекты окисления расплавленного металла , FM&T июнь 2020 г.
- Контроль оксида железа для остановки потерь углерода и кремния , FM&T Плавление и заливка: срок службы отливки
Электродуговые печи
(ДСП) начали использовать в конце 1800-х годов. Электроды пропускают электрический ток через металл внутри печи, что более эффективно, чем добавление внешнего тепла при плавлении больших объемов за один раз.Большая ДСП, используемая при производстве стали, может выдерживать до 400 тонн. «Заряд» этой стали часто состоит из тяжелого чугуна, такого как слябы и балки, измельченного лома от автомобилей и других отходов, а также слитков чугуна с плавильного завода.
После заполнения резервуара электроды помещаются в металл, и между ними проходит электрическая дуга. Когда металл начинает плавиться, электроды можно протолкнуть глубже в смесь или раздвинуть, чтобы создать большую дугу. Для ускорения процесса можно добавить тепло и кислород.Когда начинает формироваться расплавленный металл, напряжение может быть увеличено, поскольку шлак, образующийся на поверхности металла, действует как защитное одеяло для крыши и других компонентов ДСП.
Когда все расплавлено, вся печь наклоняется, чтобы выгрузить жидкий металл в расположенный ниже ковш. Иногда сами ковши могут быть меньшими по размеру электродуговыми печами, в которых перед разливкой металл остается горячим.
Индукционные печи
работают с магнитными полями, а не с электрическими дугами.Металл загружается в тигель, окруженный мощным электромагнитом из спиральной меди. Когда индукционная печь включена, катушка создает быстро меняющееся магнитное поле за счет подачи переменного тока. Когда металл плавится, электромагнит создает в жидкости завихрения, которые перемешивают материал самостоятельно. Тепло в индукционной печи создается за счет возбуждения молекул в самом железе, а это означает, что все, что попадает в тигель, именно то, что выходит наружу: кислород или другие газы не добавляются в систему.Это означает меньшее количество переменных, которые необходимо контролировать во время плавки, но это также означает, что индукционная печь не может использоваться для рафинирования стали. Что входит, то выходит. Как и в ДСП, индукционные печи часто выгружают, наклоняя их в нижние ковши.
Индукционные печи очень распространены и просты в эксплуатации при высоком качестве входных материалов. Обычные модели могут производить 65 тонн стали на каждой загрузке.
Как и традиционные кузницы по металлу, эта индукционная печь является открытой и может загружать металл в горячем состоянии.Все печи литейного цеха сталкиваются со смертельным врагом: паром. Вода, даже в небольших количествах, может вызвать разбрызгивание или взрыв, поэтому весь лом и ферросплавы, а также все инструменты, используемые в производстве, должны быть высушены перед использованием. У металлолома не должно быть закрытых участков, в которых могла бы оставаться вода или пар. Даже инструменты, используемые литейщиками, не должны содержать конденсата или влаги. На многих литейных заводах есть сушильные печи, чтобы убедиться, что металлолом и инструменты высохли до кости, прежде чем что-либо коснется литейной печи.
Разливочные ковши
После того, как металл расплавлен, его необходимо поместить в изложницу. В небольших литейных цехах все это может происходить за одну стадию: наклонный или выдвижной тигель может переносить металл из печи в песок. Однако это непрактично, когда печь вмещает много тонн металла. Обычно при производстве черных металлов ковши перекачивают меньшие порции расплава из основной печи.
Ковш наклоняется для разливки расплавленной стали. Расстояние избавляет рабочих от опасности.В этих системах ковш может подавать металл прямо в изложницу.Однако перегрузочный ковш может подавать жидкость в накопительный бак или вторичную печь. Ковши для обработки — еще один доступный тип, используемый для разделения расплава на порции, как пекарь может разделить основное тесто, чтобы использовать его в качестве основы для других рецептов. Например, жидкий чугун может содержать агенты, добавленные в ковш для обработки, чтобы сделать углерод внутри него сферической формы, а не чешуйчатым, создавая более ковкий металл, называемый высокопрочным чугуном.
