Магнитопорошковый контроль, оборудование, Виматек
Сущность метода магнитопорошкового контроля (МПК)
Магнитопорошковый контроль — один из самых распространённых, надёжных и производительных методов неразрушающего контроля поверхностей изделий из ферромагнитных материалов в их производстве и эксплуатации.
Магнитопорошковый метод контроля — один из четырех классических методов неразрушающего контроля, а также один из наиболее старых методов неразрушающего контроля, связанных с применением приборов и дефектоскопических материалов для неразрушающего контроля. Первые опыты описали феномен полей магнитного рассеяния и объяснили их значение. Впоследствии были предприняты попытки найти применение этому явлению и ввести его в техническую практику. В 1868 году англичанин Саксби применил компас для определения дефектов в пушечных стволах. В 1917 году американец Хок применил железные опилки для обнаружения трещин в стальных деталях.
Суть магнитопорошкового метода такова: магнитный поток в бездефектной части изделия не меняет своего направления; если же на пути его встречаются участки с пониженной магнитной проницаемостью, например дефекты в виде разрыва сплошности металла (трещины, неметаллические включения и т.
Магнитопорошковый контроль предназначен для выявления тонких поверхностных и подповерхностных нарушений сплошности металла – дефектов, распространяющихся вглубь изделий. Такими дефектами могут быть трещины, волосовины надрывы, флокены, непровары, поры. Наибольшая вероятность выявления дефектов достигается в случае, когда плоскость дефекта составляет угол 90° с направлением намагничивающего поля (магнитного потока).
Чувствительность метода магнитопорошковой дефектоскопии определяется магнитными характеристиками материала контролируемого изделия (магнитной индукцией (В), остаточной намагниченностью (Br ), максимальной магнитной проницаемостью (µmax ), коэрцитивной силой (Н0), шероховатостью поверхности контроля, напряженностью намагничивающего поля, его ориентацией по отношению к плоскости дефекта, качеством дефектоскопических средств и освещенностью контролируемой поверхности.
Магнитопорошковый метод контроля находит применение практически во всех отраслях промышленности:
- металлургия
- машиностроение
- авиапромышленность
- автомобильная промышленность
- судостроение
- строительство (стальные конструкции, трубопроводы)
- энергетическое и химическое машиностроение
- транспорт (авиация, железнодорожный, автотранспорт)
Магнитопорошковый контроль является самостоятельным технологическим процессом и включает в себя:
- подготовку поверхностей изделий к контролю
- намагничивание деталей
- обработку поверхности детали суспензией (порошком)
- осмотр деталей
- размагничивание
- контроль качества процесса
скачайте опросник по Вашей задаче магнитопорошкового контроля
Капиллярный и магнитопорошковый контроль
Магнитопорошковый метод неразрушающего контроля основан на явлении притяжения частиц магнитного порошка магнитными потоками рассеяния, возникающими над дефектами в намагниченных объектах контроля. Наличие и протяженность индикаторных рисунков, вызнанных полями рассеяния дефектов, можно регистрировать визуально или автоматическими устройствами обработки изображения. Метод предназначен для выявления поверхностных и подповерхностных нарушений сплошности: волосовин, трещин различного происхождения, непроваров сварных соединений, флокенов, закатов, надрывов и т.п. Компания Magnaflux представляет широкий спектр материалов для проведения магнитопорошкового контроля – сухие порошки, магнитные концетраты для приготовления водных суспензий и суспензий на основе масляных носителей, готовые к применению суспензии (популярные – 7hf и контрастный краситель WCP-2, 14NF ).
Капиллярный контроль предназначен для выявления невидимых или слабо видимых невооруженным глазом поверхностных и сквозных дефектов в объектах контроля, определения их расположения, протяженности и ориентации по поверхности. Капиллярный метод контроля применяется при контроле объектов любых размеров и форм, изготовленных из черных и цветных металлов, легированных сталей, чугуна, металлических покрытий, пластмасс, стекла и керамики.
Показать: 20255075100
Сортировка: По умолчаниюНазвание (А — Я)Название (Я — А)Цена (низкая > высокая)Цена (высокая > низкая)Рейтинг (начиная с высокого)Рейтинг (начиная с низкого)Модель (А- Я)Модель (Я — А)
MAGNAFLUX WCP-2 — готовый к использованию, быстро сохнущий, белый контрастный краситель, изготовл..
700.00p.
Используется для контроля наличия поверхностных дефектов всевозможных не пористых материалов,..
1800.00p.
MAGNAGLO 14HF — это готовая к употреблению люминесцентная магнитная суспензия на масляной основе,.
700.00p.
MAGNAGLO 410 HF – это готовая к употреблению люминесцентная магнитная суспензия на масляной основ..
700.00p.
Пенетранты, очистители, проявители, DP-55 SHERWIN, D-100 SHERWIN, DR-60 SHERWIN DP-55 SHERWIN..
2450.00p. 2100.00p.
600.00p.
MAGNAFLUX 7HF – это готовая к употреблению суспензия черного цвета на масляной основе. MAGNAFLUX ..
700.00p.
Indumos.su. Неразрушающий контроль :: Каталог :: Расходные материалы для капиллярной и магнитопорошковой дефектоскопии Waygate Technologies :: Магнитопорошковый метод ARDROX
Магнитопорошковый метод неразрушающего контроля используют при поиске поверхностных и подповерхностных микродефектов в сварных швах, деталях и конструкциях из ферромагнитных материалов. С этой целью изделие намагничивают и покрывают магнитным порошком, который оседает на неоднородностях магнитного поля в зоне дефектов, формируя видимые «следы» дефектов. Этот метод позволяет обнаруживать тонкие, невидимые глазом поверхностные дефекты, материала типа трещин (закалочных, сварочных, шлифовочных, усталостных, штамповочных, литейных и др.), волосовин, флокенов, закатов, заковов, надрывов, рихтовочных трещин, некоторых видов расслоений.
Магнитопорошковый метод широко применяется во многих отраслях промышленности:авиации, машиностроении, судостроении, автомобилестроении и др.
Продукт | Описание | Стандарт |
---|---|---|
При дневном свете | ||
ARDROX 800/3 | Черная магнитная суспензия. Обладает высокой чувствительностью. Размер зерен 0,2мкм. Используется при контроле шероховатой поверхности. Готовая форма для применения (керосиновая основа) | BS 4069, Rolls-Royse RPS 700, MSRR 9976, TSD 594 |
FRAMAGNETO № 3 | Жидкий концентрат черной магнитной суспензии. Обладает высокой чувствительностью. Размер зерен 0,2мкм. После разбавления водой 5%. | AFNOR NF.A09.125 RCCM MC 5000 BS 4069 |
ARDROX 8901W | Белая грунтовочная краска. Суспензия белого пигмента в слаболетучем растворителе, не содержит хлорированные углеводороды. Наносится слоем 25мкм. | BS 5044 ASME Code, S.V. |
Флуоресцирующие | ||
ARDROX 8530 | Люминесцентная магнитная суспензия.![]() | Rolls-Royse, BS 4069, AMS 3045B |
ARDROX 8544 | Жидкий концентрат люминесцентной магнитной суспензии. Размер зерен 5мкм. Отличная смачиваемость. После разбавления водой 2,5-5,0%. | |
ARDROX 8510 | Люминесцентный сухой магнитный порошок. Разводится 1г на 1л очищенного керосина. | Rolls-Royse, BS 4069, AMS 3045B |
FRAMAGNETO № 8 | Жидкий концентрат люминесцентной магнитной суспензии. Универсальный. Размер зерен 5мкм. После разбавления водой 3%. | AFNOR NF.A09.125 RCCM MC 5000 BS 4069 |
ARDROX 8600 | Жидкий концентрат люминесцентной магнитной суспензии. Размер зерен 5мкм. После разбавления в масляном носителе 0,1-0,5%. |
Магнитопорошковая дефектоскопия МПД | НТЦ «РЭП»
Высокая производительность, наглядность результатов, невысокая цена – все это выделяет магнитопорошковую дефектоскопию (МПД). Она основана на нанесении магнитной суспензии или ферромагнитного порошка и его притяжении под действием сил магнитного поля. Метод позволяет выявить поверхностные и подповерхностные дефекты, будь то трещины, расслоения, надрывы, волосовины, поры, непровары.
Лаборатория неразрушающего контроля ООО «НТЦ «РЭП» обладает всем необходимым для выполнения МПД: аттестованная команда специалистов с допуском 2 уровня, качественные материалы Sherwin и Magnaflux
! Сфера применения: метод подходит для авиационной, нефтегазовой, машиностроительной, металлургической промышленностей. А также для железнодорожной и судостроительной отраслей. С его помощью можно контролировать состояние магистральных трубопроводов, сварных швов и любых других изделий из ферромагнитных материалов.