Ковши могут быть очень маленькими и подниматься литейщиками, или они могут вмещать много тонн металла и нуждаться в механической поддержке.Самые большие ковши перемещаются через литейный цех с помощью ковшовой тележки, мостового крана или путевой системы.
Ковши всех типов предназначены для защиты рабочего от брызг, пламени или искр во время заливки. Некоторые ковши переливаются через верхнюю кромку или сливной носик, и их необходимо наклонять: у них часто есть шестерни, которые позволяют литейщику тщательно контролировать скорость разливки. У других ковшей разливочный носик находится на дне ковша, и разливка контролируется путем снятия и замены заглушки.
Смешивание сплавов
Металлические сплавы состоят из смесей элементов, стандартизированных формулой, в которой указывается процентное содержание каждого типа, а также шаги, предпринятые при его производстве. В плавильных печах и ковшах литейного производства создаются эти типы сплавов для отливок.
Литейные заводы часто специализируются либо на сплавах черных металлов, которые содержат железо, либо на определенных цветных сплавах, таких как драгоценные металлы, сплавы на основе меди или алюминия.
Сортировка ферросплавов на чугун и сталь. Сплавы чугуна включают серый чугун, в состав которого входит кремний, и ковкий чугун, который имеет тип сферического углерода. Марки литой стали определяются процентным содержанием углерода и других добавок в смеси. Нержавеющая сталь — это сталь, в состав которой входит хром для предотвращения ржавчины за счет пассивации.
Цветные сплавы включают в себя все другие металлы, поэтому неудивительно, что существует дальнейшая специализация в производстве цветных металлов. Некоторые предприятия специализируются на цинке, некоторые — на алюминии; другие работают в основном со сплавами на основе меди, такими как латунь и бронза.Однако есть кроссовер. Например, если конкретное литейное производство работает как с бронзой, так и с алюминием, они, вероятно, будут специализироваться на определенных сортах каждого из них.
С какими бы сплавами ни работал литейный завод, предпосылка изготовления расплавленного металла и литья в пустоты для его придания одинаковой форме. Идея становится актуальной в тот момент, когда металл льется в форму.
Почему плавка железа — такой странный процесс
Поделиться
АртикулВы можете поделиться этой статьей с указанием авторства 4.0 Международная лицензия.
Когда железо нагревается, расположение его атомов несколько раз меняется, прежде чем оно расплавится. Это странное поведение — одна из причин того, почему сталь, в которой железо играет большую роль, является такой прочной. Это также объясняет, почему мы используем сталь для всего, от чайников до небоскребов.
Новое исследование предлагает доказательства того, как магнетизм железа играет роль в этом любопытном свойстве — понимание, которое может помочь исследователям разработать лучшую и прочную сталь.
«Люди работали с обычным старым железом в течение тысяч лет, но это часть его термодинамики, которую никто никогда не понимал», — говорит Брент Фульц, профессор материаловедения и прикладной физики Калифорнийского технологического института.
Чугунное литье. (Кредит: iStockphoto)Законы термодинамики регулируют естественное поведение материалов, например температуру, при которой вода кипит, и время химических реакций. Эти же принципы определяют расположение атомов в твердых телах, а в случае железа природа несколько раз меняет свое мнение при высоких температурах.
При комнатной температуре атомы железа находятся в необычной рыхлой открытой структуре; когда железо нагревается выше 912 градусов по Цельсию, атомы становятся более плотно упакованными, после чего снова разрыхляются при 1394 градусах Цельсия и в конечном итоге плавятся при 1538 градусах Цельсия.
Железо является магнитным при комнатной температуре, и предыдущие исследования показали, что магнетизм железа способствует его открытой структуре при низких температурах, но при 770 градусах Цельсия железо теряет свой магнетизм.
Однако железо сохраняет свою открытую структуру более чем на 100 градусов за пределами этого магнитного перехода.Это привело исследователей к мысли, что необычным термодинамическим свойствам железа должно быть что-то еще.
Для этого недостающего звена аспирантке Лизе Могер и ее коллегам нужно было поднять напряжение. Твердые тела накапливают тепло в виде небольших атомных колебаний — колебаний, которые создают беспорядок или энтропию. При высоких температурах энтропия доминирует в термодинамике, а колебания атомов являются крупнейшим источником энтропии в железе. Изучая, как эти колебания меняются при повышении температуры и потере магнетизма, исследователи надеялись узнать больше о том, что движет этими структурными перестройками.
Магноны и фононы
Для этого группа взяла образцы железа на луч группы высокого давления в усовершенствованном источнике фотонов в Аргоннской национальной лаборатории в Аргонне, штат Иллинойс. Эта синхротронная установка производит интенсивные вспышки рентгеновского излучения, которые можно настроить на обнаружение квантовых частиц атомных колебаний — так называемых фононных возбуждений — в железе.
Объединив эти колебательные измерения с ранее известными данными о магнитном поведении железа при этих температурах, исследователи обнаружили, что колебательная энтропия железа намного больше, чем предполагалось изначально.
Фактически, избыток был подобен вкладу энтропии от магнетизма — предполагая, что магнетизм и атомные колебания взаимодействуют синергетически при умеренных температурах. Эта избыточная энтропия увеличивает стабильность открытой структуры железа, даже когда образец нагревается после магнитного перехода.
Этот метод позволил исследователям впервые экспериментально заключить, что магноны — квантовые частицы электронного спина (магнетизма) — и фононы взаимодействуют, повышая стабильность железа при высоких температурах.
«Рецепт» получше
Поскольку измерения группы Caltech совпали с теоретическими расчетами, которые одновременно проводились в лаборатории Йорга Нойгебауэра в Max-Planck-Institut für Eisenforschung GmbH (MPIE), результаты Маугера также способствовали валидации новой вычислительной модели.
[связанные]
«Долгое время предполагалось, что структурная стабильность железа тесно связана с внутренней связью между магнетизмом и движением атомов», — говорит Фриц Кёрманн, научный сотрудник MPIE и первый автор вычислительной статьи.
«Фактическое обнаружение этой связи и то, что данные наших коллег-экспериментаторов и наши собственные результаты расчетов находятся в таком превосходном соответствии, было действительно захватывающим моментом», — говорит Нойгебауэр. «Недавно полученное понимание того, как термодинамическая стабильность реализуется в чугуне, поможет сделать разработку новых сталей более систематизированной».
На протяжении тысячелетий металлурги работали над производством более прочных сталей почти так же, как вы пытаетесь разработать рецепт лучшего печенья в мире: угадывай и проверяй.Сталь начинается с основы из стандартных ингредиентов — железа и углерода — так же, как обычное тесто для печенья начинается с муки и масла. И так же, как вы настраиваете рецепт печенья, варьируя количество других ингредиентов, таких как специи и орехи, свойства стали можно настраивать, добавляя различные количества других элементов, таких как хром и никель.
Благодаря улучшенной вычислительной модели термодинамики железа при различных температурах, учитывающей эффекты как магнетизма, так и атомных колебаний, металлурги теперь смогут более точно предсказать термодинамические свойства сплавов железа по мере изменения своих рецептов.
Экспериментальная работа появляется в журнале Physical Review B . Вычислительная статья, написанная в соавторстве с Фульцем и Могером под руководством исследователей из Института Макса Планка, опубликована в журнале Physical Review Letters . Министерство энергетики США поддержало работу Фульца и Могера.