Способы магнитопорошкового контроля
Для необработанных поверхностей применяем сухой метод нанесения индикатора (порошка). Для изделий, отличающихся высоким классом шероховатости, используем мокрый метод – магнитную суспензию.
В зависимости от технических характеристик детали применяем один из способов намагничивания – СОН или СПП.
Для каких деталей применяется | ||
Остаточной | Отличается более высокой производительностью и удобством в сравнении с СПП. | Магнитотвердые с коэрцитивной силой от 10 А/См |
Приложенного | Подходит для проведения контроля поверхностных дефектов с глубиной от 0,01 мм, а также дефектов, находящихся под немагнитным покрытием |
|
Особенность метода и зависимость от свойств металла
В бездефектной части изделия магнитный поток не меняет направления. После намагничивания и нанесения индикатора (магнитный порошок или суспензия, представляющая взвесь магнитных частиц в жидкости) дефекты вызывают отклонение магнитных потоков, что приводит к ориентации частиц порошка или суспензии определенным образом.
В итоге образуются характерные рисунки по форме дефектов, что позволяет наглядно оценить качество изделия. Ширина рисунка зачастую много больше ширины самого дефекта, в связи с этим возможно различать без использования оптических приборов даже очень небольшие дефекты. Достоверность результатов напрямую зависит от состояния поверхностного слоя металла. А также других свойств – формы, габаритов, состояния поверхности.
Плюсы и минусы метода МПД
Из преимуществ МПД можно выделить:
- оперативность;
- высокая чувствительность;
- большая точность при глубине подповерхностных дефектов не более 1.5-2 мм, поверхностных с шириной раскрытия от 0.002 мм, глубиной от 0.01 мм;
- возможность определения усталостных трещин, которые появляются в течение эксплуатации;
- возможность выявления как несплошностей заполненных другими веществами (пылью, водой, нефтепродуктами), так и полых дефектов.
Недостатки метода – сложность определения глубины распространения трещин, низкая эффективность при поиске дефектов округлой формы, будь то поры или раковины.
! Факт: при магнитопорошковой дефектоскопии наибольшая вероятность выявить дефекты, имеющие угол 900 относительно направления магнитного потока.
Законодательная база
Основные документы, регулирующие проведение МПД
Контроль неразрушающий. Магнитопорошковый метод. Типовые технологические процессы | |
ГОСТ Р ИСО 9934-1-2011 | Контроль неразрушающий. Магнитопорошковый метод. Часть 1 |
ГОСТ Р ИСО 9934-2-2011 | Контроль неразрушающий. Магнитопорошковый метод. |
ГОСТ Р 53700-2009 (ИСО 9934-3:2002) | Контроль неразрушающий. Магнитопорошковый метод. Часть 3 |
Контроль неразрушающий магнитный. Термины и определения |
Почему стоит заказать магнитопорошковый контроль в ООО «НТЦ «РЭП»
- аттестованная лаборатория и персонал. Наши специалисты аттестованы в соответствии с ПБ 03-440-02 и ISO 9712 по магнитному и другим методам контроля. Это позволяет нам работать со всеми объектами, указанными в утвержденном Ростехнадзором перечне объектов контроля. Также работаем с объектами российского морского регистра судоходства.
- полноценная материально-техническая база. Применяем оборудование и расходные материалы от мировых брендов.
- универсальность. Используем намагничивающее устройство с постоянными магнитами, что позволяет работать в местах, где нет источника тока. В нашу команду входят промышленные альпинисты, благодаря чему мы работаем на высоте.
Хотите заказать услуги ООО «НТЦ «РЭП», но еще остались вопросы?
Проконтролируйте состояние трубопроводов или металлоконструкций на производстве с минимумом вложений – позвоните по телефону +7(812)309-95-67 или обратитесь через форму обратной связи. Мы проконсультируем Вас!
Магнитопорошковый метод неразрушающего контроля — I уровень
Программа предназначена для проведения специальной подготовки слушателей в области неразрушающего контроля, претендующих на аттестацию / сертификацию в качестве специалистов I-го уровня квалификации в Единой системе оценки соответствия.
Программа разработана с учетом требований СДАНК-02-2020 «Правила аттестации персонала в области неразрушающего контроля» и ГОСТ Р ИСО 9712-2019 «Контроль неразрушающий. Квалификация и сертификация персонала».
Основные направления подготовки и содержание тем (модулей) подготовки определяются в соответствии с квалификационными требованиями, установленными профессиональным стандартом «Специалист по неразрушающему контролю», утвержденным приказом Министерства труда и социальной защиты Российской Федерации от 3 декабря 2015 г. № 976н.
Неразрушающий контроль – контроль надежности основных рабочих свойств и параметров объекта или отдельных его элементов/узлов. Метод может использоваться для поиска дефектов оборудования без его разрушения и демонтажа, сложного технологического оборудования, зданий и сооружений, а современные способы делают неразрушающий контроль быстрым и точным.
Магнитный контроль (МК) – метод неразрушающего контроля для проверки изделий из ферромагнитных материалов (сталь, чугун и пр.) на наличие поверхностных дефектов (трещин, волосовин, закатов, надрывов и др.). Кроме того данный метод контроля используется для измерения толщины защитных покрытий на стали, оценки структуры и напряженно-деформированного состояния ферромагнитных материалов. Магнитный метод используется для контроля полуфабрикатов, деталей, элементов конструкций, а также сварных соединений. Среди преимуществ данного метода можно выделить возможность выявления дефектов неразличимых невооруженным взглядом, возможность контроля деталей сложной формы, простота, быстрота и эффективность операций.
Магнитный контроль – контроль, основанный на регистрации магнитных полей рассеяния, возникающих над дефектами, или на определении магнитных свойств объекта контроля. В основу данного способа исследования ложится взаимодействие контрольного металлического порошка с возникающими в результате намагничивания обследуемого объекта полями. При отсутствии дефектов на поверхности образуется равномерный слой, но любые искажения магнитного поля приведут к формированию характерных скоплений порошка, которые можно обнаружить во время проведения визуального осмотра с использованием вспомогательных средств.
Оборудование по Магнитному методу неразрушающего контроля
Магнитопорошковый контроль сварных соединений | Айронкон-Лаб
Обзорная статья, которая поможет непрофессионалу понять смысл метода магнитопорошковой дефектоскопии при контроле качества швов на сварных соединениях металлических деталей и конструкций. Материалы статьи расскажут о технологии применения и этапах процесса.
Для чего нужен контроль сварных швов
Вместе с развитием технологий сварки металлических конструкций, растут требования к качеству изделий. Также руководители предприятий и инвесторы стремятся сократить убытки из-за внеплановых ремонтов и профилактических работ. Промышленность и бизнес требуют соблюдения эксплуатационных характеристик — как экономических, так и временных параметров, заложенных в проект объекта, конструкции или изделия.
Прочность конструкции — технологический параметр, от которого зависит не только работоспособность и производительность объекта, но и безопасность людей и окружающей среды. Пропущенный при визуальном контроле «подповерхностный изъян» сварного шва или несплошность проварки, во время эксплуатации объекта начнут разрастаться под нагрузкой. Однажды шов лопнет, что повлечет за собой череду нарастающих поломок с последующей аварией или катастрофой.
Поэтому, показателям и методам дефектоскопии и контролю за точностью параметров сварных соединений уделяют повышенное внимание не только заказчики и исполнители. Для разработки регламентов и новых способов измерений привлекают учёных из различных отраслей. А государственные службы технического регулирования, стандартизации, метрологии и сертификации создают единые системы измерений.
Из-за своей простоты использования и достаточной точности измеряемых показателей, признание и распространение получила магнитопорошковая дефектоскопия сварных швов. О ней и пойдет речь в этой статье. Чтобы понять преимущества этого метода контроля мы сравним его с другими вариантами проверки качества сварных соединений.
Какие методы проверки сварных соединений применяются
Способы разделяются на две группы:
- Неразрушающий контроль (далее НК).
- Методы разрушающего контроля.
Из второй группы чаще всего применяются механические испытания.
В промышленном использовании, транспорте, строительстве и народном хозяйстве признание и распространение получили неразрушающие способы. Развитие измерительных технологий происходит именно в этой сфере контроля. Разберем способы НК подробнее.
- Визуально-измерительный контроль. Это первоначальный способ проверки качества выполненных работ. Включает в себя внешний осмотр швов и замер геометрических параметров. Для этого используются простые измерительные приборы. Полученные цифры сверяются с нормами в проектной документации, ГОСТах, СНиП и ТУ. Используется как первичный способ выявления дефектов и не способен выявить мелкие и скрытые, внутришовные дефекты.
- Капиллярный контроль. Этот подход основывается на свойствах жидкостей проникать в мельчайшие трещины, поры, каверны или несплавления. Подробнее о дефектах соединений — ниже по тексту. Особые проникающие свойства присущи определённым жидкостям — пенетрантам. На их основе изготавливают составы для нанесения на сварные швы и для магнитопорошковой проверки.
- Ультразвуковые методы контроля (УЗК). Повсеместный и универсальный метод дефектоскопии сварных соединений. Анализ показателей и выявление трещин проводится с помощью дефектоскопов, которые состоят из излучателей и приемников ультразвука.
Различают эхо-импульсный, эхо-зеркальный и зеркально-теневой методы УЗК.
- TOFD или дифракционно-временной способ контроля. Чаще применяется для исследований и выявления дефектов на кольцевых и продольных сварных швах с помощью ультразвукового эха. Действие основано на разнице отраженных волн от трещины или от цельнопроваренной поверхности. Применяется как одногрупповой TOFD метод, так и способы с мультиподдержкой нескольких групп или методики с сочетанием других способов контроля, например с импульсными или эхоповерхностными волнами.
- Вихретоковый анализ. Проводится с помощью сертифицированных приборов — вихревых дефектоскопов. Основан на определении проблем в испытуемых швах с помощью сравнения изменений вихревого тока и электромагнитных полей. Схож по своей работе с ультразвуковыми способами контроля. Как и магнитопорошковый способ, используется для проверки глубиной до 2 мм.
- Радиационная дефектоскопия сварных соединений. На практике ее ещё называют проверка рентгеном, потому что исследования проводят с помощью рентгеновского гамма излучения.
Это самый эффективный способ контроля, но он имеет весьма ограниченное применение из-за радиационной опасности и обязательном использовании специальных средств защиты.
- Магнитопорошковый контроль или дефектоскопия (МПК или МПД). Главный герой сегодняшнего обзора. Позволяет определять дефекты в металле швов типа трещин, непроваров или несплавлений, пор и полостей, твердых включений шлака на глубине не более 2 мм. В следующем разделе статьи мы расскажем о нормативных документах и характеристиках дефектов сварных швов.
Благодаря простоте использования непосредственно на местах, а также способности быстро выявлять тонкие и мельчайшие трещины, МПД получила повсеместное распространение. Метод не нуждается в дорогостоящем и сложном оборудовании и длительной подготовке обслуживающего персонала. Преимущество этого варианта контроля в хорошей визуализации дефектов. Заказчик, без потери времени получает наглядные результаты. Которые видны представителям проверяющей и принимающей сторон. Важно, чтобы результаты исследования были промаркированы для сварщика, который будет устранять выявленные недочеты.
В ходе процесса проверки используется оборудование для намагничивания и размагничивания соответствующие ГОСТ Р 53700-2009. Для измерений на нелинейных поверхностях, например, в углах и цилиндрах, используются насадки и призмы с разными радиусами. Также ими контролируют качество сварных швов на резьбовых соединениях, галтелях и проточках. А для испытаний вращающихся валов задействуют специальные призмы-ложементы.
После магнитопорошкового контроля и проверки объекта дефектоскопистами, они оформляют протокол испытаний с указанием объекта и деталей исследования. В документе отражается дата, место, оборудование и методы контроля. Записываются фамилии ответственных специалистов и их экспертное заключение.
Что такое дефекты швов при сварке?
В Российской Федерации и странах СНГ определения всех дефектов соединений при сварке металлов плавлением обозначены и классифицированы в ГОСТ Р ИСО 6520-1-2012.
Дефекты сварных соединений — это не что иное, как поверхностные или подповерхностные изъяны внутри шва. Они отличаются друг от друга характером, конфигурацией, размером и приводят к сокращению полезного срока эксплуатации металлической конструкции. Воздействуют на ее пользовательские характеристики, приводят к возникновению аварийных ситуаций, в связи с чем, лучше их не допускать. А конструкцию с дефектами – срочно вывести из эксплуатации для дефектовки и последующего восстановления или утилизации изделия.
Магнитопорошковый способ обнаружения изъянов соединения помогает оперативному выявлению дефектов любого типа.
Факторы возникновения дефектов сварных соединений:
- Швы могут обладать низким качеством выполнения, если сварщик не имеет большого опыта проведения работ. В ходе процедуры нарушается технология электродуговой, аргоновой, лучевой сварки. Отсутствует подготовка, термообработка узлов, перепутана схема сборки элементов. Выбран неподходящий режим работы аппарата при лазерной сварке и прочее.
- Некачественные швы появляются по причине использования не профессионально произведенной или поломанной техники при ручной электродуговой сварке, либо металла низкого качества или бюджетных расходных материалов.
- На снижение качества большое влияние оказывают вплавления шлака, множественные брызги металла, загрязнения на сплавляемых поверхностях и плохая организация рабочего места.
Все шовные недостатки имеют разные названия и условно делятся на три группы, каждая из которых обладает своими особенностями. Изъяны бывают:
- наружными;
- внутренними;
- сквозными.
Способ исправления недостатков сварного соединения обусловлен его особенностями. Для предотвращения таких проблем в дальнейшем сварщик исправляет ошибки самостоятельно и осознаёт, что привело к неудовлетворительным результатам. Магнитопорошковый способ контроля в этом случае помогает визуально фиксировать эти ошибки.
Иногда, из-за перегрева, возникают температурные деформации или изменения прочности металла, которые не соответствуют проектным характеристикам конструкции или объекта. Чаще это относится к сварным соединениям калёных и различных по составу металлов. Например, при стыке нержавеющего сплава аустенитного класса с углеродистой сталью.
Технология МПД
Для нахождения специалисты НК используют поверенное оборудование и применяют цветной ферромагнитный компонент, то есть, магнитный порошок. Они наносят этот маркировочный состав на исследуемый сварной стык посредством сухого или мокрого метода.
В первом случае подходит стандартное магнитопорошковое вещество. При выборе мокрого – приготавливается суспензия, включающая магнитный порошок и жидкость с проникающими характеристиками. Для этого используют трансформаторное масло в сочетании с керосином, или воду, в комплексе с веществами, которые препятствуют возникновению коррозии. Эти жидкости называют пенетрантами, т.е. они проникают во все поры, полости и капилляры.
Выбор метода зависит от ситуации. Иногда их сочетают между собой. Независимо от того, какое магнитное вещество будут применять, это помогает выявить минимальные дефекты, В случае использования порошка или суспензии вещество «сосредотачивается» вокруг изъяна, формируя причудливые рисунки, при многочисленных дефектах. Так получается выяснить не только место, но и размер изъяна.
Как правило, дефектоскоп выбирают, учитывая сферу его эксплуатации. Если магнитопорошковая дефектоскопия сварных соединений планируется на выезде, то главным параметром выступает компактность. Если исследования делают стационарно в лаборатории, то размер прибора не имеет значения. В подобных случаях приоритетным является функционал и выбирают более технологичную модель.
Процесс магнитопорошковой дефектоскопии сварных швов
Эта технология контроля качества стыков, производимых сваркой, ее принцип состоит в выявлении магнитных полей на поверхности металла над имеющимся дефектом в шве с использованием ферромагнитных компонентов.
Если заготовка обладает каким-нибудь недостатком, то над ней непременно создается магнитное поле, которое станет изменяться. Участок контроля намагничивается и поток магнитных линий минует дефектные области, возникающие на пути. В итоге магнитное поле искажается. Вместе с тем по краям заготовки формируются магнитные полюса, образующие обособленные магнитные поля.
Все данные о деформации магнитного поля закрепляются магнитопорошковым дефектоскопом. Чем изъян значительнее, тем большая степень рассеивания, а, следовательно, и возможность его выявления. Если поток магнитных линий находится под углом 90 градусов по отношению к изъяну, то возможность его обнаружения возрастает.
На месте дефектов линии создают пик, который выходит за пределы заготовки. Если на местах искажения наблюдаются мелкие частицы ферромагнитных веществ, они изменят свое положение в пространстве, будут совпадать с направлением силовых линий магнитного поля.
Чем значительнее неоднородность поля над дефектом, тем более сильной будет появляющаяся электромагнитная сила, отвечающая за перемещение намагниченных частиц. Из них, в зоне изъяна, формируются цепочки.
Особенности технологии
Проведение магнитно-порошковой дефектоскопии отличается характерными особенностями. Главной из них является то, что невозможно его провести, если заготовка выполнена не из ферромагнитных металлов. Это требуется учесть, если планируется выполнить контроль элементов из цинка или меди, поскольку они относятся к диамагнетикам, поэтому качественного контроля этим способом провести не удастся.
Если потребуется, то в строительной лаборатории IRONCON подберут выездной способ проверки для немагнитных металлов, а также для других видов строительных материалов и конструкций: бетонных и кирпичных изделий, арматуры, сыпучих материалов и пожарных лестниц.