Источник: Caltech
(PDF) Плавка серого чугуна на основе стального лома с использованием карбида кремния
АРХИВ ЛИТЕЙНОГО ПРОИЗВОДСТВА Том 14, Выпуск 3/2014, 77-82
Рис.11. Чугун W7pig (FeSi75) матрица
После анализа фотографий было установлено, что как для чугуна
, так и для чугуна, выплавленного на основе передельного чугуна, и для чугуна
на основе стального лома, дефицит кремния был компенсирован за счет
При добавлении карбида кремниямогут возникать некоторые различия между формой выделения графита
, его количеством и размером. Самой крупной группой
были поля с однородными осадками чешуйчатого графита.
Появляются участки упорядоченно ориентированных междендритных чешуек графита
, а также формируются поля «закрученных» выделений. В полученном
синтетическом чугуне наблюдаются микроструктуры, полученные с использованием карбида кремния
, более объемные чешуйки графита по сравнению с чугуном
, выплавленным на основе чугуна.
На основании матричного анализа внутри произведенного синтетического чугуна
(рис. 7-11) можно констатировать, что в большинстве образцов
появляется перлитная матрица или перлитная только с небольшим количеством
феррит внутри него.
5. Выводы
Проведенные эксперименты показали, что синтетический чугун
можно производить исключительно на основе стального лома с заменой карбюризатора
карбидом кремния. Это позволяет в
одновременно компенсировать небольшой дефицит кремния. Чугун
имеет большее количество осадков графита.
Кроме того, эти осадки немного толще.
Наилучшим методом добавления карбида кремния из углерода
и с точки зрения коэффициента ассимиляции кремния является его добавление в твердый заряд
.Когда SiC добавляется на поверхность жидкого металла, эффективность
может уменьшиться вдвое, а время плавления должно быть увеличено на
на несколько десятков минут.
Эффективность использования углерода при добавлении SiC
в твердую шихту составляла EC = 14,9-28,6%, тогда как коэффициент ассимиляции кремния
составлял ESi = 49,5-66,7%, помимо аналогичного химического состава карбида кремния
. Суммарный КПД использования
элементов изменялся в очень узком диапазоне 78.1-81,6%.
На кривых затвердевания и кристаллизации, зарегистрированных до настоящего времени
, значительных различий между температурами ликвидуса для отдельных расплавов
не наблюдалось. Литература предполагает, что в некоторых местах
карбид кремния должен повышать эту температуру
пункта [9].
Список литературы
[1] Янерка, К. (2010). Науглероживание жидких ферросплавов.
Гливице: Изд. Силезский технологический университет.(по польски).
[2] Янерка, К., Барточа, Д., Езерски Дж. И Шайнар, Дж. (2010).
Влияние качества науглероживания на процесс повторного науглероживания чугуна
. Foundry Trade Journal
International. 184 (3679), 282-286.
[3] Янерка, К., Барточа, Д. и Шайнар, Дж. (2009). Качество карбюризатора
и его влияние на процесс науглероживания.
Архив литейного дела. 9 (3), 249-254.
[4] Янерка, К., Барточа, Д., Шайнар, Дж. И Чолева, М. (2007).
Влияние науглероживания различных типов и
науглероживания на эффективность и структуру железа.
Архив металлургии и материалов. 52 (3), 467-474.
[5] Janerka, K., Jezierski, J. & Szajnar, J. (2011). Оценка
эффективности процесса повторного науглероживания жидкого чугуна по
с использованием различных науглероживающих средств и методов повторного науглероживания.
Труды 20-й юбилейной международной конференции
по металлургии и материалам METAL 2011, Брно, Чехия
Республика.
[6] Янерка, К., Барточа, Д., Шайнар, Дж. И Езерски, Дж. (2010).
Влияние карбюризатора на процесс кристаллизации и
на микроструктуру синтетического чугуна. Архив
Металлургия и материалы. 55 (3), 851-859.
[7] Янерка, К., Павлита, М., Езерски, Дж., Шайнар, Дж. И
Барточа, Д. (2014).