Параметры чувствительности
Помните, что у магнитопорошковой дефектоскопии сварных швов есть определенный параметр чувствительности. Это степень того, с какой точностью будет обнаружен изъян. На чувствительность оказывают влияние магнитные свойства металлов, напряженность магнитного поля, число дефектов, их площадь. Также влияет размер и форма заготовки.
Иногда на чувствительность влияет способ нанесения ферромагнитного вещества (сухой или мокрый, суспензионный). Все это требуется помнить, чтобы понимать, насколько эффективным будет контроль. Важный момент заключается в том, что применение магнитопорошковой дефектоскопии целесообразно в комплексе с другими способами контроля для получения объективной картины и точных цифр.
Виды намагничивания
В рамках проводимого метода применяется 4 варианта намагничивания:
- циркулярный;
- продольный;
- комбинированный;
- в магнитном поле, которое вращается.
Самыми востребованными являются 3 первых типа. Если говорить об элементах, имеющих простую конструкцию, формулировка намагниченности будет такой.
- Циркулярный – представляет собой вид намагничивания, при котором магнитное поле становится замкнутым внутри элемента, а на его концах не образуются магнитные полюса.
- Продольный вариант, в ходе которого магнитное поле направляется вдоль детали, при этом на ее концах формируются магнитные полюса.
- Комбинированный – когда элемент расположен под воздействием двух или более магнитных полей с разным направлением.
Этапы проведения контроля
1. Подготовка заготовки или конструкции к процедуре.
Подготовительный процесс к проведению магнитопорошкового контроля сварных соединений состоит в очистке поверхности элемента от коррозии, загрязнений, а также от смазочных материалов и масел, если контроль выполняется посредством водной суспензии либо сухого порошка. Если поверхность элемента темного цвета и черный магнитный порошок на ней недостаточно заметен, то элемент покрывают слоем красящего состава белого оттенка.
2. Намагничивание заготовки.
Это одно из приоритетных мероприятий магнитопорошкового метода. От того, насколько верно выбран способ, направление и вид намагничивания, а также род тока, зависит чувствительность и определение недостатков.
3. Нанесение на поверхность элемента магнитного индикатора.
Лучшее решение нанесения суспензии состоит в погружении элемента в емкость, в которой суспензия тщательно перемешивается, и в постепенном извлечении из нее. Но такой способ не всегда целесообразен. Обычно суспензию наносят посредством шланга, распыления или душа.
Важно соблюсти слабый напор струи, тогда магнитный порошок остается на дефектных местах. В случае выбора сухой методики магнитопорошкового контроля данные требования касаются давления струи воздуха, посредством которой магнитный порошок наносится на элемент.
Период стекания дисперсной среды повышенной вязкости занимает больше времени, поэтому продуктивность работы контролёра сокращается.
4. Зрительный осмотр заготовки.
Расшифровка индикаторного изображения и выполнение разбраковки. Контролер обязан провести осмотр элемента после стекания с нее основной массы суспензии, когда отложения порошка становятся одинаковыми.
Детали проверяются зрительно, но в некоторых ситуациях для расшифровки типа изъянов используется профессиональная оптика. Ее настройка выполняется согласно официальной документации.
Кто проводит МПД
В строительной лаборатории IRONCON-Lab проводят магнитопорошковый контроль и радиографический контроль сварных соединений по выгодным ценам. Испытания делают либо в помещении, оборудованной специальной техникой, либо на стройплощадке объекта. В процессе экспертизы составляется протокол, в котором дефектоскописты сделают вывод о соответствии или несоответствии выполненных строительных работ.
Магнитопорошковый метод неразрушающего контроля, МПК деталей и конструкций
Методы нанесения магнитно порошкового слоя:
— сухой способ, когда используют намагниченный порошок;
— влажный способ, когда используют суспензию;
— метод, когда наносится магнитогумированная паста.
Нанесение магнитных материалов присущих каждому методу осуществляется так:
— сухой порошок распыляют по исследуемой поверхности специальным распылителем или погружают изделие на некоторое время в посуду, где находится порошок;
— суспензия наносится путем наливания на поверхность и ее распределения по поверхности или окунанием изделия в раствор суспензии. В последнее время стали использовать аэрозольные баллоны, которые распыляют водный или масляный раствор суспензии на объект исследования.
При определении качества используемых магнитных материалов руководствуются показателями, приведенными в техническом описании к магнитосодержащему материалу, и прилагающейся методикой проверки качества на опытных образцах деталей, уже имеющих описание обнаруженных дефектов. Благодаря таким предварительным исследованиям удается добиться нужной технологии контроля и выявить чувствительность магнитных материалов.
Вследствие проведения контроля составные частицы материала подлежат намагничиванию и выстраиванию их в виде валиков. Индикаторная картинка достигает фиксирующего положения изображения из осевшего порошка. Тогда она и рассматривается под оптическими устройствами, увеличивающими изображения в разных ракурсах света (местного и общего).
Когда применяют люминесцентные порошки, то осматривают поверхность при помощи ультрафиолетовых лучей.
Преимущество применяемого метода, проводящегося щадящим для изделия методом, обусловлено не трудоёмкостью используемого процесса,обладающего высокой производительностью, и быстрым обнаружением дефектов изделия как поверхностного, так и подповерхностного слоя.
Метод магнитопорошкового контроля позволяет определить незаполненные полости и дефекты, которые заполнились инородными для структуры веществами.Используемый метод может с успехом использоваться на различных этапах изготовления деталей, а также для обнаружения дефектов, появившихся в результате усталости металла. Недостаток, который имеет метод, один — сложности при определении глубины, на которую распространилась трещина.
Недостаток магнитопорошкового метода неразрушающего контроля выражается в том, что метод не позволяет проконтролировать процессы изменения в конструкциях и деталях из неферромагнитных сталей, которые не имеют достаточного намагничивания на поверхности, что способствовало бы нанесению индикатора,необходимого для проведения контроля. Она неоднородна по своему строению, имеет изменения в структуре, обозначенные неоднородностью и несоответствием направления намагниченных слоев, или не соответствует принятому за основу углу в 30 градусов.
Контроль магнитных частиц — обзор
Другие методы обнаружения трещин
Широко используются несколько других методов обнаружения трещин, включая контроль магнитных частиц, дефектоскопию красителя и ультразвук. Для магнитопорошкового контроля и дефектоскопии красителей используются многие химические препараты. К ним относятся растворители, красители и «проявители». Многие из них удобно упакованы в аэрозоли. Другие состоят из ванн, в которые погружаются проверяемые детали.
Растворители, как правило, обладают обезжиривающим действием и поэтому вредны для кожи. Они могут вызвать дерматит в долгосрочной перспективе, если не свести к минимуму контакт с кожей. Обычно они относительно летучие и выделяют пары, которые можно вдохнуть. Воздействие на здоровье зависит от воздействия и относительной токсичности растворителя. Они могут включать раздражение глаз и легких, головную боль, тошноту, головокружение и головокружение. Бессознательное состояние или даже смерть могут возникнуть в результате воздействия паров растворителей в больших количествах.
Когда-то предпочтительным вариантом были хлорированные растворители, поскольку они, как правило, негорючие. Стратегия заключалась в использовании растворителя с наименьшей токсичностью. Однако из-за опасений по поводу атмосферы многие обычные хлорированные растворители в настоящее время больше не используются. Это заставило работодателей выбирать альтернативы, некоторые из которых более токсичны, а некоторые легко воспламеняются. Таким образом, перед использованием растворителя необходимо изучить паспорт безопасности (MSDS) производителя, чтобы получить представление обо всех его свойствах, чтобы можно было принять меры по его правильному хранению и избежать воздействия паров и любых опасностей возгорания, которые могут возникают.Растворители всегда следует использовать в хорошо вентилируемых помещениях, чтобы избежать образования высоких концентраций паров.
Многие аэрозоли раньше содержали пропелленты на основе хлорированных углеводородов или хлорированных фторуглеродов (CFC), но сейчас они не используются. Используемые в настоящее время пропелленты включают некоторые легковоспламеняющиеся вещества, такие как бутан. Следует внимательно прочитать паспорт безопасности материала. Некоторые хлорированные растворители все еще используются. Они имеют тенденцию разлагаться в дуге с образованием чрезвычайно токсичных продуктов, таких как фосген и хлористый водород.Поэтому очень важно следить за тем, чтобы пары растворителя не попадали в зоны, где выполняется сварка.
Объемные запасы растворителей или аэрозолей следует хранить отдельно от рабочего помещения в контейнерах, соответствующих их свойствам, например: легковоспламеняющиеся вещества и препараты следует хранить в металлических шкафах с четкой маркировкой, указывающей на характер содержимого. В рабочем помещении следует держать только количество, необходимое для немедленной работы.
Если используются ванны для парового обезжиривания, они должны содержаться в хорошем рабочем состоянии — конструкция должна содержать пар, чтобы сотрудники не подвергались воздействию.
Следует по возможности избегать протирания предметов тканями, пропитанными растворителем, поскольку выброшенные салфетки могут представлять опасность пожара, и такая практика имеет тенденцию приводить к сильному воздействию на кожу и дыхательную систему.
Везде, где есть вероятность попадания капель жидкости в глаза, следует надевать средства защиты глаз. Персонал не должен есть или курить в местах, где есть растворители. Их следует тщательно мыть после работы, а также перед едой или курением.
Контроль магнитных частиц, влажный флуоресцентный контроль
Намагничивает для поиска разрывов
Магнитопорошковый контроль успешно обнаруживает поверхностные и приповерхностные дефекты в ферромагнитных материалах, таких как сталь и железо.Это всего лишь один из видов неразрушающего контроля (NDT), выполняемый в Laboratory Testing Inc. Методы неразрушающего контроля позволяют испытывать или проверять материалы и продукты без повреждений. LTI также обеспечивает проникающий, ультразвуковой, радиографический (рентгеновский) и визуальный контроль, а также испытания под гидростатическим давлением. Эти методы неразрушающего контроля будут рассмотрены в следующих нескольких выпусках LabNews.
Процесс
Магнитопорошковый контроль выполняется путем распределения мелких магнитных частиц по поверхности образца, когда он намагничивается, что вызывает скопление частиц на неоднородностях, таких как трещина, нахлест, включение или шов.Эти частицы обладают высокой магнитной проницаемостью, поэтому они легко намагничиваются и притягиваются небольшими магнитными полями рассеяния из неоднородностей. Обученный и опытный техник интерпретирует показания, которые могут наблюдаться во время осмотра.
Магнитные частицы можно наносить в сухом виде в виде порошка или во влажном виде в виде суспензии в носителе на нефтяной или водной основе. Сухие частицы чаще всего используются для полевых проверок. Флуоресцентный влажный контроль считается лучшим для обнаружения очень мелких неоднородностей, потому что он использует гораздо более мелкие частицы, а жидкий носитель позволяет этим частицам легко течь в небольшие поля утечки для формирования индикаторов.
Влажный контроль имеет преимущество перед сухим контролем, потому что оборудование, используемое в этом процессе, может быстро и легко распылять равномерный слой частиц по поверхности материала или детали, подлежащей контролю. Магнитное поле может создаваться с помощью цепей постоянного тока (DC) или цепей переменного тока (AC). Цепи переменного тока создают поля, которые ограничены близкой поверхностью испытуемого образца и полезны при обнаружении поверхностных трещин. Цепи постоянного тока создают магнитные поля, которые проникают на небольшое расстояние в испытуемый образец и полезны также для обнаружения неоднородностей под поверхностью.
Магнитопорошковый контроль может применяться к сырью, деталям или продуктам на различных этапах производственного процесса. Он также применяется при техническом обслуживании и капитальном ремонте оборудования или техники для обнаружения усталостных трещин.
Инспекции в LTI
В LTI наиболее распространенным методом, используемым для контроля магнитных частиц, является флуоресцентный мокрый непрерывный метод с использованием полноволнового постоянного тока (FWDC). Деталь помещается в один из трех горизонтальных блоков влажной флуоресцентной лампы, а затем прикладывается магнитное поле, в то время как суспензия магнитных частиц распыляется или выливается на испытуемый образец.Наши горизонтальные блоки имеют размер от 6 футов до 12 футов в длину. Детали большего размера проверяются с помощью кабелей, хомутов и переносного оборудования.
Преимущества и ограничения
Относительно нет ограничений на размер деталей, которые могут быть проверены с использованием метода магнитных частиц, за исключением ограничений, связанных с производительностью испытательного оборудования. Для осмотра крупных деталей обычно требуются высокие токи. Проверки необходимо проводить в двух направлениях, чтобы гарантировать обнаружение неоднородностей в продольном и окружном направлениях.
Не требуется тщательной или сложной предварительной очистки деталей перед проверкой, обычно для удаления масел требуется только обезжиривание растворителем. Краску, окалину после термообработки, жир и т. Д. Следует удалить, чтобы получить наиболее точные результаты испытаний. Осмотр можно проводить до и после нанесения покрытия. Стандартной практикой является размагничивание деталей после осмотра и дополнительная очистка деталей от магнитных частиц.
Стандарты и спецификации
В качестве основы для проведения магнитопорошкового контроля используются различные стандарты и спецификации.К ним относятся разделы кодексов Американского общества инженеров-материаловедов (ASME), Спецификации аэрокосмических материалов (AMS), Спецификации Общества автомобильных инженеров (SAE), Стандарты Американского общества испытаний и материалов (ASTM), различные военные стандарты и Американское общество Рекомендации по неразрушающему контролю (ASNT).
Контроль магнитных частиц — Magna Chek
Ограничиваясь исследованием деталей из железа и стали, на которые сильно влияют магниты (ферромагнетики), Контроль магнитных частиц очень полезен для обнаружения мелких поверхностных и приповерхностных трещин на глубину. около 0.100 ”.
Магнитный контроль частиц используется для тестирования широкого спектра сырьевых или промышленных материалов и компонентов, включая отливки, поковки и сварные детали, важные для безопасности автомобильные детали и инфраструктуру, такую как мосты или резервуары для хранения.
Magna Chek оснащена высококачественными машинами Magna Flux для проведения испытаний на магнитные частицы на самых разных деталях как по размеру, так и по геометрии. Скорость и относительная простота этой технологии делают ее идеальной для приложений большого объема.Испытания проводятся на крупных партиях со скоростью до 1500 деталей в час.
Устройство Wet Magna-Glo 12 футов — это устройство Magna-Glo на 6000 А с вторичной катушкой на 2000 А, которая вмещает детали от 1 до 12 дюймов длиной и до 24 дюймов в диаметре. Производительность составляет около 1000 штук в час. Использование вторичной обмотки позволяет нам выполнять проверку головки и змеевика одновременно.
Конвейерная установка Magna-Glo с двумя дозаторами с автоматической катушкой, размагничивателем и конвейером, обрабатывает до 1500 штук в час и идеально подходит для тестирования деталей большого объема, таких как болты, винты и т.
Конвейерный контроль влажных магнитных частиц Duo-VEC создает многовекторное поле в детали для обнаружения как продольных, так и поперечных дефектов. Это специально разработанное устройство идеально подходит для испытаний нестандартных конфигураций деталей длиной до 24 дюймов, таких как шатуны, рулевые рычаги, хомуты, компоненты подвески, небольшие поковки и отливки.
Magna Chek может выполнять контроль магнитных частиц на месте с помощью одного из наших мобильных устройств. Эти устройства могут быть оснащены широким спектром устройств неразрушающего контроля по требованию заказчика, что позволяет нам планировать комплексный подход к вашим материалам и обнаруживать поверхностные и подповерхностные неоднородности. Мы доступны для проверки на месте энергетических турбин, котлов, котлов, сосудов, конструкционных сварных соединений, крановых узлов и крюков, подъемно-транспортного оборудования и трубопроводов.
Испытание магнитными частицами
Контроль магнитных частиц (MPT) — это стандартный метод неразрушающего контроля (NDE) для обнаружения дефектов в ферромагнитных материалах, таких как железо, никель и кобальт, а также в некоторых из их сплавов.
Магнитно-порошковые испытания — это относительно простой метод испытаний для обнаружения поверхностных и подповерхностных дефектов с использованием принципа рассеяния магнитного потока для проверки слитков, отливок, поковок, прокатных листов, листов, прутков, стержней, сварных соединений, валов, шестерен и других инженерных компонентов в литые, кованые, механически обработанные, во время производства и эксплуатационных проверок.
Его также можно использовать для проверки того, что технологические операции, такие как термообработка, механическая обработка и шлифование, не выявили и не привели к нарушениям целостности. Испытание на магнитные частицы состоит из намагничивания изделия, нанесения частиц и интерпретации рисунков, образованных частицами, когда они притягиваются магнитными полями рассеяния.
MPT — наиболее широко используемый метод испытаний в черной металлургии, производстве стали и обрабатывающей промышленности.
Типы магнитных частиц
- Сухие частицы (красные и желтые)
- Влажные частицы (черные и флуоресцентные)
Методы магнетизма
- Непрерывный метод
- Остаточный метод
Типы магнетизма
- Круговой магнетизм — выстрел в голову, стержни и центральный проводник.
- Продольный магнетизм — катушка и ярмо
Стенд
Хомут
Заявки:
- Этот метод используется для проверки различных форм изделий, включая отливки, поковки и сварные детали.
- Многие отрасли промышленности используют магнитопорошковый контроль для определения пригодности компонента к использованию.