свойства карбюризатора передают структуру плавленого чугуна. Журнал материалов
Технология обработки.214, 794-801.
[8] Янерка, К., Езерски, Дж., Барточа, Д. и Шайнар, Дж. (2013).
Наследственность структуры и свойств серого чугуна
, выплавляемого на основе стального лома. Расширенные материалы
Исследования. 622-623, 685-689.
[9] Эдалати, К., Ахлаги, Ф. и Нили-Ахмадабади, М. (2005).
Влияние добавок SiC и FeSi на характеристики
расплавов серого чугуна, разлитых при различных температурах.Журнал
технологии обработки материалов. 160, 183–187.
[10] Онсойен, М.И., Скаланд, Т. (2001). Предварительное кондиционирование расплавов серого железа
с использованием ферросилиция или карбида кремния. Американское
Литейное общество.
[11] Шмидт-Саловски, К., Шафран, М., Сентек Дж., Бобрик Э.
(2013). Химическая технология. Варшава: PWN. (по польски).
[12] Белянски А. (2010). Основы неорганической химии, т.2.
Варшава: PWN.(по польски).
[13] Кельски А. (1969). Основы технологии керамики. Эд. нет. 152.
Краков: AGH. (по польски).
Без аутентификации
Дата загрузки | 21.11.15, 6:39
металлургия — Какой материал используется для удержания расплавленного железа в печи?
Тигли футерованы огнеупорными материалами. При обработке стали используется графит или комбинация хромита и магнезита для прямого контакта с расплавом. При переработке чугуна часто используются синтетические глины, также известные как смеси оксида алюминия, магнезии и кремнезема.Графит сложнее сформировать, чем огнеупоры глиняного типа. Чтобы быть пригодным в качестве огнеупора, материал должен соответствовать ряду требований к свойствам, чтобы быть экономичным и безопасным.
Как вы отметили, железо в виде чистого железа имеет верхнюю точку плавления около 1540 ° C в крайней левой части фазовой диаграммы $ \ textrm {Fe-C} $ ниже. Есть две категории материалов с более высокими температурами плавления, но лишь некоторые из них экономичны и безопасны. Как правило, любой материал с точкой плавления, достаточно высокой, чтобы выдерживать температуры плавления коммерчески используемых металлов, таких как железо, медь и алюминий, называют огнеупорными материалами .
Источник: ispatguru.com
тугоплавкие металлы (непригодны для литейного производства)
Первая категория материалов с высокой температурой плавления, из которых вы отметили один материал, называются тугоплавкими металлами. Обратите внимание, что в литейной промышленности их обычно не называют огнеупорами или огнеупорными материалами. Они состоят из ниобия, молибдена, вольфрама, тантала и рения (Nb, Mo, W, Ta, Re) и имеют температуры плавления от примерно 2500 ° C до 3500 ° C.Хотя точки плавления достаточно высоки, и они обладают достаточной прочностью в качестве конструкционных материалов, а также некоторой ударной вязкостью, существует ряд факторов, ограничивающих их использование.
- Высокая реакционная способность с кислородом
- Высокая химическая активность по отношению к другим металлам
- Высокая стоимость веса
- Высокая плотность
- Высокая теплоемкость
- Высокая теплопроводность
- Сложная форма (требуется либо тщательно контролируемая плавка в вакууме, либо порошковая металлургия)
Огнеупорная керамика (для литейного производства)
Вторая категория огнеупорных материалов основаны на различных керамики, и называются огнеупорных керамических , или чаще всего огнеупоров.Однако подходит не всякая керамика. В идеале керамика должна иметь чрезвычайно высокую прочность атомных связей или более высокое сродство к кислороду, чем плавящийся металл. Это сделало бы материал относительно инертным по отношению к расплавленному металлу. Такая керамика также должна быть легко формованной, иметь низкую теплоемкость и теплопроводность и должна быть относительно недорогой.