- Некоторыми примерами отраслей промышленности, использующих контроль магнитных частиц, являются сталелитейная, автомобильная, нефтехимическая, энергетическая и аэрокосмическая промышленность.Подводный контроль — это еще одна область, где магнитопорошковый контроль может использоваться для проверки таких объектов, как морские конструкции и подводные трубопроводы.
Что такое испытание магнитными частицами?
Что такое испытание магнитными частицами?
Проверка магнитных частиц, также известная как проверка магнитных частиц (MPI), — это процесс, при котором компонент намагничивается для создания линий магнитного потока внутри компонента. Когда линии магнитного потока встречаются с разрывом, который обычно находится в перпендикулярной ориентации к направлению потока магнитного потока, на поверхности компонента и непосредственно над ней формируется поле рассеяния магнитного потока.
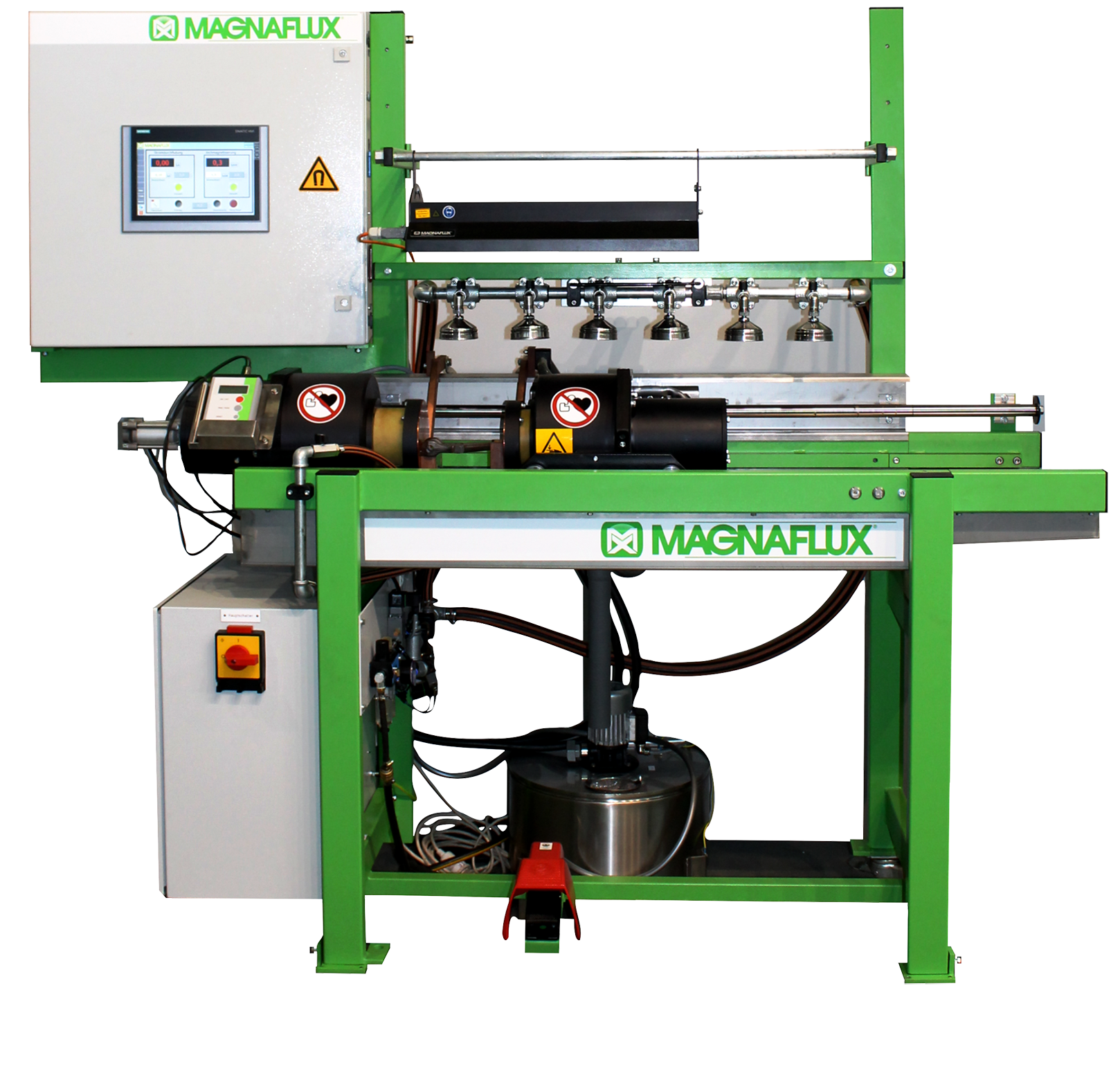
Какие методы намагничивания?
Существует два основных метода создания магнитного потока в исследуемом компоненте.Поток магнитного потока может быть создан путем введения внешнего магнитного поля в компонент от источника, такого как постоянный магнит, электромагнит или проводник с током, примыкающий к компоненту или сформированный в виде катушки. В качестве альтернативы, электрический ток можно пропустить непосредственно через компонент, который будет индуцировать магнитный поток в компоненте, перпендикулярном направлению потока тока. Используемая форма волны тока может варьироваться от постоянного до полного переменного тока. Как правило, переменный ток очень чувствителен к поверхностным нарушениям сплошности, в то время как постоянный ток может обнаруживать небольшие подповерхностные неоднородности.
Сухие и влажные магнитные частицы
Частицы, используемые при испытании магнитных частиц, важны для индикации неоднородностей в исследуемой детали. Свойства магнитных частиц, используемых при испытании магнитных частиц, должны включать высокую магнитную проницаемость (способность намагничиваться), чтобы позволить частицам притягиваться к полям рассеяния магнитного потока, и низкую удерживающую способность (способность частиц сохранять намагниченность) для предотвращения частицы от прикрепления друг к другу или к поверхности компонента.Используются два типа магнитных частиц:
Сухие магнитные частицы — этот метод включает использование изменения размеров частиц для обозначения различных размеров мест утечки потока. Более мелкие частицы более чувствительны к участкам / полям утечки потока и, следовательно, способны идентифицировать более мелкие дефекты / дефекты, а более крупные частицы способны идентифицировать более крупные места утечки потока.
Влажные магнитные частицы — Этот метод включает в себя взвешивание магнитных частиц в таком веществе, как вода или масло.Этот метод более чувствителен к участкам утечки магнитного потока, вызванным дефектами и дефектами, чем сухие магнитные частицы, поскольку частицы более подвижны во взвешенном состоянии. Этот метод также позволяет покрыть большую площадь поверхности, что указывает на большее количество мест утечки потока.
TWI Services
Тестирование с помощью магнитных частиц — это метод неразрушающего контроля, который можно использовать для проверки различных ферромагнитных компонентов и продуктов. К ним относятся отливки, поковки и сварные детали.Этот метод используется в различных отраслях промышленности, особенно при определении пригодности компонента для эксплуатации. Отрасли, в которых используются испытания на магнитные частицы, включают аэрокосмическую, автомобильную, морскую, энергетическую, нефтегазовую, компоненты и конструкции, машиностроение и производство.
TWI использовали свой 40-летний опыт для разработки широкого спектра методов неразрушающего контроля (NDT) и предоставили услуги в отрасли, связанные с контролем магнитных частиц. Примеры этой работы включают:
Компоненты и конструкции
- TWI проверил компонент в механической системе с помощью магнитопорошкового контроля для обнаружения поверхностных или приповерхностных дефектов или дефектов.
- TWI исследовала технику горячего предварительного напряжения. TWI изучила влияние этих испытаний под давлением и то, как они влияют на испытания, проводимые на протяжении всего срока службы компонента / конструкции. В этой статье также рассматривается использование тестирования магнитных частиц, выполненного в рамках этого исследования.
- Метод магнитопорошкового контроля был проведен TWI для исследования сварного клапана коллектора (компонента / части оборудования, который соединяет клапаны гидравлической системы).
Нефть и газ
Aerospace
Marine
Power
- TWI проверила отремонтированный реактор на атомной электростанции с помощью магнитопорошкового контроля. Основная ответственность TWI заключалась в том, чтобы в отремонтированном компоненте не было дефектов, включая поверхностные и подповерхностные трещины.
Как член Института сварки вы имеете доступ к нашим преимуществам членства. Как инженер, техник или персонал, занимающийся испытанием магнитных частиц, Институт сварки имеет преимущества, которые могут вам помочь, в том числе:
Щелкните здесь, чтобы просмотреть все преимущества нашего членства!
Учебные курсы по испытанию магнитных частиц
Ознакомьтесь с нашим разделом «Тестирование магнитных частиц — TWI Training and Examinations Insight», чтобы узнать больше о курсах, предлагаемых TWI Training and Examinations!