Графит — разумный выбор для прямого контакта со сталью и алюминием, так как прочность углерод-углеродной связи очень высока и он имеет достаточно высокую температуру плавления, превышающую температуру его разложения в атмосфере.Формование графита несколько дороже, чем его альтернативы, хотя тигли обычно служат дольше. Графитовые тигли обладают высокой прочностью, но, как и вся керамика, низкой ударной вязкостью. Он имеет низкую плотность и меньшую теплоемкость и теплопроводность, чем тугоплавкие металлы. Магнезит $ \ left (\ textrm {MgCO} _3 \ right) $ и хромит $ \ left (\ textrm {FeCr} _2 \ textrm {O} _4 \ right) $ также являются распространенными стальными огнеупорами.
Другой вариант — это системы, расположенные ниже линии $ \ textrm {Fe} + \ textrm {O} _2 \ rightleftharpoons \ textrm {FeO} _2 $ на диаграмме Эллингема ниже.
Chromia $ \ left (\ textrm {Cr} _2 \ textrm {O} _3 \ right) $ может использоваться для некоторых материалов, но имеет высокую плотность и высокую теплоемкость, а также несколько более высокую стоимость.
Кремнезем $ \ left (\ textrm {SiO} _2 \ right) $ подходит для металлов и сплавов с более низкими температурами плавления, но имеет низкую термостойкость. Чистый диоксид кремния (плавленый диоксид кремния) имеет гораздо более высокую стойкость к тепловому удару, но он очень дорог и труден в формировании. Используется в зеркалах телескопов.
Глинозем $ \ left (\ textrm {Al} _2 \ textrm {O} 3 \ right) $ и магнезия $ \ left (\ textrm {MgO} \ right) $ обычно используются в чугунных приложениях, где графит предпочтительнее для низколегированной стали. Технические глины, которые фактически представляют собой специфические смеси оксида алюминия, магнезии и кремнезема, также часто используются для крупномасштабных применений в производстве чугуна, поскольку они очень недороги и их очень легко формовать на месте при применении в 100 тонн и более. Кроме того, чугун имеет более низкую температуру плавления, чем сталь (см. Вертикальную линию около 4.3% углерода на фазовой диаграмме $ \ textrm {Fe-C} $ и далее до жидкой области) и, таким образом, несколько менее строгие требования к прочности и реакционной способности огнеупоров.
Как правило, известь $ \ left (\ textrm {CaO} \ right) $ не используется для изготовления конструкционных материалов, так как она слишком хрупкая и имеет тенденцию быстро превращаться в порошок. Однако иногда его используют в качестве добавки к связующему, но промышленность отходит от этого, поскольку кальций разрушает другие огнеупоры, снижая их долговечность. См. Диаграмму Эллингема ниже: известь находится в самом низу диаграммы.
Титания $ \ left (\ textrm {TiO} 2 \ right) $ и оксид марганца $ \ left (\ textrm {MnO}) \ right) $ обычно не используются, хотя я не знаю почему; вероятно какое-то сочетание теплоемкости и механических свойств.
Для наших целей способ чтения диаграммы Эллингема состоит в том, что движение вверх по графику означает уменьшение сродства к кислороду, а движение вниз означает увеличение сродства. Диагональные линии с химическими уравнениями указывают стандартную свободную энергию этой реакции (вертикальная ось) при данной температуре (горизонтальная ось).Если при данной температуре одна реакционная линия находится выше другой, более высокая реакция будет протекать к чистому металлу плюс кислород (химическое восстановление), тогда как более низкая реакция будет протекать к оксиду металла (химическое окисление). Следовательно, тугоплавкие материалы с более высоким сродством к кислороду, чем расплавленный металл, будут химически стабильными во время плавления. Обратите внимание, что существуют или могут быть построены дополнительные диаграммы для неоксидных материалов с использованием термодинамических принципов и некоторых экспериментов, и их труднее найти в Интернете.
Источник: Cambridge Ellingham Diagram Tutorial
.