Магнитные частицы, уровни 1 и 2
Цели обучения
Этот курс содержит подробные инструкции по теории и практике контроля магнитных частиц, включая возможности и ограничения этого метода.Будут даны инструкции по общепринятым методам проверки в соответствии с нормами и стандартами.
Применимые стандарты
Этот курс соответствует требованиям учебной программы CAN / CGSB-48.9712, ISO 9712 и SNT-TC-1A.
Определение персонала уровня 2 (согласно CGSB)
Персонал уровня 2 определяется как персонал, имеющий квалификацию в области испытаний на магнитные частицы, который будет выполнять и / или осуществлять непосредственный контроль магнитных частиц в соответствии с установленными или признанными процедурами и нести ответственность за магнитные частицы. метод или технику, которые будут использоваться, и для оценки результатов испытаний.
Краткое содержание курса
- Введение
- Краткое описание ролей: Канадский институт неразрушающей оценки; Канадский совет по общим стандартам; Министерство природных ресурсов Канады; SNT-TC-1A
- Процедуры сертификации и форматы заявок
- Преимущества и недостатки основных методов неразрушающего контроля
- История магнитопорошкового контроля
- Основные принципы магнитов и магнитных полей
- Магнитное поле Земли
- Теория магнетизма
- Закон магнетизма
- Магниты и их магнитное поле
- Кривые магнитных характеристик и гистерезис
- Материалы, связанные с магнитными полями
- Ферромагнитные материалы
- Материалы диамагнитные
- Парамагнитные материалы
- Обнаружение направления и неоднородности магнитного поля
- Поверхностные неоднородности
- Подземные неоднородности
- Влияние на показания
- Намагничивание и электрические токи
- Основная терминология, связанная с электрическими токами
- Создание круговых магнитных полей: правило правой руки; Приложения; обнаруживаемые неоднородности; оборудование; меры предосторожности
- Производство продольных полей
- Намагничивание круговыми полями
- Выстрелы в голову
- Центральные проводники
- Катушки и кабельная обмотка
- Штыри и электромагниты
- Основные этапы контроля магнитных частиц
- Выбор правильного метода намагничивания
- Форма, состояние и расположение детали
- Искомые нарушения целостности
- Установление действующих требований
- Последовательность операций
- Контрольные материалы
- Мокрый и сухой методы
- После проверки производительности
- Электромагнитный спектр и черные огни
- Размагничивание
- Основные принципы
- Методы
- Причины на
- Терминология, связанная с размагничиванием
- Оборудование
- Методы размагничивания
- Измерение остаточных полей
- Требования к размагничиванию
- Типы оборудования
- Общедоступное оборудование
- Оборудование специального назначения
- В соответствии с письменными процедурами
- Где искать и что искать
Примечание. Защитная обувь обязательна для всех лабораторных работ.
Этот курс предлагается в партнерстве с Канадским институтом неразрушающей оценки (CINDE).
Посетите веб-сайт CINDE, чтобы зарегистрироваться.
МАГНИТНАЯ ЧАСТЬ
МАГНИТНАЯ ЧАСТЬ ПРОВЕРКА МАГНИТНОЙ ЧАСТИЦЫМагнитопорошковый контроль — метод обнаружения невидимых трещин. и другие дефекты в ферромагнитных материалах, таких как железо и сталь. Этот Метод контроля — неразрушающий контроль, то есть выполняется на реальной части без повреждения детали.Это не применимо к немагнитные материалы.
При быстром вращении, возвратно-поступательном движении, вибрации и других высоких нагрузках детали самолета, небольшие дефекты часто развиваются до такой степени, что вызывают полный отказ детали. Магнитопорошковый контроль зарекомендовал себя надежен для быстрого обнаружения таких дефектов, расположенных на или рядом с поверхность. При использовании этого метода контроля локализация дефекта указан, и указаны приблизительный размер и форма.
Процесс проверки состоит из намагничивания детали и последующего применения ферромагнитные частицы на исследуемую поверхность. Ферромагнетик частицы (обозначающая среда) могут находиться во взвешенном состоянии в жидкости, которая промывается по детали; деталь может быть погружена в суспензионную жидкость; или частицы в форме сухого порошка могут быть напылены на поверхность часть. Мокрый процесс чаще используется при досмотре самолетов. части.
Если присутствует разрыв, магнитные силовые линии будут нарушены и противоположные полюса будут существовать по обе стороны от разрыва. В намагниченные частицы, таким образом, образуют узор в магнитном поле между противоположные полюса. Этот шаблон, известный как «указание», предполагает примерная форма проекции поверхности разрыва. Разрыв может быть определено как нарушение нормальной физической структуры или конфигурации такой детали, как трещина, ковочный нахлест, шов, включение, пористость и подобное, аналогичное, похожее.Прерывистость может повлиять или не повлиять на полезность детали.
Разработка показаний
Когда несплошность намагниченного материала открывается на поверхности и магнитное вещество в виде средства индикации доступно на поверхности утечка потока на неоднородности имеет тенденцию к формированию указание среды на путь с более высокой проницаемостью. (Проницаемость термин, используемый для обозначения легкости, с которой может быть установлен магнитный поток в данной магнитной цепи.) Из-за магнетизма в детали и прилипание магнитных частиц друг к другу, индикация остается на поверхности детали в виде примерного контура разрыв, который находится непосредственно под ним.
То же действие происходит, когда разрыв не открыт для поверхность, но поскольку количество утечки потока меньше, меньше частиц удерживаются на месте, и появляется более слабая и менее четкая индикация. полученный.
Если неоднородность находится очень далеко от поверхности, возможно, нет
утечка потока и, следовательно, отсутствие индикации на поверхности. Утечка флюса
на поперечном разрыве показано на рисунке 10-1. Утечка флюса
на продольном разрыве показано на рисунке 10-2.
Типы раскрытых нарушений целостности
Следующие типы несплошностей обычно обнаруживаются магнитопорошковый тест: трещины, нахлесты, швы, холодные отборы, включения, сколы, слезы, трубы и пустоты.Все это может повлиять на надежность деталей. в сервисе.
Трещины, трещины, разрывы, разрывы, швы, пустоты и трубы образуются фактический разрыв или разрыв твердого металла. Холодные затворы и нахлёстки складки, образовавшиеся в металле, нарушающие его непрерывность.
Включения — это инородный материал, образованный примесями в металле во время
этапы обработки металла. Они могут состоять, например, из кусочков
футеровка печи, подобранная при плавке основного металла или другого
иностранные составляющие.Включения нарушают целостность металла
потому что они препятствуют соединению или сварке смежных поверхностей металла.
Подготовка деталей к испытаниям
Жир, масло и грязь должны быть удалены со всех частей, прежде чем они будут проверено. Очистка очень важна, так как любой жир или другие посторонние предметы наличие может давать несущественные признаки из-за налипания магнитных частиц к инородному материалу, поскольку суспензия стекает из детали.
Смазка или посторонний материал в достаточном количестве на неоднородности может также предотвратить образование рисунка на неоднородности. это не рекомендуется полагаться на суспензию магнитных частиц для очистки часть. Очистка суспензией не тщательная, а также наличие посторонних материалов снятие с детали приведет к загрязнению подвески, тем самым уменьшив его эффективность.
При сухой процедуре тщательная очистка абсолютно необходима.Смазка или другой посторонний материал может удерживать магнитный порошок, что приведет к не относящиеся к делу показания и делающие невозможным распространение показаний средний равномерно по поверхности детали.
Все небольшие отверстия и масляные отверстия, ведущие во внутренние проходы или полости следует заткнуть парафином или другим подходящим неабразивным материалом.
Покрытия из кадмия, меди, олова и цинка не мешают удовлетворительные результаты магнитопорошкового контроля, если покрытия необычно тяжелые или обнаруживаемые неоднородности необычно небольшой.
Хромирование и никелирование обычно не влияет на показания трещин, открытых на поверхности основного металла, но предотвратит появление признаков мелких неоднородностей, таких как включения.
Поскольку он более магнитный, никелирование более эффективно
чем хромирование в предотвращении образования показаний.
Влияние направления потока Чтобы обнаружить дефект в детали, необходимо, чтобы магнитный силовые линии проходят примерно перпендикулярно дефекту.Следовательно, необходимо индуцировать магнитный поток более чем в одном направлении, так как дефекты могут располагаться под любым углом к главной оси детали. Это требует две отдельные операции намагничивания, называемые круговым намагничиванием и продольная намагниченность. Эффект направления потока проиллюстрирован. на рисунке 10-3. Круговое намагничивание — это индукция магнитного поля, состоящего из концентрических окружностей силы вокруг и внутри детали, пропуская электрические ток через деталь.Этот тип намагничивания позволяет обнаружить дефекты. идущий примерно параллельно оси детали. Показано круговое намагничивание части твердого поперечного сечения. на рисунке 10-4. Каждая головка намагничивающего устройства электрически подключена к кнопочному управлению, так что при установлении контакта ток намагничивания переходит от одной головы к другой через деталь. |
На рисунке 10-5 показано круговое намагничивание. полой детали, пропуская ток намагничивания через проводник планка, расположенная на оси детали.
При продольном намагничивании магнитное поле создается в направлении параллельно длинной оси детали. Это достигается путем размещения часть соленоида, возбуждаемая электрическим током. Металлическая часть тогда становится сердечником электромагнита и намагничивается за счет индукции от магнитное поле, создаваемое в соленоиде.
При продольном намагничивании длинных деталей соленоид должен перемещаться вдоль детали, чтобы намагнитить ее.(См. Рисунок 10-6.) Это необходимо для обеспечения надлежащей напряженности поля во всем на всю длину детали.
Соленоиды создают эффективное намагничивание примерно на 12 дюймов с каждого конца катушки, таким образом размещая части или секции приблизительно 30 дюймов в длину. Продольная намагниченность, эквивалентная полученной соленоидом может быть выполнено наматывание гибкого электрического проводника вокруг детали, как показано на рисунке 10-7.Хотя этот метод не так удобен, он имеет то преимущество, что катушки соответствуют ближе к форме детали, таким образом создавая несколько более однородный намагниченность.
Метод гибкой катушки также подходит для больших или неправильной формы детали, для которых нет стандартных соленоидов.
Влияние плотности потока
Эффективность магнитопорошкового контроля также зависит от плотность потока или напряженность поля на поверхности детали, когда указывающая среда применяется.Поскольку плотность магнитного потока в детали увеличивается, чувствительность теста увеличивается из-за большей утечки магнитного потока на несплошностях и, как следствие, улучшенное формирование магнитных частиц узоры.
Однако чрезмерно высокие плотности магнитного потока могут давать несущественные показания; например, модели движения зерна в материале. Эти указания будет мешать обнаружению закономерностей, возникающих в результате значительного разрывы. Поэтому необходимо использовать поле высокой напряженности. достаточно, чтобы выявить все возможные вредные разрывы, но недостаточно сильные давать сбивающие с толку несущественные показания.
Методы намагничивания
Когда деталь намагничивается, напряженность поля в детали увеличивается до максимума для конкретной силы намагничивания и остается на этом максимуме пока сохраняется сила намагничивания.
При снятии намагничивающей силы напряженность поля уменьшается до более низкой остаточной стоимости в зависимости от магнитных свойств материала и форма детали. Эти магнитные характеристики определяют, непрерывный или остаточный метод используется для намагничивания детали.
При непрерывном контроле деталь намагничивается, а указывает среду, применяемую при сохранении силы намагничивания. В доступная плотность магнитного потока в детали, таким образом, является максимальной. Максимальное значение потока напрямую зависит от силы намагничивания и проницаемости из материала, из которого изготовлена деталь.
Непрерывный метод может применяться практически во всех круговых и продольных процедуры намагничивания. Непрерывная процедура обеспечивает большую чувствительность чем остаточная процедура, особенно при обнаружении подземных разрывов.Высокая критичность деталей и узлов самолета и необходимость для подземной инспекции во многих приложениях привели к непрерывному метод получил более широкое распространение.
Поскольку непрерывная процедура выявляет более незначительные разрывы, чем остаточная процедура, тщательная и разумная интерпретация и оценка разрывов, обнаруженных в результате этой процедуры, необходима.
Процедура остаточного контроля предполагает намагничивание детали. и приложение показывающей среды после того, как сила намагничивания был удален.Эта процедура основана на остаточном или постоянном магнетизме. в части и более практична, чем непрерывная процедура, когда намагничивание достигается за счет гибких катушек, намотанных вокруг детали.
Как правило, остаточная процедура используется только для сталей, подвергнуты термообработке для работы в напряженных условиях
Обозначение показаний
Правильная оценка характера показаний крайне важно, но иногда трудно сделать это, наблюдая за показаниями один.Основными отличительными чертами показаний являются форма, наращивание, ширина и резкость контура. Эти характеристики, в общем, более ценны для различения типов разрывов, чем в определении их степени тяжести. Однако внимательное наблюдение за персонажем картины магнитных частиц всегда следует включать в оценка значимости указанного разрыва.
Наиболее заметными признаками являются признаки трещин. открытый на поверхность.Эти несплошности включают усталостные трещины, нагрев лечить трещины, усадочные трещины в сварных швах и отливках, а также шлифовальные трещины.
Усталостные трещины дают четкие четкие узоры, обычно однородные и непрерывные. по всей длине и с хорошим наращиванием. Они часто бывают неровными внешний вид, по сравнению с прямыми признаками шва, и может также немного меняют направление в локализованных областях. Фигура 10-8 иллюстрирует усталостную трещину.
Усталостные трещины обнаружены на деталях, которые были в эксплуатации, но ни разу не нашел в новых запчастях.Обычно они находятся в очень напряженных областях часть или где по какой-то причине существует концентрация напряжений. это важно понимать, что даже небольшая усталостная трещина указывает на положительный что происходит отказ задействованных частей.
Трещины после термообработки имеют гладкие очертания, но обычно менее четкие и меньше наростов, чем усталостные трещины. На тонких срезах, таких как цилиндр стенки ствола, трещины от термообработки могут давать очень тяжелые узоры (рисунок 10-9).Эти трещины термообработки имеют характерную форму, состоящую из коротких зубчатых линий, сгруппированных вместе.
Усадочные трещины дают четкий, четкий рисунок, а линия обычно очень зазубренный. Поскольку стенки усадочных трещин находятся близко друг к другу, их признаки обычно накапливаются в меньшей степени, чем признаки усталостных трещин.
Трещины от шлифования мелкие и острые, но редко имеют наросты, потому что их ограниченной глубины. Трещины шлифования отличаются от однолинейных указателей. к разветвленной сети линий.Трещины при шлифовании обычно связаны с направление шлифования. Например, трещина обычно начинается и продолжается перпендикулярно движению шлифовального круга, что дает довольно симметричный шаблон. Признаки шлифовальных трещин часто можно определить по средства этого отношения.
Швы обычно прямые, острые и мелкие. Они есть часто с перерывами и иногда с очень небольшим накоплением.
Волосы — это очень тонкие швы, в которых стороны шва прижимаются очень близко друг к другу во время изготовления.Показания к линии роста волос очень тонкий и острый, с очень небольшим налетом. Разрывы этого тип обычно считается вредным только в сильно нагруженных частях.
Включения представляют собой неметаллические материалы, такие как шлаковые материалы и химические вещества. соединения, которые были захвачены затвердевающим слитком. Они обычно удлиненные и растянутые по мере обработки слитка при последующей обработке операции.
Включения появляются в частях различных размеров и форм, от стрингеров. легко видимые глазу частицы, видимые только при увеличении.В готовой детали они могут проявляться как поверхностные, так и подповерхностные неоднородности.
Признаки подповерхностных включений обычно широкие и нечеткие. Они редко бывают непрерывными или равномерной ширины и плотности по всей длине. Появляются более крупные включения, особенно те, которые находятся рядом с поверхностью или открыты для нее. более четко определено. Однако внимательное изучение обычно выявляет их отсутствие определения и тот факт, что указание состоит из нескольких параллельные линии, а не одна линия.Эти характеристики обычно отличить тяжелое включение от трещины.
Если полости расположены значительно ниже поверхности детали, испытание магнитными частицами не является надежным методом их обнаружения. Если будет получено какое-либо указание, скорее всего, оно будет нечетким и неточным. очертания полости, при этом магнитное вещество стремится распределить по всей площади, а не четко очерчивать границы прерывность.Дефекты этого типа легче обнаружить рентгенологически. процедуры.
Круги можно отличить по форме и расположению. Они имеют тенденцию происходить на концах или залитом поковки. Показания обычно тяжелые и нерегулярные. Острова и короткие указатели ответвлений обычно ломают круг индикация любой длины, а шкала неизменно включается в нахлест дает нечеткие или мелкие папоротниковые узоры, происходящие от основного признака.
Когда слиток затвердевает, распределение различных элементов или соединения, как правило, неоднородны по массе слитка.Таким образом, может произойти заметная сегрегация некоторых составляющих. Поскольку слиток кованые, а затем прокатанные, эти сегрегации удлиняются и уменьшаются в поперечное сечение. При последующей обработке они могут выглядеть очень тонкими. параллельные линии или полосы, известные как полосы.
Сегрегация в виде полосатости иногда выявляется магнитным контроль частиц, особенно при использовании поля с высокой напряженностью. Бандаж обычно не считается значимым.
Наиболее серьезные формы сегрегации, вероятно, возникают в отливках.